LTAP News, Issue 91, Fall 2006
Total Page:16
File Type:pdf, Size:1020Kb
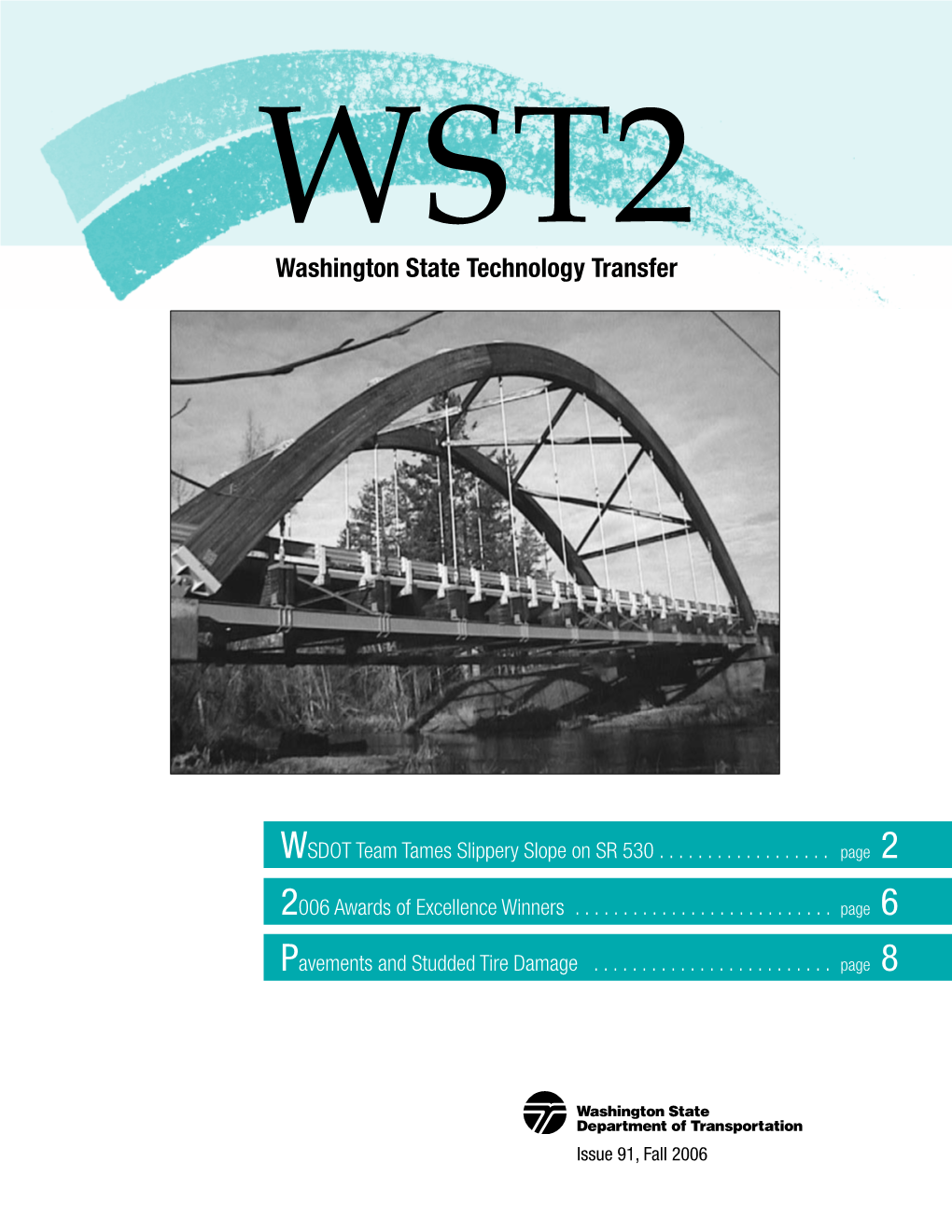
Load more
Recommended publications
-
Guide for Partial- and Full-Depth Pavement Recycling in California
December 2020 Guideline: UCPRC-GL-2020-01 Guide for Partial- and Full-Depth Pavement Recycling in California Authors: D. Jones, S. Louw, and J. Harvey Partnered Pavement Research Center (PPRC) Contract Strategic Plan Elements 4.59, 4.65, 4.69, and 4.70 (DRISI Tasks 2707, 3194, 3195, and 3196): Improved Guidance and Specifications for In-Place Recycling PREPARED FOR: PREPARED BY: California Department of Transportation University of California Division of Research, Innovation and System Information Pavement Research Center Office of Materials and Infrastructure Roadway Research UC Davis and UC Berkeley TECHNICAL REPORT DOCUMENTATION PAGE 1. REPORT NUMBER 2. GOVERNMENT ASSOCIATION NUMBER 3. RECIPIENT’S CATALOG NUMBER UCPRC-GL-2020-01 4. TITLE AND SUBTITLE 5. REPORT PUBLICATION DATE Guide for Partial- and Full-Depth Pavement Recycling in California December 2020 6. PERFORMING ORGANIZATION CODE 7. AUTHOR(S) 8. PERFORMING ORGANIZATION REPORT D. Jones, S. Louw, and J. Harvey NO. UCPRC-GL-2020-01 UCD-ITS-RR-21-11 9. PERFORMING ORGANIZATION NAME AND ADDRESS 10. WORK UNIT NUMBER University of California Pavement Research Center Department of Civil and Environmental Engineering, UC Davis 11. CONTRACT OR GRANT NUMBER 1 Shields Avenue 65A0542 and 65A0628 Davis, CA 95616 12. SPONSORING AGENCY AND ADDRESS 13. TYPE OF REPORT AND PERIOD COVERED California Department of Transportation Guideline Division of Research, Innovation, and System Information 14. SPONSORING AGENCY CODE P.O. Box 942873 Sacramento, CA 94273-0001 15. SUPPLEMENTAL NOTES doi:10.7922/G2TX3CN8 16. ABSTRACT This document has been prepared to guide practitioners on project investigation, recycling strategy selection, pavement structural design, environmental life cycle and life cycle cost assessment, mix design, and construction of in-place pavement recycling projects on flexible pavements in California. -
Bar Harbor Pedestrian Ramp Construction Win 022469.00 2016
BAR HARBOR PEDESTRIAN RAMP CONSTRUCTION WIN 022469.00 2016 1 Updated 11/15/15 STATE PROJECT MAINTENANCE & OPERATIONS 2 BIDDING INSTRUCTIONS 1. Use pen and ink to complete all paper Bids. 2. As a minimum, the following must be received prior to the time of Bid opening: For a Paper Bid: a) a copy of the Notice to Contractors, b) the completed Acknowledgement of Bid Amendments form, c) the completed Schedule of Items, d) two copies of the completed and signed Contract Agreement, Offer & Award form, e) a Bid Guaranty, f) the completed Contractor Information Sheet, and g) any other certifications or Bid requirements listed in the Bid Documents as due by Bid opening. For an Electronic Bid: a) a completed Bid using Expedite® software and submitted via the Bid Express™ web- based service, b) an electronic Bid Guaranty (if required) or a faxed copy of a Bid Bond (with original to be delivered within 72 hours), and c) any other Certifications or Bid requirements listed in the Bid Documents as due by Bid opening. 3. Include prices for all items in the Schedule of Items. 4. Bid Guaranty acceptable forms are: a) a properly completed and signed Bid Bond on the Department’s prescribed form (or on a form that does not contain any significant variations from the Department’s form as determined by the Department) for 5% of the Bid Amount or b) an Official Bank Check, Cashier’s Check, Certified Check, U.S. Postal Money Order or Negotiable Certificate of Deposit in the amount stated in the Notice to Contractors or c) an electronic bid bond submitted with an electronic bid. -
Full-Depth Recycling Study
STATE OF CALIFORNIA • DEPARTMENT OF TRANSPORTATION ADA Notice TECHNICAL REPORT DOCUMENTATION PAGE For individuals with sensory disabilities, this document is available in alternate TR0003 (REV 10/98) formats. For information call (916) 654-6410 or TDD (916) 654-3880 or write Records and Forms Management, 1120 N Street, MS-89, Sacramento, CA 95814. 1. REPORT NUMBER 2. GOVERNMENT ASSOCIATION NUMBER 3. RECIPIENT'S CATALOG NUMBER CA 17-2707 4. TITLE AND SUBTITLE 5. REPORT DATE Full-Depth Recycling Study: Test Track Construction and First-Level Analysis of Phase 1 and Phase 2 HVS Testing, Forensic Investigation, and Phase 1 Laboratory Testing 07/11/2016 6. PERFORMING ORGANIZATION CODE 7. AUTHOR(S) 8. PERFORMING ORGANIZATION REPORT NO. D. Jones, S. Louw, and R. Wu UCPRC-RR-2015-02 9. PERFORMING ORGANIZATION NAME AND ADDRESS 10. WORK UNIT NUMBER University of California Pavement Research Center Department of Civil and Environmental Engineering, UC Davis 1 Shields Avenue 11. CONTRACT OR GRANT NUMBER Davis, Ca 95616 65A0542 12. SPONSORING AGENCY AND ADDRESS 13. TYPE OF REPORT AND PERIOD COVERED California Department of Transportation Research Report Division of Research, Innovation, and System Information October 2014 - September 2017 P.O. Box 942873 14. SPONSORING AGENCY CODE Sacramento, CA 94273-0001 RPMD Task ID: 2707 15. SUPPLEMENTARY NOTES 16. ABSTRACT This First-level report describes the first two phases of a study comparing the performance of four different full-depth pavement reclamation strategies, namely pulverization with no stabilization (FDR-NS), stabilization with foamed asphalt and portland cement (FDR-FA), stabilization with portland cement only (FDR-PC), and stabilization with engineered asphalt emulsion (FDR-EE). -
Department of Transportation and Infrastructure Renewal
Department of Transportation and Infrastructure Renewal Annual Accountability Report 2009-2010 Accountability Report Fiscal Year 2009-2010 Transportation and Infrastructure Renewal Table of Contents 1. Accountability Statement.....................................................................................................1 2. Message from the Minister..................................................................................................2 3. Introduction..........................................................................................................................4 4. 2009-2010 Department Priorities and Accomplishments....................................................4 5. Other Accomplishments.....................................................................................................22 6. Financial Results................................................................................................................23 7. Performance Measures.......................................................................................................24 Accountability Report Fiscal Year 2009-2010 Transportation and Infrastructure Renewal 1. Accountability Statement The accountability report of the Department of Transportation and Infrastructure Renewal (TIR) for the year ended March 31, 2010, is prepared pursuant to the Provincial Finance Act and government policies and guidelines. These authorities require the reporting of outcomes against TIR business plan information for the fiscal year 2009-2010. The reporting -
Matters Fall 2004
cal Ass hni ista ec nc l T e a P c r o o L g r a m MATTERSLTAP Montana's Answers To Technical Education of Roads & Streets LTAP College of Engineering Montana State University-Bozeman Bozeman, MT 59717-3910 a Montan 1-800-541-6671 Fall 2004 October November December Vol.22, No.4 INSIDE Partnerships Create Winners at Snow Rodeo by Michele Beck 2-3 Snow Rodeo (cont’d) hat do Montana LTAP, coordinate all that he wanted it to W APWA, City of Great be. With the help of Debbie 4 Annual Calendar Falls, Montana Department of Kimball, Program Specialist, City 5 Calendar of Transportation, and Tractor & of Great Falls, they worked toward Fall Events Equipment have in common? They establishing contacts to assist them all were partners at the 15th Annual in the Rodeo. Basta noted that the 6-7 Snow Rodeo (cont’d) Equipment Operator Training and success of the Rodeo comes from Snow Rodeo held in Great Falls, these valuable partnerships and the 8-9 Traffic Signs for Montana, this September. teamwork from all involved. Wildland Fire Incidents: Meeting National Standards Beginnings... Montana LTAP’s Involvement... The Montana Snow Rodeo grew Montana LTAP provided Winter 10-11 Pedestrian Safety at from an idea that Marty Basta, Survival training on the first day of Intersections Operations Manager, City of Great the Rodeo, along with panel/ 12-15 LTAP Library participant discussion regarding road maintenance, road funding, and dealing with the public. Partici- pants were split into two groups. During the morning, one group stayed in the classroom while the other group went outside for hands- on equipment training. -
Construction Route 15 Ditching Deer Isle And
CONSTRUCTION ROUTE 15 DITCHING DEER ISLE$1'6721,1*721 WIN 21468.00 2015 1 Updated 11/05/14 STATE PROJECT ."*/5&/"/$&01&3"5*0/4 2 BIDDING INSTRUCTIONS 1. Use pen and ink to complete all paper Bids. 2. As a minimum, the following must be received prior to the time of Bid opening: For a Paper Bid: a) a copy of the Notice to Contractors, b) the completed Acknowledgement of Bid Amendments form, c) the completed Schedule of Items, d) two copies of the completed and signed Contract Agreement, Offer & Award form, e) the completed Contractor Information Sheet, and f) any other certifications or Bid requirements listed in the Bid Documents as due by Bid opening. For an Electronic Bid: a) a completed Bid using Expedite® software and submitted via the Bid Express™ web- based service, and b) any other Certifications or Bid requirements listed in the Bid Documents as due by Bid opening. 3. Include prices for all items in the Schedule of Items. 4. All Bid Packages which are mailed or sent express, shall be provided in double (one envelope inside the other) envelopes, for security and other reasons. The Inner Envelope shall have the following information provided on it: Bid Enclosed - Do Not Open WIN: Town: Date of Bid Opening: Name of Contractor with mailing address and telephone number: In Addition to the usual address information, the Outer Envelope should have written or typed on it: Double Envelope: Bid Enclosed WIN: Town: Date of Bid Opening: Name of Contractor: If a paper Bid is to be sent express, “FedEx First Overnight” delivery is suggested as the package is delivered directly to the DOT Headquarters Building, Mailroom, in Augusta located at 24 Child Street in Augusta. -
Full-Depth Recycling Study: Test Track Construction And
September 2015 Research Report: UCPRC-RR-2015-02 Authors: D. Jones, S. Louw, and R. Wu Partnered Pavement Research Center (PPRC) Contract Strategic Plan Element 4.59 (DRISI Task 2707): Guidelines for Full-Depth Reclamation of Pavements PREPARED FOR: PREPARED BY: California Department of Transportation University of California Division of Research, Innovation, and System Information Pavement Research Center Office of Materials and Infrastructure Roadway Research UC Davis, UC Berkeley DOCUMENT RETRIEVAL PAGE Research Report: UCPRC-RR-2015-02 Title: Full-Depth Recycling Study: Test Track Construction and First-Level Analysis of Phase 1 and Phase 2 HVS Testing, Forensic Investigation, and Phase 1 Laboratory Testing Authors: D. Jones, S. Louw, and R. Wu Caltrans Technical Lead: D. Maskey Prepared for: FHWA No.: Report Submitted: Final Publication Date Caltrans CA172707A 04/21/2016 07/11/2016 Strategic Plan Element No: DRISI Task No.: Status: Version No.: 4.59 2707 Final 1 Abstract: This first-level report describes the first two phases of a study comparing the performance of four different full-depth pavement reclamation strategies, namely pulverization with no stabilization (FDR-NS), stabilization with foamed asphalt and portland cement (FDR-FA), stabilization with portland cement only (FDR-PC), and stabilization with engineered asphalt emulsion (FDR-EE). A literature review, the test track layout and design, stabilization and asphalt concrete mix designs, and test track construction are discussed, as well as the results of Heavy Vehicle Simulator (HVS) and preliminary laboratory testing, and a forensic investigation of the HVS test sections. A number of problems were experienced during construction of the FDR-PC and FDR-EE lanes on the test track and consequently only the FDR-NS and FDR-FA lanes and one section of the FDR-PC lane (5 percent measured cement content) were considered satisfactorily uniform for the purposes of HVS testing. -
Annual Research Program Overview
Texas Department of Transportation Research Program Fiscal Year 2020 Annual Research Program Overview Research and Technology Implementation Division For individuals with sensory disabilities, this document is available in alternate formats. To obtain a copy in an alternate format, contact: Texas Department of Transportation Research and Implementation Division 118 E. Riverside Drive Austin, Texas 78704 512-416-4730 [email protected] © Copyright 2020 Texas Department of Transportation ALL RIGHTS RESERVED Table of Contents (Click section title to go directly to section) Message from the Director........................................................................................... 2 Universities Active in TxDOT’s 2020 Research Program ............................................. 3 Fiscal Year 2020 Research Program Overview and Related Funding ........................ 4 TxDOT Districts and Divisions Key ................................................................................ 6 Construction, Maintenance and Materials Projects .................................................... 8 Planning and Environmental Projects ........................................................................ 46 Safety and Operations Projects .................................................................................. 61 Strategy and Innovation Projects ............................................................................... 93 Structures and Hydraulics Projects ........................................................................... -
Full-Depth Recycling Study: Test Track Construction and First Level Analysis of Phase 1 HVS and Laboratory Testing Authors: D
June 2014 Research Report: UCPRC-RR-2014-03 Authors: D. Jones, R. Wu, and S. Louw Partnered Pavement Research Center (PPRC) Contract Strategic Plan Element 4.36: Recycling of Rubberized HMA in RAP and FDR Projects PREPARED FOR: PREPARED BY: California Department of Transportation University of California Division of Research, Innovation, and System Information Pavement Research Center Office of Materials and Infrastructure Roadway Research UC Davis, UC Berkeley DOCUMENT RETRIEVAL PAGE Research Report: UCPRC-RR-2014-03 Title: Full-Depth Recycling Study: Test Track Construction and First Level Analysis of Phase 1 HVS and Laboratory Testing Authors: D. Jones, R. Wu, and S. Louw Caltrans Technical Leads: A. Fong and D. Maskey Prepared for: FHWA No.: Work submitted: Date Caltrans CA152374A 8/20/2014 June 2014 Strategic Plan Element No: Status: Version No.: 4.36 Final 1 Abstract: This first-level report describes the first phase of a study comparing the performance of four different full-depth pavement reclamation strategies, namely pulverization with no stabilization (FDR-NS), stabilization with foamed asphalt and portland cement (FDR-FA), stabilization with portland cement only (FDR-PC), and stabilization with engineered asphalt emulsion (FDR-EE). A literature review, the test track layout and design, stabilization and asphalt concrete mix designs, and test track construction are discussed, as well as results of Heavy Vehicle Simulator (HVS) and laboratory testing. A number of problems were experienced during construction of the FDR-PC and FDR-EE lanes on the test track and consequently only the FDR-NS and FDR-FA lanes and one section of the FDR-PC lane (5 percent measured cement content) were considered satisfactorily uniform for the purposes of accelerated pavement testing. -
Rapid Flash Pedestrian Signs Supply and Delivery MATERIALS WIN 18876.00 Statewide 2015
Rapid Flash Pedestrian Signs Supply and Delivery MATERIALS WIN 18876.00 Statewide 2015 1 Updated 11/05/14 FEDERAL PROJECT 2 Effective November 05, 2014 Supersedes January 19, 2012 BIDDING INSTRUCTIONS FOR ALL PROJECTS: 1. Use pen and ink to complete all paper Bids. 2. As a minimum, the following must be received prior to the time of Bid opening: For a Paper Bid: a) a copy of the Notice to Contractors, b) the completed Acknowledgement of Bid Amendments form, c) the completed Schedule of Items in Appendix A, d) two copies of the completed and signed Contract to Purchase Supplies, Materials and/or Equipment for a Specific Project, e) the completed Contractor Information Sheet, and f) any other certifications or Bid requirements listed in the Bid Documents as due by Bid opening. 3. Include prices for all items in the Schedule of Items. 4. If a paper Bid is to be hand carried, deliver directly to the Reception Desk using the “Public Entrance” which is located on the Capitol Street side of the DOT Headquarters Building in Augusta. If a paper Bid is to be sent, “FedEx First Overnight” delivery is suggested as the package is delivered directly to the DOT Headquarters Building located at 24 Child Street in Augusta. Other means, such as U.S. Postal Service’s Express Mail has proven not to be reliable. IN ADDITION, FOR FEDERAL AID PROJECTS: 5. Complete the DBE Proposed Utilization form, and submit with your bid. If you need further information regarding Bid preparation, call the DOT Contracts Section at (207) 624-3410. -
Full-Depth Reclamation (FDR) for Suburban/Urban and Local Roads Application
Full-Depth Reclamation (FDR) for Suburban/Urban and Local Roads Application Mihai Marasteanu, Principal Investigator Department of Civil, Environmental, and Geo- Engineering University of Minnesota December 2016 Research Project Final Report 2016-37 To request this document in an alternative format, such as braille or large print, call 651-366- 4718 or 1-800-657-3774 (Greater Minnesota) or email your request to [email protected]. Please request at least one week in advance. Technical Report Documentation Page 1. Report No. 2. 3. Recipients Accession No. MN/RC 2016-37 4. Title and Subtitle 5. Report Date Full-Depth Reclamation (FDR) for Suburban/Urban and Local December 2016 Roads Application 6. 7. Author(s) 8. Performing Organization Report No. Marcella Hartman, Mugur Turos, Debaroti Ghosh, Mihai Marasteanu 9. Performing Organization Name and Address 10. Project/Task/Work Unit No. Department of Civil, Environmental and Geo- Engineering CTS #2015009 University of Minnesota 11. Contract (C) or Grant (G) No. 500 Pillsbury Drive, Minneapolis, MN 55455 (c) 99008 (wo) 147 12. Sponsoring Organization Name and Address 13. Type of Report and Period Covered Minnesota Local Road Research Board Final Report Minnesota Department of Transportation 14. Sponsoring Agency Code Research Services & Library 395 John Ireland Boulevard, MS 330 St. Paul, MN 55155 15. Supplementary Notes http://mndot.gov/research/reports/2016/201637.pdf 16. Abstract (Limit: 250 words) Full-depth reclamation (FDR) as a rehabilitation method improves the service life of pavement structures by reusing asphalt materials, thereby reducing costs and allowing for conservation of nonrenewable resources. However, the lack of mechanics- based material testing procedures and performance-based specifications limit the use of FDR processes. -
Road Construction Options
ROAD CONSTRUCTION OPTIONS ASPHALT OVERLAY An asphalt overlay is an additional layer of asphalt that covers imperfections in existing asphalt. Asphalt overlays are commonly applied to driveways, parking lots, and pavement that have minor damage like light cracking, mild deterioration, or slightly sunken areas. The process of overlaying asphalt commonly includes a leveling out of the old asphalt's shape, ensuring a smooth, even surface on which to add additional layers. After the minor imperfections in the original asphalt have been filled in, butt joints are typically utilized to ensure the base layer remains level. This guarantees the asphalt overlay will match the height of doorways, garage thresholds, roads, sidewalks, and curbs. A special primer is then applied to the surface; this primer acts as the glue that secures the second layer of asphalt to the first. At this point, crushed stone may be necessary to further ensure a level asphalt overlay design. Once the stone has been compressed and graded, the paving begins. Asphalt concrete overlay is poured over the original layer, primer, and crushed stone. The butt joints make certain the asphalt meets the perimeters of the area and remains level. Once it is dried, the overlay has a sleek, smooth appearance that is free of defects. When preparing to administer an asphalt concrete overlay, it is important to bear a couple of considerations in mind. First, it is important that the damage on the original layer not be too deep. If it is, the second layer will simply seep into the cracks and indentations of the foundation, and the problem will remain unsolved.