Gears & Gear Lubrication
Total Page:16
File Type:pdf, Size:1020Kb
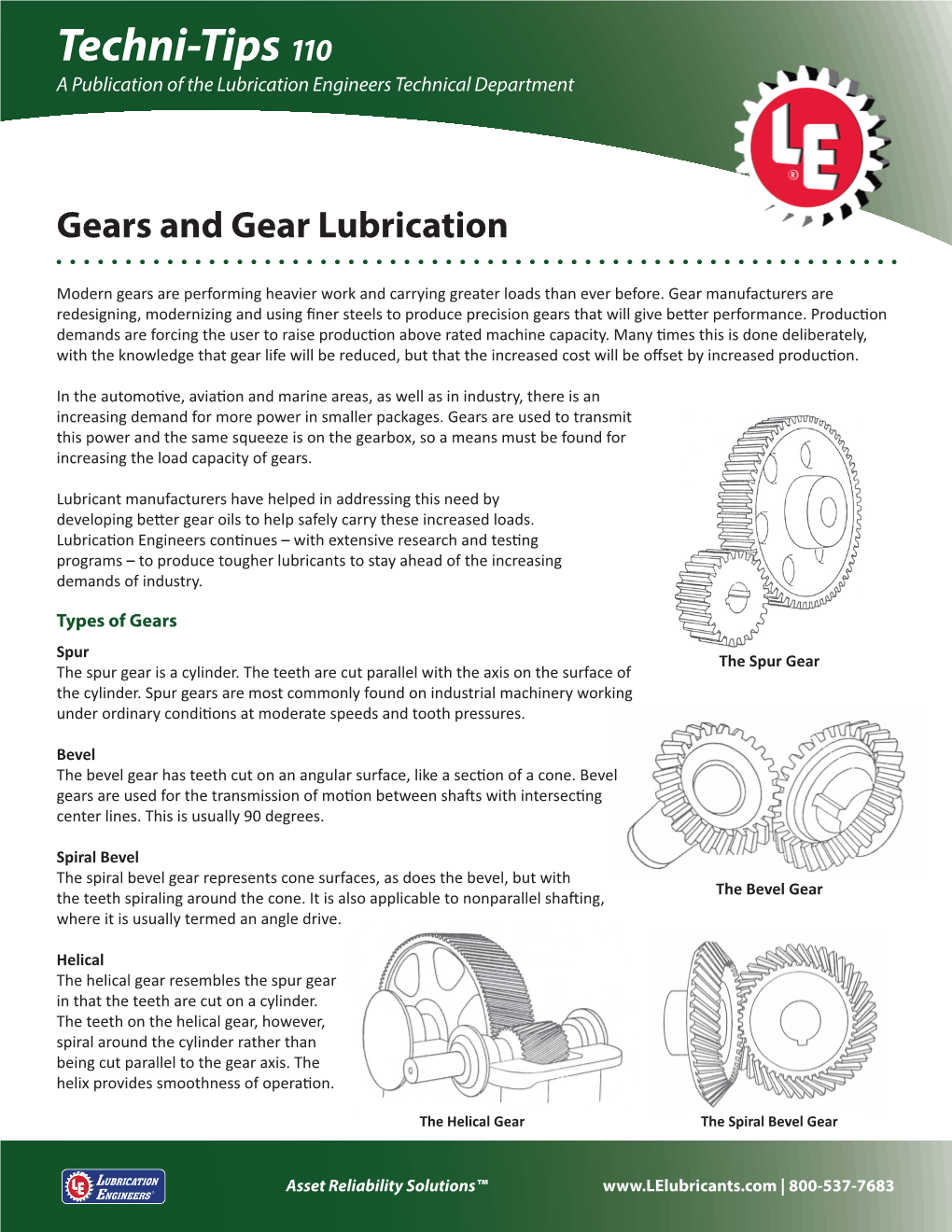
Load more
Recommended publications
-
Identification and Proposed Control of Helicopter Transmission Noise at the Source
~ I \. USAAVSCOM-TR-87-C-2 Identification and Proposed Control of Helicopter Transmission Noise at the Source John J. Coy, Robert F. Handschuh, and David G. Lewicki Propulsion Directorate U.S. Army Research and Technology Activity-AVSCOM Lewis Research Center Cleveland, Ohio Ronald G. Huff, Eugene A. Krejsa, and Allan M. Karchmer Lewis Research Center Cleveland, Ohio (NASA-TH-89312) IDENTIEICA?ICh AND PROPOSED 1487- 168 16 CCNTRCL CF HELICCE'ILR TEANSMISSlCN dOISE AT TEE SCUBCE (NASA) 23 i; csci 01c Unclas 63/05 43744 Preprint for the NASA/Army Rotorcraft Technology Conference held at NASA Ames Research Center Moffett Field, California, March 17-19, 1987 IDENTIFICATION AND PROPOSED CONTROL OF HELICOPTER TRANSMISSION NOISE AT THE SOURCE John J. Coy, Robert F. Handschuh, and David G. Lewicki Propulsion Directorate U.S. Army Research and Technology Activity - AVSCOM Lewis Research Center Cleveland, Ohio 44135 Ronald 6. Huff, Eugene A. Krejsa, and Allan M. Karchmer National Aeronautics and Space Administration Lewis Research Center Cleveland, Ohio 44135 SUMMARY Helicopter cabin interiors require noise treatment which is expensive and adds weight. The gears inside the main power transmission are major sources of cabin noise. This paper describes gork conducted by the NASA Lewis Research Center in measuring cabin interior noise and in relating the noise spectrum to the gear vibration of the Army's OH-58 helicopter. Flight test data indicate that the planetary gear traln Is a major source of cabin noise and that other low frequency sources are present that could dominate the cabin noise. Compan- ion vibration measurements were made in a transmission test stand, revealing that the single largest contributor to the transmission vibration was the spiral bevel gear mesh. -
Computer Numerical Control Grinding of Spiral Bevel Gears
AUG 31 '95 09:03 FR NASA LERC 216 433 5783 TO 913816218134 P.83 NASA AVSCOM Contractor Report 187175 Technical Report 90- F- 6 Computer Numerical Control Grinding of Spiral Bevel Gears H. Wayne Scott Bell Helicopter Textron, Inc. Fort Worth, Texas August 1991 •.& PUBLICLY AVAII_. BLE . .... .. luly 1995 Prepared for Lewis Research Center Under Contract NAS3 - 25030 and Propulsion Directorate U.S. Army Aviation Research and Technology--AVSCOM AI/ A NatJot_ Aeronauticsand Spaoe Administration - - • ' " (NASA-CR-187175) COMPUTER N96-10758 NUMERICAL CONTROL GRINDING OF SPIRAL BEVEL GEARS (Textron Bell Helicopter) 89 p Unclas J J G3/37 0064089 IF TABLE OF CONTENTS SECTION TITLE PAGE I. Introduction ............................................................... 1 II. Background ............................................................... 2 III. Program Plan .............................................................. 4 IV. Technical Approach ........................................................ 6 4.1 Phase I - Definition of the Prototype CNC Grinder ......................... 6 4.1.1 Task 1- Baseline Grinder 4.1.2 Task 2 - Definition of Prototype 4.1.3 Task 3- Economic Analysis 4.1.4 Task 4- Drawings and Oral Briefings 4.2 Phase II - Integration of Hardware and Software into Prototype CNC Grinder for Spiral Bevel Gears ............................................... 12 4.2.1 Task 5 - Implementation of Conversion Hardware to Baseline Grinder 4.2.2 Task 6 - Add CNC to the Converted Grinder 4.2.3 Task 7 - Demonstrate CNC - Controlled Grinder 4.2.4 Task 8 - Update Economic Analysis 4.2.5 Task 9 - Drawings and Oral Briefing 4.3 Phase III- Pilot Production ............................................. 44 4.3.1 Task 10 - Production Runs Using the Proof of Concept Grinder 4.3.1.1 Development Activities 4.3.2 Task 11 - Update Conversion to CNC Cost and Estimated Savings on Finish Grinding 4.3.3 Task 12- Government/Industries Briefing 4.3.4 Task 13 - Documentation V. -
Contact Mechanics in Gears a Computer-Aided Approach for Analyzing Contacts in Spur and Helical Gears Master’S Thesis in Product Development
Two Contact Mechanics in Gears A Computer-Aided Approach for Analyzing Contacts in Spur and Helical Gears Master’s Thesis in Product Development MARCUS SLOGÉN Department of Product and Production Development Division of Product Development CHALMERS UNIVERSITY OF TECHNOLOGY Gothenburg, Sweden, 2013 MASTER’S THESIS IN PRODUCT DEVELOPMENT Contact Mechanics in Gears A Computer-Aided Approach for Analyzing Contacts in Spur and Helical Gears Marcus Slogén Department of Product and Production Development Division of Product Development CHALMERS UNIVERSITY OF TECHNOLOGY Göteborg, Sweden 2013 Contact Mechanics in Gear A Computer-Aided Approach for Analyzing Contacts in Spur and Helical Gears MARCUS SLOGÉN © MARCUS SLOGÉN 2013 Department of Product and Production Development Division of Product Development Chalmers University of Technology SE-412 96 Göteborg Sweden Telephone: + 46 (0)31-772 1000 Cover: The picture on the cover page shows the contact stress distribution over a crowned spur gear tooth. Department of Product and Production Development Göteborg, Sweden 2013 Contact Mechanics in Gears A Computer-Aided Approach for Analyzing Contacts in Spur and Helical Gears Master’s Thesis in Product Development MARCUS SLOGÉN Department of Product and Production Development Division of Product Development Chalmers University of Technology ABSTRACT Computer Aided Engineering, CAE, is becoming more and more vital in today's product development. By using reliable and efficient computer based tools it is possible to replace initial physical testing. This will result in cost savings, but it will also reduce the development time and material waste, since the demand of physical prototypes decreases. This thesis shows how a computer program for analyzing contact mechanics in spur and helical gears has been developed at the request of Vicura AB. -
Evaluation on Failure Analysis of an Automobile Differential Pinion Assembly (IJIRST/ Volume 1 / Issue 12 / 054)
IJIRST –International Journal for Innovative Research in Science & Technology| Volume 1 | Issue 12 | May 2015 ISSN (online): 2349-6010 Evaluation on Failure Analysis of an Automobile Differential Pinion Assembly Ronak P Panchal Pratik B. Umrigar M.E. Student Department of Automobile Engineering Department of I.C. Engine & Automobile GTU, Mahesana, India GTU, Mahesana, India Abstract Bevel gears have become a subject to research interest because the dynamicload, attention of the noise level during operation and demand for lighter and smaller. In such type of gears there is a problems of failures contact at meshing the teeths. This can be avoided or minimized by proper method analysis and modification of the different gear parameters. This thesis presents characteristics of a bevel gear in dynamic condition involving meshing stiffness and other stresses produce. The purpose of this thesis is by using numerical approach to develop theoretical model of bevel gear and to determine the effect of meshing gear tooth stresses by taking material case hardened alloy steel (15Ni4Cr1) . To estimate the meshing stiffness, three-dimensional solid models for different number of teeth are generated by Solid works and the numerical solution is done in Ansys which is a finite element analysis. Keywords: Design of Spiral Bevel Gear, Analysis of Spiral Bevel Gear _______________________________________________________________________________________________________ I. INTRODUCTION Gear is a mechanical device used in transmission systems that allows rotational force to be transferred to another gears . The gear teeth allow force to be fully transmitted without slip and depending on the configuration can transmit forces at different speeds, torques, and even in a different directions. -
Gear Resonance Analysis
GEAR SOLUTIONS GEAR MAGAZINE GEAR RESONANCE ANALYSIS Using Rapid Prototyped Gears Upgrading and Testing a 72,000 HP GEARBOX INNOVATION IN Spline Rolling Rack Tooling UNIMILL: Prototype and Bevel Gear IMTS 2014 IMTS Manufacturing SEPTEMBER 2014 SEPTEMBER Your Resource for Machines, Services, and Tooling for the Gear Industry SEPTEMBER 2014 gearsolutions.com Indiana Technology & Manufacturing Companies, Inc. (ITAMCO), left to right: Nobel Neidig - President Joel D. Neidig - Technology Manager Gary Neidig - Vice President Growth Fund. Invest in your future. Kapp Niles machines provide increased productivity to grow your business. Our machines are built for the long haul, so you can pass them down from generation to generation – with 97% of our finishing machines still in operation since 1984. Plus, our quality service and retrofitting capabilities allow you to stay current with changing technologies. Invest in Kapp-Niles and invest in the future of your business. ZPI/E: Profile grinding of internal gears with large modules. Switches from internal to exter- nal grinding by swiveling the grinding arm 1800. Wheels are dressed while in grinding position. Precise, efficient, flexible. Booth #N-7036 See us on the web! kapp-usa.com 2870 Wilderness Place | Boulder, CO 80301 p: 303.447.1130 | f: 303.447.1131 | [email protected] The most interesting man in the gear world He once climbed the Matterhorn and attended a machine run off, in Germany, on the same afternoon He has been known to hand carry parts to his secret manufacturing plant, in an unknown location But, when it comes to workholding, He always prefers König Stay productive, my friends 1921 Miller Drive Longmont, CO 80501 303-776-6212 www.toolink-eng.com OUR LINE JUST GOT LONGER.. -
Design and Fabrication of Shaft Drive for Two Wheelers
International OPEN ACCESS Journal Of Modern Engineering Research (IJMER) Design and Fabrication of Shaft Drive for two Wheelers K.Vinoth Kumar1, Kari Naga Nikhil2, Kakollu Manoj Kumar3, Kaza Sai Sravan4, K.Subha Theja5 1,2,3,4,5Student, Department Of Mechanical Engineering R.M.K College Of Engineering & Technology, Thiruvallur , India 1. Abstract 1.1 Role Of Automobile In Our Day To Day Life In modern world the living status were developed and developing more equipped. The automobile takes a great part in the development, since it plays a major key in daily life while automobile is concern two wheeler i.e.(motor cycles and bike) it plays very important role because it saves the time of traveller by reaching the target place very faster. Although it saves the time, it makes lots of noise by the chain drive and also makes greasy over the parts of the bike by the chain drive lubrication. It leads to lot of maintenance cost. So by keeping maintenance as the main concept in our mind we had planned to do this project. 1.2 Proposed Method A shaft-driven two wheeler is a two wheeler that uses a drive shaft instead of a chain to transmit power from the pedals to the wheel arrangement. Shaft drives were introduced over a century ago, but were mostly supplanted by chain-driven two wheelers due to the gear ranges possible with sprockets and derailleur. Recently, due to advancements in internal gear technology, a small number of modern shaft-driven two wheelers have been introduced. Shaft-driven bikes have a large bevel gear where a conventional bike would have its chain ring. -
JOURNAL of MECHANICAL and CIVIL ENGINEERING Shivam Bansal Mechanical Department Dronacharya College of Engineering Khentawa
- - IJRDO - Journal of Computer Science and Engineering ISSN: 2456-1843 JOURNAL OF MECHANICAL AND CIVIL ENGINEERING GEARS Shivam Bansal Mechanical Department Dronacharya College of Engineering Khentawas, Farukhnagar,Gurgaon [email protected] Yogesh Vashiath Mechanical Department Dronacharya College of Engineering Khentawas, Farukhnagar,Gurgaon [email protected] Ujjwal Batra Mechanical Department Dronacharya College of Engineering Khentawas, Farukhnagar,Gurgaon [email protected] INTRODUCTION A gear or cogwheel is a rotating machine part having cut teeth, or cogs, which mesh with another toothed part in order to transmit torque, in most cases with teeth on the one gear being of identical shape, and often also with that shape on the other gear. Two or more gears working in tandem are called a transmission and can produce a mechanical advantage through a gear ratio and thus may be considered a simple machine. Geared devices can change the speed, torque, and direction of a power source. The most common situation is for a gear to mesh with another gear; however, a gear can also mesh with a non-rotating toothed part, called a rack, thereby producing translation instead of rotation. The gears in a transmission are analogous to the wheels in a crossed belt pulley system. An advantage of gears is that the teeth of a gear prevent slippage. When two gears mesh, and one gear is bigger than the other (even though the size of the teeth must match), a mechanical advantage is produced, with the rotational speeds and the torques of the two gears differing in an inverse relationship. In transmissions which offer multiple gear ratios, such as bicycles, motorcycles, and cars, the term gear, as in first gear, refers to a gear ratio rather than an actual physical gear. -
Spur and Straight Bevel Gears
FUNdaMENTALS of Design Topic 6 Power Transmission Elements II © 2000 Alexander Slocum 6-0 1/25/2005 Topic 6 Power Transmission Elements II Topics: • Screws! • Gears! www.omax.com © 2000 Alexander Slocum 6-1 1/25/2005 Screws! • The screw thread is one of the most important inventions ever made • HUGE forces can be created by screw threads, so they need to be carefully engineered: – Leadscrews – Physics of operation –Stresses – Buckling and shaft whip – Mounting • When HUGE forces are created by screws – The speed is often slow – Always check to make sure you get what you want Mike Schmidt-Lange designed this auger-wheeled vehicle for the “sands” of 1995’s 2.007 contest Pebble Beach, and – If you try sometime, you just might get what you need ☺ years later, a major government lab “invented” the idea as a Mars rover sand-propulsion device… Someday, apples will be so plentiful, people will need machines to peel © 2000 Alexander Slocum 6-2 them…!1/25/2005 Screws: Leadscrews & Ballscrews • Leadscrews are essentially accurate screws used to move a nut attached to a load, and they have been used for centuries to convert rotary motion into linear motion – Leadscrews are commonly used on rugged economy machine tools – Efficiency in a leadscrew system may be 30-50%, • Precision machine or those concerned with high efficiency often uses a ballscrew – Sliding contact between the screw and nut is replaced by recirculating ball bearings and may have 95% efficiency Carriage Rotary Encoder AC Brushless Motor Flexible Coupling Support Bearings Bearing -
Automatic Gear Shifting Mechanism in Two Wheelers Using Electromagnetic Actuator
International Research Journal of Engineering and Technology (IRJET) e-ISSN: 2395-0056 Volume: 07 Issue: 09 | Sep 2020 www.irjet.net p-ISSN: 2395-0072 Automatic Gear Shifting Mechanism in Two Wheelers Using Electromagnetic Actuator Mr. Uzair Ahmed Shaikh Student, Department of Mechanical Engineering, Shivajirao S. Jondhle college of Engineering & Technology, Asangaon, Maharashtra, India. ---------------------------------------------------------------------***---------------------------------------------------------------------- Abstract - Motorbikes are broadly used around the world 2. GENERAL COMPONENTS/TERMINOLOGIES mostly in countries like India, Thailand, Indonesia, etc. The gear shifting arrangement of the motorbikes is conventionally 2.1 Sensor manual. The main purpose of the project is to automate the gear transmission for the standard motorcycle by using A proximity sensor is a non-contact device that senses the embedded system. As the increase in demand for CVT presence of an object. According to the application, proximity (Continuous Variable Transmission) which are gearless system sensors are classified into different types. In this project, but, has low fuel efficiency as compared to geared Motorcycle. inductive type proximity sensor is used. This sensor detects This system not only increases the fuel efficiency but also only metallic object placed next to it. This sensor works eliminate the human intervention in gear system, making under the electrical principal of inductance, the fluctuating driving easy. The manual mechanical gear shifting will remain current indices induces the EMF (electromotive force) in a unchanged in this arrangement as there is an electromagnetic target object. The cost of this sensor is comparatively low and actuator placed with the lever which helps to shift the gear operating distance is less than 50mm. -
Worm Gear Screw Jacks Reliable and Versatile High Performance Screw Jacks
Worm Gear Screw Jacks Reliable and versatile high performance screw jacks www.thomsonlinear.com Thomson – the Choice for Optimized Motion Solutions Often the ideal design solution is not about finding the fastest, sturdiest, most accurate or even the least expensive option. Rather, the ideal solution is the optimal balance of performance, life and cost. The Best Positioned Supplier of Mechanical Motion Technology Thomson has several advantages that make us the supplier of choice for motion control technology. • Thomson owns the broadest standard product offering of mechanical motion technologies in the industry. • Modified versions of standard product or white sheet design solutions are routine for us. • Choose Thomson and gain access to over 70 years of global application experience in industries including packaging, factory automation, material handling, medical, clean energy, printing, automotive, machine tool, aerospace and defense. A Name You Can Trust A wealth of product and application information as well as 3D models, software tools, our distributor locator and global contact information is available at www.thomsonlinear.com. For assistance in Europe, contact us at +44 1271 334 500 or e-mail us at [email protected]. Talk to us early in the design process to see how Thomson can help identify the optimal balance of performance, life and cost for your next application. And, call us or any of our 2000+ distribution partners around the world for fast delivery of replacement parts. Local Support Around the Globe Application -
A New Methodology to Optimize Spiral Bevel Gear Topography Emmanuel Mermoz, Julien Astoul, Marc Sartor, Jean-Marc Linares, Alain Bernard
A new methodology to optimize spiral bevel gear topography Emmanuel Mermoz, Julien Astoul, Marc Sartor, Jean-Marc Linares, Alain Bernard To cite this version: Emmanuel Mermoz, Julien Astoul, Marc Sartor, Jean-Marc Linares, Alain Bernard. A new method- ology to optimize spiral bevel gear topography. CIRP Annals - Manufacturing Technology, Elsevier, 2013, 62, pp.119 - 122. 10.1016/j.cirp.2013.03.067. hal-01440192 HAL Id: hal-01440192 https://hal-amu.archives-ouvertes.fr/hal-01440192 Submitted on 23 Jan 2017 HAL is a multi-disciplinary open access L’archive ouverte pluridisciplinaire HAL, est archive for the deposit and dissemination of sci- destinée au dépôt et à la diffusion de documents entific research documents, whether they are pub- scientifiques de niveau recherche, publiés ou non, lished or not. The documents may come from émanant des établissements d’enseignement et de teaching and research institutions in France or recherche français ou étrangers, des laboratoires abroad, or from public or private research centers. publics ou privés. A new methodology to optimize spiral bevel gear topography a, a b c d Emmanuel Mermoz (3) *, Julien Astoul , Marc Sartor , Jean Marc Linares (2) , Alain Bernard (1) a EUROCOPTER, Aeroport de Marseille Provence, 13700 Marignane, France b Universite de Toulouse, INSA, UPS, Mines Albi, ISAE, ICA (Institut Clement Ader), 135, avenue de Rangueil, F-31077 Toulouse, France c Aix-Marseille Universite, CNRS, ISM UMR 7287, 13288 Marseille Cedex 09, France d Ecole Centrale de Nantes, IRCCyN, UMR CNRS 6597, BP 92101, 1 rue de la Noe, 44321 Nantes Cedex 3, France Keywords: Optimization, Finite element, method, Spiral bevel gear This paper aims to present the new method developed to generate optimized spiral bevel gear surfaces. -
Study of Differential Bevel Gear Through Machining Method
International Journal of Engineering and Technical Research (IJETR) ISSN: 2321-0869, Volume-1, Issue-3, May 2013 STUDY OF DIFFERENTIAL BEVEL GEAR THROUGH MACHINING METHOD Mohd Abbas, Sanjeev Sharma, Vinit Kumar Sharma Straight Path. Abstract— In this paper we have selected the machining method, a cost saving manufacturing process to produce If the left side gear (red) encounters resistance, the planet straight bevel gears without any compromise with quality gear (Green) rotates about the left side gear, in turn applying parameters, then validate the samples taken from vendor as extra rotation to the right side gear (yellow). per our design requirement and to increase Durability & Productivity of Straight Bevel Gears. To validated we have used tractor as a testing equipment and validate the gears to our design specification. Index Terms— Straight Bevel Gear, Spiral Bevel Gear Circular Pitch, Pressure Angle, Pitch Diameter, Tooth Parts. I. INTRODUCTION Power is supplied from the engine, via the gearbox, to a driveshaft, which runs to the drive axle. A pinion gear at the end of the propeller shaft is encased within the differential Figure 2: Differential Dynamics When Vehicle Takes Turn. itself, and it engages with the large crown-wheel. The crown-wheel is attached to a carrier, which holds a set of A general Gear manufacturing process contains the three-four small planetary straight bevel gears. The three following process- planetary gears are set up in such a way that the two outer gears (the side gears) can rotate in opposite directions relative to each other. The pair of side gears drive the axle shafts to each of the wheels.