Influence of Machine Fleet and Operation on Solid Waste Compaction
Total Page:16
File Type:pdf, Size:1020Kb
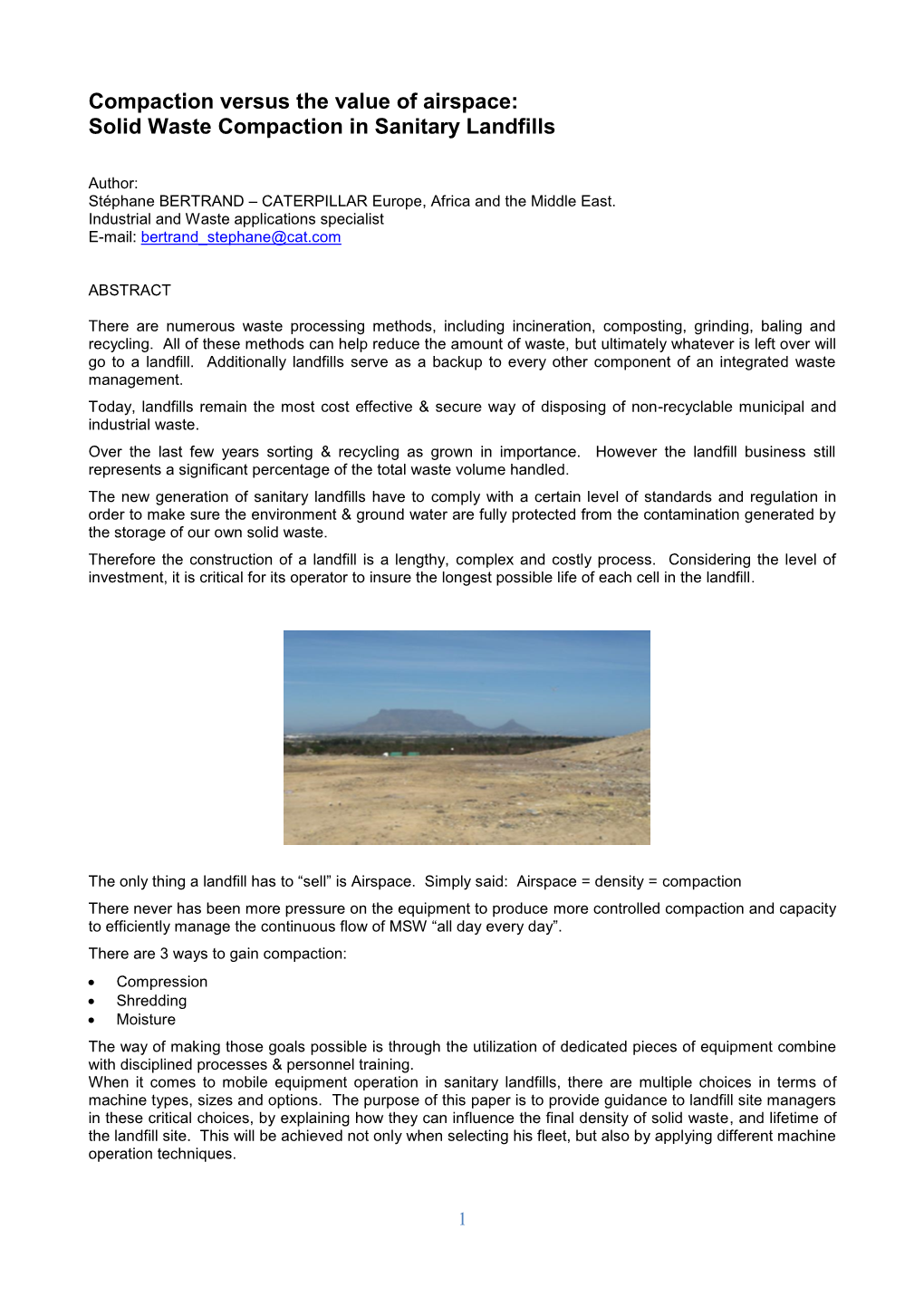
Load more
Recommended publications
-
Municipal Solid Waste Landfill Operation and Management Workbook
MUNICIPAL SOLID WASTE LANDFILL OPERATION AND MANAGEMENT WORKBOOK Revised April 2018 Preface In many ways, constructing, operating and maintaining a municipal solid waste landfill is similar to constructing, operating, and maintaining a highway, dam, canal, bridge, or other engineered structure. The most important similarity is that landfills, like other engineered structures, must be constructed and operated in a manner that will provide safe, long-term, and reliable service to the communities they serve. Proper design, construction, operation, monitoring, closure and post-closure care are critical because after disposal the waste can be a threat to human health and the environment for decades to centuries. This workbook is intended to provide municipal landfill operators and managers in Wyoming with the fundamental knowledge and technical background necessary to ensure that landfills are operated efficiently, effectively, and in a manner that is protective of human health and the environment. This workbook contains information regarding basic construction and operation activities that are encountered on a routine basis at most landfills. The basic procedures and fundamental elements of landfill permitting, construction management, monitoring, closure, post-closure care, and financial assurance are also addressed. The workbook includes informative tips and information that landfill operators and managers can use to conserve landfill space, minimize the potential for pollution, reduce operating costs, and comply with applicable rules and regulations. In addition to this workbook, operators and managers need to become familiar with the Wyoming Solid Waste Rules and Regulations applicable to municipal solid waste. The DEQ also provides numerous guidelines that may help understand regulatory requirements in more detail. -
Radioactive Waste
Radioactive Waste 07/05/2011 1 Regulations 2 Regulations 1. Nuclear Regulatory Commission (NRC) 10 CFR 20 Subpart K. Various approved options for radioactive waste disposal. (See also Appendix F) 10 CFR 35.92. Decay in storage of medically used byproduct material. 10 CFR 60. Disposal of high-level wastes in geologic repositories. 10 CFR 61. Shallow land disposal of low level waste. 10 CFR 62. Criteria and procedures for emergency access to non-Federal and regional low-level waste disposal facilities. 10 CFR 63. Disposal of high-level rad waste at Yucca Mountain, NV 10 CFR 71 Subpart H. Quality assurance for waste packaging and transportation. 10 CFR 72. High level waste storage at an MRS 3 Regulations 2. Department of Energy (DOE) DOE Order 435.1 Radioactive Waste Management. General Requirements regarding radioactive waste. 10 CFR 960. General Guidelines for the Recommendation of Sites for the Nuclear Waste Repositories. Site selection guidelines for a waste repository. The following are not regulations but they provide guidance regarding the implementation of DOE Order 435.1: DOE Manual 435.1-1. Radioactive Waste Management Manual. Describes the requirements and establishes specific responsibilities for implementing DOE O 435.1. DOE Guide 435.1-1. Suggestions and acceptable ways of implementing DOE M 435.1-1 4 Regulations 3. Environmental Protection Agency 40 CFR 191. Environmental Standards for the Disposal of Spent Nuclear Fuel, High-level and Transuranic Radioactive Wastes. Protection for the public over the next 10,000 years from the disposal of high-level and transuranic wastes. 4. Department of Transportation 49 CFR Parts 171 to 177. -
Bioreactor Brochure
City of Columbia, Missouri Glossary of Terms Questions? Public Works Department Aerobic: living or existing in the presence of oxygen For more information, visit our web page at Airspace: the available space in a cell where trash is placed www.GoColumbiaMo.com (GoLandfill) or call the for disposal Solid Waste Division at 573-874-6290. BIOREACTOR Anaerobic: living or existing in the absence of free oxygen LANDFILL Bioreactor: a controlled landfill or landfill disposal cell MORE INFO: US EPA where liquid and gas conditions are actively managed in WASTE STABILIZATION order to accelerate or enhance biostabilization of waste GENERAL: http://www.epa.gov/garbage/landfill/bioreactors. Biosolids: treated residuals from wastewater treatment htm facilities The City of Columbia Public Works Cell: a contained area of the landfill where waste is SPECIFIC: deposited http://www.epa.gov/epaoswer/nonhw/muncpl/ Department has begun planning for landfill/biowork/index.htm the next sanitary landfill disposal cell. Inorganic: being or composed of matter other than plant As part of this planning process, or animal bioreactor technology is being ACKNOWLEDGEMENTS examined as a means to accelerate LCS: leachate collection system waste biostabilization. We thank the following individuals and Leachate: liquid that filters through MSW organizations for contributions to this brochure. LFG: landfill gas Camp Dresser and McKee Inc. Liner: an engineered impermeable barrier at the bottom of Engineering Consulting Firm the landfill cell to prevent liquid from leaving the landfill University of Missouri Methane: a colorless, odorless, flammable gas produced by Dr. John Bowders decomposition of organic matter Civil Engineering Department MSW: municipal solid waste Organic: relating to or derived from living things (plant or animals), containing carbon compounds City of Columbia Post Closure: covers a regulated (currently 30 years) Public Works Department period after waste is last accepted when the owner is Solid Waste Division financially obligated to maintain the area to the designed P. -
EPA-P1-500, Needham, the Likely Medium to Long-Term Generation
R&D Technical Report P1-500/1/TR The likely medium to long-term generation of defects in geomembrane liners Environment Agency Likely medium to long-term generation of defects in geomembranes 1 The Environment Agency is the leading public body protecting and improving the environment in England and Wales. It’s our job to make sure that air, land and water are looked after by everyone in today’s society, so that tomorrow’s generations inherit a cleaner, healthier world. Our work includes tackling flooding and pollution incidents, reducing industry’s impacts on the environment, cleaning up rivers, coastal waters and contaminated land, and improving wildlife habitats. Published by: Authors: Environment Agency Needham, A., Gallagher, E., Peggs, I., Howe, G. & Norris, J. Rio House EDGE Consultants UK Ltd, in association with I-Corp International Waterside Drive, Aztec West Inc., Nottingham Trent University and RAPRA Technology Ltd. Almondsbury, Bristol BS32 4UD Tel: 01454 624400 Fax: 01454 624409 Statement of use: This report presents a review of the processes and rates of ISBN: 1 84432 180 0 geomembrane degradation reported from laboratory and field studies. It reviews landfill monitoring data and research © Environment Agency, January 2004 from related fields to predict future rates of defect generation in geomembrane liners, for use in risk and performance All rights reserved. This document may be reproduced assessment of new landfill sites. This report should be used with prior permission of the Environment Agency. in conjunction with the Agency’s guidance on hydrogeological risk assessment for landfills and LandSim This report is printed on Cyclus Print, a 100% recycled v2.5+. -
Chapter 7. Best Practices for Landfill Gas Collection System Design And
7. Best Practices for Landfill Gas Collection System Design and Installation Photo credits: Advance One Development, Inc. and Smith Gardner, Inc. Landfill owners and operators collect landfill gas (LFG) for various reasons, including using LFG for energy, complying with local/state/federal regulations and controlling odors. Regardless of the motivation, owners and operators want to maximize the amount of LFG that is collected while minimizing the amount lost as fugitive or odorous emissions. In general, minimizing fugitive emissions and maximizing collection efficiency improves environmental benefits such as reducing hazardous and greenhouse gas (GHG) emissions and controlling odors and preventing them from migrating off site. Maximizing collection efficiency also improves economic return for LFG energy projects. This chapter provides an overview of design and installation best practices for a planned The federal New Source Performance Standards and gas collection system (GCS). Advantages and Emission Guidelines (NSPS and EG) and National disadvantages of GCS components as well as Emission Standards for Hazardous Air Pollutants considerations are presented. Owners and (NESHAP) for MSW landfills require landfills that operators that install a GCS can use this exceed the established size and emission thresholds information to better understand options to install a well-designed and well-operated gas collection and control system (GCCS). available and to ensure their GCS is robust and well maintained to minimize surface Although the regulations contain specifications for emissions and system downtime. Each best active collection systems and overall operational practice may not be suited for a particular requirements, they are intended to provide flexibility landfill so application must be determined on and allow innovation, recognizing that site-specific a site-specific basis. -
INTEGRATED SOLID WASTE MANAGEMENT for LOCAL GOVERNMENTS a Practical Guide
INTEGRATED SOLID WASTE MANAGEMENT FOR LOCAL GOVERNMENTS A Practical Guide Improving solid waste management is crucial for countering public health impacts of uncollected waste and environmental impacts of open dumping and burning. This practical reference guide introduces key concepts of integrated solid waste management and identifi es crosscutting issues in the sector, derived mainly from fi eld experience in the technical assistance project Mainstreaming Integrated Solid Waste Management in Asia. This guide contains over 40 practice briefs covering solid waste management planning, waste categories, waste containers and collection, waste processing and diversion, landfi ll development, landfi ll operations, and contract issues. About the Asian Development Bank ADB’s vision is an Asia and Pacifi c region free of poverty. Its mission is to help its developing member countries reduce poverty and improve the quality of life of their people. Despite the region’s many successes, it remains home to a large share of the world’s poor. ADB is committed to reducing poverty through inclusive economic growth, environmentally sustainable growth, and regional integration. Based in Manila, ADB is owned by members, including from the region. Its main instruments for helping its developing member countries are policy dialogue, loans, equity investments, guarantees, grants, and technical assistance. INTEGRATED SOLID WASTE MANAGEMENT FOR LOCAL GOVERNMENTS A Practical Guide ASIAN DEVELOPMENT BANK 6 ADB Avenue, Mandaluyong City 1550 Metro Manila, Philippines 9 789292 578374 ASIAN DEVELOPMENT BANK www.adb.org Tool Kit for Solid Waste Management in Asian_COVER.indd 1 6/1/2017 5:14:11 PM INTEGRATED SOLID WASTE MANAGEMENT FOR LOCAL GOVERNMENTS A Practical Guide Improving solid waste management is crucial for countering the public health impacts of uncollected waste as well as the environmental impacts of open dumping and burning. -
Compaction Characteristics of Municipal Solid Waste James L
View metadata, citation and similar papers at core.ac.uk brought to you by CORE provided by DigitalCommons@CalPoly Compaction Characteristics of Municipal Solid Waste 1 2 James L. Hanson, Ph.D., P.E., M.ASCE ; Nazli Yesiller, Ph.D., A.M.ASCE ; Shawna A. Von Stockhausen, 3 4 P.E., M.ASCE ; and Wilson W. Wong, A.M.ASCE Abstract: Compaction characteristics of municipal solid waste �MSW� were determined in the laboratory and in the field as a function of moisture content, compactive effort, and seasonal effects. Laboratory tests were conducted on manufactured wastes using modified and 4X modified efforts. Field tests were conducted at a MSW landfill in Michigan on incoming wastes without modifications to size, shape, or composition, using typical operational compaction equipment and procedures. Field tests generally included higher efforts and resulted in higher unit weights at higher water contents than the laboratory tests. Moisture addition to wastes in the field was more effective in winter than in summer due to dry initial conditions and potential thawing and softening of wastes. The measured parameters in the � / 3 � / 3 laboratory were dmax-mod =5.2 kN m , wopt-mod =65%, dmax-4�mod =6.0 kN m , and wopt-4�mod =56%; in the field with effort were � / 3 � / 3 � dmax-low =5.7 kN m , wopt-low =70%; dmax-high =8.2 kN m , and wopt-high =73%; and in the field with season were dmax-cold / 3 � / 3 =8.2 kN m , wcold =79.5%, dmax-warm =6.1 kN m , and wwarm =70.5%. -
Development Team
Paper No: 11 Solid and Hazardous Waste Management Module: 12 Waste Processing – Volume reduction Development Team Prof. R.K. Kohli Principal Investigator & Prof. V.K. Garg &Prof.AshokDhawan Co- Principal Investigator Central University of Punjab, Bathinda Dr. Yogalakshmi K. N., Paper Coordinator Central University of Punjab, Bathinda Dr. Rajesh Banu., Content Writer Anna University Regional Centre Tirunelveli Content Reviewer Dr. Yogalakshmi K. N., Central University of Punjab, Bathinda Anchor Institute Central University of Punjab 1 Solid and Hazardous Waste Management Environmental Sciences Waste Processing – Volume reduction Description of Module Subject Name Environmental Sciences Paper Name Solid and Hazardous Waste Management Module Name/Title Waste Processing – Volume reduction Module Id EVS/SHWM-XI/12 Pre-requisites Basic knowledge on To minimize the amount of solid waste material to be processed at the dumping site. Objectives To increase the efficiency of collection and disposal of solid wastes. To enhance the durability of dumping sites. Finally, to prepare the economic viability of solid waste management system. Keywords Waste processing, volume reduction, mechanical, compactors, balers, pelletization 2 Solid and Hazardous Waste Management Environmental Sciences Waste Processing – Volume reduction Module 1: Learning Objectives: To minimize the amount of solid waste material to be processed at the dumping site. To increase the efficiency of collection and disposal of solid wastes. To enhance the durability of dumping sites. Finally, to prepare the economic viability of solid waste management system. Volume reduction Volume reduction is a type of waste processing where the nature of the waste is altered physically. It is one of the essential steps in waste management system. -
Waste-To-Energy and Waste Export by Rail Feasibility Study
Attachment A WASTE-TO-ENERGY AND WASTE EXPORT BY RAIL FEASIBILITY STUDY September 2019 WASTE-TO-ENERGY AND WASTE EXPORT BY RAIL FEASIBILITY STUDY WASTE-TO-ENERGY AND WASTE EXPORT BY RAIL FEASIBILITY STUDY Prepared for: King County Office of Performance, Strategy, and Budget Chinook Building, 8th Floor 401 Fifth Avenue Seattle, WA 98104 Prepared by: Arcadis U.S., Inc. 1100 Olive Way Suite 800 Seattle, Washington 98101 Tel 206 325 5254 Fax 206 325 8218 Our Ref.: 30015954 (WTE42955.0001) Date: September 2019 This document is intended only for the use of the individual or entity for which it was prepared and may contain information that is privileged, confidential and exempt from disclosure under applicable law. Any dissemination, distribution or copying of this document is strictly prohibited. arcadis.com WASTE-TO-ENERGY AND WASTE EXPORT BY RAIL FEASIBILITY STUDY CONTENTS Acronyms and Abbreviations ........................................................................................................................ ix Executive Summary ........................................................................................................................................ i Waste Tonnage Forecast ......................................................................................................................... i Waste-to-Energy Methodology ............................................................................................................... ii Waste Export by Rail Methodology ....................................................................................................... -
Redalyc.Analysis of the Role of the Sanitary Landfill in Waste
Ambiente & Água - An Interdisciplinary Journal of Applied Science ISSN: 1980-993X [email protected] Universidade de Taubaté Brasil Lombardi, Francesco; Costa, Giulia; Sirini, Piero Analysis of the role of the sanitary landfill in waste management strategies based upon a review of lab leaching tests and new tools to evaluate leachate production Ambiente & Água - An Interdisciplinary Journal of Applied Science, vol. 12, núm. 4, julio- agosto, 2017, pp. 543-555 Universidade de Taubaté Taubaté, Brasil Available in: http://www.redalyc.org/articulo.oa?id=92851634003 How to cite Complete issue Scientific Information System More information about this article Network of Scientific Journals from Latin America, the Caribbean, Spain and Portugal Journal's homepage in redalyc.org Non-profit academic project, developed under the open access initiative Ambiente & Água - An Interdisciplinary Journal of Applied Science ISSN 1980-993X – doi:10.4136/1980-993X www.ambi-agua.net E-mail: [email protected] Analysis of the role of the sanitary landfill in waste management strategies based upon a review of lab leaching tests and new tools to evaluate leachate production doi:10.4136/ambi-agua.2096 Received: 15 Feb. 2017; Accepted: 10 May 2017 Francesco Lombardi1*; Giulia Costa1; Piero Sirini2 1University of Rome “Tor Vergata”, via del Politecnico 1, I-00133 Rome, Italy Department of Civil Engineering and Computer Science Engineering 2University of Florence, Via Santa Marta 3, I-50139 Florence, Italy Department of Civil and Environmental Engineering *Corresponding author: e-mail: [email protected] [email protected], [email protected] ABSTRACT This paper reviews the role of sanitary landfills in current and future waste management strategies based upon the principles and the goals established by the European Framework Directive on Waste (2008/98/EC). -
Environmental Assessment Idaho National Engineering Laboratory Low-Level and Mixed Waste Processing
DOE.'EA-0843 June 1994 ENVIRONMENTAL ASSESSMENT IDAHO NATIONAL ENGINEERING LABORATORY LOW-LEVEL AND MIXED WASTE PROCESSING Prepared for the U.S. DEPARTMENT OF ENERGY Office of Environmental Restoration and Waste Management DISCLAIMER This report was .prepared as an account of work sponsored by an agency of the United States Government. Neither the United States Government nor any agency thereof, nor any of their employees, make any warranty, express or implied, or assumes any legal liability or responsibility for the accuracy, completeness, or usefulness of any information, apparatus, product, or process disclosed, or represents that its use would not infringe privately owned rights. Reference herein to any specific commercial product, process, or service by trade name, trademark, manufacturer, or otherwise does not necessarily constitu~e or imply its endorsement, recommendation, or favoring by the United States Government or any agency thereof. The views and opinions of authors expressed herein do not necessarily state or reflect those of the United States Government or any agency thereof• .--~ . ,.~~ -.- '.'- ..~------ DISCLAIMER Portions of this document may be illegible in electronic image products. Images are produced from the best available original document. PREFACE In response to public comments, DOE is now proposing only a portion of the proposed actions analyzed in this Environmental Assessment (EA). The following provides information about the modified" proposed action.. DOE initially prepared a draft EA to assess the environmental -
Taking on the Resource Challenge Hills Waste Solutions
Hills Waste Solutions Taking on the resource challenge Hills Waste Solutions Taking on the resource challenge with . ● Waste management strategy ● Waste-to-energy ● Dry mixed recycling ● Household kerbside recycling ● Household waste recycling centres ● Non-hazardous and hazardous waste landfill disposal ● Skip and bulk container hire ● Trade waste collections ● Waste compaction service ● Waste transfer stations ● Materials recovery facilities (MRF) ● Mechanical biological treatment ● Composting ● Wood chipping ● Leachate water treatment www.hills-group.co.uk 1 Good waste management makes good business sense The changing face of waste Managing our waste more sustainably is one of the great challenges of our time. The drive to reduce, reuse, recycle and recover is one in which we all need to engage as individuals but is even more pertinent to local authorities and businesses. The Government has set councils tough landfill reduction targets and companies face similar penalties if they fail to meet their responsibilities as major producers of waste. Good waste management also makes good business sense. It has been estimated that manufacturers could make savings equivalent to 1 per cent of their turnover by instigating simple but effective techniques to minimise their waste.* The issues for the major producers of waste can be complex, with the result that the process can be both costly and time consuming. It is against this backdrop that Hills Waste Solutions offers a range of specialist waste management services over a wide area of western and southern England. * Source: Department for Environment Food and Rural Affairs 2 The greatest value we give to our clients lies in our expertise, ideas and relationships Tailoring our approach to your needs Our mission is to help our customers in both the private and public sectors reduce, reuse and recycle their waste.