Compact, Lightweight, High Efficiency Rotary Engine for Generator, Apu, and Range-Extended Electric Vehicles
Total Page:16
File Type:pdf, Size:1020Kb
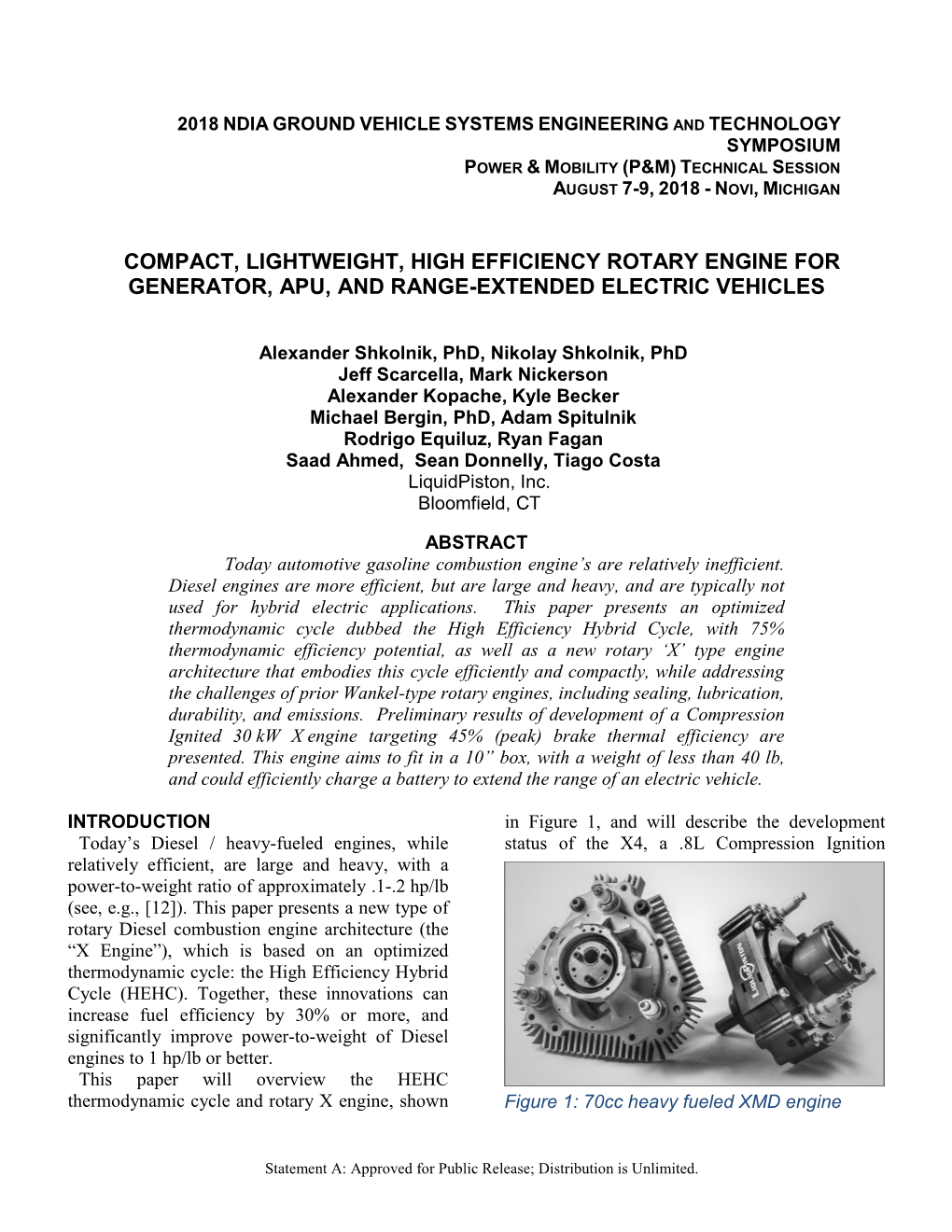
Load more
Recommended publications
-
Fiber Optic (Flight Quality) Sensors for Advanced Aircraft Propulsion
/ .. < / • _7 _ NASA Contractor Report 191195 ? R94AEB175 Fiber Optic (Flight Quality) Sensors For Advanced Aircraft Propulsion Final Report Gary L. Poppel GE Aircraft Engines Cincinnati, Ohio 45215 July 1994 Prepared for: Robert J. Baumbick, Project Manager National Aeronautics and Space Administration 2 I000 Brookpark Road Cleveland, Ohio 44135 Contract NAS3-25805 N94-37401 (NASA-CR-I9II95) FISER OPTIC (FLIGHT QUALITY) SENSORS FOR NationalAeronauticsand ADVANCED AIRCRAFT PROPULSION Fina] Uncl as Space Administration Report, Jan. 1990 - Jun. 1994 (GE) 90 p G3/06 0016023 TABLE OF CONTENTS Section Page 1.0 SUMMARY 2.0 INTRODUCTION 3.0 SENSOR SET DESCRIPTION 3.1 Identification and Requirements 3.2 Engine/System Schematics 3.3 F404 Implementation 3.4 Optical/Electrical Signal Comparison 9 4.0 SENSOR DESIGN, FUNCTIONALITY, & TESTING 9 4.1 TI Temperature Sensor 4.2 T2.5 Temperature Sensor I0 11 4.3 T5 Temperature Sensor 4.4 FVG Position Sensor 12 14 4.5 CVG Position Sensor 4.6 VEN Position Sensor 15 16 4.7 NL Speed Sensor 17 4.8 Nil Speed Sensor 4.9 AB Flame Detector 18 20 5.0 ELECTRO-OPTIC CIRCUITRY 5.1 Litton EOA Circuitry 20 23 5.2 GE Circuitry 24 5.3 Conax T5 Signal Processor 5.4 Ametek AB Flame Detector Assembly 25 26 6.0 ELECTRO-OPTICS UNIT DESIGN, ASSEMBLY, & TESTING 26 6.1 Chassis Design 26 6.2 Assembly Process 6.3 Internal Features 26 27 6.4 Input/Output Interfaces 6.5 Thermal Studies 27 27 6.6 Testing 7.0 CABLE DESIGN & FABRICATION 33 7.1 Identification of Cable Set 33 33 7.2 Optical Sensor Loop Configurations 7.3 GE-Designed Fiber -
Constant Volume Combustion Cycle for IC Engines
Constant Volume Combustion Cycle for IC Engines Jovan Dorić Assistant This paper presents an analysis of the internal combustion engine cycle in University of Novi Sad Faculty of Technical Sciences cases when the new unconventional piston motion law is used. The main goal of the presented unconventional piston motion law is to make a Ivan Klinar realization of combustion during constant volume in an engine’s cylinder. Full Professor The obtained results are shown in PV (pressure-volume) diagrams of University of Novi Sad Faculty of Technical Sciences standard and new engine cycles. The emphasis is placed on the shortcomings of the real cycle in IC engines as well as policies that would Marko Dorić contribute to reducing these disadvantages. For this paper, volumetric PhD student efficiency, pressure and temperature curves for standard and new piston University of Novi Sad Faculty of Agriculture motion law have been calculated. Also, the results of improved efficiency and power are presented. Keywords: constant volume combustion, IC engine, kinematics. 1. INTRODUCTION of an internal combustion engine, whose combustion is so rapid that the piston does not move during the Internal combustion engine simulation modelling has combustion process, and thus combustion is assumed to long been established as an effective tool for studying take place at constant volume [6]. Although in engine performance and contributing to evaluation and theoretical terms heat addition takes place at constant new developments. Thermodynamic models of the real volume, in real engine cycle heat addition at constant engine cycle have served as effective tools for complete volume can not be performed. -
Steady State and Transient Efficiencies of A
STEADY STATE AND TRANSIENT EFFICIENCIES OF A FOUR CYLINDER DIRECT INJECTION DIESEL ENGINE FOR IMPLEMENTATION IN A HYBRID ELECTRIC VEHICLE A Thesis Presented to The Graduate Faculty of The University of Akron In Partial Fulfillment of the Requirements for the Degree Masters of Science Charles Van Horn August, 2006 STEADY STATE AND TRANSIENT EFFICIENCIES OF A FOUR CYLINDER DIRECT INJECTION DIESEL ENGINE FOR IMPLEMENTATION IN A HYBRID ELECTRIC VEHICLE Charles Van Horn Thesis Approved: Accepted: Advisor Department Chair Dr. Scott Sawyer Dr. Celal Batur Faculty Reader Dean of the College Dr. Richard Gross Dr. George K. Haritos Faculty Reader Dean of the Graduate School Dr. Iqbal Husain Dr. George R. Newkome Date ii ABSTRACT The efficiencies of a four cylinder direct injection diesel engine have been investigated for the implementation in a hybrid electric vehicle (HEV). The engine was cycled through various operating points depending on the power and torque requirements for the HEV. The selected engine for the HEV is a 2005 Volkswagen 1.9L diesel engine. The 2005 Volkswagen 1.9L diesel engine was tested to develop the steady-state engine efficiencies and to evaluate the transient effects on these efficiencies. The peak torque and power curves were developed using a water brake dynamometer. Once these curves were obtained steady-state testing at various engine speeds and powers was conducted to determine engine efficiencies. Transient operation of the engine was also explored using partial throttle and variable throttle testing. The transient efficiency was compared to the steady-state efficiencies and showed a decrease from the steady- state values. -
MANUAL Kohler 1000 DIESEL Kohler 750 EFI Intimidator 800
2017 OWNER’S MANUAL Kohler 1000 DIESEL Kohler 750 EFI Intimidator 800 UTVRevised 10/18/2017 Owner Memo Name: ____________________________________ Purchasing Date: ____________________________ Type: _____________________________________ Pin Number: _______________________________ Special Notice: _____________________________ Key Number: _______________________________ PAGE 2 OWNER’S MANUAL Table of Contents: Title ........................... Page Number Introduction ......................................................Page 4 Definitions ........................................................Page 4 Safety Labels ...............................................Pages 4-8 ROPS Inspection Guide .............................Pages 9-10 General Safety ..........................................Pages 11-14 Safe Riding Gear .............................................Page 15 Features, Controls and Operation ............Pages 16-33 New Vehicle Break-in ......................................Page 33 Service and Maintenance .........................Pages 34-71 Storing and Maintaining Appearance .......Pages 72-73 Transporting your Intimidator .........................Page 74 Accessories ....................................................Page 74 Specifications ......................................... Pages 75-83 Troubleshooting ...................................... Pages 84-89 Warranties .............................................. Pages 90-99 Service Record .................................... Pages 100-101 Training Certificate ........................................Page -
Benchmarking a 2018 Toyota Camry 2.5L Atkinson Cycle Engine With
Downloaded from SAE International by John Kargul, Thursday, April 04, 2019 2019-01-0249 Published 02 Apr 2019 Benchmarking a 2018 Toyota Camry 2.5-Liter INTERNATIONAL. Atkinson Cycle Engine with Cooled-EGR John Kargul, Mark Stuhldreher, Daniel Barba, Charles Schenk, Stanislav Bohac, Joseph McDonald, and Paul Dekraker US Environmental Protection Agency Josh Alden Southwest Research Institute Citation: Kargul, J., Stuhldreher, M., Barba, D., Schenk, C. et al., “Benchmarking a 2018 Toyota Camry 2.5-Liter Atkinson Cycle Engine with Cooled-EGR,” SAE Technical Paper 2019-01-0249, 2019, doi:10.4271/2019-01-0249. Abstract idle, low, medium, and high load engine operation. Motoring s part of the U.S. Environmental Protection Agency’s torque, wide open throttle (WOT) torque and fuel consumption (EPA’s) continuing assessment of advanced light-duty are measured during transient operation using both EPA Tier Aautomotive technologies in support of regulatory and 2 and Tier 3 test fuels. Te design and performance of this 2018 compliance programs, a 2018 Toyota Camry A25A-FKS 2.5-liter engine is described and compared to Toyota’s published 4-cylinder, 2.5-liter, naturally aspirated, Atkinson Cycle engine data and to EPA’s previous projections of the efciency of an with cooled exhaust gas recirculation (cEGR) was bench- Atkinson Cycle engine with cEGR. The Brake Thermal marked. Te engine was tested on an engine dynamometer Efciency (BTE) map for the Toyota A25A-FKS engine shows with and without its 8-speed automatic transmission, and with a peak efciency near 40 percent, which is the highest value of the engine wiring harness tethered to a complete vehicle parked any publicly available map for a non-hybrid production gasoline outside of the test cell. -
Sae 2019-01-0249
Downloaded from SAE International by John Kargul, Friday, May 29, 2020 2019-01-0249 Published 02 Apr 2019 Benchmarking a 2018 Toyota Camry 2.5-Liter INTERNATIONAL. Atkinson Cycle Engine with Cooled-EGR John Kargul, Mark Stuhldreher, Daniel Barba, Charles Schenk, Stanislav Bohac, Joseph McDonald, and Paul Dekraker US Environmental Protection Agency Josh Alden Southwest Research Institute Citation: Kargul, J., Stuhldreher, M., Barba, D., Schenk, C. et al., “Benchmarking a 2018 Toyota Camry 2.5-Liter Atkinson Cycle Engine with Cooled-EGR,” SAE Int. J. Advances & Curr. Prac. in Mobility 1(2):601-638, 2019, doi:10.4271/2019-01-0249. This article was presented at WCXTM19, Detroit, MI, April 9-11, 2019. Abstract idle, low, medium, and high load engine operation. Motoring s part of the U.S. Environmental Protection Agency’s torque, wide open throttle (WOT) torque and fuel consumption (EPA’s) continuing assessment of advanced light-duty are measured during transient operation using both EPA Tier Aautomotive technologies in support of regulatory and 2 and Tier 3 test fuels. Te design and performance of this 2018 compliance programs, a 2018 Toyota Camry A25A-FKS 2.5-liter engine is described and compared to Toyota’s published 4-cylinder, 2.5-liter, naturally aspirated, Atkinson Cycle engine data and to EPA’s previous projections of the efciency of an with cooled exhaust gas recirculation (cEGR) was bench- Atkinson Cycle engine with cEGR. The Brake Thermal marked. Te engine was tested on an engine dynamometer Efciency (BTE) map for the Toyota A25A-FKS engine shows with and without its 8-speed automatic transmission, and with a peak efciency near 40 percent, which is the highest value of the engine wiring harness tethered to a complete vehicle parked any publicly available map for a non-hybrid production gasoline outside of the test cell. -
Hybrid Electric Vehicles: a Review of Existing Configurations and Thermodynamic Cycles
Review Hybrid Electric Vehicles: A Review of Existing Configurations and Thermodynamic Cycles Rogelio León , Christian Montaleza , José Luis Maldonado , Marcos Tostado-Véliz * and Francisco Jurado Department of Electrical Engineering, University of Jaén, EPS Linares, 23700 Jaén, Spain; [email protected] (R.L.); [email protected] (C.M.); [email protected] (J.L.M.); [email protected] (F.J.) * Correspondence: [email protected]; Tel.: +34-953-648580 Abstract: The mobility industry has experienced a fast evolution towards electric-based transport in recent years. Recently, hybrid electric vehicles, which combine electric and conventional combustion systems, have become the most popular alternative by far. This is due to longer autonomy and more extended refueling networks in comparison with the recharging points system, which is still quite limited in some countries. This paper aims to conduct a literature review on thermodynamic models of heat engines used in hybrid electric vehicles and their respective configurations for series, parallel and mixed powertrain. It will discuss the most important models of thermal energy in combustion engines such as the Otto, Atkinson and Miller cycles which are widely used in commercial hybrid electric vehicle models. In short, this work aims at serving as an illustrative but descriptive document, which may be valuable for multiple research and academic purposes. Keywords: hybrid electric vehicle; ignition engines; thermodynamic models; autonomy; hybrid configuration series-parallel-mixed; hybridization; micro-hybrid; mild-hybrid; full-hybrid Citation: León, R.; Montaleza, C.; Maldonado, J.L.; Tostado-Véliz, M.; Jurado, F. Hybrid Electric Vehicles: A Review of Existing Configurations 1. Introduction and Thermodynamic Cycles. -
RECIPROCATING ENGINES Franck Nicolleau
RECIPROCATING ENGINES Franck Nicolleau To cite this version: Franck Nicolleau. RECIPROCATING ENGINES. Master. RECIPROCATING ENGINES, Sheffield, United Kingdom. 2010, pp.189. cel-01548212 HAL Id: cel-01548212 https://hal.archives-ouvertes.fr/cel-01548212 Submitted on 27 Jun 2017 HAL is a multi-disciplinary open access L’archive ouverte pluridisciplinaire HAL, est archive for the deposit and dissemination of sci- destinée au dépôt et à la diffusion de documents entific research documents, whether they are pub- scientifiques de niveau recherche, publiés ou non, lished or not. The documents may come from émanant des établissements d’enseignement et de teaching and research institutions in France or recherche français ou étrangers, des laboratoires abroad, or from public or private research centers. publics ou privés. Distributed under a Creative Commons Attribution - NonCommercial| 4.0 International License Mechanical Engineering - 14 May 2010 -1- UNIVERSITY OF SHEFFIELD Department of Mechanical Engineering Mappin street, Sheffield, S1 3JD, England RECIPROCATING ENGINES Autumn Semester 2010 MEC403 - MEng, semester 7 - MEC6403 - MSc(Res) Dr. F. C. G. A. Nicolleau MD54 Telephone: +44 (0)114 22 27700. Direct Line: +44 (0)114 22 27867 Fax: +44 (0)114 22 27890 email: F.Nicolleau@sheffield.ac.uk http://www.shef.ac.uk/mecheng/mecheng cms/staff/fcgan/ MEng 4th year Course Tutor : Pr N. Qin European and Year Abroad Tutor : C. Pinna MSc(Res) and MPhil Course Director : F. C. G. A. Nicolleau c 2010 F C G A Nicolleau, The University of Sheffield -2- Combustion engines Table of content -3- Table of content Table of content 3 Nomenclature 9 Introduction 13 Acknowledgement 16 I - Introduction and Fundamentals of combustion 17 1 Introduction to combustion engines 19 1.1 Pistonengines.................................. -
9914 the Manufacturability of the Rotapower® Engine
9914 The Manufacturability of the Rotapower® Engine Paul S. Moller, Ph.D. Freedom Motors Freedom Motors 1855 N 1st St., Suite B Dixon, CA 95620 www.freedom-motors.com All rights reserved. © 2018. No part of this publication may be reproduc ed, stored in a retrieval system, or transmitted in any form or by any means, electronic, mechanical, photocopying, and recording or otherwise without the prior written permission of the authors. 9914 The Manufacturability of the Rotapower® Engine Paul S. Moller, Ph.D. Freedom Motors ABSTRACT introduced their rotary powered Evinrude RC-35-Q and Johnson Phantom snowmobiles. There are many elements of the charge cooled Wankel type rotary engine that make it inexpensive OMC also investigated liquid cooled housing marine to produce. OMC was able to show that they could models. OMC’s four rotor outboards raced six produce this type of engine at a cost competitive times in the summer and fall of 1973, winning every with their carbureted two-stroke engines. race in U class (unlimited). At the Galveston Speed Classic, they placed 1 st, 2nd and 3rd, lapping the THE PRODUCTION CHARGE COOLED WANKEL entire field three times (a fourth OMC boat rolled). WAS FIRST INTRODUCED AS A POTENTIALLY It was rumored that they once made a straightaway CLEAN, LOW COST, POWERFUL REPLACEMENT pass at 165 mph. FOR TW O-STROKES. THE CHARGE-COOLED ROTOR WANKEL TYPE In the late 60’s Outboard Marine Corporation ENGINE HAS A LOW PART COUNT (OMC) recognized the market value of an advanced, more powerful engine. This interest was When choosing an engine for a particular intensified by a growing concern that emission application or comparing the part count between issues would necessitate a clean burning, engines, the required power and torque environmentally friendly powerplant. -
Efficiency of Atkinson Engine at Maximum Power Density Using Temperature Dependent Specific Heats
Volume 2, Number 2, Jun. 2008 ISSN 1995-6665 JJMIE Pages 71 - 75 Jordan Journal of Mechanical and Industrial Engineering Efficiency of Atkinson Engine at Maximum Power Density using Temperature Dependent Specific Heats A. Al-Sarkhi, B. Akash *, E. Abu-Nada and I. Al-Hinti Department of Mechanical Engineering, Hashemite University, Zarqa, 13115, Jordan Abstract Thermodynamic analysis of an ideal air-standard Atkinson cycle with temperature dependant specific heat is presented in this paper. The paper outlines the effect of maximizing power density on the performance of the cycle efficiency. The power density is defined as the ratio of the power output to the maximum cycle specific volume. It showed significant effect on the performance of the cycle over the constant specific heat model. The results obtained from this work can be helpful in the thermodynamic modeling and in the evaluation of real Atkinson engines over other engines. © 2008 Jordan Journal of Mechanical and Industrial Engineering. All rights reserved Keywords: Atkinson engine; power density; temperature dependant specific heat; specific heats of air (the working fluid) were used. The maximization of the power density is defined as the ratio 1. Introduction of the maximum power to the maximum specific volume in the cycle. It takes into consideration the engine size The Atkinson cycle (the complete expansion cycle) is instead of just maximizing its power output. The inclusion named after its inventor James Atkinson in 1882 [1]. As of the engine size in the calculation of its performance is a shown in Fig. 1, the cycle involves isentropic compression very important factor from an economical point of view. -
Numerical Analysis on Combustion Characteristic of Leaf Spring Rotary Engine
Energies 2015, 8, 8086-8109; doi:10.3390/en8088086 OPEN ACCESS energies ISSN 1996-1073 www.mdpi.com/journal/energies Article Numerical Analysis on Combustion Characteristic of Leaf Spring Rotary Engine Yan Zhang, Zhengxing Zuo and Jinxiang Liu * School of Mechanical Engineering, Beijing Institute of Technology, Beijing 100081, China; E-Mails: [email protected] (Y.Z.); [email protected] (Z.Z.) * Author to whom correspondence should be addressed; E-Mail: [email protected]; Tel./Fax: +86-10-6891-1392. Academic Editors: Paul Stewart and Chris Bingham Received: 19 March 2015 / Accepted: 17 July 2015 / Published: 4 August 2015 Abstract: The purpose of this paper is to investigate combustion characteristics for rotary engine via numerical studies. A 3D numerical model was developed to study the influence of several operative parameters on combustion characteristics. A novel rotary engine called, “Leaf Spring Rotary Engine”, was used to illustrate the structure and principle of the engine. The aims are to (1) improve the understanding of combustion process, and (2) quantify the influence of rotational speed, excess air ratio, initial pressure and temperature on combustion characteristics. The chamber space changed with crankshaft rotation. Due to the complexity of chamber volume, an equivalent modeling method was presented to simulate the chamber space variation. The numerical simulations were performed by solving the incompressible, multiphase Unsteady Reynolds-Averaged Navier–Stokes Equations via the commercial code FLUENT using a transport equation-based combustion model; a realizable turbulence model and finite-rate/eddy-dissipation model were used to account for the effect of local factors on the combustion characteristics. -
Generation of Entropy in Spark Ignition Engines
Int. J. of Thermodynamics ISSN 1301-9724 Vol. 10 (No. 2), pp. 53-60, June 2007 Generation of Entropy in Spark Ignition Engines Bernardo Ribeiro, Jorge Martins*, António Nunes Universidade do Minho, Departamento de Engenharia Mecânica 4800-058 Guimarães PORTUGAL [email protected] Abstract Recent engine development has focused mainly on the improvement of engine efficiency and output emissions. The improvements in efficiency are being made by friction reduction, combustion improvement and thermodynamic cycle modification. New technologies such as Variable Valve Timing (VVT) or Variable Compression Ratio (VCR) are important for the latter. To assess the improvement capability of engine modifications, thermodynamic analysis of indicated cycles of the engines is made using the first and second laws of thermodynamics. The Entropy Generation Minimization (EGM) method proposes the identification of entropy generation sources and the reduction of the entropy generated by those sources as a method to improve the thermodynamic performance of heat engines and other devices. A computer model created and implemented in MATLAB Simulink was used to simulate the conventional Otto cycle and the various processes (combustion, free expansion during exhaust, heat transfer and fluid flow through valves and throttle) were evaluated in terms of the amount of the entropy generated. An Otto cycle, a Miller cycle (over-expanded cycle) and a Miller cycle with compression ratio adjustment are studied using the referred model in order to evaluate the amount of entropy generated in each cycle. All cycles are compared in terms of work produced per cycle. Keywords: IC engines, Miller cycle, entropy generation, over-expanded cycle 1.