Social Security Cards
Total Page:16
File Type:pdf, Size:1020Kb
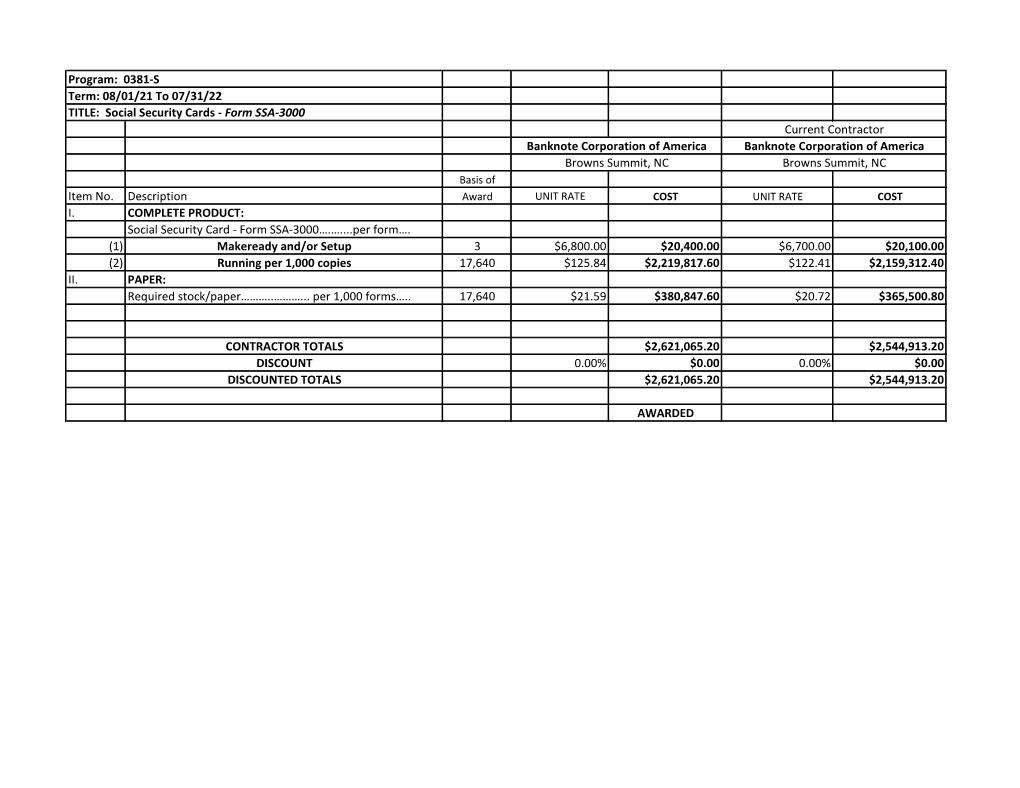
Load more
Recommended publications
-
Qualification of Test Method for Package Perforation Evaluation
Rochester Institute of Technology RIT Scholar Works Theses 4-8-2016 Qualification of estT Method for Package Perforation Evaluation Di Wang Follow this and additional works at: https://scholarworks.rit.edu/theses Recommended Citation Wang, Di, "Qualification of estT Method for Package Perforation Evaluation" (2016). Thesis. Rochester Institute of Technology. Accessed from This Thesis is brought to you for free and open access by RIT Scholar Works. It has been accepted for inclusion in Theses by an authorized administrator of RIT Scholar Works. For more information, please contact [email protected]. Qualification of Test Method for Package Perforation Evaluation By DI WANG A Thesis Submitted in Partial Fulfillment of the Requirements for the Degree of Master of Science in Packaging Science Department of Packaging Science College of Applied Science and Technology Rochester Institute of Technology Date of Submission: 04/08/2016 Committee Approval: Deanna Jacobs Date Thesis Advisor Changfeng Ge Date Thesis Advisor Kathy Myers Date Committee Member Carol Herring Date Committee Member Abstract The purpose of this paper was to develop a new test method for packaging perforation evaluation to replace the current test method due to the human variables during test and the inconsistency of test results. First, an end user survey was conducted to find out a typical opening pattern which was used by most of the consumers when opening the packaging perforation. Second, the typical opening pattern was further analyzed by an experiment. The opening process was recorded as videos and the relationship between displacement and time was analyzed in Matlab. It was found that the opening process of typical opening pattern was consist of horizontal direction movement and vertical direction movement. -
Estimation of the Compressive Strength of Corrugated Cardboard Boxes with Various Perforations
energies Article Estimation of the Compressive Strength of Corrugated Cardboard Boxes with Various Perforations Tomasz Garbowski 1 , Tomasz Gajewski 2 and Jakub Krzysztof Grabski 3,* 1 Department of Biosystems Engineering, Poznan University of Life Sciences, Wojska Polskiego 50, 60-627 Pozna´n,Poland; [email protected] 2 Institute of Structural Analysis, Poznan University of Technology, Piotrowo Street 5, 60-965 Pozna´n,Poland; [email protected] 3 Institute of Applied Mechanics, Poznan University of Technology, Jana Pawła II Street 24, 60-965 Pozna´n,Poland * Correspondence: [email protected] Abstract: This paper presents a modified analytical formula for estimating the static top-to-bottom compressive strength of corrugated board packaging with different perforations. The analytical framework is based here on Heimerl’s assumption with an extension from a single panel to a full box, enhanced with a numerically calculated critical load. In the proposed method, the torsional and shear stiffness of corrugated cardboard, as well as the panel depth-to-width ratio is implemented in the finite element model used for buckling analysis. The new approach is compared with the successful though the simplified McKee formula and is also verified with the experimental results of various packaging designs made of corrugated cardboard. The obtained results indicate that for boxes containing specific perforations, simplified methods give much larger estimation error than the analytical– numerical approach proposed in the article. To the best knowledge of the authors, the influence of the perforations has never been considered before in the analytical or analytical–numerical approach for estimation of the compressive strength of boxes made of corrugated paperboard. -
Improvement of Punch and Die Life and Part Quality in Blanking of Miniature Parts
Improvement of Punch and Die Life and Part Quality in Blanking of Miniature Parts DISSERTATION Presented in Partial Fulfillment of the Requirements for the Degree Doctor of Philosophy in the Graduate School of The Ohio State University By Soumya Subramonian Graduate Program in Mechanical Engineering The Ohio State University 2013 Dissertation Committee: Dr.Taylan Altan, Advisor Dr.Blaine Lilly, Advisor Dr.Gary L.Kinzel Dr.Jerald Brevick Abstract Blanking or piercing is one of the most commonly used sheet metal manufacturing processes in the industry. Having a good understanding of the fundamentals and science behind this high deformation shearing process can help to improve the tool life and blanked edge quality in various ways. Finite Element Modeling of the blanking process along with experimental testing is used in this study to study the influence of various process parameters on punch and die life and blanked edge quality. In high volume blanking and blanking of high strength materials, improving the tool life can save not only tool material but also change over time which can take up to a few hours for every change over. The interaction between punch, stripper plate and sheet material is first studied experimentally since a fundamental understanding of the behavior of these components at different blanking speeds is very essential to design robust tooling for high speeds. A methodology is developed using the experimentally obtained blanking load and FEM of blanking to obtain flow stress data of the sheet material at high strains and strain rates. This flow stress data is used to investigate the effects of various process parameters on tool stress and blanked edge quality. -
Dupont™ Tyvek® Sheathing Membrane Installation Guidelines
Installation Guidelines Installation DuPont ™ Tyvek ® Sheathing Sheathing Membrane DuPont™ Tyvek® Sheathing Membrane Installation Guidelines HELPING YOU GET THE JOB DONE RIGHT FOR BUILDINGS LESS THAN 5 STORIES AND Canadian Version REVISION 1/19 LOW-RISE MULTI-FAMILY RESIDENTIAL BUILDINGS LESS THAN 6 STORIES DuPont™ Tyvek® Sheathing Membrane Installation Guidelines Table of Contents Applicable Products Applicable Products ............................................................................................................................3 Sheathing Membranes Required Materials Based on Project Requirements, Details, and Specifications ..............................4 PRODUCT DIMENSIONS AREA Warranty .............................................................................................................................................4 Sheathing Membrane Code Requirements ........................................................................................4 DuPont™ Tyvek® HomeWrap® 18 in x 100 ft 150 sq ft General Instructions ...........................................................................................................................5 (0.46 m x 30.48 m) (13.93 m2) Special Considerations .......................................................................................................................5 3 ft x 100 ft 300 sq ft Continuity ...........................................................................................................................................7 (0.91 m x 30.48 m) (27.87 m2) -
The Influence of the Piercing Punch Profile on the Stress Distribution on Its Cutting Edge
MATEC Web of Conferences 254, 02001 (2019) https://doi.org/10.1051/matecconf/201925402001 MMS 2018 The influence of the piercing punch profile on the stress distribution on its cutting edge Dominik Wojtkowiak1,* and Krzysztof Talaśka1 1 Chair of Basics of Machine Design, Poznan University of Technology, ul. Piotrowo 3, 60-965 Poznań, Poland; Abstract. Modifying the piercing punch profile may have a positive effect on the belt perforation process. Using the proper shape of the tool may reduce the perforation force and improve the quality of the holes. However, complex geometry of the punch can also cause an adverse stress distribution, which leads to a faster tool wear. In the presented paper, several different piercing punch profiles were tested using FEM analyses in ABAQUS and the obtained stress distributions along its cutting edges were analyzed. For the selected group of the piercing punches, the influence of variable geometrical features (a radius of rounding, an angle of chamfering or a depth of the bowl) on the stress distribution were also shown. Based on the results, it is possible to predict how modifying the punch profile will affect the shortening of the tool life, compared to the basic flat-end cylindrical piercing punch. The following research can be useful in the design process of the punching tools used for vacuum conveyor belts perforation. Keywords: belt, perforation, punching, tool optimization, polymer composite 1 Introduction Due to the variety of the construction, and as a result the mechanical properties of the polymer composite belts, which are subject to the perforation process (Fig. 1), it is very difficult to design the universal tool for each type of belt [1-3]. -
Estimation of the Perforation Force for Polymer Composite Conveyor Belts Taking Into Consideration the Shape of the Piercing Punch
The International Journal of Advanced Manufacturing Technology (2018) 98:2539–2561 https://doi.org/10.1007/s00170-018-2381-3 ORIGINAL ARTICLE Estimation of the perforation force for polymer composite conveyor belts taking into consideration the shape of the piercing punch Dominik Wojtkowiak1 · Krzysztof Talaska´ 1 · Ireneusz Malujda1 · Grzegorz Domek2 Received: 16 February 2018 / Accepted: 27 June 2018 / Published online: 13 July 2018 © The Author(s) 2018 Abstract Due to the improvement of the mechanical properties of polymer composite belts used in vacuum belt conveyors, its perforation process causes a lot of technical issues for manufacturers worldwide. The objective of this paper is to analyze the belt punching process with two cutting edges and present the influence of the piercing punch shape on the perforation force. Based on the analysis, the analytical stress model was derived and validated by using both empirical and FEM tests. The application of the proposed model was proved by presenting the methodology used to estimate the perforation force for the flat piercing punch based on the mechanical properties of the belt obtained from simple strength tests (uniaxial tension, compression, and shear), with an error between 4 and 15%. In this report, the analysis of the piercing punch profiles was made and eight different piercing punch profiles were tested. Presented results confirmed that the spherical bowl punch may be considered as a most effective tool for belt punching, because it reduced the perforation force by 60% and the precision of the created holes was the best among the tested punch profiles for all three groups of polymer composite belts. -
Cutting-Dies for Packaging. Exceptional Performance
English Editorial 3 EDITORIAL. The world is evolving. The packaging industry as well. As are your requirements. And those of your customers. Individualization is the slogan of the future. A product does not have only one kind of packaging. It has many. One Easter edition. One summer edition. One winter edition. And on top of that various special sizes. And all this for one and the same product. We are all part of this evolution. You as our client. We as a manufacturer of cutting-dies. Of thermoforming tools. Of machines. And materials. As the Marbach Group. In these changing times we at Marbach concentrate on one clear goal: the best performance. For you. Your demands. And not only in the high-end segment. The best performance in every price range. Our experienced team does everything to enhance your performance. With every process. Every thought. And every breath. For you. You can sense it when our experts advise, support and attend to you with experience second to none. So you are in safe hands. And always one decisive step ahead. With the best performance. Packaging. Performance. You. Come with us. into a successful future. Peter Marbach Owner & Managing Director Marbach Group PACKAGING. 8 The world of packaging A history of success PERFORMANCE. 14 By Marbach In all areas YOU. 20 In the best hands Logistics CSR. Taking care of the future For your security PRODUKTE. 28 Cutting-dies for packaging 30 Dieboards 32 Knifing 36 Nicks 38 Cutting rules 40 Rubbering 44 Finishing 48 Embossing 52 Special technologies 54 Braille 56 Crease plate die 58 mpower|+ 60 Cutting-dies for special applications 62 Counter plates 64 Stripping 70 Tools Materials Blanking 76 Tools Materials Quality control 82 Logistics & equipment 84 Rotary tools for corrugated board 86 Rotary cut, crease and embossing tools 90 MACHINES. -
Laser Perforation for Computer Paper Claude F
Rochester Institute of Technology RIT Scholar Works Theses Thesis/Dissertation Collections 1-1-1989 Laser perforation for computer paper Claude F. Gattuso Follow this and additional works at: http://scholarworks.rit.edu/theses Recommended Citation Gattuso, Claude F., "Laser perforation for computer paper" (1989). Thesis. Rochester Institute of Technology. Accessed from This Thesis is brought to you for free and open access by the Thesis/Dissertation Collections at RIT Scholar Works. It has been accepted for inclusion in Theses by an authorized administrator of RIT Scholar Works. For more information, please contact [email protected]. LASER PERFORATION FOR COMPUTER PAPER by Claude F. GATTUSO A thesis submitted in partial fulfillment of the requirements for the degree of Master of Science in the School of Printing Management and Sciences in the College of Graphic Arts and Photography of the Rochester Institute of Technology January, 1989 Thesis Advisor: Mr. Chester Daniels Certificate of approval -- Master's Thesis School of Printing Management and Sciences Rochester Institute of Technology Rochester, New York CERTIFICATE OF APPROVAL MASTER'S THESIS This is to certify that the Master's Thesis of Claude GATTUSO with a major in Printing Technology has been approved by the Thesis Committee as satisfactory for the thesis requirements for the Master of Science degree at the convocation of January, 1989. Thesis Committee: Chester A Daniels Thesis Advisor Joseph L Noga_ Graduate Coordinator Joseph E Brown Director or Designate ii Title of Thesis: Laser perforation for Computer paper I, Claude Gattuso, prefer to be contacted each time a request for reproduction is made. I can be reached at the following address. -
Retention Fastener Preference for Fisher-Price Toy Packaging
Rochester Institute of Technology RIT Scholar Works Theses 2010 Retention fastener preference for Fisher-Price toy packaging Lakeshia Haynes Follow this and additional works at: https://scholarworks.rit.edu/theses Recommended Citation Haynes, Lakeshia, "Retention fastener preference for Fisher-Price toy packaging" (2010). Thesis. Rochester Institute of Technology. Accessed from This Thesis is brought to you for free and open access by RIT Scholar Works. It has been accepted for inclusion in Theses by an authorized administrator of RIT Scholar Works. For more information, please contact [email protected]. Retention Fastener Preference for Fisher-Price Toy Packaging By Lakeshia P. Haynes Thesis Submitted to the Department of Packaging Science College of Applied Science and Technology In partial fulfillment of the requirements for the degree of Master of Science Rochester Institute of Technology 2010 1 Department of Packaging Science College of Applied Science and Technology Rochester Institute of Technology Rochester, New York CERTIFICATE OF APPROVAL ___________________________ M.S. DEGREE THESIS __________________________ The M.S. degree thesis of Lakeshia Haynes has been examined and approved by the thesis committee as satisfactory for the requirements for the Master of Science Degree __________________Deanna Jacobs __________________Craig E. Densmore ________________ November, 15, 2010 2 Dedication This thesis is dedicated to my family, friends, and those who have encouraged and supported me throughout this journey. You have been a source of motivation and inspiration to me in so many ways… Thank - You 3 Retention Fastener Preference for Fisher-Price Toy Packaging By Lakeshia Haynes Abstract “Wrap Rage” continues to be a growing phenomenon as consumers become increasingly frustrated with toy packaging. -
Determination of the Effective Geometrical Features of the Piercing
The International Journal of Advanced Manufacturing Technology (2019) 104:315–332 https://doi.org/10.1007/s00170-019-03746-7 ORIGINAL ARTICLE Determination of the effective geometrical features of the piercing punch for polymer composite belts Dominik Wojtkowiak1 · Krzysztof Talaska´ 1 Received: 21 December 2018 / Accepted: 14 April 2019 / Published online: 31 May 2019 © The Author(s) 2019 Abstract Punch optimization is important in improving the technological process of belt perforation. Research about this process can rarely be found in the scientific literature. The objective of this paper is to determine the effective geometry of the piercing punches with a spherical bowl used for polymer composite belts. In order to fulfill this goal, the complex research of the influence of the geometrical features of the piercing punch on the perforation force, the hole quality, and the tool life has been conducted. For derivation of the proposed model, the authors have used the combination of analytical and FEM analyses, along with the experimental tests validation. Based on the results, there are clear correlations between the depth of the spherical bowl punch and the perforation force or the hole diameter deviation. By analyzing the ratio of the perforation and transverse force, we are able to evaluate how the tool life will change for different sets of geometrical parameters. All these correlations have been used to derive the indicators of the perforation force, tool life, and hole quality. Based on those, the optimization function has been specified. Finding the minimum value of this function makes it possible to define the optimal tool geometry. -
Dupont Self-Adhered Flashing Systems
DuPont™ DUPONT SELF-ADHERED FLASHING SYSTEMS INSTALLATION GUIDELINES FOR BUILDINGS GREATER THAN 4 STORIES AND HIGH PERFORMANCE INSTALLATIONS OF ANY HEIGHT REVISION 6/18 DuPont Self-Adhered Flashing Systems Installation Guidelines Table of Contents Note Note .................................................................................................................................. 2 This installation guideline outlines recommended installation techniques and details for ™ ™ ® Applicable Products .......................................................................................................... 3 DuPont self-adhered flashing products and where applicable, DuPont Tyvek CommercialWrap and/or DuPont™ Tyvek® CommercialWrap D, referred to in this Warranty ........................................................................................................................... 3 document as DuPont™ Tyvek® air and water barriers. General Instructions ........................................................................................................ 3 Key Installation Requirements for Drainable Window / Door Installation Under the Limited Product and Labor Warranty ................................................................................ 4 Installation Methods for DuPont Flashing Systems products AFTER DuPont™ Tyvek® Air and Water Barrier is Installed......................... 6 Non-Flanged Window .................................................................................................. 6 Non-Flanged Window with -
Perforations
technicaloverview Perforations Background Selecting the appropriate The purpose of this bulletin is to help educate and define Perforation TPI different types of perforation blades used in the industry and how to select the appropriate perforation for each application. Perforation Blades Perforation Rule In the label industry perforation blades are made to cut through to the anvil (metal to metal) and are set into engraved rotary tools which can be made with multiple precision milled slots at equal or special locations around the roll. Perforation blades 3-4 TPI – When one section of the substrate needs to detach can also be engraved as part of a regular die cutting tool, easily from another. This TPI is often applied in business forms pending on the complexity of the label. Paper and film facestock that contain stubs. can be perforated, but generally in the label industry, it is only 5-6 TPI – Stronger than 3-4 TPI, this TPI has more tears, but is recommend to perforate paper liners. too loose for forms that must remain intact. Perforations with the appropriate cut to tie ratio are used when 7-10 TPI – A medium release with moderate tear resistance, this labels have to be fan folded as part of the finishing process. TPI is commonly used for perforating the liner between labels so Perforations can be used in the machine or cross direction of the end user can tear with ease. the web. If used in the machine, direction perforation wheels are typically used, while blades or perforation rules are used in the 11-14 TPI – These perforations can be used in fan folding cross direction.