Effect of Machining Parameters on Tool Wear and Hole Quality of AISI 316L Stainless Steel in Conventional Drilling
Total Page:16
File Type:pdf, Size:1020Kb
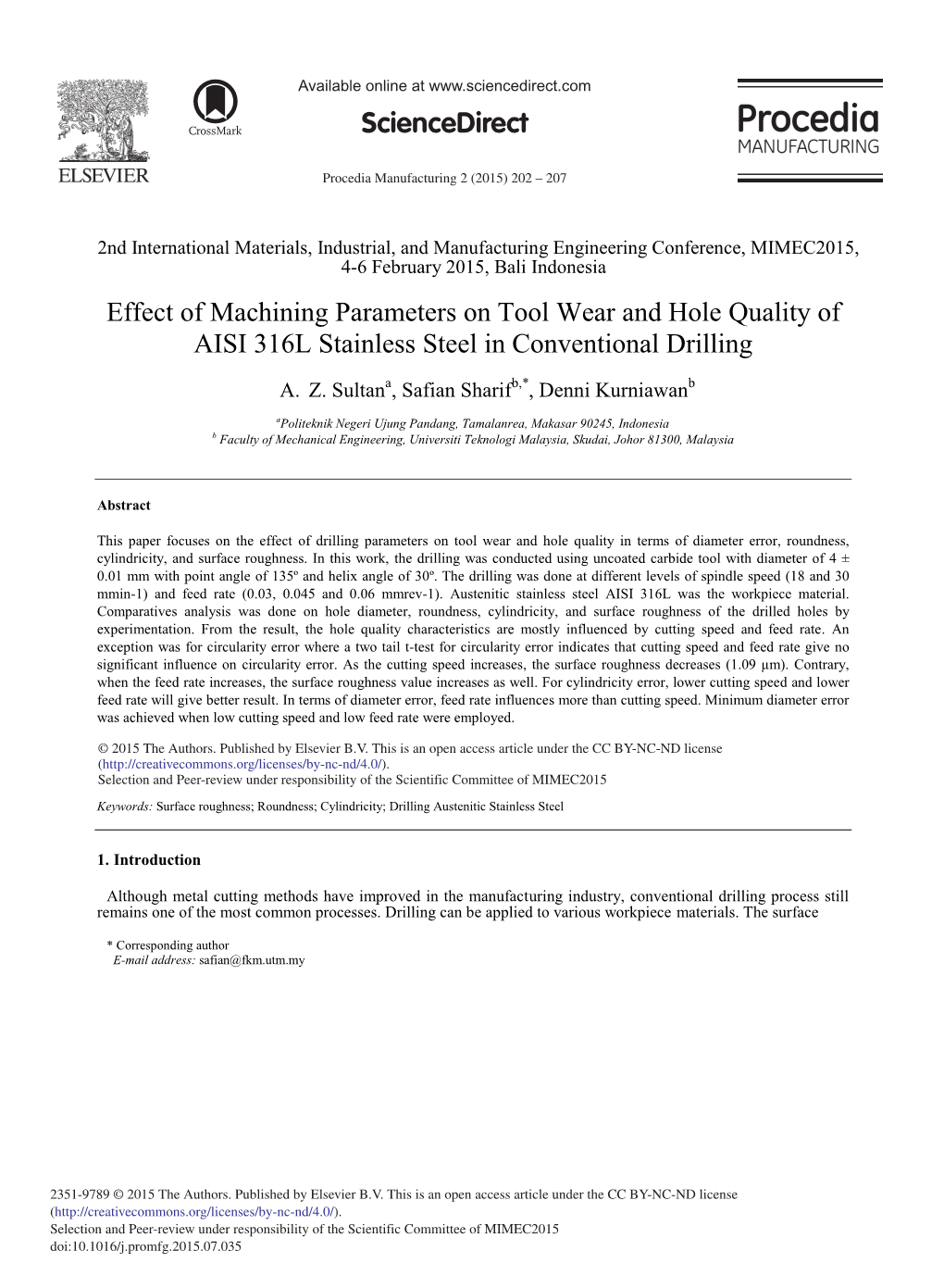
Load more
Recommended publications
-
Prediction and Classification of Tool Wear in Drill and Blast Tunnelling
PREDICTION AND CLASSIFICATION OF TOOL WEAR IN DRILL AND BLAST TUNNELLING Ralf J. Plinninger1, Georg Spaun1 and Kurosch Thuro2 ABSTRACT: After introducing basic ideas on tools, rock fragmentation and wear mechanisms this paper presents and discusses options to classify bit wear types and to predict the rate of button bit wear. Results show that model tests, such as the CERCHAR scratch test may only give an idea of the rocks abrasivity but show no distinct correlation between encountered tool wear rates. Based on conventional rock parameters and taking into account the whole range of scale from grain mineral to rock mass, the presented schemes may help to predict tool wear rates and hint at possible problems in excavation and specific requirements for the tools used RÉSUMÉ: According to Point 6.5.2 of the IAEG bylaws all papers must be preceded by an abstract in both English and French. Please have your English abstract translated and include it here so that non-English speaking readers can determine the scope of your work and its conclusions. According to Point 6.5.2 of the IAEG bylaws all papers must be preceded by an abstract in both English and French. Please have your English abstract translated and include it here so that non-English speaking readers can determine the scope of your work and its conclusions. INTRODUCTION: TOOLS AND WEAR BASICS Tool wear in drill and blast tunnelling Drill & Blast is a commonly used excavation method for the construction of underground openings (e.g. tunnels, caverns) in hardrock conditions worldwide. The working cycle itself consists of the main steps: 1) drilling of blastholes 2) charging 3) blasting 4) ventilation and muck-out 5) rock supporting and surveying (Figure 1). -
Characterization of Tool Wear in Friction Drilling
Jurnal Tribologi 17 (2018) 93-103 Characterization of tool wear in friction drilling Mohd Zurrayen Abdul Mutalib *, Mohd Idris Shah Ismail, Nawal Aswan Abdul Jalil, Azizan As’arry Department of Mechanical and Manufacturing, Faculty of Engineering, Universiti Putra Malaysia, 43400 UPM Serdang, Selangor, MALAYSIA. *Corresponding author: [email protected] KEYWORD ABSTRACT Friction drilling is a non-traditional hole-making process, where the rotating conical tool between the thin workpiece produces a heat due to penetration to soften the workpiece and form a hole. It creates a bushing without generates the chip. Tool wear in friction drilling is crucial because it affects the tolerances that are achievable. In this study, the tool wear characteristics of friction drilling on low carbon steel were experimentally investigated using tungsten carbide tool. Tool wear characteristics were quantified by measuring the changes Friction drilling in tool shape and weight reduction. The energy dispersive Tool wear spectrometry was utilized to analyze the element Chipless hole-making containing on the tool surface, and the observation of wear Tungsten carbide was made using optical microscope and scanning electron microscope. The results indicated that the conical tungsten carbide tool is durable and can be used up to 1000 holes. The changes of tool shape and weight reduction were concentrated at the tool center and conical regions. It confirmed that the abrasive wear revealed at the same regions with circular grooves. The adhesive wear was observed at the tool center and conical regions, and oxidation wear was identified with a dark burned appearance at the tool surface. 1.0 INTRODUCTION Friction drilling is a new progressive hole-making process that utilize the heat where is generated from frictional rotating conical tool and workpiece in initial penetration to soften thin- walled workpiece. -
Failure of Cutting Tools and Tool Wear
Failure of Cutting Tools and Tool Wear Fracture failure Cutting force becomes excessive, leading to brittle fracture Temperature failure Cutting temperature is too high for the tool material Gradual wear Gradual wearing of the cutting tool Preferred Mode of Tool Failure: Gradual Wear Fracture and temperature failures are premature failures Gradual wear is preferred because it leads to the longest possible use of the tool Gradual wear occurs at two locations on a tool: Crater wear – occurs on top rake face Flank wear – occurs on flank (side of tool) Figure - Diagram of worn cutting tool, showing the principal locations and types of wear that occur Figure - (a) Crater wear, and (b) flank wear on a cemented carbide tool, as seen through a toolmaker's microscope (Source: Manufacturing Technology Laboratory, Lehigh University, photo by J. C. Keefe) Figure - Tool wear as a function of cutting time Flank wear (FW) is used here as the measure of tool wear Crater wear follows a similar growth curve Figure - Effect of cutting speed on tool flank wear (FW) for three cutting speeds, using a tool life criterion of 0.50 mm flank wear Taylor Tool Life Equation This relationship is credited to F. W. Taylor (~1900) vT n = C where v = cutting speed; T = tool life; and n and C are parameters that depend on feed, depth of cut, work material, tooling material, and the tool life criterion used • n is the slope of the plot • C is the intercept on the speed axis Typical Values of n and C in Taylor Tool Life Equation Tool material n C (m/min) C (ft/min) High speed steel: Non -steel work 0.125 120 350 Steel work 0.125 70 200 Cemented carbide Non-steel work 0.25 900 2700 Steel work 0.25 500 1500 Ceramic Steel work 0.6 3000 10,000 Tool Life Criteria in Production 1. -
Tool-Wear Analysis Using Image Processing of the Tool Flank
S S symmetry Article Tool-Wear Analysis Using Image Processing of the Tool Flank Ovidiu Gheorghe Moldovan 1,†,‡, Simona Dzitac 2,‡, Ioan Moga 1,‡, Tiberiu Vesselenyi 1,‡ and Ioan Dzitac 3,4,*,‡ 1 Department of Mechatronics, University of Oradea, 410087 Oradea, Romania; [email protected] (O.G.M.); [email protected] (I.M.); [email protected] (T.V.) 2 Department of Energy Engineering, University of Oradea, 410087 Oradea, Romania; [email protected] 3 Department of Mathematics—Computer Science, Aurel Vlaicu University of Arad, 310025 Arad, Romania 4 Department of Social Sciences, Agora University, 410526 Oradea, Romania * Correspondence: [email protected]; Tel.: +40-359-101-032 † Current address: Department of Mathematics—Computer Science, Aurel Vlaicu University of Arad, 310025 Arad, Romania. ‡ These authors contributed equally to this work. Received: 5 November 2017; Accepted: 28 November 2017; Published: 30 November 2017 Abstract: Flexibility of manufacturing systems is an essential factor in maintaining the competitiveness of industrial production. Flexibility can be defined in several ways and according to several factors, but in order to obtain adequate results in implementing a flexible manufacturing system able to compete on the market, a high level of autonomy (free of human intervention) of the manufacturing system must be achieved. There are many factors that can disturb the production process and reduce the autonomy of the system, because of the need of human intervention to overcome these disturbances. One of these factors is tool wear. The aim of this paper is to present an experimental study on the possibility to determine the state of tool wear in a flexible manufacturing cell environment, using image acquisition and processing methods. -
Detection of Tool Wear in Drilling Process Using Vibration Signal Analysis
International Journal of Mechanical And Production Engineering, ISSN: 2320-2092, Volume- 5, Issue-2, Feb.-2017 http://iraj.in DETECTION OF TOOL WEAR IN DRILLING PROCESS USING VIBRATION SIGNAL ANALYSIS 1M. AMARNATH, 2P. RAMAKRISHNA, 3H. CHALLADURAI Tribology and Machine Dynamics Laboratory, Department of Mechanical Engineering, Indian Institute of Information Technology Design and Manufacturing Jabalpur, Jabalpur 482001, India Abstract- Drilling is a machining process where a multi-point tool is used to produce desired holes by removing unwanted material. In this process, the contact between the cutting tool and the work piece generates forces which in turn create torques on the spindle and drive motors. Excessive forces and torques can cause tool failure, spindle stall, undesired structural deflections etc. The vibration levels, cutting forces, torques and power directly affect the other process parameters viz. machinating accuracy, tool wear and chip morphology.Therefore, these parameters are often monitored and regulated due to which productivity is maximized. This paper addresses the results of experimental investigations carried out to monitor drill wear and its corresponding effects on parameters such as vibrations levels, hole accuracy, chip morphology etc. during drilling of AISI 1040 steel. Results highlight the importance of vibration signal analysis techniques to assess tool wear severity. I. INTRODUCTION (PVD) method. Results highlighted the advantages of TiN coating in enhancement of hardness, surface Metal cutting processes are widely used in finish and compressive strength on the surface of the manufacturing industry which includes operations specimen. Wardany et al. (1995) carried out such as turning, milling, drilling and grinding. The experiments to investigate the wear and failure of the trend towards automation in machining has been drill using vibration signature analysis. -
Tool Wear and Surface Evaluation in Drilling Fly Ash Geopolymer Using HSS, HSS-Co, and HSS-Tin Cutting Tools
materials Article Tool Wear and Surface Evaluation in Drilling Fly Ash Geopolymer Using HSS, HSS-Co, and HSS-TiN Cutting Tools Mohd Fathullah Ghazali 1,2,* , Mohd Mustafa Al Bakri Abdullah 2,3,*, Shayfull Zamree Abd Rahim 1,2, Joanna Gondro 4 , Paweł Pietrusiewicz 4 , Sebastian Garus 5 , Tomasz Stachowiak 5, Andrei Victor Sandu 2,6,7 , Muhammad Faheem Mohd Tahir 2,3, Mehmet Erdi Korkmaz 8 and Mohamed Syazwan Osman 9 1 Faculty of Mechanical Engineering Technology, Universiti Malaysia Perlis, Perlis 01000, Malaysia; [email protected] 2 Center of Excellence Geopolymer and Green Technology (CEGeoGTech), Universiti Malaysia Perlis, Perlis 01000, Malaysia; [email protected] (A.V.S.); [email protected] (M.F.M.T.) 3 Faculty of Chemical Engineering Technology, Universiti Malaysia Perlis, Perlis 01000, Malaysia 4 Department of Physics, Cz˛estochowaUniversity of Technology, 42-200 Cz˛estochowa,Poland; [email protected] (J.G.); [email protected] (P.P.) 5 Faculty of Mechanical Engineering and Computer Science, Cz˛estochowaUniversity of Technology, 42-200 Cz˛estochowa,Poland; [email protected] (S.G.); [email protected] (T.S.) 6 Faculty of Material Science and Engineering, Gheorghe Asachi Technical University of Iasi, 41 D. Mangeron St., 700050 Iasi, Romania 7 National Institute for Research and Development for Environmental Protection INCDPM, 294 Splaiul Inde-pendentei, 060031 Bucharest, Romania 8 Citation: Ghazali, M.F.; Abdullah, Machine Engineering Department, Faculty of Engineering, Karabuk University, 78050 Karabuk, Turkey; M.M.A.B.; Abd Rahim, S.Z.; Gondro, [email protected] 9 Faculty of Chemical Engineering, Universiti Teknologi MARA, Cawangan Pulau Pinang, J.; Pietrusiewicz, P.; Garus, S.; 13500 Permatang Pauh, Malaysia; [email protected] Stachowiak, T.; Sandu, A.V.; Mohd * Correspondence: [email protected] (M.F.G.); [email protected] (M.M.A.B.A.) Tahir, M.F.; Korkmaz, M.E.; et al. -
1 Tool Wear and Surface Quality of Mmcs Due to Machining- a Review F
Tool wear and surface quality of MMCs due to machining- a review F. Hakami1, A. Pramanik1*, A. K. Basak2 1 Department of Mechanical Engineering, Curtin University, Bentley, Australia 2 Adelaide Microscopy, University of Adelaide, Adelaide, SA, Australia *Corresponding author, Email: [email protected], Phone + 61 8 9266 7981 Abstract Higher tool wear and inferior surface quality of the specimens during machining restrict MMCs’ application in many areas in spite of their excellent properties. The researches in this field are not well organised and knowledges are not properly linked to give a complete overview. Thus, it is hard to implement it in practical fields. To address this issue, this paper reviews tool wear and surface generation, and latest developments in machining of MMCs. This will provide an insight and scientific overview in this filed which will facilitate the implementation of the obtained knowledge in the practical fields. It was noted that the hard reinforcements initially start abrasive wear on the cutting tool. The abrasion exposes new cutting tool surface, which initiates adhesion of matrix material to the cutting tool and thus causes adhesion wear. Build-up-edges also generates at lower cutting speeds. Though different types of coating improve tool life, only diamond cutting tools show considerably longer tool life. The application of the coolants improves tool life reasonably at higher cutting speed. Pits, voids, micro-cracks, and fractured reinforcements are common in the machined MMC surface. These are due to ploughing, indentation, and dislodgement of particles from the matrix due to tool-particle interactions. Further, compressive residual stress is caused by the particles’ indentation in the machined surface. -
Sensitivity Analysis of Tool Wear in Drilling of Titanium Aluminides
metals Article Sensitivity Analysis of Tool Wear in Drilling of Titanium Aluminides Aitor Beranoagirre 1,*, Gorka Urbikain 1,* , Raúl Marticorena 2, Andrés Bustillo 2 and Luis Norberto López de Lacalle 3 1 Department of Mechanical Engineering, University of the Basque Country (UPV/EHU), Plaza Europa 1, 20018 San Sebastián, Spain 2 Department of Civil Engineering, Universidad de Burgos, Avda Cantabria s/n, 09006 Burgos, Spain; [email protected] (R.M.); [email protected] (A.B.) 3 CFAA, University of the Basque Country (UPV/EHU), Parque Tecnológico de Zamudio 202, 48170 Bilbao, Spain; [email protected] * Correspondence: [email protected] (A.B.); [email protected] (G.U.); Tel.: +34-943-018-636 (A.B.); +34-943-018-643 (G.U.) Received: 6 February 2019; Accepted: 27 February 2019; Published: 6 March 2019 Abstract: In the aerospace industry, a large number of holes need to be drilled to mechanically connect the components of aircraft engines. The working conditions for such components demand a good response of their mechanical properties at high temperatures. The new gamma TiAl are in the transition between the 2nd and 3rd generation, and several applications are proposed for that sector. Thus, NASA is proposing the use of the alloys in the Revolutionary Turbine Accelerator/Turbine-Based Combined Cycle (RTA/TBCC) Program for the next-generation launch vehicle, with gamma TiAl as a potential compressor and structural material. However, the information and datasets available regarding cutting performance in titanium aluminides are relatively scarce. So, a considerable part of the current research efforts in this field is dedicated to process optimization of cutting parameters and tool geometries. -
A Review on Tool Wear Mechanisms in Milling of Super Alloy
International Journal of Scientific & Engineering Research, Volume 6, Issue 12, December-2015 ISSN 2229-5518 220 A Review on Tool Wear Mechanisms in Milling of Super Alloy Laveena Makaji, Mithilesh Gaikhe, Vivek Mahabale, Naval Gharat Saraswati College of Engineering, Kharghar, Navi Mumbai Abstract: Super alloys have vast range of greater extent and also at high speed cutting force applications in gas turbine engines of aircraft due increases simultaneously. to their ability to withstand all the mechanical Super alloys properties at elevated temperature. Super alloys It is an alloy based on group VII elements are difficult to cut material which involves large (Nickel, cobalt, or iron with high percentage of nickel amount of cutting forces while its machining. added) to a multiplicity of alloying elements are These large cutting forces lead to frequent tool added. The defining feature of a super alloy is that it wear which consumes tool replacement time and demonstrates a combination of relatively high cost. This work deals with the review of various mechanical strengths and surface stability at high tool wear mechanism in cutting of super alloys for temperature [12]. proper selection of tools for particular material. Key words: BUE, Crater wear, Flank wear, notch Nickel-Iron-base alloys wear. This type of super alloys possess high toughness and ductility and are used in applications INTRODUCTION IJSERwhere this properties are required e.g. turbine discs Super alloys have vast range of applications and forged rotors. Their cost is low due to substantial like Gas turbine Engine, Reciprocating engines etc. amount of iron added. There are three groups of Inconel718 is a Nickel based super alloy which is nickel iron based super alloy. -
TOOL WEAR ANALYSIS in VARIOUS MACHINING PROCESSES and STUDY of MINIMUM QUANTITY LUBRICATION (MQL) by Kyung Hee Park a DISSERTAT
TOOL WEAR ANALYSIS IN VARIOUS MACHINING PROCESSES AND STUDY OF MINIMUM QUANTITY LUBRICATION (MQL) By Kyung Hee Park A DISSERTATION Submitted to Michigan State University in partial fulfillment of the requirements for the degree of DOCTOR OF PHILOSOPHY Mechanical Engineering 2010 ABSTRACT TOOL WEAR ANALYSIS IN VARIOUS MACHINING PROCESSES AND STUDY OF MINIMUM QUANTITY LUBRICATION (MQL) By Kyung Hee Park The tool wear analysis on the multilayer coated carbide inserts in turning and milling of AISI 1045 steels was performed using advanced microscope and image processing techniques. In turning process, the flank wear evolution, surface roughness and groove sizes on the coating layers were analyzed to understand the flank wear mechanism(s) involved. The dominant wear phenomenon was abrasion and, after carbide was exposed, adhesion took over. For flank wear prediction, 2-body abrasion model was used along the interface conditions from finite element (FE) model, which provides the temperature on the cutting tool. In a face milling study, multilayer cutting tools, double (TiN/TiAlN) and triple (TiN/Al2O3/TiCN) layered coated carbide, processed by physical vapor deposition (PVD) and chemical vapor deposition (CVD) respectively, were evaluated in terms of various cutting conditions. Similar to the turning case, abrasion was found to be the most dominant tool wear mechanism in milling. Edge chipping and micro-fracture were the tool failure modes. Overall, the double layer coating was superior to the triple layer coating under various cutting conditions due to the benefit coming from the coating deposition processes themselves. On the other hand, drilling of carbon fiber reinforced polymer (CFRP)/titanium (Ti) stacks has been performed using carbide and PCD drills. -
TABLE of CONTENTS 974 CUTTING SPEEDS and FEEDS 978 Cutting Tool Materials 982 Cutting Speeds 983 Cutting Conditions 983 Selectin
TABLE OF CONTENTS MACHINING OPERATIONS CUTTING SPEEDS AND FEEDS ESTIMATING SPEEDS AND MACHINING POWER 978 Cutting Tool Materials 982 Cutting Speeds 1044 Planer Cutting Speeds 983 Cutting Conditions 1044 Cutting Speed and Time 983 Selecting Cutting Conditions 1044 Planing Time 983 Tool Troubleshooting 1044 Speeds for Metal-Cutting Saws 985 Cutting Speed Formulas 1044 Turning Unusual Material 987 RPM for Various Cutting Speeds 1046 Estimating Machining Power and Diameter 1046 Power Constants SPEED AND FEED TABLES 1047 Feed Factors 1048 Tool Wear Factors 991 Introduction 1050 Metal Removal Rates 991 Feeds and Speeds Tables 1051 Estimating Drilling Thrust, 995 Speed and Feed Tables for Turning Torque, and Power 1000 Tool Steels 1053 Work Material Factor 1001 Stainless Steels 1053 Chisel Edge Factors 1002 Ferrous Cast Metals 1054 Feed Factors 1004 Turning-Speed Adjustment 1055 Drill Diameter Factors Factors MACHINING ECONOMETRICS 1004 Tool Life Factors 1005 Adjustment Factors for HSS 1056 Tool Wear And Tool Life Tools Relationships 1006 Copper Alloys 1056 Equivalent Chip Thickness (ECT) 1007 Titanium and Titanium Alloys 1057 Tool-life Relationships 1008 Superalloys 1061 The G- and H-curves 1009 Speed and Feed Tables for Milling 1062 Tool-life Envelope 1012 Slit Milling 1065 Forces and Tool-life 1013 Aluminium Alloys 1067 Surface Finish and Tool-life 1014 Plain Carbon and Alloy Steels 1069 Shape of Tool-life Relationships 1018 Tool Steels 1070 Minimum Cost 1019 Stainless Steels 1071 Production Rate 1021 Ferrous Cast Metals 1071 The Cost Function -
A Review of Tool Wear Estimation Using Theoretical Analysis and Numerical Simulation Technologies
Int. Journal of Refractory Metals and Hard Materials 35 (2012) 143–151 Contents lists available at SciVerse ScienceDirect Int. Journal of Refractory Metals and Hard Materials journal homepage: www.elsevier.com/locate/IJRMHM A review of tool wear estimation using theoretical analysis and numerical simulation technologies Bin Li ⁎ Department of Mechanical Engineering, Luoyang Institute of Science and Technology, Wangcheng Avenue 90, Luoyang 471023, Henan Province, PR China article info abstract Article history: A thorough understanding of the material removal process in cutting is essential in selecting the tool material Received 21 February 2012 and in design, and also in assuring consistent dimensional accuracy and surface integrity of the finished prod- Accepted 7 May 2012 uct. Tool wear in cutting process is produced by the contact and relative sliding between the cutting tool and the workpiece, and between the cutting tool and the chip under the extreme conditions of cutting area. This Keywords: paper presents the information on development of study on theoretical analysis and numerical simulation of Simulation tool wear in all over the world. Hidden Markov models (HMMs) were introduced to estimate tool wear in Tool wear fl Metal cutting cutting, which are strongly in uenced by the cutting temperature, contact stresses, and relative strains at the interface. Finite element method (FEM) is a powerful tool to predict cutting process variables, which are difficult to obtain with experimental methods. The objective of this work focuses on the new develop- ment in predicting the tool wear evolution and tool life in orthogonal cutting with FEM simulations. © 2012 Elsevier Ltd. All rights reserved.