OVERVIEW of PORT RELATED INDUSTRIES Public Disclosure Authorized
Total Page:16
File Type:pdf, Size:1020Kb
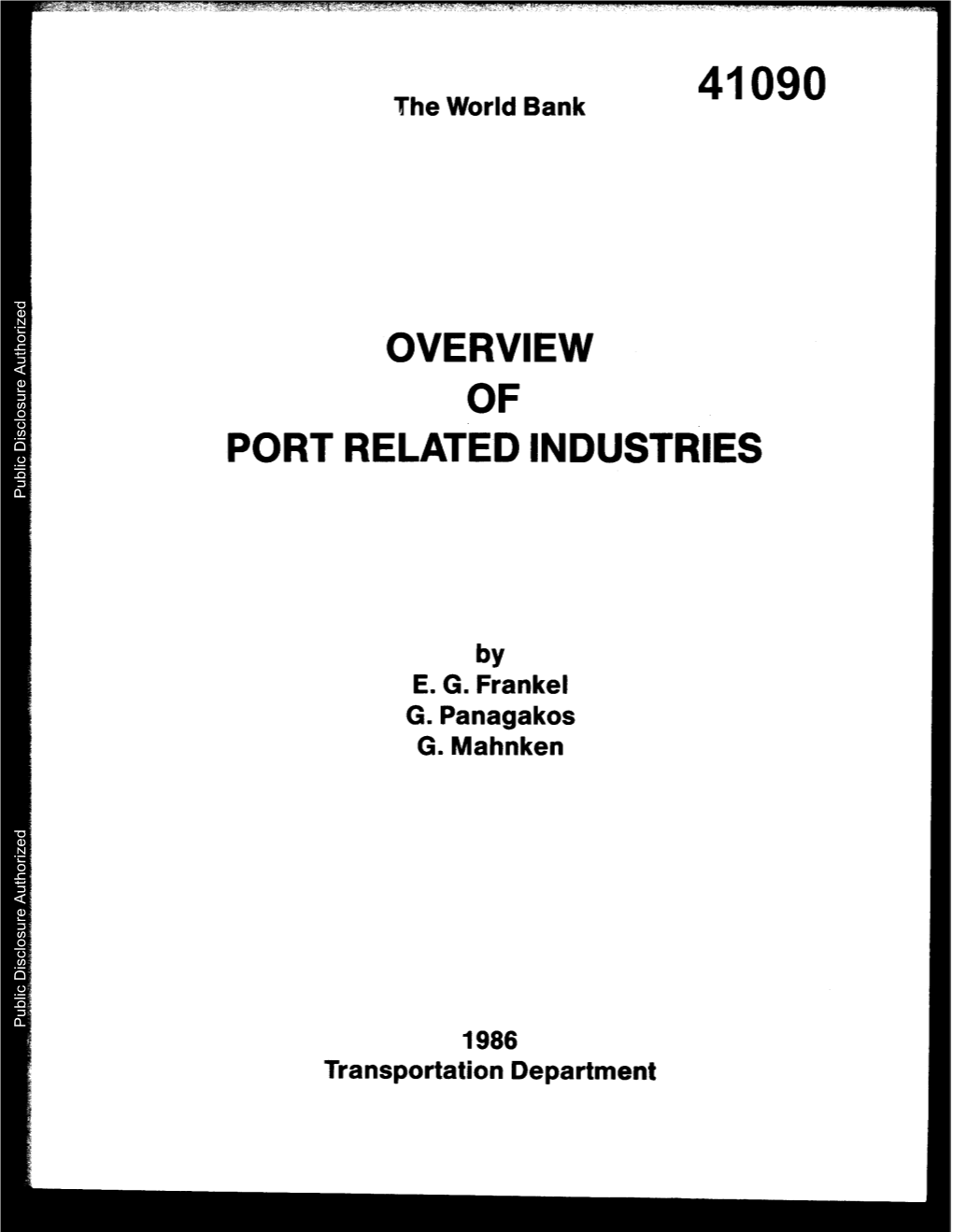
Load more
Recommended publications
-
Arcelormittal Is Again Counting on the Strengths of the AUMUND Drag Chain Conveyor Type LOUISE São Paulo, Brazil, April 2017
Press Information ArcelorMittal is again counting on the strengths of the AUMUND Drag Chain Conveyor Type LOUISE São Paulo, Brazil, April 2017 The steel maker ArcelorMittal is building on proven solutions and reliable partners in Brazil. About 20 years ago, a shock-pressure-proof drag chain conveyor was ordered for Brazil from LOUISE Fördertechnik before this company was acquired by AUMUND Fördertechnik GmbH, and now AUMUND has won an order for another drag chain conveyor type LOUISE TKF. The shock-pressure-proof design of its predecessor was no longer required for the new model because of the change in classification of the plant segment. The dispatch of the machine is planned for June 2017. 1998: AUMUND Drag Chain Conveyor, type LOUISE TKF, in ArcelorMittal’s João Monlevade plant in Brazil (photo AUMUND) The earlier model drag chain conveyor was ordered in 1998 by the then Brazilian arm of the Luxemburg steel company Arbed, CSBM, Companhia Siderurgica Belgo Mineira. Arcelor was created by the merger of Aceralia and Usinor and merged with Mittal in 2006 to become ArcelorMittal, the world’s leading steel concern. Press Information Around fifteen years ago, AUMUND Fördertechnik GmbH integrated the products of the LOUISE subsidiary into its own portfolio. This double strand drag chain conveyor with a capacity of 3 kW, a centre distance of 10.4 m and a performance of 25 t/h, will be used for bunker extraction. The previous machine proved its durability in an interesting way. One of the supports of a weighing cell collapsed and caused one side of the silo to subside. -
The Modern Brazilian Steel Industry
THE MODERN BRAZILIAN STEEL INDUSTRY By Professor Celso Lafer* *Minister of Foreign Relations Notwithstanding the importance of pioneer initiatives by the first generation of Brazilian industrialists, the foundation and growth of the modern steel industry in Brazil was made, in great part, by the state. Steel symbolized industrialization which, for many decades, was synonymous with progress. The government realized, correctly, that having vast reserves of iron ore, Brazil could aspire to a significant steel industry. And it acted on this belief, creating the industry during the Getúlio Vargas administration and promoting its growth during the decades of 1960 and 1970. The predominantly state model that was necessary at the industry’s inception had some success cases. Without the government’s action in the 1930s and 1940s, Brazil would probably not have developed a robust steel-producing base. During the following decades Brazil positioned itself among the main producers and exporters of steel in the world. The state model came to an end, as happened in other sectors, when the government management crisis brought to the surface unsustainable inefficiencies and weaknesses of the productive segment. During the 1990s the steel sector experienced a great transformation. In three years, between 1991 and 1993, all of the state steel industry was privatized through public bidding, and massive investment began to modernize it. In 1998 alone more funds were invested than the sum of monies invested during the 5-year period 1989-1994. In total, between 1994 and 2000, the new steel mill owners invested US$ 10.2 billion in modernization, upgrading, cost reduction and environmental protection works. -
Ironmaking Process Alternatives Screening Study, Volume I
Ironmaking Process Alternatives Screening Study Volume I: Summary Report ORE TO CONCENTRATOR IRON ORE MINE SLURRY ORE BENEFICIATION PIPELINE CONCENTRATOR CONCENTRATE SLURRY ELECTRIC PELLET RECEIVING, PELLET POWER STOCKPILE DEWATERING PLANT (50% FROM COAL, 50% FROM N.G.) DIRECT REDUCTION PLANTS NATURAL GAS EAF MELTING NATURAL GAS DRI PRODUCTION STEEL TO PORT SLABS SLAB LMFs CASTER SLAB VACUUM SHIPPING DEGASSING October 2000 LG Job No. 010529.01 DISCLAIMER This report was prepared as an account of work sponsored by an agency of the United States Government. Neither the United States Government nor any agency thereof, nor any of their employees, makes any warranty, expressed or implied, or assumes any legal liability or responsibility for the accuracy, completeness, or usefulness of any information, apparatus, product, or process disclosed, or represents that its use would not infringe privately owned rights. Reference herein to any specific commercial product, process, or service by trade name, trademark, manufacturer, or otherwise does not necessarily constitute or imply its endorsement, recommendation, or favoring by the United States Government or any agency thereof. The views and opinions of authors expressed herein do not necessarily state or reflect those of the United States Government or any agency thereof. Contents Volume I: Ironmaking Alternative Study Executive Summary...............................................................................1 Study Scope and Methodology............................................................2 -
“Social Aspects and Financing of Industrial Restructuring”
INTERNATIONAL LABOUR ORGANIZATION UNITED NATIONS ECONOMIC COMMISSION FOR EUROPE REGIONAL FORUM “Social Aspects and Financing of Industrial Restructuring” 26 and 27 November 2003, Moscow, Russian Federation Topic 2. Social costs of restructuring and their financing: a closer view Restructuring in the Industry of Luxembourg. Major Issues, Actors and Lessons to Learn By Mr. Albert ZENNER – Director Human Resources, Arbed – Arcelor Group Luxembourg (This paper is being circulated by the secretariat as received from the author) UNITED NATIONS Page 1 sur 13 Restructuring in the Industry of Luxembourg Major issues, Actors and Lessons to learn By Albert ZENNER, Director Human Resources, Arbed – Arcelor Group. Luxembourg might be known by many of You as a banking centre or a country hosting European institutions, and some of You will even know that it is the Headquarters of ARCELOR, the world’s largest steel producer, created by the merger of three companies: the French USINOR, the Spanish ACERALIA, and ARBED, the steel company of LUXEMBOURG. All this is true, but LUXEMBOURG is also an independent country, which has undergone deep changes during the last three decades. These changes result from the restructuring of the steel industry, which for more than a century has been the pillar of the Luxembourg economy. During my presentation I will speak about the major issues of this restructuring, the key players, and the lessons to learn from our point of view. I will also try to show how some of the lessons are applied now within the new group ARCELOR. GEOGRAPHICAL LOCATION AND POPULATION. For locating Luxembourg geographically we have to zoom the map of Western Europe. -
Studies in Global Social History
Fabricating Modern Societies <UN> Studies in Global Social History Series Editor Marcel van der Linden (International Institute of Social History, Amsterdam, The Netherlands) Editorial Board Sven Beckert (Harvard University, Cambridge, MA, usa) Dirk Hoerder (University of Arizona, Phoenix, AZ, usa) Chitra Joshi (Indraprastha College, Delhi University, India) Amarjit Kaur (University of New England, Armidale, Australia) Barbara Weinstein (New York University, New York, NY, usa) volume 37 The titles published in this series are listed at brill.com/sgsh <UN> Fabricating Modern Societies Education, Bodies, and Minds in the Age of Steel Edited by Karin Priem and Frederik Herman leiden | boston <UN> This is an open access title distributed under the terms of the CC-BY-NC 4.0 License, which permits any non-commercial use, distribution, and reproduction in any medium, provided the original author(s) and source are credited. Cover illustration: Apprentices with a telescope at the seaside in Belgium. Undated. Digital positive from glass plate negative. © Institut Emile Metz. cna Collection (HISACS000048V01). The Library of Congress Cataloging-in-Publication Data is available online at http://catalog.loc.gov lc record available at http://lccn.loc.gov/2019023135 Typeface for the Latin, Greek, and Cyrillic scripts: “Brill”. See and download: brill.com/brill-typeface. issn 1874-6705 isbn 978-90-04-34423-5 (hardback) isbn 978-90-04-41051-0 (e-book) Copyright 2019 by the Authors. Published by Koninklijke Brill NV, Leiden, The Netherlands. Koninklijke Brill NV incorporates the imprints Brill, Brill Hes & De Graaf, Brill Nijhoff, Brill Rodopi, Brill Sense, Hotei Publishing, mentis Verlag, Verlag Ferdinand Schöningh and Wilhelm Fink Verlag. -
BAT Guide for Electric Arc Furnace Iron & Steel Installations
Eşleştirme Projesi TR 08 IB EN 03 IPPC – Entegre Kirlilik Önleme ve Kontrol T.C. Çevre ve Şehircilik Bakanlığı BAT Guide for electric arc furnace iron & steel installations Project TR-2008-IB-EN-03 Mission no: 2.1.4.c.3 Prepared by: Jesús Ángel Ocio Hipólito Bilbao José Luis Gayo Nikolás García Cesar Seoánez Iron & Steel Producers Association Serhat Karadayı (Asil Çelik Sanayi ve Ticaret A.Ş.) Muzaffer Demir Mehmet Yayla Yavuz Yücekutlu Dinçer Karadavut Betül Keskin Çatal Zerrin Leblebici Ece Tok Şaziye Savaş Özlem Gülay Önder Gürpınar October 2012 1 Eşleştirme Projesi TR 08 IB EN 03 IPPC – Entegre Kirlilik Önleme ve Kontrol T.C. Çevre ve Şehircilik Bakanlığı Contents 0 FOREWORD ............................................................................................................................ 12 1 INTRODUCTION. ..................................................................................................................... 14 1.1 IMPLEMENTATION OF THE DIRECTIVE ON INDUSTRIAL EMISSIONS IN THE SECTOR OF STEEL PRODUCTION IN ELECTRIC ARC FURNACE ................................................................................. 14 1.2 OVERVIEW OF THE SITUATION OF THE SECTOR IN TURKEY ...................................................... 14 1.2.1 Current Situation ............................................................................................................ 14 1.2.2 Iron and Steel Production Processes............................................................................... 17 1.2.3 The Role Of Steel Sector in -
Trend of Ironmaking Technology in Japan After 2000
NIPPON STEEL TECHNICAL REPORT No. 123 MARCH 2020 Technical Review UDC 669 . 162 : 622 . 785 /. 788 Trend of Ironmaking Technology in Japan after 2000 Seiji NOMURA* Abstract The first two decades of the 21st century were turbulent for the steel industry. The reor- ganization of the steel industry across borders has progressed and the increased demand for steel products has caused a rise in the price of raw materials such as iron ore and metal- lurgical coal. Furthermore, more emphasis has been placed on global environmental pro- tection and carbon dioxide emission control than ever before. The ironmaking technology division in Japan has struggled to cope with these changes both at home and abroad. This report describes the trend of the development and commercial application of the ironmaking technology of Japan in the first two decades of the 21st century. 1. Introduction—Situation of Japan’s Ironmaking ply of high-quality iron ore and coking coal was suddenly consid- after 2000 ered as a bottleneck, and their market prices became highly volatile Soon after the rapid valuation of the Japanese yen brought about over the last few years depending on the supply-demand balance by the Plaza Accord in 1985, the blast furnace operators of Japan (see Fig. 1). 1) took business streamlining measures and eliminated their blast fur- In contrast, the production amounts of pig iron and crude steel of naces one after another. Then in the 1990s, the Japanese steel indus- Japan have remained substantially unchanged over the last 20 years try was forced into tough times facing sluggish demand resulting except for a temporary and significant slump in the aftermath of from the breakdown of the bubble economy and further valuation of Lehman’s fall, and owing to stagnant domestic steel consumption, the currency. -
City Promenade
CITY PROMENADE LUXEMBOURG-CENTRE, OLD TOWN, FORTRESS WALLS AND BEST VIEWS 19 HISTORIC SURVEY In 963, the Count Siegfried of the Ardennes built his forti- fied castle on the Bock promontory, and it became the cradle of the city of Luxembourg. The first markets were held in front of Saint Michael’s Church, surrounded by a simple fortification. Across the centuries, a second and then a third wall were erected on the Western side, while the rocks of the Alzette and Pétrusse valleys served as a natural defence. Never- theless, these strong fortified structures did not prevent Burgundians from taking over the city in 1443, a city which beyond any doubt was to own a major strategic position on the European chessboard. For over four centuries, the best military engineers from Burgundy, Spain, France, Austria and the German Con- federation ended up turning it into one of the most forti- fied places on earth, the so-called “Gibraltar of the North”. The strength of its defence stemmed from its three forti- fied belts, the first of which was composed of bastions, the second of 15 forts and the third, being the outside wall, was composed of 9 forts, all of which were carved into the rock. An extraordinary 14.2 mile-network of underground galleries – the famous Casemates – and more than 1 2 3 4 5 7 40,000 square meters of bomb-shelters were lodged in the city’s rocks. They could shelter not only thousands of defenders, including their horses and equipment, but also artillery and weapon workshops, kitchens, bakeries, slaughterhouses, and so forth. -
Annual Report 2019 Contains a Full Overview of Its Corporate Stakeholder Expectations As Well As Long-Term Trends Governance Practices
Table of Contents Management report Company overview 4 Business overview 5 Disclosures about market risk 44 Group organizational structure 47 Key transactions and events in 2019 50 Recent developments 53 Research and development 54 Sustainable development 57 Corporate governance 67 Luxembourg takeover law disclosure 108 Additional information 110 Chief executive officer and chief financial officer’s responsibility statement 115 Financial statements of ArcelorMittal parent company for the year ended December 31, 2019 116 Statements of financial position 117 Statements of operations and statements of other comprehensive income 118 Statements of changes in equity 119 Statements of cash flows 120 Notes to the financial statements 121 Report of the réviseur d’entreprises agréé 170 4 Management report Company overview other countries, such as Kazakhstan, South Africa and Ukraine. In addition, ArcelorMittal’s sales of steel products History and development of the Company are spread over both developed and developing markets, which have different consumption characteristics. ArcelorMittal is the world’s leading integrated steel and ArcelorMittal’s mining operations, present in North and mining company. It results from the merger in 2007 of its South America, Africa, Europe and the CIS region, are predecessor companies Mittal Steel Company N.V. and integrated with its global steel-making facilities and are Arcelor, each of which had grown through acquisitions over important producers of iron ore and coal in their own right. many years. Since its creation ArcelorMittal has experienced periods of external growth as well consolidation Products: ArcelorMittal produces a broad range of high- and deleveraging (including through divestments), the latter quality finished and semi-finished steel products (“semis”). -
2020-Arcelormittal-Annual-Report.Pdf
Table of Contents Page Page Share capital 183 Management report Additional information Introduction Memorandum and Articles of Association 183 Company overview 3 Material contracts 192 History and development of the Company 3 Exchange controls and other limitations affecting 194 security holders Forward-looking statements 9 Taxation 195 Key transactions and events in 2020 10 Evaluation of disclosure controls and procedures 199 Risk Factors 14 Glossary - definitions, terminology and principal 201 subsidiaries Business overview Chief executive officer and chief financial officer’s 203 Business strategy 35 responsibility statement Research and development 36 Sustainable development 40 Consolidated financial statements 204 Products 54 Consolidated statements of operations 205 Sales and marketing 58 Consolidated statements of other comprehensive 206 Insurance 59 income Intellectual property 59 Consolidated statements of financial position 207 Government regulations 60 Consolidated statements of changes in equity 208 Organizational structure 67 Consolidated statements of cash flows 209 Notes to the consolidated financial statements 210 Properties and capital expenditures Property, plant and equipment 69 Report of the réviseur d’entreprises agréé - 322 consolidated financial statements Capital expenditures 91 Reserves and Resources (iron ore and coal) 93 Operating and financial review Economic conditions 99 Operating results 120 Liquidity and capital resources 132 Disclosures about market risk 137 Contractual obligations 139 Outlook 140 Management and employees Directors and senior management 141 Compensation 148 Corporate governance 164 Employees 173 Shareholders and markets Major shareholders 178 Related party transactions 180 Markets 181 New York Registry Shares 181 Purchases of equity securities by the issuer and 182 affiliated purchasers 3 Management report Introduction Company overview ArcelorMittal is one of the world’s leading integrated steel and mining companies. -
Economic and Social Portrait of Luxembourg NOTES
Economic and social portrait of Luxembourg NOTES 1. This publication is being released at a time 2. In this “economic and social” portrait, par- when great uncertainty regarding the global ticular emphasis has been placed on compara- situation is weighing heavily on Luxembourg’s tive aspects, which should make it possible to economic prospects. There has been a marked position Luxembourg’s economic development change in climate in Luxembourg. GDP growth in relation to other European countries. As (in volume) fell from 8.9 % in 2000 to 1 % in there is often a two-to-three year delay in pub- 2001. At the time of publication, STATEC fore- lication of the comparative and harmonised casts are banking on GDP growth of 0.5 % for statistics by EUROSTAT and the OECD, many 2002 and 2 % for 2003. In this document, it has comparative tables and charts relate to the not been possible to carry out a detailed analy- year 2000, and in some cases 1999. As regards sis of the impact of this current decline on the comparative statistics, the document Luxembourg’s economy, especially as the sta- deliberately confines itself to structural social tistical data for 2002 is still incomplete. In fact, and economic indicators relating to 2001 is the most recent year included in most Luxembourg’s economy and society which are of the charts and tables. The publication deals unlikely to be deeply affected by short-term mainly with the development of economic changes. structures since 1985. Recent economic events are referred to only where they represent changes likely to affect future developments. -
Restructuring of the Steel Industry in Eight Countries
Upjohn Press Upjohn Research home page 1-1-1992 Banking the Furnace: Restructuring of the Steel Industry in Eight Countries Trevor Bain University of Alabama Follow this and additional works at: https://research.upjohn.org/up_press Part of the Industrial Organization Commons Citation Bain, Trevor. 1992. Banking the Furnace: Restructuring of the Steel Industry in Eight Countries. Kalamazoo, MI: W.E. Upjohn Institute for Employment Research. https://doi.org/10.17848/ 9780880995399 This work is licensed under a Creative Commons Attribution-Noncommercial-Share Alike 4.0 License. This title is brought to you by the Upjohn Institute. For more information, please contact [email protected]. Restructuring of the Steel Industry in Eight Countries Trevor Bain University of Alabama 1992 W.E. UPJOHN INSTITUTE for Employment Research Kalamazoo, Michigan Library of Congress Cataloging-in-Publication Data Bain, Trevor. Banking the furnace : restructuring of the steel industry in eight countries / Trevor Bain. p. cm. Includes bibliographical references and index. ISBN 0-88099-128-3. ISBN 0-88099-127-5 (pbk.) 1. Steel industry and trade. 2. Collective bargaining Steel industry and trade. 3. Corporate reorganizations. I. Title. HD9510.5.B25 1992 338.4*7669142 dc20 92-18358 CIP Copyright 1992 W.E. Upjohn Institute for Employment Research 300 S. Westnedge Avenue Kalamazoo, Michigan 49007 THE INSTITUTE, a nonprofit research organization, was established on July 1, 1945. It is an activity of the W.E. Upjohn Unemployment Trustee Corporation, which was formed in 1932 to administer a fund set aside by the late Dr. W.E. Upjohn for the pur pose of carrying on "research into the causes and effects of unemployment and mea sures for the alleviation of unemployment." The facts presented in this study and the observations and viewpoints expressed are the sole responsibility of the author.