The Third International Conference on Containment Design and Operation
Total Page:16
File Type:pdf, Size:1020Kb
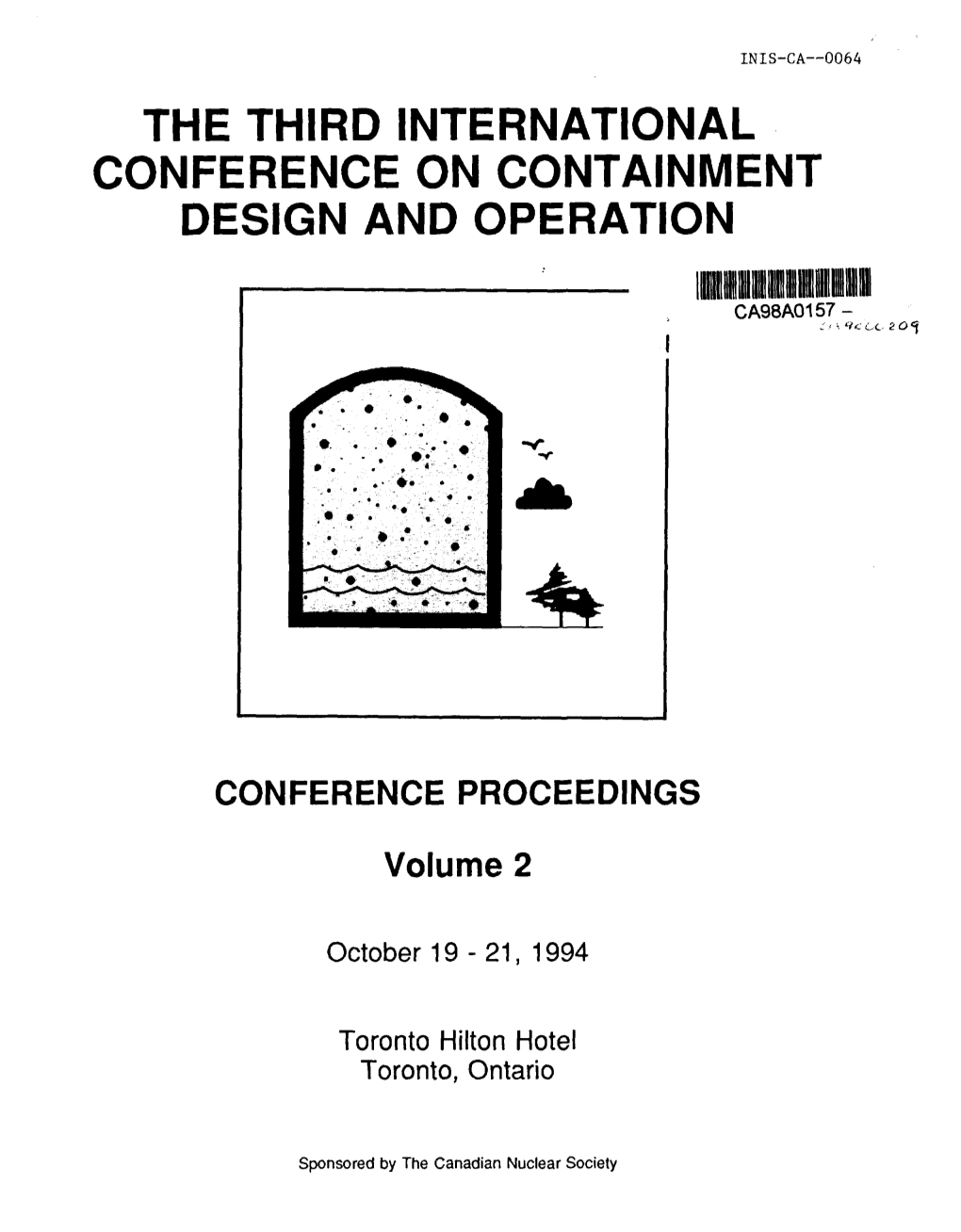
Load more
Recommended publications
-
Nuclear Energy and Environment
In Memoriam of Alain Bugat Alain Bugat, Honorary President of the National Academy of Technologies of France, former General Administrator of the Commissariat à l’Energie Atomique (CEA) and a staunch defender of nuclear energy, initiated the three-Academies collaboration on Nuclear energy. He had invested much time and effort in shaping this report, bringing together experts from the three academies and giving it credibility and excellence. To our great grief, he passed away in January 2019 at a time where the report was already at an advanced stage of completion. The memory of his energetic and charismatic personality rests in our minds. Nuclear Energy and the Environment A COLLABORATIVE PROGRAMME BETWEEN FRENCH and CHINESE ACADEMIES May 2019 Foreword This report on nuclear energy and the environment is jointly released by the Chinese Academy of Engineering, the National Academy of Technologies of France and the French Academy of sciences. It is a second collaborative study of the three academies on nuclear energy matters. The first report, issued in August 2017, covered many aspects of nuclear energy and offered joint, mostly technical, recommendations for the direction of nuclear energy in the future. It was an attempt to provide an objective overview of many scientific and technological issues on nuclear energy (its position in the future energy mix, benefits, strengths and weak points, research and development perspectives, technology and safety, engineering etc.), as well as societal issues (education, training, risk perception, public awareness etc.). But it was admittedly far from being exhaustive. Environmental issues were not considered in sufficient depth in the previous report despite their being crucial for the future of this industry, and the Academies felt it necessary to pursue their cooperation and further address these important issues. -
WRFPM 2014.Indd 1 14/09/04 18:05 SPONSORS
Official Program Westinghouse Electric Company LLC Westinghouse Electric Company LLC Westinghouse WRFPM 2014 NONO COMPANYCOMPANY ISIS 2014 Water Reactor Fuel Performance Meeting/ Top Fuel / LWR Fuel Performance Meeting SENDAI MOREMORE FOCUSEDFOCUSED ONON 14 -17 September 2014, FUELFUEL RELIABILITYRELIABILITY Sendai, Japan Sendai International Center – Pursuit of the world's highest level of safety – TOKYO Westinghouse’sWestinghouse’s robust robust fuel fuel designs designs and and proven proven performance performance makemake us us the the industry industry leader leader in in fuel fuel reliability. reliability. Leak-free Leak-free fuel fuel is is notnot only only an an industry industry goal, goal, it’s it’s also also Westinghouse’s Westinghouse’s mission. mission. ToTo learn learn more more about about fuel fuel reliability, reliability, visit visit us us at at www.westinghousewww.westinghousenuclearnuclear.com.com Sponsor Cosponsor In cooperation with IAEA WestinghouseWestinghouse @WECNuclear@WECNuclear ElectricElectric Company Company Supported by _WRFPM 2014.indd 1 14/09/04 18:05 SPONSORS Sponsor Atomic Energy Society of Japan Cosponsors Korean Nuclear Society, Chinese Nuclear Society, European Nuclear Society and American Nuclear Society In cooperation with IAEA Supported by Sendai Tourism & Convention Bureau 2 _WRFPM 2014.indd 2 14/09/04 18:05 ORGANIZERS Organizing Committee (Chair) Hideo ISHIBASHI The Japan Atomic Power Company Harunobu GODA Zirco Products Co., Ltd. Daisuke GOTO Global Nuclear Fuel - Japan Co., Ltd. Shinji IGARASHI Tokyo Electric Power Company Yuzo INABA Nuclear Fuel Industries, Ltd. Shuichi IWATA The Graduate School of Project Design Katsuichiro KAMIMURA Nuclear Regulation Authority Hiroshi KOBAYASHI Nuclear Development Corporation Mitsuhiro KODAMA Nippon Nuclear Fuel Development Co., Ltd. -
Energy Resources Climate OCTOBER 2013
record energy resources climate OCTOBER 2013 Chinese O&G firms ‘go global’ must rely on market forces rather than administrative fiat. MIIT issued new regulations to expedite consoli- China University of Petroleum’s Wang Zhen dation and structural upgrade—which should reduce 王震 announces Chinese O&G firms as the industry to five or six large firms. Irrational product globally competitive ‘state-owned multinationals’. Hu mixes, overreliance on exports, and unbalanced tech- 胡卫平 Weiping China Overseas Development Associ- nological development remain key structural prob- ation is less sanguine. Chinese O&G investments over- lems says Chinese consultants Zero Power Intelligence. seas are concentrated in politically unstable regions, They praise the new NDRC and MIIT industry support were recently acquired at high cost and lack technical policies, but caution that timely delivery of promised know how. Bilateral investment protection mecha- subsidies is key to the survival of many PV generators. nisms, greater familiarity with international laws and conventions, and coordinated government policies at Surviving the doldrums in wind power home would help. Curtailed wind power led to more than C¥10 Dependency on foreign oil—how much is too much? billion in economic losses in 2012. Xiamen University’s Lin Boqiang 林伯强 says grid inadequacies China must harness new technologies in cause over-capacity in northern wind-rich areas— extraction, energy saving, coal liquefac- better to restrict wind power installation where coal- tion and gasification, and renewable energy to reduce fired power dominates. Xinjiang Goldwind chairman oil dependency, says Xu Hongcai 徐洪才 China Centre Wu Gang 武钢 says the industry has been responsive for International Economic Exchanges. -
An Analysis of the U.S.-China Nuclear Energy Cooperation Agreement Benjamin M
Maryland Journal of International Law Volume 10 | Issue 2 Article 7 An Analysis of the U.S.-China Nuclear Energy Cooperation Agreement Benjamin M. Chin Follow this and additional works at: http://digitalcommons.law.umaryland.edu/mjil Part of the International Law Commons Recommended Citation Benjamin M. Chin, An Analysis of the U.S.-China Nuclear Energy Cooperation Agreement, 10 Md. J. Int'l L. 321 (1986). Available at: http://digitalcommons.law.umaryland.edu/mjil/vol10/iss2/7 This Notes & Comments is brought to you for free and open access by DigitalCommons@UM Carey Law. It has been accepted for inclusion in Maryland Journal of International Law by an authorized administrator of DigitalCommons@UM Carey Law. For more information, please contact [email protected]. NOTES AND COMMENTS AN ANALYSIS OF THE U.S.-CHINA NUCLEAR ENERGY COOPERATION AGREEMENT I. INTRODUCTION ................................... 321 II. BACKGROUND .................................... 323 A. China's Nuclear Policy ........................ 323 1. Developing Nuclear Capability ............. 323 2. China's Arm's Control and Non-proliferation P olicy ............ .................... 324 B. U.S. Nuclear Policy ........................... 327 III. HISTORY OF THE U.S.-CHINA NUCLEAR ENERGY COOP- ERATION AGREEMENT .............................. 328 IV. ANALYSIS OF STATUTORY COMPLIANCE FOR A NUCLEAR COOPERATION AGREEMENT ......................... 333 A. Section 123 Atomic Energy Act of 1954 ......... 333 1. A rticle 5 ................................ 335 a. Proponents........................... 336 b. Opponents ........................... 337 2. A rticle 8 ................................ 337 a. Proponents........................... 338 b. Opponents ........................... 338 3. Procedural Compliance and CongressionalRe- view .................................... 339 B. Section 129 Atomic Energy Act 1954 ............ 341 V. SUBSEQUENT MEASURES ..................... 341 A. Judicial Intervention - Cranston v. Reagan ...... 341 B. Legislative and Executive Intervention - U.S. -
Areva in China
PRESS KIT AREVA IN CHINA Press contact: Frédérique Michaux / Nicolas Hélas-Othenin Tel.: 00 86 10 85322300 Fax: 00 86 10 85324801 Julien Duperray Tel: 33.1.34.96.11.47 Fax: 33.1.34.96.16.54 [email protected] November 2007 2 CONTENTS Introduction page 2 China's need for energy page 4 Sources of China's energy mix page 6 The challenges of China's nuclear program page 14 AREVA - Supporting China's ambitious nuclear program page 18 Strong opportunities in renewable energy page 21 A high potential market for AREVA's T&D Division page 22 Main Acronyms and References page 25 1 INTRODUCTION China has a great need for secure, safe, and economic energy supplies that combat the greenhouse effect and global warming. Since January 2002, China, the most heavily populated country with more than 1.3 billion inhabitants in a territory of 9.5 million km2 (17 times larger than France), has a nuclear capacity of 9 GWe with 11 nuclear plants on line. Forecasts of electricity consumption report a need for 900 to 1,000 GWe per year through 2020, and at this time the country’s objective is to increase nuclear- generated electricity from 1% to 4% of its total output. This means a need for additional 30 GWe, which is the equivalent of twenty 1,500 MWe reactors. In addition to nuclear power, China is pushing renewable energy. With the passage of the 2005 Renewable Energy Law, China's government imposed a national renewable energy requirement that is expected to boost the use of renewable energy capacity from 10 to 12 percent by 2020, up from 3% in 2003. -
Proposal Czech-China Nuclear Partnership from Dynatom
STRICTLY CONFIDENTIAL PROPRIETY OF DYNATOM INTERNATIONAL GmbH Dynatom International GmbH The Establishment of the Czech -‐China Nuclear Partnership a. The HAF 604 barrier and its impact in the tenders ................................ ...................................... 3 b. Second challenge, the condition of the listing at the EPC ................................ ............................ 5 c. Government Policy and impact on localization rate................................ ..................................... 5 d. New entrants meet new challenges................................ .................................................................... 5 (i) The French Nuclear Industry the is still largest partner ................................ ........................................ 5 (ii) The Small and Medium Size Enterprise are not insistent ................................ ................................ 6 (iii) Cross Cultural issue ................................ ........................................................................................................... 7 a. Remodeling of the key players ................................ ............................................................................. 9 (iv) The lack of financial strength and lower margin ................................ ................................................. 7 b. International ambitions ................................ ......................................................................................... 9 c. Creating national champions -
Rating the Report on China Huaneng Group Sustainability Report 2011
About this Report: Time Covered Jan 01, 2011 – Dec 31, 2011. Where appropriate, the report includes A “red” company serving the needs of socialism with Chinese characteristics additional content and information that pre-dates the stated reporting period. A “green” company advocating technological innovation and environmental protection Reporting Cycle Our sustainability report is published annually, this being the sixth re- A “blue” company advancing via continuous innovation and internationalization port since 2006. Main Contents This report outlines our performance in 2011 on safety, environmental, economic and social issues. It includes information and typical cases from documents, statements and information platforms of the Com- pany and its grassroots-level enterprises. Persist in adhering to and serving national interests and development strategies, so as to set an example in promoting economic and social development in all respects. Compilation Conformance This report is compiled in accordance with the Guidelines on Perform- Persist in scientific development and technological innovation, so as to set an example in ing Social Responsibility by Central Enterprises released by the State- building a resource-conserving and environmentally-friendly society. owned Assets Supervision and Administration Commission (SASAC) of the State Council and in light of the Sustainability Reporting Guide- lines (G3.1) from the Global Reporting Initiative (GRI), Guidelines on Persist in pursuing operational performance in a rational way, so as to set -
Beautiful Huaneng in Action 08
About this Report Time Covered Jan 01, 2013 - Dec 31, 2013. Where appropriate, the report includes additional content and information that pre-dates the Declaration on Sustainable Development stated reporting period. Persist in serving national interests and development strategies, so as to set an Reporting Cycle example in promoting economic and social development in all respects. Our sustainability report is published annually, this being the eighth report since 2006. Main Contents Persist in scientific development and technological innovation, so as to set an This report outlines our performance in 2013 on safety, en- example in building a resource-conserving and environmentally-friendly society. vironmental, economic and social issues. It includes infor- mation and typical cases from documents, statements and Persist in pursuing operational performance in a rational way, so as to set an information platforms of the Company and its grassroots-level enterprises. example in promoting harmony between enterprises and society. Compilation Conformance Guidelines on Corporate Social Responsibility Reporting for Persist in relying on employees and working with the public to develop the en- Chinese Enterprises (CASS-CSR 3.0) terprise so as to set an example in putting people first and sharing benefits. The Sustainability Reporting Guidelines (G4) from the Global Reporting Initiative (GRI) Persist in contributing to society and benefiting the people, so as to set an ex- ISO 26000: Guidance on Social Responsibility Guidelines on Social Responsibilities of Chinese Industrial ample in practicing social ethics. Enterprises and Industrial Associations References to China Huaneng Group In this report, “Huaneng Group”, “Huaneng”, “the Company” and “we” refer to the “China Huaneng Group”. -
Glossary of Abbreviations and Acronyms
This Glossary has not been updated since 2015-03-24. Glossary of Abbreviations and Acronyms A A activity A adenine A ampere [unit of electric current] Å angstrom a atto [prefix for SI and metric units, 10-18] a year A1 maximum activity of special form radioactive (IAEA Transport material that can be transported in a Type A Regulations) package A2 maximum activity of any radioactive material other (IAEA Transport than special form radioactive material that can be Regulations) transported in a Type A package AAA awareness, appropriateness and audit AAAID Arab Authority for Agricultural Investment and Development AAA Program Advanced Accelerator Applications Program [In (USA) 2003 this developed into the Advanced Fuel Cycle Initiative (AFCI).] AAAS American Association for the Advancement of Science AAB Audit Advisory Board (India) AAC Austrian Accreditation Council AACB Association of African Central Banks AACR Anglo–American Cataloguing Rules AADFI Association of African Development Finance Institutions AAEA Arab Atomic Energy Agency AAEC Australian Atomic Energy Commission [This was replaced in 1987 by the Australian Nuclear Science and Technology Organisation (ANSTO).] AAEE American Academy of Environmental Engineers (USA) AAEHC Afghan Atomic Energy High Commission AAES American Association of Engineering Societies (USA) AAFICS Australian Association of Former International Civil Servants AAIS Austrian Accident Insurance Scheme (IAEA) - 1 - This Glossary has not been updated since 2015-03-24. Please check IAEAterm (http://iaeaterm.iaea.org) -
Global Engagement: Rethinking the Risk in the Research Enterprise
Global Engagement Global Engagement RETHINKING RISK IN THE RESEARCH ENTERPRISE Edited by GLENN TIFFERT H O O V E R I N S T I T U T I O N P R E S S stanford university stanford, california With its eminent scholars and world- renowned library and archives, the Hoover Institution seeks to improve the human condition by advancing ideas that promote economic opportunity and prosperity, while securing and safeguarding peace for Amer i ca and all mankind. The views expressed in its publications are entirely those of the authors and do not necessarily reflect the views of the staff, officers, or Board of Overseers of the Hoover Institution. hoover.org Hoover Institution Press Publication Hoover Institution at Leland Stanford Ju nior University, Stanford, California 94305-6003 Copyright © 2020 by the Board of Trustees of the Leland Stanford Ju nior University All rights reserved. No part of this publication may be reproduced, stored in a retrieval system, or transmitted in any form or by any means, electronic, mechanical, photocopying, recording, or other wise, without written permission of the publisher and copyright holders. First printing 2020 26 25 24 23 22 21 20 7 6 5 4 3 2 1 Manufactured in the United States of America Printed on acid-free, archival-quality paper CONTENTS Foreword vii H. R. McMaster Acknowledgments xv Introduction 1 Larry Diamond Executive Summary 5 1 Under the Radar: National Security Risk in US- China Scientific Collaboration 19 Jeffrey Stoff and Glenn Tiffert appendix to chapter 1 Sources and Methodologies 100 2 Global Engagement: A New Paradigm for Managing Risk 105 Kevin Gamache and Glenn Tiffert Contributors 141 Index 144 FOREWORD Under Chairman Xi Jinping, the Chinese Communist Party (CCP) has resolved to strengthen its grip on power, take center stage in the world, and make good on Xi’s pledge to lead the development of new rules and a new international order sympathetic to China’s interests. -
IYNC BULLETIN International Youth Nuclear Congress
IYNC BULLETIN International Youth Nuclear Congress March 2014 www.iync.org Asia Going Nuclear Editorial Bulletin: Asia Going Nuclear Dear IYNC community, The nuclear industry is growing in Asia where 49 nuclear power reac- tors are under construction. One of the main objectives of the 2012- 2014 term IYNC officers was to develop the IYNC network in this region. Besides our historic partners such as South Korea and Japan, IYNC has made great progress in extending its network to India and China. Those two countries have started their local YGN (Young Generation in Nu- clear) with the help of IYNC and are willing to be involved more in our activities and to take a significant place in the IYNC congress. China joined the IYNC Board last August. To start the cooperation, an IYNC delegation visited the country in November. Don’t miss the report of this historic trip in this bulletin. I’m currently working on the AP1000 construction site in Sanmen, China. It’s a great challenge and a unique opportunity. The nuclear industry offers great experience worldwide. Don’t miss them and travel while you’re young! Asia will also have an important contribution in our next congress in Burgos on July 6-12 2012. Top executives from China and South Korea have already confirmed their presence and we are close to confirm the presence of important speakers from Saoudi Arabia and India. Besides that, other important top executive have confirmed their presence to the congress like Mike Weightman (former ONR HM Chief Inspector), Ken Ellis (WANO Managing Director), Alejo Vidal-Quadras Roca (Europe- an Parlement Vice-President) and Danny Roderick (President and CEO of Westinghouse). -
Chinese Nuclear Society
Chinese Nuclear Society Invitation for International Summit on Nuclear Energy and Environment Development The International Summit on Nuclear Energy & Environment Development (ISNEED) will be held in Weihai, China from May 15 to 17, 2019, hosted by the Chinese Academy of Engineering in cooperation with Chinese Nuclear Society, French National Academy of Sciences and National Academy of Technologies. With support of the 2017 program (Program Phase-I), three academies (the Chinese Academy of Engineering, French Academy of Sciences, and National Academy of Technologies of France) from China and France jointly drafted a splendid report titled Joint Proposals On Future Of Nuclear Energy which received warm response after its release in the IAEA General Conference. In 2018, the three academies continued the cooperation to implement Program Phase-II and chose “nuclear energy and environment” as the topic of the joint research. The research deals with the central issue of the impact of nuclear energy on the environment considering all operations from uranium mining to radioactive waste disposal. The joint research results of the three academies Program Phase-II will be released on this summit. The summit will focus on the application of civil nuclear technology, the sustainable development of nuclear energy. The summit has invited experts from China, France, Russia, Japan, Sweden, Ukraine, IAEA and the other nuclear players in the world through Keynote session, plenary session, and Roundtable Discussion. The summit will bring new impetus to accelerating development of the world nuclear energy, enhancing influence of the nuclear industry and promoting more potential countries to realize nuclear power generation. Detailed information as follows: I.