ABSTRACT CARCATERRA, BRIAN THOMAS. Investigation of Energy
Total Page:16
File Type:pdf, Size:1020Kb
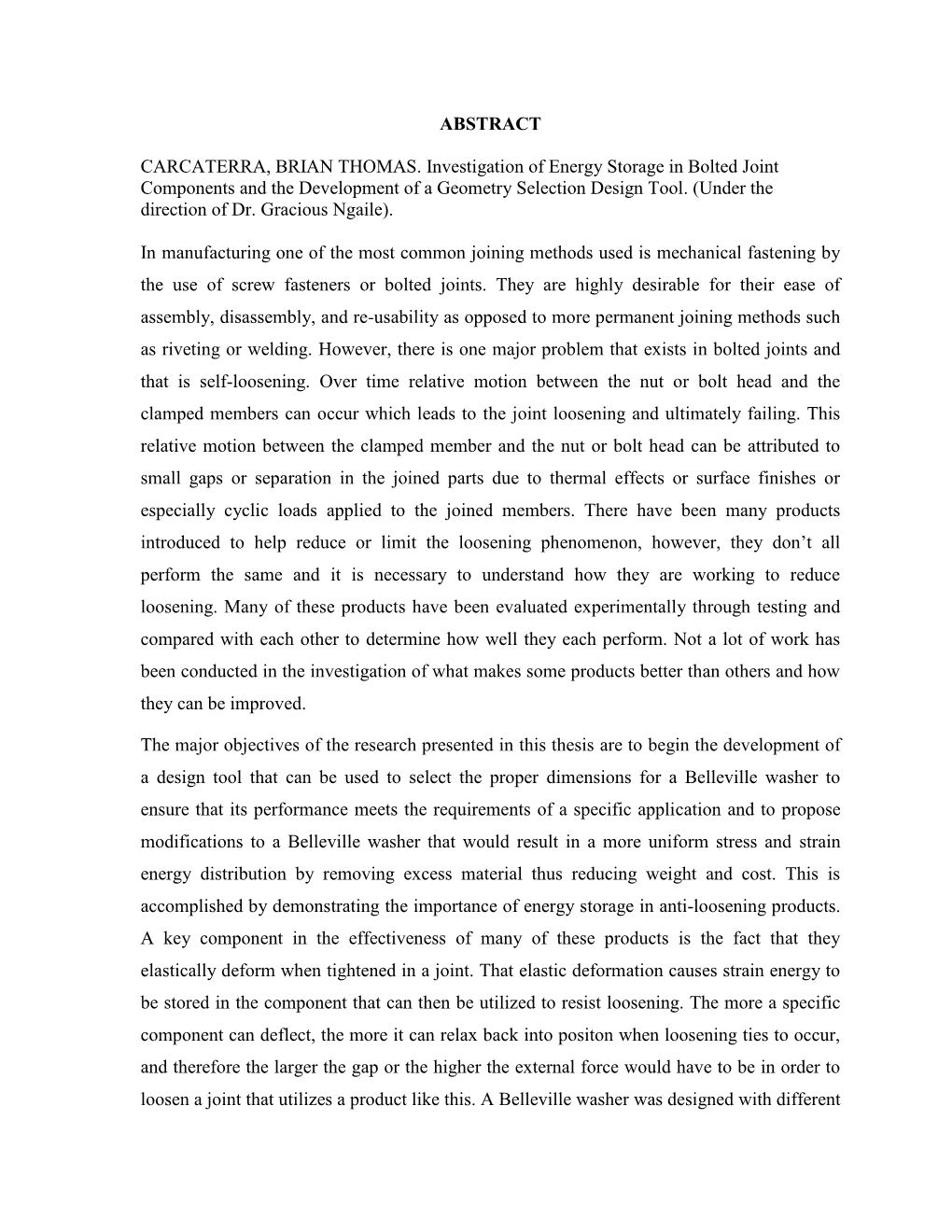
Load more
Recommended publications
-
[email protected]
BOLTING Basics, Tips & Best Practices g... urin Feat SmartBolts® Direct Tension Indicating Fasteners™ Address: 202 Perry Parkway, Suite 7 Gaithersburg, MD 20877 United States Phone: +1 (240) 631-7246 Fax: +1 (240) 750-6025 Email: [email protected] URL: www.smartbolts.com www.stressindicators.com Stress Indicators Incorporated is a solutions-driven engineering and manufacturing firm based in Maryland, USA. Formed in 1992, we provide innovative Visual Indication Systems™ solutions for customers worldwide. Stress Indicators Incorporated invented and developed SmartBolts® technology and commercialized the products to enable broad industry acceptance. All SmartBolts® are manufactured from quality fasteners at our USA facility. Disclaimer While we try to make sure that all data/information posted in this report is accurate at all times, we are not responsible for typographical and other errors that may appear. Data/Information is subject to change without notice. Stress Indicators assumes no responsibility or liability for any damages incurred directly or indirectly as a result of any data errors, omissions, or discrepancies. BOLTING Basics, Tips & Best Practices Table of Contents Introduction ................................................................................................................................................. 4 Part One: Basics of Specifying a Bolt Step One: Specifying the Basics of a Fastener .......................................................................................... 6 Selecting a Head Type ............................................................................................................................. -
LIO-360-B1G6 Engine Maintenance Manual Lycoming Part Number: MM-LIO-360-B1G6
Engine Maintenance Manual (Principal Manual) LIO-360-B1G6 Engine September 2017 Part No. MM-LIO-360-B1G6 © 2017 Avco Corporation. All Rights Reserved. LIO-360-B1G6 Engine Maintenance Manual Lycoming Part Number: MM-LIO-360-B1G6 Contact Us: Mailing Address: Lycoming Engines 652 Oliver Street Williamsport, PA 17701 USA Phone: U.S. and Canada Toll Free: +1 (800) 258-3279 Factory Direct: +1 (570) 323-6181 Technical Support Hotline • +1 (877) 839-7878 (Toll Free) • +1 (570) 327-7222 Lycoming’s regular business hours are Monday through Friday from 8:00AM through 5:00PM Eastern Time (-5 GMT). Visit us Online: www.Lycoming.com LIO-360-B1G6 Engine Maintenance Manual RECORD OF REVISIONS Revision Revised Revision Date By Revision Description Original Original Release of Maintenance Manual - Part No. MM-LIO-360-B1G6 © 2017 Avco Corporation. All Rights Reserved Record of Revisions September 2017 Page i LIO-360-B1G6 Engine Maintenance Manual This page intentionally left blank. Record of Revisions © 2017 Avco Corporation. All Rights Reserved Page ii September 2017 LIO-360-B1G6 Engine Maintenance Manual SERVICE DOCUMENT LIST NOTICE: The following is a list of service documents referenced in or incorporated into the information in this manual. Always refer to the latest revision of any service document (including any supplements) for changes or additional information. Number Incorporation Subject Date S.B. 201 09/17 Inspection of Crankshaft Flange S.B. 240 09/17 Mandatory Parts Replacement at Overhaul and During Repair or Maintenance S.B. 342 09/17 Fuel Line (Stainless Steel Tube Assy.) and Support Clamp Inspection and Installation S.B. -
PDF Product List
STRUCTURAL BOLTS MACHINE BOLTS NUTS A325 Screw Only, A193 B7 Heavy Hex Head Bolt Acorn (Cap) Nut Domestic & Import A307A Breakaway Bolt Allen Nut A325 Bolt with Nut A307B Heavy Head Bolt Cap (Acorn) Nut A325 Type 3 Bolt, Domestic F1554 Hex Machine Bolt Castle Nut A325 Interference Body Bolt (Grades 36, 55, & 105) Coupling Nut Canadian A325 Bolt w/DH Nut, Square Head Machine Bolt Coupling Nut, Reducer Hot Dip Galvanized Coupling Nut, Heavy Duty A490 Screw Only, BOLTS & SCREWS Hex Nut Domestic & Import Carriage Bolt Hex Nut, Left Hand TC A325 Assembly, Countersunk Bolt Hex Nut, Heavy Grade 4 Domestic& Import Counterbore Screw, 12 Point Hex Nut, Heavy, Grade 7 TC A490 Assembly, Elevator Bolt Hvy Double Recess Guardrail Nut Domestic & Import Flange Bolt Jack Nut Flat Head Bolt, Slotted Jam Nut STRUCTURAL NUTS Guardrail Bolt Jam Nut, Left Hand A194 2H Nut, Domestic Hanger Bolt Flange Nut A194 2H Nut, Import Lag Screw High Nut A563 Grade DH Heavy Nut, Lag Screw, 1-Way Truss Head Knurled Nut Domestic Lag Screw, Indented HWH Machine Screw Nut, Hex A563 DH Type 3 Nut Full Thread Machine Screw Nut, Small Pattern ANCO Heavy Hex Locknut Lag Screw, Square Head Machine Screw Nut, Square ANCO Finished Locknut Penta Head Bolt Palnut ANCO 2H Heavy Locknut Place Bolt Panel Nut ANCO A325 Locknut Plow Bolt, Grade 2 Slotted Nut Plow Bolt, Grade 5 Slotted Nut, Heavy STRUCTURAL WASHERS Plow Bolt, Grade 8 Square Nut F436 Hardened Washer Shaker Screen Bolt, Grade 5 Square Nut, Heavy Domestic & Import Shackle Bolt Tee Nut F436 Type 3 Washer Security Bolt Wing -
Threaded Fasteners
Threaded Fasteners Introduction If you are designing and building a Formula SAE vehicle, threaded fasteners will likely be used to join the various components and systems together and allow the vehicle to function as a unified machine. The reliability of your vehicle is key to realize your potential at the competition. Even though threaded fasteners have been in use for hundreds of years and are in products that we use every day, their performance is dependent on a wide range of factors. This chapter covers some of the main factors that can influence reliability and is intended as an aid in joint design, fastener selection, and installation. The first portion of this chapter covers several design and installation factors that can work together to improve the reliability of your vehicle’s bolted joints. These topics include, the importance of generating and maintaining clamp load, and how clamp load, along with joint stiffness, can work together to prevent self-loosening and improve fatigue performance. The second portion of this chapter reviews how installation method and torque are related to clamp load, and also includes a comparison between common fastener types to aid in selection. The chapter concludes with a short tutorial showing how to obtain Mil Spec information on fasteners and similar hardware. Disclaimer – Multiple factors on each component in a bolted joint affect its performance. Additionally, service requirements for every joint differ. Each joint must be evaluated and tested for its ability to perform the desired function. The information in this chapter provides general background and does not represent how a specific design or piece of hardware will perform. -
Maclean ESNA's Catalog
611 COUNTRY CLUB ROAD POCAHONTAS, ARKANSAS 72445 SALES: 1-(800)-331-6469 FAX: 1-(870)-892-8938 WWW.MACLEANFOGGCS.COM 1 The ESNA® story began in 1927, when a young engineer named Carl Arthur Swanstrom came to this country from Sweden. He brought with him a license to manufacture and sell a unique new self-locking fastener. The Inventor called the new fastener an “Elastic Stop® nut” because the nut remained “stopped” anywhere along the bolt threads. A non-damaging insert, fitted into the top of the nut, gripped the bolt threads firmly, holding the nut in position without seating against the work or using secondary locking devices. The only problem with the new nut was the inability to mass-produce them. The next few years were spent perfecting an automatic assembly machine to insert the locking device into the top of the nut. Swanstrom perfected the machine in the early 1930s and only four years later the Elastic Stop® Nut Corporation of America was founded. A threaded fastener, able to positively resist the loosening effect of vibration, had long been sought by manufacturers of every type of equipment. The Elastic Stop® nut proved to be the answer — totally reliable, able to reduce maintenance costs and prevent equipment failure. The outstanding performance of the Elastic Stop® nut was further substantiated in 1943 when the Air Force tested and issued the first approval letter to use ESNA® fasteners on military aircraft, both fuselage and engines. During WWII billions of Elastic Stop® nuts were produced for every branch of the armed services. -
Bus and Coach Rear Drive Axles Revised 06-16
Maintenance Manual 23A Bus and Coach Rear Drive Axles Revised 06-16 59000 Series 61000 Series 71000 and 79000 Series RC-26-700 Series Service Notes About This Manual How to Obtain Additional Maintenance, This manual provides maintenance and service information for the Service and Product Information Meritor 59000, 61000, 71000, 79000, RC-23-160 and Visit Literature on Demand at meritor.com to access and order RC-26-700 Series bus and coach rear drive and center axles and T additional information. Series parking brake. Contact the Meritor OnTrac™ Customer Call Center at Before You Begin 866-668-7221 (United States and Canada); 001-800-889-1834 (Mexico); or email [email protected]. 1. Read and understand all instructions and procedures before you begin to service components. If Tools and Supplies are Specified in 2. Read and observe all Warning and Caution hazard alert This Manual messages in this publication. They provide information that can Contact Meritor’s Commercial Vehicle Aftermarket at help prevent serious personal injury, damage to components, 888-725-9355. or both. 3. Follow your company’s maintenance and service, installation, Kiene Diesel Accessories, Inc., 325 S. Fairbanks Street, Addison, IL 60101. Call the company’s customer service center at and diagnostics guidelines. 800-264-5950, or visit their website at kienediesel.com. 4. Use special tools when required to help avoid serious personal injury and damage to components. SPX/OTC Service Solutions, 655 Eisenhower Drive, Owatonna, MN 55060. Call the company’s customer service center at Hazard Alert Messages and Torque 800-533-6128, or visit their website at otctools.com. -
ABS Fastener Catalog
ABS FASTENERS OFFERS A COMPLETE LINE OF COMMERCIAL STANDARDS AND SPECIALS. We are your premier source for commercial grade fasteners, nuts, bolts, screws, and hard- ware. For more than 60 years, ABS has set the standard for quality, value-added services, and superior customer service. From our seven ABS warehouses strategically located across the USA and Mexico stocking several million in inventory, we are uniquely poised to serve your fastener and hardware needs for manufacturing and assembly. 4 ...........Anchors 20 .........Custom Fasteners & Hardware 5 ...........Bits 21 .........Value Added Services 6-7 ........Bolts 22 .........Quick Fastener Reference 8-9 ........Nuts 23 .........Heads, Threads, and Drive Styles 10 .........Washers 24 .........Thread Pitch Guide 11 .........Socket Products 25 .........Material Reference 12 .........Machine Screws 26 .........Plating Reference 13 .........Wood Screws 27 .........Painting Services 14 .........Construction Screws 28 .........Staple Reference 15 .........Self Drilling Screws 29 .........Nail Reference 16-17 ...Sheet Metal Screws 30 .........Hardware Off ering 18 .........Nails & Rivets 29 .........ABS Locations & Contact Info 19 .........Pins & Miscellaneous Items © 2017 American Bolt & Screw. All Rights Reserved. Reproducing or copying any part of this catalog without permission is unlawful under the United States Copyright Act. Violaters are subject to full prosecution under federal law. We hold industry together... You are not anchored to other suppliers! We have the anchors you need for light or heavy jobs. Conical Plastic Anchors E-Z Anchors Toggle Bolts Light-duty wall anchor used with a sheet metal or wood Pre-drills own hole in gympsum wallboard.Replaces A machine screw and toggle wing anchoring system screw in drywall,concrete or hollow brick. -
EML2322L Fastener Reference Guide
EML2322L Fastener Reference Guide Introduction Common Fastener Head, Nut, and Washer Types Fasteners are connective hardware that can easily Fastener Name Tighten With be installed and removed with common hand tools. Bolts, screws, nuts, and rivets are typical examples flat head slotted head of fasteners. The difference between a bolt, screw, (slotted) screwdriver and a stud is determined by its use. pan head Phillips head (Phillips) screwdriver wrench, socket hex head wrench button Allen/hex head cap wrench screw Allen/hex set screw Bolts are headed fasteners with external threads wrench that meet an exacting, uniform thread specification such that they can accept a standardized nut. In the Allen/hex socket head most general sense, screws are headed, externally- wrench threaded fasteners that can cut their own internal threads when installed. In mechanical and aero- shoulder Allen/hex space design applications (which are what we care screw wrench about as design engineers), screws are identical to wrench, socket bolts, but do not require nuts, as they instead screw stud wrench into threaded holes previously created in work- pieces. Studs are externally threaded headless fasteners with which one end usually mates with a rivet rivet gun threated component and the other end typically wrench, socket mates with a standardized nut. hex nut wrench Purpose wrench, socket Nyloc nut wrench The ONLY purpose of fasteners is to clamp parts together. Standard fasteners are NOT intended to serrated wrench, socket be used to for positioning or pivoting; that is the flange nut wrench function of dowel pins, locating shoulders, and flat washer - piloting diameters. -
Fastener Design Manual
. _- NASA 'Reference Publication 1228 March 1990 Fastener Design Manual Richard T. Barrett . , :. ? . ,' - ' ' - "'".'-*'" _,'" ' "l ......... ' " • ' ¢ ",;L, NASA Reference Publication 1228 1990 Fastener Design Manual Richard T. Barrett Lewis Research Center Cleveland, Ohio National Aeronautics and Space Administration Office of Management Scientific and Technical Information Division ERRATA NASA Reference Publication 1228 Fastener Design Manual Richard T. Barrett March 1990 The manual describes various platings that may be used for corrosion control including cadmium and zinc plating. It does not mention outgassing problems caused by the relatively high vapor pressure of these metals. The fastener manual was intended primarily for aeronautical applica- tions, where outgassing is typically not a concern. Issued June 17, 2008 Summary ........... ..... ............. ..... ..... ..... ................................ ..... ....... ....... ............. 1 Introduction ... .................. .......... ..... ..... ..... ..... ..... .......... ............ ..... ....... ............... 1 General Design Information Fastener Materials .... ........ ..... ..... ..... ..... ...................... .......... ............ ............ ..... .. 1 Platings and Coatings ... ..... ..... .......... ..... ..... ..... ..... ................. ..... ............ .............. 1 Thread Lubricants ... ....................... ...................... .......... ................. ....... ..... ..... .... 4 Corrosion ........ ..... .................. ..... .... -
UNITED's Nuts! Acorn, Lock - Spherical Flange Coupling, Lock and Flange Nuts GET MORE for LESS at UNITED! ACORN NUTS See Section G for Stainless
Nuts: Acorn-Coupling- UNITED's Nuts! Acorn, Lock - Spherical Flange Coupling, Lock and Flange Nuts GET MORE FOR LESS AT UNITED! ACORN NUTS See Section G for Stainless. Closed end ACORN NUT A B C protects stud UDB-925000 1/4-20 1/2 1/2 threads from UDB-925005 5/16-18 5/8 9/16 damage. Heat UDB-925010 3/8 – 16 3/4 11/16 treated black UDB-925015 1/2-13 15/16 7/8 B oxide finish. UDB-925020 5/8-11 1-3/16 1-1/16 UDB-925025 3/4 – 10 1-3/8 1-1/4 C12L15 STEEL — HEAT TREATED WITH BLACK OXIDE FINISH. UDB-925030 7/8 – 9 1-7/16 1-7/16 KNURLED LOCK NUTS See Section G for Stainless. Quick thread 1018 STEEL — HEAT TREATED — BLACK OXIDE locking on jigs STEEL STAINLESS A THD B O. D. C STEP D E F DIA PART NO. PART NO. I. D. SIZE DIA DIA WIDTH LIP +.005 and fixtures. 1/4 -.000 detents permit UDB-925110 UDB-925110S 1/4 – 20 1-1/8 1" 7/16 1/16 .250 additional UDB-925115 UDB-925115S 3/8 – 16 1-1/8 1" 7/16 1/16 .250 tightening with UDB-925120 UDB-925120S 1/2 – 13 1-1/8 1" 7/16 1/16 .250 1/4" pin. UDB-925125 UDB-925125S 5/8 – 11 1-3/8 1" 7/16 1/16 .250 COUPLING NUTS Makes unlimited COUPLING NUT A B C stud length UDB-925050 3/8 – 16 1 11/16 combinations UDB-925055 1/2-13 1-1/4 7/8 available. -
Bolted Timber Joints with Self-Tapping Screws
Revista EIA, ISSN 1794-1237 Número 8, p. 37-47. Diciembre 2007 Escuela de Ingeniería de Antioquia, Medellín (Colombia) BOLTED TIMBER JOINTS WITH SELF-TAPPING SCREWS CÉSAR ECHAVARRÍA* ABSTRACT The use of self-tapping screws with continuous threads in the joint area as a reinforcement to avoid splitting of timber members is studied. A theoretical model is developed to calculate the stress distribution around a pin-loaded hole in a timber joint, to predict brittle failure modes in bolted connections and to cal- culate the load in the reinforcing screws. Laboratory experiments on reinforced and non-reinforced timber joints with 15,9-mm bolts have shown good agreement with the model predictions. KEYWORDS: timber joints; brittle failure mode; reinforcement perpendicular-to-grain; analytical model. RESUMEN En este artículo se estudia el uso de tornillos autoperforantes como refuerzo para evitar rupturas frágiles en uniones de madera. Se presenta un modelo teórico para calcular la distribución de esfuerzos alrededor de un perno en una unión de madera, predecir las rupturas frágiles y evaluar el esfuerzo en los tornillos autoperforantes. Los ������������������������������������������������������������������������experimentos de laboratorio con uniones de madera, con pernos de 15,9 mm de diámetro, reforzadas y no reforzadas mostraron la efectividad del modelo teórico propuesto. PALABRAS CLAVE: uniones de madera; ruptura frágil; refuerzo perpendicular a las fibras; modelo analítico. * Ingeniero Civil, Universidad Nacional de Colombia; Master in Timber Structures and Docteur en Sciences, École Polytechnique Fédérale de Lausanne, Switzerland. Ph.D. Researcher, Département des sciences du bois et de la forêt, Université Laval, Québec. [email protected] Associate Professor, Faculty of Architecture, School of Construction, Universidad Nacional de Colombia. -
Bolted Joint Design
Bolted Joint Design There is no one fastener material that is right for every environment. Selecting the right fastener material from the vast array of those available can be a daunting task. Careful consideration must be given to strength, temperature, corrosion, vibration, fatigue, and many other variables. However, with some basic knowledge and understanding, a well thought out evaluation can be made. Mechanical Properties of Steel Fasteners in Service Most fastener applications are designed to support or transmit some form of externally applied load. If the strength of the fastener is the only concern, there is usually no need to look beyond carbon steel. Considering the cost of raw materials, non-ferrous metals should be considered only when a special application is required. Tensile strength is the mechanical property most widely associated with standard threaded fasteners. Tensile strength is the maximum tension-applied load the fastener can support prior to fracture. The tensile load a fastener can withstand is determined by the formula P = St x As . • P= Tensile load– a direct measurement of clamp load (lbs., N) • St= Tensile strength– a generic measurement of the material’s strength (psi, MPa). • As= Tensile stress area for fastener or area of material (in 2, mm 2) To find the tensile strength of a particular P = St x As bolt, you will need to refer to Mechanical P = tensile load St = tensile strength As = tensile stress area Properties of Externally Threaded Fasteners (lbs., N) (psi, MPa) (sq. in, sq. mm) chart in the Fastenal Technical Reference Applied to a 3/4-10 x 7” SAE J429 Grade 5 HCS Guide.