Oxidation of Beryllium – a Scanning Auger Investigation
Total Page:16
File Type:pdf, Size:1020Kb
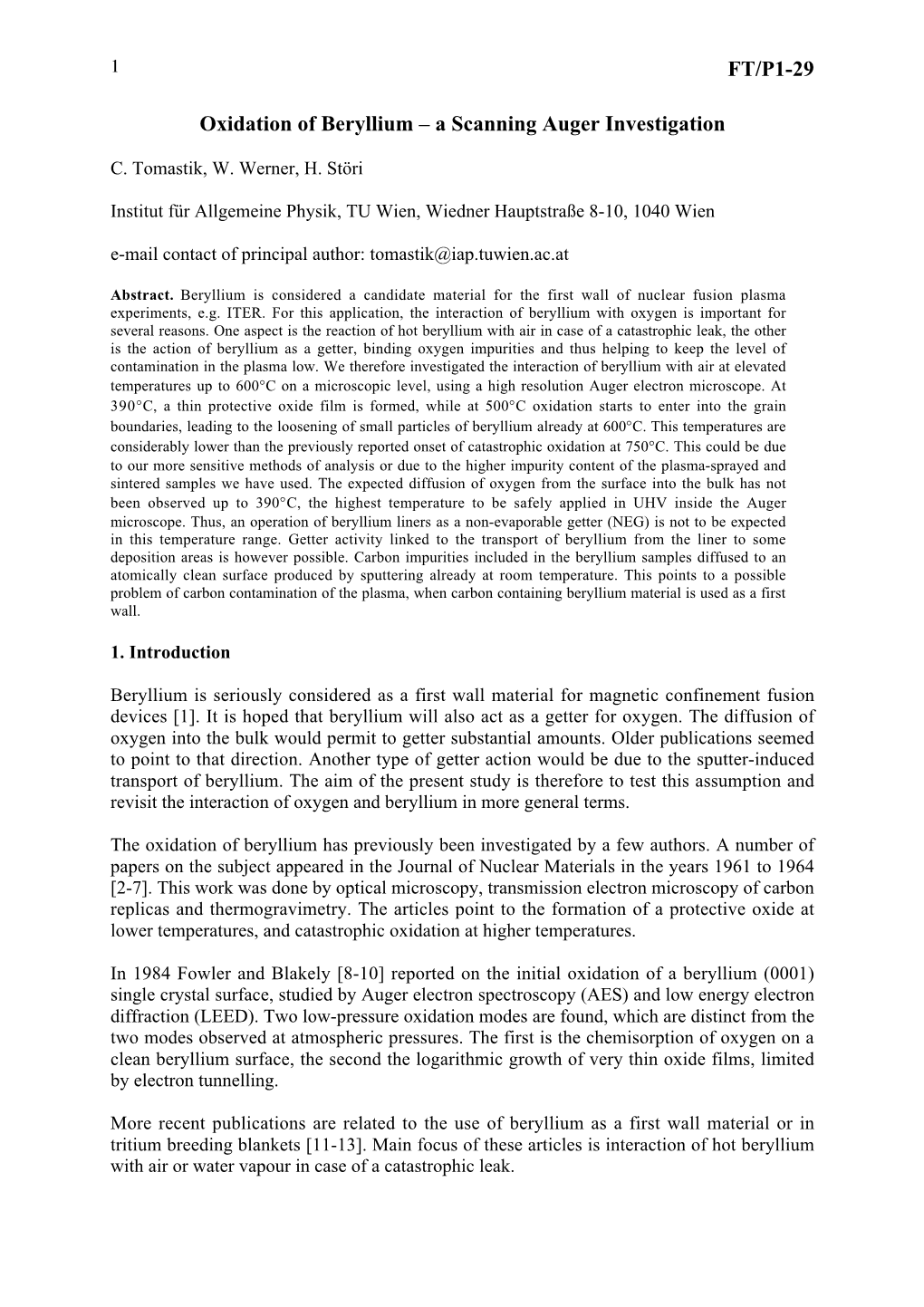
Load more
Recommended publications
-
Report of the Advisory Group to Recommend Priorities for the IARC Monographs During 2020–2024
IARC Monographs on the Identification of Carcinogenic Hazards to Humans Report of the Advisory Group to Recommend Priorities for the IARC Monographs during 2020–2024 Report of the Advisory Group to Recommend Priorities for the IARC Monographs during 2020–2024 CONTENTS Introduction ................................................................................................................................... 1 Acetaldehyde (CAS No. 75-07-0) ................................................................................................. 3 Acrolein (CAS No. 107-02-8) ....................................................................................................... 4 Acrylamide (CAS No. 79-06-1) .................................................................................................... 5 Acrylonitrile (CAS No. 107-13-1) ................................................................................................ 6 Aflatoxins (CAS No. 1402-68-2) .................................................................................................. 8 Air pollutants and underlying mechanisms for breast cancer ....................................................... 9 Airborne gram-negative bacterial endotoxins ............................................................................. 10 Alachlor (chloroacetanilide herbicide) (CAS No. 15972-60-8) .................................................. 10 Aluminium (CAS No. 7429-90-5) .............................................................................................. 11 -
Preparing the Future Post-Mortem Analysis of Beryllium-Based JET and ITER Samples by Multi-Wavelengths Raman Spectroscopy on Implanted Be, and Co-Deposited Be M
Preparing the future post-mortem analysis of beryllium-based JET and ITER samples by multi-wavelengths Raman spectroscopy on implanted Be, and co-deposited Be M. Rusu, C. Pardanaud, Y. Ferro, G. Giacometti, C. Martin, Y. Addab, P. Roubin, M. Minissale, L. Ferri, F. Virot, et al. To cite this version: M. Rusu, C. Pardanaud, Y. Ferro, G. Giacometti, C. Martin, et al.. Preparing the future post-mortem analysis of beryllium-based JET and ITER samples by multi-wavelengths Raman spectroscopy on im- planted Be, and co-deposited Be. Nuclear Fusion, IOP Publishing, 2017, 57, pp.076035. 10.1088/1741- 4326/aa70bb. hal-01787067 HAL Id: hal-01787067 https://hal.archives-ouvertes.fr/hal-01787067 Submitted on 7 May 2018 HAL is a multi-disciplinary open access L’archive ouverte pluridisciplinaire HAL, est archive for the deposit and dissemination of sci- destinée au dépôt et à la diffusion de documents entific research documents, whether they are pub- scientifiques de niveau recherche, publiés ou non, lished or not. The documents may come from émanant des établissements d’enseignement et de teaching and research institutions in France or recherche français ou étrangers, des laboratoires abroad, or from public or private research centers. publics ou privés. Preparing the future post-mortem analysis of beryllium-based JET and ITER samples by multi-wavelengths Raman spectroscopy on implanted Be, and co-deposited Be M. I. Rusua,b, C. Pardanaudb*, Y. Ferrob, G. Giacomettib, C. Martinb, Y. Addabb, P. Roubinb, M. Minissaleb,f, L. Ferryb,c, F. Virotc, M. Barrachin c, C P Lungud, C Porosnicud, P Dincad, M Lungud, M. -
WO 2016/074683 Al 19 May 2016 (19.05.2016) W P O P C T
(12) INTERNATIONAL APPLICATION PUBLISHED UNDER THE PATENT COOPERATION TREATY (PCT) (19) World Intellectual Property Organization International Bureau (10) International Publication Number (43) International Publication Date WO 2016/074683 Al 19 May 2016 (19.05.2016) W P O P C T (51) International Patent Classification: (81) Designated States (unless otherwise indicated, for every C12N 15/10 (2006.01) kind of national protection available): AE, AG, AL, AM, AO, AT, AU, AZ, BA, BB, BG, BH, BN, BR, BW, BY, (21) International Application Number: BZ, CA, CH, CL, CN, CO, CR, CU, CZ, DE, DK, DM, PCT/DK20 15/050343 DO, DZ, EC, EE, EG, ES, FI, GB, GD, GE, GH, GM, GT, (22) International Filing Date: HN, HR, HU, ID, IL, IN, IR, IS, JP, KE, KG, KN, KP, KR, 11 November 2015 ( 11. 1 1.2015) KZ, LA, LC, LK, LR, LS, LU, LY, MA, MD, ME, MG, MK, MN, MW, MX, MY, MZ, NA, NG, NI, NO, NZ, OM, (25) Filing Language: English PA, PE, PG, PH, PL, PT, QA, RO, RS, RU, RW, SA, SC, (26) Publication Language: English SD, SE, SG, SK, SL, SM, ST, SV, SY, TH, TJ, TM, TN, TR, TT, TZ, UA, UG, US, UZ, VC, VN, ZA, ZM, ZW. (30) Priority Data: PA 2014 00655 11 November 2014 ( 11. 1 1.2014) DK (84) Designated States (unless otherwise indicated, for every 62/077,933 11 November 2014 ( 11. 11.2014) US kind of regional protection available): ARIPO (BW, GH, 62/202,3 18 7 August 2015 (07.08.2015) US GM, KE, LR, LS, MW, MZ, NA, RW, SD, SL, ST, SZ, TZ, UG, ZM, ZW), Eurasian (AM, AZ, BY, KG, KZ, RU, (71) Applicant: LUNDORF PEDERSEN MATERIALS APS TJ, TM), European (AL, AT, BE, BG, CH, CY, CZ, DE, [DK/DK]; Nordvej 16 B, Himmelev, DK-4000 Roskilde DK, EE, ES, FI, FR, GB, GR, HR, HU, IE, IS, IT, LT, LU, (DK). -
Chemical Names and CAS Numbers Final
Chemical Abstract Chemical Formula Chemical Name Service (CAS) Number C3H8O 1‐propanol C4H7BrO2 2‐bromobutyric acid 80‐58‐0 GeH3COOH 2‐germaacetic acid C4H10 2‐methylpropane 75‐28‐5 C3H8O 2‐propanol 67‐63‐0 C6H10O3 4‐acetylbutyric acid 448671 C4H7BrO2 4‐bromobutyric acid 2623‐87‐2 CH3CHO acetaldehyde CH3CONH2 acetamide C8H9NO2 acetaminophen 103‐90‐2 − C2H3O2 acetate ion − CH3COO acetate ion C2H4O2 acetic acid 64‐19‐7 CH3COOH acetic acid (CH3)2CO acetone CH3COCl acetyl chloride C2H2 acetylene 74‐86‐2 HCCH acetylene C9H8O4 acetylsalicylic acid 50‐78‐2 H2C(CH)CN acrylonitrile C3H7NO2 Ala C3H7NO2 alanine 56‐41‐7 NaAlSi3O3 albite AlSb aluminium antimonide 25152‐52‐7 AlAs aluminium arsenide 22831‐42‐1 AlBO2 aluminium borate 61279‐70‐7 AlBO aluminium boron oxide 12041‐48‐4 AlBr3 aluminium bromide 7727‐15‐3 AlBr3•6H2O aluminium bromide hexahydrate 2149397 AlCl4Cs aluminium caesium tetrachloride 17992‐03‐9 AlCl3 aluminium chloride (anhydrous) 7446‐70‐0 AlCl3•6H2O aluminium chloride hexahydrate 7784‐13‐6 AlClO aluminium chloride oxide 13596‐11‐7 AlB2 aluminium diboride 12041‐50‐8 AlF2 aluminium difluoride 13569‐23‐8 AlF2O aluminium difluoride oxide 38344‐66‐0 AlB12 aluminium dodecaboride 12041‐54‐2 Al2F6 aluminium fluoride 17949‐86‐9 AlF3 aluminium fluoride 7784‐18‐1 Al(CHO2)3 aluminium formate 7360‐53‐4 1 of 75 Chemical Abstract Chemical Formula Chemical Name Service (CAS) Number Al(OH)3 aluminium hydroxide 21645‐51‐2 Al2I6 aluminium iodide 18898‐35‐6 AlI3 aluminium iodide 7784‐23‐8 AlBr aluminium monobromide 22359‐97‐3 AlCl aluminium monochloride -
Durham E-Theses
Durham E-Theses Co-ordination chemiatiy of beryllium Green, S.I.E. How to cite: Green, S.I.E. (1962) Co-ordination chemiatiy of beryllium, Durham theses, Durham University. Available at Durham E-Theses Online: http://etheses.dur.ac.uk/9108/ Use policy The full-text may be used and/or reproduced, and given to third parties in any format or medium, without prior permission or charge, for personal research or study, educational, or not-for-prot purposes provided that: • a full bibliographic reference is made to the original source • a link is made to the metadata record in Durham E-Theses • the full-text is not changed in any way The full-text must not be sold in any format or medium without the formal permission of the copyright holders. Please consult the full Durham E-Theses policy for further details. Academic Support Oce, Durham University, University Oce, Old Elvet, Durham DH1 3HP e-mail: [email protected] Tel: +44 0191 334 6107 http://etheses.dur.ac.uk Co-ordination Chemistry of Beryllium hy S. I. E. Green A thesis submitted for the Degree of Doctor of Philosophy in the University of Durham. June 1962 Acknowledgements The author would like to thank Professor 6. E. Coates for hie help and constant encouragement given during the course of this work. Thanks are also given to Sr. K. Wade and Br. 6. P. Cox for many helpful discussions, and Professor R. S. Nyholm and Dr. C. S. Pande for magnetic susceptibility measurements. The author is indebted to the Department of Scientific and Industrial Research for a Researoh Studentship. -
"Sony Mobile Critical Substance List" At
Sony Mobile Communications Public 1(16) DIRECTIVE Document number Revision 6/034 01-LXE 110 1408 Uen C Prepared by Date SEM/CGQS JOHAN K HOLMQVIST 2014-02-20 Contents responsible if other than preparer Remarks This document is managed in metaDoc. Approved by SEM/CGQS (PER HÖKFELT) Sony Mobile Critical Substances Second Edition Contents 1 Revision history.............................................................................................3 2 Purpose.........................................................................................................3 3 Directive ........................................................................................................4 4 Application ....................................................................................................4 4.1 Terms and Definitions ...................................................................................4 5 Comply to Sony Technical Standard SS-00259............................................6 6 The Sony Mobile list of Critical substances in products................................6 7 The Sony Mobile list of Restricted substances in products...........................7 8 The Sony Mobile list of Monitored substances .............................................8 It is the responsibility of the user to ensure that they have a correct and valid version. Any outdated hard copy is invalid and must be removed from possible use. Public 2(16) DIRECTIVE Document number Revision 6/034 01-LXE 110 1408 Uen C Substance control Sustainability is the backbone -
Printed Copies for Reference Only
Supplier Environmental Health and Safety Number:CHI-EHS30-000 Revision:A Specification 1 APPROVERS INFORMATION PREPARED BY: Jennilyn Rivera Dinglasan Title: EHS DATE: 5/3/2017 2:35:30 AM APPROVED BY: Jennilyn DATE: 8/10/2017 7:00:05 Rivera Dinglasan Title: EHS PM DATE: 7/21/2017 2:43:17 APPROVED BY: Aline Zeng Title: Purchasing AM APPROVED BY: Bill Hemrich Title: Purchasing DATE: 6/1/2017 3:28:35 PM DATE: 6/11/2017 11:05:48 APPROVED BY: Jade Yuan Title: Purchasing PM APPROVED BY: Matthew DATE: 5/26/2017 6:54:14 Briggs Title: Purchasing AM DATE: 5/26/2017 3:56:07 APPROVED BY: Michael Ji Title: Purchasing AM DATE: 8/31/2017 4:24:35 APPROVED BY: Olga Chen Title: Purchasing AM APPROVED BY: Alfredo DATE: 6/2/2017 11:54:20 Heredia Title: Supplier Quality AM APPROVED BY: Audrius DATE: 5/31/2017 1:20:01 Sutkus Title: Supplier Quality AM DATE: 5/26/2017 2:03:53 APPROVED BY: Sam Peng Title: Supplier Quality AM APPROVED BY: Arsenio DATE: 6/28/2017 2:43:49 Mabao Cesista Jr. Title: EHS Manager AM Printed copies for reference only Printed copies for reference only Supplier Environmental Health and Safety Number:CHI-EHS30-000 Revision:A Specification 1 1.0 Purpose and Scope 1.1 This specification provides general requirements to suppliers regarding Littelfuse Inc’s EHS specification with regards to regulatory compliance, EHS management systems, banned and restricted substances, packaging, and product environmental content reporting. 1.2 This specification applies to all equipment, materials, parts, components, packaging, or products supplied to Littelfuse, Inc. -
A Unique Beryllium Carbide Thin Film: Synthesis, Chemical and Thermal Characterizations
A UNIQUE BERYLLIUM CARBIDE THIN FILM: SYNTHESIS, CHEMICAL AND THERMAL CHARACTERIZATIONS Yixiang Xie* Richard B. Stephens Nicholas C. Morosoff William J. James Electronic Materials Fusion Group Department of Chemical Department of Applied Research General Atomics Engineering, University Chemistry, University of Center, University of P. O. Box 85608 of Missouri-Rolla Missouri-Rolla Missouri-Rolla San Diego, CA 92186- Rolla, MO 65401 Rolla, MO 65401 Rolla, MO 65401 5608 (*contact person, [email protected]) KEYWORDS: plasma deposition, magnetron sputtering, beryllium carbide, inertial fusion ABSTRACT different directions onto a tiny capsule called the target Plasma-deposited coatings containing beryllium which contains the fuel, deuterium and tritium. The in excess of 50 atomic percent and oxygen content <5 hollow spherical capsules have a multilayer plastic wall atomic percent would meet the requirements for the made of hydrocarbon-based plasma polymers of a desired outermost coating, the outer ablator of the multilayered thickness as an outer ablator [3]. Other ablator materials microsphere for inertial confinement fusion (ICF). Films have been used such as pure Be and Al [4, 5] and metal- containing a Be2C composite with Be contents as high as doped hydrocarbon plasma polymers [3, 6-8]. The 75 atomic percent (O < 2 atomic percent) have been minimum condition for the production of practical fusion deposited on a variety of substrates via magnetron power is that the energy released from the fusion reactions sputtering of Be into a methane/argon plasma. The after conversion to electricity must exceed the energy elemental composition was controlled by adjusting the required to run the ignition lasers [2]. -
MTCR Annex Handbook
Introduction The Missile Technology Control I N T R O D U C Regime The Missile Technology Control Regime (MTCR) is an informal political MTCR Members arrangement to control the proliferation of rocket and unmanned air vehicle systems capable of delivering weapons of mass destruction and their associ- Original Members ated equipment and technology. The MTCR was formed in 1987 by in Alphabetical Canada, France, Germany, Italy, Japan, the United Kingdom, and the Order • Canada United States. Membership has expanded to 29 countries, as of June 1998. • Federal Republic of The Regime’s controls are applicable to such rocket and unmanned air vehi- Germany cle systems as ballistic missiles, space launch vehicles, sounding rockets, un- • France manned air vehicles, cruise missiles, drones, and remotely piloted vehicles. • Italy • Japan The MCTR is not a treaty but a voluntary agreement among member coun- • United Kingdom tries sharing a common interest in controlling missile proliferation. MTCR • United States members meet at least once a year in a plenary session to exchange infor- mation, discuss policy issues, and examine ways to improve the Regime. In Additional January 1993, the MTCR revised its guidelines to address delivery systems Members in Order for all types of weapons of mass destruction—biological, chemical, or nu- of Admission clear weapons. Originally, the MTCR Guidelines only addressed nuclear • Spain • Netherlands weapons delivery systems. • Belgium • Luxembourg The Regime’s documents include the Guidelines and the Equipment and • Australia Technology Annex (copies of each are annexed to this publication). The • New Zealand Guidelines define the purpose of the MTCR and provide overall guidance • Denmark to member countries and those adhering unilaterally to the Guidelines. -
Experimental Electronic Structure of Be2c
PHYSICAL REVIEW B VOLUME 58, NUMBER 11 15 SEPTEMBER 1998-I Experimental electronic structure of Be2C C.-T. Tzeng Institute of Electro-Optical Engineering, National Chiao-Tung University, Hsinchu, Taiwan, Republic of China K.-D. Tsuei Synchrotron Radiation Research Center, Hsinchu, Taiwan, Republic of China and Department of Physics, National Tsing-Hua University, Hsinchu, Taiwan, Republic of China W.-S. Lo Synchrotron Radiation Research Center, Hsinchu, Taiwan, Republic of China ~Received 12 March 1998! The insulating Be2C thin films have been successfully prepared on a Be surface. A low-energy electron diffraction pattern shows that the films have ~100! orientation along the surface normal. We have used angle- resolved photoemission to map out the occupied bulk band dispersion along the G-X direction. The band-gap edges at the X point are 6.7 and 11.5 eV below the valence-band maximum, which is located at the G point. These values are in good agreement with theoretical calculations. The unoccupied bulk electronic structure is measured using C 1s near-edge x-ray-absorption spectroscopy. The spectrum is similar in shape to the energy- loss spectrum and the calculated p-partial density of states, while the peak positions are different. @S0163-1829~98!01335-6# I. INTRODUCTION photoemission. The result is in good agreement with recent calculations. The unoccupied conduction band density of The insulating crystal, beryllium carbide (Be2C) is be- states is measured by C 1s near-edge photoabsorption. The lieved to be a strongly ionic crystal. Its strong chemical Be and C 1s core-level binding energies measured by pho- bonding leads to high melting temperature, which implies toemission are found to be consistent with the description of potential use as refractories and large elastic constants, strongly ionic bonding of the compound. -
Draft Report on Carcinogens Monograph on Antimony Trioxide
Draft Report on Carcinogens Monograph on Antimony Trioxide Peer-Review Draft November 29, 2017 Office of the Report on Carcinogens Division of the National Toxicology Program National Institute of Environmental Health Sciences U.S. Department of Health and Human Services This information is distributed solely for the purpose of pre-dissemination peer review under applicable information quality guidelines. It has not been formally distributed by the National Toxicology Program. It does not represent and should not be construed to represent any NTP determination or policy. This Page Intentionally Left Blank Peer-Review Draft RoC Monograph on Antimony Trioxide 11/29/17 Foreword The National Toxicology Program (NTP) is an interagency program within the Public Health Service (PHS) of the Department of Health and Human Services (HHS) and is headquartered at the National Institute of Environmental Health Sciences of the National Institutes of Health (NIEHS/NIH). Three agencies contribute resources to the program: NIEHS/NIH, the National Institute for Occupational Safety and Health of the Centers for Disease Control and Prevention (NIOSH/CDC), and the National Center for Toxicological Research of the Food and Drug Administration (NCTR/FDA). Established in 1978, the NTP is charged with coordinating toxicological testing activities, strengthening the science base in toxicology, developing and validating improved testing methods, and providing information about potentially toxic substances to health regulatory and research agencies, scientific and medical communities, and the public. The Report on Carcinogens (RoC) is prepared in response to Section 301 of the Public Health Service Act as amended. The RoC contains a list of identified substances (i) that either are known to be human carcinogens or are reasonably anticipated to be human carcinogens and (ii) to which a significant number of persons residing in the United States are exposed. -
Hazardous Waste Management Guidebook
Hazardous Waste Management Guidebook FOR UNIVERSTIY AT BUFFALO CAMPUS LABORATORIES Prepared By Environment, Health & Safety Services 220 Winspear Avenue Buffalo, NY 14215 Phone: 716-829-3301 Web: www.ehs.buffalo.edu UB EH&S Hazardous Waste Management Guidebook Table of Contents 1.0 PURPOSE ........................................................................................... 3 2.0 SCOPE ............................................................................................... 4 3.0 DEFINITIONS ...................................................................................... 4 4.0 RESPONSIBILITIES ............................................................................... 5 4.1 EH&S ................................................................................................... 5 4.2 Faculty, Staff, and Students ............................................................. 5 5.0 PROCEDURES ....................................................................................... 6 5.1 Hazardous Waste Determination ................................................... 6 5.1.1 Characteristic Hazardous Wastes .......................................... 7 5.1.2 Listed Hazardous Wastes ........................................................ 9 5.2 Satellite Accumulation of Hazardous Waste ............................ 9 5.2.1 Accumulation Areas ............................................................. 10 5.2.2 Requirements for Hazardous Waste Containers ................ 10 5.2.3 Segregation of Hazardous Wastes .....................................