Tailored Syngas Production from Residual Biomass Gasification for The
Total Page:16
File Type:pdf, Size:1020Kb
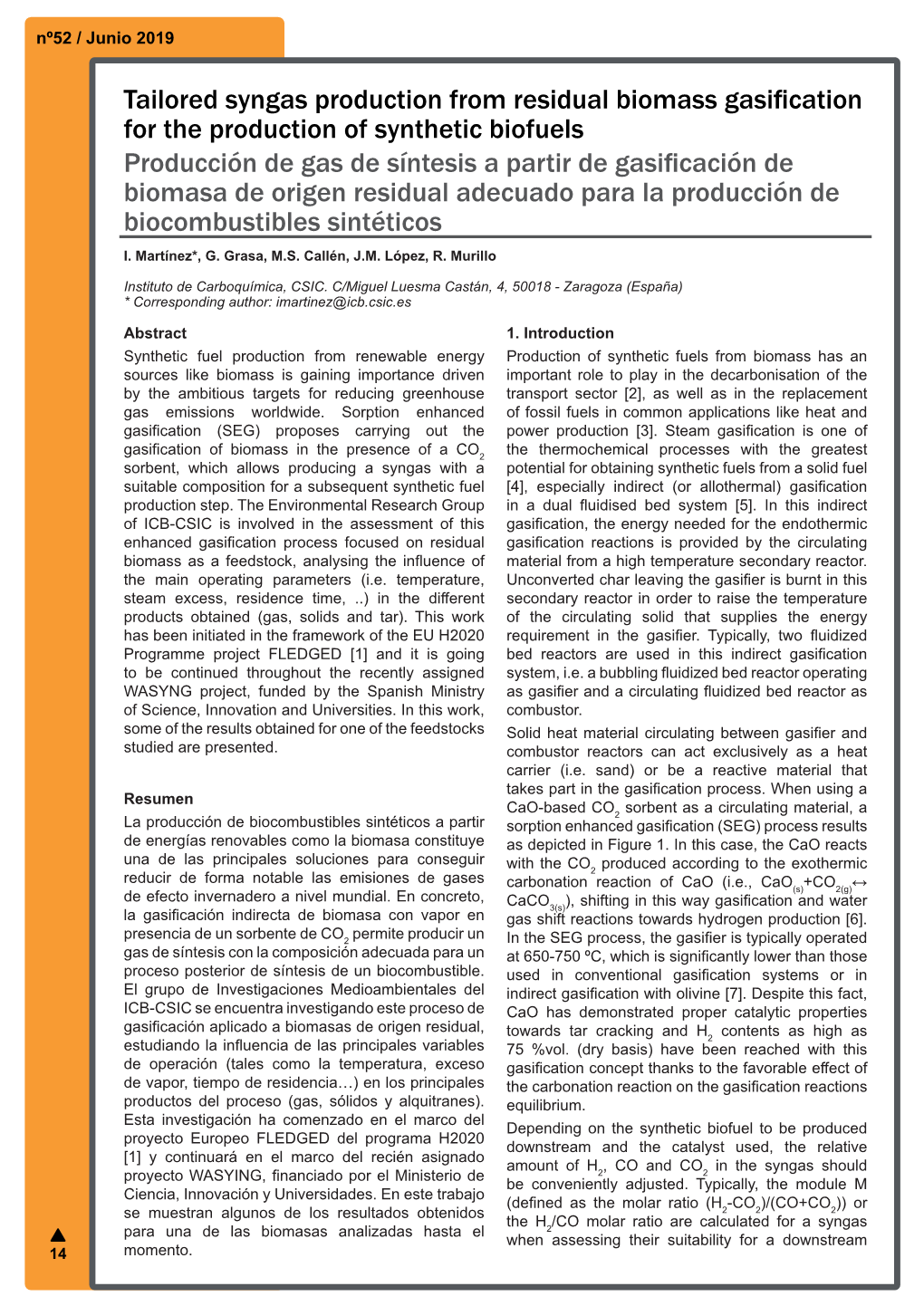
Load more
Recommended publications
-
Biomass-Derived Hydrogen from a Thermally Ballasted Gasifier
Proceedings of the 2002 U.S. DOE Hydrogen Program Review NREL/CP-610-32405 Biomass-Derived Hydrogen from a Thermally Ballasted Gasifier Robert C. Brown, Glenn Norton, Andy Suby, Jerod Smeenk, Keith Cummer, and Josh Nunez Center for Sustainable Environmental Technologies Iowa State University Ames, IA 50011-3020 INTRODUCTION The goal of this project is to optimize performance of an indirectly heated gasification system that converts switchgrass into hydrogen-rich gas suitable for powering fuel cells. We have developed a thermally ballasted gasifier that uses a single reactor for both combustion and pyrolysis. Instead of spatially separating these processes, they are temporally isolated. The producer gas is neither diluted with nitrogen or the products of combustion. The heat released during combustion at 850°C is stored as latent heat in the form of molten salt sealed in tubes immersed in the fluidized bed. During the pyrolysis phase, which occurs at temperatures between 600 and 850°C, the reactor is fluidized with steam or recycled producer gas rather than air. Heat stored in the phase change material is released during this phase of the cycle to support the endothermic reactions of the pyrolysis stage. Because air is not used during the gas-producing phase of the cycle, nitrogen does not dilute the product gas, resulting in relatively high concentrations of hydrogen and carbon monoxide in the producer gas compared to conventional gasifiers. The carbon monoxide, along with steam used to fluidize the reactor, can be shifted to additional hydrogen by the water-gas shift reaction. Objectives in the first year include: • Determine whether switchgrass is a suitable fuel for the ballasted gasifier. -
Lng Flow Calibration Facilities
LNG FLOW CALIBRATION FACILITIES Oswin Kerkhof, VSL Mijndert van der Beek, VSL Peter Lucas, VSL Maria Mirzaei, VSL Gerard Blom, VSL Gertjan Kok, VSL Keywords: calibration, flow, flowmeter, custody transfer, measurement, uncertainty, accuracy, transport fuel, quality measurement, 1. Introduction Reliable, accurate and commonly agreed measurement methods are a first requirement for the trade of goods. For the large scale LNG distribution chain there is a commonly agreed measurement practice as described in various ISO standards and in the GIIGNL “Custody transfer handbook”. In comparison with other commodities like natural gas or gasoline the total uncertainty on measured energy is very high for LNG. The LNG industry is therefore committed to improve their measurement accuracies to reduce their financial risks and to optimize their mass and energy balances. As an extension of the traditional distribution chain for LNG a new market of professional consumers is developing with LNG as transport fuel. In this case there is no commonly agreed measurement practice and the metrological framework is not yet in place. This will be a showstopper for the roll-out of the LNG as transport fuel because laws will be enforcing protection of (professional) consumers. For small scale LNG the legal metrology framework will lay down requirements on traceability to national standards and will define maximum permissible measurement errors. This is not the case for large scale LNG where the industrial players are assumed to take care of their own business interests. For this reason the development of an LNG calibration facility is a crucial step and urgently required for the development of the small scale LNG distribution chain. -
Field Reference Manual, 2015
CALIFORNIA DEPARTMENT OF FOOD AND AGRICULTURE DIVISION OF MEASUREMENT STANDARDS FIELD REFERENCE MANUAL 2015 California Code of Regulation Title 4, Division 9 Chapter 1 Tolerances and Specifications for Commercial Weighing and Measuring Devices NIST Handbook 44 Sections 3.30. Liquid-Measuring Devices through 3.39 Hydrogen Gas-Measuring Devices DISCLAIMER This document represents the Division of Measurement Standards’ field manual for enforcing regulations pertaining to weights and measures in California. This field manual is not to be considered as the official Code of Regulations, as published by Barclays Law Publishers. NOTE: Language in Handbook 44 that is not adopted is annotated “[NOT ADOPTED]” in this document. NOTE: Requirements are different than, or in addition to, the requirements of Handbook 44 are included in the appropriate section this document. They are shaded, bordered, and numbered in the 4002 series to differentiate them from the Handbook 44 requirements. To find the latest online version of the California Code of Regulations (CCR) Title 4, Division 9, visit the California Office of Administration Law (OAL) at: http://ccr.oal.ca.gov/linkedslice/default.asp?SP=CCR-1000&Action=Welcome The CCR may also be accessed at http://oal.ca.gov/ by selecting the link Titled “California Code of Regulations” under the list of “Sponsored Links” in the left column on the OAL Home page. For information concerning the contents of this document, please contact the Division of Measurement Standards by e-mail at [email protected]. NIST Handbook 44 (2015 Edition) - Specifications, Tolerances, and Other Technical Requirements for Weighing and Measuring Devices as adopted by the 98th National Conference on Weights and Measures July 2014 is available at: www.nist.gov/pml/wmd/pubs/hb44.cfm 3.30. -
Guidelines for Gas Meters & Manifolds
Guidelines for Gas Meters & Manifolds * By carefully following attached suggestions, you will help us get your meters set on the first trip and avoid costly delays related to return trips (for which you are being charged $65 per trip). CoServ Gas Engineering (940) 270-7585 For Gas Emergencies or Leaks call: (844) 330-0763 CoServ Gas Meters and Manifolds Builder & Customer Requirements 1) Gas Meter Planning Guidelines a. The size of gas metering and regulating facilities varies widely depending upon the gas-load needs of each residence, business or commercial building. Due to the parameters associated with meter and regulator selection, it is imperative that the Customer, or the Customer’s agent, contact the assigned CoServ Gas representative prior to construction to determine the exact requirements for specific installations, including location and space requirements. Consulting with us early in the process may eliminate the need for changes to the gas metering facilities or gas Main Extensions or relocation of gas risers at a later date with additional delays and expense to Builder or Customer. 2) Meter Selection Criteria a. To assure proper operation, each gas meter must be the proper size and type for the maximum gas demand and required pressure. The maximum gas demand is determined by adding the Btu input ratings of all gas burning devices that may possibly be operating simultaneously. Furnaces, space heaters, water heaters, boilers, pool heaters, fireplace logs, gas clothes dryers, gas lights, and gas generators should be included at their maximum input ratings. b. The type of meter installed can also vary depending upon the Customer’s usage factors, e.g., what type of business, hours of operation, critical operations, etc. -
Sub-Metering of Natural Gas Flexible Flow Measurement Delivers Improved Accuracy and Substantial Savings
WHITEPAPER Sub-Metering of Natural Gas Flexible Flow Measurement Delivers Improved Accuracy and Substantial Savings by: Scott Rouse, VP Product Management, Sierra Instruments, Inc fter a decade of remarkable growth, This natural gas boom highlights the importance A the United States has become the for utility companies to provide homes, world’s number one producer of natural gas, businesses, and mid-to-large size facilities and its largest consumer, with consumption in with accurate natural gas billing. Traditionally, 2019 at 31 trillion cubic feet. This high growth utility companies have used diaphragm meters rate is expected to continue. For example, to measure natural gas usage, which is then electricity generation using natural gas has charged to customers on their monthly energy increased from 17% to 35% of total electrical bill. Although diaphragm meters are a trusted consumption, and is likely to increase to 50% billing mechanism by utility companies, they by mid-century. may not provide customers with the most accurate natural gas bill. Diaphragm meters have SUB-METERING OF NATURAL GAS WHITEPAPER limitations in natural gas measurement. If the WHAT IS NATURAL GAS? diaphragm meter does not ac curately measure Natural gas is the cleanest burning fossil the natural gas, this can result in utility companies fuel, producing by-products of mostly carbon overcharging customers. dioxide and water vapor. It is used extensively To avoid this problem, many mid-to-large-size in power generation, industrial and commercial facilities use flow meters to sub-meter their applications, and for home utility and heating. natural gas usage to validate the diaphragm Natural gas is primarily a mixture of methane, meters’ readings and more efficiently allocate ethane and propane, but those components energy. -
Performance of a Pilot Scale Biomass Gasification and Producer
Iowa State University Capstones, Theses and Graduate Theses and Dissertations Dissertations 2010 Performance of a pilot scale biomass gasification and producer gas combustion system using feedstock with controlled nitrogen content Sharan Sethuraman Iowa State University Follow this and additional works at: https://lib.dr.iastate.edu/etd Part of the Mechanical Engineering Commons Recommended Citation Sethuraman, Sharan, "Performance of a pilot scale biomass gasification and producer gas combustion system using feedstock with controlled nitrogen content" (2010). Graduate Theses and Dissertations. 11725. https://lib.dr.iastate.edu/etd/11725 This Thesis is brought to you for free and open access by the Iowa State University Capstones, Theses and Dissertations at Iowa State University Digital Repository. It has been accepted for inclusion in Graduate Theses and Dissertations by an authorized administrator of Iowa State University Digital Repository. For more information, please contact [email protected]. Performance of a pilot scale biomass gasification and producer gas combustion system using feedstock with controlled nitrogen content by Sharan Sethuraman A thesis submitted to the graduate faculty in partial fulfillment of the requirements for the degree of MASTER OF SCIENCE Major: Mechanical Engineering Program of Study Committee: Song-Charng Kong, Major Professor Terrence Meyer Gap Yong Kim Iowa State University Ames, Iowa 2010 ii TABLE OF CONTENTS LIST OF FIGURES .................................................................................................................................. -
Anaerobic Digester / Biogas Operator Guidebook
EPA 430-B-20-003 Anaerobic Digester/Biogas System Operator Guidebook A Guidebook for Operating Anaerobic Digestion/Biogas Systems on Farms in the United States November 2020 AgSTAR Operator Guidebook PREFACE U.S. EPA AgSTAR Program AgSTAR is a voluntary outreach program that encourages the implementation of anaerobic digestion (AD) projects in the agricultural and livestock sector to reduce methane (CH4) emissions from agricultural residuals including livestock waste. AD projects can be cost-effective mitigation techniques and provide numerous co-benefits to the local communities where they are installed, including environmental, energy, financial, and social sector benefits. AgSTAR is a collaborative program sponsored by the U.S. Environmental Protection Agency (EPA) and the U.S. Department of Agriculture (USDA) that promotes the use of biogas recovery systems to reduce CH4 emissions from livestock waste. As an education and outreach program, AgSTAR disseminates information relevant to livestock AD projects and synthesizes it for stakeholders who implement, enable, or purchase AD projects. The program’s goals are to provide information that helps stakeholders evaluate the appropriateness of an AD project in a specific location, to provide objective information on the benefits and risks of AD projects, and to communicate the status of AD projects in the livestock sector. Through the AgSTAR website (www.epa.gov/agstar) and at public events and other forums, AgSTAR communicates unbiased technical information and helps create a supportive environment for the implementation of livestock AD projects. AgSTAR provides technical input to the USDA Rural Energy for America Program, which provides grant funding for AD systems at farms. -
Industrial Gas Meter with M-Bus for Compressed Air, Natural Gas, Biogas
Flow Industrial gas meter with M-Bus for compressed air, natural gas, biogas... Compressed air and natural gas meters with M-Bus now also directly from the manufacturer. CS Instruments GmbH & Co. KG was the OEM-manufacturer of the ENDYS AIR compressed air meter with M-Bus from 2010 to the end of 2017. The ENDYS AIR products have been marketed exclusively through Hochhut GmbH, wich now works with another manufacturer. The CS Instruments GmbH & Co. KG now offers the products themselves. The successor product of ENDYS AIR now offers all the possibilities of digitization and is the ideal consumption meter for Industry 4.0. The successor products of the well-known ENDYS AIR company Hochhuth have been metrologically improved and completely revised and in addition to the M-Bus interface also have the following additional outputs or bus systems: • Modbus RTU • Modbus TCP or TCP PoE • Profibus, Profinet • 4..20 mA and pulse • Hard (in preparation) The VA 520, VA 500, VA 550 and VA 570 industrial gas meters with M-Bus are the ideal compressed air meters or consumption meters for natural gas, biogas, methane, nitrogen, argon, carbon dioxide for consumption measurement and flow measurement. VA 520, VA 500, VA 550, VA 570 with M-Bus are ideal for conversion or retrofitting and for new installations of gas meters, com- pressed air meters, flow meters, etc. to existing or new energy management software according to DIN ISO 50001 and DIN ISO 16247 and building management systems. Advantages: • Direct display in Nm3/h, or NI/min and temperature in C° • Calorimetric measuring principle - no additional pressure and temperature measurement necessary • High measurement accuracy ¼ to 3 inches • VA 500 and VA 550 insert version from ½ inch to DN 400 / DN 500 www.cs-instruments.com 1 Flow VA 520 Compressed air meter with M-Bus Display twist able by 180°C e.g. -
Trac 2. CO Meter 3. 4 Mulm-‐Gas Detector
HyaHsville Volunteer Fire 2epartment Training Gas Meters 7as Meter9s Carried on the Squad 1. Gas-‐Trac 2. CO Meter 3. 4 Mul5-‐Gas$Detector$8MiniMax$X4$Mul5$Gas$ Detector) 11/22/09 Gas$Meters$ Ga%*5rac General*@nformaon ,he$Gas$,rac$is$an$instrument that is$capable$of$ detec5ng$combus5ble$gases.$,he$Gas$,rac is factory$calibrated$for$methane$in$the$air.$,he$ alarm$Iill$be$set oJ$Ihen$the$methane$ concentra5on$in$the$air$approaches$20$percent of$ the$loIer$explosive$limit 11/22/09 Gas$Meters$ Most Common 2etectable 7ases • Acetone • Smoke$ • Alcohol$ • Steam$ • Ammonia • Industrial$Solvents$ • BenNene • Uet Fuel$ • Ethane$ • Lacquer$,hinner$ • Ethylene$ • Methane$ • Gasoline$ • Naphtha • Propane$ • Hydrogen$Sul[de$ • Refrigerants$ 11/22/09 Gas$Meters$ 11/22/09 Gas$Meters$ Direcons*/o*Dse 1. ,urn$the$Gas-‐,rac$on$in$a non-‐contaminated$ atmosphere$$$ 2. ,he$ready$light should$come$on$to$determine$ that the$meter$is$ready$for$use$ 3. ,he$L.E.D.$labeled$“Slight]$Iill$light Ihen$.1%$of$ the$gas$is$detected.$,he$“Medium]$light Iill$ light Ihen$1%$of$the$gas$is$detected.$,he$ “Alarm]$light Iill$come$on$Ihen$.%$of$the$gas$ is detected. 11/22/09 Gas$Meters$ Direcons*/o*Ds)*EConB.uedF 2.$,o$pinpoint a leak$source_$adjust the$“,icS$Rate]$ control$for$the$sloIest uniform$5cSing$sound.$ ,he$5cS$rate$Iill$then$vary_$corresponding$to$the$ change$in$gas$concentra5on$detected.$,he$5cS$ rate$is$independent of$the$lights$and$alarm_$ Ihich$are$calibrated$to$appropriate$gas$ concentra5ons.$ 11/22/09 Gas$Meters$ CO Meter ,he$C0$Meter$should$be$turned$on$in$an$ uncontaminated$atmosphere.$ ase$common$sense$Ihen$using$the$meter_$if$ people$are$complaining$of$head$aches_$SCMA$ must be$Iorn.$ Donbt rely$on$home$detectors_$as$they$are$not alIays$accurate.$ 11/22/09 Gas$Meters$ CO EIposure Chart EAll 2ata Based on 1 Hour EIposuresF • MNO*334*E3#0ts per*4illion) $no$health$risSc$normal$C0$levels$ COP in$air. -
An Indirect Measurement Method for Gas Consumption of a Diaphragm Gas Meter Based on Gas Pressure Signal Detection
applied sciences Article An Indirect Measurement Method for Gas Consumption of a Diaphragm Gas Meter Based on Gas Pressure Signal Detection Zhao Han , Xiaoli Wang *, Baochen Jiang and Xiaopeng Chen School of Mechanical, Electrical and Information Engineering, Shandong University, Weihai 264209, China; [email protected] (Z.H.); [email protected] (B.J.); [email protected] (X.C.) * Correspondence: [email protected]; Tel.: +86-138-6302-6640 Received: 19 March 2019; Accepted: 31 May 2019; Published: 18 June 2019 Featured Application: This indirect measurement method can be utilized to improve the remote meter reading technology for gas meter. Abstract: At present, the remote meter reading problem for a large number of existing domestic diaphragm gas meters has not been reliably solved. The diaphragm gas meter uses a physical structure to measure gas consumption, so the main problem of remote meter reading is the digitization of gas consumption. Although it is possible to digitize the consumption data by modifying the internal structure of the gas meter or adding sensors, thereby realizing the function of remote meter reading, the modification process is complicated, the modification cost is high, and manual meter reading can only be used for the existing diaphragm gas meters. For this reason, this paper proposes an indirect measurement method of gas consumption based on gas pressure signal detection. The method can digitalize the metering results of the mechanical diaphragm gas meter and develop a state detection function by analyzing the pressure signal of the outlet of the meter without modifying the internal structure of a meter, thus addressing the key difficulties in the construction of a gas meter remote meter reading system. -
Natural Gas Meter Installations
Hibbing Public Utilities Policy Number: CUST094gasmeterinstall Date: May 1, 2004 Subject: NATURAL GAS METER INSTALLATIONS General Requirements Gas meters used to measure the quantity of natural gas used by a customer are owned by the HPUC. The HPUC and the customer will jointly determine the location of all natural gas meters. The HPUC will install, set, and maintain the natural gas meter. Only authorized HPUC personnel can set a meter, turn a meter on or off (except in emergencies), connect a meter to the main gas system, o remove a natural gas meter. Residential Natural Gas Installations The location of residential meters will be jointly determined by the HPUC and then customer in accordance with the following guidelines: 1. Meter installations must comply with all local, state, or federal regulations as stipulated in CFR Part 192. 2. Meters will be located in a safe location that is readily accessible for meter reading and repair. 3. Outside meter locations are mandatory. Outside meters will be installed by a meter set bracket. 4. Inside gas meters are prohibited. 5. Meters and associated relief valves will not be closer than 3 feet to any source of ignition such as electric meters, switches, and transformers. 6. Meter locations will avoid water taps, electric facilities, air intake vents, edges of sidewalks, and driveways. 7. Meters must be installed at least 6 inches above finished grade level. Adopted by Commission Action Pg. 2 – Custo94gasmeterinstall Commercial and Industrial Natural Gas Meter Installations 1) Factors that determine the design of a commercial or industrial natural gas meter installation include: a. -
Section 3.33. Hydrocarbon Gas Vapor-Measuring Devices1
Handbook 44 - 2007 3.33. Hydrocarbon Gas Vapor-Measuring Devices Section 3.33. Hydrocarbon Gas Vapor-Measuring Devices1 A. Application A.1. - This code applies to devices used for the measurement of hydrocarbon gas in the vapor state, such as propane, propylene, butanes, butylenes, ethane, methane, natural gas and any other hydrocarbon gas/air mix. (Amended 1984, 1986, 1988, and 1991) A.2. - This code does not apply to: (a) Liquid-measuring devices used for dispensing liquefied petroleum gases in liquid form (see Sec. 3.32; Code for Liquefied Petroleum Gas and Anhydrous Ammonia Liquid-Measuring Devices). (b) Natural, liquefied petroleum, and manufactured-gas-vapor meters when these are operated in a public utility system. (c) Mass flow meters (see Sec. 3.37. Code for Mass Flow Meters) (Added 1994) A.3. - See also Sec. 1.10; General Code requirements. S. Specifications S.1. Design of Indicating and Recording Elements and of Recorded Representations. S.1.1. Primary Elements. S.1.1.1. General. - A device shall be equipped with a primary indicating element and may also be equipped with a primary recording element. S.1.1.2. Units. - A volume-measuring device shall indicate, and record if equipped to record, its deliveries in terms of cubic meters or cubic feet, or multiple or decimal subdivisions of cubic meters or cubic feet. (Amended 1972 and 1991) S.1.1.3. Value of Smallest Unit. - Volume-Measuring Devices: The value of the smallest unit of indicated delivery, and recorded delivery if the device is equipped to record, shall not exceed: (a) 1 m3 (1000 dm3) (100 ft3) when the maximum rated gas capacity is less than 100 m3/h (10 000 ft3/h); (b) 10 m3 (1000 ft3) when the maximum rated gas capacity is 280 m3/h (10 000 ft3/h) up to, but not including, 1700 m3/h (60 000 ft 3/h); (c) 100 m3 (10 000 ft3) when the maximum rated gas capacity is 1700 m3/h (60 000 ft3/h) or more.