Final Report RO-2017-101: Signal Passed at Danger 'A' at Compulsory
Total Page:16
File Type:pdf, Size:1020Kb
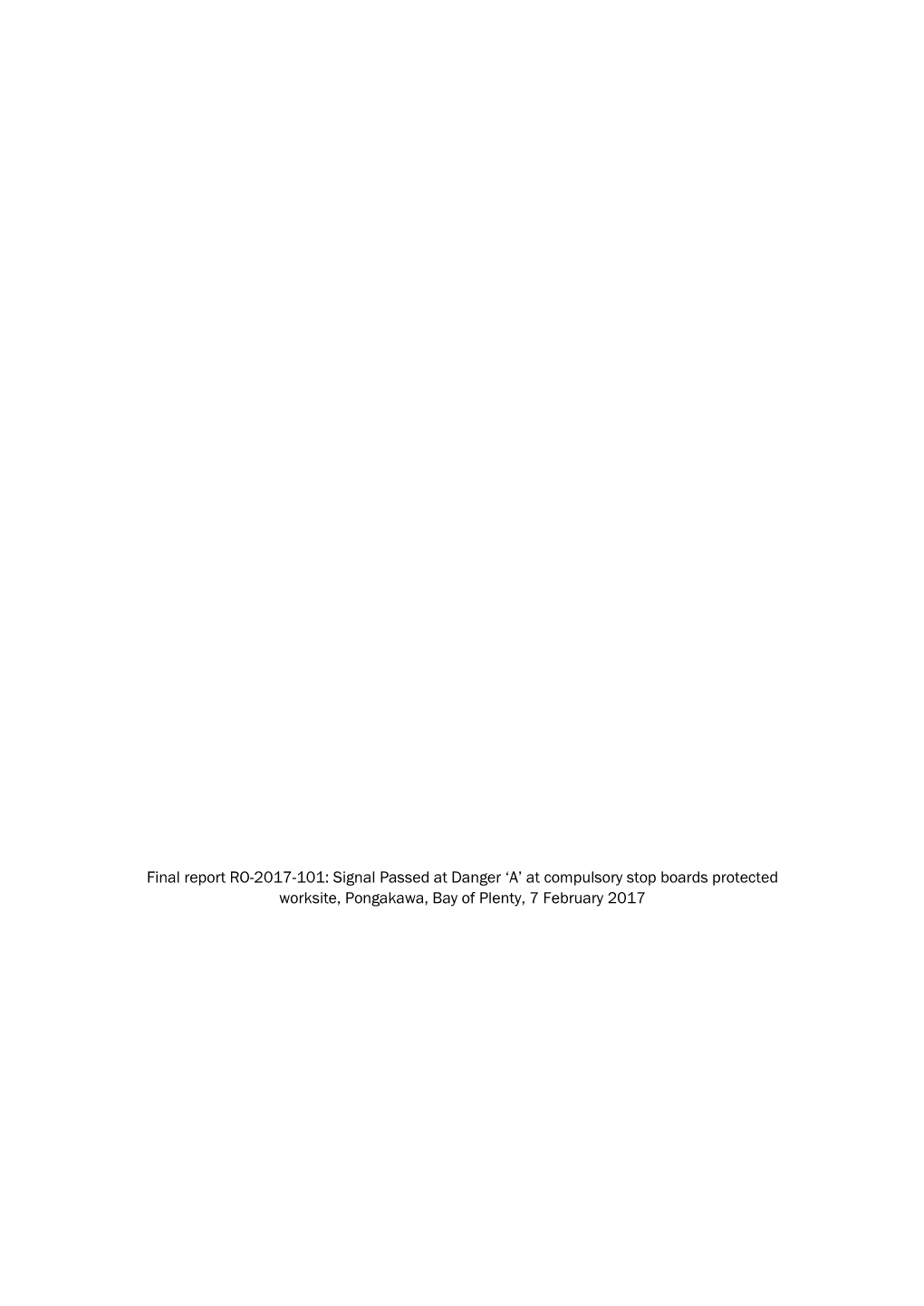
Load more
Recommended publications
-
Auckland Open Day the Strand Railway Station, Ngaoho Place, Parnell 10Am – 4Pm, Sunday 29 September 2013
Auckland Open Day The Strand Railway Station, Ngaoho Place, Parnell 10am – 4pm, Sunday 29 September 2013 Media contact: Kimberley Brady (021) 942 519 COME AND SEE: • The Exhibition Express - Jump into the drivers seat of a KiwiRail locomotive and talk with the locomotive engineer (train driver) - Get on board our new KiwiRail Scenic passenger carriages - Discover the amazing achievements of our early rail builders in our Moving through the Times display - Enjoy an experiential journey in our Moving Experience display - Learn more about the way rail Moves the Economy - Find out about the importance of Moving Safely and Responsibly when near rail • Career Opportunities - Talk with our Human Resources team about the many job opportunities that exist in KiwiRail, KiwiRail Scenic, Interislander, and KiwiRail Freight • Safety Awareness - Talk with our Safety Team about keeping safe near the track • Heritage trains on show - Take a look back in time by viewing Mainline Steam’s Ja1275, which will be on display. OTHER ACTIVITIES: Calling all Aucklanders to do ‘The Loco...motion!’ We want to rock Auckland with the largest locomotion dance ever seen! We loved it when Kylie did it – now it’s your turn. Bust out your 80s party moves, put on your dancing shoes and join in the fun! Join the ZM Black Thunders at KiwiRail “Keeping NZ on the Move” Exhibition Express open day at 11:30am and do the Locomotion. Don’t be a-freight! The Exhibition Express Prize Draw The prize of a return journey aboard KiwiRail Scenic’s Northern Explorer service for a family (2 adults and 3 children) will be drawn at the Open Day. -
Bay of Plenty Region Passenger and Freight Rail FINAL Report May 2019
1 | P a g e Bay of Plenty Passenger and Freight Rail Phase 1 Investigation Report May 2019 Contents Page Contents Page ......................................................................................................................................... 2 1.0 Introduction ................................................................................................................................ 4 2.0 Overall Findings and Future Opportunities ................................................................................. 6 2.1 Overall Findings ....................................................................................................................... 6 2.2 Future Opportunities ............................................................................................................ 10 3.0 Bay of Plenty Passenger and Freight Rail Investigation 2019 ................................................... 13 3.1 Phase 1 Investigation ............................................................................................................ 13 3.2 Stakeholders / Partners ........................................................................................................ 13 3.3 New Zealand Transport Agency Business Case Approach .................................................... 14 3.4 Bay of Plenty Rail Strategy 2007 ........................................................................................... 14 4.0 National Strategy and Policy Settings ...................................................................................... -
Delivering Rail Decarbonisation to New Zealand
Delivering rail decarbonisation to New Zealand TRANSFORMATIONAL CHANGE AND BOLD DECISIONS REQUIRED TO DELIVER A DECARBONISED RAIL NETWORK IN NEW ZEALAND. 1 Introduction ........................................................................................................3 Contents 2 Challenges ............................................................................................................4 3 Opportunity .........................................................................................................7 4 Conclusion ............................................................................................................9 PAGE | 2 WSP | 01 | 02 | 03 | 04 | 01 Introduction Angus Gabara, Principal Rail and Transit Advisory Here, KiwiRail has embarked on a study to understand WSP NZ Rail and Transit discipline, describes the the costs of completing the electrification partos of the transformational change and bold decisions required network including: to deliver a decarbonised rail network in Aotearoa, • the North Island Main Trunk Line between Auckland New Zealand. and Wellington, At the end of 2020, with mounting pressure to affect • the East Coast Main Trunk to Tauranga, change that delivers its carbon reduction goal, the Labour Government declared a climate emergency • the Wairarapa line to Masterton for New Zealand. The transport industry’s response to Electrification will be a huge step towards this emergency is pivotal and the rail industry is no decarbonisation, and provide efficient and safe exception. intercity -
Mahere Waka Whenua Ā-Rohe Regional Land Transport Plan 2021 - 2031
Mahere Waka Whenua ā-rohe Regional Land Transport Plan 2021 - 2031 1 Mahere Waka Whenua ā-rohe Regional Land Transport Plan - 2021-2031 AUTHOR SERVICE CENTRES Horizons Regional Transport Committee, Kairanga which includes: Cnr Rongotea and Kairanga -Bunnythorpe Roads, Horizons Regional Council Palmerston North Marton Horowhenua District Council 19 Hammond Street Palmerston North City Council Taumarunui Manawatū District Council 34 Maata Street Whanganui District Council REGIONAL HOUSES Tararua District Council Palmerston North Rangitīkei District Council 11-15 Victoria Avenue Ruapehu District Council Whanganui 181 Guyton Street Waka Kotahi NZ Transport Agency New Zealand Police (advisory member) DEPOTS KiwiRail (advisory member) Taihape Torere Road, Ohotu Road Transport Association NZ (advisory member) Woodville AA road users (advisory member) 116 Vogel Street Active transport/Public transport representative (advisory member) CONTACT 24 hr freephone 0508 800 800 [email protected] www.horizons.govt.nz Report No: 2021/EXT/1720 POSTAL ADDRESS ISBN 978-1-99-000954-9 Horizons Regional Council, Private Bag 11025, Manawatū Mail Centre, Palmerston North 4442 Rārangi kaupapa i Table of contents He Mihi Nā Te Heamana - Introduction From The Chair 02 Rautaki Whakamua - Strategic Context And Direction 03 1 He kupu whakataki - Introduction 04 1.1 Te whāinga o te Mahere / Purpose of the Plan 05 Te hononga o te Mahere Waka Whenua ā-Rohe ki ētahi atu rautaki - Relationship of the Regional Land Transport Plan to other 1.2 06 strategic documents 2 Horopaki -
IN the MATTER of the Resource Management Act 1991 and in THE
IN THE MATTER of the Resource Management Act 1991 AND IN THE MATTER of a Board of Inquiry appointed under section 149J of the Resource Management Act 1991 to consider a Plan Change Request by Tainui Group Holdings Limited and Chedworth Properties Limited. STATEMENT OF EVIDENCE OF DAVID GORDON FOR KIWIRAIL HOLDINGS LIMITED 26 MARCH 2014 STATEMENT OF EVIDENCE OF DAVID GORDON ON BEHALF OF KIWIRAIL HOLDINGS LIMITED 1. INTRODUCTION Qualifications and experience 1.1 My full name is David Stuart Gordon. 1.2 I am the General Manager Network Performance for KiwiRail Holdings Limited (“KiwiRail”), and am authorised to present this evidence on behalf of KiwiRail. The specific accountabilities within my portfolio relevant to this evidence are: (a) Network Planning and Capital Budgeting; (b) Access Rights and Network Control Services; (c) Asset Management Planning; and (d) Resource Management Act Planning. 1.3 I have been involved in the rail business either as a contractor or employee for 14 years. 1.4 I have a BA and Diploma of Town Planning, although I have never practised as a planner and make no claims to be an expert in that discipline. 1.5 Given my evidence touches on noise it may also be relevant that I have had some exposure to noise issues in my previous employment. I was the Planning and Development Manager for Wellington International Airport Limited in the 1990’s with RMA responsibility when innovations such as the air noise boundary, and Noise Management Plans were introduced. However I make no claims to be an expert in noise matters. -
Wiri to Westfield the Case for Investment
Wiri to Westfield The Case for Investment WSP | Parsons Brinckerhoff DECEMBER 2016 Wiri to Westfield (W2W) – The Case for Investment CONTENTS Executive Summary ............................................................................................................................................... E PART A – THE CASE FOR THE PROJECT ....................................................................................................... 8 1 Introduction ...................................................................................................................................................... 8 1.1 Background ...................................................................................................................... 8 1.2 Developed in Collaboration............................................................................................. 8 2 Strategic Context ........................................................................................................................................ 11 2.1 National Context ............................................................................................................ 11 2.2 W2W A Major Constraint in the National Network ...................................................... 11 2.3 Regional Context ........................................................................................................... 12 W2W Rail Network .................................................................................................................. 12 Strategic Road Network -
Single Stage Business Case Hamilton to Auckland Start-Up
SINGLE STAGE BUSINESS CASE HAMILTON TO AUCKLAND START-UP PASSENGER RAIL SERVICE PREPARED FOR WAIKATO REGIONAL COUNCIL November 2018 HAMILTON TO AUCKLAND PASSENGER SERVICE SSBC This document has been prepared for the benefit of the Waikato Regional Council. No liability is accepted by this company or any employee or sub-consultant of this company with respect to its use by any other person. This disclaimer shall apply notwithstanding that the report may be made available to other persons for an application for permission or approval to fulfil a legal requirement. QUALITY STATEMENT PROJECT MANAGER PROJECT TECHNICAL LEAD Andrew Maughan Doug Weir PREPARED BY Andrew Maughan, Doug Weir, Sarah Loynes, Shaun Bosher CHECKED BY Andrew Maughan REVIEWED BY Phil Peet APPROVED FOR ISSUE BY Andrew Maughan 9/11/2018 HAMILTON 468 Tristram Street, Whitiora, Hamilton 3200 PO Box 13-052, Armagh, Christchurch 8141 TEL +64 7 839 0241, FAX +64 7 839 4234 Stantec │ Hamilton to Auckland Start-Up Passenger Rail Service │ November 2018 Status: Final │ Project No.: 80510468 │ Our ref: Single Stage BC Master Report FINAL_TIO HAMILTON TO AUCKLAND PASSENGER SERVICE SSBC REVISION SCHEDULE Signature or Typed Name (documentation on file) Rev Date Description No. Prepared Checked Reviewed Approved by by by by 1 31/8/18 Draft one AM, PP, SL, 2 4/9/18 Draft for client review AM PP AM DW 3 7/9/18 Draft for client review AM, DW AM PP AM 4 11/9/18 Draft for TCWG Review AM, DW AM PP AM 5 12/9/18 TIO Submission AM, DW AM AM AM 6 19/10/18 Review document SB SB Working draft for -
Kiwirail Auckland Metro Programme Urgent Track Repairs August 2020
KIWIRAIL AUCKLAND METRO PROGRAMME URGENT TRACK REPAIRS AUGUST 2020 WHAT IS THE AUCKLAND METRO RAIL areas – such as the Wellington metro network and PROGRAMME? on the East Coast Main Trunk between Hamilton and Tauranga. KiwiRail’s $1 billion Auckland Metro Programme is a suite of projects that will ease congestion in WHEN DID YOU FIRST BECOME AWARE OF the busiest parts of the network by building new track and a third main line, extend electrification THE ISSUE IN AUCKLAND AND WHAT HAS to Pukekohe, build new stations around Drury and BEEN DONE TO RESOLVE THIS? deliver city-wide renewals that will cut delays and All rail is subject to wear and tear, but we began make sure Auckland is ready for the City Rail Link. seeing a more widespread issue in Auckland Modernising the track and replacing worn rail is part around three years ago. In early 2018 we of this programme. established a technical working group with Auckland Transport to investigate the root causes WHAT HAS CAUSED THE ISSUE WITH THE and identify infrastructure and/or rolling stock WORN TRACKS? solutions. In 2019 we received additional funding from Rail track becomes worn over time as a result the Government that enabled us to take a more of usage, in the same way that road surfaces intensive approach to resolving this. deteriorate. Immediate actions included enhanced track One particular type of damage, Rolling Contact inspections and accelerated replacement of rail Fatigue (RCF), has become increasingly prevalent around the network, additional rail grinding and on the Auckland metro rail network. It occurs when the introduction of new testing technology to the stress created by contact between rail and the detect the extent of the issue. -
Names & Opening & Closing Dates of Railway Stations
Names & Opening & Closing Dates of Railway Stations in New Zealand 1863 to 2010 Researched & Written by Juliet Scoble for the Rail Heritage Trust of New Zealand JRS/291 © Juliet Scoble 4/2010 © Rail Heritage Trust of New Zealand 4/2010 Introduction This document lists the names of railway stations and the dates they were opened and closed. Included are the dates stations were opened for goods and or passenger traffic before the lines were officially opened or handed over to the Working Railways Department. Often the Public Works Department would run goods and passenger services whilst the list was still in their custody. These services were operated by the Public Works Department's ballast engine. Goods were carried in Working Railway's wagons. Occasionally a passenger car or covered wagon fitted with seats were provided, but most times passengers were carried in Public Works' ballast wagons. I have included the stations on the lines owned by the government railways, and private lines where government rolling stock was run thereon. This is an on-going work as I am still looking through files and am finding more names and other information to include in this document. Revised versions will be issued from time to time, the frequency depending upon the new information I find. Juliet Scoble 4/2010 Acknowledgements Most information has been obtained from the Rail Heritage Trust's Station Archive created and researched by Juliet Scoble, and from research specifically undertaken for this document. Additional information supplied by: Auckland -
Regional Rapid Rail Report
REGIONAL RAPID RAIL Upper North Island Passenger Network © Chris Gin WWW.GREATERAUCKLAND.ORG.NZ CONTENTS Contents ........................................................... 2 Executive Summary ................................................... 3 Next Steps .......................................................... 6 Introduction ......................................................... 7 What is Regional Rapid Rail? ........................................... 15 Regional Rapid Rail Stages ............................................. 18 Stage 1 ............................................................. 19 Stage 2 ............................................................. 24 Stage 3 ............................................................. 32 Integration With Freight and Urban Public Transport Networks ............. 39 Regional Development and Liveable Towns – Not Just a Rapid Train ......... 43 Frameworks for Implementation ....................................... 47 Conclusion .......................................................... 49 Frequently Asked Questions ........................................... 50 Appendix – Stage 1 Operating Plan and Cost Data ......................... 52 Appendix – Stage 2 Operating Plan and Cost Data ......................... 56 Appendix – Stage 3 Operating Plan and Cost Data ......................... 61 Written and developed by Greater Auckland with grateful assistance from many others Principal authors: Harriet Gale and Nicolas Reid Layout and document design: Cornelius Blank © 2017 Greater -
Kiwirail Holdings Limited 106919
BACKGROUND KiwiRail Holdings limited “KiwiRail” is the State Owned Enterprise responsible for the management and operation of the national rail network. This includes managing the national rail infrastructure and land as well as rail freight and passenger logistics within New Zealand. KiwiRail is also the Requiring Authority for land designated for “Railway Purposes” in District Plans throughout New Zealand. There are two rail lines within Hamilton City Council’s jurisdiction; the North Island Main Trunk Line and the East Coast Main Trunk Line. The North Island Main Trunk (NMIT) extends through the city in a north to south direction and is the primary rail spine for the entire North Island. The East Coast Main Trunk (EMCT) branches from the North Island Main Trunk at the Hamilton Railway Station, and heads east out of the city through the suburb of Ruakura. It provides the only rail access from the Bay of Plenty and Port of Tauranga to the North Island Main Trunk. The NIMT provides a rail freight and passenger link between Wellington and Auckland, while the ECMT provides a freight link between Hamilton and the Bay of Plenty, including the Port of Tauranga and the proposed Ruakura logistics hub. These lines are key strategic freight routes and as such are an important part of the KiwiRail network. SUBMISSION KiwiRail supports the development of a Regional and Golden Triangle Inter Modal Terminal (IMP) and the broad strategic direction on land and transport management set out in the Proposed Ruakura Plan Change. 2 We have liaised briefly with NZTA and AT on matters of mutual interest and our submissions also raise and/or addresses similar matters. -
Kiwirail Holdings Limited (Kiwirail)
18 December 2015 Hamilton City Council Private Bag 3010 HAMILTON 3240 By email to: [email protected] SUBMISSION ON PUBLICLY NOTIFIED PROPOSAL FOR PLAN, CHANGE OR VARIATION (FORM 5) Hamilton Proposed District Plan Variation 1: Ruakura- NAME OF SUBMITTER: KiwiRail Holdings Limited (KiwiRail) ADDRESS FOR SERVICE: Level 1 Wellington Railway Station Bunny Street PO Box 593 WELLINGTON 6140 Attention: Rebecca Beals Ph: 04 498 3389 Email: [email protected] KiwiRail Submissions on Proposed District Plan Variation: Ruakura KiwiRail Holdings Limited (KiwiRail) is the State Owned Enterprise responsible for the management and operation of the national railway network. This includes managing railway infrastructure and land, as well as rail freight and passenger services within New Zealand. KiwiRail Holdings Limited is also the Requiring Authority for land designated “Railway Purposes” (or similar) in District Plans throughout New Zealand. There are two rail lines within Hamilton City Council’s jurisdiction; the North Island Main Trunk Line and the East Coast Main Trunk Line. The North Island Main Trunk extends through the city in a north to south direction and is the primary rail spine for the entire North Island. The East Coast Main Trunk branches from the North Island Main Trunk at the Hamilton Railway Station, and heads east out of the city through the suburb of Ruakura. It provides the only rail access from the Bay of Plenty and Port of Tauranga to the North Island Main Trunk. KiwiRail Holdings Ltd | www.kiwirail.co.nz | Level 1, Wellington Railway Station, Bunny Street, Wellington 6011 PO Box 593, Wellington 6140, New Zealand | Phone 0800 801 070, Fax +64-4-473 1589 These lines are key freight routes and as such are an important part of the KiwiRail network.