Contributions to the Chemistry and Physics of Cotton Fibers
Total Page:16
File Type:pdf, Size:1020Kb
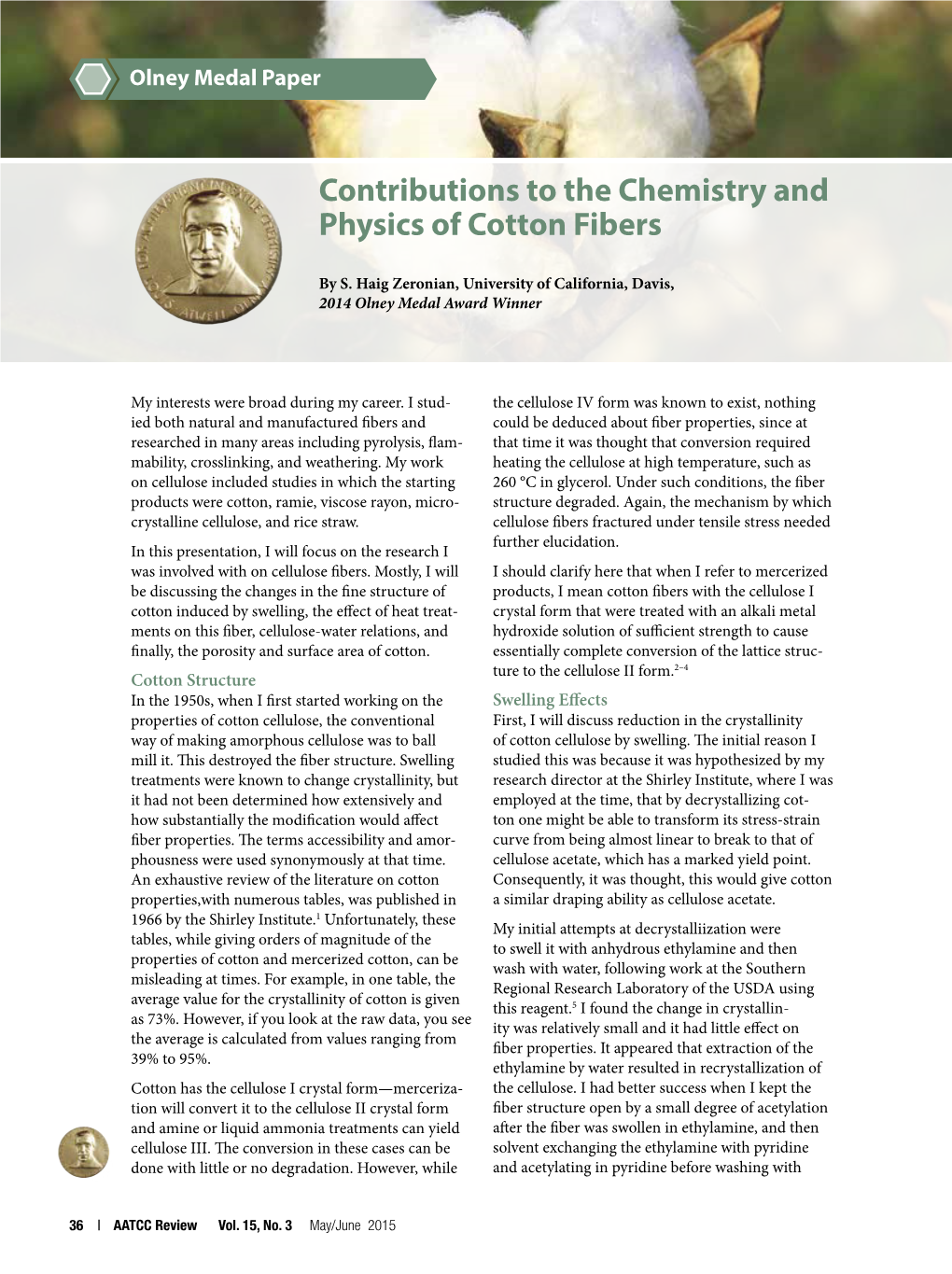
Load more
Recommended publications
-
Eastman Naia™ Cellulosic Fiber Process Infographic —
S U The process starts with pine and eucalyptus S T wood sourced exclusively from sustainably A * managed and certified forests and IN plantations in North America and Brazil. A B LY M Sustainably sourced wood is turned into wood A ™ N pulp, ready to enter the Naia production process AG S in Eastman´s safe and eco-friendly facility in the ED FOREST U.S., where Naia™ is produced. PULP WOOD Wood pulp is combined with acetic acid to make ACETONE cellulose acetate granules. & Handled safely in a closed-loop ACETATE GRANULES CELLULOSE process, the granules are SAFE SOUND SOLVENT dissolved in acetone to make a USE cellulose acetate dope solution. Solvents used in the process are ™ recycled back into the system EASTMAN NAIA CELLULOSIC for reuse with no release into the environment. Used water is SPINNINGDRY FIBER PORTFOLIO cleaned and returned to the The dope is finally spun source with routine testing to through tiny holes in a PRODUCTION PROCESS ensure thriving biodiversity in spinneret and air-dried the local river. to form cellulose From tree to fiber, the Naia™ production process acetate fiber. Dry is designed to ensure the lowest environmental spinning Naia™ does not require any water. impact. With an extremely low water footprint, CLOSED LOOP Naia™ uses only sustainably sourced wood and safe solvents which are recycled and reused. Eastman Naia™ cellulosic fiber portfolio includes: • Naia™ cellulosic fiber, a cellulose acetate staple fiber • Naia™ cellulosic yarn, a cellulose acetate filament The cellulose acetate yarn is wound onto large SHIPPING- bobbins—ready for shipping to fabric mills and READY yarn Eastman warehouses around the world. -
Corning® Filtration Guide Innovative Products for Filtration and Ultrafiltration Table of Contents
Corning® Filtration Guide Innovative Products for Filtration and Ultrafiltration Table of Contents Filtration Selecting the Best Filter for Your Application .............................................................................. 1 Improving Filter Performance ......................................................................................................... 5 Spin-X® Tube Purification of DNA from Agarose Gels .............................................................. 6 Safety Precautions .............................................................................................................................. 7 Bibliography ......................................................................................................................................... 7 Ordering Information ........................................................................................................................ 8 Ultrafiltration ........................................................................................................................................ 12 Introduction ...................................................................................................................................... 12 Choosing the Right Concentrator Doesn’t Have to be Complicated .................................. 12 Choosing the Best Molecular Weight Cut-off Membrane .................................................... 14 Helpful Hints .................................................................................................................................... -
Environmental Testing for Water Physical Analysis
GE Healthcare Great savings Environmental testing for water Physical analysis Solids analysis The level of suspended solids in a water sample is determined Suspended solids measurements are typically by pouring a carefully measured volume of water through performed using glass fiber filter circles that need a preweighed filter with a specified pore size, drying additional preparation prior to use. However, GE has the filter to remove the water, and then weighing the developed ready-to-use 934-AH RTU glass fiber filters, filter again. The weight gain of the filter is a dry weight which are supplied in a prewashed and preweighed measure of the particulates present in the water sample format and enable considerable time savings in the expressed in units derived or calculated from the volume laboratory. 934-AH RTU filters also provide reproducible of water filtered (typically milligrams per liter). results and low background contamination. Prepare filter per Heat retained solids on Evaporate liquid filtrate Calculate weight method by washing, Filter and filter to 500°C and measure and weigh the retained of suspended solids drying, and weighing dry sample weight change to calculate solute to calculate captured on filter as appropriate volatile solids dissolved solids Fig 1. Total solids analysis workflow using filtration-based methods. What are you testing for? Product Characteristics and benefits Solids, including: GF/C™ • Conform to requirements of standard methodologies: GF/C for EN 872 (Fig 2); 934-AH for Standard Method 2540D • total suspended 934-AH™ • High loading capacity enabling filtration of very • total dissolved glass fiber filters turbid samples Ordering information p. -
How to Choose the Right Filter > Membrane Selection Guide
> Membrane selection guide > UptiDisc™ technology Cellulose Acetate - CA: Ideal hydrophilic membrane for the filtration of aqueous samples, with low PVDF - polyvinylidene difluoride: solvent resistance. Hydrophilic membrane with a good solvent resistance. Ideal for filtration Less chemical resistance compare to RC membranes. of HPLC mobile phase solvents and for most of biological samples. A Glass pre-filter membrane is used for tissue culture media filtration, biolo- PVDF membrane is also considered as having the lowest protein binding. gical sample filtration, as clarification and sterilization of aqueous samples. Very low protein binding (binding < PVDF, PS), the Glass pre-filter PTFE - polytetrafluoroethylene: increases filtrate volume yield by 3. Hydrophobic membrane chemically resistant to solvents, acids and bases. Regenerated Cellulose - RC: This membrane is ideal for filtration of chromatography solvents, with no Hydrophilic membrane that has the same properties as cellulose acetate extractable due to the PTFEmembrane. but stable with most HPLC solvents. This membrane is used for HPLC solvents, degassing, and filtration and is PP - polypropylene: compatible with aqueous samples in a pH range from 2 to 12. High resistance, may be used with virtually all solvents, acids and bases. With a non-specific low protein binding, this membrane is chosen for protein filtration when maximum yield of recovery is needed. Glass Fiber - GF: Commonly used as a pre-filter for most of filtrations devices. Nylon - polyamide 6-6: It increase by 3 times the filtration capacity. Commonly used for HPLC samples filtration prior to injection, with good Typically used for crude samples and used for the cleaning and purifica- solvent resistance. Having hydrophilic properties, it gives good results with tion of DNA. -
IPI Storage Guide for Acetate Film
IPI Storage Guide for Acetate Film James M. Reilly • Director, Image Permanence Institute Instructions for Using the Wheel, Graphs, and Table Basic Strategy for Film Preservation l The IPI Storage Guide for Acetate Film provides an overview of environmental specifications for film storage. It explains the relationship between temperature, relative humidity (RH), and “vinegar syndrome,” the slow chemical decomposition of acetate plastics leading to loss of their value in a film collection. l The main purpose of the Guide is to help collection managers evaluate the quality of the storage environment they provide for their film. The Guide is not meant to predict the life of any individual film; it merely uses predicted life span as a yardstick to measure the quality of the storage environment. l CONTENTS What the Guide Is (and What It Is Not) ................... 2 The Wheel ................................................................ 4 Time Contours for Vinegar Syndrome .................... 7 The Time Out of Storage Table ............................... 8 Chemical Deterioration of Film Bases .................. 10 The Course of the Vinegar Syndrome .................. 13 Does the Guide Apply to Nitrate Film? ................. 15 Polyester Base Film ............................................... 15 The General Philosophy of Film Storage .............. 16 History of Film Supports ........................................ 21 References ............................................................. 23 ANSI and ISO Film Storage Standards ................. 24 Rochester Institute of Technology, 70 Lomb Memorial Drive, Rochester, NY 14623-5604 Phone: 716-475-5199 Fax: 716-475-7230 Image Permanence Institute Image Permanence l WHAT THE GUIDE IS (AND WHAT IT IS NOT) The IPI Storage Guide for Acetate Film is a tool for evaluating and planning storage environments for acetate base photographic film, cinema film, and microfilms. -
Rapid Identification of Cellulose Nitrate and Cellulose Acetate Film In
Carter et al. Herit Sci (2020) 8:51 https://doi.org/10.1186/s40494-020-00395-y RESEARCH ARTICLE Open Access Rapid identifcation of cellulose nitrate and cellulose acetate flm in historic photograph collections Elizabeth A. Carter1,2* , Brad Swarbrick2, Thérèse M. Harrison1 and Lucilla Ronai3 Abstract Cellulose nitrate transparent plastic flm was used by photographers and movie flmmakers from its release in the 1880s to the 1950s. The storage of this material is a challenge for cultural institutions because of its instability and haz- ardous nature, as nitrate is highly fammable and deteriorates over time. Historically, cellulose acetate gradually began to replace cellulose nitrate as it is not fammable. Despite its non-fammable properties, leading to cellulose acetate being called ‘safety’ flm, over time it became clear that it also deteriorates in hazardous ways. Identifcation of cellu- lose nitrate and cellulose acetate in collections is necessary for preservation and risk management to collections and humans. Both cellulose nitrate and cellulose acetate are found in gallery, library, archive and museum photographic collections. As a result, identifcation and management of this material might be the responsibility of curators, librar- ians, archivists, collection managers, registrars or conservators, depending on the institution stafng and structure. Currently, there is no single identifcation method readily available to heritage institutions that meets the require- ments to identify and distinguish between cellulose nitrate and cellulose acetate reliably, non-destructively and rapidly. In this study samples from both the Sydney University Museums and Australian National Maritime Museum collections have been analysed using infrared total refectance spectroscopy, a novel approach which demonstrates great potential for rapid and non-invasive identifcation particularly when combined with multivariate statistical analysis methods. -
Production, Properties and Applications of Cellulose Acetate
Production, properties and applications of Cellulose Acetate http://www.tatvachintan.com Cellulose acetate (C6H7O2(OH)3 ), basically a chain of glucose molecules, is a heavily useful industrial compound that is used in many important products used worldwidely everyday. It is an acetate ester also known as Cellon or Rhodoid or Zyl or Zylonite. Mostly it is used as fiber material in industries. Production Procedure of Cellulose Acetate -Cellulose is derived from wood pulp or linters of cotton. This is not 100% pure cellulose. Instead, it is 6-7% concentrated cellulose in water. -In displacement and acetylation phase, firstly water or impure acetic base used to make cellulose suspension is replaced with 100% of pure acetic acid. This process is done with “displacement filter”. -Then the suspension is sent to Acetylation kneader where acetylation takes place and dough acetic syrup is produced. This syrup is mixed with certain amount of water to avoid excessive anhydride and introduce certain amoun of water for next stage of process. -This sough mixture is then sent for hydrolysis. After end of hydrolysis, we get Cellulose acetate with acetic acid content around 54-55 percent. -The syrup is then precipitated as acid-resin flakes. -The acid-resin flakes suspension is then sent into ripening rotary drum -From ripening rotary drum, it is fed into washing rotary filter where it is filtered . The washing rotary filter is fed with water and delivers diluted acid. -Spinning solution is then extruded through conveyer belts into a column of warm air and thus solvent is recovered. -Recovered solvent (Dry cellulose acetate) filaments are then stretched onto cones and bobbins. -
Review on the Biological Degradation of Polymers in Various Environments
materials Review Review on the Biological Degradation of Polymers in Various Environments Silvia Kliem * , Marc Kreutzbruck and Christian Bonten Institut für Kunststofftechnik, University of Stuttgart, Pfaffenwaldring 32, 70569 Stuttgart, Germany; [email protected] (M.K.); [email protected] (C.B.) * Correspondence: [email protected]; Tel.: +49-711-685-62831 Received: 10 September 2020; Accepted: 12 October 2020; Published: 15 October 2020 Abstract: Biodegradable plastics can make an important contribution to the struggle against increasing environmental pollution through plastics. However, biodegradability is a material property that is influenced by many factors. This review provides an overview of the main environmental conditions in which biodegradation takes place and then presents the degradability of numerous polymers. Polylactide (PLA), which is already available on an industrial scale, and the polyhydroxyalkanoates polyhydroxybutyrate (PHB) and polyhydroxybutyrate-co-valerate (PHBV), which are among the few plastics that have been proven to degrade in seawater, will be discussed in detail, followed by a summary of the degradability of further petroleum-, cellulose-, starch-, protein- and CO2-based biopolymers and some naturally occurring polymers. Keywords: biodegradable polymers; environmental pollution; end of life scenario; plastics in the environment 1. Introduction Plastics have become an indispensable part of everyday life. The various strengths of plastics come into their own in a wide variety of applications—packaging, clothing, car tires and much more. At the same time, however, the often-desired resistance to environmental influences and other stresses represents a major challenge. Plastic waste is increasingly found in the oceans, in rivers and in the ground, mostly as a result of human misconduct. -
Reliadisc™ Membrane Filters
WWW.AHLSTROM-MUNKSJO.COM ReliaDisc™ Membrane Filters Ahlstrom-Munksjö’s premium brands complete the portfolio in laboratory filtration. Ahlstrom-Munksjö offers gridded sterile membranes Ahlstrom-Munksjö ReliaDisc™ packed individually specifically designed to save time – Wide variety of polymers and pore sizes available when performing colony counting and microbiological quality control. These cellulose nitrate membranes are – High lot-to-lot reliability and reproducibility available in a 47 and 50 mm ready-to-use standard for consistent filtration quality size and support optimum colony growth. – Ultra-pure production facility in Germany Ahlstrom-Munksjö supplies a wide range of plain according to the highest quality control white non-sterile microfiltration membranes used to standards remove particles and microorganisms from various – Various filter diameters and pack sizes organic solvents and aqueous solutions. available on demand ™ Ahlstrom-Munksjö ReliaDisc - Membrane Filters are – Available in sterile or non-sterile offered in the most popular membrane materials for packaging diverse applications including: – Gridded membrane filters available – Particle retention and collection for easy colony counting – Sterile filtration of solutions – Microbiological applications for cell growth and colony counting – Particulate analysis – Air monitoring applications – Microbiological analysis of potable and waste waters Benefits and Characteristics Cellulose Acetate: low protein-binding, well suited for sterile filtration and clarification of aqueous solutions (pH 4-8), nutrient media, buffers, and sera. Also compatible with alcohol and oil. These hydrophilic membranes offer high and consistent flow rates. Maximum thermal stability: 180°C. Cellulose Nitrate: set standard in both analytical and microbiological filtration. Available in a wide range of pore size and is well suited for microbial analysis in water, food and beverage application in the pH range 4-8. -
The Acetate Negative Survey
THE ACETATE NEGATIVE SURVEY FINAL REPORT A PROJECT FUNDED BY THE UNIVERSITY OF LOUISVILLE AND THE NATIONAL MUSEUM ACT David G. Horvath University of Louisville Ekstrom Library Photographic Archives February 1987 The University of Louisville Photographic Archives Ekstrom Library Louisville, KY 40292 ACKNOWLEDGMENTS The subject of this study should be of great interest to those who are responsible for the preservation of historical photographic negatives. It has involved the cooperation and advice of many people who, piece by piece, have helped construct the method, process, and format of the final product. My wife, Mary has been very supportive and kept me from becoming discouraged by the endless details of the project. My colleagues at the Photographic Archives were most helpful in their constant encouragement, suggestions and warm friendship, especially Andy Anderson, Bill Carner, and Barbara Crawford; Michel C. Atlas was invaluable for her editorial contributions. I thank the National Museum Act of the Smithsonian Institution and the University of Louisville for their assistance and support, especially Barbara Schneider and Martha Bowman, the University of Louisville Librarian. I am indebted to all the institutions which allowed me access to their collections and provided me with a wealth of background information upon which much of this study is based. I owe special thanks to Ford Peatross, Carol Johnson, and Stephen Ostrow of the Library of Congress; Amy Doherty of the Special Collection Department at Syracuse University; Tim Peterson -
How to Make and Use a Film Viewer
Completing the Polarization Test How to Make and Use a Film Viewer The film viewer is valuable tool for distinguishing polyester film supports from cellulose acetate and cellulose nitrate film supports in a simple and no‐destructive manner (NOTE: It cannot distinguish between cellulose nitrate and cellulose acetate). This information is important to know when considering your park unit’s cold storage needs, as B&W polyester films are significantly more stable than cellulosic film supports and do not need cold storage. Therefore, such materials may be stored in normal environmental conditions (70 degrees /50%RH) within museum storage spaces. Ultimately, this may save considerable space within a freezer compartment or cold storage vault. Instructions on How to Make a Film Viewer Materials Needed: • Polarizing Filter sheet film (available at photo supply stores) • Archival Mat Board • 3M‐415 Clear, Double‐sided tape (1/4” width, recommended) • Tyvek tape (2 ¼” width, recommended) • Scissors • Scalpel/blade or Exacto knife • Paper cutter or blade for cutting mat board and polarizing filter/film To make a 6” x 8” viewer tool: 1. Cut mat board into two 6x8” pieces 2. Cut two 3x3” square pieces of polarizing filter/film 3. With mat board lying flat, use scalpel/blade or Exactor knife to cut out a 2x2” square in lower right corner. Square should be 1 inch from each edge. Cut these in both mat boards. 4. Place one board on top of the other so the squares match up (this is how the mat boards will look when taped together. You will be able to open it like a book. -
Cellulose Acetate / Plasticizer Systems: Structure, Morphology And
Cellulose acetate / plasticizer systems : structure, morphology and dynamics Congyu Bao To cite this version: Congyu Bao. Cellulose acetate / plasticizer systems : structure, morphology and dynamics. Polymers. Université Claude Bernard - Lyon I, 2015. English. NNT : 2015LYO10049. tel-01186696 HAL Id: tel-01186696 https://tel.archives-ouvertes.fr/tel-01186696 Submitted on 25 Aug 2015 HAL is a multi-disciplinary open access L’archive ouverte pluridisciplinaire HAL, est archive for the deposit and dissemination of sci- destinée au dépôt et à la diffusion de documents entific research documents, whether they are pub- scientifiques de niveau recherche, publiés ou non, lished or not. The documents may come from émanant des établissements d’enseignement et de teaching and research institutions in France or recherche français ou étrangers, des laboratoires abroad, or from public or private research centers. publics ou privés. N° d’ordre 49-2015 Année 2015 THESE DE L‘UNIVERSITE DE LYON Délivrée par L’UNIVERSITE CLAUDE BERNARD LYON 1 ECOLE DOCTORALE MATERIAUX DIPLOME DE DOCTORAT (Arrêté du 7 août 2006) Soutenue publiquement le 28 avril 2015 par Cong Yu BAO CELLULOSE ACETATE/PLASTICIZER SYSTEMS: STRUCTURE, MORPHOLOGY AND DYNAMICS Devant la commission d’examen M. Christian CARROT Rapporteur M. Laurent DAVID M. Laurent HEUX Rapporteur M. Didier LONG Directeur de thèse Mme. Valérie MIRI M. Yoshiyuki NISHIO M. Armin STEIN M. Caroll VERGELATI Encadrant industriel 1 Acknowledgement ACKNOWLEDGEMENT First, I would like to thank my PhD supervisor Dr. Didier LONG and my industrial advisor Dr. Caroll VERGELATI. Their advices and trust were one of the most important keys of my success. I would like to give the second acknowledgement to Acetow GmbH of Solvay group.