The Ultimate Silver Metal Clay Firing Guide
Total Page:16
File Type:pdf, Size:1020Kb
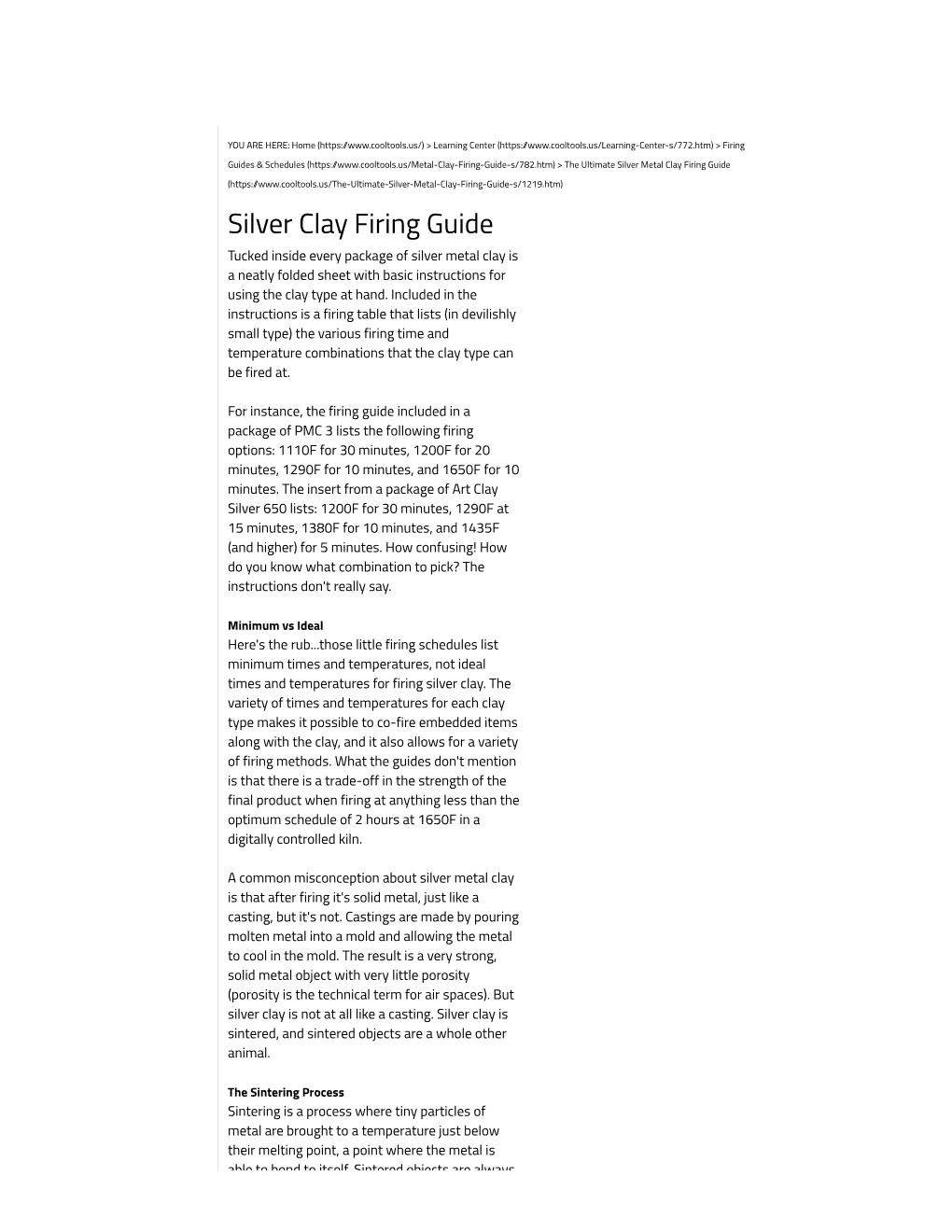
Load more
Recommended publications
-
Tumbaga-Metal Figures from Panama: a Conservation Initiative to Save a Fragile Coll
SPRING 2006 IssuE A PUBLICATION OF THE PEABODY MUSEUM AND THE DEPARTMENT OF ANTHROPOLOGY, HARVARD UNIVERSITY • 11 DIVINITY AVENUE CAMBRIDGE, MA 02138 DIGGING HARVARD YARD No smoking, drinking, glass-break the course, which was ing-what? Far from being a puritani taught by William Fash, cal haven, early Harvard College was a Howells director of the colorful and lively place. The first Peabody Museum, and Harvard students did more than wor Patricia Capone and Diana ship and study: they smoked, drank, Loren, Peabody Museum and broke a lot of windows. None of associate curators. They which was allowed, except on rare were assisted by Molly occasion. In the early days, Native Fierer-Donaldson, graduate American and English youth also stud student in Archaeology, ied, side by side. Archaeological and and Christina Hodge, historical records of early Harvard Peabody Museum senior Students excavating outside Matthews Hall. Photo by Patricia bring to life the experiences of our curatorial assistant and Capor1e. predecessors, teaching us that not only graduate student in is there an untold story to be Archaeology at Boston unearthed, but also, that we may learn University. ALEXANDER MARSHACK new perspectives by reflecting on our Archaeological data recovered from ARCHIVE DONATED TO THE shared history: a history that reaches Harvard Yard enriches our view of the PEABODY MUSEUM beyond the university walls to local seventeenth- through nineteenth-cen Native American communities. tury lives of students and faculty Jiving The Peabody Museum has received the The Fall 2005 course Anthropology in Harvard Yard. In the seventeenth generous donation of the photographs 1130: The Archaeology of Harvard Yard century, Harvard Yard included among and papers of Alexander Marshack brought today's Harvard students liter its four buildings the Old College, the from his widow, Elaine. -
S O C I E T Y O F S O U T H E R N C a L I F O R N
May / June 2019May METALSOCIETY OF SOUTHERN ARTS CALIFORNIA Elise Preiss MASSC Member Spotlight PRESIDENT’S MESSAGE EDITOR’S NOTES Angelina Smith John Lemieux Rose Springtime Greetings! It’s a very exciting time of year for us Metalsmiths as there are so many upcoming events and fun times. I hope everybody had a chance to finish their entries for the 2019 Metals Challenge. The deadline was April 26th, Part of the mission of The Metal so if you didn’t finish in time, you aren’t alone. I didn’t finish either. But I Arts Society of Southern Califor- still can’t wait to see the pieces that did get completed in time. They will nia is promoting our members all be on display at the Metals Challenge Luncheon on June 2nd. Thats’s and work of Southern California right! This year’s Luncheon is JUST AROUND THE CORNER! June 2nd, artists. Of course, we do that 10:00 am - 2:30 pm in Westminster. Be sure to get your tickets. We will here in our newsletter, and I’ll take the opportunity to be announcing the winner of the Nancy Monkman “Jewelry Arts Dream” invite you to be one of our Featured Artists. Just email Scholarship. The Nancy Monkman Estate Sale was well attended, thanks me a couple of photos of your work to everybody who came and purchased things, and bigger thanks to the ( [email protected] ), and I’ll take it from there. folks who spent time helping to sort, price and organize the sale. You can also show us what you are up to on Insta- Very happy to report that we conducted another successful downtown jewelry district tour this year. -
Tarnish Resistance, Corrosion and Stress Corrosion Cracking of Gold Alloys
View metadata, citation and similar papers at core.ac.uk brought to you by CORE provided by Springer - Publisher Connector Tarnish Resistance, Corrosion and Stress Corrosion Cracking of Gold Alloys WS Rapson Tarnishing, corrosion and stress corrosion cracking (SeC) of gold alloys are related phenomena. They present problems when they occur in gold jewellery, dental gold alloys and electronic devices. They are exploited, however, in the depletion gilding and finishing of gold jewellery; and in the extraction, refining and fire assaying of gold. There is still much that is not known about these phenomena, but a coherent picture of their mechanisms is emerging as a result ofstudies of not only gold alloys themselves, but also of other alloys. Aspects ofthis development are discussed. Tammann's extensive studies (1) established that the their metallurgical histories. Thus alloys which are resistance ofgold to tarnish and corrosion is not greatly homogeneous solid solutions and which do not reduced by the addition to it ofsilver and base metals, undergo separation into two immiscible solid phases are so long as the gold content of the resulting alloy is not in general more tarnish and corrosion resistant than below 50 at.%. This corresponds to about 15.6 carat those which are mixtures of two phases. In the latter for Au-Ag alloys and to about 18 carat for Au-Cu case, as exemplified by some nickel white gold alloys, alloys. the one phase may contain too little gold to make it Tammann's observations are of limited corrosion resistant. There is also the possibility of significance, however, when considering the resistance galvanic effects between the separated phases where the to tarnish and corrosion in the three areas in which this compositions of these differ significantly; and the property is of particular significance. -
Corinthian Bronze and the Gold of the Alchemists
View metadata, citation and similar papers at core.ac.uk brought to you by CORE provided by Springer - Publisher Connector Corinthian Bronze and the Gold of the Alchemists DavidM Jacobson The Centre fOr RapidDesign and Manufacture, Buckingham Chilterns University College, High Wycombe, HP11 2JZ, UK Received: 1 July 1999 Alloys that went under the name of Corinthian Bronze were highly prized in the Roman Empire at the beginning of the Christian era, when Corinthian Bronze was used to embellish the great gate of Herod's Temple in Jerusalem. From the ancient texts it emerges that Corinthian Bronze was the name given to a family of copper alloys with gold and silver which were depletion gilded to give them a golden or silver lustre. An important centre of production appears to have been Egypt where, by tradition, alchemy had its origins. From an analysis of the earliest alchemical texts, it is suggested that the concept of transmutation of base metals into gold arose from the depletion gilding process. CORINTHIAN BRONZE AND ITS main constituent because it is classified as bronze (aes IDENTIFICATION in Latin), and is discussed by Pliny in the section of his encyclopaedia dealing with copper and bronze. Ancient texts in Latin, Greek, Hebrew and Syriac refer However, Pliny indicates that their hue varied from to a type of metal called Corinthian Bronze which they golden to silvery, depending on the proportions of the prize above all other copper alloys. The Roman precious metal additions, and it was this lustre that encyclopaedist, Pliny, who lived in the 1st century AD, gave this bronze its attractive appearance. -
Assaying of Gold Jewellery – Choice of Technique DR CHRISTOPHER W
Assaying of gold jewellery – Choice of technique DR CHRISTOPHER W. CORTI World Gold Council, London, E nglan d Introduction A s sa yi n g o f gol d je we lle ry Ancient man first learnt the craft of coin, w hen melt ed, resu lts in the gold plating alloying with the underlying Why assay? metalworking several thousand years Why do we need to assay gold ago, making jew ellery and other base metal with a consequent colour jew ellery in modern times? Why? – decorative artefacts from native gold change. Because gold jewellery is sold on the and copper, well before the Bronze How ever, as well as these rough and ready methods of testing basis of its gold content. We desc ribe and Iron Ages. This native gold jew ellery in terms of its Fineness, in contained silver and other metals as precious metals, the ancient Greeks parts per thousand gold, or Caratage, impu rities, but it did not take long for knew of 3 quantitative methods for where 24 carat represents pure gold. man to deliberately alloy gold w ith assaying gold and silver and all 3 are still in use today: the touchstone, fire In many countries, there are laws that copper to improve properties during govern the actual caratages of the second millennium BC. All this assay and density methods. We will jew ellery that can be sold and the naturally led to the early use of gold examine each of these techniques allowable tolerances on the gold and silver as coinage around the 7th later in terms of their relevance in today’s world. -
Iron, Steel and Swords Script - Page 1 Getting Gold in the Old Times Was Not All That Difficult, Especially If You Had an Unlimited Supply of Slaves
Early Metal Technology 1. Gold Origin, Deposits and Recovery We find gold (Au) more or less on the surface of this planet (let's not get excited about a few miles below the surface here). The same is true for other "heavy" metals like platinum (Pt). This was a big puzzle. There shouldn't be any of that "heavy" stuff around. Why? Well, when this planet was formed some 4 billion years ago, all this heavy stuff was a (small) part of a liquid magma ball consisting mostly of iron and nickel. Gold and other heavy stuff in there did exactly what you would expect: it sunk to the center and stayed there. It's still there - at the very center of the still mostly liquid ball we call earth. Just the surface has solidified by now, forming a kind of thin crust or dross layer on the liquid inside. And that is still mostly iron and nickel. Yes - there is a lot of gold, platinum, and so on, right at the center of the earth. No doubt about this, and no way of getting to it, and no puzzle there. The puzzle is: why was some of the stuff left back on the surface? The answer is: There wasn't anything left back. The original gold is all deep down. The gold and platinum that we find now was deposited later by huge meteorites that crashed onto the already solidified surface of the earth . They struck the planet about 3.9 billion years ago, 200 million years after the earth had formed. -
The Deterioration of Gold Alloys and Some Aspects of Their Conservation Author(S): David A
The Deterioration of Gold Alloys and Some Aspects of Their Conservation Author(s): David A. Scott Source: Studies in Conservation , Nov., 1983, Vol. 28, No. 4 (Nov., 1983), pp. 194-203 Published by: Taylor & Francis, Ltd. on behalf of the International Institute for Conservation of Historic and Artistic Works Stable URL: http://www.jstor.com/stable/1505967 REFERENCES Linked references are available on JSTOR for this article: http://www.jstor.com/stable/1505967?seq=1&cid=pdf- reference#references_tab_contents You may need to log in to JSTOR to access the linked references. JSTOR is a not-for-profit service that helps scholars, researchers, and students discover, use, and build upon a wide range of content in a trusted digital archive. We use information technology and tools to increase productivity and facilitate new forms of scholarship. For more information about JSTOR, please contact [email protected]. Your use of the JSTOR archive indicates your acceptance of the Terms & Conditions of Use, available at https://about.jstor.org/terms Taylor & Francis, Ltd. and International Institute for Conservation of Historic and Artistic Works are collaborating with JSTOR to digitize, preserve and extend access to Studies in Conservation This content downloaded from 128.194.18.45 on Thu, 18 Jun 2020 14:47:09 UTC All use subject to https://about.jstor.org/terms THE DETERIORATION OF GOLD ALLOYS AND SOME ASPECTS OF THEIR CONSERVATION David A. Scott Abstract-The different ways in which gold alloys wide can occurrence, both for the production of coinage deteriorate are described. The principal alloys discussed and for a variety of decorative metalwork [7]. -
Silver and Gold Coating
Copyright © Tarek Kakhia. All rights reserved. http://tarek.kakhia.org Gold & Silver Coatings By A . T . Kakhia 1 Copyright © Tarek Kakhia. All rights reserved. http://tarek.kakhia.org 2 Copyright © Tarek Kakhia. All rights reserved. http://tarek.kakhia.org Part One General Knowledge 3 Copyright © Tarek Kakhia. All rights reserved. http://tarek.kakhia.org 4 Copyright © Tarek Kakhia. All rights reserved. http://tarek.kakhia.org Aqua Regia ( Royal Acid ) Freshly prepared aqua regia is colorless, Freshly prepared aqua but it turns orange within seconds. Here, regia to remove metal fresh aqua regia has been added to these salt deposits. NMR tubes to remove all traces of organic material. Contents 1 Introduction 2 Applications 3 Chemistry 3.1 Dissolving gold 3.2 Dissolving platinum 3.3 Reaction with tin 3.4 Decomposition of aqua regia 4 History 1 - Introduction Aqua regia ( Latin and Ancient Italian , lit. "royal water"), aqua regis ( Latin, lit. "king's water") , or nitro – hydro chloric acid is a highly corrosive mixture of acids, a fuming yellow or red solution. The mixture is formed by freshly mixing concentrated nitric acid and hydro chloric acid , optimally in a volume ratio of 1:3. It was named 5 Copyright © Tarek Kakhia. All rights reserved. http://tarek.kakhia.org so because it can dissolve the so - called royal or noble metals, gold and platinum. However, titanium, iridium, ruthenium, tantalum, osmium, rhodium and a few other metals are capable of with standing its corrosive properties. IUPAC name Nitric acid hydro chloride Other names aqua regia , Nitro hydrochloric acid Molecular formula HNO3 + 3 H Cl Red , yellow or gold Appearance fuming liquid 3 Density 1.01–1.21 g / cm Melting point − 42 °C Boiling point 108 °C Solubility in water miscible in water Vapor pressure 21 mbar 2 – Applications Aqua regia is primarily used to produce chloro auric acid, the electrolyte in the Wohl will process. -
Foil and Leaf Gilding on Cultural Artifacts; Forming and Adhesion E
Revista Matéria, v. 16, n. 1, pp. 540 –559, 2011 ISSN 1517-7076 http://www.materia.coppe.ufrj.br/sarra/artigos/artigo11439 Foil and leaf gilding on cultural artifacts; forming and adhesion E. Darque-Ceretti I, Eric Felder I, Marc Aucouturier II I MINES Paristech-CEMEF, Centre de Mise en Forme des Matériaux, CNRS UMR 7635, BP 207, F-06904 Sophia-Antipolis, France. e-mails: [email protected] ; [email protected] II Centre de Recherche et de Restauration des Musées de France, CNRS UMR 171, Palais du Louvre, porte des Lions, 14 quai François Mitterrand, F-75001 Paris France. e-mail: [email protected] ABSTRACT The process used to obtain foils of more and more thin thickness and coat them on artefacts varied during centuries. It started from thick foils of the first ages mechanically assembled and evolved until the rolled and beaten leaves, a few hundred nanometres thick. This paper will develop, through examples taken from laboratory studies on museum objects, the main evolution steps of gold leaf forming. It will discuss the present knowledge about processes used by hand-workers of different origins and periods: antic Egypt, Roman Empire, western and oriental Middle-Age, South America, modern Europe. A recent mechanical modelling work about gold forming by beating will be exposed. Then will be described, still through recent examples, some of the non-destructive and destructive laboratory methods used to characterise ancient and modern gildings, their composition, thickness and adhesion modes. The different coating process will be discussed, owing to the presently available knowledge. -
Etching Solutions
Etching Solutions This section deals with etching solutions that can be used for archaeological metals. Further details regarding etchants can be found in the literature referred to in Chap. 3. The listing below is therefore very selective and represents the etchants which have been found useful in the experience of the authors. As regards the solvents used in etching solutions, water (H2O) should be distilled water, and ethanol (C2H6O) should be anhydrous (99%) or not less than 95% alco- hol. All chemicals refer to common commercially available concentrated laboratory grade substances and must be handled with care and in accordance to laboratory safety regulations currently in force in the laboratories concerned. The manufactur- ers of these chemicals also provide safety data sheets which can be consulted for further information regarding storage, handling and use. Before etching, ensure that the sample is as scratch-free as possible and that the surface is free of oil, water or ethanol staining, as these will all interfere with the correct etching of the sample. Some samples are liable to be stained on etching due to the presence of different phases, holes or interdendritic porosity. In such cases the sample should be carefully washed in ethanol after etching and dried as thoroughly as possible to prevent excessive staining. Samples can be repolished, cleaned in ethanol and then dried and re-etched. This is often advisable if the finish is less than desired on the final polishing and first etching. For etching the sample can be held in a pair of tongs, of which there are many different types available. -
Depletion Gilding: an Ancient Method for Surface Enrichment of Gold Alloys
Mechanics, Materials Science & Engineering, January 2016 – ISSN 2412-5954 Depletion Gilding: An Ancient Method for Surface Enrichment of Gold Alloys Amelia Carolina Sparavigna 1 – Department of Applied Science and Technology, Politecnico di Torino, Torino, Italy Keywords: Gilding, Depletion Gilding, Gold-Copper Alloys, Tumbaga, Gold-Silver-Copper Alloys, Electrum, Archaeological Artefacts, Gold-Copper nanoparticles, Nanoporous Gold. ABSTRACT. Ancient objects made of noble metal alloys, that is, gold with copper and/or silver, can show the phenomenon of surface enrichment. This phenomenon is regarding the composition of the surface, which has a percentage of gold higher than that of the bulk. This enrichment is obtained by a depletion of the other elements of the alloy, which are, in some manner, removed. This depletion gilding process was used by pre-Columbian populations for their “tumbaga”, a gold-copper alloy, to give it the luster of gold. Introduction: A phenomenon often encountered when ancient objects made of noble metal alloys are analyzed is that of their surface enrichment. Let us consider, for instance, a statuette made of an alloy of gold with copper and/or silver; it can occur that its surface has a percentage of gold higher than that of the bulk. This enrichment can be due to an addition of gold on the surface, or to a depletion process during which the less chemically stable elements leach out causing the surface composition to change. In both cases, the local percentage of gold is increased consequently. Therefore, both processes are gilding processes, the second being known as “depletion gilding”. It happens because a specific depletion process had been applied to the surface of the object or because it had been buried for a rather long time [1] (of course, besides such a slow gilding process, time is causing a long series of damaging and corrosive effects [2]). -
The Conservation of Tumbaga Metals from Panama at the Peabody Museum, Harvard University
Article: The conservation of tumbaga metals from Panama at the Peabody Museum, Harvard University Author(s): Scott Fulton and Sylvia Keochakian Source: Objects Specialty Group Postprints, Volume Twelve, 2005 Pages: 76-90 Compilers: Virginia Greene and Patricia Griffin th © 2005 by The American Institute for Conservation of Historic & Artistic Works, 1156 15 Street NW, Suite 320, Washington, DC 20005. (202) 452-9545 www.conservation-us.org Under a licensing agreement, individual authors retain copyright to their work and extend publications rights to the American Institute for Conservation. Objects Specialty Group Postprints is published annually by the Objects Specialty Group (OSG) of the American Institute for Conservation of Historic & Artistic Works (AIC). A membership benefit of the Objects Specialty Group, Objects Specialty Group Postprints is mainly comprised of papers presented at OSG sessions at AIC Annual Meetings and is intended to inform and educate conservation-related disciplines. Papers presented in Objects Specialty Group Postprints, Volume Twelve, 2005 have been edited for clarity and content but have not undergone a formal process of peer review. This publication is primarily intended for the members of the Objects Specialty Group of the American Institute for Conservation of Historic & Artistic Works. Responsibility for the methods and materials described herein rests solely with the authors, whose articles should not be considered official statements of the OSG or the AIC. The OSG is an approved division of the AIC but does not necessarily represent the AIC policy or opinions. AIC Objects Specialty Group Postprints, Volume 12, 2005 THE CONSERVATION OF TUMBAGA METALS FROM PANAMA AT THE PEABODY MUSEUM, HARVARD UNIVERSITY Scott Fulton and Sylvia Keochakian Abstract A grant awarded by the Institute for Museum and Library Services (IMLS) made possible a major conservation initiative for an important but very fragile group of tumbaga (gold/copper alloy) figurines from Veraguas, Panama (ca.1300-1500 A.D.).