High Power, Reflection Tolerant Rf Solid State Amplifier Design
Total Page:16
File Type:pdf, Size:1020Kb
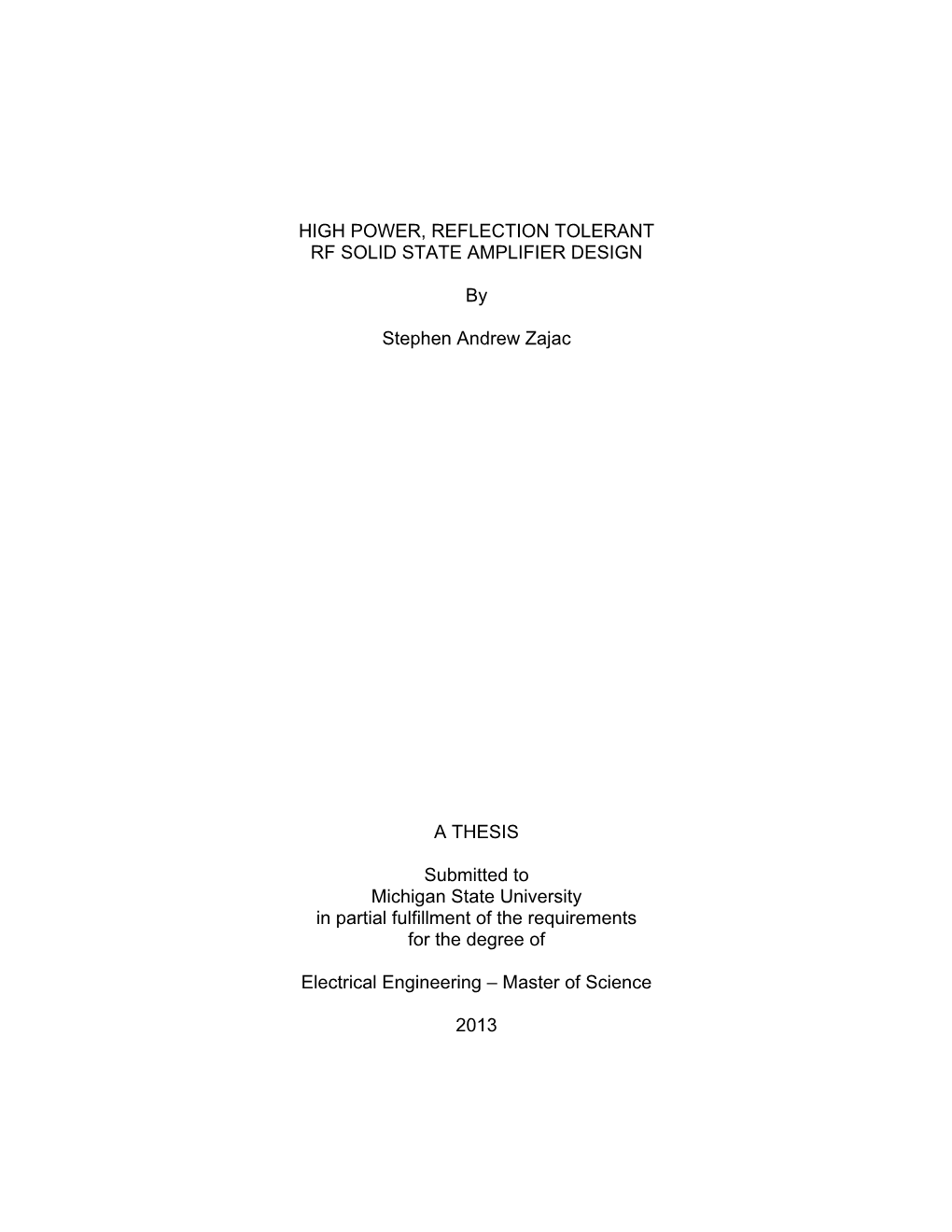
Load more
Recommended publications
-
RF Connector Overview Guide Linx Technologies Offers a Wide Variety of SMA, MCX, MMCX and MHF Radio Frequency Connector and Cable Assemblies
RF Connector Overview Guide Linx Technologies offers a wide variety of SMA, MCX, MMCX and MHF radio frequency connector and cable assemblies. RF connectors and cables consist of miniature precision-machined mechanical components and clever designs with complex assembly which are necessary to minimize losses and reflections. This requires tight tolerances, quality surface finishing and proper choice of metals and insulators. By combining domestic design and quality with offshore connector manufacturing, Linx offers low loss connectors at very competitive prices for OEM customers. – 1 – Revised 9/24/15 SMA Connectors Cable Termination SMA and RP-SMA Connecctors SMA (subminiature version A) connectors are high performance coaxial RF connectors with 50-ohm matching and Connector Body Orientation Mount Style Cable Types Polarity Part Numbers excellent electrical performance up to 18GHz with insertion loss as low as 0.17dB. They also have high mechanical Type Finish RG-174, RG-188A, Standard CONSMA007 strength through their thread coupling. This coupling minimizes reflections and attenuation by ensuring uniform SMA007 Straight Crimp End Plug Nickel RG-316 contact. SMA connectors are among the most popular connector type for OEMs as they offer high durability, low Reverse CONREVSMA007 RG-58/58A/58C, Standard CONSMA007-R58 VSWR and a variety of antenna mating choices. In order to comply with FCC Part 15 requirements for non-standard SMA007-R58 Straight Crimp End Plug Nickel RG-141A Reverse CONREVSMA007-R58 antenna connectors, SMA connectors are -
RF/Microwave Connectors on Printed Circuit Boards
High Frequency Design CONNECTORS ON PCBs RF/Microwave Connectors on Printed Circuit Boards By Gary Breed Editorial Director hen mounting This month’s tutorial takes a an RF/micro- look at the practical matter Wwave or high of characterizing, then speed digital connector to installing, an RF connector a printed circuit board, on a printed circuit board the transition from the connector body and inner conductor pin to the printed traces is often the source of excessive mismatch. The discontinu- ity in size, shape and surrounding conductors Figure 1 · Connectors must provide a tran- results in an area with a characteristic sition from a round coaxial transmission line impedance that can be much different (usual- to the planar microstrip or stripline structure ly lower) that the system impedance of 50 of a p.c. board. ohms (RF/microwave) or 75 ohms (data or video). An additional challenge is the transition increases the characteristic impedance in the from the round coaxial structure of cables and area where the required solder pad is much their connectors, to the planar stripline or wider than a normal 75-ohm microstrip line. microstrip structure of signal paths on a p.c. Figure 2 illustrates the problem by showing board. The connector shown in Figure 1 the relative widths of the solder pad and demonstrates one approach to solving the microstrip lines on the top metal layer. Figure problem. The connector body is designed to 3 shows how the top metal and the metal of minimize the VSWR “bump” caused by the the next lower layer are modified to create a change from coaxial to planar transmission region with higher characteristic impedance. -
Table of Contents
TABLE OF CONTENTS CHAPTER SUBJECT PAGE 1 Theory of Operation ........................................................................1-1 Line of Sight .............................................................................1-3 Troposcatter ..............................................................................1-4 Diffraction .................................................................................1-5 Fading .......................................................................................1-7 Diversity Reception ..................................................................1-7 Characteristics of AN/TRC-170 (V)2, 3, 5 ...............................1-9 Service Range of the V2, V3 ....................................................1-10 2 AC Power ..........................................................................................2-1 Power Entry Panel Controls & Indicators .................................2-3 Low Voltage Power Supply #1 .................................................2-11 Low Voltage Power Supply #2 .................................................2-12 AC-AC Converter .....................................................................2-14 3 DC POWER ……………………………………………………….3-1 4 TQG Operation ................................................................................4-1 Fault Indicator Panel .................................................................4-6 Generator Switch Over .............................................................4-10 5 Signal Flow .......................................................................................5-1 -
Fiscal 2010 Annual Report
Fiscal 2010 Annual Report A V I E L Electronics Chief Executive Officer’s Letter to Stockholders September 22, 2011 Fellow Stockholders: Fiscal Year 2010, which ended on October 31, 2010, was a year in which RF Industries achieved its eighteenth consecutive year of profitability and rebounded from a sales decline in Fiscal 2009 that was the result of the recession and the industry-wide slowdown in wireless infrastructure spending. The improvements in our operations in 2010, and the strengthening of our balance sheet in Fiscal 2010 enabled us to once again focus on our longer term goals of growth and acquisitions. Despite the general economic uncertainty in 2010, the improvement of RF Industries’ operations in Fiscal 2010 and the strength of its October 31, 2010 balance sheet provided us with the security and comfort to (i) expand our operations to the East Coast through the purchase Cables Unlimited, Inc., our new fiber optics and harness assembly subsidiary that we purchased in June 2011, and (ii) significantly increase the dividends that we are distributing to you stockholders. Fiscal 2010 Results For the fiscal year ended October 31, 2010, sales were $16,322,000, compared to sales of $14,213,000 in fiscal 2009. Operating income was $2,004,000 compared to $906,000 in 2009, and net income after taxes was $1,220,000, or $0.38 per diluted share, compared to net income of $656,000, or $0.20 per diluted share for fiscal 2009. Sales at the RF Connector and Cable Assembly segment, our most profitable business segment, increased 16% to $14,094,000 from $12,154,000 in fiscal 2009. -
RS Enterprises
+91-8048372651,225 RS Enterprises https://www.indiamart.com/rsenterpriseskannauj/ We “RS Enterprises” are a Sole Proprietorship based firm, engaged as the foremost Wholesaler of Coaxial Cable, BLW98 Transistor, Coaxial Connector, MS Connector, etc. About Us Established in the year 2017 at Kannauj, Uttar Pradesh, We “RS Enterprises” are a Sole Proprietorship based firm, engaged as the foremost Wholesaler of Coaxial Cable, BLW98 Transistor, Coaxial Connector, MS Connector, etc. Our products are high in demand due to their premium quality, seamless finish, different patterns and affordable prices. Furthermore, we ensure to timely deliver these products to our clients, through this we have gained a huge clients base in the market. For more information, please visit https://www.indiamart.com/rsenterpriseskannauj/about-us.html O u r P r o d u c t s E L B A C L A I X A O C Coaxial Cable RG6 Dual Shielded Coaxial Cable RG6 Coaxial Cable RF Coaxial Cable O u r P r o d u c t s R O T S I S N A R T 8 9 W L B BLW98 Transistor 15 AMP 32V/40V FUSABLE RESISTANCE (ALSO AVAILABLE IN DIFFERENT TYPE OF RESISTANCE) Solenoid Valve Model- 30126- ON5040 MOSFET 3-2G-S8 (Fluid control system) TRANSISTOR Make- Rotex O u r P r o d u c t R s O T C E N N O C L A I X A O C N Type Coaxial Connector F Coaxial Connector 75 Ohm F Connector MCX TO SMA Cable Connector O u r P r o d u c t s R O T I C A P A C A C I M 680pf 500v 1% silver dipped MATEL TYPE MICA CAPACITOR mica capacitor Mica Capacitor Mica Capacitor 120NF, 20NF,10NF ( 120000PF,20000PF.10000PF) O u r P r o d -
Variable Capacitors in RF Circuits
Source: Secrets of RF Circuit Design 1 CHAPTER Introduction to RF electronics Radio-frequency (RF) electronics differ from other electronics because the higher frequencies make some circuit operation a little hard to understand. Stray capacitance and stray inductance afflict these circuits. Stray capacitance is the capacitance that exists between conductors of the circuit, between conductors or components and ground, or between components. Stray inductance is the normal in- ductance of the conductors that connect components, as well as internal component inductances. These stray parameters are not usually important at dc and low ac frequencies, but as the frequency increases, they become a much larger proportion of the total. In some older very high frequency (VHF) TV tuners and VHF communi- cations receiver front ends, the stray capacitances were sufficiently large to tune the circuits, so no actual discrete tuning capacitors were needed. Also, skin effect exists at RF. The term skin effect refers to the fact that ac flows only on the outside portion of the conductor, while dc flows through the entire con- ductor. As frequency increases, skin effect produces a smaller zone of conduction and a correspondingly higher value of ac resistance compared with dc resistance. Another problem with RF circuits is that the signals find it easier to radiate both from the circuit and within the circuit. Thus, coupling effects between elements of the circuit, between the circuit and its environment, and from the environment to the circuit become a lot more critical at RF. Interference and other strange effects are found at RF that are missing in dc circuits and are negligible in most low- frequency ac circuits. -
Agilent RF and Microwave Switch Selection Guide
Agilent RF and Microwave Switch Selection Guide Agilent Technologies — Your one-stop switching solution provider Key Features • High reliability and exceptional repeatability ensure excellent measurement accuracy • Excellent RF specifi cations optimize your test system measurement capability • Broad selection of switches provides confi guration fl exibility for various applications Agilent RF and Microwave Switches Agilent has been a leading designer and manufacturer of RF and microwave Agilent RF and microwave switches in the global marketplace for more than 60 years. RF and microwave switches provide: switches are used extensively in microwave test systems for signal routing between instruments and devices under test (DUT). Incorporating a switch into • Superior RF performance to a switch matrix system enables you to route signals from multiple instruments optimize test equipment to single or multiple DUTs. This allows multiple tests to be performed with the performance same setup, eliminating the need for frequent connects and disconnects. The • Unmatched quality and reliability entire testing process can thus be automated, increasing the throughput in to minimize measurement high-volume production environments. uncertainty Agilent designs and manufacturers a comprehensive range of RF and microwave • Ultra broadband to meet the switches to meet your switching requirements. There are two mainstream demands of today’s devices switch technologies in use today: solid state and electromechanical. Agilent’s solid state and electromechanical switches operate across a broad frequency range and come in a variety of confi gurations. Designed with high accuracy and repeatability for automated test and measurement, signal monitoring and routing applications, Agilent switches have a proven track record for high performance, quality and reliability. -
Development of a Solid State Rf Amplifier in the Kw Regime for Application with Low Beta Superconducting Rf Cavities C
Proceedings of 2005 Particle Accelerator Conference, Knoxville, Tennessee DEVELOPMENT OF A SOLID STATE RF AMPLIFIER IN THE KW REGIME FOR APPLICATION WITH LOW BETA SUPERCONDUCTING RF CAVITIES C. Piel#, Accel GmbH, Bergisch Gladbach, Germany B. Aminov, A. Borisov, S. Kolesov, H. Piel, Cryoelectra GmbH, Wuppertal, Germany Abstract input and output baluns. The input and output matching Projects based on the use of low beta superconducting networks are composed of two sections, designed using cavities for ions are under operation or development at lumped as well as distributed components. Four tubular several labs worldwide. Often these cavities are trimming capacitors are used for the precise individual individually driven by RF power sources in the kW tuning of the matching circuits. Special loading networks regime [1, 2]. For an ongoing project a modular 2 kW, at the input and output are used to prevent any common- 176 MHz unconditionally stable RF amplifier for CW and mode oscillations. Integrated circuit voltage regulators pulsed operation was designed, built, and tested In order stabilize gate-source voltage. to optimize the performance of the power transistors and The quiescent drain current of the power transistor were other thermally loaded components an extended thermal adjusted to 1A (0.5A per transistor section) at 50VDC of analysis was performed to develop a high performance the drain voltage to ensure a class-AB operation. One of water cooling system. The paper outlines the design the 275 W modules is shown in Fig. 1. concept of the amplifier and presents characteristic experimental results obtained from a series of 6 high power amplifiers. -
Detection of Arcs in Automotive Electrical Systems
Detection of Arcs in Automotive Electrical Systems by Matthew David Mishrikey S.B., Massachusetts Institute of Technology (2002) Submitted to the Department of Electrical Engineering and Computer Science in partial fulfillment of the requirements for the degree of Master of Engineering at the MASSACHUSETTS INSTITUTE OF TECHNOLOGY January 2005 c Matthew David Mishrikey, MMV. All rights reserved. The author hereby grants to MIT permission to reproduce and distribute publicly paper and electronic copies of this thesis document in whole or in part. Author............................................. ............................... Department of Electrical Engineering and Computer Science January 31, 2005 Certified by......................................... ............................... Professor Markus Zahn Thomas and Gerd Perkins Professor of Electrical Engineering Thesis Supervisor Certified by......................................... ............................... Dr. Thomas A. Keim Assistant Director of the Laboratory for Electromagnetic and Electronic Systems Thesis Supervisor Accepted by......................................... .............................. Arthur C. Smith Chairman, Department Committee on Graduate Students – ii – Detection of Arcs in Automotive Electrical Systems by Matthew David Mishrikey Submitted to the Department of Electrical Engineering and Computer Science on January 31, 2005, in partial fulfillment of the requirements for the degree of Master of Engineering Abstract At the present time, there is no established method for the detection of DC electric arcing. This is a concern for forthcoming advanced automotive electrical systems which consist of higher DC electric power bus voltages, such as the automotive industry proposed 42 volt standard. At these higher voltages, wire faults can lead to stable electric arcs, which may hazardously cause insulation to catch on fire. This thesis presents the results of investiga- tions of phase noise and broadband emissions as indicators of DC electric arcing. -
ZSA4848-80M1G Broadband RF Power Amplifier Series 80Mhz-1Ghz/55W CW Made in Japan Apr.28,2012/DS0014-01
ZSA4848-80M1G Broadband RF Power Amplifier Series 80MHz-1GHz/55W CW Made in Japan http://www.rfad.co.jp Apr.28,2012/DS0014-01 MODEL : ZSA4848 – 80M1G ・ Class AB Solid state Built – In Protection ・Utilises the latest LDMOS ・Broadband(Instantaneous Single Band) ・High Temperature ・Linear Output Power(1dB Gain Compression) ・Supply Current and Voltage ・Low Distortion ・FWD Over Power ・Internal Systems Diagnostics and Status Indicator ・REF Over Power ・19” Rack / 3U / Bench Case ・3Years Standard Warranty Maintenance Other Amplifiers Available ・Amplifier Designed For Minimal Maintenance ・ZSA4646 – 80M1G ⇒ 35W ・Rapid Diagnostic ・ZSA5050 – 80M1G ⇒ 100W ・Minimal Downtime ・ZSA5353 – 80M1G ⇒ 180W ・ZSA5757 – 80M1G ⇒ 500W Applications Additional Options ・EMC Tests ・RF Connector Type ・RF Tests And Instrumentation ・RF Connector on Rear Panel ・Radio communication ・RF Sample Port (Front or Rear Panel) ・Measurement And Research Laboratories ・Detected Sample Port (Front or Rear Panel) ・RF Input Switch ・Gain Control ・IEEE488 Control Outline Drawing ※ In Millimeters (FRONT VIEW) (SIDE VIEW) 480 30 499 16.8 RF Power Amplifier ZSA4848-80M1G 80MHz~1GHz +48dB 55W 37.6 FWD 0 55 W REF 0 55 W Intake 25.0゜C 7 OPERATE RESET NEXT POWER 57.2 RF IN RF OUT 132.5 MAX INPUT +3dBm CAUTION 50Ω 50Ω 37.7 2.5 10 455 10 2.5 10.5 (REAR VIEW) 440 2 10A 10A FUSE FUSE EMERGENCY AC100V IN STOP 127.5 REMOTE GND 3 Rf Amplifier Design Co.,Ltd. A-3 Fuji-Incubatecenter 2586-3 Obuchi Fuji Shizuoka 417-0801 Japan Tel/Fax:0545-35-1174 E-mail:[email protected] - 1 - ZSA4848-80M1G Broadband RF Power -
Detailed Drawings.Pdf
Southwest Florida Water Management District 2379 Broad Street Brooksville, Florida 34604 TAMPA OFFICE BOARDROOM A/V RENOVATION & UPGRADES Index: AV-101 LEGEND INFORMATION PAGE AV-102 BUILDING LAYOUT AND ROOM LOCATIONS AV-103 BOARDROOOM FLOOR PLAN- DAIS - STAFF TABLES AV-104 CRESTRON CONTROL SYSTEM AV-105 BiAMP DSP-01 CONNECTIONS AV-106 BiAMP DSP-02 COONNECTIONS AV-107 HD-SDI ROUTER & VTC SYSTEM AV-108 DAIS & STAFF TABLES - VIDEO DISTRIBUTION AV-109 VIDEO PRODUCTION SYSTEMS AV-110 DEVICE LOCATIONS & MISC SYSTEMS AV-111 AUDIO AMPLIFIERS AND CEILING SPEAKERS AV-112 REMOTE ROOM DISPLAYS 1 2 3 4 5 6 7 8 9 10 Equipment Type Prefixes Connector Type Prefixes Cable Signal Type Prefixes Drawing Symbols J ACO - Auto Changeover, Protection Switch $ - Unknown Connector AUD - Audio Signal J ACOMB - Audio Combiner - Stereo to Mono 9D - 9Pin Sub-D Connector BB - Black Burst Reference Signal 2'X2' LIGHT FIXTURE ADC - Analog to Digital Converter 15HD - 15Pin High Density Connector CTL - Control 2'X2' LIGHT FIXTURE ADLY - Audio Delay Device 25D - 25 Pin Sub-D Connector DAT - DATA AP - Audio Processor- Compressor/Limiter, ETC B - BNC Connector DGA - Digital Audio R RECESSED LIGHT FIXTURE ASPLT - Audio Splitter - Mono to Stereo BT - Bantum Connector DGV - Digital Video Signal SP FIRE SPRINKLIER CAM - CAMERA DIN - DIN Type Connector DTE - Dante-Digital Audio Data I CC - Closed Captions Equipment DVI - 29Pin DVI Connector HDBNC - Mini BNC Connector WIFI ANTENNA I CIM - Computer Interface Module- KVM Dongle DVI-D - DVI-D Digital Video Connector LAN - Ethernet/ -
Data Sheets SKY65050-372LF: 0.45-6.0 Ghz Low Noise Transistor
DATA SHEET SKY65050-372LF: 0.45-6.0 GHz Low Noise Transistor Applications • Wireless infrastructure: WLAN, WiMAX, broadband, cellular base stations • Test instrumentation • LNA for GPS receivers • Satellite receivers Features Figure 1. SKY65050-372LF Block Diagram • Externally matched for wideband operation Description • Noise Figure = 0.45 dB @ 2.4 GHz of device only The SKY65050-372LF is a high performance, n-channel low-noise • Noise Figure = 0.65 dB @ 2.4 GHz including matching network transistor. The device is fabricated from Skyworks advanced loss depletion mode pHEMT process and is provided in a • Gain = 15.5 dB @ 2.4 GHz 2.20 x 1.35 x 1.10 mm, 4-pin SC-70 package. • OIP3 = +23.5 dBm @ 2.4 GHz, VDD = 3 V, IDD = 20 mA The transistor’s low Noise Figure (NF), high gain, and excellent 3rd • P1dB = +10.5 dBm @ 2.4 GHz, VDD = 3 V, IDD = 20 mA Order Intercept Point (IP3) allow the device to be used in various • Adjustable supply current, 5 to 55 mA receiver and transmitter applications. • Small, SC-70 (4-pin, 2.20 x 1.35 x 1.10 mm) package (MSL1, A functional block diagram is shown in Figure 1. The pin 260 °C per JEDEC J-STD-020) configuration and package are shown in Figure 2. Signal pin assignments and functional pin descriptions are provided in Table 1. Figure 2. SKY65050-372LF Pinout – 4-Pin SC-70 (Top View) Skyworks Solutions, Inc. • Phone [781] 376-3000 • Fax [781] 376-3100 • [email protected] • www.skyworksinc.com 200967G • Skyworks Proprietary Information • Products and Product Information are Subject to Change Without Notice • November 14, 2012 1 DATA SHEET • SKY65050-372LF LOW NOISE TRANSISTOR Table 1.