A Review of Stress Corrosion Cracking/Fatigue Modeling for Light Water Reactor Cooling System Components
Total Page:16
File Type:pdf, Size:1020Kb
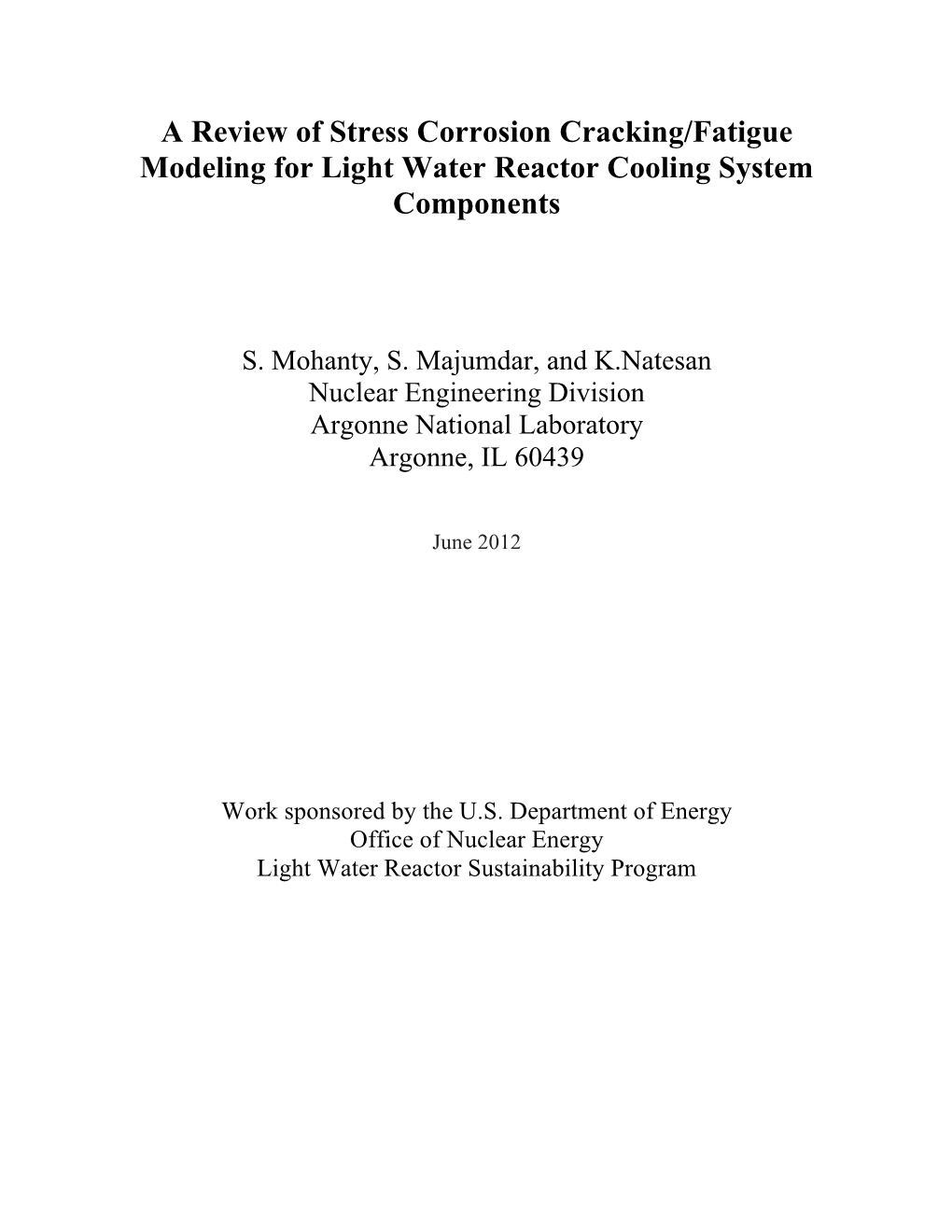
Load more
Recommended publications
-
10-1 CHAPTER 10 DEFORMATION 10.1 Stress-Strain Diagrams And
EN380 Naval Materials Science and Engineering Course Notes, U.S. Naval Academy CHAPTER 10 DEFORMATION 10.1 Stress-Strain Diagrams and Material Behavior 10.2 Material Characteristics 10.3 Elastic-Plastic Response of Metals 10.4 True stress and strain measures 10.5 Yielding of a Ductile Metal under a General Stress State - Mises Yield Condition. 10.6 Maximum shear stress condition 10.7 Creep Consider the bar in figure 1 subjected to a simple tension loading F. Figure 1: Bar in Tension Engineering Stress () is the quotient of load (F) and area (A). The units of stress are normally pounds per square inch (psi). = F A where: is the stress (psi) F is the force that is loading the object (lb) A is the cross sectional area of the object (in2) When stress is applied to a material, the material will deform. Elongation is defined as the difference between loaded and unloaded length ∆푙 = L - Lo where: ∆푙 is the elongation (ft) L is the loaded length of the cable (ft) Lo is the unloaded (original) length of the cable (ft) 10-1 EN380 Naval Materials Science and Engineering Course Notes, U.S. Naval Academy Strain is the concept used to compare the elongation of a material to its original, undeformed length. Strain () is the quotient of elongation (e) and original length (L0). Engineering Strain has no units but is often given the units of in/in or ft/ft. ∆푙 휀 = 퐿 where: is the strain in the cable (ft/ft) ∆푙 is the elongation (ft) Lo is the unloaded (original) length of the cable (ft) Example Find the strain in a 75 foot cable experiencing an elongation of one inch. -
Corrosion Fatigue: Type 304 Stainless Steel in Acid-Chloride and Implant Metals in Biological Fluid
76-9939 BOWERS, Davtd Francis, 1937- CORROSION FATIGUE: TYPE 304 STAINLESS STEEL IN ACID-CHLORIDE AND IMPLANT METALS IN BIOLOGICAL FLUID. The Ohio State University, Ph.D., 1975 Engineering, metallurgy Xerox University Microfilms, Ann Arbor, Michigan 48ioe CORROSION FATIGUE: TYPE 304 STAINLESS STEEL IN ACID-CHLORIDE AND IMPLANT METALS IN BIOLOGICAL FLUID Dissertation Presented in Partial Fulfillment of the Requirements for the Degree Doctor of Philosophy in the Graduate School of The Ohio State University by David Francis Bowers, B.S., M.S. Metallurgical Engineering The Ohio State University 1975 Approved by (dviser Department of Metallurgical Engineering Reading Committee: Dr. Mars G. Fontana Dr. Frank Beck Dr. John P. Hirth To My Wife and Daughter TABLE OF CONTENTS Page ACKNOWLEDGEMENTS.......................................... iv VITA........................................................ vi LIST OF TABLES............................................. viii LIST OF FIGURES... ...................... x INTRODUCTION.................. .. ......................... 1 I. LITERATURE SURVEY..................... 4 1.1 Concepts and Theory of Fatigue Crack Growth.. 4 1.2 Fracture Mechanics Approach to Crack Growth in Engineering Structures..................... 18 1.3 Effect of Microstructure on Fatigue Cracking Growth................................ 24 1.4 Mechanical Variables in Corrosion Fatigue.... 41 1.5 Environmental Interaction with Fatigue Crack Growth.................................... 59 II. EXPERIMENTAL DETAILS............................... -
Top Performance When the Going Gets Tough
Top performance when the going gets tough The Alfa Laval DuroShell plate-and-shell heat exchanger Sub-headline coming soon DuroShell – plate-and-shell made tougher Alfa Laval DuroShell is a specially engineered plate-and-shell heat exchanger ideal for demanding duties and corrosive media. Able to withstand fatigue even at high temperatures and pressures, it outperforms not only traditional heat exchangers, but also other plate-and-shells. As flexible as it is strong DuroShell creates new possibilities through its com- pactness, efficiency and exceptional resistance to fatigue. Able to work with liquids, gases and two- phase mixtures, it stands out among heat exchangers in its duty range. DuroShell handles pressures up to 100 barg (1450 psig) in compliance with PED and ASME, and temperatures as high as 450 °C (842 °F). Built for your application DuroShell is fully welded and gasket-free, with internal features that make it still more robust. Plates are avail- able in 316L stainless steel, while the pressure vessel itself can be built in 316L stainless steel or carbon steel. Three different sizes are possible, with heat transfer surfaces ranging 2–235 m2 (21.5–2530 ft 2) in area. DuroShell RollerCoaster Robust and efficient performance. DuroShell PowerPack Optimized flow distribution and fatigue resistance. Learn more at www.alfalaval.com/duroshell Plate-and-shell benefits made better • More uptime and longer life due to • Installation savings through even greater fatigue resistance more compact, lightweight design • Higher operating pressures thanks • Greater reliability as a result of to robust, patented construction closed, fully welded construction • Operational gains created by 15–20 % higher thermal efficiency How it works Revolutionary technology Optimized flow DuroShell is a plate-and-shell heat exchanger, but one DuroShell operates with one media on the plate side with a unique internal design. -
Corrosion-Fatigue Evaluation of Uncoated Weathering Steel Bridges
applied sciences Article Corrosion-Fatigue Evaluation of Uncoated Weathering Steel Bridges Yu Zhang, Kaifeng Zheng, Junlin Heng * and Jin Zhu Department of Bridge Engineering, School of Civil Engineering, Southwest Jiaotong University, Chengdu 610031, China * Correspondence: [email protected]; Tel.: +86-182-8017-6652 Received: 19 July 2019; Accepted: 19 August 2019; Published: 22 August 2019 Featured Application: The new findings highlight the enhancement in corrosion-fatigue performance of steel bridges by using the uncoated weathering steel. Besides, an innovative approach has been established to simulate the corrosion-fatigue process in uncoated weathering steel bridges, providing deep insights into the service life of the bridges. The approaches suggested in the article can be used (not limited to) as a reference for the research and design of uncoated weathering steel bridges. Abstract: Uncoated weathering steel (UWS) bridges have been extensively used to reduce the lifecycle cost since they are maintenance-free and eco-friendly. However, the fatigue issue becomes significant in UWS bridges due to the intended corrosion process utilized to form the corrodent-proof rust layer instead of the coating process. In this paper, an innovative model is proposed to simulate the corrosion-fatigue (C-F) process in UWS bridges. Generally, the C-F process could be considered as two relatively independent stages in a time series, including the pitting process of flaw-initiation and the fatigue crack propagation of the critical pitting flaw. In the proposed C-F model, Faraday’s law has been employed at the critical flaw-initiation stage to describe the pitting process, in which the pitting current is applied to reflect the pitting rate in different corrosive environments. -
Fatigue Overview Introduction to Fatigue Analysis
Fatigue overview Introduction to fatigue analysis • Fatigue is the failure of a component after several repetitive load cycles. • As a one-time occurrence, the load is not dangerous in itself. Over time the alternating load is able to break the structure anyway. • It is estimated that between 50 and 90 % of product failures is caused by fatigue, and based on this fact, fatigue evaluation should be a part of all product development. What is fatigue? In materials science, fatigue is the progressive and localized structural damage that occurs when a material is subjected to cyclic loading (material is stressed repeatedly). Clients tous différents Routes de qualités variables Contraintes Fatigue Design in Automotive Industry Conception fiable PSA (Peugeot Citroën) Résistances 3s 3s Dispersion matériau Dispersion de production Fatigue • Fracture mechanics can be divided into three stages: 1. Crack nucleation 2. Crack-growth 3. Ultimate ductile failure Introduction to fatigue analysis • Fatigue is the failure of a component after several repetitive load cycles. • As a one-time occurrence, the load is not dangerous in itself. Over time the alternating load is able to break the structure anyway. • It is estimated that between 50 and 90 % of product failures is caused by fatigue, and based on this fact, fatigue evaluation should be a part of all product development. Historical background • In comparison to the classical stress analysis, fatigue theory is a relative new phenomenon. The need to understand fatigue arose after the industrial revolution introduced steel structures. Three areas were particularly involved in early failures: Railway trains, Mining equipment and Bridges. Historical background • 1837: Wilhelm Albert publishes the first article on fatigue. -
Engineering Viscoelasticity
ENGINEERING VISCOELASTICITY David Roylance Department of Materials Science and Engineering Massachusetts Institute of Technology Cambridge, MA 02139 October 24, 2001 1 Introduction This document is intended to outline an important aspect of the mechanical response of polymers and polymer-matrix composites: the field of linear viscoelasticity. The topics included here are aimed at providing an instructional introduction to this large and elegant subject, and should not be taken as a thorough or comprehensive treatment. The references appearing either as footnotes to the text or listed separately at the end of the notes should be consulted for more thorough coverage. Viscoelastic response is often used as a probe in polymer science, since it is sensitive to the material’s chemistry and microstructure. The concepts and techniques presented here are important for this purpose, but the principal objective of this document is to demonstrate how linear viscoelasticity can be incorporated into the general theory of mechanics of materials, so that structures containing viscoelastic components can be designed and analyzed. While not all polymers are viscoelastic to any important practical extent, and even fewer are linearly viscoelastic1, this theory provides a usable engineering approximation for many applications in polymer and composites engineering. Even in instances requiring more elaborate treatments, the linear viscoelastic theory is a useful starting point. 2 Molecular Mechanisms When subjected to an applied stress, polymers may deform by either or both of two fundamen- tally different atomistic mechanisms. The lengths and angles of the chemical bonds connecting the atoms may distort, moving the atoms to new positions of greater internal energy. -
Corrosion Fatigue of Austenitic Stainless Steels for Nuclear Power Engineering
metals Article Corrosion Fatigue of Austenitic Stainless Steels for Nuclear Power Engineering Irena Vlˇcková 1,*, Petr Jonšta 2, ZdenˇekJonšta 2, Petra Vá ˇnová 2 and Tat’ána Kulová 2 1 RMTSC, Material & Metallurgical Research Ltd., Remote Site Ostrava, VÚHŽ a.s., Dobrá 739 51, Czech Republic 2 Department of Materials Engineering, VŠB-Technical University of Ostrava, Ostrava 708 33, Czech Republic; [email protected] (P.J.); [email protected] (Z.J.); [email protected] (P.V.); [email protected] (T.K.) * Correspondence: [email protected]; Tel.: +420-558601257 Academic Editor: Hugo F. Lopez Received: 21 September 2016; Accepted: 8 December 2016; Published: 16 December 2016 Abstract: Significant structural steels for nuclear power engineering are chromium-nickel austenitic stainless steels. The presented paper evaluates the kinetics of the fatigue crack growth of AISI 304L and AISI 316L stainless steels in air and in corrosive environments of 3.5% aqueous NaCl solution after the application of solution annealing, stabilizing annealing, and sensitization annealing. Comparisons were made between the fatigue crack growth rate after each heat treatment regime, and a comparison between the fatigue crack growth rate in both types of steels was made. For individual heat treatment regimes, the possibility of the development of intergranular corrosion was also considered. Evaluations resulted in very favourable corrosion fatigue characteristics of the 316L steel. After application of solution and stabilizing annealing at a comparable DK level, the fatigue crack growth rate was about one half compared to 304L steel. After sensitization annealing of 316L steel, compared to stabilizing annealing, the increase of crack growth rate during corrosion fatigue was slightly higher. -
Design for Cyclic Loading, Soderberg, Goodman and Modified Goodman's Equation
Design for Cyclic Loading 1. Completely reversing cyclic stress and endurance strength A purely reversing or cyclic stress means when the stress alternates between equal positive and Pure cyclic stress negative peak stresses sinusoidally during each 300 cycle of operation, as shown. In this diagram the stress varies with time between +250 MPa 200 to -250MPa. This kind of cyclic stress is 100 developed in many rotating machine parts that 0 are carrying a constant bending load. -100 When a part is subjected cyclic stress, Stress (MPa) also known as range or reversing stress (Sr), it -200 has been observed that the failure of the part -300 occurs after a number of stress reversals (N) time even it the magnitude of Sr is below the material’s yield strength. Generally, higher the value of Sr, lesser N is needed for failure. No. of Cyclic stress stress (Sr) reversals for failure (N) psi 1000 81000 2000 75465 4000 70307 8000 65501 16000 61024 32000 56853 64000 52967 96000 50818 144000 48757 216000 46779 324000 44881 486000 43060 729000 41313 1000000 40000 For a typical material, the table and the graph above (S-N curve) show the relationship between the magnitudes Sr and the number of stress reversals (N) before failure of the part. For example, if the part were subjected to Sr= 81,000 psi, then it would fail after N=1000 stress reversals. If the same part is subjected to Sr = 61,024 psi, then it can survive up to N=16,000 reversals, and so on. Sengupta MET 301: Design for Cyclic Loading 1 of 7 It has been observed that for most of engineering materials, the rate of reduction of Sr becomes negligible near the vicinity of N = 106 and the slope of the S-N curve becomes more or less horizontal. -
Oversimplified Viscoelasticity
Oversimplified Viscoelasticity THE MAXWELL MODEL At time t = 0, suddenly deform to constant displacement Xo. The force F is the same in the spring and the dashpot. F = KeXe = Kv(dXv/dt) (1-20) Xe is the displacement of the spring Xv is the displacement of the dashpot Ke is the linear spring constant (ratio of force and displacement, units N/m) Kv is the linear dashpot constant (ratio of force and velocity, units Ns/m) The total displacement Xo is the sum of the two displacements (Xo is independent of time) Xo = Xe + Xv (1-21) 1 Oversimplified Viscoelasticity THE MAXWELL MODEL (p. 2) Thus: Ke(Xo − Xv) = Kv(dXv/dt) with B. C. Xv = 0 at t = 0 (1-22) (Ke/Kv)dt = dXv/(Xo − Xv) Integrate: (Ke/Kv)t = − ln(Xo − Xv) + C Apply B. C.: Xv = 0 at t = 0 means C = ln(Xo) −(Ke/Kv)t = ln[(Xo − Xv)/Xo] (Xo − Xv)/Xo = exp(−Ket/Kv) Thus: F (t) = KeXo exp(−Ket/Kv) (1-23) The force from our constant stretch experiment decays exponentially with time in the Maxwell Model. The relaxation time is λ ≡ Kv/Ke (units s) The force drops to 1/e of its initial value at the relaxation time λ. Initially the force is F (0) = KeXo, the force in the spring, but eventually the force decays to zero F (∞) = 0. 2 Oversimplified Viscoelasticity THE MAXWELL MODEL (p. 3) Constant Area A means stress σ(t) = F (t)/A σ(0) ≡ σ0 = KeXo/A Maxwell Model Stress Relaxation: σ(t) = σ0 exp(−t/λ) Figure 1: Stress Relaxation of a Maxwell Element 3 Oversimplified Viscoelasticity THE MAXWELL MODEL (p. -
Creep-Fatigue Interaction Cumulative Damage
r ^«M!«je^. ^\~*t. re» .• «J^* -•^*'*5i "^' ^•-^^•fB^^^^'C^- '•'• "^ ORNL-4757 '•«* CREEP-FATIGUE INTERACTION and CUMULATIVE DAMAGE EVALUATIONS for TYPE 304 STAINLESS STEEL Hold-Time Fatigue Test Program and Review of Multiaxial Fatigue E. P. Esztergar BLANK PAGE Printed in the United States of America. Available from National Technical Information Service US. Department of Commerce 5285 Port Royal Road. Springfield. Virginia 22151 Price: Printed Copy $3.00; Microfiche $0.95 This report was prepared as an account of work sponsored by the United States Government. Neither the United States nor the United States Atomic Energy Commission, nor any of their employees, nor any of their contractors, subcontractors, or their employees, makes any warranty, express or impliad, or assumes any legal liability or responsibility for the accuracy, completeness or usefulness of any information, apparatus, product or process drsdosed. or leuiesenu that its use would not infringe privately owned rights. 0RHL-VT5T UC-60 — Reactor Technology Contract No. W-74Q5-eng-26 Reactor Division CHEEP-FATIGUE IHTERACTIOH AM) CUMULATIVE BAM/UJE EVALUATIOHS FOR TYPE 304 STAIHEESS STEEL Hold-Tine Fatigue Test Program and Review of MultlaxLal Fatigue E. P. Esztergar NOTICE— Consultant JUNE 1972 OAK RIDGE HATIOHAL LABORATORY Oak Ridge, Tennessee 37830 operated by UKOH CAREER CORPORATIOH for the U.S. ATOMIC EHERGY COMMISSIOR tmawmm of nw Mctmnr n mumm iii CONTENTS Page PREFACE . v ACKNOWLEDGMENTS vii ABSTRACT 1 1. INTRODUCTION 2 2. BACKGROUND k 2.1 Review of Time Effects on Fatigue Behavior k Strain rate k Cyclic relaxation U Cyclic creep 9 2.2 Basis for High-Temperature Design Procedures 10 The t-n diagram 12 Continuous-cycle fatigue data 15 Cyclic-relaxation data 18 Cyclic-creep data 21 3. -
The Environmental Effect on Corrosion Fatigue Behavior of Austenitic Stainless Steels
The Environmental Effect on Corrosion Fatigue Behavior of Austenitic Stainless Steels by Lun Yu B.S. Nuclear Engineering (2013) Shanghai Jiao Tong University SUBMITTED TO THE DEPARTMENT OF NUCLEAR SCIENCE AND ENGINEERING IN PARTIAL FULFILLMENT OF THE REQUIREMENTS FOR THE DEGREE OF DOCTOR OF PHILOSOPHY IN NUCLEAR SCIENCE AND ENGINEERING AT THE MASSACHUSETTS INSTITUTE OF TECHNOLOGY September, 2017 © 2017 Massachusetts Institute of Technology. All rights reserved. Signature of Author: _____________________________________________________________ Lun Yu Department of Nuclear Science and Engineering August 25, 2017 Certified by: __________________________________________________________________ Ronald G. Ballinger Professor of Nuclear Science and Engineering, Materials Science and Engineering Thesis Supervisor Certified by: ___________________________________________________________________ Michael P. Short Assistant Professor of Nuclear Science and Engineering Thesis Reader Accepted by: ___________________________________________________________________ Ju Li Battelle Energy Alliance Professor of Nuclear Science and Engineering, Professor of Materials Science and Engineering Chair, Department Committee on Graduate Students This page was left blank intentionally The Environmental Effect on Corrosion Fatigue Behavior of Austenitic Stainless Steels by Lun Yu Submitted to the Department of Nuclear Science and Engineering on September 1, 2017 in Partial Fulfillment of the Requirements for the Degree of Doctor of Philosophy in Nuclear Science and -
Very High Cycle Fatigue of Engineering Materials
Faculty of Technology and Science Materials Engineering Vitaliy Kazymyrovych Very high cycle fatigue of engineering materials (A literature review) Karlstad University Studies 2009:22 Vitaliy Kazymyrovych Very high cycle fatigue of engineering materials (A literature review) Karlstad University Studies 2009:22 Vitaliy Kazymyrovych. Very high cycle fatigue of engineering materials - A literature review Research Report Karlstad University Studies 2009:22 ISSN 1403-8099 ISBN 978-91-7063-246-4 © The Author Distribution: Faculty of Technology and Science Materials Engineering SE-651 88 Karlstad +46 54 700 10 00 www.kau.se Printed at: Universitetstryckeriet, Karlstad 2009 Very high cycle fatigue of engineering materials (A literature review) V.Kazymyrovych* Department of Materials Engineering, Karlstad University SE-651 88, Sweden * Email address: [email protected] Abstract This paper examines the development and present status of the Very High Cycle Fatigue (VHCF) phenomenon in engineering materials. The concept of ultrasonic fatigue testing is described in light of its historical appearance covering the main principles and equipment variations. The VHCF behaviour of the most important materials used for very long life applications is presented, with particular attention paid to steels. In section 3 the VHCF properties of titanium-, nickel-, aluminium- and magnesium alloys are described. Furthermore, the typical fatigue behaviour and mechanisms of pure metals are presented. Section 4 examines the VHCF properties of various types of steels e.g. low carbon steel, spring steel, stainless steel, bearing steel as well as tool steel. In addition to this, the main material defects that initiate VHCF failure are examined in this study. Furthermore, the different stages characteristic for fatigue crack development in VHCF are described in section 5 in terms of relative importance and sequence.