Aerodynamic Design of a Reusable Booster Stage Flight Experiment
Total Page:16
File Type:pdf, Size:1020Kb
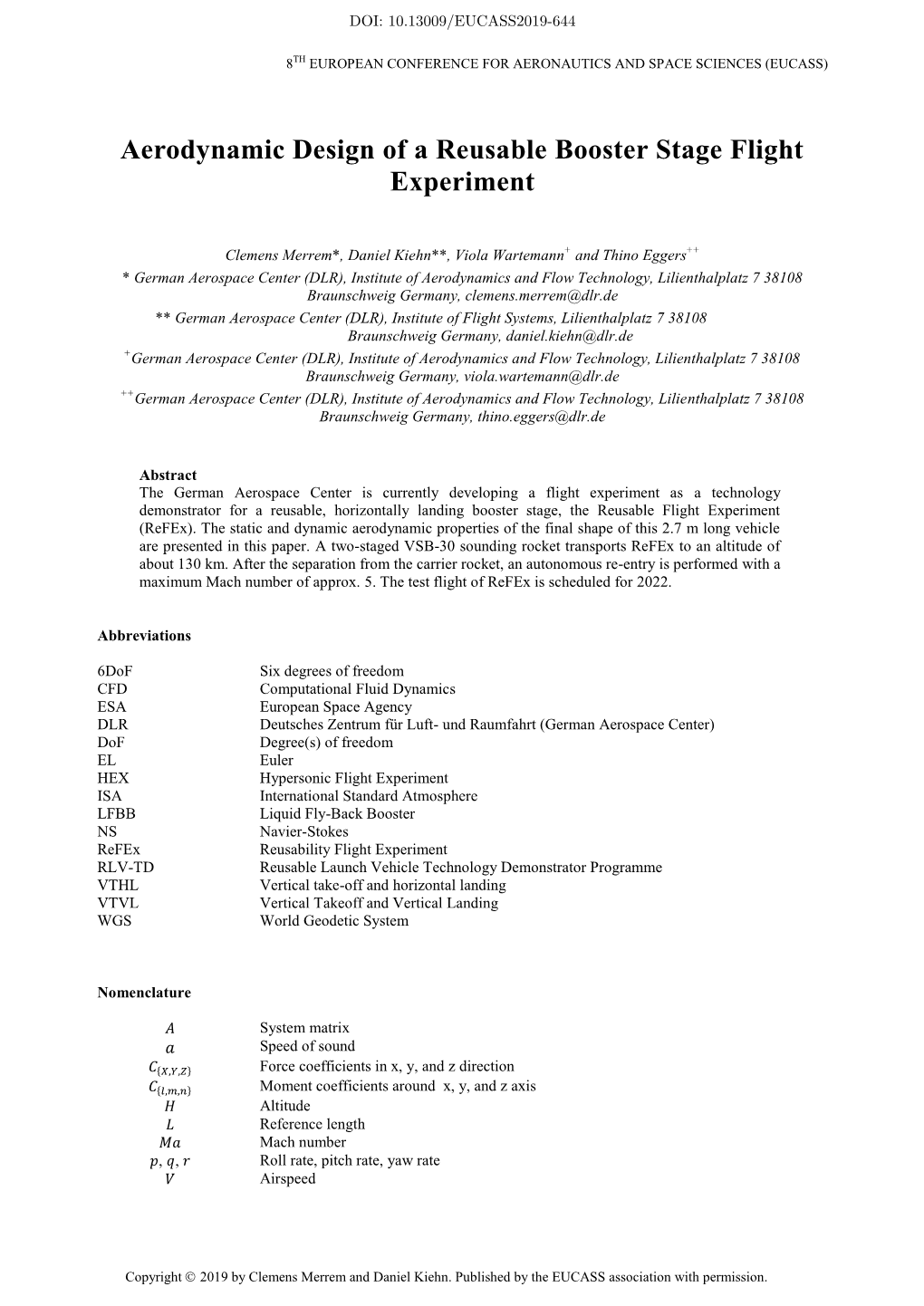
Load more
Recommended publications
-
Validation of Wind Tunnel Test and Cfd Techniques for Retro-Propulsion (Retpro): Overview on a Project Within the Future Launchers Preparatory Programme (Flpp)
VALIDATION OF WIND TUNNEL TEST AND CFD TECHNIQUES FOR RETRO-PROPULSION (RETPRO): OVERVIEW ON A PROJECT WITHIN THE FUTURE LAUNCHERS PREPARATORY PROGRAMME (FLPP) D. Kirchheck, A. Marwege, J. Klevanski, J. Riehmer, A. Gulhan¨ German Aerospace Center (DLR) Supersonic and Hypersonic Technologies Department Cologne, Germany S. Karl O. Gloth German Aerospace Center (DLR) enGits GmbH Spacecraft Department Todtnau, Germany Gottingen,¨ Germany ABSTRACT and landing (VTVL) spacecraft, assisted by retro-propulsion. Up to now, in Europe, knowledge and expertise in that field, The RETPRO project is a 2-years activity, led by the Ger- though constantly growing, is still limited. Systematic stud- man Aerospace Center (DLR) in the frame of ESA’s Future ies were conducted to compare concepts for possible future Launchers Preparatory Program (FLPP), to close the gap of European launchers [2, 3], and activities on detailed inves- knowledge on aerodynamics and aero-thermodynamics of tigations of system components of VTVL re-usable launch retro-propulsion assisted landings for future concepts in Eu- vehicles (RLV) recently started in the RETALT project [4, 5]. rope. The paper gives an overview on the goals, strategy, and Nevertheless, validated knowledge on the aerodynamic current status of the project, aiming for the validation of inno- and aerothermal characteristics of such vehicles is still lim- vative WTT and CFD tools for retro-propulsion applications. ited to a small amount of experimental and numerical inves- Index Terms— RETPRO, retro-propulsion, launcher tigations mostly on lower altitude VTVL trajectories, e. g. aero-thermodynamics, wind tunnel testing, CFD validation within the CALLISTO project [6, 7, 8]. Other studies were conducted to analyze the aerothermodynamics of a simplified generic Falcon 9 geometry during its re-entry and landing 1. -
Spacex Launch Manifest - a List of Upcoming Missions 25 Spacex Facilities 27 Dragon Overview 29 Falcon 9 Overview 31 45Th Space Wing Fact Sheet
COTS 2 Mission Press Kit SpaceX/NASA Launch and Mission to Space Station CONTENTS 3 Mission Highlights 4 Mission Overview 6 Dragon Recovery Operations 7 Mission Objectives 9 Mission Timeline 11 Dragon Cargo Manifest 13 NASA Slides – Mission Profile, Rendezvous, Maneuvers, Re-Entry and Recovery 15 Overview of the International Space Station 17 Overview of NASA’s COTS Program 19 SpaceX Company Overview 21 SpaceX Leadership – Musk & Shotwell Bios 23 SpaceX Launch Manifest - A list of upcoming missions 25 SpaceX Facilities 27 Dragon Overview 29 Falcon 9 Overview 31 45th Space Wing Fact Sheet HIGH-RESOLUTION PHOTOS AND VIDEO SpaceX will post photos and video throughout the mission. High-Resolution photographs can be downloaded from: http://spacexlaunch.zenfolio.com Broadcast quality video can be downloaded from: https://vimeo.com/spacexlaunch/videos MORE RESOURCES ON THE WEB Mission updates will be posted to: For NASA coverage, visit: www.SpaceX.com http://www.nasa.gov/spacex www.twitter.com/elonmusk http://www.nasa.gov/nasatv www.twitter.com/spacex http://www.nasa.gov/station www.facebook.com/spacex www.youtube.com/spacex 1 WEBCAST INFORMATION The launch will be webcast live, with commentary from SpaceX corporate headquarters in Hawthorne, CA, at www.spacex.com. The webcast will begin approximately 40 minutes before launch. SpaceX hosts will provide information specific to the flight, an overview of the Falcon 9 rocket and Dragon spacecraft, and commentary on the launch and flight sequences. It will end when the Dragon spacecraft separates -
Open-Loop Flight Testing of COBALT GN&C Technologies for Precise Soft Landing
Open-Loop Flight Testing of COBALT GN&C Technologies for Precise Soft Landing John M. Carson III1,3,∗, Farzin Amzajerdian2,y, Carl R. Seubert3,z, Carolina I. Restrepo1,x 1NASA Johnson Space Center (JSC), 2NASA Langley Research Center (LaRC), 3Jet Propulsion Laboratory (JPL), California Institute of Technology, A terrestrial, open-loop (OL) flight test campaign of the NASA COBALT (CoOper- ative Blending of Autonomous Landing Technologies) platform was conducted onboard the Masten Xodiac suborbital rocket testbed, with support through the NASA Advanced Exploration Systems (AES), Game Changing Development (GCD), and Flight Opportuni- ties (FO) Programs. The COBALT platform integrates NASA Guidance, Navigation and Control (GN&C) sensing technologies for autonomous, precise soft landing, including the Navigation Doppler Lidar (NDL) velocity and range sensor and the Lander Vision System (LVS) Terrain Relative Navigation (TRN) system. A specialized navigation filter running onboard COBALT fuzes the NDL and LVS data in real time to produce a precise navi- gation solution that is independent of the Global Positioning System (GPS) and suitable for future, autonomous planetary landing systems. The OL campaign tested COBALT as a passive payload, with COBALT data collection and filter execution, but with the Xo- diac vehicle Guidance and Control (G&C) loops closed on a Masten GPS-based navigation solution. The OL test was performed as a risk reduction activity in preparation for an upcoming 2017 closed-loop (CL) flight campaign in which Xodiac G&C will act on the COBALT navigation solution and the GPS-based navigation will serve only as a backup monitor. I. Introduction Introduction will discuss the NASA need for Precision Landing and Hazard Avoidance (PL&HA) tech- nologies for future, prioritized solar-system destinations (robotic and human missions), as well as provide an overview for the COBALT project and how it fits within the NASA PL&HA technology development roadmap. -
Reusable Launch Vehicle Technology Program{
Acta Astronautica Vol. 41, No. 11, pp. 777±790, 1997 # 1998 Published by Elsevier Science Ltd. All rights reserved Printed in Great Britain PII: S0094-5765(97)00197-5 0094-5765/98 $19.00 + 0.00 REUSABLE LAUNCH VEHICLE TECHNOLOGY PROGRAM{ DELMA C. FREEMAN{ JR. and THEODORE A. TALAY} NASA Langley Research Center, Hampton, Virginia 23681-0001, USA R. EUGENE AUSTIN} NASA Marshall Space Flight Center, Marshall Space Flight Center, Alabama 35812-1000, USA (Received 25 April 1997) AbstractÐIndustry/NASA reusable launch vehicle (RLV) technology program eorts are underway to design, test, and develop technologies and concepts for viable commercial launch systems that also satisfy national needs at acceptable recurring costs. Signi®cant progress has been made in understanding the technical challenges of fully reusable launch systems and the accompanying management and oper- ational approaches for achieving a low-cost program. This paper reviews the current status of the RLV technology program including the DC-XA, X-33 and X-34 ¯ight systems and associated technology programs. It addresses the speci®c technologies being tested that address the technical and operability challenges of reusable launch systems including reusable cryogenic propellant tanks, composite structures, thermal protection systems, improved propul- sion, and subsystem operability enhancements. The recently concluded DC-XA test program demon- strated some of these technologies in ground and ¯ight tests. Contracts were awarded recently for both the X-33 and X-34 ¯ight demonstrator systems. The Orbital Sciences Corporation X-34 ¯ight test ve- hicle will demonstrate an air-launched reusable vehicle capable of ¯ight to speeds of Mach 8. -
World Relieved by Safe Splashdown
COSP' TH2 LI33AH? OF 3 R BOCA BAIOI^ FL*\ 33432 Vol. 15, No. 95 BOCA RATON NEWS Sunday^April 19, 1970 30 Pages 10 Cents Wr? Telegrams pouring in World relieved by safe splashdown By United Press International immediately sent President Nixon boulevards as the spacecraft flashed Hundreds of persons gathered in front downtown Tehran, when the news nations applauded, cheered and raised It was a rare example of world unity "assurance of deep admiration . ." into view on television screens. of the U.S. Embassy to watch a series came. United Nations Secretary General glasses of champagne to toast the born of monumental relief and At the American Embassy in Lon- of placards telling of progress in the hi Moscow, the Soviet news agency United States. gratitude at the safe return Friday of Thant was among the first to send don, callers jammed the switchboard, spacecraft's return. Tass praised the "courage and cool U.S. Apollo 13 astronauts James Nixon his congratulations. congratulating the United States on the In Beirut, roars of approval erupted heads" of the Americans. Moscow Sirens of the Buenos Aires Lovell, Fred Haise and Jack Swigert. "The entire world is thankful and all safe return of the astronauts. from Arab cafes, jammed with people radio cut into its regular domestic newspapers La Prensa, Clarin and La Vatican aides said the Pope had men will long marvel at the un- "Most of the people were so who heard the landing on transistor newscast to report on Apollo 13's Nation blared at the moment the seldom looked so happy. -
On Orbital Debris JEFF FOUST, COLLEGE PARK, Md
NOVEMBER 24, 2014 SPOTLIGHT Clyde Space See page 12 www.spacenews.com VOLUME 25 ISSUE 46 $4.95 ($7.50 Non-U.S.) PROFILE/22> YVONNE PENDLETON DIRECTOR, SOLAR SYSTEM EXPLORATION RESEARCH VIRTUAL INSTITUTE INSIDE THIS ISSUE LAUNCH INDUSTRY Swift Development of Ariane 6 Urged Applauding the end of a French-German impasse over the Ariane 6 rocket, the European Satellite Operators Association said the vehicle needs to be in service as quickly as possible. See story, page 8 ATK Hints at Antares Engine Selection Alliant Techsystems Chief Executive Mark DeYoung said there are no near-term liquid- propulsion alternatives to Russian engines for U.S. rockets. See story, page 6 ESA PHOTO Virginia May Seek Federal Funds for Wallops > “We have found a compromise that is OK for both countries, for the other participating states and also for industry,” Brigitte Zypries (above), Germany’s Virginia’s two U.S. senators said they may seek federal funds to cover $20 million in repairs to the space minister, said of an agreement under which Germany and France will back the Ariane 6 rocket and scrap the Ariane 5 Midlife Evolution. Wallops Island launch pad damaged when Orbital Sciences’ Antares exploded. See story, page 6 MILITARY SPACE Protected Tactical Waveform Taking Shape German-French Compromise The U.S. Air Force is expected to demonstrate its protected tactical waveform in new modems and reworked terminals as early as 2018. See story, page 11 U.S. To Grant Indirect Access to Space Fence Paves Direct Path to Ariane 6 The Pentagon’s international space surveillance partners will have indirect access to data from the Air Force’s next-generation Space Fence tracking system. -
A Review of Current Research in Subscale Flight Testing and Analysis of Its Main Practical Challenges
aerospace Article A Review of Current Research in Subscale Flight Testing and Analysis of Its Main Practical Challenges Alejandro Sobron * , David Lundström and Petter Krus Department of Management and Engineering, Division of Fluid and Mechatronic Systems, Linköping University, SE-58183 Linköping, Sweden; [email protected] (D.L.); [email protected] (P.K.) * Correspondence: [email protected]; Tel.: +46-1328-1893 Abstract: Testing of untethered subscale models, often referred to as subscale flight testing, has traditionally had a relatively minor, yet relevant use in aeronautical research and development. As recent advances in electronics, rapid prototyping and unmanned-vehicle technologies expand its capabilities and lower its cost, this experimental method is seeing growing interest across academia and the industry. However, subscale models cannot meet all similarity conditions required for simulating full-scale flight. This leads to a variety of approaches to scaling and to other alternative applications. Through a literature review and analysis of different scaling strategies, this study presents an overall picture of how subscale flight testing has been used in recent years and synthesises its main issues and practical limitations. Results show that, while the estimation of full-scale characteristics is still an interesting application within certain flight conditions, subscale models are progressively taking a broader role as low-cost technology-testing platforms with relaxed similarity constraints. Different approaches to tackle the identified practical challenges, implemented both by the authors and by other organisations, are discussed and evaluated through flight experiments. Citation: Sobron, A.; Lundström, D.; Keywords: subscale flight testing; similarity; scale model; remotely piloted aircraft; demonstration; Krus, P. -
+ Part 10: Test and Evaluation
10. Test and Evaluation 10.1 Approach Architecture Design, Development, Test, and Evaluation (DDT&E) schedule, costs, and risk are highly dependent on the integrated test and evaluation approach for each of the major elements. As a part of the Exploration Systems Architecture Study (ESAS), a top-level test and evaluation plan, including individual flight test objectives, was developed and is summarized in this section. The test and evaluation plan described here is derived from the Apollo Flight Test Program of the 1960s. A more detailed test and evaluation plan will be based on detailed verification requirements and objectives documented in specifications and verification plans. In order to support schedule, cost, and risk assessments for the reference ESAS architecture, an integrated test and evaluation plan was developed to identify the number and type of major test articles (flight and ground) and the timing and objectives of each major flight test, including facilities and equipment required to support those tests. This initial plan is based on the Apollo Program and the ESAS Ground Rules and Assumptions (GR&As)—including the human- rating requirements from NASA Procedural Requirements (NPR) 8705.2A, Human-Rating Requirements for Space Systems. 10. Test and Evaluation 645 10.2 Ground Rules and Assumptions ESAS GR&As establish the initial set of key constraints to testing. Although all ESAS GR&As are considered, the specific ones listed below are particularly significant, as they deal with schedule and testing/qualification assumptions. • The crew launch system shall facilitate crew survival using abort and escape. There will be three all-up tests of the Launch Abort System (LAS). -
Space Shuttle Program
Space Shuttle program The Space Shuttle Columbia seconds after engine ignition, 1981 (NASA). For the first two missions only, the external fuel tank spray-on foam insulation (SOFI) was painted white. Subsequent missions have featured an unpainted tank thus exposing the orange/rust colored foam insulation. This resulted in a weight saving of over 1,000 lb (450 kg), a savings that translated directly to added payload capacity to orbit. NASA's Space Shuttle, officially called Space Transportation System (STS), is the United States government's sole manned launch vehicle currently in service. The winged shuttle orbiter is launched vertically, carrying usually five to seven astronauts and up to about 22,700 kg (50,000 lbs) of payload into low earth orbit. When its mission is complete, it reenters the earth's atmosphere and makes an unpowered gliding horizontal landing, usually on a runway at Kennedy Space Center. The Space Shuttle orbiter was manufactured by North American Rockwell, now part of the Boeing Company. Martin Marietta (now part of Lockheed Martin) designed the external fuel tank and Morton Thiokol (now part of Alliant Techsystems (ATK)) designed the solid rocket boosters. The Shuttle is the first orbital spacecraft designed for partial reusability. It carries large payloads to various orbits, provides crew rotation for the International Space Station (ISS), and performs servicing missions. While the vehicle was designed with the capacity to recover satellites and other payloads from orbit and return them to Earth, this capacity has not been used often; it is, however, an important use of the Space Shuttle in the context of the ISS program, as only very small amounts of experimental material, hardware needing to be repaired, and trash can be returned by Soyuz. -
MT Aerospace (Germany)
https://ntrs.nasa.gov/search.jsp?R=20080014278 2019-08-30T04:19:50+00:00Z European Directions for Hypersonic Thermal Protection Systems and Hot Structures 31st Annual Conference on Composites Materials and Structures Daytona Beach, FL January 22, 2007 David E. Glass NASA Langley Research Center, Hampton, VA 23681 Approved for Public Release, Distribution Unlimited Agenda ♦ Background • Comments on prior ESA workshop • X-38 • Hopper ♦ Flight Vehicle Based Technology Development • IXV (ESA) • EXPERT (ESA) • USV (Italy) • SHEFEX (Germany) • SHyFE (UK) • LEA (France) • Foton (Russia) ♦ Non-Vehicle Specific Technology ♦ Concluding Remarks 2 European TPS and Hot Structures Research and Development ♦TPS and hot structures research and development critical for future space vehicles ♦Developing next generation TPS and hot structures technology (not Space Shuttle derived technology) ♦Long-term funding based on technology needs ♦Wide industry support and commitment to X-38 program ♦Test facilities developed for TPS and hot structures development • Thermal/structural test chamber • Arc-jet tunnels developed in recent years ♦Technology development has broad base • Fabrication • Testing • Large components • Fasteners • Bearings • Oxidation protection • Damage repair • Life cycle Wayne Sawyer comments from previous ESA TPS & Hot Structures Workshop 3 European TPS and Hot Structures Research and Development ♦ Proposing numerous experimental launch vehicles dedicated to or with TPS and hot structures research of prime consideration ♦ Committing significant -
Mission Analysis and Preliminary Re-Entry Trajectory Design of the DLR Reusability Flight Experiment Refex
8TH EUROPEAN CONFERENCE FOR AERONAUTICS AND SPACE SCIENCES (EUCASS) Mission Analysis and Preliminary Re-entry Trajectory Design of the DLR Reusability Flight Experiment ReFEx Sven Stappert*, Peter Rickmers*, Waldemar Bauer*, Martin Sippel* *German Aerospace Center (DLR), Institute of Space Systems, Robert-Hooke-Straße 7, 28359 Bremen [email protected], [email protected], [email protected], [email protected] Abstract Driven by the recently increased demand for investigating reusable launchers, the German Aerospace Center (DLR) is currently developing the Reusability Flight Experiment (ReFEx). The goal is to demonstrate the capability of performing an atmospheric re-entry, representative of a possible future winged reusable stage, and to develop and test key technologies for such reusable stages. The flight demonstrator ReFEx shall perform a controlled and autonomous re-entry from hypersonic velocity of approximately Mach 5 down to subsonic velocity after separation from the VSB-30 booster. The focus of this paper is the re-entry trajectory design for the ReFEx mission. Abbreviations AoA Angle of Attack AVS Avionics BC Ballistic Coefficient BoGC Begin of Guided Control CALLISTO Cooperative Action Leading to Launcher Innovation in Stage Tossback Operation DOF Degree of Freedom ELV Expendable Launch Vehicle EoE End Of Experiment GNC Guidance, Navigation and Control L/D Lift-to-Drag Ratio FPA Flight Path Angle LFBB Liquid Fly-Back Booster MECO Main Engine Cut-Off RCS Reaction Control System RLV Reusable Launch Vehicle TOSCA Trajectory Optimization and Simulation of Conventional and Advanced Spacecraft VTHL Vertical Takeoff, Horizontal Landing VTVL Vertical Takeoff, Vertical Landing 1. Introduction The recent successes of the emerging private space companies SpaceX and Blue Origin in landing, recovering and relaunching reusable first stages have demonstrated the possibility of building reliable and competitive reusable first stages. -
The Annual Compendium of Commercial Space Transportation: 2012
Federal Aviation Administration The Annual Compendium of Commercial Space Transportation: 2012 February 2013 About FAA About the FAA Office of Commercial Space Transportation The Federal Aviation Administration’s Office of Commercial Space Transportation (FAA AST) licenses and regulates U.S. commercial space launch and reentry activity, as well as the operation of non-federal launch and reentry sites, as authorized by Executive Order 12465 and Title 51 United States Code, Subtitle V, Chapter 509 (formerly the Commercial Space Launch Act). FAA AST’s mission is to ensure public health and safety and the safety of property while protecting the national security and foreign policy interests of the United States during commercial launch and reentry operations. In addition, FAA AST is directed to encourage, facilitate, and promote commercial space launches and reentries. Additional information concerning commercial space transportation can be found on FAA AST’s website: http://www.faa.gov/go/ast Cover art: Phil Smith, The Tauri Group (2013) NOTICE Use of trade names or names of manufacturers in this document does not constitute an official endorsement of such products or manufacturers, either expressed or implied, by the Federal Aviation Administration. • i • Federal Aviation Administration’s Office of Commercial Space Transportation Dear Colleague, 2012 was a very active year for the entire commercial space industry. In addition to all of the dramatic space transportation events, including the first-ever commercial mission flown to and from the International Space Station, the year was also a very busy one from the government’s perspective. It is clear that the level and pace of activity is beginning to increase significantly.