Preparation of Modified Acetate Fiber with Sodium Hydroxide Haiyan Zhang
Total Page:16
File Type:pdf, Size:1020Kb
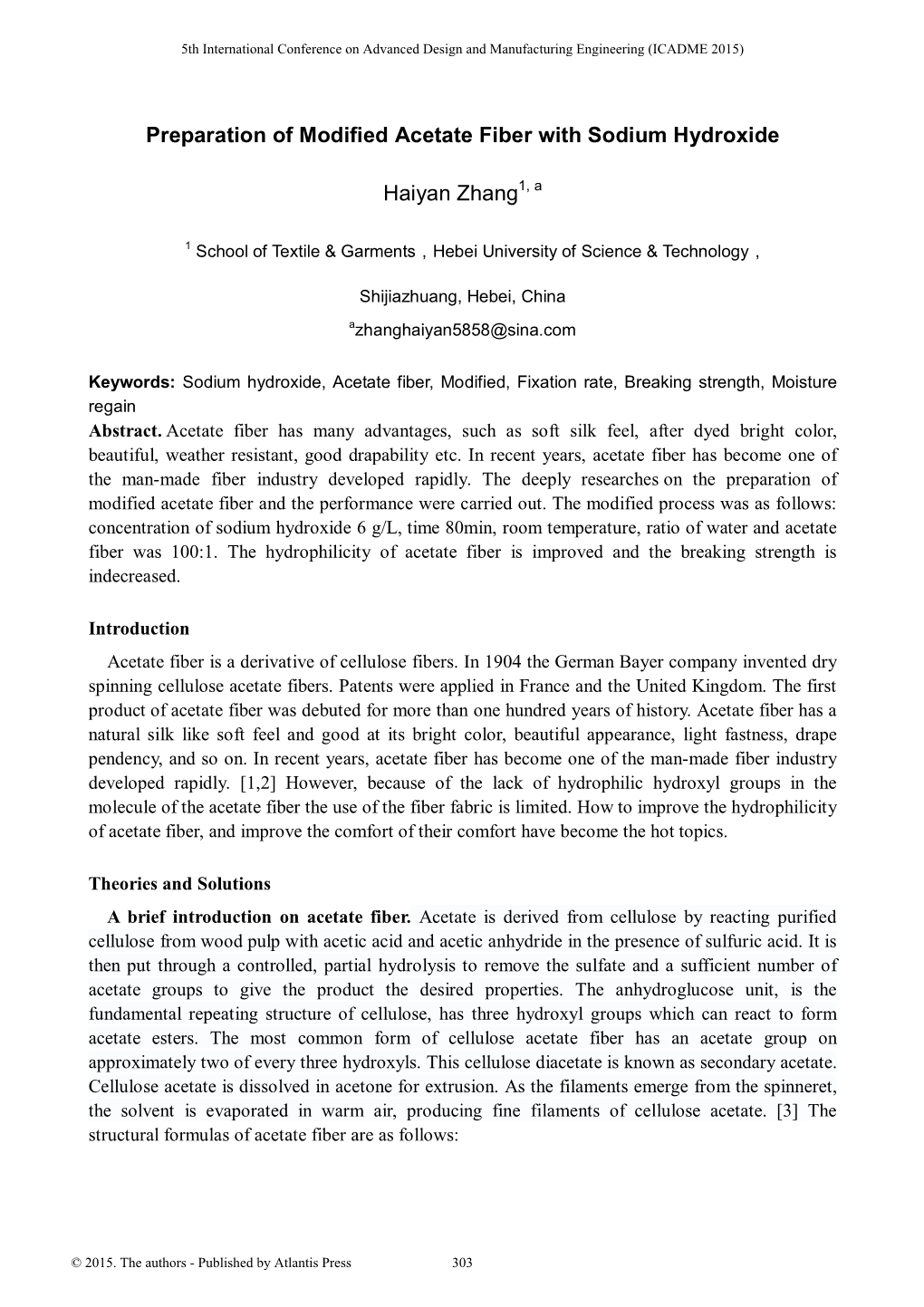
Load more
Recommended publications
-
Preparation and Physical Properties of the Biocomposite, Cellulose Diacetate/Kenaf Fiber Sized with Poly(Vinyl Alcohol)
Macromolecular Research, Vol. 18, No. 6, pp 566-570 (2010) www.springer.com/13233 DOI 10.1007/s13233-010-0611-0 Preparation and Physical Properties of the Biocomposite, Cellulose Diacetate/Kenaf Fiber Sized with Poly(vinyl alcohol) Chang-Kyu Lee, Mi Suk Cho, In Hoi Kim, and Youngkwan Lee* Department of Chemical Engineering, Sungkyunkwan University, Suwon 440-746, Korea Jae Do Nam Department of Polymer Engineering, Sungkyunkwan University, Suwon 440-746, Korea Received November 2, 2009; Revised February 5, 2010; Accepted February 9, 2010 Abstract: Cellulose diacetate (CDA)/kenaf fiber biocomposites were prepared using a melting process. In order to increase the fiber density and compatibilize the kenaf fiber with CDA, the fiber was sized with poly(vinyl alco- hol)(PVA). The sized kenaf fiber was compounded with the plasticized CDA using a twin screw extruder, and the opti- mal processing conditions were determined. The incorporated kenaf fiber improved the mechanical and thermal properties of CDA. In the case of the composites containing 30 wt% kenaf fibers, the tensile strength and modulus increased almost 2 and 3 fold, which were 85.6 MPa and 4831 MPa, respectively. The PVA treated kenaf fiber showed better adhesion to the CDA matrix. Keywords: cellulose diacetate, kenaf fiber, PVA, sizing. Introduction CDA, its processability is improved, whereas its unique mechanical properties and thermal stability are deteriorated. Synthetic polymers are widely used in everyday life and In order to increase the physical strength of CDA, the use of are increasingly being used in more diverse areas due to various reinforcing agents were generally accepted.7-9 Natu- their easy processability, permanent stability, low price, and ral fiber is completely biodegraded in the natural environ- antibacterial properties. -
Production of Cellulosic Polymers from Agricultural Wastes
ISSN: 0973-4945; CODEN ECJHAO E-Journal of Chemistry http://www.e-journals.net Vol. 5, No. 1, pp. 81-85, January 2008 Production of Cellulosic Polymers from Agricultural Wastes A.U. ISRAEL, I.B. OBOT *, S. A. UMOREN, V. MKPENIE and J.E. ASUQUO Department of Chemistry,Faculty of Science, University of Uyo, P.M.B. 1017, Uyo, Nigeria. [email protected] Received 12 May 2007; Accepted 10 July 2007 Abstract: Cellulosic polymers namely cellulose, di-and triacetate were produced from fourteen agricultural wastes; Branch and fiber after oil extraction from oil palm ( Elais guineensis ), raffia, piassava, bamboo pulp, bamboo bark from raphia palm ( Raphia hookeri ), stem and cob of maize plant (Zea mays ), fruit fiber from coconut fruit ( Cocos nucifera ), sawdusts from cotton tree ( Cossypium hirsutum ), pear wood ( Manilkara obovata ), stem of Southern gamba green (Andropogon tectorus), sugarcane baggase ( Saccharium officinarum ) and plantain stem (Musa paradisiaca). They were subjected to soda pulping and hypochlorite bleaching system. Results obtained show that pulp yield from these materials were: 70.00, 39.59, 55.40, 86.00, 84.60, 80.00, 40.84, 81.67, 35.70, 69.11, 4.54, 47.19, 31.70 and 52.44% respectively. The pulps were acetylated with acetic anhydride in ethanoic acid catalyzed by conc. H 2SO 4 to obtain cellulose derivatives (Cellulose diacetate and triacetate). The cellulose diacetate yields were 41.20, 17.85, 23.13, 20.80, 20.23, 20.00, 39.00, 44.00, 18.80, 20.75, 20.03, 41.20, 44.00, and 39.00% respectively while the results obtained as average of four determinations for cellulose triacetate yields were: 52.00, 51.00, 43.10, 46.60, 49.00, 35.00, 40.60, 54.00, 57.50, 62.52, 35.70. -
Benefits of APTA: Case of Cambodia
03_Study on APTA benefits for Cambodia_August 2009.doc DRAFT Benefits of APTA: Case of Cambodia BY RAJAN SUDESH RATNA1 PROFESSOR CENTRE FOR WTO STUDIES INDIAN INSTITUTE OF FOREIGN TRADE NEW DELHI [email protected] [email protected] 1 The views expressed by author are purely personal and does not reflect the views of the Institute where he is currently working. 1 03_Study on APTA benefits for Cambodia_August 2009.doc DRAFT Benefits of joining APTA: Case of Cambodia Introduction The Asia-Pacific Trade Agreement (APTA), previously known as the Bangkok Agreement (BA), was signed in 1975. It is the oldest preferential trade agreement between developing countries in the Asia-Pacific region that aims at promoting economic development through a continuous process of trade expansion and furthering international economic cooperation through the adoption of mutually beneficial trade liberalization measures. Current members include Bangladesh, China, India, Lao PDR, Republic of Korea and Sri Lanka. ESCAP Secretariat provides secretarial support to APTA. The text of the agreement was revised during the Third Round of negotiations and the list of items on which tariff concessions were exchanged expanded to more than 4,000 items. The Members also adopted common rules of origin with minimum local value content requirement of 45 per cent f.o.b. (35 per cent for LDCs) for availing the tariff concessions. The rules are simple and easy to operate. APTA allows any developing member country of UNESCAP to become a member. This agreement links three major economies of Asia namely China, India & Republic of Korea and thus provides preferential market access to one of the largest market in the world. -
Eastman Naia™ Cellulosic Fiber Process Infographic —
S U The process starts with pine and eucalyptus S T wood sourced exclusively from sustainably A * managed and certified forests and IN plantations in North America and Brazil. A B LY M Sustainably sourced wood is turned into wood A ™ N pulp, ready to enter the Naia production process AG S in Eastman´s safe and eco-friendly facility in the ED FOREST U.S., where Naia™ is produced. PULP WOOD Wood pulp is combined with acetic acid to make ACETONE cellulose acetate granules. & Handled safely in a closed-loop ACETATE GRANULES CELLULOSE process, the granules are SAFE SOUND SOLVENT dissolved in acetone to make a USE cellulose acetate dope solution. Solvents used in the process are ™ recycled back into the system EASTMAN NAIA CELLULOSIC for reuse with no release into the environment. Used water is SPINNINGDRY FIBER PORTFOLIO cleaned and returned to the The dope is finally spun source with routine testing to through tiny holes in a PRODUCTION PROCESS ensure thriving biodiversity in spinneret and air-dried the local river. to form cellulose From tree to fiber, the Naia™ production process acetate fiber. Dry is designed to ensure the lowest environmental spinning Naia™ does not require any water. impact. With an extremely low water footprint, CLOSED LOOP Naia™ uses only sustainably sourced wood and safe solvents which are recycled and reused. Eastman Naia™ cellulosic fiber portfolio includes: • Naia™ cellulosic fiber, a cellulose acetate staple fiber • Naia™ cellulosic yarn, a cellulose acetate filament The cellulose acetate yarn is wound onto large SHIPPING- bobbins—ready for shipping to fabric mills and READY yarn Eastman warehouses around the world. -
Performance Analysis of Blended Membranes of Cellulose Acetate with Variable Degree of Acetylation for CO2/CH4 Separation
membranes Article Performance Analysis of Blended Membranes of Cellulose Acetate with Variable Degree of Acetylation for CO2/CH4 Separation Ayesha Raza 1,*, Sarah Farrukh 1, Arshad Hussain 1, Imranullah Khan 1, Mohd Hafiz Dzarfan Othman 2 and Muhammad Ahsan 1 1 Department of Chemical Engineering, School of Chemical and Materials Engineering, National University of Sciences and Technology, Islamabad 44000, Pakistan; [email protected] (S.F.); [email protected] (A.H.); [email protected] (I.K.); [email protected] (M.A.) 2 Advanced Membrane Technology Research Centre (AMTEC), Faculty of Chemical and Energy Engineering, University of Technology Malaysia, Skudai 81310, Malaysia; hafi[email protected] * Correspondence: [email protected] Abstract: The separation and capture of CO2 have become an urgent and important agenda because of the CO2-induced global warming and the requirement of industrial products. Membrane-based technologies have proven to be a promising alternative for CO2 separations. To make the gas- separation membrane process more competitive, productive membrane with high gas permeability and high selectivity is crucial. Herein, we developed new cellulose triacetate (CTA) and cellulose diacetate (CDA) blended membranes for CO2 separations. The CTA and CDA blends were chosen because they have similar chemical structures, good separation performance, and its economical Citation: Raza, A.; Farrukh, S.; and green nature. The best position in Robeson’s upper bound curve at 5 bar was obtained with Hussain, A.; Khan, I.; Othman, M.H.D.; Ahsan, M. Performance the membrane containing 80 wt.% CTA and 20 wt.% CDA, which shows the CO2 permeability Analysis of Blended Membranes of of 17.32 barrer and CO2/CH4 selectivity of 18.55. -
Corning® Filtration Guide Innovative Products for Filtration and Ultrafiltration Table of Contents
Corning® Filtration Guide Innovative Products for Filtration and Ultrafiltration Table of Contents Filtration Selecting the Best Filter for Your Application .............................................................................. 1 Improving Filter Performance ......................................................................................................... 5 Spin-X® Tube Purification of DNA from Agarose Gels .............................................................. 6 Safety Precautions .............................................................................................................................. 7 Bibliography ......................................................................................................................................... 7 Ordering Information ........................................................................................................................ 8 Ultrafiltration ........................................................................................................................................ 12 Introduction ...................................................................................................................................... 12 Choosing the Right Concentrator Doesn’t Have to be Complicated .................................. 12 Choosing the Best Molecular Weight Cut-off Membrane .................................................... 14 Helpful Hints .................................................................................................................................... -
United States Patent Office Patented Feb
2,780,511 United States Patent Office Patented Feb. 5, 1957 2 advantageous when applied to the viscose staple rayon 2,780,511 having a permanent structural crimp. This crimp, in con trast to the mechanically applied crimp of the thermo oD of MAKING CELLULOSE ACETATE plastic fibers, originates in the fine inner structure of the XTILE FIBERS BY ACETYLIZATION OF fibers and is permanent through spinning, weaving, Wash GENERATED CELLULOSE FIBERs ing, ironing and other similar fabric treatments, which Takagi, Tokyo, Japan, assignor to Toho Rayon makes such viscose fiber particularly valuable. The per Co., Ltd., Tokyo, Japan, a corporation of Japan manent structural crimp of such viscose staple rayon is No Drawing. Application May 14, 1953, retained throughout the acetylation process of the present ... " . Serial No. 355,150 10 invention. - The invention may be applied to continuous cellulosic 3 Claims. (CI. 8-121) fibers which may be lightly twisted together to form a yarn or rope prior to acetylation, or it may be applied to a This invention relates to the preparation of cellulose mass of loose staple fibers which may be conveyed through acetate fiber having an acetic acid content of at least 40% 5 the several steps of the process on a suitable belt or wire by vapor phase acetylation of cellulosic fibers while re mesh conveyor, or the like. If desired, the cellulosic taining the fiber structure. fibers, either continuous or staple, may be loosely woven It has previously been proposed to acetylate cellulosic or knitted to form a fabric which may then be subjected fibers while retaining their fiber structure by carrying out to the acetylation process of the present invention. -
Environmental Aspects of Clarifoil Cellulose Diacetate Film
Data sheet code: CFL 120 Revision number: 6 Date of revision: April 2018 Number of pages: 1 of 8 Environmental Aspects of Clarifoil Cellulose Diacetate Film Clarifoil is the trade name for a range of films based on cellulose diacetate. From very glossy, highly transparent films to semi-matt and matt films, covering a thickness range from 14µ - 500µ. The properties of these films reflect their cellulosic origins and thus offer an attractive combination of environmental features. Their cellulosic nature also makes Clarifoil films ideally suited to be used in contact with paper and board in packaging applications such as window cartons and film- laminated printed material. Clarifoil Manufacture The diacetate raw material is produced by treating cellulose from wood pulp or cotton linters with acetic anhydride. The resulting flake is mixed with a small proportion of plasticiser and traces of anti-block compound and is cast onto a continuous band to produce a non-oriented film with exceptional optical properties. The major raw material, cellulose, comes from PEFC (Program for the Endorsement of Forest CertificationTM) managed forestry. The PEFC program is an international non-profit, non- governmental organization dedicated to promoting Sustainable Forest Management (SFM) through independent third-party certification. PEFC works throughout the entire forest supply chain to promote good practice in the forest and to ensure that timber and non-timber forest products are produced with respect for the highest ecological, social and ethical standards. The trees that are harvested are naturally grown and are certified as 100% GMO free. For more information please visit http://www.pefc.org Clarifoil is distinguished from most other thermoplastic films in that it comes from a sustainable resource and its main component is not derived from fossil fuels. -
Environmental Testing for Water Physical Analysis
GE Healthcare Great savings Environmental testing for water Physical analysis Solids analysis The level of suspended solids in a water sample is determined Suspended solids measurements are typically by pouring a carefully measured volume of water through performed using glass fiber filter circles that need a preweighed filter with a specified pore size, drying additional preparation prior to use. However, GE has the filter to remove the water, and then weighing the developed ready-to-use 934-AH RTU glass fiber filters, filter again. The weight gain of the filter is a dry weight which are supplied in a prewashed and preweighed measure of the particulates present in the water sample format and enable considerable time savings in the expressed in units derived or calculated from the volume laboratory. 934-AH RTU filters also provide reproducible of water filtered (typically milligrams per liter). results and low background contamination. Prepare filter per Heat retained solids on Evaporate liquid filtrate Calculate weight method by washing, Filter and filter to 500°C and measure and weigh the retained of suspended solids drying, and weighing dry sample weight change to calculate solute to calculate captured on filter as appropriate volatile solids dissolved solids Fig 1. Total solids analysis workflow using filtration-based methods. What are you testing for? Product Characteristics and benefits Solids, including: GF/C™ • Conform to requirements of standard methodologies: GF/C for EN 872 (Fig 2); 934-AH for Standard Method 2540D • total suspended 934-AH™ • High loading capacity enabling filtration of very • total dissolved glass fiber filters turbid samples Ordering information p. -
How to Choose the Right Filter > Membrane Selection Guide
> Membrane selection guide > UptiDisc™ technology Cellulose Acetate - CA: Ideal hydrophilic membrane for the filtration of aqueous samples, with low PVDF - polyvinylidene difluoride: solvent resistance. Hydrophilic membrane with a good solvent resistance. Ideal for filtration Less chemical resistance compare to RC membranes. of HPLC mobile phase solvents and for most of biological samples. A Glass pre-filter membrane is used for tissue culture media filtration, biolo- PVDF membrane is also considered as having the lowest protein binding. gical sample filtration, as clarification and sterilization of aqueous samples. Very low protein binding (binding < PVDF, PS), the Glass pre-filter PTFE - polytetrafluoroethylene: increases filtrate volume yield by 3. Hydrophobic membrane chemically resistant to solvents, acids and bases. Regenerated Cellulose - RC: This membrane is ideal for filtration of chromatography solvents, with no Hydrophilic membrane that has the same properties as cellulose acetate extractable due to the PTFEmembrane. but stable with most HPLC solvents. This membrane is used for HPLC solvents, degassing, and filtration and is PP - polypropylene: compatible with aqueous samples in a pH range from 2 to 12. High resistance, may be used with virtually all solvents, acids and bases. With a non-specific low protein binding, this membrane is chosen for protein filtration when maximum yield of recovery is needed. Glass Fiber - GF: Commonly used as a pre-filter for most of filtrations devices. Nylon - polyamide 6-6: It increase by 3 times the filtration capacity. Commonly used for HPLC samples filtration prior to injection, with good Typically used for crude samples and used for the cleaning and purifica- solvent resistance. Having hydrophilic properties, it gives good results with tion of DNA. -
Functionalization of Cellulose Acetate Fibers with Engineered Cutinases
Functionalization of Cellulose Acetate Fibers with Engineered Cutinases Teresa Matama´, Rita Arau´jo Textile Engineering Dept., University of Minho, Campus Azure´m, 4800-058 Guimara˜es, Portugal Georg M. Gu¨bitz Dept. of Environmental Biotechnology, Graz University of Technology, 8010 Graz, Austria Margarida Casal Dept. of Biology, CBMA – Centre of Molecular and Environmental Biology, University of Minho, Campus Gualtar, 4710-057 Braga, Portugal Artur Cavaco-Paulo Textile Engineering Dept., University of Minho, Campus Azure´m, 4800-058 Guimara˜es, Portugal DOI 10.1002/btpr.364 Published online December 15, 2009 in Wiley InterScience (www.interscience.wiley.com). In the present work, we describe for the first time the specific role of cutinase on surface modification of cellulose acetate fibers. Cutinase exhibits acetyl esterase activity on diacetate and triacetate of 0.010 U and 0.007 U, respectively. An increase on the hydroxyl groups at the fiber surface of 25% for diacetate and 317% for triacetate, after a 24 h treatment, is estimated by an indirect assay. Aiming at further improvement of cutinase affinity toward cellulose acetate, chimeric cutinases are genetically engineered by fusing the 3 0-end coding sequence with a bacterial or a fungal carbohydrate-binding module and varying the linker DNA sequence. A comparative analysis of these genetic constructions is presented showing that, the superficial regeneration of cellulose hydrophilicity and reactivity on highly substi- tuted cellulose acetates is achieved by chimeric cutinases. VC 2009 American Institute of Chemical Engineers Biotechnol. Prog., 26: 636–643, 2010 Keywords: carbohydrate esterase, functionalization of polymers, cellulose-binding domain, biodegradable Introduction easier control, being environmental friendly processes and performing specific nondestructive transformations on poly- Cellulose is the most abundant natural polymer and it is a mer surfaces (Gu¨bitz and Cavaco-Paulo, 2003, 2008). -
IPI Storage Guide for Acetate Film
IPI Storage Guide for Acetate Film James M. Reilly • Director, Image Permanence Institute Instructions for Using the Wheel, Graphs, and Table Basic Strategy for Film Preservation l The IPI Storage Guide for Acetate Film provides an overview of environmental specifications for film storage. It explains the relationship between temperature, relative humidity (RH), and “vinegar syndrome,” the slow chemical decomposition of acetate plastics leading to loss of their value in a film collection. l The main purpose of the Guide is to help collection managers evaluate the quality of the storage environment they provide for their film. The Guide is not meant to predict the life of any individual film; it merely uses predicted life span as a yardstick to measure the quality of the storage environment. l CONTENTS What the Guide Is (and What It Is Not) ................... 2 The Wheel ................................................................ 4 Time Contours for Vinegar Syndrome .................... 7 The Time Out of Storage Table ............................... 8 Chemical Deterioration of Film Bases .................. 10 The Course of the Vinegar Syndrome .................. 13 Does the Guide Apply to Nitrate Film? ................. 15 Polyester Base Film ............................................... 15 The General Philosophy of Film Storage .............. 16 History of Film Supports ........................................ 21 References ............................................................. 23 ANSI and ISO Film Storage Standards ................. 24 Rochester Institute of Technology, 70 Lomb Memorial Drive, Rochester, NY 14623-5604 Phone: 716-475-5199 Fax: 716-475-7230 Image Permanence Institute Image Permanence l WHAT THE GUIDE IS (AND WHAT IT IS NOT) The IPI Storage Guide for Acetate Film is a tool for evaluating and planning storage environments for acetate base photographic film, cinema film, and microfilms.