Masters of the Bu I L Di Ng Art S
Total Page:16
File Type:pdf, Size:1020Kb
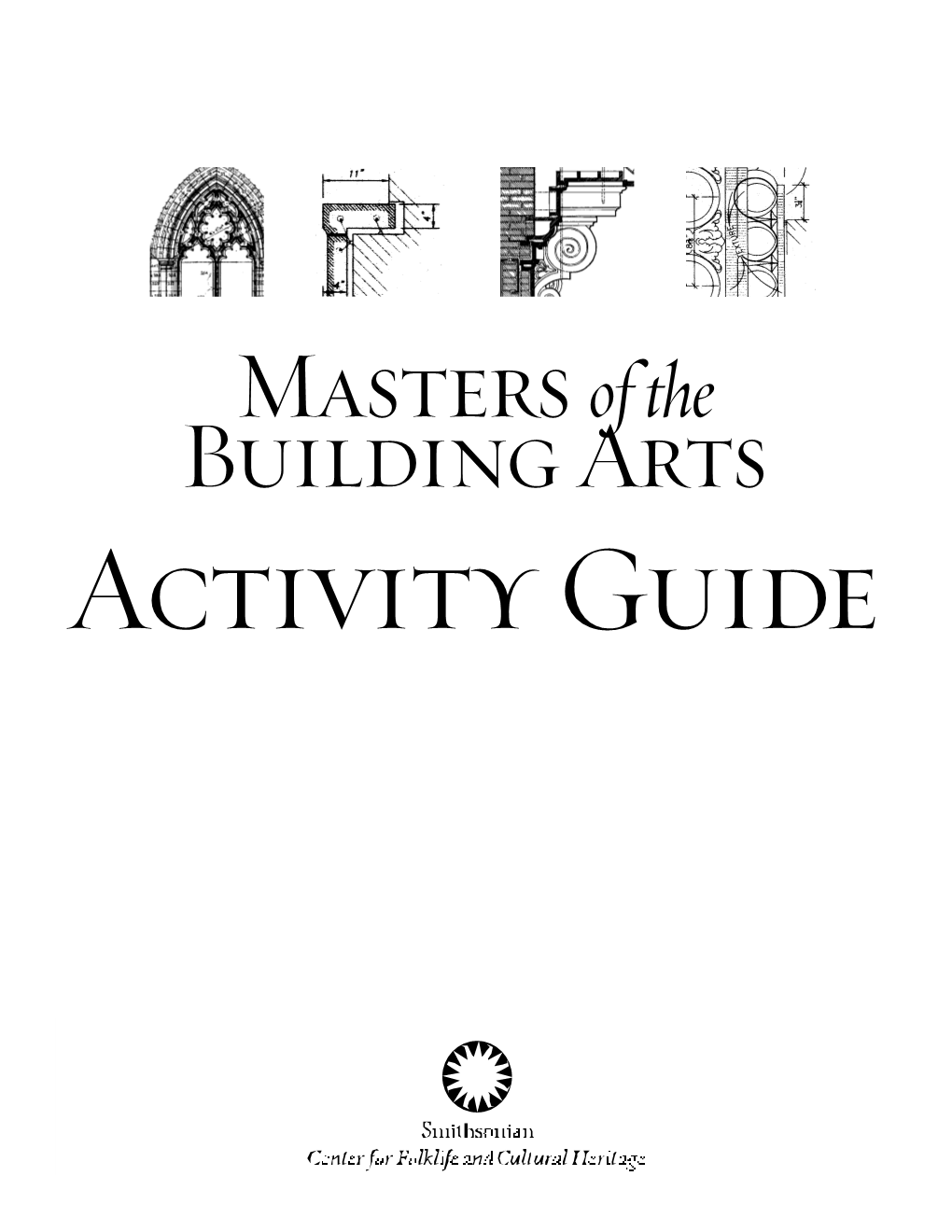
Load more
Recommended publications
-
TFEC 1-2019 Standard for Design of Timber Frame Structures And
TFEC 1-2019 Standard for Design of Timber Frame Structures and Commentary TFEC 1-2019 Standard Page 1 January 2019 TFEC 1-2019 Standard for Design of Timber Frame Structures and Commentary Timber Frame Engineering Council Technical Activities Committee (TFEC-TAC) Contributing Authors: Jim DeStefano Jeff Hershberger Tanya Luthi Jaret Lynch Tom Nehil Dick Schmidt, Chair Rick Way Copyright © 2019, All rights reserved. Timber Framers Guild 1106 Harris Avenue, Suite 303 Bellingham, WA 98225 TFEC 1-2019 Standard Page 2 January 2019 Table of Contents 1.0 General Requirements for Structural Design and Construction .......................................6 1.1 Applicability and Scope ........................................................................................ 6 1.2 Liability ................................................................................................................. 6 1.3 General Requirements ........................................................................................... 7 1.3.1 Strength ........................................................................................................... 7 1.3.2 Serviceability ................................................................................................... 7 1.3.3 General Structural Integrity ............................................................................. 7 1.3.4 Conformance with Standards .......................................................................... 7 1.4 Design Loads ........................................................................................................ -
Innovations in Heavy Timber Construction • © 2011 Woodworks
I NNOVAT I ONS I N T I MBER C ONSTRU C T I ON eavy timber construction—used for hundreds of years around the world—successfully combines the Combining beauty of exposed wood with the strength and fire the Beauty Hresistance of heavy timber. The traditional techniques used in ancient churches and temples, with their of Timber high-vaulted ceilings, sweeping curves and enduring strength, still influence today’s structures. The hallmarks of heavy timber—prominent wood beams and timbers—now also include elegant, leaner framing that celebrates the with Modern expression of structure with a natural material. A visual emphasis on beams, purlins and connections lends character and a powerful aesthetic sense Construction of strength. Historically a handcrafted skill of mortise and tenon joinery, heavy timber construction has been modernized by tools such as CNC machines, high- strength engineered wood products, and mass-production techniques. A growing environmental awareness that recognizes wood as the only renewable and sustainable structural building material is also invigorating this type of construction. Heavy timbers are differentiated from dimensional lumber by having minimum dimensions required by the building code. Modern versions include sawn stress-grade lumber, timber tongue and groove decking, glued-laminated timber (glulam), parallel strand lumber (PSL), laminated veneer lumber (LVL) and cross laminated timber (CLT). Structural laminated products can be used as solid walls, floors and columns to construct an entire building. Modern heavy timber construction contributes to the appeal, comfort, structural durability and longevity of schools, churches, large-span recreation centers, mid-rise/multi-family housing and supermarkets, among many other buildings. -
18Th Annual Eastern Conference of the Timber Framers Guild
Timber Framers Guild 18th Annual Eastern Conference November 14–17, 2002, Burlington, Vermont The Timber Framer’s Panel Company www.foardpanel.com P.O. Box 185, West Chesterfield, NH 03466 ● 603-256-8800 ● [email protected] Contents FRANK BAKER Healthy Businesses. 3 BRUCE BEEKEN Furniture from the Forest . 4 BEN BRUNGRABER AND GRIGG MULLEN Engineering Day to Day ENGINEERING TRACK . 6 BEN BRUNGRABER AND DICK SCHMIDT Codes: the Practical and the Possible ENGINEERING TRACK . 8 RUDY CHRISTIAN Understanding and Using Square Rule Layout WORKSHOP . 13 RICHARD CORMIER Chip Carving PRE-CONFERENCE WORKSHOP . 14 DAVID FISCHETTI AND ED LEVIN Historical Forms ENGINEERING TRACK . 15 ANDERS FROSTRUP Is Big Best or Beautiful? . 19 ANDERS FROSTRUP Stave Churches . 21 SIMON GNEHM The Swiss Carpenter Apprenticeship . 22 JOE HOWARD Radio Frequency Vacuum Drying of Large Timber: an Overview . 24 JOSH JACKSON Plumb Line and Bubble Scribing DEMONSTRATION . 26 LES JOZSA Wood Morphology Related to Log Quality. 28 MICHELLE KANTOR Construction Law and Contract Management: Know your Risks. 30 WITOLD KARWOWSKI Annihilated Heritage . 31 STEVE LAWRENCE, GORDON MACDONALD, AND JAIME WARD Penguins in Bondage DEMO 33 ED LEVIN AND DICK SCHMIDT Pity the Poor Rafter Pair ENGINEERING TRACK . 35 MATTHYS LEVY Why Buildings Don’t Fall Down FEATURED SPEAKER . 37 JAN LEWANDOSKI Vernacular Wooden Roof Trusses: Form and Repair . 38 GORDON MACDONALD Building a Ballista for the BBC . 39 CURTIS MILTON ET AL Math Wizards OPEN ASSISTANCE . 40 HARRELSON STANLEY Efficient Tool Sharpening for Professionals DEMONSTRATION . 42 THOMAS VISSER Historic Barns: Preserving a Threatened Heritage FEATURED SPEAKER . 44 Cover illustration of the Norwell Crane by Barbara Cahill. -
SUMMER 1993 PAGE THREE in 1926, Powers a Saw Mill, a Woodworking Shop, and a Feed E.A.I.A
THE MILL Sawyers and Millwrights AT LEDYARD, of Saugerties, New York CONNECTICUT I n response to my request for information on up-and.-down sawmills, a friend in Albany county, New York, sent a draw ing of a blade he had document ed on a mill at Kent, Connecti cut, and a letter telling of anot-her vertical mill he had discovered in Ledyard, Connect icut. He had visited the Led yard site in July but it was not in operation because the water in the millpond was low. He planned to go back in April or May of this year when the mill would De working and open to the public. In early May I called the number he had given me and was told b,y Ruth Dyer, one of the volunteers at the site, that the mill had just suffered a major breakdown. The men who O1arlie i:nd Michael Rothe TrainiQ9 Their Tean, Michael operate and maintain it were keeps six Belgian hOrses for logglng. They are ideal for working on the problem but were selective harvesting and do less dcmage to the forest than not sure when it would be oper modern diesel equipment, (Photo by P.Sinclair) ational. I told her I would come anyway. Afterall, mainte nance and repair are important aspects of a water mill. Ithough little remains in the vritten record, some Ledyard, Connecticut, is A a hilly township a few miles believed there was a sawmill in the mid-Hudson Valley at from the states southern coast the present town of Saugerties, New York, before the area It lies in the watershed of the was formally settled in the 168Os. -
Framing the Cabildo Roof Livestock .Heritage
-_.-.,~ A Quarterl Journal of Historical Preservation Volume 2, Number 2 Preserving American Framing the Cabildo Roof Livestock .Heritage Aound the world the extinction ofspecies proceeds at an alarming rate as deforestation, agricultural development, human population expansion and ecologi cal degridation continue. Even the farm yards, pasturesandfields ofNorthAmerica no longer support the diverse livestock breeds of 50 to 100 years ago. About fifteen years ago, agricultural historians in Massachusetts who had rec reated early agricultural habitats at Old Sturbridge Village and Plymoth Planta tion were hard pressed to find authentic livestock to stock their recreations. The American Minor Breeds Conservancy (AMBC) was conceived out ofthe recogni tion of a need to preserve the vanishing American livestock diversity. In this short time AMBC has grown rapidly to become The Cabildo, Jackson Square, New Orleans, Louisiana, as itappearedbeforethe 1988fire. Photocourtesy active throughut America and has begun ofKoch & Wilson Architects, New Orleans. to go worldwide in efforts to preserve en dangered breeds. "The procedures ofFrench scribe layout could not be more unlike the square rule In 1985 AMBC began a comprehen practice used today in most American shops. Where modern American timber framing is sive list of American livestock breeds to a patchwork quilt oftradition and invention. French scribe is a tapestry, a whole piece of identify those which are in danger of ex cloth woven over centuries ofcontinuous practice." tinction. Aftercareful considerationofcen sus results, the following definitions have -Ed Levin, Timber Framing, 1992 been developed. RARE ... Cattle and horse breeds with less than 200 registrations per year. About 150yemagoiu muoh ofAmeri..a new""ternoftimberframing'alled Sheep, goat, and pigbreeds with less than square rule replaced the older European method known as scribe rule. -
Nembe-English Dictionary
NEMBE-ENGLISH DICTIONARY 2nd edition of the Nembe dictionary, M.H.I. Kaliai, University of Ibadan Press, 1964. This version prepared and edited by Roger Blench Roger Blench Mallam Dendo 8, Guest Road Cambridge CB1 2AL United Kingdom Voice/ Fax. 0044-(0)1223-560687 Mobile worldwide (00-44)-(0)7967-696804 E-mail [email protected] http://www.rogerblench.info/RBOP.htm To whom all correspondence should be addressed. This printout: August 6, 2008 i TABLE OF CONTENTS Abbreviations: ................................................................................................................................................. 2 Editor’s Preface............................................................................................................................................... 3 i Abbreviations: Parts of speech of headwords have been indicated in this edition as follows adj. adjective aux. v. auxiliary verb cf. compare coll. colloquial conj. conjunction dem. demonstrative E. English enc. enclitic esp. especially ext. suff. extensional suffix H. Hausa infl. suff. inflectional suffix int. interjection int. interrogative lit. literally n. noun num. numeral p.n. proper name prep. preposition pron. pronoun poss. possessive pronoun quant. quantifier v. verb Y. Yoruba derived from ii Nembe dictionary. Kaliai revised Blench. Circulation draft 6-Aug-08 Editor’s Preface The present Nembe dictionary is a revised and expanded version of the Nembe dictionary published by M.H.I. Kaliai at the University of Ibadan in 1964. died in early January 2005, with it still unpublished. During the 1990s, the manuscript was typed without alteration into an Apple-based system under the auspices of the late Professor Kay Williamson. The files transferred to an IBM system in the early 2000s, but without any conversion of the character codes. This was only partly successful, and several sections of the dictionary became corrupted. -
IV. COMPOSITE and RAISED BOTTOM CHORD TRUSSES Jan Lewandoski
TIMBERTIMBER FRAMINGFRAMING JOURNALJOURNAL OFOF THETHE TIMBERTIMBER FRAMERSFRAMERS GUILDGUILD NumberNumber 74,74, DecemberDecember 20042004 D-I-Y Down Under TIMBER FRAMING JOURNAL OF THE TIMBER FRAMERS GUILD NUMBER 74 DECEMBER 2004 CONTENTS TOPICS TOPICS 2 Rick Collins HISTORIC AMERICAN ROOF TRUSSES 4 IV. COMPOSITE AND RAISED BOTTOM CHORD TRUSSES Jan Lewandoski COMPOSITE AND RAISED BOTTOM CHORD 20 TRUSS ENGINEERING Ed Levin D-I-Y DOWN UNDER II 22 Rob Hadden Respectful Restoration HE Illinois Yearly Friends Meeting House in McNabb, Ill., On the cover, end view and interior detail of newly made barn was raised in 1874 by English-descended Quakers moving with guest quarters in Castlemaine, Victoria, Australia. The west, and has since withstood tornadoes, termites, lightning owner-builder, an artist and self-taught mason and timber T and other mortal threats. When the original Quaker settlers moved framer, chainmilled most of the timber from salvage logs of to central Illinois earlier in the 19th century, they built their small many species and gathered and laid all the stones in the community on some of the most fertile land in North America. masonry foundation. Inspired by English design largely from Their first meetinghouse rose in 1831. The 1874 structure is the the Welsh Marches, though not exclusively so, the frame was cut third to stand in the settlement. by English scribe rule and raised piece by piece using gin pole, The building sits on a limestone foundation, probably quarried shear legs and tackle. Pegs are cleft and shaved. Photos by from the nearby Illinois River valley, and typical of the period in Mandy Murphy. -
Envisioning Evolution: Alternative Paths to Success in Timber Framing
Envisioning Evolution: 2017 TFG Alternative Paths to Success in Timber Framing Conference Christian Gudmand (Hardwick Post & Beam) Matt Hunter (Ashland Post & Beam) Stephen Morrison (MoreSun Custom Woodworking, Inc.) Ariel Schecter (Timber Homes Vermont) Autumn Peterson (Heritage Natural Finishes, LLC) Michael Cuba, Moderator (Knobb Hill Joinery) The current economic and regulatory environment presents both challenges and opportunities for those endeavoring to run a business or make a career in timber framing. As an inherently creative group of craftspeople, many of us find that tried-and-true formulas for prosperity in business don’t always fit our own visions of what it means to be successful. We are looking for a conversation be- tween folks who have been in the trade for several years and looking to plan for the long-term career, whether it is starting a new business, changing a current business model or moving up in your cur- rent employment. This session will use a roundtable format to catalyze and facilitate discussion about roads less trav- eled in developing careers and businesses in the timber framing industry today. We will discuss strategies; when and how to work with other timber framing professionals; when to take risks and when to cut losses; how to find, train, and retain good employees; and more. We are hopeful that at- tendees will participate and help to guide the direction of the discussion. Our goal is to broaden the context in which we view opportunities to apply our creativity and grow sustainable businesses. About the Speakers Michael Cuba (moderator) Michael Cuba is a co-founder of Knobb Hill Joinery, a historic preservation company in northern Vermont focused on traditional restorative joinery techniques. -
TIMBER FRAMING JOURNAL of the TIMBER FRAMERS GUILD Number 69, September 2003
TIMBER FRAMING JOURNAL OF THE TIMBER FRAMERS GUILD Number 69, September 2003 Tour Charpentier de France TIMBER FRAMING JOURNAL OF THE TIMBER FRAMERS GUILD NUMBER 69 SEPTEMBER 2003 CONTENTS LETTERS 2 Paul Oatman, Peter Sinclair, Joel McCarty HISTORIC AMERICAN ROOF TRUSSES 4 I. SCISSOR TRUSSES Jan Lewandoski LETTERS HISTORIC SCISSOR TRUSS ANALYSIS 15 Ed Levin More Words, Please OUR OWN TOUR DE FRANCE 18 Will Beemer GLOSSARY of timber frame terms is indeed needed and you have published the first draft (TF 68). Although you LIFTING APPARATUS CALCULATIONS 29 refer to a couple of notable sources for your definitions, you Grigg Mullen A bypassed the most notable reference in the English language, the Oxford English Dictionary, a work 70 years in the making, first published in 1928 with five supplements and newly published in On the cover, view of a well-preserved street in Rouen, a town the year 2000. (However, in my research on drawboring [see TF visited by several Guild members following a guided tour of 67], I was able to predate the OED, which cites J. Smith’s reference timber-framed buildings in northeastern France. Note trussed of 1812; I quote Moxon from 1703. I have not told the OED of wall framing over broad shop windows, slate siding on build- this find as I am still searching for earlier sources.) All words should ings at the center of the view and the exuberant multiplicity of be given with their first usage. For some reason this was done with bracing patterns. The building visible at the far end of the street only one term, tusk tenon. -
Mass Timber in North America Expanding the Possibilities of Wood Building Design
CONTINUING EDUCATION Presented by: MASS TIMBER IN NORTH AMERICA EXPANDING THE POSSIBILITIES OF WOOD BUILDING DESIGN LEARNING OBJECTIVES Upon completion of this course the student will be able to: 1. Examine the trend toward mass timber buildings in the context of carbon footprint, construction efficiency, fire and life safety, occupant well-being, and other potential advantages. 2. Identify a range of mass timber products available to North American building designers. 3. Discuss research and resources related to the structural performance and fire/life safety of mass timber products. 4. Based on examples of mass timber buildings either built or under construction, describe how all-wood and hybrid systems are expanding the options for wood design. CONTINUING EDUCATION Earn 0.1 ICC Continuing Education Unit (CEU) Use the learning objectives above to focus your study as you read this article. To receive credit, you are required to read the entire article and Albina Yard pass the test. Go to www.awc.org for complete Location: Portland, Oregon text and take the test for free. Architect: LEVER Architecture Structural Engineer: KPFF Consulting Engineers AWC Course #DES610-A Developer: reworks ICC#9766OD Photo courtesy of LEVER Architecture It’s been a while since a major category Lighter carbon footprint: Mass timber firm’s experience, a mass timber project is of building materials inspired the kind of products allow the use of a renewable and approximately 25 percent faster to construct widespread enthusiasm currently being shown sustainable resource as an alternative to more than a similar project in concrete. Noting the for mass timber. -
Craft Matters with My Hands—Use a Chainsaw, Sew Sailcloth Into Sails, Manipulate an Axe and an Adze
Life+Style Southwest by Steve Thomas the PBS Adventure film by the same title. Satawal’s is a handmade culture, very closed, and I was accepted into it because I could work craft matters with my hands—use a chainsaw, sew sailcloth into sails, manipulate an axe and an adze. Build stuff. Craft stuff. The Last Navigator was broadcast in 1989, virtually the same month a call to arms I was offered the job to host This Old House. The first project I did as (and saws, host of This Old House was the timber frame barn in Concord, Massachusetts, erected by the Timber Framers Guild. It remains one and hammers) of the most popular This Old House projects largely because viewers for the next are drawn to the beauty of the craft of timber framing. At the same time I was also buying, renovating, and selling historic generation of homes in Salem, Massachusetts, working on a First Period Colonial builders from the 1700s that ended up being our family home for 27 years. I remember with particular vividness stripping off the lath and plaster in the living room to reveal perfect timber frame joinery, executed and assembled with skill and respect some 250 years earlier. Whoever put that frame together understood that craftsmanship, like integrity, means Steve Thomas doing the right thing, even when no one is looking. And I’m betting it Douglas Merriam endowed that craftsman with pride, strength, and a certain nobility. These are not easy attributes to come to these days, so I would invite you to join our tribe. -
Read the Review
TIMBER FRAMING JOURNAL OF THE TIMBER FRAMERS GUILD Number 136, June 2020 New and Renewed in Vermont TIMBER FRAMING JOURNAL OF THE TIMBER FRAMERS GUILD NUMBER 136 JUNE 2020 CONTENTS BOOK REVIEW: CRUCK BUILDING 2 Jack A. Sobon A HYBRID FRAME IN VERMONT 4 Will Gusakov SAVING A LARGE NEW ENGLAND BARN 8 Eliot Lothrop On the cover, Wolcott, Vermont, barn lifted and shored in place while a new foundation is poured. See article, page 8. Photo: Alex Howe. On the back cover, Bedstone Manor (1448), Shropshire, England. Drawing shows asymmetry common in cruck framing, including molding details. In photo, massive free dovetail linking cruck blade and spur. Drawing and photo: M. Moran (from Cruck Building). Copyright © 2020 Timber Framers Guild 116 Pleasant Street, Suite 334, Easthampton, MA 01027 833-862-7376 | [email protected] Cruck Building Editorial Correspondence Please email [email protected]. Cruck Building: A Survey. Nat Alcock, P. S. Barnwell, and Martin Cherry, editors. Donington, UK: Shaun Tyas, 2019. 7½ in. x 10 in., Editors Michael Cuba, Adam Miller 406 pp. 421 illustrations. Hardcover, £50. Editor Emeritus Kenneth Rower RUCK framing is a historic method of timber building, Contributing Editors found primarily in the British Isles, where the roof is History Jan Lewandoski, Jack A. Sobon supported by pairs of curved or elbowed timbers (called Ben Brungraber, Tom Nehil Ccruck ) rising from the sill and joined at their apex, an early Engineering blades A-frame (Fig. 1). Since I first saw images of cruck frames in the Layout/Design Erin Moore classic book Shelter (Shelter Publications, 1973) back in the ’70s, I have been smitten with their beauty, grace, and charm, constructing Printed on Anthem Plus, an FSC® certified paper my first cruck frame in 1985.