Structural Design of a Cantilevered Building
Total Page:16
File Type:pdf, Size:1020Kb
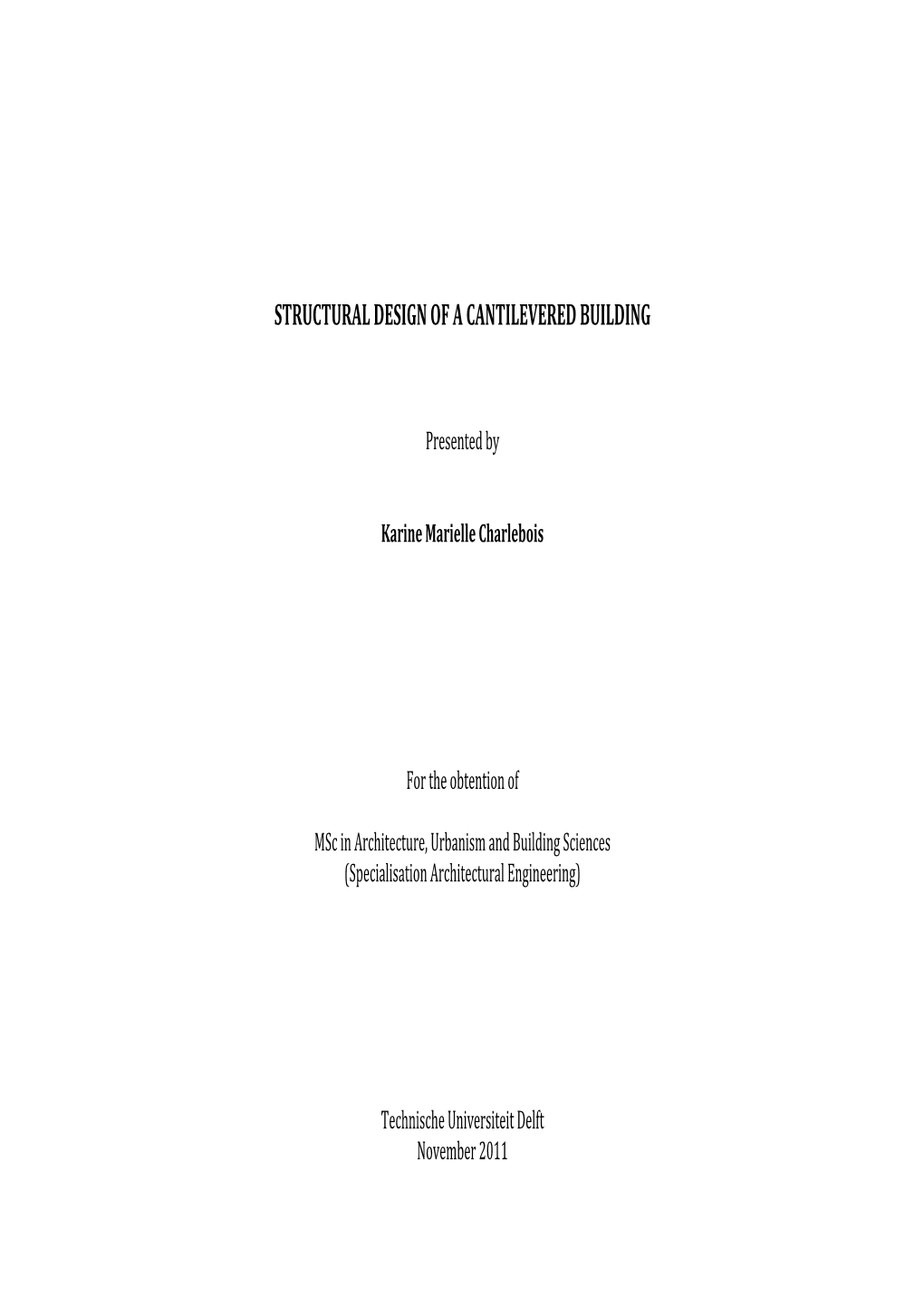
Load more
Recommended publications
-
Adobe Corporate Campus Utah, Usa – Structure Becomes the Architecture
ADOBE CORPORATE CAMPUS UTAH, USA – STRUCTURE BECOMES THE ARCHITECTURE GEOFF S SHARP Senior Project Engineer, Holmes Consulting Group LP SUMMARY Phase one of Adobe Corporation’s new corporate campus is an example of where the thoughtful selection of structural system and construction materials allowed for seamless integration of engineering and architecture. Constructed of post tensioned and conventionally reinforced concrete the office structure showcases what can be achieved when the structure becomes the architecture. At over 200 metres in length and boasting cantilevered frames and a 25 metre “bridge” the use of concrete was essential to the success of this new office building. INTRODUCTION In late 2012, United States based software giant Adobe Corporation moved into their new 28,000 square metre campus in Lehi, Utah. The decision to expand away from their long standing Silicon Valley home required their new facility to make a statement. It needed to attract a new class of outdoors-loving young professionals. Located approximately 50km south of Salt Lake City, the resulting buildings form stage one of their impressive new home on the “Silicon Slopes” of Utah. Challenges included a highly sloped site with significant variation in subsoil conditions and a dual carriage roadway dividing the property. Figure 1 below shows a rendering of the phase one buildings Figure 1 - Phase 1 Adobe Campus Rendering, courtesy of WRNS Studio The lead architects for the project were WRNS Studio of San Francisco with structural engineering delivered through a collaboration between Holmes Culley in San Francisco and Dunn Associates in Salt Lake City. The design process between architect and engineer was very successful due to an open and collaborative approach. -
Cantilever Bridges: the Governor Harry W
CANTILEVER BRIDGES: THE GOVERNOR HARRY W. NICE MEMORIAL BRIDGE From a technical perspective, cantilever construction of a bridge defines a specific form of support of the bridge rather than a particular bridge type such as the truss or girder. Simply supported bridges are directly supported on piers and abutments, while continuous structures, as developed in both metal and reinforced concrete during the late nineteenth and early twentieth centuries, include spans that are continuous across one or more intermediate supports. By contrast, the cantilever form of support occurs when the support is at one end and the other end of the span is free. Cantilever bridges consist of a series of cantilevered spans including a main span and two anchor spans which flank it (Pennsylvania Historical and Museum Commission, and Pennsylvania Department of Transportation 1986:124). Based on historical research alone, cantilever bridges in Maryland appear to be represented by only one bridge, which may be briefly described in order to provide historic technological context for the evaluation of that bridge, the 1940 Governor Harry W. Nice Memorial Bridge carrying U.S. 301 over the Potomac River. Bridge historian J.A.L. Waddell noted that "the development of the cantilever. did not proceed very far until modern times, when the truss form of structure had become established and when iron and steel constituted the materials of construction" (Waddell 1916:7). Waddell and subsequent technological historians dated the major advent of modern cantilever bridges to the design and construction of the high bridge over the Kentucky River at Dixville in 1876-1877. -
Using a Cmos-Biomems Cantilever Sensor For
USING A CMOS-BIOMEMS CANTILEVER SENSOR FOR ORCHID VIRUS DETECTION Lu-Hsun Cheng1, Ya-Chun Chang2, Wen-Chi Hu2, Hsin-Hao Liao3, Hann-Huei Tsai3,Ying-Zong Juang3 and Yen-Wen Lu1 1Dept. of Bio-Industrial Mechatronics Engineering, 2Dept. of Plant Pathology & Microbiology, National Taiwan University, Taipei Taiwan, ROC, 3National Chip Implementation Center (CIC), Hsinchu, Taiwan, R.O.C ABSTRACT We present a preliminary study on utilizing cantilever biosensors to detect Odontoglossum ringspot tobamovirus (ORSV) - one of the most prevalent viruses affecting the health of orchids. The cantilever surfaces of the biosensor are immobilized by ORSV-antibody (Ab) as the recognition probe for ORSV detection. Implemented by using commercially available CMOS technology and post-processed for bio-MEMS capability, the biosensors are embedded with piezoresistors, which can realize surface stress changes due to cantilever deflection coming from the specific bioaffinity between the antigen (Ag) and the antibody. The result shows -0.7% and +0.6% resistivity change when ORSV-Ab and ORSV are respectively presented. KEYWORDS: Cantilever, Odontoglossum ringspot tobamovirus, Piezoresistor, CMOS BioMEMS INTRODUCTION Cantilever biosensors have been used as a sensitive and label-free diagnostic platform for malignant disease diagnosis by detecting DNA mismatch or protein biomarkers [1-3]. Figure 1 depicted the schematics of our device that contained an array of cantilevers with imbedded piezoresistors. The detection is normally achieved by modifying the surface of the cantilever with recognition molecules. The specific interaction between the recognition molecules and the target biomarkers generates surface stress and makes the deflection of the cantilever. The deflection, which is normally several nanometers, can be measured using either optical or piezoresistive readouts. -
Basic Structures
Basic Structures What is a structure? The structure of a building is the part which is responsible for maintaining the original shape of the building under the influence of the forces, loads and other environmental factors to which is subjected. Examples of structural components include: _Steel beams, columnsm roof trusses ans space frames _Reinforced concrete beams, columns, retaining walls and foundations Below picture shows the Lower Manhattan skyline in New York, one of the greatest concentrations of high-rise buildings in the world. Space limitations on the island meant building construction had to proceed upwards rather than outwards, and the presence of solid rock made foundations for these soaring structures feasible. [Image below: Lower Manhattan skyline in New York, USA] Structural understanding The basic function of a structure is to transmit loads from the position of application of the load to the point of support and thus to the foundations in the ground. Any structure must satisfy the following criteria: 01// Aesthetics (it must look nice). 02// Ease of maintenance. 03// Durability. This means that the materials used must be resistant to corrosion, spalling (pieces falling off), chemical attack, rot. 04// Fire resistance. While few materials can completely resist the effects of fire, it is important for a building to resist fire long enough for its occupants to be safely evacuated. [Image below: Roof structure of Quartier 206 shopping mall, Berlin, Germany] Safety and serviceability There are two main requirements of any structure: it must be safe and it must be serviceable. Safe means that the structure should not collapse Serviceability means that the structure should not deform unduly under the effects of defl ection, cracking or vibration. -
Builder's Guide to Trusses
Table of Contents Roof Construction Techniques: Pro’s and Con’s . 2 Trusses: Special Benefits for Architects and Engineers . 4 Special Benefits for Contractors and Builders . 5 Special Benefits for the Owner. 5 How Does A Truss Work? . 6 Typical Framing Systems. 8 Gable Framing Variations . 11 Hip Set Framing Variations . 13 Additional Truss Framing Options Valley Sets . 15 Piggyback Trusses . 17 Typical Truss Configurations . 18 Typical Truss Shapes. 20 Typical Bearing / Heel Conditions Exterior Bearing Conditions. 21 Crushing at the Heel . 22 Trusses Sitting on Concrete Walls . 22 Top Chord Bearing. 23 Mid-Height Bearing . 23 Leg-Thru to the Bearing. 23 Tail Bearing Tray. 24 Interior Bearing Conditions . 24 Typical Heel Conditions. 25 Optional End Cosmetics Level Return. 25 Nailer . 25 Parapet. 26 Mansard . 26 Cantilever. 26 Stub . 26 Bracing Examples . 27 Erection of Trusses . 29 Temporary Bracing . 30 Checklist for Truss Bracing Design Estimates . 32 Floor Systems . 33 Typical Bearing / Heel Conditions for Floor Trusses Top Chord, Bottom Chord, and Mid-Height Bearing. 34 Interior Bearing Conditions . 35 Ribbon Boards, Strongbacks and Fire Cut Ends . 36 Steel Trusses . 37 Ask Charlie V. 38 Charlie’s Advice on Situations to Watch Out for in the Field. 41 Glossary of Terms. 42 Appendix - References. 48 1 Builders, Architects and Home Owners today have many choices about what to use in roof and floor systems Traditional Stick Framing – Carpenters take 2x6, Truss Systems – in two primary forms: 2x8, 2x10 and 2x12 sticks of lumber to the job • Metal Plate Connected Wood Trusses – site. They hand cut and fit this lumber together Engineered trusses are designed and into a roof or floor system. -
1 Classical Architectural Vocabulary
Classical Architectural Vocabulary The five classical orders The five orders pictured to the left follow a specific architectural hierarchy. The ascending orders, pictured left to right, are: Tuscan, Doric, Ionic, Corinthian, and Composite. The Greeks only used the Doric, Ionic, and Corinthian; the Romans added the ‘bookend’ orders of the Tuscan and Composite. In classical architecture the selected architectural order for a building defined not only the columns but also the overall proportions of a building in regards to height. Although most temples used only one order, it was not uncommon in Roman architecture to mix orders on a building. For example, the Colosseum has three stacked orders: Doric on the ground, Ionic on the second level and Corinthian on the upper level. column In classical architecture, a cylindrical support consisting of a base (except in Greek Doric), shaft, and capital. It is a post, pillar or strut that supports a load along its longitudinal axis. The Architecture of A. Palladio in Four Books, Leoni (London) 1742, Book 1, plate 8. Doric order Ionic order Corinthian order The oldest and simplest of the five The classical order originated by the The slenderest and most ornate of the classical orders, developed in Greece in Ionian Greeks, characterized by its capital three Greek orders, characterized by a bell- the 7th century B.C. and later imitated with large volutes (scrolls), a fascinated shaped capital with volutes and two rows by the Romans. The Roman Doric is entablature, continuous frieze, usually of acanthus leaves, and with an elaborate characterized by sturdy proportions, a dentils in the cornice, and by its elegant cornice. -
Design of Reinforced Concrete Bridges
Design of Reinforced Concrete Bridges CIV498H1 S Group Design Project Instructor: Dr. Homayoun Abrishami Team 2: Fei Wei 1000673489 Jonny Yang 1000446715 Yibo Zhang 1000344433 Chiyun Zhong 999439022 Executive Summary The entire project report consists of two parts. The first section, Part A, presents a complete qualitative description of typical prestressed concrete bridge design process. The second part, Part B, provides an actual quantitative detailed design a prestressed concrete bridge with respect to three different design standards. In particular, the first part of the report reviews the failure of four different bridges in the past with additional emphasis on the De La Concorde Overpass in Laval, Quebec. Various types of bridges in terms of materials used, cross-section shape and structural type were investigated with their application as well as the advantages and disadvantages. In addition, the predominant differences of the Canadian Highway and Bridge Design Code CSA S6-14 and CSA S6-66, as well as AASHTO LRFD 2014 were discussed. After that, the actual design process of a prestressed concrete bridge was demonstrated, which started with identifying the required design input. Then, several feasible conceptual design options may be proposed by design teams. Moreover, the purpose and significance of structural analysis is discussed in depth, and five different typical analysis software were introduced in this section. Upon the completion of structural analysis, the procedure of detailed structure design and durability design were identified, which included the choice of materials and dimensions of individual specimens as well as the detailed design of any reinforcement profile. Last but not least, the potential construction issues as well as the plant life management and aging management program were discussed and presented at the end of the Part A. -
Comparative Design of a Balanced Cantilever Bridge in Java and Eurocode
The International Journal of Engineering and Science (IJES) || Volume || 10 || Issue || 3 || Series I || Pages || PP 15-33 || 2021 || ISSN (e): 2319-1813 ISSN (p): 20-24-1805 Comparative Design of a Balanced Cantilever Bridge In Java And Eurocode Umeonyiagu I.E. 1, Onwuka F.E.2, Ogbonna N.P3. 1. Department of Civil Engineering, Chukwuemeka Odumegwu Ojukwu University, Uli, Nigeria. 2. Department of Civil Engineering, Chukwuemeka Odumegwu Ojukwu University, Uli, Nigeria. 3. Federal polytechnic Nekede Owerri, Nigeria. --------------------------------------------------------ABSTRACT---------------------------------------------------------------- This research analyzed, designed and detailed balanced cantilever bridges to Euro codes using manual and computer methods. The design was done considering only the superstructure which forms the dynamic element as a load carrying member. A Java based computer program to analyze, design and detail the balanced cantilever bridge was also written. The Java program focused on the design of prestressing cables for box- girder bridges using balanced cantilever method. The program made use of algorithms and visualization techniques. The segments of the bridge ranged from 15 to 48. The maximum number of cables was 819. Also the maximum number of strands was 9822. The maximum bending moment and shear force were 5790000kNm and 44362.5kN respectively. The manual design were done for 100m, 150m 200m 250m and 300m main spans. These results were then compared to the results gotten from the Java computer program. It could be seen that the results of both analyses and designs obtained using manual procedures and computer program were approximately the same. Furthermore, the percentage difference results showed very little or no differences between the various results obtain from both manual and computer program analyses. -
The Typology of the Historical Timber Bridges of Turkey
Süheyla Yilmaz, Halide Sert. & Nurdan Apaydin, Int. J. of Herit. Archit., Vol. 2, No. 2 (2018) 230–247 THE TYPOLOGY OF THE HISTORICAL TIMBER BRIDGES OF TURKEY SÜHEYLA YILMAZ HALİDE SERT & NURDAN APAYDIN Historical Bridges Division, Department of Structures, General Directorate of Highways, Ankara, Turkey. ABSTRACT Timber was probably the first material used by humans to construct a bridge structure since Neolithic era. The oldest man-made bridges were probably done by laying tree trunks across streams in girder fashion. Later, many timber bridges were built all over the world, using many variants of beams, can- tilevers, trusses and arches. In Turkey, the Hittite Bridge in Ambarlıkaya near Hattuşa, the capital city of the Hittite Empire, today in Çorum Province, is known as the oldest bridge constructed with wooden beams laid across Ambarlıkaya gorge. In Turkey, historical timber bridges belonging to ancient times could not survive till now while only a few belonging to the 19th century are still standing and reflect the materials and construction technologies of the past. Those bridges, therefore, are very valuable and deserve to be discovered in terms of their technical specifications. The present study is an effort to classify the historical timber bridges in Turkey that have survived up until today. To do that, the study has started with literature survey about the historical development and classification of timber bridges throughout the history in the world. By using that knowledge, the historical timber bridges in Turkey were classified in groups depending on their construction technologies. Discovery of the visible and invisible technical features of historical timber bridges has vital importance for transferring that knowl- edge to conservation practitioners for repairs and maintenance of these bridges. -
Basic Aircraft Construction
CHAPTER 4 AIRCRAFT BASIC CONSTRUCTION INTRODUCTION useless. All materials used to construct an aircraft must be reliable. Reliability minimizes the possibility of Naval aircraft are built to meet certain specified dangerous and unexpected failures. requirements. These requirements must be selected so they can be built into one aircraft. It is not possible for Many forces and structural stresses act on an one aircraft to possess all characteristics; just as it isn't aircraft when it is flying and when it is static. When it is possible for an aircraft to have the comfort of a static, the force of gravity produces weight, which is passenger transport and the maneuverability of a supported by the landing gear. The landing gear absorbs fighter. The type and class of the aircraft determine how the forces imposed on the aircraft by takeoffs and strong it must be built. A Navy fighter must be fast, landings. maneuverable, and equipped for attack and defense. To During flight, any maneuver that causes meet these requirements, the aircraft is highly powered acceleration or deceleration increases the forces and and has a very strong structure. stresses on the wings and fuselage. The airframe of a fixed-wing aircraft consists of the Stresses on the wings, fuselage, and landing gear of following five major units: aircraft are tension, compression, shear, bending, and 1. Fuselage torsion. These stresses are absorbed by each component of the wing structure and transmitted to the fuselage 2. Wings structure. The empennage (tail section) absorbs the 3. Stabilizers same stresses and transmits them to the fuselage. -
Cantilever Type Switch Design
IJRET: International Journal of Research in Engineering and Technology eISSN: 2319-1163 | pISSN: 2321-7308 CANTILEVER TYPE SWITCH DESIGN Gajanan D.Patil1, N. R. Kolhare2, Pradip Bhosale3, A.I.Rokade4 1Assistant Professor, Dept. of Electronics and Tele-Communication, PRMIT&R, Amravati (M.S.), India 2Assistant Professor, Dept. of Electronics and Tele-Communication, GECA, Aurangabad (M.S.), India 3Assistant Professor, Dept. of Electronics and Tele-Communication, SGOI COE, BELHE, A.nagar (M.S.), India 4Assistant Professor, Dept. of Electronics and Tele-Communication, PRMIT&R, Amravati (M.S.), India Abstract This paper deals with the RF (Radio Frequency)-MEMS (Micro-Electro-Mechanical-System) switch design using the coventorware software and its superiority over the existing technologies like PIN Diodes and Field-Effect-Transistors regarding size, power, Isolation and Insertion loss, and graphically how Pull-in voltage affects on the deflection of the switch. Also this paper deals with the fabrication process of the cantilever switch. Keywords: Etching, Sacrificial Layer, Actuation Voltage, Electrostatic Force, RF Switch, PIN Diodes, Stiction, Isolation and Insertion loss. --------------------------------------------------------------------***---------------------------------------------------------------------- 1. INTRODUCTION Table -1: Comparison between various RF Switches Switch Isolatio Insertion Power Switchi Linea RF MEMS Switches are used for make and break contact Type n Loss Consu- ng Time rity between the transmission lines, and -
Signature Redacted
Structural Systems and Conceptual Design of Cantilevers by Lingxiao Han B.A. Architecture University of California, Berkeley, 2013 Submitted to the Department of Civil and Environmental Engineering in Partial Fulfillment of the Requirements for the Degree of Master of Engineering in Civil and Environmental Engineering at the MA3SACHU-TS,NSTETE OF TEC'HNOLOGY Massachusetts Institute of Technology IN 2014 June 2014 ©2014 Lingxiao Han. All rights reserved RA R IES The author hereby grants MIT permission to reproduce and to distribute publicly paper and electronic copies of this thesis document in whole or in part in any medium now created. known or herpafter Signature redacted Signature of Author: Department of Civil and Environmental Engineering May 9, 2014 Signature redacted Certified by: Pierre Ghisbain Lecturer of Civil and Environmental Engineering Thesis Supervisor Signature redacted Certified by: Jerome. J. Connor Professor of Civil and Environmental Engineering ThesisfA-SupervisqV Signature redacted Accepted by: If *V Heidi M. Neiff Chair, Departmental Committee for Graduate Students Structural Systems and Conceptual Design of Cantilevers by Lingxiao Han Submitted to the Department of Civil and Environmental Engineering on May 9, 2014 in Partial Fulfillment of the Requirements for the Degree of Master of Engineering in Civil and Environmental Engineering ABSTRACT Cantilevers are a popular way to express form and create unique feature spaces. From a design perspective, cantilevers are amazing feats for the built environment, and structurally, present many opportunities. However, conceptual cantilever design can be a difficult task for Architects and Structural Engineers because there are many structural systems or strategies designers could choose to carry loads to supports.