Research Review of a Vehicle Energy-Regenerative Suspension System
Total Page:16
File Type:pdf, Size:1020Kb
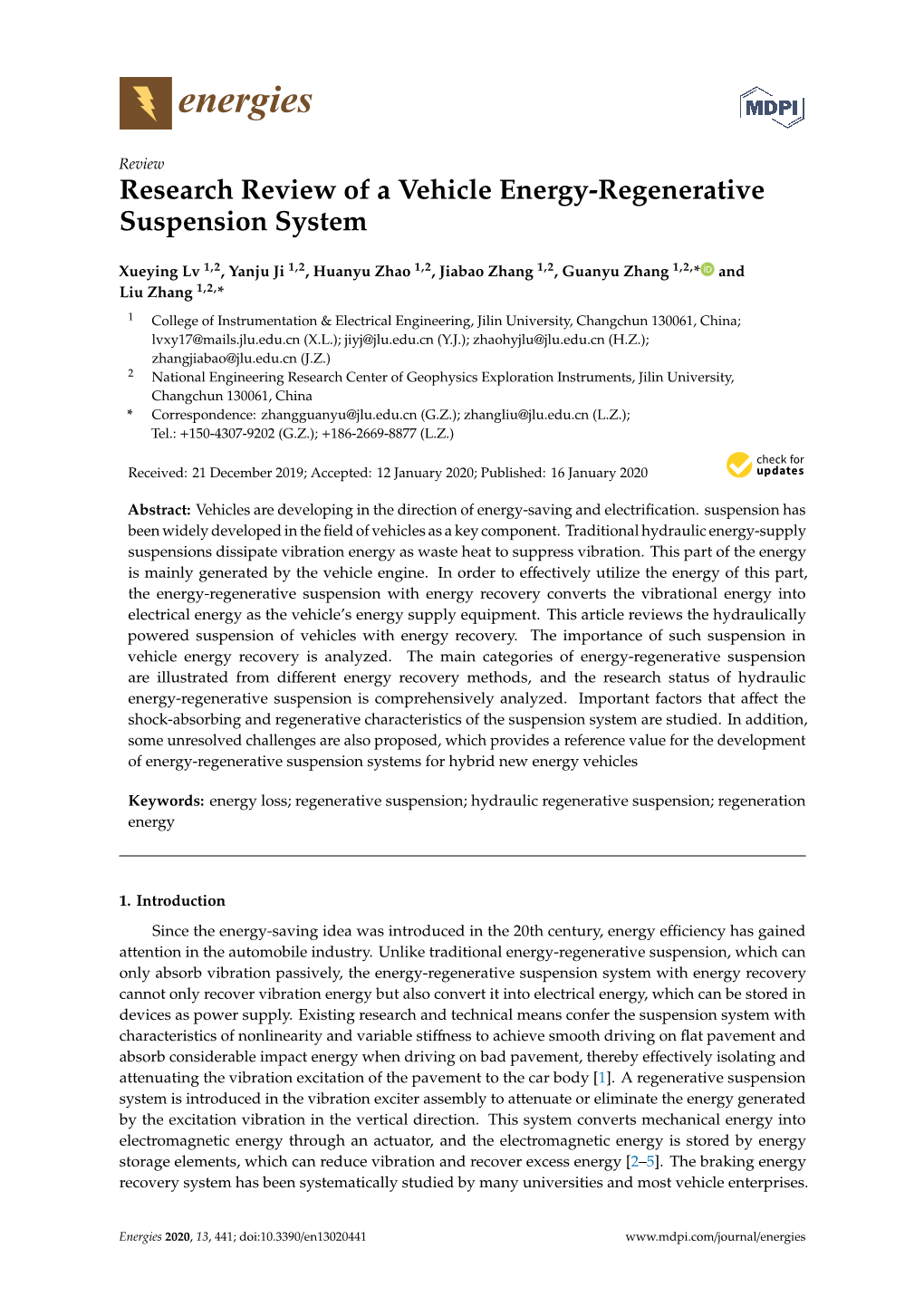
Load more
Recommended publications
-
Active Suspension Control of Electric Vehicle with In-Wheel Motors
University of Wollongong Research Online University of Wollongong Thesis Collection 2017+ University of Wollongong Thesis Collections 2018 Active suspension control of electric vehicle with in-wheel motors Xinxin Shao University of Wollongong Follow this and additional works at: https://ro.uow.edu.au/theses1 University of Wollongong Copyright Warning You may print or download ONE copy of this document for the purpose of your own research or study. The University does not authorise you to copy, communicate or otherwise make available electronically to any other person any copyright material contained on this site. You are reminded of the following: This work is copyright. Apart from any use permitted under the Copyright Act 1968, no part of this work may be reproduced by any process, nor may any other exclusive right be exercised, without the permission of the author. Copyright owners are entitled to take legal action against persons who infringe their copyright. A reproduction of material that is protected by copyright may be a copyright infringement. A court may impose penalties and award damages in relation to offences and infringements relating to copyright material. Higher penalties may apply, and higher damages may be awarded, for offences and infringements involving the conversion of material into digital or electronic form. Unless otherwise indicated, the views expressed in this thesis are those of the author and do not necessarily represent the views of the University of Wollongong. Recommended Citation Shao, Xinxin, Active suspension control of electric vehicle with in-wheel motors, Doctor of Philosophy thesis, School of Electrical, Computer and Telecommunications Engineering, University of Wollongong, 2018. -
Review on Active Suspension System
SHS Web of Conferences 49, 02008 (2018) https://doi.org/10.1051/shsconf/20184902008 ICES 2018 Review on active suspension system 2 Aizuddin Fahmi Mohd Riduan1, Noreffendy Tamaldin , Ajat Sudrajat3, and Fauzi Ahmad4 1,2,4Centre for Advanced Research on Energy, Universiti Teknikal Malaysia Melaka, Hang Tuah Jaya, 76100 Durian Tunggal, Melaka Malaysia. 1,2,4Faculty of Mechanical Engineering, Universiti Teknikal Malaysia Melaka, Hang Tuah Jaya, 76100 Durian Tunggal, Melaka, Malaysia. 3Engineering Physics, Faculty of Science and Technology, Universitas Nasional-Jakarta JL. Sawo Manila, Pasar Minggu, Jakarta 12520, Indonesia. Abstract. For the past decade, active suspension systems had made up most of research area concerning vehicle dynamics. For this review, recent studies on automobile active suspensions systems were examined. Several vehicular suspension types were also described to compare amongst them. From published investigations by previous researchers, various automotive suspensions in terms of cost, weight, structure, reliability, ride comfortability, dynamic and handling performance were exhibited and compared. After careful examination, it was concluded that electromagnetic active suspensions should be the general direction of vehicle suspension designs due to its energy regeneration, high bandwidth, simpler structure, flexible and accurate force control, better handling performance as well as drive characteristics. Keywords: Active Suspension, Handling Performance, Dynamic Performance 1 Introduction Vehicle suspension main task -
Semi-Active Suspension
KYB TECHNICAL REVIEW No. 55 OCT. 2017 Glossary Semi-active Suspension Included in “The technical term used in Development of Externally-Mounted Shock Absorber with Adjustable Solenoid Damping Force” P. 25 ITO Naoki KYB TECHNICAL REVIEW editor 1 Semi-active Suspension Skyhook damper Cs (imaginary) Acceleration Speed Semi-active suspension is a type of automotive suspension systems that controls the damping force of the shock absorber in response to input from the continuously varying road surfaces. It is intended to approximately Cp: Damping coefcient of implement the active suspension (to be described later) passive damper with a damping force adjustable shock absorber Cs: Damping coefcient of Skyhook damper (hereinafter “SA”). Fcont: Controlling force M2: Sprung mass Semi-active suspension may be implemented by several M1: Unsprung mass types of control methodologies. A generally known typical K2: Suspension spring constant K1: Tire spring constant technology is Skyhook control. X0: Road surface variation X1: Unsprung variation Fig. 1 shows a Skyhook control model. An imaginary X2: Sprung variation damper (= Skyhook damper) hung from an aerial height with its end fi xed there is implemented by generating a Fig. 1 Skyhook control model force of the sprung (vehicle body) speed multiplied by the damping coeffi cient sC . A passive (= uncontrolled) damper 4th quadrant 1st quadrant (Cp), which is installed in parallel with the Skyhook damper (Cs), provides a force equivalent to the SOFT damping force of the damping force adjustable SA. When this damper model is given a random input from the road surface, the relationship between the required Contraction Expansion combined damping forces of the Skyhook and passive dampers, and the relative speed (piston speed) between the sprung and unsprung components (including tires) is Relative speed (m/s) shown in Fig. -
Adaptive Semi-Active Suspension and Cruise Control Through LPV Technique
applied sciences Article Adaptive Semi-Active Suspension and Cruise Control through LPV Technique Hakan Basargan 1 , András Mihály 2, Péter Gáspár 2,* and Olivier Sename 3 1 Department of Control for Transportation and Vehicle Systems, Budapest University of Technology and Economics, M˝uegyetemrkp. 3, H-1111 Budapest, Hungary; [email protected] 2 Systems and Control Laboratory, Institute for Computer Science and Control, Kende u. 13-17, H-1111 Budapest, Hungary; [email protected] 3 GIPSA-lab, INPG, Université Grenoble Alpes, 11 Rue des Mathématiques, 38000 Grenoble, France; [email protected] * Correspondence: [email protected]; Tel.: +36-1-279-6171 Abstract: Several studies exist on topics of semi-active suspension and vehicle cruise control systems in the literature, while many of them just consider actual road distortions and terrain characteristics, these systems are not adaptive and their subsystems designed separately. This study introduces a new method where the integration of look-ahead road data in the control of the adaptive semi-active suspension, where it is possible to the trade-off between comfort and stability orientation. This trade-off is designed by the decision layer, where the controller is modified based on prehistorical passive suspension simulations, vehicle velocity and road data, while the behavior of the controller can be modified by the use of a dedicated scheduling variable. The adaptive semi-active suspension control is designed by using Linear Parameter Varying (LPV) framework. In addition to this, it proposes designing the vehicle velocity for the cruise controller by considering energy efficiency and comfort together. -
Mercedes Benz ABC Active Body Control Information Sheet Www
Mercedes Benz ABC Active Body Control Information Sheet www.abcspecialist.nl Active Body Control, or ABC, is the Mercedes-Benz fully-active suspension system, that in real time controls the vehicle body motions and virtually eliminates body rol and vibrations in many driving situations including cornering, accelerating, and braking. Disclaimer ABCspecialist is a Dutch company specialized in hydraulic suspension systems. Since 2010 we sell all parts for the ABC system of Mercedes Benz from our stock exclusively for the business market. All the information on our websites, in our documents, advertisements and our communication has been compiled, written, and realized with the utmost care. Nevertheless, there is always the possibility that certain information will become obsolete over time, is no longer correct, or that errors have occurred during the translation. We have compiled the content with the utmost care, but cannot give any guarantees with regard to the content. No rights or liability can be dissected from information, prices, advice or any text in this document, on our website or in advertisements or communications, and ABCspecialist is not liable for the consequences of activities that are taken on this basis. Nothing from this document and our website will be reproduced or published without the prior written permission of ABCspecialist. Reading this document signifies your agreement to our terms and conditions. Work should only be performed by a trained mechanic else damage might be caused to the vehicle. The ABC system is working under a pressure of over 200 bar, taking the wrong installation steps can have serious consequences. You are responsible for studying the official service manual and the necessary safety proceedings that should be taken before working on, and raising the vehicle as when errors are made serious injuries and death can occur. -
Chassis Control Systems for Safety, Environmental Performance, and Driving Comfort
Hitachi Review Vol. 63 (2014), No. 2 122 Chassis Control Systems for Safety, Environmental Performance, and Driving Comfort Tadahiko Nogami OVERVIEW: Chassis subsystems, such as suspensions, steering, and brakes, Motohiro Higuma play an important role in determining driving, cornering, and stopping Yasuhiko Amari performance of a vehicle. Hitachi supplies a wide range of such products and has drawn on technologies, which have built up with conventional Fumiyuki Yamaoka products to incorporate electronics and electric drive into these systems. By Mitsuo Sasaki drawing on capabilities from throughout Hitachi, including making further enhancements to cooperative control techniques for electric powertrains of HEVs and EVs and for engine-driven powertrains (a fi eld in which progress is being made on improving fuel economy), integrating information and recognition systems such as car navigation and cameras, and developing systems for integrated control of chassis subsystems and for autonomous driving, Hitachi is seeking to be a supplier that can provide the entire world with vehicles that are safer, greener, and more comfortable. INTRODUCTION from cameras and radar, and information acquired via ELIMINATING traffi c accidents is an ever-present car-to-car communications and car-to-infrastructure objective for society, and factors such as aging drivers communications, with growing activity in the are behind stronger demand for accident prevention development of technology that has potential for use systems. Along with electronic stability control in autonomous driving systems. Through integrated (ESC) for preventing skidding, there are also moves control involving the cooperative interoperation of toward mandating systems that brake automatically in these technologies with chassis control systems, emergent situations. -
The Automotive Suspension Systems Report Supplierbusiness
SupplierBusiness The Automotive Suspension Systems Report 2013 Edition The Automotive Suspension Systems Report CONTENTS Introduction ................................................................................................................ 7 Key market drivers .................................................................................................... 12 Fuel efficiency and CO2 emissions .......................................................................... 12 The United States ................................................................................................ 12 The European Union ........................................................................................... 13 Japan .................................................................................................................. 14 China .................................................................................................................. 14 Other countries .................................................................................................... 15 Materials considerations ......................................................................................... 15 Increasing electrification ......................................................................................... 20 Systems integration.............................................................................................. 20 Challenges and barriers ........................................................................................... 24 Chassis -
Active Roll Control (ARC): System Design and Hardware-In- The-Loop Test Bench
Active Roll Control (ARC): System Design and Hardware-In- the-Loop Test Bench A. SORNIOTTI, A. MORGANDO and M. VELARDOCCHIA* Politecnico di Torino, Department of Mechanics Correspondence *Corresponding author. Email: [email protected] Abstract. The first part of the paper describes the targets related to the design of an Active Roll Control (ARC) system, based on the hydraulic actuation of the anti-roll bars of an automobile. Then the basic static and dynamic design principles of the system are commented in detail. The second part of the paper presents the Hardware-In-the-Loop (HIL) test bench implemented to evaluate the designed system. In the end, the main experimental results are summarized and discussed, also from the point of view of the integration of ARC with Electronic Stability Program (ESP). Keywords: Active Roll Control; Hardware-In-the-Loop; Handling; Comfort 1 Targets and Fundamentals The first target of the Active Roll Control (ARC) system is the reduction of the roll angle for small values of vehicle body lateral acceleration during semi-stationary manoeuvres. This target improves the comfort feeling transmitted by the vehicle to the passengers. In addition, it reduces the variation of the characteristic angles, especially camber angle, between the tires and the road plane during vehicle turning. It can provoke, according to the characteristics of the suspensions, a substantial improvement of vehicle dynamics in semi-stationary manoeuvres. The second target of the ARC system is the reduction of body sideslip angle and body yaw rate oscillations during dynamic manoeuvres, like step steer or double lane change. This target can be reached through a dynamic variation of the roll stiffness distribution between the two axles of the car. -
Magneride Performance and Challenges
MagneRide Performance and Challenges Vehicle Dynamics Expo 2008 06 May 2008 1 Delphi MagneRide System MagneRide Advantages • Wide range between minimum and maximum forces • High authority at low piston velocities • Fast and linear response to control input • No moving parts Yaw Body Control Stability and Handling Control – Reduces body motions – Improves vehicle stability, steering response, and directional control – Improves impact isolation – Controls transient pitch/roll motions – Improves ride quality and comfort – Improves handling Pitch Roll Wheel Control Adaptive Controls – Reduces wheel shake/resonance during – Driver Mode switch and after impacts Heave – Load compensation – Reduces tire normal load variation and improves road holding – Vehicle speed dependence – Improves feeling of safety – Special events management – Provide vehicle refinement Delphi is a leader in Controlled Damping Systems Technology 2 MagneRide Piston Principle of Operation F High Pressure Magnetic Field Low Pressure MR FLUID 3 Vehicle Performance Vehicle test and configuration Vehicle: • Type: Large European Luxury Car • Mass: 2100 kg (distribution of 57% / 43%) • Tyres: Bridgestone 255/45 ZR 18 Semi-active suspension systems compared: • Reference car : Production Semi-Active Suspension with levelling (Ref) • Delphi car : MagneRide system with levelling (MR) => Suspension modes : Two, Soft and Hard for each vehicle Vehicle Handling Tests: VDA ISO 7401 Acceleration to 90km/ Sweep ISO7401 Step steer ISO 7401 on referenced bumpy road Freq: 0. to 2.5 Hz 80kph, -
Chassis & Suspension
Applications – Chassis & Suspension Introduction The chassis is considered to be one of the significant structures of an automobile. It is the frame which holds both the car body and the power train. Various mechanical parts like the engine and the drive train, the axle assemblies including the wheels, the suspension parts, the brakes, the steering components, etc., are bolted onto the chassis. The chassis provides the strength needed for supporting the different vehicular components as well as the payload and helps to keep the automobile rigid and stiff. Consequently, the chassis is also an important component of the overall safety system. Furthermore, it ensures low levels of noise, vibrations and harshness throughout the automobile. Suspension is the term given to the system of springs, shock absorbers and linkages that connects the vehicle to its wheels. The suspension system serves a dual purpose. It contributes to the car's road performance, the braking characteristics for good active safety and the driving pleasure. It also keeps the vehicle occupants comfortable and reasonably well isolated from road noise, bumps, and vibrations. Chassis design concepts Originally, automobile designs used the body-on-frame construction where a load-bearing chassis consisting of a ladder frame, the powertrain, and the suspension formed the base vehicle which then supported a non-load-bearing body. In the beginning used on almost all vehicles, the ladder frame has been gradually phased out on passenger cars around the 1940s in favor of perimeter frames. In the second half of the last century, the frame chassis design was more and more displaced by monocoque constructions, integrating the body and chassis into a single unit. -
Active Suspension 1 Active Suspension
Active suspension 1 Active suspension The active suspension and adaptive suspension/semi-active suspension are types of automotive suspensions that controls the vertical movement of the wheels with an onboard system, rather than in passive suspensions where the movement is being determined entirely by the road surface. This technology allows car manufacturers to achieve a greater degree of ride quality and car handling by keeping the tires perpendicular to the road in corners, allowing better traction and control. An onboard computer detects body movement from sensors throughout the vehicle and, using data calculated by opportune control techniques, controls the action of the active and semi-active suspensions. The system virtually eliminates body roll and pitch variation in many driving situations including cornering, accelerating, and braking. Active suspensions can be generally divided into two main classes: pure active suspensions and adaptive/semi-active suspensions. While adaptive suspensions only vary shock absorber firmness to match changing road or dynamic conditions, active suspensions uses some type of actuator to literally raise and lower the chassis independently at each wheel. Manufacturer brand names for adaptive suspensions include Airmatic suspension (Mercedes-Benz), Adaptive Damping, and Road-Sensing Suspension. Active suspensions include Active Body Control (Mercedes-Benz) and Active Roll Stabilization (BMW).[1][2][3][4] For instance, in the 2005 model year, the Mercedes-Benz S55 AMG has the Active Body Control active suspension as standard equipment, while the Mercedes-Benz S430 comes with the Airmatic adaptive suspension and has Active Body Control as an option.[5] According to The Truth About Cars, Active Body Control (ABC) "senses body movement and strangles it at birth. -
Design and Development of Off Road Vehicle Handling by Active Tubular Stabilizer Bar for Enhancing Yaw Stability
Volume 2, Issue 10, October– 2017 International Journal of Innovative Science and Research Technology ISSN No: - 2456 – 2165 Design and Development of Off Road Vehicle Handling by Active Tubular Stabilizer Bar for Enhancing Yaw Stability Vardham Devendra Prasad1, Darahas.V2, Theepalapudi Vihari2, Rupak Sai Nag.V2 1,2Department of Mechanical Engineering, Sathyabama University Email: [email protected],[email protected] Abstract:-The stabilizer bar plays an important role in the automotive vehicle, especially in traction and braking condition. Stabilizer bars (also known as Traction bar, Sway bars or Anti-roll bars) are used to stabilize a vehicles from excessive chassis roll when the vehicle running in high traction conditions. Stabilizer bars are generally used on smooth traction conditions. Anti-roll bars improve cornering behavior by reducing body roll. The aim of the project is to replace “Forged Solid stabilizer rod by using High strength Tubular stabilizer bar” there by reducing the weight of the product and increase the fuel efficiency of the vehicle. The project involves theoretical estimation of torsional stress in the stabilizer bar and validate with finite element analysis and experimental results. I. INTRODUCTION The purpose of a vehicle suspension system can be summarised as follows: To isolate the vehicle from the uncomfortable vibrations transmitted from the road through the tyres and to control the transmitted forces back to the tyres so that the driver can keep the vehicle under control. The fact is that vehicles are often designed for off road conditions. They are designed with a high centre of gravity (CG) due to the Fig.1: Front Suspension of the Vehicle increased ground clearance required.