Schneider Electric Instrument Transformers
Total Page:16
File Type:pdf, Size:1020Kb
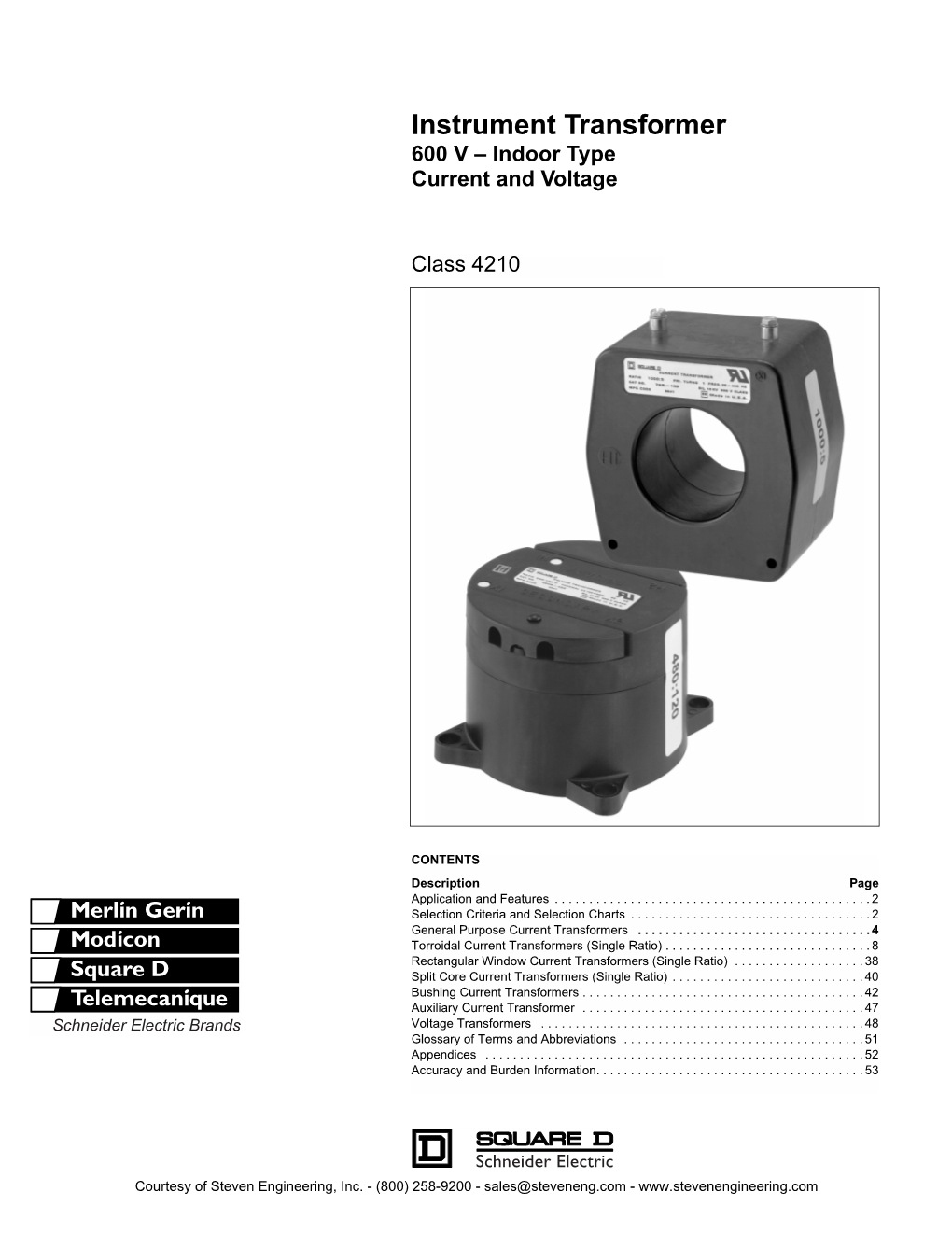
Load more
Recommended publications
-
Mutual Inductance and Transformer Theory Questions: 1 Through 15 Lab Exercise: Transformer Voltage/Current Ratios (Question 61)
ELTR 115 (AC 2), section 1 Recommended schedule Day 1 Topics: Mutual inductance and transformer theory Questions: 1 through 15 Lab Exercise: Transformer voltage/current ratios (question 61) Day 2 Topics: Transformer step ratio Questions: 16 through 30 Lab Exercise: Auto-transformers (question 62) Day 3 Topics: Maximum power transfer theorem and impedance matching with transformers Questions: 31 through 45 Lab Exercise: Auto-transformers (question 63) Day 4 Topics: Transformer applications, power ratings, and core effects Questions: 46 through 60 Lab Exercise: Differential voltage measurement using the oscilloscope (question 64) Day 5 Exam 1: includes Transformer voltage ratio performance assessment Lab Exercise: work on project Project: Initial project design checked by instructor and components selected (sensitive audio detector circuit recommended) Practice and challenge problems Questions: 66 through the end of the worksheet Impending deadlines Project due at end of ELTR115, Section 3 Question 65: Sample project grading criteria 1 ELTR 115 (AC 2), section 1 Project ideas AC power supply: (Strongly Recommended!) This is basically one-half of an AC/DC power supply circuit, consisting of a line power plug, on/off switch, fuse, indicator lamp, and a step-down transformer. The reason this project idea is strongly recommended is that it may serve as the basis for the recommended power supply project in the next course (ELTR120 – Semiconductors 1). If you build the AC section now, you will not have to re-build an enclosure or any of the line-power circuitry later! Note that the first lab (step-down transformer circuit) may serve as a prototype for this project with just a few additional components. -
Diploma in Electrical and Electronics Engineering PAGE 1
` DIPLOMA IN ELECTRICAL AND ELECTRONICS ENGINEERING COURSES OFFERED CODE COURSE CREDITS YEAR/SEMESTER 15O A) FOUNDATION COURSES : (49 CREDITS) (COMMON FOR ALL PROGRAMMES) 0101 Communicative English – I 5 I/ODD 0102 Engineering Mathematics-I 8 I/ODD 0103 Engineering Physics – I 5 I/ODD 0104 Engineering Chemistry – I 5 I/ODD 0105 Engineering Physics- I Practical 1 I/ODD 0106 Engineering Chemistry – I Practical 1 I/ODD 0107 Communicative English – II 4 I/EVEN 0108 Engineering Mathematics-II 5 I/EVEN 0109 Applied Mathematics 5 I/EVEN 0110 Engineering Physics – II 4 I/EVEN 0111 Engineering Chemistry – II 4 I/EVEN 0112 Engineering Physics – II Practical 1 I/EVEN 0113 Engineering Chemistry – II Practical 1 I/EVEN B) CORE TECHNOLOGY COURSES : ( 43 CREDITS) 0201A Workshop Practical 1 I/ODD 0202 Engineering Graphics-I 3 I/ODD 0203 Engineering Graphics-II 3 I/EVEN 0204 Computer Applications Practical – I 1 I/ODD 0205 Computer Applications Practical – II 1 I/EVEN 3201 Electrical Circuit Theory 6 II/ODD 3202 Electrical Machines - I 5 II/ODD 3203 Electronic Devices and Circuits 5 II/ODD 3204 Electrical Circuits and Machines Practical 3 II/ODD 3205 Electronic Devices and Circuits Practical 3 II/ODD 3206 Electrical Workshop Practical 2 II/ODD 3207 Life and Employability Skills Practical 2 II/ODD 3208 Digital Electronics 5 II/EVEN 3209 Integrated CircuitsPractical 3 II/EVEN Diploma in Electrical and Electronics Engineering PAGE 1 ` C) APPLIED TECHNOLOGY COURSES: (58 CREDITS) 3301 Electrical Machines – II 5 II/EVEN 3302 Measurements and Instruments 4 II/EVEN -
LTC3723-1/LTC3723-2 Synchronous Push-Pull PWM Controllers
LTC3723-1/LTC3723-2 Synchronous Push-Pull PWM Controllers FEATURES DESCRIPTIO U ■ High Efficiency Synchronous Push-Pull PWM The LTC®3723-1/LTC3723-2 synchronous push-pull PWM ■ 1.5A Sink, 1A Source Output Drivers controllers provide all of the control and protection func- ■ Supports Push-Pull, Full-Bridge, Half-Bridge, and tions necessary for compact and highly efficient, isolated Forward Topologies power converters. High integration minimizes external ■ Adjustable Push-Pull Dead-Time and Synchronous component count, while preserving design flexibility. Timing The robust push-pull output stages switch at half the ■ Adjustable System Undervoltage Lockout and Hysteresis oscillator frequency. Dead-time is independently pro- ■ Adjustable Leading Edge Blanking grammed with an external resistor. Synchronous rectifier ■ Low Start-Up and Quiescent Currents timing is adjustable to optimize efficiency. A UVLO pro- ■ Current Mode (LTC3723-1) or Voltage Mode gram input provides precise system turn-on and turn off (LTC3723-2) Operation voltages. The LTC3723-1 features peak current mode ■ Single Resistor Slope Compensation control with programmable slope compensation and lead- ■ ing edge blanking, while the LTC3723-2 employs voltage VCC UVLO and 25mA Shunt Regulator ■ Programmable Fixed Frequency Operation to 1MHz mode control with voltage feedforward capability. ■ 50mA Synchronous Output Drivers The LTC3723-1/LTC3723-2 feature extremely low operat- ■ Soft-Start, Cycle-by-Cycle Current Limiting and ing and start-up currents. Both devices provide reliable Hiccup Mode Short-Circuit Protection short-circuit and overtemperature protection. The ■ 5V, 15mA Low Dropout Regulator LTC3723-1/LTC3723-2 are offered in a 16-pin SSOP ■ Available in 16-Pin SSOP Package package. -
THE ULTIMATE Tesla Coil Design and CONSTRUCTION GUIDE the ULTIMATE Tesla Coil Design and CONSTRUCTION GUIDE
THE ULTIMATE Tesla Coil Design AND CONSTRUCTION GUIDE THE ULTIMATE Tesla Coil Design AND CONSTRUCTION GUIDE Mitch Tilbury New York Chicago San Francisco Lisbon London Madrid Mexico City Milan New Delhi San Juan Seoul Singapore Sydney Toronto Copyright © 2008 by The McGraw-Hill Companies, Inc. All rights reserved. Manufactured in the United States of America. Except as permitted under the United States Copyright Act of 1976, no part of this publication may be reproduced or distributed in any form or by any means, or stored in a database or retrieval system, without the prior written permission of the publisher. 0-07-159589-9 The material in this eBook also appears in the print version of this title: 0-07-149737-4. All trademarks are trademarks of their respective owners. Rather than put a trademark symbol after every occurrence of a trademarked name, we use names in an editorial fashion only, and to the benefit of the trademark owner, with no intention of infringement of the trademark. Where such designations appear in this book, they have been printed with initial caps. McGraw-Hill eBooks are available at special quantity discounts to use as premiums and sales promotions, or for use in corporate training programs. For more information, please contact George Hoare, Special Sales, at [email protected] or (212) 904-4069. TERMS OF USE This is a copyrighted work and The McGraw-Hill Companies, Inc. (“McGraw-Hill”) and its licensors reserve all rights in and to the work. Use of this work is subject to these terms. Except as permitted under the Copyright Act of 1976 and the right to store and retrieve one copy of the work, you may not decompile, disassemble, reverse engineer, reproduce, modify, create derivative works based upon, transmit, distribute, disseminate, sell, publish or sublicense the work or any part of it without McGraw-Hill’s prior consent. -
IEEE/PES Transformers Committee
Transformers Committee Chair: Sue McNelly Vice Chair: Bruce Forsyth Secretary: Ed teNyenhuis Treasurer: Paul Boman Awards Chair/Past Chair: Stephen Antosz Standards Coordinator: Jim Graham IEEE/PES Transformers Committee Spring 2019 Meeting Minutes Anaheim, CA March 24 – 28, 2019 Unapproved (These minutes are on the agenda to be approved at the next meeting in Fall 2019) TABLE OF CONTENTS GENERAL ADMINISTRATIVE ITEMS 1.0 Agenda 2.0 Attendance OPENING SESSION – MONDAY MARCH 25, 2019 3.0 Approval of Agenda and Previous Minutes – Susan McNelly 4.0 Chair’s Remarks & Report – Susan McNelly 5.0 Vice Chair’s Report – Bruce Forsyth 6.0 Secretary’s Report – Ed teNyenhuis 7.0 Treasurer’s Report – Paul Boman 8.0 Awards Report – Stephen Antosz 9.0 Administrative SC Meeting Report – Susan McNelly 10.0 Standards Report – Jim Graham 11.0 Liaison Reports 11.1. CIGRE – Craig Swinderman 11.2. IEC TC14 – Phil Hopkinson 11.3. Standards Coordinating Committee, SCC No. 18 (NFPA/NEC) – David Brender 11.4. Standards Coordinating Committee, SCC No. 4 (Electrical Insulation) – Evanne Wang 11.5. ASTM D27 – Tom Prevost 12.0 Approval of Transformer Committee P&P Manual - Bruce Forsyth 13.0 Hot Topics for the Upcoming – Subcommittee Chairs 14.0 Opening Session Adjournment CLOSING SESSION – THURSDAY MARCH 28, 2019 15.0 Chair’s Remarks and Announcements – Susan McNelly 16.0 Meetings Planning SC Minutes & Report – Tammy Behrens 17.0 Reports from Technical Subcommittees (decisions made during the week) 18.0 Report from Standards Subcommittee (issues from the week) 19.0 -
SP0504 Power Transformer Testing
POWER TRANSFORMER TESTING SWP • Hold current licences for any vehicles and equipment they 1. PURPOSE AND SCOPE may be required to operate. The purpose of this Standard Work Practice (SWP) is to Required Training standardise and prescribe the method for testing power transformers. Staff must be current in all Statutory Training relevant for the task. Testing of current transformers, voltage transformers or auxiliary transformers internal to the power transformer are not included in All workers must have completed Field Induction or have this SWP. recognition of prior Ergon Energy Field Experience. Contractors must have completed Ergon Energy's Generic 2. STAFFING RESOURCES Contractor Worker Induction. Adequate staffing resources with the competencies to safely complete the required tasks as per MN000301R165: 8 Level Field 3. DOCUMENTATION Test Competency CS000501F115 . Daily/Task Risk Management Plan These competencies can be gained from, but not limited to any or ES000901R102 . Health and Safety Risk Control Guide all of the following:- SP0504R01. Power Transformer Testing Job Safety Analysis • Qualifying as an Electrical Fitter Mechanic. SP0504C01R01. Power Transformer IR and DDF Temperature • Qualifying as a Technical Service Person. Correction • Training in the safe use of relevant test equipment. SP0504C04. Power Transformer No Load Loss Test Report Requirement for all live work: SP0504C05. Power Transformer Load Loss Test Report • Safety Observer (required for all “live work” as defined in SP0504C06. Power Transformer Load Loss and Impedance the ESO Code of Practice for Electrical Work). Calculation All resources are required to: SP0504C08. Power Transformer Testing Competency Assessment • Have appropriate Switching and Access authorisations for the roles they are required to perform and have the ability SP0504C13. -
Instruction Manual Installation Operation Copyright © 2012 Kato Engineering, Inc
Instruction Manual Installation Operation Copyright © 2012 Kato Engineering, Inc. All rights reserved Maintenance Motor-Generator Set Synchronous Common Shaft Publication 350-03006-00 (07/18/2012) Kato Engineering, Inc. | P.O. Box 8447 | Mankato, MN USA 56002-8447 | Tel: 507-625-4011 [email protected] | www.KatoEngineering.com | Fax: 507-345-2798 Copyright © 2012 Kato Engineering, Inc. All rights reserved Page 1 Table of Contents Introduction............................................................................... 4 Foreword..................................................................................... 4 Safety instructions.......................................................................4 Ratings/description......................................................................4 Construction and Operating Principles.................................. 5 Stator...........................................................................................5 Rotor........................................................................................... 5 Brushless exciters....................................................................... 6 Installation................................................................................. 7 Receiving inspection................................................................... 7 Unpacking and moving............................................................... 7 Location...................................................................................... 7 Mounting.................................................................................... -
Current Transformer Theory & Testing
Current Transformer Theory & Testing Hands On Relay School 2016 Jay Anderson – Omicron [email protected] www.OmicronEnergy.com Agenda • Introduction • Current Transformer Basics • Construction & Types • Industry Standards • Applications • Testing Current Transformer Basics © OMICRON Page 3 Function of Current Transformers • Convert Primary Power Signals to Manageable Values for • Indicating Meters • Revenue Metering • Protective Relay Systems • Power Generation • Plant Monitoring Systems • Fault Recorders • SCADA • Overall Electric Grid Monitoring (Local Dispatch & ISO Level) • Building (Energy) Management Systems (HVAC,refrigeration...) • Load Control January 19, 2016 Page: 4 Current Transformers • Insulation from High Voltages and Currents • Isolation from other systems • Safety • Standardization • Accuracy ( Ratio & Phase) • Typically Low Power Rating • Thermal Considerations • Burden Considerations January 19, 2016 Page: 5 Current Transformers • Insulation Consistent With Voltage Use • Wide Range of Current to Replicate (Unlike VTs) • Metering or Protective Class Ratings • Typically Unprotected • Dangerous When Open Circuited January 19, 2016 Page: 6 Compliance & Standards Instrument Transformers Are Expected to Perform & Conform IEEE ANSI IEC in Europe & Asia NERC Reliability Standards in US Supported standards • IEEE C57.13 standard requirements for instrument transformers • IEEE C57.13.6 standard for high-accuracy instrument transformers • IEC 60044-1 current transformers • IEC 60044-6 requirements for protective current -
The Remote Calibration of Instrument Transformers
The remote calibration of instrument transformers S. Rens orcid.org/0000-0001-8428-3893 Dissertation submitted in fulfilment of the requirements for the degree Master of Engineering in Electrical and Electronic Engineering at the North-West University Supervisor: Prof. A.P.J. Rens Co-supervisor: Prof. J.E.W. Holm Graduation ceremony: May 2019 Student number: 23509333 ABSTRACT Successful operation and control of a power system is dependent on the accurate measurement of field data. Each measurement received is the result of a chain of instrumentation and data handling processes, and with each process a certain amount of uncertainty is introduced in the measurement result. Instrument transformers, additional transducers, analog-to-digital (A/D) converters, scaling and conversion procedures, synchrophasor recorders and communication equipment all contribute to the uncertainty in measurement. Errors in this measurement chain can either be systematic, random or installation errors. Instrumentation transformers convert (and isolate) primary power system current and voltage waveforms into standardised instrumentation circuit values (i.e. 110 V and 5 A) for more convenient measurement purposes. Nominal conversion ratios, specified on nameplates, may differ from the actual conversion ratios due to manufacturing, drift over time and environmental conditions. To eliminate biased measurements received from instrument transformers, calibration of instrument transformers should be performed periodically. Traditionally this has been done by means field work creating an out-of-service condition. It is time-consuming, expensive and labour intensive. An opportunity exists due to the increased availability of synchronous data for the idea of remote calibration of instrument transformers. This idea estimates a ratio correction factor (RCF) for the instrument transformers using synchrophasor data over a transmission line. -
Explore New Paths with the CT Analyzer – Extended Testing Benefits for Your Applications
Presentation – 4.1 Explore new paths with the CT Analyzer – Extended testing benefits for your applications Florian Predl, OMICRON, Austria Ie excitation current IS secondary current 1. Introduction IP primary current Xm main inductivity of the core This paper describes on the one hand side the principal Rm magnetic losses of the core test procedure of the CT Analyzer and points out the NP,NS amount of turns of the ideal core advantages of this test method in regards to a RCT ohmic resistance of secondary turns conventional high current injection measurement EMF Electro-Motive Force – secondary core voltage method. On the other hand side it elucidates special US secondary terminal voltage current transformer testing applications and reveals RB ohmic part of complex burden attempts at solutions. Furthermore, the CT Analyzer PC XB inductive part of complex burden Tools are introduced and their advantages and φB phase angle of burden possibilities for the individual user are presented. Figure 2 shows the vector diagram of current and voltages for a linear main inductivity. 2. Principal Test Procedure of the CT Analyzer The CT Analyzer measures the losses of a current transformer according to the equivalent circuit diagram of the current transformer, in terms of the copper losses and the iron losses. The copper losses are described as the winding resistance RCT of the current transformer. The iron losses are described as the eddy losses as eddy resistance Reddy and the hysteresis losses as hysteresis resistance RH of the core. With this knowledge about the total losses of the core, the CT Analyzer is able to calculate the current ratio error and the phase displacement for any primary current and for any secondary burden. -
Distribution Transformers–Medium and High Voltage Section 21
Distribution Transformers–Medium and High Voltage Section 21 com . Secondary Substation – SST .....................................................21-2 Three-phase Padmounted – PADS ..........................................21-4 Single-Phase Pole-Mounted – POLES......................................21-6 Network Transformers ..............................................................21-9 Voltage Regulators VR-1 .............................................................................................................21-10 Bushing Potential Devices......................................................21-13 ElectricalPartManuals . Publications and Reference: See Section 22 for a complete list of additional product-related publications Rev. 1/08 ® 21-1 Prices and data subject www.geelectrical.com BuyLog Catalog wwwto change without notice Distribution Transformers–Medium and High Voltage Section 21 GE-PROLEC® Liquid Filled Secondary Substation Transformers-SST GE-PROLEC® Secondary Substation Transformers will meet all of your industrial applications for power distribution. These transformers have a robust construction and are designed with the capability to coordinate with a wide diversity of equipment such as switchboards, LIS, MCCs, etc. com Applications Industrial . —Oil and Gas —Chemical Industry —Paper Industry —Steel Industry —Cement Industry Commercial —Airports —Stadiums —Office Building —Waste Water General Construction Features —Stores —The liquid insulated, secondary type substation transformer Utility is designed, manufactured -
B. Tech Electrical.Pdf
JECRC University Course Structure for Electrical Engineering (B.Tech.) JECRC UNIVERSITY Faculty of Engineering & Technology B.Tech in Electrical Engineering Teaching Scheme Semester III Subject Code Subject Contact Hrs Credits L-T-P Electronics Devices & Circuits 3-1-2 5 Circuit Analysis – I 3-1-0 4 Electrical Machines – I 3-1-2 5 Electrical Measurements 3-1-2 5 Mathematics – III 3-1-0 4 Computer Programming – I 3-0-2 4 Total 18-5-8 27 JECRC UNIVERSITY Faculty of Engineering & Technology B.Tech in Electrical Engineering Teaching Scheme Semester IV Subject Code Subject Contact Hrs Credits L-T-P Analogue Electronics 3-1-2 5 Digital Electronics 3-0-2 4 Circuit Analysis – II 3-1-0 4 Electrical Machines – II 3-1-2 5 Advanced Mathematics 3-1-0 4 Generation of Electric Power 3-0-0 3 Total 18-4-6 25 JECRC UNIVERSITY Faculty of Engineering & Technology B.Tech in Electrical Engineering Teaching Scheme Semester V Subject Code Subject Contact Hrs Credits L-T-P Power Electronics-I 3-1-2 5 Microprocessor & Computer 3-0-2 4 Architecture Transmission & Distribution – I 3-1-0 4 Control Systems 3-1-2 5 Utilization of Electrical Power 3-0-0 3 Digital Signal Processing 3-0-0 3 Total 18-3-6 24 JECRC UNIVERSITY Faculty of Engineering & Technology B.Tech in Electrical Engineering Teaching Scheme Semester VI Subject Code Subject Contact Hrs Credits L-T-P Power Electronics –II 3-1-2 5 Power System Analysis 3-1-2 5 EHV AC/DC Transmission 3-0-0 3 Switch Gear & protection 3-0-0 3 Instrumentation 3-0-0 3 Transmission & Distribution – II 3-1-0 4 Economics 0-0-2 1