Synthetic Fibers and Textiles
Total Page:16
File Type:pdf, Size:1020Kb
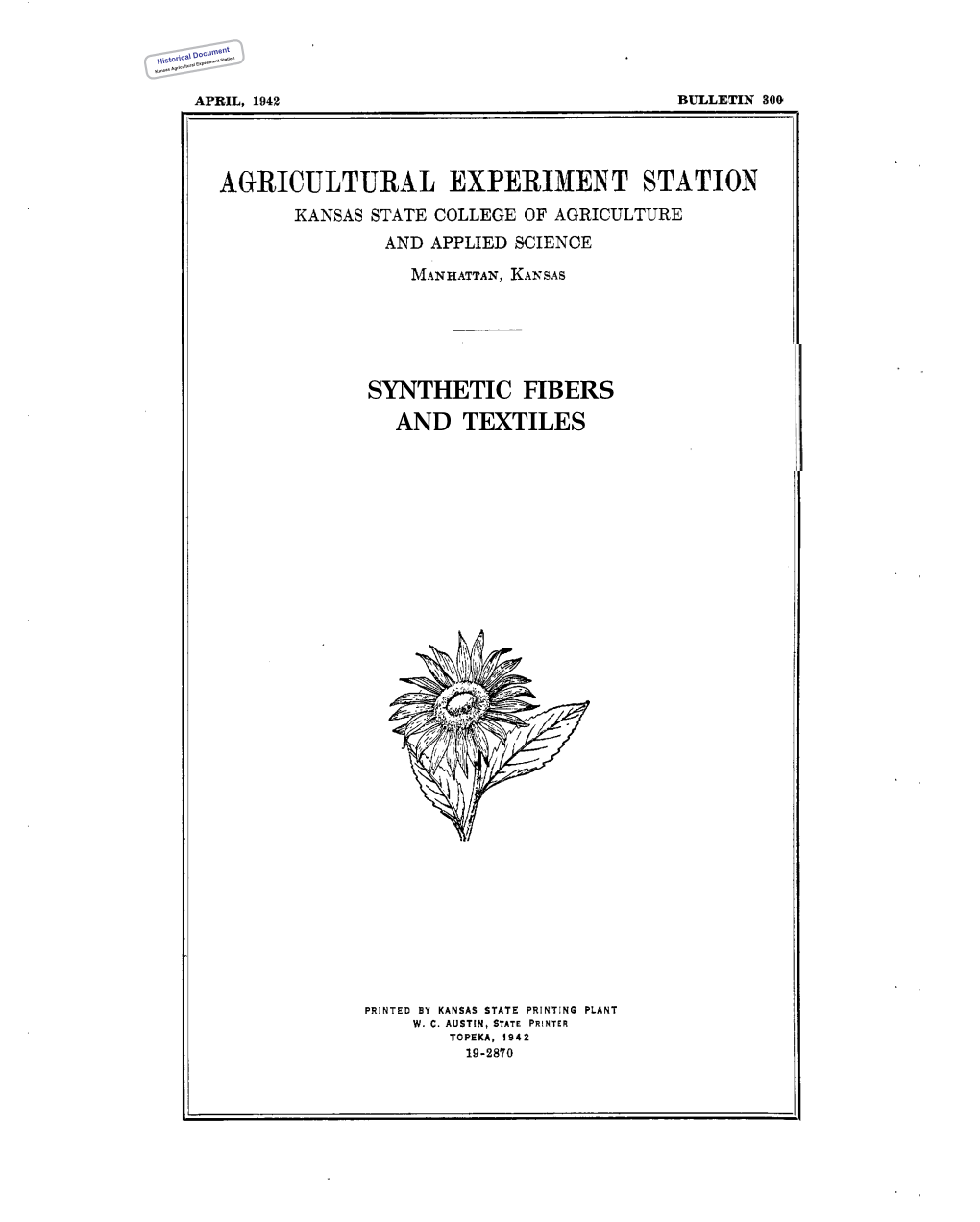
Load more
Recommended publications
-
Care Label Recommendations
CARE LABEL RECOMMENDATIONS RECOMMENDED CARE FOR APPAREL PRODUCTS Fiber content, fabric construction, color, product construction, finish applications and end use are all considered when determining recommended care. Following are recommended care instructions for Nordstrom Products, however; the product must be tested to confirm that the care label is suitable. GARMENT/ CONSTRUCTION/ FIBER CONTENT FABRICATION CARE LABEL Care ABREVIATION EMBELLISHMENTS Knits and Sweaters Acetate/Acetate Blends Knits / Sweaters K & S Dry Clean Only DCO Acrylic Sweater K & S Machine Wash Cold, Gentle Cycle With Like Colors Only Non-Chlorine Bleach If Needed MWC GC WLC ONCBIN TDL RP CIIN Tumble Dry Low, Remove Promptly Cool Iron If Needed Acrylic Gentle Or Open Construction, Chenille K & S Turn Garment Inside Out Or Loosely Knit Machine Wash Cold, Gentle Cycle With Like Colors TGIO MWC GC WLC ONCBIN R LFTD CIIN Only Non-Chlorine Bleach If Needed Reshape, Lay Flat To Dry Cool Iron If Needed Acrylic / Rayon Blends Sweaters / Gentle Or Open K & S Professionally Dry Clean Construction, Chenille Or Loosely Knit Short Cycle, No Steam PDC SC NS Acrylic / Wool Blends Sweaters with Embelishments K & S Hand Wash Cold, Separately Only Non-Chlorine Bleach If Needed, No Wring Or Twist Reshape, Lay Flat To Dry Cool Iron If Needed HWC S ONCBIN NWOT R LFTD CIIN DNID Do Not Iron Decoration Acrylic / Wool Blends Sweaters K & S Hand Wash Cold, Separately Only Non-Chlorine Bleach If Needed Roll In Towel To Remove Excess Moisture Reshape, Lay Flat To Dry HWC S ONCBIN RITTREM -
Choosing the Proper Short Cut Fiber for Your Nonwoven Web
Choosing The Proper Short Cut Fiber for Your Nonwoven Web ABSTRACT You have decided that your web needs a synthetic fiber. There are three important factors that have to be considered: generic type, diameter, and length. In order to make the right choice, it is important to know the chemical and physical characteristics of the numerous man-made fibers, and to understand what is meant by terms such as denier and denier per filament (dpf). PROPERTIES Denier Denier is a property that varies depending on the fiber type. It is defined as the weight in grams of 9,000 meters of fiber. The current standard of denier is 0.05 grams per 450 meters. Yarn is usually made up of numerous filaments. The denier of the yarn divided by its number of filaments is the denier per filament (dpf). Thus, denier per filament is a method of expressing the diameter of a fiber. Obviously, the smaller the denier per filament, the more filaments there are in the yarn. If a fairly closed, tight web is desired, then lower dpf fibers (1.5 or 3.0) are preferred. On the other hand, if high porosity is desired in the web, a larger dpf fiber - perhaps 6.0 or 12.0 - should be chosen. Here are the formulas for converting denier into microns, mils, or decitex: Diameter in microns = 11.89 x (denier / density in grams per milliliter)½ Diameter in mils = diameter in microns x .03937 Decitex = denier x 1.1 The following chart may be helpful. Our stock fibers are listed along with their density and the diameter in denier, micron, mils, and decitex for each: Diameter Generic Type -
Performance Evaluation of 3-D Basalt Fiber Reinforced Concrete & Basalt
Highway IDEA Program Performance Evaluation of 3-D Basalt Fiber Reinforced Concrete & Basalt Rod Reinforced Concrete Final Report for Highway IDEA Project 45 Prepared by: V Ramakrishnan and Neeraj S. Tolmare, South Dakota School of Mines & Technology, Rapid City, SD Vladimir B. Brik, Research & Technology, Inc., Madison, WI November 1998 IDEA PROGRAM F'INAL REPORT Contract No. NCHRP-45 IDEA Program Transportation Resea¡ch Board National Research Council November 1998 PERFORMANCE EVALUATION OF 3.I) BASALT ITIBER REINFORCED CONCRETE & BASALT R:D RETNFORCED CONCRETE V. Rarnalaishnan Neeraj S. Tolmare South Dakota School of Mines & Technolory, Rapid City, SD Principal Investigator: Madimir B. Brik Research & Technology, lnc., Madison, WI INNOVATIONS DESERVING EXPLORATORY ANALYSIS (IDEA) PROGRAMS MANAGED BY THE TRANSPORTATION RESEARCH BOARD (TRB) This NCHRP-IDEA investigation was completed as part of the National Cooperative Highway Research Program (NCHRP). The NCHRP-IDEA program is one of the four IDEA programs managed by the Transportation Research Board (TRB) to foster innovations in highway and intermodal surface transportation systems. The other three IDEA program areas are Transit-IDEA, which focuses on products and results for transit practice, in support of the Transit Cooperative Research Program (TCRP), Safety-IDEA, which focuses on motor carrier safety practice, in support of the Federal Motor Carrier Safety Administration and Federal Railroad Administration, and High Speed Rail-IDEA (HSR), which focuses on products and results for high speed rail practice, in support of the Federal Railroad Administration. The four IDEA program areas are integrated to promote the development and testing of nontraditional and innovative concepts, methods, and technologies for surface transportation systems. -
Interfacial Adhesion in Rayon/Nylon Sheath/Core Composite Fibers. Weiying Tao Louisiana State University and Agricultural & Mechanical College
Louisiana State University LSU Digital Commons LSU Historical Dissertations and Theses Graduate School 1991 Interfacial Adhesion in Rayon/Nylon Sheath/Core Composite Fibers. Weiying Tao Louisiana State University and Agricultural & Mechanical College Follow this and additional works at: https://digitalcommons.lsu.edu/gradschool_disstheses Recommended Citation Tao, Weiying, "Interfacial Adhesion in Rayon/Nylon Sheath/Core Composite Fibers." (1991). LSU Historical Dissertations and Theses. 5213. https://digitalcommons.lsu.edu/gradschool_disstheses/5213 This Dissertation is brought to you for free and open access by the Graduate School at LSU Digital Commons. It has been accepted for inclusion in LSU Historical Dissertations and Theses by an authorized administrator of LSU Digital Commons. For more information, please contact [email protected]. INFORMATION TO USERS This manuscript has been reproduced from the microfilm master. UMI films the text directly from the original or copy submitted. Thus, some thesis and dissertation copies are in typewriter face, while others may be from any type of computer printer. The quality of this reproduction is dependent upon the quality of the copy submitted. Broken or indistinct print, colored or poor quality illustrations and photographs, print bleedthrough, substandard margins, and improper alignment can adversely affect reproduction. In the unlikely event that the author did not send UMI a complete manuscript and there are missing pages, these will be noted. Also, if unauthorized copyright material had to be removed, a note will indicate the deletion. Oversize materials (e.g., maps, drawings, charts) are reproduced by sectioning the original, beginning at the upper left-hand corner and continuing from left to right in equal sections with small overlaps. -
Immersion Dyeing Nylon and Acetate Rayon Using Prosperse Disperse Dyes Please Read Directions Carefully Before Starting
Immersion Dyeing Nylon and Acetate Rayon using PROsperse Disperse Dyes Please read directions carefully before starting. For medium to dark shades, it is recommended that nylon be dyed with acid dyes, because disperse dyes lack acceptable fastness. Acetate rayon can only be dyed with disperse dyes and has acceptable fastness in all depths of shade with the disperse dyes. All Dyeing should be done in a stainless steel or enamelware container only. Never use aluminum pots. Use Pyrex or stainless steel measuring utensils and a large wooden dowel for stirring in the boiling dye bath. Always do test samples before working on a large project. Please Note: These dyes have the potential to stain any sink that is not made of stainless steel or fireclay ceramic. For additional information, visit our web site at www.prochemicalanddye.com. Wear rubber gloves, apron, or old clothes. Utensils used for dyeing should never be used for food preparation. Supplies PROsperse Disperse Dye Citric Acid Crystals or White Distilled Vinegar Synthrapol PRO Dye Activator or Soda Ash Procedure 1. Scour the fabric by machine washing in HOT 140F (60C) water, or by hand in a pot on the stove with 2 tsp (2 gm) PRO Dye Activator or Soda Ash and 2 tsp (2.5 ml) Synthrapol per pound of fabric (454 gm, or 3 to 4 yards of muslin weight fabric). Rinse thoroughly. This step does not add the dye fixative to the fabric; it prepares your fabric for dyeing by removing any dirt, oil or sizing. 2. Dissolve the dye. Thoroughly dissolve the desired amount of dye powder, from the chart below, in 1 cup (250 ml) of boiling water. -
New Hemp-Based Fiber Enhances Wet-Mix Shotcrete Performance
New Hemp-Based Fiber Enhances Wet-Mix Shotcrete Performance By Dudley R. (Rusty) Morgan, Lihe (John) Zhang, and Mike Pildysh n innovative processed natural hemp-based fiber without any fibers and mixtures with a synthetic (polypro- has been developed for use in concrete and shot- pylene) microfiber. These studies, conducted in Vancouver, A crete (wet- and dry-mix shotcrete processes) in lieu BC, Canada, demonstrated that when used at equivalent of conventional synthetic fibers, which are derived from fiber-volume addition rates, not only was the natural hemp- hydro-carbon (oil and/or gas) feedstock. A driving force based fiber more effective in mitigating plastic shrinkage behind this development has been the desire to produce cracking than synthetic microfiber but it also provided many a truly sustainable green fiber with dramatic reductions in additional benefits in the plastic and hardened concretes. This was particularly true for the wet-mix shotcrete process, CO2 emissions into the atmosphere during fiber production, compared to the synthetic (mainly polypropylene) fibers cur- where some marked benefits to the shotcrete application rently being used in the concrete and shotcrete industries. and finishing processes were found. Synthetic microfibers have mainly been used in concrete This article provides a summary of the findings from and shotcrete to help mitigate early-age plastic shrinkage the wet-mix shotcrete laboratory study. It also provides cracking. In the absence of adequate protection and initial observations from a subsequent full-scale field application curing, plastic shrinkage cracking has been an issue in the of wet-mix shotcrete with the natural hemp-based fiber, shotcrete industry. -
All About Fibers
RawRaw MaterialsMaterials ¾ More than half the mix is silica sand, the basic building block of any glass. ¾ Other ingredients are borates and trace amounts of specialty chemicals. Return © 2003, P. Joyce BatchBatch HouseHouse && FurnaceFurnace ¾ The materials are blended together in a bulk quantity, called the "batch." ¾ The blended mix is then fed into the furnace or "tank." ¾ The temperature is so high that the sand and other ingredients dissolve into molten glass. Return © 2003, P. Joyce BushingsBushings ¾The molten glass flows to numerous high heat-resistant platinum trays which have thousands of small, precisely drilled tubular openings, called "bushings." Return © 2003, P. Joyce FilamentsFilaments ¾This thin stream of molten glass is pulled and attenuated (drawn down) to a precise diameter, then quenched or cooled by air and water to fix this diameter and create a filament. Return © 2003, P. Joyce SizingSizing ¾The hair-like filaments are coated with an aqueous chemical mixture called a "sizing," which serves two main purposes: 1) protecting the filaments from each other during processing and handling, and 2) ensuring good adhesion of the glass fiber to the resin. Return © 2003, P. Joyce WindersWinders ¾ In most cases, the strand is wound onto high-speed winders which collect the continuous fiber glass into balls or "doffs.“ Single end roving ¾ Most of these packages are shipped directly to customers for such processes as pultrusion and filament winding. ¾ Doffs are heated in an oven to dry the chemical sizing. Return © 2003, P. Joyce IntermediateIntermediate PackagePackage ¾ In one type of winding operation, strands are collected into an "intermediate" package that is further processed in one of several ways. -
Eastman Naia™ Cellulosic Fiber Process Infographic —
S U The process starts with pine and eucalyptus S T wood sourced exclusively from sustainably A * managed and certified forests and IN plantations in North America and Brazil. A B LY M Sustainably sourced wood is turned into wood A ™ N pulp, ready to enter the Naia production process AG S in Eastman´s safe and eco-friendly facility in the ED FOREST U.S., where Naia™ is produced. PULP WOOD Wood pulp is combined with acetic acid to make ACETONE cellulose acetate granules. & Handled safely in a closed-loop ACETATE GRANULES CELLULOSE process, the granules are SAFE SOUND SOLVENT dissolved in acetone to make a USE cellulose acetate dope solution. Solvents used in the process are ™ recycled back into the system EASTMAN NAIA CELLULOSIC for reuse with no release into the environment. Used water is SPINNINGDRY FIBER PORTFOLIO cleaned and returned to the The dope is finally spun source with routine testing to through tiny holes in a PRODUCTION PROCESS ensure thriving biodiversity in spinneret and air-dried the local river. to form cellulose From tree to fiber, the Naia™ production process acetate fiber. Dry is designed to ensure the lowest environmental spinning Naia™ does not require any water. impact. With an extremely low water footprint, CLOSED LOOP Naia™ uses only sustainably sourced wood and safe solvents which are recycled and reused. Eastman Naia™ cellulosic fiber portfolio includes: • Naia™ cellulosic fiber, a cellulose acetate staple fiber • Naia™ cellulosic yarn, a cellulose acetate filament The cellulose acetate yarn is wound onto large SHIPPING- bobbins—ready for shipping to fabric mills and READY yarn Eastman warehouses around the world. -
Corning® Filtration Guide Innovative Products for Filtration and Ultrafiltration Table of Contents
Corning® Filtration Guide Innovative Products for Filtration and Ultrafiltration Table of Contents Filtration Selecting the Best Filter for Your Application .............................................................................. 1 Improving Filter Performance ......................................................................................................... 5 Spin-X® Tube Purification of DNA from Agarose Gels .............................................................. 6 Safety Precautions .............................................................................................................................. 7 Bibliography ......................................................................................................................................... 7 Ordering Information ........................................................................................................................ 8 Ultrafiltration ........................................................................................................................................ 12 Introduction ...................................................................................................................................... 12 Choosing the Right Concentrator Doesn’t Have to be Complicated .................................. 12 Choosing the Best Molecular Weight Cut-off Membrane .................................................... 14 Helpful Hints .................................................................................................................................... -
Fabric Fiber Content
Fabric Types, Count & Fiber Content Zweigart Linen Count Content Belfast 32 100% linen Afghans - 100% Polyacrylic Cashel 28 100% linen Abby 18ct Alba 14ct Almanac 14ct Cork 19 100% linen Anne Cloth 18ct Baby Snuggle 18ct Country Home 18ct Dublin 25 100% linen Diamond 18ct Gloria 14ct Hearthside 14ct Edinborough 36 100% linen Honeycomb 18ct Novara 14ct Patrice 14ct Fine Linen 45 55% linen + 45% cotton Afghans - 100% Cotton Glasgow 28 100% linen Anne Cloth 18ct Augusta 14 ct Novara 14ct Kingston 50 100% linen Teresa 14ct Newcastle 40 100% linen Afghans- Misc Normandie 55% cotton + 45% linen Pastel LinenD 28 52% cotton + 48% linen Gloria 14ct 70% rayon + 30% linen Pearl Linen 20, 25, 28 60% polyester + 40% linen Merino 28ct 100% Wool Mosaik 18ct 52% cotton + 42% rayon Patterned Count Content Tannenbaum 18ct 52% cotton + 42% rayon Cottage Huck 14 100% cotton Aida Weave Count Content Belinda 20 52% cotton + 48% rayon Diana 20 52% cotton + 48% rayon Aida 8, 11, 14, 16, 18 100% cotton Newport 28 100% linen Country AidaD 7 100% polyacrylic Sambuca 28 60% polyester + 40% linen Damask Aida 11,14,18 52% cotton + 48% rayon Saronno 28 52% cotton + 48% rayon GoldauD 7 55% rayon + Shenandoah 28 55% linen + 45% rayon 40% cotton + 5% metallic Hardanger 22 100% cotton Canvas Count Content Hearthstone 14 60% cotton + 40% linen Congress 24 100% cotton Herta 6 100% cotton Congressa 24 100% cotton Huck 14 100% cotton Cordova 22 100% cotton Klostern 7 60% rayon + 40% cotton Double Mesh 5, 6.5, 7.5, 10, 12, Linen Hardanger 22 100% linen 14, 16, 18, 20 100% cotton -
Evaluation of the Physical and Diagnostic Nature of Swabs W
EVALUATION OF THE PHYSICAL AND DIAGNOSTIC NATURE OF SWABS W. Nugent, M.D.1, M.J. Russell1 S. Beck 2, and G.P. Leonardi, Ph.D.1,3 NASSAU 1 M44 Department of Pathology, Nassau University Medical Center, East Meadow, NY ; UNIVERSITY Department of Biology, Nassau Community College, Garden City, NY2 and Sunrise Medical Laboratories, Hauppauge, NY3 medicalcenter Abstract: Conclusions: Proper specimen collection is the single most important factor in obtaining a reliable and and reweighed. Following addition of water (1.0ml), tubes were shaken at high speeds ß Fiber confi guration and size of the nylon-fl ocked swab allowed for greater accurate diagnostic result. Swabs are often employed to collect specimens for a variety for 1 minute, followed by centrifugation using a table-top Hermle Z180M centrifuge absorbance than the actual nylon material itself. of microbiologic assays. A novel, nylon-tipped, “fl ocked“ swab (Copan, Inc; Corona, CA) (Universal Labnet Co., Edison, NJ) for 5 minutes at maximum speed. Unabsorbed water FIG. 1 FIG. 2 has recently become commercially available. Unlike conventional swabs in which fi bers ß There are numerous other factors, not presently examined, which can aff ect was removed by decanting and wiping the inner tube surface with bibulous paper, swab performance. are woven on a shaft material, fl ocked swabs have a “one piece” construction with nylon and the tube was reweighed. This exercise was repeated twice. fi bers radiating from the shaft tip. This construction may enhance the amount of specimen ß Nevertheless, our data suggests that using of nylon-fl ocked swabs would available for diagnostic testing. -
Effect of Hybridization of Glass/Kevlar Fiber on Mechanical Properties of Bast Reinforced Polymer Composites: a Review
View metadata, citation and similar papers at core.ac.uk brought to you by CORE provided by Ivy Union Publishing (E-Journals) American Journal of Polymer Science & Engineering Kumar S et al., American Journal of Polymerhttp://www.ivyunion.org/index.php/ajpse/ Science & Engineering 2017, 5:13-23 Page 1 of 11 Review Article Effect of Hybridization of Glass/kevlar Fiber on Mechanical Properties of Bast Reinforced Polymer Composites: A Review Sandeep Kumar1, Lalta Prasad2, and Vinay Kumar Patel2* 1 Mechanical Engineering Department, S.O.E.T., H.N.B. Garhwal University Srinagar Garhwal- 246174, Uttarakhand, India 2 Department of Mechanical Engineering, Govind Ballabh Pant Engineering College Pauri Garhwal, Uttarakhand, India Abstract Natural fibres are gaining more and more interest as reinforcing materials for polymer composite due to their environmental and economical benefits. Bast fibers is a prominent reinforcement for use in polymeric materials because of its low specific weight and cost, eco-friendly and abundantly available in nature. Several authors manifest the cellulosic fibers based polymeric composites as advantageously used in automobile industries and structural applications, but certain problems have been associated during usage of such fiber such as high water/mosture-uptake and low strength than inorganic fibers. These problems have been reduced to a major extent with enhancements in mechanical properties by the researchers through hybridization of these natural fiber based composites with synthetic fiber (glass/Kevlar). In the present article, we reviewed the effect of hybridization of glass/Kevlar synthetic fibers on mechanical properties of bast fiber (jute, hemp, kenaf, flax) reinforced polymer composites. Keywords : Bast fiber; glass /kevlar fibre; hybrid composites; Mechanical properties Received : November 13, 2016; Accepted: January 8, 2017; Published: January 25, 2017 Competing Interests: The authors have declared that no competing interests exist.