Soyuz Crew Operations Manual (Soycom) (ROP-19) (Final)
Total Page:16
File Type:pdf, Size:1020Kb
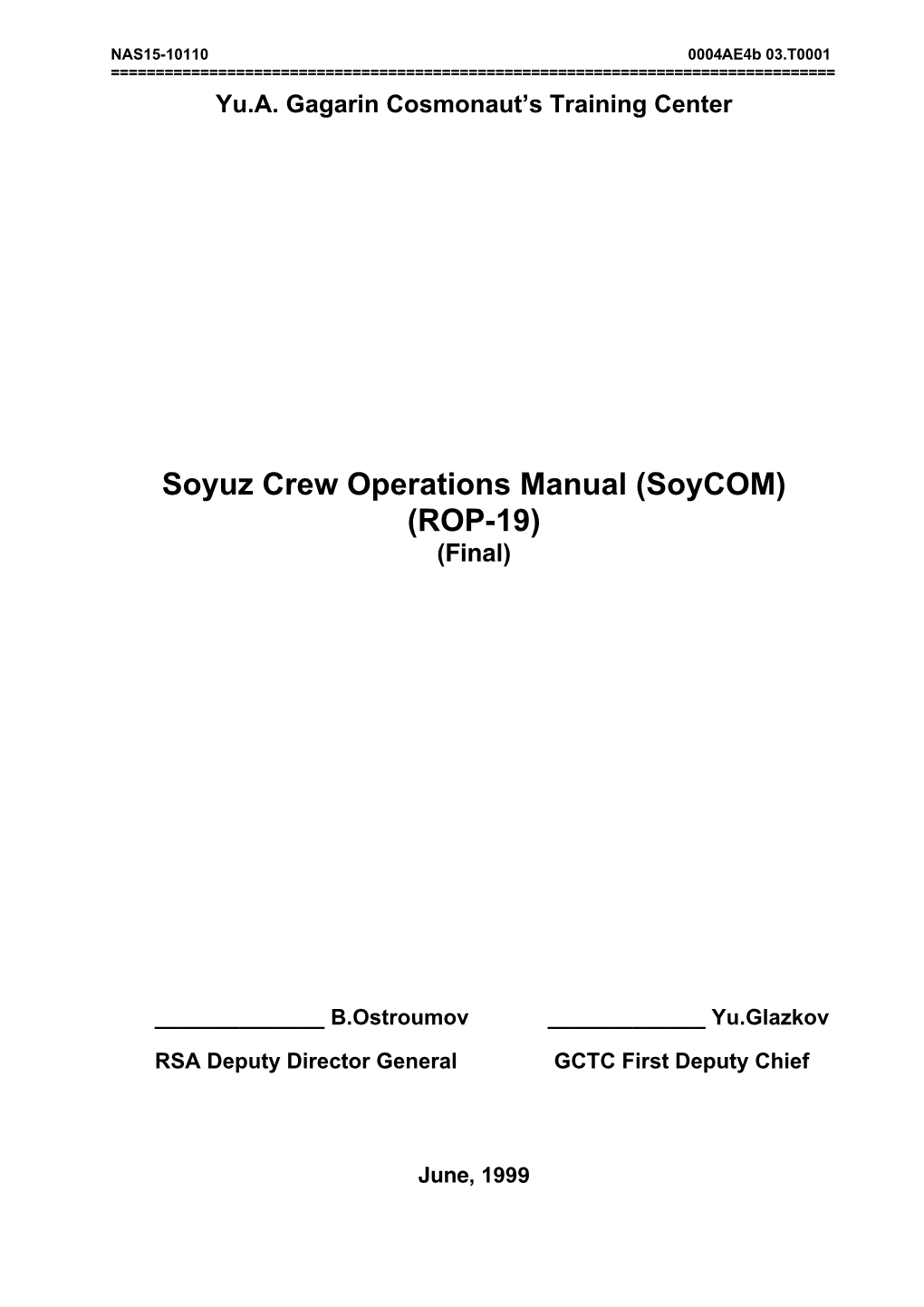
Load more
Recommended publications
-
ORION ORION a to Z APOGEE to Break the Frangible Joints and Separate the Fairings, Three Parachutes
National Aeronautics and Space Administration ORION www.nasa.gov ORION A to Z APOGEE to break the frangible joints and separate the fairings, three parachutes. The next two parachutes will then VAN ALLEN RADIATION BELTS The term apogee refers to the point in an elliptical exposing the spacecraft to space. LAS - LAUNCH ABORT SYSTEM deploy and open. Once the spacecraft slows to around The Van Allen Belts are belts of plasma trapped by orbit when a spacecraft is farthest from the Earth. Orion’s Launch Abort System (LAS) is designed to 100 mph, the three main parachutes will then deploy the Earth’s magnetic field that shield the surface of During Exploration Flight Test-1, Orion’s flight path will GUPPY propel the crew module away from an emergency on using three pilot parachutes and slow the spacecraft the Earth from much of the radiation in space. During take it to an apogee of 3,600 miles. Just how high is The Super Guppy is a special airplane capable of the launch pad or during initial takeoff, moving the to around 20 mph for splashdown in the Pacific Ocean. Exploration Flight Test-1, Orion will pass within the Van that? A commercial airliner flies about 8 miles above transporting up to 26 tons in its cargo compartment crew away from danger. Orion’s LAS has three new When fully deployed, the canopies of three main Allen Radiation Belts and will spend more time in the the Earth’s surface, so Orion’s flight is 450 times farther measuring 25 feet tall, 25 feet wide, and 111 feet long. -
The Orbital-Hub: Low Cost Platform for Human Spaceflight After ISS
67th International Astronautical Congress (IAC), Guadalajara, Mexico, 26-30 September 2016. Copyright ©2016 by the International Astronautical Federation (IAF). All rights reserved. IAC-16, B3,1,9,x32622 The Orbital-Hub: Low Cost Platform for Human Spaceflight after ISS O. Romberga, D. Quantiusa, C. Philpota, S. Jahnkea, W. Seboldta, H. Dittusb, S. Baerwaldeb, H. Schlegelc, M. Goldd, G. Zamkad, R. da Costae, I. Retate, R. Wohlgemuthe, M. Langee a German Aerospace Center (DLR), Institute of Space Systems, Bremen, Germany, [email protected] b German Aerospace Center (DLR), Executive Board, Space Research and Technology, Cologne, Germany, c European Space Agency (ESA) Contractor, Johnson Space Center, Houston, USA, d Bigelow Aerospace, Las Vegas / Washington, USA, e Airbus DS, Bremen, Germany Abstract The International Space Station ISS demonstrates long-term international cooperation between many partner governments as well as significant engineering and programmatic achievement mostly as a compromise of budget, politics, administration and technological feasibility. A paradigm shift to use the ISS more as an Earth observation platform and to more innovation and risk acceptance can be observed in the development of new markets by shifting responsibilities to private entities and broadening research disciplines, demanding faster access by users and including new launcher and experiment facilitator companies. A review of worldwide activities shows that all spacefaring nations are developing their individual programmes for the time after ISS. All partners are basically still interested in LEO and human spaceflight as discussed by the ISECG. ISS follow-on activities should comprise clear scientific and technological objectives combined with the long term view on space exploration. -
Moscow Defense Brief Your Professional Guide Inside # 1, 2011
Moscow Defense Brief Your Professional Guide Inside # 1, 2011 Russian Army’s New Look CONTENTS Defense Industries #1 (23), 2011 New Management at the United Aircraft Corporation 2 PUBLISHER Centre for Analysis of Arms Trade Strategies and Russian Arms Trade in 2010 4 Technologies CAST Director & Publisher Procurement Ruslan Pukhov Editor-in-Chief Russian Military Spending in 2011-2020 12 Mikhail Barabanov Advisory Editors Konstantin Makienko Space Alexey Pokolyavin Russian Space Industry in 2010 17 Researchers Ruslan Aliev Polina Temerina Armed Forces Dmitry Vasiliev Russia’s “New-Look” Army: the Medical Service 20 Editorial Office 3 Tverskaya-Yamskaya, 24, office 5, Demographics vs the Russian Army 25 Moscow, Russia 125047 phone: +7 499 251 9069 fax: +7 495 775 0418 Our Authors 28 http://www.mdb.cast.ru/ To subscribe, contact phone: +7 499 251 9069 or e-mail: [email protected] Moscow Defense Brief is published by the Centre for Analysis of Strategies and Technologies All rights reserved. No part of this publication may be reproduced in any form or by any means, electronic, mechanical or photocopying, recording or otherwise, without reference to Moscow Defense Brief. Please note that, while the Publisher has taken all reasonable care in the compilation of this publication, the Publisher cannot accept responsibility for any errors or omissions in this publication or for any loss arising therefrom. Authors’ opinions do not necessary reflect those of the Publisher or Editor Translated by: Ivan Khokhotva Computer design & pre-press: B2B design bureau Zebra www.zebra-group.ru Cover Photo: Soldiers of the 5th Independent Motorized Rifle Brigade on a rest break during an exercise Photo by: Vadim Savitsky © Centre for Analysis of Strategies and Technologies, 2011 Printed in Russia # 1, 2011 Moscow Defense Brief 1 Defense Industries New Management at the United Aircraft Corporation Konstantin Makienko ew management has arrived at the United Aircraft Sukhoi company. -
Paper Session II-A - Energy Block of International Space Station "Alpha"
1995 (32nd) People and Technology - The Case The Space Congress® Proceedings For Space Apr 26th, 2:00 PM - 5:00 PM Paper Session II-A - Energy Block of International Space Station "Alpha" Anatoli I. Kiselev General Director Khrunichev, SRPSC Follow this and additional works at: https://commons.erau.edu/space-congress-proceedings Scholarly Commons Citation Kiselev, Anatoli I., "Paper Session II-A - Energy Block of International Space Station "Alpha"" (1995). The Space Congress® Proceedings. 28. https://commons.erau.edu/space-congress-proceedings/proceedings-1995-32nd/april-26-1995/28 This Event is brought to you for free and open access by the Conferences at Scholarly Commons. It has been accepted for inclusion in The Space Congress® Proceedings by an authorized administrator of Scholarly Commons. For more information, please contact [email protected]. ENERGY BLOCK OF INTERNATIONAL SPACE STATION "ALPHA" Ana10Ji I.Kisclev - General Director K.hrunichcv SRPSC Anatoli i.Nedaivoda - General Designer Valdimir K.Karra.sk - Professor, Design Center Director The international space station "Alpha" consists of the American, Rus sian, European and Japanese segments. Its integration in the orbit will take place in November, 1997 starting from the injection of 20-tonn erergy block on the basis of the unified functional c.argo blade (russian abbr1.. "' iation as EFGB) by means of the "Proton" LY. The EFG B is designed by the KHRUNICHEV State Research and Production Space Center (KSRPSC) The orbit hight with the inclination of 51.6 deg for EFGB is so selected thett by the end of December, 1997 it can be decreased upto the hight (approx. -
The SKYLON Spaceplane
The SKYLON Spaceplane Borg K.⇤ and Matula E.⇤ University of Colorado, Boulder, CO, 80309, USA This report outlines the major technical aspects of the SKYLON spaceplane as a final project for the ASEN 5053 class. The SKYLON spaceplane is designed as a single stage to orbit vehicle capable of lifting 15 mT to LEO from a 5.5 km runway and returning to land at the same location. It is powered by a unique engine design that combines an air- breathing and rocket mode into a single engine. This is achieved through the use of a novel lightweight heat exchanger that has been demonstrated on a reduced scale. The program has received funding from the UK government and ESA to build a full scale prototype of the engine as it’s next step. The project is technically feasible but will need to overcome some manufacturing issues and high start-up costs. This report is not intended for publication or commercial use. Nomenclature SSTO Single Stage To Orbit REL Reaction Engines Ltd UK United Kingdom LEO Low Earth Orbit SABRE Synergetic Air-Breathing Rocket Engine SOMA SKYLON Orbital Maneuvering Assembly HOTOL Horizontal Take-O↵and Landing NASP National Aerospace Program GT OW Gross Take-O↵Weight MECO Main Engine Cut-O↵ LACE Liquid Air Cooled Engine RCS Reaction Control System MLI Multi-Layer Insulation mT Tonne I. Introduction The SKYLON spaceplane is a single stage to orbit concept vehicle being developed by Reaction Engines Ltd in the United Kingdom. It is designed to take o↵and land on a runway delivering 15 mT of payload into LEO, in the current D-1 configuration. -
View / Download
www.arianespace.com www.starsem.com www.avio Arianespace’s eighth launch of 2021 with the fifth Soyuz of the year will place its satellite passengers into low Earth orbit. The launcher will be carrying a total payload of approximately 5 518 kg. The launch will be performed from Baikonur, in Kazakhstan. MISSION DESCRIPTION 2 ONEWEB SATELLITES 3 Liftoff is planned on at exactly: SOYUZ LAUNCHER 4 06:23 p.m. Washington, D.C. time, 10:23 p.m. Universal time (UTC), LAUNCH CAMPAIGN 4 00:23 a.m. Paris time, FLIGHT SEQUENCES 5 01:23 a.m. Moscow time, 03:23 a.m. Baikonur Cosmodrome. STAKEHOLDERS OF A LAUNCH 6 The nominal duration of the mission (from liftoff to separation of the satellites) is: 3 hours and 45 minutes. Satellites: OneWeb satellite #255 to #288 Customer: OneWeb • Altitude at separation: 450 km Cyrielle BOUJU • Inclination: 84.7degrees [email protected] +33 (0)6 32 65 97 48 RUAG Space AB (Linköping, Sweden) is the prime contractor in charge of development and production of the dispenser system used on Flight ST34. It will carry the satellites during their flight to low Earth orbit and then release them into space. The dedicated dispenser is designed to Flight ST34, the 29th commercial mission from the Baikonur Cosmodrome in Kazakhstan performed by accommodate up to 36 spacecraft per launch, allowing Arianespace and its Starsem affiliate, will put 34 of OneWeb’s satellites bringing the total fleet to 288 satellites Arianespace to timely deliver the lion’s share of the initial into a near-polar orbit at an altitude of 450 kilometers. -
13Th International Conference on Cyber Conflict: Going Viral 2021
2021 13th International Conference on Cyber Confict: Going Viral T. Jančárková, L. Lindström, G. Visky, P. Zotz (Eds.) 2021 13TH INTERNATIONAL CONFERENCE ON CYBER CONFLICT: GOING VIRAL Copyright © 2021 by NATO CCDCOE Publications. All rights reserved. IEEE Catalog Number: CFP2126N-PRT ISBN (print): 978-9916-9565-4-0 ISBN (pdf): 978-9916-9565-5-7 COPYRIGHT AND REPRINT PERMISSIONS No part of this publication may be reprinted, reproduced, stored in a retrieval system or transmitted in any form or by any means, electronic, mechanical, photocopying, recording or otherwise, without the prior written permission of the NATO Cooperative Cyber Defence Centre of Excellence ([email protected]). This restriction does not apply to making digital or hard copies of this publication for internal use within NATO, or for personal or educational use when for non-proft or non-commercial purposes, providing that copies bear this notice and a full citation on the frst page as follows: [Article author(s)], [full article title] 2021 13th International Conference on Cyber Confict: Going Viral T. Jančárková, L. Lindström, G. Visky, P. Zotz (Eds.) 2021 © NATO CCDCOE Publications NATO CCDCOE Publications LEGAL NOTICE: This publication contains the opinions of the respective authors only. They do not Filtri tee 12, 10132 Tallinn, Estonia necessarily refect the policy or the opinion of NATO Phone: +372 717 6800 CCDCOE, NATO, or any agency or any government. NATO CCDCOE may not be held responsible for Fax: +372 717 6308 any loss or harm arising from the use of information E-mail: [email protected] contained in this book and is not responsible for the Web: www.ccdcoe.org content of the external sources, including external websites referenced in this publication. -
Soviet Steps Toward Permanent Human Presence in Space
SALYUT: Soviet Steps Toward Permanent Human Presence in Space December 1983 NTIS order #PB84-181437 Recommended Citation: SALYUT: Soviet Steps Toward Permanent Human Presence in Space–A Technical Mere- orandum (Washington, D. C.: U.S. Congress, Office of Technology Assessment, OTA- TM-STI-14, December 1983). Library of Congress Catalog Card Number 83-600624 For sale by the Superintendent of Documents, U.S. Government Printing Office, Washington, D.C. 20402 Foreword As the other major spacefaring nation, the Soviet Union is a subject of interest to the American people and Congress in their deliberations concerning the future of U.S. space activities. In the course of an assessment of Civilian Space Stations, the Office of Technology Assessment (OTA) has undertaken a study of the presence of Soviets in space and their Salyut space stations, in order to provide Congress with an informed view of Soviet capabilities and intentions. The major element in this technical memorandum was a workshop held at OTA in December 1982: it was the first occasion when a significant number of experts in this area of Soviet space activities had met for extended unclassified discussion. As a result of the workshop, OTA prepared this technical memorandum, “Salyut: Soviet Steps Toward Permanent Human Presence in Space. ” It has been reviewed extensively by workshop participants and others familiar with Soviet space activities. Also in December 1982, OTA wrote to the U. S. S. R.’s Ambassador to the United States Anatoliy Dobrynin, requesting any information concerning present and future Soviet space activities that the Soviet Union judged could be of value to the OTA assess- ment of civilian space stations. -
Initial Investigation of Reaction Control System Design on Spacecraft Handling Qualities for Earth Orbit Docking
Initial Investigation of Reaction Control System Design on Spacecraft Handling Qualities for Earth Orbit Docking Randall E. Bailey1 E. Bruce Jackson,2 and Kenneth H. Goodrich 3 NASA Langley Research Center, Hampton, Virginia, 23681 W. Al Ragsdale4, and Jason Neuhaus 5 Unisys Corporation, Hampton, VA, 23681 and Jim Barnes6 ARINC, Hampton, VA, 23666 A program of research, development, test, and evaluation is planned for the development of Spacecraft Handling Qualities guidelines. In this first experiment, the effects of Reaction Control System design characteristics and rotational control laws were evaluated during simulated proximity operations and docking. Also, the influence of piloting demands resulting from varying closure rates was assessed. The pilot-in-the-loop simulation results showed that significantly different spacecraft handling qualities result from the design of the Reaction Control System. In particular, cross-coupling between translational and rotational motions significantly affected handling qualities as reflected by Cooper-Harper pilot ratings and pilot workload, as reflected by Task-Load Index ratings. This influence is masked – but only slightly – by the rotational control system mode. While rotational control augmentation using Rate Command Attitude Hold can reduce the workload (principally, physical workload) created by cross-coupling, the handling qualities are not significantly improved. The attitude and rate deadbands of the RCAH introduced significant mental workload and control compensation to evaluate when deadband firings would occur, assess their impact on docking performance, and apply control inputs to mitigate that impact. I. Introduction Handling qualities embody “those qualities or characteristics of an aircraft that govern the ease and precision with which a pilot is able to perform the tasks required in support of an aircraft role."1 These same qualities are as critical, if not more so, in the operation of spacecraft. -
Soyuz Launch Brochure
Incredible Adventures is excited to offer a unique opportunity – a chance to visit the famous Baikonur Cosmodrome and observe a manned launch of a Russian Soyuz spacecraft. You’ll be completely immersed in the electric atmosphere surrounding a launch. You’ll explore Baikonur’s launch sites, museums and most historic places. Join IA for an Incredible Space Adventure. Highlights of Your Incredible Baikonur Adventure 800-644-7382 or 941-346-2603 www.incredible-adventures.com Observe roll-out and installation of the Soyuz rocket at launch pad. Attend international press conference of main and back- up crews. See the farewell of the crew at the cosmonaut hotel. Hear crew's ready-to-go official report. See launch of the Soyuz rocket, something you’ll never forget. Incredible Baikonur Adventure Day 1 Meet IA representative at the airport. Flight from Moscow to Baikonur .Transfer to the hotel. Time to relax. Day 2 Breakfast in the hotel Transfer to Baikonur Cosmodrome Roll-out of the Soyuz Rocket. (Follow the Soyuz to its launch site.) Observe installation of the rocket on the launch pad. Visit to the integration building of Soyuz and Progress spaceships. Transfer back to town. Visit to the International Space School. 9 Day 3 Breakfast in the hotel. Visit Museum of History Cosmodrome Baikonur. Enjoy general sightseeing in the town of Baikonur (learn history of the town, visit memorials and monuments). Transfer to Cosmonaut hotel. International press conference with the main and backup crews of Soyuz-TMA vehicle. Walk along the historical alley of Cosmonauts where personalized trees are planted. -
Rex D. Hall and David J. Shayler
Rex D. Hall and David J. Shayler Soyuz A Universal Spacecraft ruuiiMicPublishedu 11in1 aaaundiiuiassociationi witwimh ^^ • Springer Praxis Publishing PRHB Chichester, UK "^UF Table of contents Foreword xvii Authors' preface xix Acknowledgements xxi List of illustrations and tables xxiii Prologue xxix ORIGINS 1 Soviet manned spaceflight after Vostok 1 Design requirements 1 Sever and the 1L: the genesis of Soyuz 3 The Vostok 7/1L Soyuz Complex 4 The mission sequence of the early Soyuz Complex 6 The Soyuz 7K complex 7 Soyuz 7K (Soyuz A) design features 8 The American General Electric concept 10 Soyuz 9K and Soyuz 1 IK 11 The Soyuz Complex mission profile 12 Contracts, funding and schedules 13 Soyuz to the Moon 14 A redirection for Soyuz 14 The N1/L3 lunar landing mission profile 15 Exploring the potential of Soyuz 16 Soyuz 7K-P: a piloted anti-satellite interceptor 16 Soyuz 7K-R: a piloted reconnaissance space station 17 Soyuz VI: the military research spacecraft Zvezda 18 Adapting Soyuz for lunar missions 20 Spacecraft design changes 21 Crewing for circumlunar missions 22 The Zond missions 23 The end of the Soviet lunar programme 33 The lunar orbit module (7K-LOK) 33 viii Table of contents A change of direction 35 References 35 MISSION HARDWARE AND SUPPORT 39 Hardware and systems 39 Crew positions 40 The spacecraft 41 The Propulsion Module (PM) 41 The Descent Module (DM) 41 The Orbital Module (OM) 44 Pyrotechnic devices 45 Spacecraft sub-systems 46 Rendezvous, docking and transfer 47 Electrical power 53 Thermal control 54 Life support 54 -
The Soviet Space Program
C05500088 TOP eEGRET iuf 3EEA~ NIE 11-1-71 THE SOVIET SPACE PROGRAM Declassified Under Authority of the lnteragency Security Classification Appeals Panel, E.O. 13526, sec. 5.3(b)(3) ISCAP Appeal No. 2011 -003, document 2 Declassification date: November 23, 2020 ifOP GEEAE:r C05500088 1'9P SloGRET CONTENTS Page THE PROBLEM ... 1 SUMMARY OF KEY JUDGMENTS l DISCUSSION 5 I. SOV.IET SPACE ACTIVITY DURING TfIE PAST TWO YEARS . 5 II. POLITICAL AND ECONOMIC FACTORS AFFECTING FUTURE PROSPECTS . 6 A. General ............................................. 6 B. Organization and Management . ............... 6 C. Economics .. .. .. .. .. .. .. .. .. .. .. ...... .. 8 III. SCIENTIFIC AND TECHNICAL FACTORS ... 9 A. General .. .. .. .. .. 9 B. Launch Vehicles . 9 C. High-Energy Propellants .. .. .. .. .. .. .. .. .. 11 D. Manned Spacecraft . 12 E. Life Support Systems . .. .. .. .. .. .. .. .. 15 F. Non-Nuclear Power Sources for Spacecraft . 16 G. Nuclear Power and Propulsion ..... 16 Te>P M:EW TCS 2032-71 IOP SECl<ET" C05500088 TOP SECRGJ:. IOP SECREI Page H. Communications Systems for Space Operations . 16 I. Command and Control for Space Operations . 17 IV. FUTURE PROSPECTS ....................................... 18 A. General ............... ... ···•· ................. ····· ... 18 B. Manned Space Station . 19 C. Planetary Exploration . ........ 19 D. Unmanned Lunar Exploration ..... 21 E. Manned Lunar Landfog ... 21 F. Applied Satellites ......... 22 G. Scientific Satellites ........................................ 24 V. INTERNATIONAL SPACE COOPERATION ............. 24 A. USSR-European Nations .................................... 24 B. USSR-United States 25 ANNEX A. SOVIET SPACE ACTIVITY ANNEX B. SOVIET SPACE LAUNCH VEHICLES ANNEX C. SOVIET CHRONOLOGICAL SPACE LOG FOR THE PERIOD 24 June 1969 Through 27 June 1971 TCS 2032-71 IOP SLClt~ 70P SECRE1- C05500088 TOP SEGR:R THE SOVIET SPACE PROGRAM THE PROBLEM To estimate Soviet capabilities and probable accomplishments in space over the next 5 to 10 years.' SUMMARY OF KEY JUDGMENTS A.