Space Shuttle Orbiter Approach and Landing Test
Total Page:16
File Type:pdf, Size:1020Kb
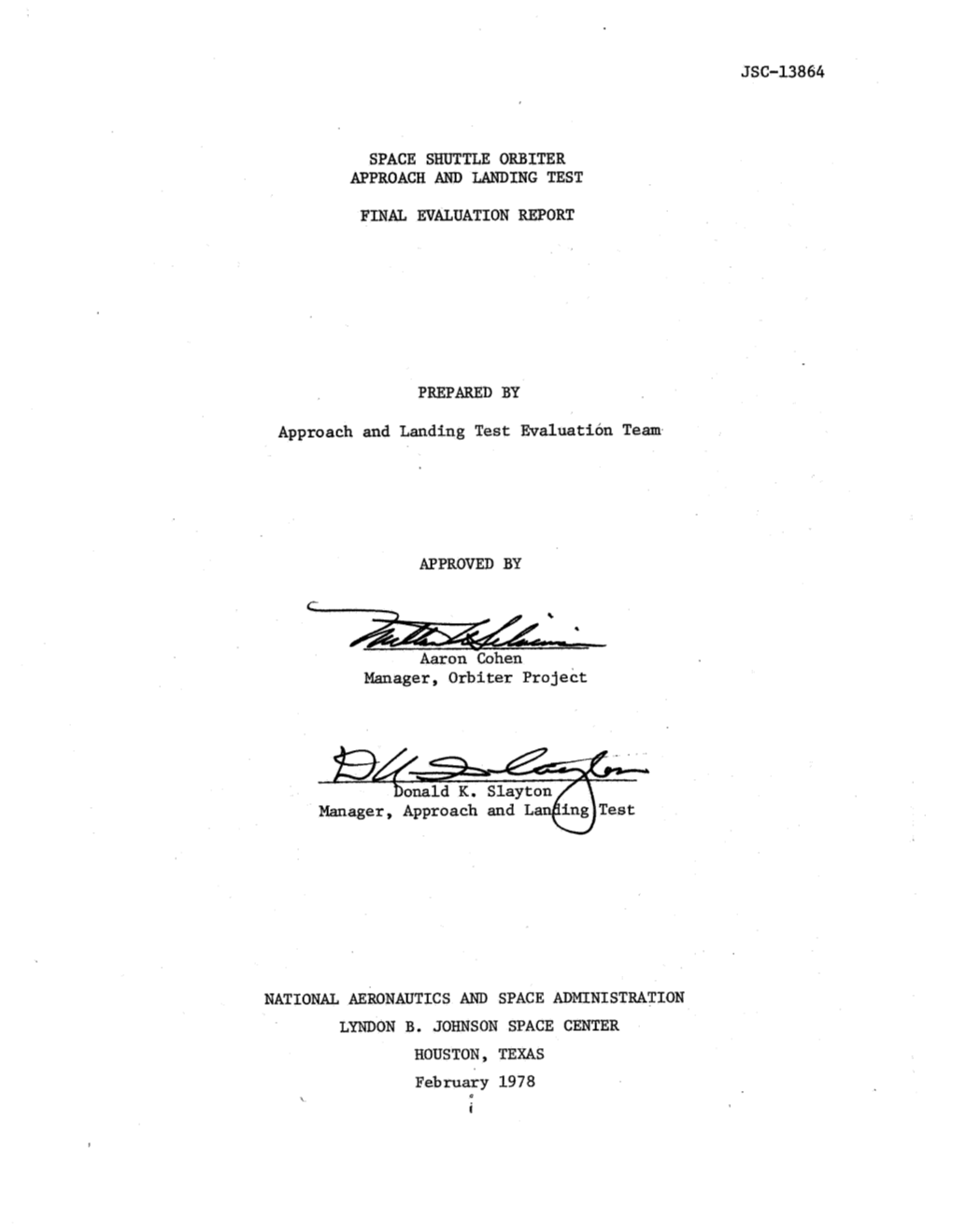
Load more
Recommended publications
-
Validation of Wind Tunnel Test and Cfd Techniques for Retro-Propulsion (Retpro): Overview on a Project Within the Future Launchers Preparatory Programme (Flpp)
VALIDATION OF WIND TUNNEL TEST AND CFD TECHNIQUES FOR RETRO-PROPULSION (RETPRO): OVERVIEW ON A PROJECT WITHIN THE FUTURE LAUNCHERS PREPARATORY PROGRAMME (FLPP) D. Kirchheck, A. Marwege, J. Klevanski, J. Riehmer, A. Gulhan¨ German Aerospace Center (DLR) Supersonic and Hypersonic Technologies Department Cologne, Germany S. Karl O. Gloth German Aerospace Center (DLR) enGits GmbH Spacecraft Department Todtnau, Germany Gottingen,¨ Germany ABSTRACT and landing (VTVL) spacecraft, assisted by retro-propulsion. Up to now, in Europe, knowledge and expertise in that field, The RETPRO project is a 2-years activity, led by the Ger- though constantly growing, is still limited. Systematic stud- man Aerospace Center (DLR) in the frame of ESA’s Future ies were conducted to compare concepts for possible future Launchers Preparatory Program (FLPP), to close the gap of European launchers [2, 3], and activities on detailed inves- knowledge on aerodynamics and aero-thermodynamics of tigations of system components of VTVL re-usable launch retro-propulsion assisted landings for future concepts in Eu- vehicles (RLV) recently started in the RETALT project [4, 5]. rope. The paper gives an overview on the goals, strategy, and Nevertheless, validated knowledge on the aerodynamic current status of the project, aiming for the validation of inno- and aerothermal characteristics of such vehicles is still lim- vative WTT and CFD tools for retro-propulsion applications. ited to a small amount of experimental and numerical inves- Index Terms— RETPRO, retro-propulsion, launcher tigations mostly on lower altitude VTVL trajectories, e. g. aero-thermodynamics, wind tunnel testing, CFD validation within the CALLISTO project [6, 7, 8]. Other studies were conducted to analyze the aerothermodynamics of a simplified generic Falcon 9 geometry during its re-entry and landing 1. -
Reusable Launch Vehicle Technology Program{
Acta Astronautica Vol. 41, No. 11, pp. 777±790, 1997 # 1998 Published by Elsevier Science Ltd. All rights reserved Printed in Great Britain PII: S0094-5765(97)00197-5 0094-5765/98 $19.00 + 0.00 REUSABLE LAUNCH VEHICLE TECHNOLOGY PROGRAM{ DELMA C. FREEMAN{ JR. and THEODORE A. TALAY} NASA Langley Research Center, Hampton, Virginia 23681-0001, USA R. EUGENE AUSTIN} NASA Marshall Space Flight Center, Marshall Space Flight Center, Alabama 35812-1000, USA (Received 25 April 1997) AbstractÐIndustry/NASA reusable launch vehicle (RLV) technology program eorts are underway to design, test, and develop technologies and concepts for viable commercial launch systems that also satisfy national needs at acceptable recurring costs. Signi®cant progress has been made in understanding the technical challenges of fully reusable launch systems and the accompanying management and oper- ational approaches for achieving a low-cost program. This paper reviews the current status of the RLV technology program including the DC-XA, X-33 and X-34 ¯ight systems and associated technology programs. It addresses the speci®c technologies being tested that address the technical and operability challenges of reusable launch systems including reusable cryogenic propellant tanks, composite structures, thermal protection systems, improved propul- sion, and subsystem operability enhancements. The recently concluded DC-XA test program demon- strated some of these technologies in ground and ¯ight tests. Contracts were awarded recently for both the X-33 and X-34 ¯ight demonstrator systems. The Orbital Sciences Corporation X-34 ¯ight test ve- hicle will demonstrate an air-launched reusable vehicle capable of ¯ight to speeds of Mach 8. -
Space Reporter's Handbook Mission Supplement
CBS News Space Reporter's Handbook - Mission Supplement Page 1 The CBS News Space Reporter's Handbook Mission Supplement Shuttle Mission STS-125: Hubble Space Telescope Servicing Mission 4 Written and Produced By William G. Harwood CBS News Space Analyst [email protected] CBS News 5/10/09 Page 2 CBS News Space Reporter's Handbook - Mission Supplement Revision History Editor's Note Mission-specific sections of the Space Reporter's Handbook are posted as flight data becomes available. Readers should check the CBS News "Space Place" web site in the weeks before a launch to download the latest edition: http://www.cbsnews.com/network/news/space/current.html DATE RELEASE NOTES 08/03/08 Initial STS-125 release 04/11/09 Updating to reflect may 12 launch; revised flight plan 04/15/09 Adding EVA breakdown; walkthrough 04/23/09 Updating for 5/11 launch target date 04/30/09 Adding STS-400 details from FRR briefing 05/04/09 Adding trajectory data; abort boundaries; STS-400 launch windows Introduction This document is an outgrowth of my original UPI Space Reporter's Handbook, prepared prior to STS-26 for United Press International and updated for several flights thereafter due to popular demand. The current version is prepared for CBS News. As with the original, the goal here is to provide useful information on U.S. and Russian space flights so reporters and producers will not be forced to rely on government or industry public affairs officers at times when it might be difficult to get timely responses. All of these data are available elsewhere, of course, but not necessarily in one place. -
A Review of Current Research in Subscale Flight Testing and Analysis of Its Main Practical Challenges
aerospace Article A Review of Current Research in Subscale Flight Testing and Analysis of Its Main Practical Challenges Alejandro Sobron * , David Lundström and Petter Krus Department of Management and Engineering, Division of Fluid and Mechatronic Systems, Linköping University, SE-58183 Linköping, Sweden; [email protected] (D.L.); [email protected] (P.K.) * Correspondence: [email protected]; Tel.: +46-1328-1893 Abstract: Testing of untethered subscale models, often referred to as subscale flight testing, has traditionally had a relatively minor, yet relevant use in aeronautical research and development. As recent advances in electronics, rapid prototyping and unmanned-vehicle technologies expand its capabilities and lower its cost, this experimental method is seeing growing interest across academia and the industry. However, subscale models cannot meet all similarity conditions required for simulating full-scale flight. This leads to a variety of approaches to scaling and to other alternative applications. Through a literature review and analysis of different scaling strategies, this study presents an overall picture of how subscale flight testing has been used in recent years and synthesises its main issues and practical limitations. Results show that, while the estimation of full-scale characteristics is still an interesting application within certain flight conditions, subscale models are progressively taking a broader role as low-cost technology-testing platforms with relaxed similarity constraints. Different approaches to tackle the identified practical challenges, implemented both by the authors and by other organisations, are discussed and evaluated through flight experiments. Citation: Sobron, A.; Lundström, D.; Keywords: subscale flight testing; similarity; scale model; remotely piloted aircraft; demonstration; Krus, P. -
+ Part 10: Test and Evaluation
10. Test and Evaluation 10.1 Approach Architecture Design, Development, Test, and Evaluation (DDT&E) schedule, costs, and risk are highly dependent on the integrated test and evaluation approach for each of the major elements. As a part of the Exploration Systems Architecture Study (ESAS), a top-level test and evaluation plan, including individual flight test objectives, was developed and is summarized in this section. The test and evaluation plan described here is derived from the Apollo Flight Test Program of the 1960s. A more detailed test and evaluation plan will be based on detailed verification requirements and objectives documented in specifications and verification plans. In order to support schedule, cost, and risk assessments for the reference ESAS architecture, an integrated test and evaluation plan was developed to identify the number and type of major test articles (flight and ground) and the timing and objectives of each major flight test, including facilities and equipment required to support those tests. This initial plan is based on the Apollo Program and the ESAS Ground Rules and Assumptions (GR&As)—including the human- rating requirements from NASA Procedural Requirements (NPR) 8705.2A, Human-Rating Requirements for Space Systems. 10. Test and Evaluation 645 10.2 Ground Rules and Assumptions ESAS GR&As establish the initial set of key constraints to testing. Although all ESAS GR&As are considered, the specific ones listed below are particularly significant, as they deal with schedule and testing/qualification assumptions. • The crew launch system shall facilitate crew survival using abort and escape. There will be three all-up tests of the Launch Abort System (LAS). -
Space Shuttle Program
Space Shuttle program The Space Shuttle Columbia seconds after engine ignition, 1981 (NASA). For the first two missions only, the external fuel tank spray-on foam insulation (SOFI) was painted white. Subsequent missions have featured an unpainted tank thus exposing the orange/rust colored foam insulation. This resulted in a weight saving of over 1,000 lb (450 kg), a savings that translated directly to added payload capacity to orbit. NASA's Space Shuttle, officially called Space Transportation System (STS), is the United States government's sole manned launch vehicle currently in service. The winged shuttle orbiter is launched vertically, carrying usually five to seven astronauts and up to about 22,700 kg (50,000 lbs) of payload into low earth orbit. When its mission is complete, it reenters the earth's atmosphere and makes an unpowered gliding horizontal landing, usually on a runway at Kennedy Space Center. The Space Shuttle orbiter was manufactured by North American Rockwell, now part of the Boeing Company. Martin Marietta (now part of Lockheed Martin) designed the external fuel tank and Morton Thiokol (now part of Alliant Techsystems (ATK)) designed the solid rocket boosters. The Shuttle is the first orbital spacecraft designed for partial reusability. It carries large payloads to various orbits, provides crew rotation for the International Space Station (ISS), and performs servicing missions. While the vehicle was designed with the capacity to recover satellites and other payloads from orbit and return them to Earth, this capacity has not been used often; it is, however, an important use of the Space Shuttle in the context of the ISS program, as only very small amounts of experimental material, hardware needing to be repaired, and trash can be returned by Soyuz. -
HOUSTON BRINGS HOME a SHUTTLE for EVERYONE to SHARE by Alicia M
HOUSTON BRINGS HOME A SHUTTLE FOR EVERYONE TO SHARE By Alicia M. Nichols All photos courtesy of Alan Montgomery and Woodallen Photography, Houston, Texas. 22 HOUSTON HISTORY Vol.12 • No.2 HOUSTON BRINGS HOME A SHUTTLE FOR EVERYONE TO SHARE By Alicia M. Nichols The new Space Center Houston exhibit will feature the mock-up shuttle Independence sitting atop the Boeing 747, in the “ ferry position.” Both exhibit director Paul Spana and educational director Dr. Melanie Johnson agree that the Houston exhibit offers a unique opportunity. Visitors here will have a far more tangible, hands-on educational experience than those who visit sites housing the formerly active shuttles. They can explore the insides of the 747 and the shuttle itself and see what it would be like to pilot the shuttle, crammed into the pilot’s deck. Interactivity and the higher level of engagement make it far more likely that young visitors will take away something from the experience, perhaps inspiring a future astronaut who will set foot on Mars.1 HOUSTON HISTORY Vol. 12 • No.2 23 hirty-one years after NASA launched the first space envisioned as a practical tool to transport people, goods, Tshuttle into Earth’s orbit, a shuttle carrier aircraft car- science experiments, and equipment between Earth and rying the space shuttle Endeavour flew over Houston. In July what became the International Space Station—a place to of 2011, the shuttle Atlantis, STS-135, marked the 135th and conduct further research and study space. Throughout the final flight of the space shuttle program, known officially 1970s, NASA scientists and engineers continued to develop as the Space Transport System (STS). -
Independence Plaza
FACT SHEET: Independence Plaza Now boarding – the new international landmark Independence Plaza Space Center Houston’s colossal new exhibit The shuttle carrier aircraft Independence Plaza presented by Boeing features This SCA is the largest intact artifact from the the historic NASA 905 shuttle carrier aircraft and shuttle program and played key roles in the the shuttle replica Independence. This landmark orbiter’s development. NASA 905 carried space attraction is the world’s only shuttle replica shuttles 223 times and amassed 11,017 flight mounted on a shuttle carrier aircraft and the only hours over 42 years. It is the first of two SCAs. place where the public can enter both vehicles. Fun facts Length: 231 feet, 4 inches (70.5 meters) Wingspan: 195 feet 8 inches (59.7 meters) The 240-ton SCA and shuttle complex stands Height: 63 feet 5 inches (19.3 meters) on a 15-inch concrete foundation that rests on Empty weight: 318,000 pounds (144,200 kg) a 20-inch layer of compacted sand. Although the main landing gear beam was cut The shuttle replica Independence for transportation to our center, the Independence was remodeled to offer reassembled 747 structure is flight certifiable. unprecedented access to previously restricted NASA called the plane NASA 905 when it was areas and is stocked with a collection of artifacts used as a shuttle carrier aircraft (SCA). to share its historic contributions. Length: 122 feet (37.2 meters) Wingspan: 78 feet (23.7 meters) Height: 57 feet (17.3 meters) Weight: 171,000 pounds (77,500 kilograms) The perfect venue for your event This historic plane and shuttle replica can be the setting for your perfect event. -
Flight Engineer Knowledge Test Guide
AC 63-1 FLIGHT ENGINEER KNOWLEDGE TEST GUIDE U.S. Department of Transportation Federal Aviation Administration 1 FLIGHT ENGINEER KNOWLEDGE TEST GUIDE 1995 U.S. DEPARTMENT OF TRANSPORTATION FEDERAL AVIATION ADMINISTRATION Flight Standards Service 2 PREFACE The Flight Standards Service of the Federal Aviation Administration (FAA) has developed this guide to help applicants meet the knowledge requirements for the computer administered tests for flight engineer turbojet, turboprop, and reciprocating class certification. This guide contains information about the knowledge test eligibility requirements, test descriptions, testing and retesting procedures, and sample test questions with answers. As a convenience to the applicant, the eligibility requirements for the oral and flight tests are included. Appendix 1 provides a list of reference materials and subject matter knowledge codes, and computer testing designees. Changes to the subject matter knowledge code list will be published as a separate advisory circular. The sample questions and answers in this guide are predicated on Federal Aviation Regulations (FAR's) and references that were current at the time of publication. Questions and answers in the computer administered knowledge tests are updated when changes are made to these reference materials. The flight engineer test question bank and subject matter knowledge code list for all airmen certificates and ratings, with changes, may be obtained by computer access from FedWorld at (703) 321-3339. This bulletin board service is provided by the U.S. Department of Commerce, 24 hours a day, 7 days per week. For technical assistance regarding computer requirements for this service, contact the FedWorld help desk at (703) 487-4608 from 7:30 a.m. -
Orbiter Processing Facility
National Aeronautics and Space Administration Space Shuttle: Orbiter Processing From Landing To Launch he work of preparing a space shuttle for the same facilities. Inside is a description of an flight takes place primarily at the Launch orbiter processing flow; in this case, Discovery. Complex 39 Area. TThe process actually begins at the end of each acts Shuttle Landing Facility flight, with a landing at the center or, after landing At the end of its mission, the Space Shuttle f at an alternate site, the return of the orbiter atop a Discovery lands at the Shuttle Landing Facility on shuttle carrier aircraft. Kennedy’s Shuttle Landing one of two runway headings – Runway 15 extends Facility is the primary landing site. from the northwest to the southeast, and Runway There are now three orbiters in the shuttle 33 extends from the southeast to the northwest fleet: Discovery, Atlantis and Endeavour. Chal- – based on wind currents. lenger was destroyed in an accident in January After touchdown and wheelstop, the orbiter 1986. Columbia was lost during approach to land- convoy is deployed to the runway. The convoy ing in February 2003. consists of about 25 specially designed vehicles or Each orbiter is processed independently using units and a team of about 150 trained personnel, NASA some of whom assist the crew in disembarking from the orbiter. the orbiter and a “white room” is mated to the orbiter hatch. The The others quickly begin the processes necessary to “safe” the hatch is opened and a physician performs a brief preliminary orbiter and prepare it for towing to the Orbiter Processing Fa- medical examination of the crew members before they leave the cility. -
Space Shuttle Now Open
EXCLUSIVE MEMBERSHIP NEWSLETTER INSIDER SUMMER 2012 SPACE SHUTTLE PAVILION NOW OPEN Intrepid’s Space Shuttle Pavilion, featuring Enterprise, officially opened on July 19th with an historic ceremony and ribbon cutting. Participants in the ceremony included Major General Charles Bolden, Jr., NASA Administrator, George Fertitta, CEO of NYC & Company and, three of the four Enterprise astronauts, Richard Truly, Joe Engle, and Fred Haise; astronaut Gordon Fullerton was unable to travel and was represented by his wife, Marie. In celebration of the opening, Intrepid presented Space Shuttle Enterprise in her new home. Samsung SpaceFest through Sunday, July 22nd, which included interactive displays and dem- onstrations from NASA, astronaut appearances and cool displays from Samsung Smart TV and Time Warner Cable’s Connect a Million Minds. SpaceFest also included a free concert – Sound Waves on the Intrepid, presented by Samsung, on Friday night and a special free screening of Star Trek (2009) on Saturday night as part of Intrepid’s free Astronaut Charles J. Camarda with a fan. Fred Haise at the opening ceremony. summer movie series on the flight deck. JOIN PROJECT ENTERPRISE AND SUPPORT THE NEW HOME PROJECT OF THE FIRST NASA ORBITER, SPACE SHUTTLE ENTERPRISE Gifts of any amount are greatly appreciated. Donors of $250 or more will have a star represented in the Space Shuttle Pavilion and in Enterprise’s ENTERPRISE future permanent home at the Intrepid Museum. BE A PART OF HISTORY Learn more at www.intrepidmuseum.org MESSAGE from the President Dear Member, This is an exciting time for the Intrepid and for all of New York City. -
20120000791.Pdf
Horizontal Launch: A Versatile Concept for Assured Space Access Report of the NASA-DARPA Horizontal Launch Study Horizontal Launch: A Versatile Concept for Assured Space Access Approved for public release; distribution is unlimited according to the National Aeronautical and Space Administration (STI case 4418) and the Defense Advanced Research Projects Agency (DISTAR case 18287). Library of Congress Cataloging-in-Publication Data Horizontal launch: a versatile concept for assured space access / Paul A. Bartolotta, Elizabeth Buchen, Walter C. Engelund, Lawrence D. Huebner, Paul L. Moses, Mark Schaffer, Randall T. Voland, David F. Voracek, Alan W. Wilhite ISBN 978-0-9798095-4-5 1. Horizontal launch 2. Assured space access 3. Future space capable vehicles NASA SP 2011-215994 Printed in the United States of America December 2011 ii HORIZONTAL LAUNCH Table of Contents Foreword ..............................................................................................................................................................................................v Preface..................................................................................................................................................................................................vii Executive Summary .........................................................................................................................................................................xi Chapter 1. Introduction ...................................................................................................................................................................1