Nonlinear Dynamic Modeling of Double Helical Gear System
Total Page:16
File Type:pdf, Size:1020Kb
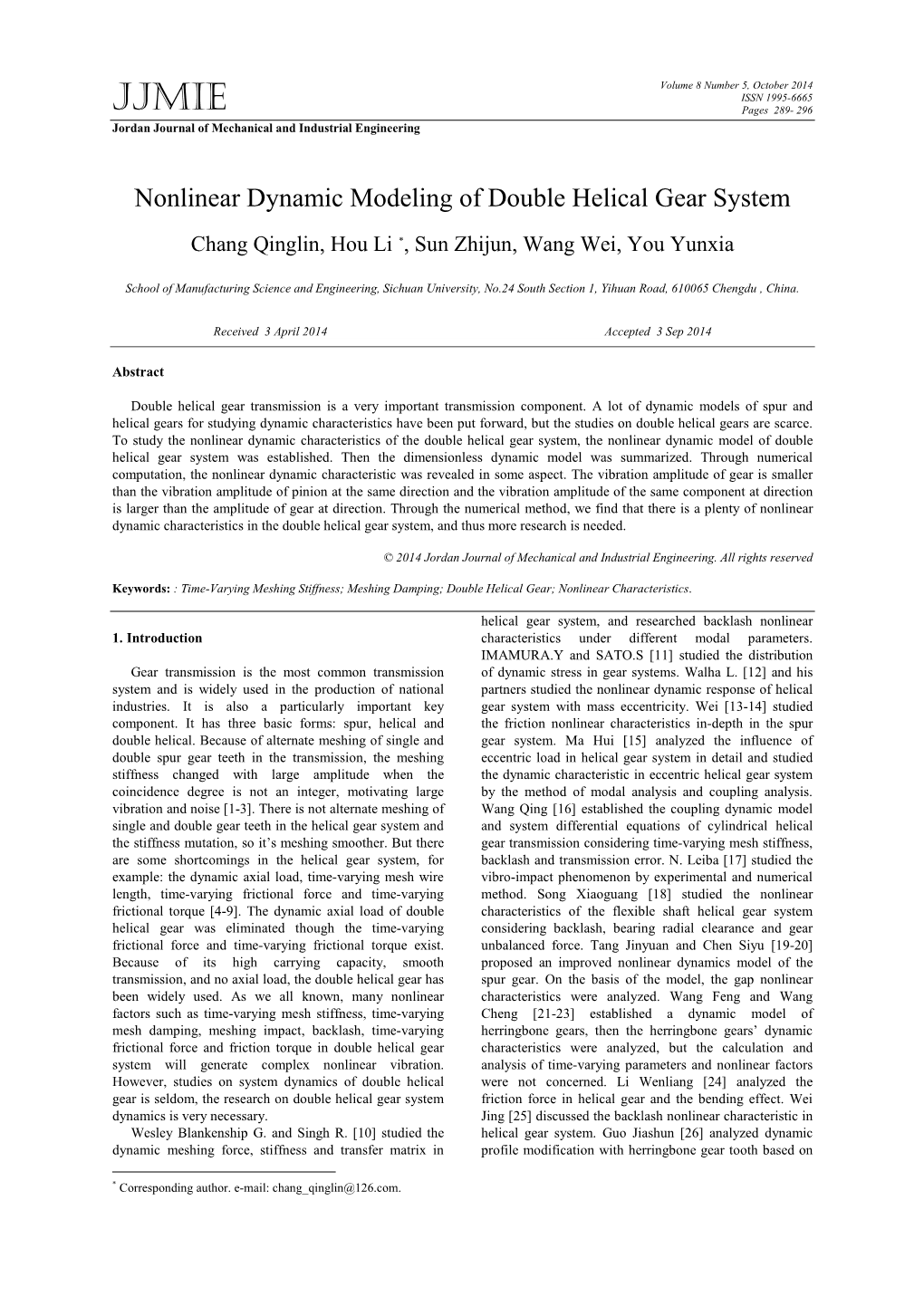
Load more
Recommended publications
-
Contact Mechanics in Gears a Computer-Aided Approach for Analyzing Contacts in Spur and Helical Gears Master’S Thesis in Product Development
Two Contact Mechanics in Gears A Computer-Aided Approach for Analyzing Contacts in Spur and Helical Gears Master’s Thesis in Product Development MARCUS SLOGÉN Department of Product and Production Development Division of Product Development CHALMERS UNIVERSITY OF TECHNOLOGY Gothenburg, Sweden, 2013 MASTER’S THESIS IN PRODUCT DEVELOPMENT Contact Mechanics in Gears A Computer-Aided Approach for Analyzing Contacts in Spur and Helical Gears Marcus Slogén Department of Product and Production Development Division of Product Development CHALMERS UNIVERSITY OF TECHNOLOGY Göteborg, Sweden 2013 Contact Mechanics in Gear A Computer-Aided Approach for Analyzing Contacts in Spur and Helical Gears MARCUS SLOGÉN © MARCUS SLOGÉN 2013 Department of Product and Production Development Division of Product Development Chalmers University of Technology SE-412 96 Göteborg Sweden Telephone: + 46 (0)31-772 1000 Cover: The picture on the cover page shows the contact stress distribution over a crowned spur gear tooth. Department of Product and Production Development Göteborg, Sweden 2013 Contact Mechanics in Gears A Computer-Aided Approach for Analyzing Contacts in Spur and Helical Gears Master’s Thesis in Product Development MARCUS SLOGÉN Department of Product and Production Development Division of Product Development Chalmers University of Technology ABSTRACT Computer Aided Engineering, CAE, is becoming more and more vital in today's product development. By using reliable and efficient computer based tools it is possible to replace initial physical testing. This will result in cost savings, but it will also reduce the development time and material waste, since the demand of physical prototypes decreases. This thesis shows how a computer program for analyzing contact mechanics in spur and helical gears has been developed at the request of Vicura AB. -
Gear Resonance Analysis
GEAR SOLUTIONS GEAR MAGAZINE GEAR RESONANCE ANALYSIS Using Rapid Prototyped Gears Upgrading and Testing a 72,000 HP GEARBOX INNOVATION IN Spline Rolling Rack Tooling UNIMILL: Prototype and Bevel Gear IMTS 2014 IMTS Manufacturing SEPTEMBER 2014 SEPTEMBER Your Resource for Machines, Services, and Tooling for the Gear Industry SEPTEMBER 2014 gearsolutions.com Indiana Technology & Manufacturing Companies, Inc. (ITAMCO), left to right: Nobel Neidig - President Joel D. Neidig - Technology Manager Gary Neidig - Vice President Growth Fund. Invest in your future. Kapp Niles machines provide increased productivity to grow your business. Our machines are built for the long haul, so you can pass them down from generation to generation – with 97% of our finishing machines still in operation since 1984. Plus, our quality service and retrofitting capabilities allow you to stay current with changing technologies. Invest in Kapp-Niles and invest in the future of your business. ZPI/E: Profile grinding of internal gears with large modules. Switches from internal to exter- nal grinding by swiveling the grinding arm 1800. Wheels are dressed while in grinding position. Precise, efficient, flexible. Booth #N-7036 See us on the web! kapp-usa.com 2870 Wilderness Place | Boulder, CO 80301 p: 303.447.1130 | f: 303.447.1131 | [email protected] The most interesting man in the gear world He once climbed the Matterhorn and attended a machine run off, in Germany, on the same afternoon He has been known to hand carry parts to his secret manufacturing plant, in an unknown location But, when it comes to workholding, He always prefers König Stay productive, my friends 1921 Miller Drive Longmont, CO 80501 303-776-6212 www.toolink-eng.com OUR LINE JUST GOT LONGER.. -
JOURNAL of MECHANICAL and CIVIL ENGINEERING Shivam Bansal Mechanical Department Dronacharya College of Engineering Khentawa
- - IJRDO - Journal of Computer Science and Engineering ISSN: 2456-1843 JOURNAL OF MECHANICAL AND CIVIL ENGINEERING GEARS Shivam Bansal Mechanical Department Dronacharya College of Engineering Khentawas, Farukhnagar,Gurgaon [email protected] Yogesh Vashiath Mechanical Department Dronacharya College of Engineering Khentawas, Farukhnagar,Gurgaon [email protected] Ujjwal Batra Mechanical Department Dronacharya College of Engineering Khentawas, Farukhnagar,Gurgaon [email protected] INTRODUCTION A gear or cogwheel is a rotating machine part having cut teeth, or cogs, which mesh with another toothed part in order to transmit torque, in most cases with teeth on the one gear being of identical shape, and often also with that shape on the other gear. Two or more gears working in tandem are called a transmission and can produce a mechanical advantage through a gear ratio and thus may be considered a simple machine. Geared devices can change the speed, torque, and direction of a power source. The most common situation is for a gear to mesh with another gear; however, a gear can also mesh with a non-rotating toothed part, called a rack, thereby producing translation instead of rotation. The gears in a transmission are analogous to the wheels in a crossed belt pulley system. An advantage of gears is that the teeth of a gear prevent slippage. When two gears mesh, and one gear is bigger than the other (even though the size of the teeth must match), a mechanical advantage is produced, with the rotational speeds and the torques of the two gears differing in an inverse relationship. In transmissions which offer multiple gear ratios, such as bicycles, motorcycles, and cars, the term gear, as in first gear, refers to a gear ratio rather than an actual physical gear. -
Chapter 8 Gears
Gears CHAPTER 8 Chapter 8 Gears Chapter Objectives When you have finished Chapter 8, “Gears,” you should be able to do the following: 1. Understand the purpose of gears and drives. 2. Identify five gear design categories and their orientation types. 3. Describe and compare various gear types, including: spur helical, herringbone, straight bevel, spiral bevel, cylindrical worm, double-enveloping worm, cycloidial, and hypoid. 4. Define the most common gear terms. 5. Explain the application requirements when selecting gears. 6. List the important specifications needed when ordering gears. 7. List five causes for gear tooth failure. 8. Name the associations that standardize gear classification. 9. Describe and compare the basic types of enclosed gear drives. 10. Explain the function and importance of seals and breathers for enclosed gears. 11. Describe the purpose and the lubrication essential for gear life. 12. Explain gear rating standards. 13. Explain the major factors for selecting and installing gear drives. Power Transmission Handbook 8-155 – Gears Introduction Open Gears A gear is a rotating machine part having cut teeth, or cogs, Gears are grouped into five design categories: spur, helical, which mesh with another toothed part in order to transmit bevel, hypoid, and worm. They are also classified according torque. Two or more gears working in tandem are called to the orientation of the shafts on which they are mounted, a transmission and can produce a mechanical advantage either in parallel or at an angle. Generally, the shaft orien- through a gear ratio and thus may be considered a simple tation, efficiency, and speed determine which type should machine. -
General Applications of Gears
UNIT - III GEAR MANUFACTURING PROCESS SPRX1008 – PRODUCTION TECHNOLOGY - II Gears are widely used in various mechanisms and devices to transmit power and motion positively (without slip) between parallel, intersecting (axis) and non-intersecting non parallel shafts, •without change in the direction of rotation •with change in the direction of rotation •without change of speed (of rotation) •with change in speed at any desired ratio Often some gearing system (rack – and – pinion) is also used to transform Rotary motion into linear motion and vice-versa. Fig.1 Features of Spur Gear Gears are basically wheels having, on its periphery, equispaced teeth which are so designed that those wheels transmit, without slip, rotary motion smoothly and uniformly with minimum friction and wear at the mating tooth – profiles. To achieve those favorable conditions, most of the gears have their tooth form based on in volute curve, which can simply be defined as Locus of a point on a straight line which is rolled on the periphery of a circle or Locus of the end point of a stretched string while its unwinding over a cylinder as indicated in Fig. General Applications of Gears Gears of various type, size and material are widely used in several machines and systems requiring positive and stepped drive. The major applications are: • Speed gear box, feed gear box and some other kinematic units of machine tools • Speed drives in textile, jute and similar machineries • Gear boxes of automobiles • Speed and / or feed drives of several metal forming machines • Machineries for mining, tea processing etc. • Large and heavy duty gear boxes used in cement industries, sugar industries, cranes, conveyors etc. -
Herringbone Gears1
HERRINGBONE GEARS1 The Design and Construction of Double Helical Gears on the Wuest System BY PERCY C. DAY That the helical principle in toothed the load is carried near the point of the gear gearing is ideal from a theoretical point of tooth, that tooth is subjected to a maximum view is well known. From a practical stand bending stress along its whole length. Dur point herringbone gears have been less sat ing the first phase, the portion of the pin isfactory than straight-cut spur gears be ion tooth near the root is sensibly sliding cause, until recently, no method was devised over the outer portion of the gear tooth ; for producing them with the requisite speed that is to say, two metallic surfaces of small and accuracy. Within the last six years a area are sliding under heavy compression. method has been found and developed, in The action during the second phase more England, to a high degree of perfection. nearly approaches ideal conditions. The teeth Herringbone gears made by this method are are engaged near their respective pitch lines called Wuest gears, after the name of the in and very little sliding takes place. ventor, and can be produced with even great During the third and final phase, the pin er accuracy than cut gears of the spur type. ion tooth is subjected to a maximum bend The distinction between these gears and ing stress, while the tooth surfaces again those of the ordinary herringbone type is slide over each other, this time with the outer that the teeth of the former, instead of join portion of the pinion tooth engaging the ing at a common apex at the center of the gear tooth near its root. -
Transmission of SAE Baja
IJIRST –International Journal for Innovative Research in Science & Technology| Volume 4 | Issue 5 | October 2017 ISSN (online): 2349-6010 Transmission of SAE Baja Naveen Kumar Nikhil Verma UG Student UG Student Department of Mechanical Engineering Department of Mechanical Engineering Chandigarh University Gharuan, Punjab Chandigarh University Gharuan, Punjab Abstract The automatic transmission is a unit which supplies the power from the Engine to the wheels .There are some types of gear transmission system which help to improve the economy and efficiency of the work transfer .Besides the traditional automatic transmission, there are also other types such as continuously variable transmission (CVT),dual clutch transmission (DCT) and automated manual transmission system .Gear shifting strategy is the core of intelligent control of any automatic transmission used in modern vehicles. It directly effects the vehicle performance, drivers comfort and fuel economy .The comparison between all types of transmission system, the gear shifting strategy in transmission systems and power transmitting drives are explained. Keywords: Clutch, Sequential Gearbox, CVT, Differential & Its Types, Power Transmitting Drives, CV Shafts _______________________________________________________________________________________________________ I. INTRODUCTION Transmission System is the next and final stage of the engine generated power before it hits the wheels. The whole system is responsible to connect engine and wheels, driving and alter the output shaft rotation to a desired speed/torque ratio, allowing a wide range of speed and better performance as the engine has its own RPM limit and maximum torque. Transmission system consists of following major parts. Clutch (Dry/Wet). Gearbox/ CVT. Differential (Open, Torsen). Power transmitting drives (Chain, Belts, Cv shafts). Each part has a specific role in transmitting power from the engine to the wheels ensuring correct rpm and torque. -
980 a Textbook of Machine Design
980 A Textbook of Machine Design ZN 3 K = p ∴ Bearing modulus at the minimum point of friction, 1.⎛⎞ZN =× 1 = K = ⎜⎟ 28 9.33 33⎝⎠p ⎛⎞ZN. = Since the calculated value of bearing characteristic number ⎜⎟12.24 is more than 9.33, ⎝⎠p therefore the bearing will operate under hydrodynamic conditions. 4. From Table 26.3, we find that for centrifugal pumps, the clearance ratio (c/d) = 0.0013 5. We know that coefficient of friction, 33⎛⎞⎛⎞ZN d += 33 × × 1 + μ = ⎜⎟⎜⎟ k 12.24 0.002 1088⎝⎠pc⎝⎠ 10 0.0013 = 0.0031 + 0.002 = 0.0051 ... [From Art. 26.13, k = 0.002] 6. Heat generated, ⎛⎞πdN. ⎛⎞πdN. Q = μ=μWV W⎜⎟W ...⎜⎟QV = g ⎝⎠60 ⎝⎠60 ⎛⎞π×0.1 × 900 = 0.0051×= 20000⎜⎟ 480.7 W ⎝⎠60 ... (d is taken in metres) 7. Heat dissipated, Qd = C.A (tb – ta) = C.l.d (tb – ta) W ... ( QA = l × d) We know that 1 1 (tb – ta)= 2 (t0 – ta) = 2 (55°– 15.5°) = 19.75°C ∴ Qd = 1232 × 0.16 × 0.1 × 19.75 = 389.3 W ... (l and d are taken in metres) We see that the heat generated is greater than the heat dissipated which indicates that the bear- ing is warming up. Therefore, either the bearing should be redesigned by taking t0 = 63°C or the bearing should be cooled artificially. We know that the amount of artificial cooling required = Heat generated – Heat dissipated = Qg – Qd = 480.7 – 389.3 = 91.4 W Mass of lubricating oil required for artificial cooling Let m = Mass of the lubricating oil required for artificial cooling in kg / s. -
GEAR DRIVES for TURBOMACHINERY by Peter Lynwander
GEAR DRIVES FOR TURBOMACHINERY by Peter Lynwander INTRODUCTION driven machinery: Gearboxes for turbomachinery applications are Horsepower transmitted designed to achieve years of trouble-free oper- Ratio required (reduction or increasing) ation. As operating speeds increase, and relia- Speeds bility requirements become critical due to the Arrangement of Shafting (Fig. 1) high cost of downtime, gear manufacturers are When specifying a gear drive, the efficiency refining their analytical, design and manufac- requirement, noise generation, and space and turing techniques to keep pace with new tech- weight limitation must also be considered. The nology. It has become apparent that gear units, physical environment, dust, humidity, corrosive when incorporated into a system of rotating atmosphere, etc. must be addressed in the machinery, become susceptible to a variety of design stage. problems. The gear manufacturer and the user, Although the input and output shaft arrange- therefore, must take a systems approach to the ment can be concentric, parallel offset, right specification, installation, operation and mainte- nance of a gearbox. All characteristics of the drive system from the driver to the driven equip- Input Input ment including the lubrication system and acces- sories can influence gearbox operation. This chapter presents material concerning all phases of gearbox application with emphasis on information that will help the user operate and maintain the equipment. A discussion of selection and design procedures is included to familiarize Parallel Concentric the reader with gearbox principles. Offset Throughout the chapter standards and prac- tices developed by the American Gear Manufac- turers Association are referred to. Successful Input selection, rating, installation and maintenance of gearboxes can be accomplished by the use of AGMA standards and practices. -
Transmission Error in Spur Gears: Static and Dynamic
Transmission Error in Spur Gears: Static and Dynamic Finite-Element Modeling and Design Optimization By Raul Tharmakulasingam BEng. MSc. (Eng) Submitted in accordance with the requirements for the degree of Doctor of Philosophy School of Engineering and Design Brunel University United Kingdom October 2009 ACKNOWLEDGEMENTS “Success is sweet: the sweeter if long delayed and attained through manifold struggles and defeats.” I would like to take this opportunity to thank everyone who has helped me in my pursuit of success in my PhD. Firstly; I would like to thank my supervisor Dr. Giulio Alfano for helping me shape my research and motivating me at the right times with a timely reminder of how much we have achieved. I would also like to Dr Mark Atherton for bringing a fresh perspective to everything we did during the research, and always providing a kind ear and an objective view to all our problems. I am also very grateful to Prof. Luiz Wrobel for providing me with the opportunity to undertake my PhD research, and also helping me with my numerous problems while carrying out my research. To the colleagues who helped me with moments of respite during a hard day’s work, inspiration by example, and lasting friendships, I thank you from the bottom of my heart and look forward to keeping in touch. My family who have endured my worst and celebrated my best of times during my PhD also receive a heartfelt embrace and acknowledgement for everything they have done for me. My dear friends who constantly reminded me of my duty to hand in my Thesis by the incessant question “Have you submitted yet?”. -
Design, Modelling and Analysis of Herringbone Gear Using Ansys D.Ramakrishna [1], Ch.V.S.Paramaeswararao [2], S
International Journal of Engineering Trends and Applications (IJETA) – Volume 3 Issue 4, Jul-Aug 2016 RESEARCH ARTICLE OPEN ACCESS Design, Modelling and Analysis of Herringbone Gear Using Ansys D.Ramakrishna [1], Ch.V.S.ParamaeswaraRao [2], S. Siva Naga MalleswarRao [3] M.Tech Research Scholar [1], Professor [2] & [3] Department of Mechanical Engineering PBR VITS, Kavali-524201 India ABSTRACT Herringbone gears, also called as double helical gears are the gear sets designed to transmit power through either parallel or less commonly perpendicular axes. The unique tooth structure of a herringbone gear consists of two adjoining opposite helixes that appear in the shape of the letter 'V'. Herringbone gears usually mate via the use of smooth, precisely manufactured V-shaped teeth. Like helical gears multiple teeth are engaged during rotation, distributing the work load and offering a quiet operation. However, due to their tooth structure, herringbone gears nullify the axial thrust unlike helical gears. The gear set's teeth may be manufactured so that tooth-tip aligns with the opposite tooth-tip or the opposite gear's tooth trough. In this project, herringbone gears that are used in a rolling mill gear box is designed using a 3D modelling software called Solid works. Static, Modal and Fatigue Analysis has been carried out on herringbone gears using ANSYS tool. Alloy Steel, GRP and Carbon fiber materials have been analysed and studied for comparison. The selection of better material for herringbone gear is determined out of this analysis. This Paper is the result of the analysis carried out by using ANSYS 14.5 on a 3D model of Herringbone gear which was generated using Solid works tool. -
V19 GE-1018 Lynwander Gear Drive Systems (Excerpts).Pdf
GE-1018.001 GE-1018.002 MAI TJ184/.L993/’1983 Gear drive systems ’ design and application / Peter Lynwander, ~ DCO cyxe c. GE-1018.003 APR ~ 7 ?0~5 GE-1018.004 GEAR DRIVE SYSTEMS DESIGN AND APPLICATION GE-1018.005 MECHANICAL ENGINEERING A Series of Textbooks and Reference Books EDITORS L. L. FAULKNER S. B. MENKES Departmen t of Mechanical Engineering Departmen t of Mechanical Engineering The Ohio State University The City College of the Columbus, Ohio City.University of New York .New York, .New York 1. Spring Designer’s Handbook, by Harold Carlson 2. Computer-Aided Graphics and Design, by Daniel L. Ryan 3. Lubrication Fundamentals, by J. George Wills 4. Solar Engineering for Domestic Buildings, by William A. Himmelman 5. Applied Engineering Mechanics: Statics and Dynamics, by G. Boothroyd and C Poli 6. Centrifugal Pump Clinic, by Igor J. Karassik 7. Computer-Aided Kinetics for Machine Design, by Daniel L. Ryan 8. Plastics Products Design Handbook, Part A: Materials and Components, edited by Edward Miller 9. Turbomachinery: Basic Theory and Applications, by Earl Logan, Jr. 10. Vibrations of Shells and Plates, by Werner Soedel 11. Flat and Corrugated Diaphragm Design Handbook, by Mario Di Giovanni 12. Practical Stress Analysis in Engineering Design, by Alexander Blake 13. An Introduction to the Design and Behavior of Bolted Joints, by John H. Bickford 14. Optimal Engineering Design: Principles and Applications, by.James N. Siddall 15. Spring Manufacturing Handbook, by Harold Carlson GE-1018.006 16. Industrial Noise Control: Fundamentals and Applications; by Lewis H. Bell 17.. Gears and Their Vibration: A Basic Approach to Understanding Gear Noise, by J.