Fabricator Survival Guide
Total Page:16
File Type:pdf, Size:1020Kb
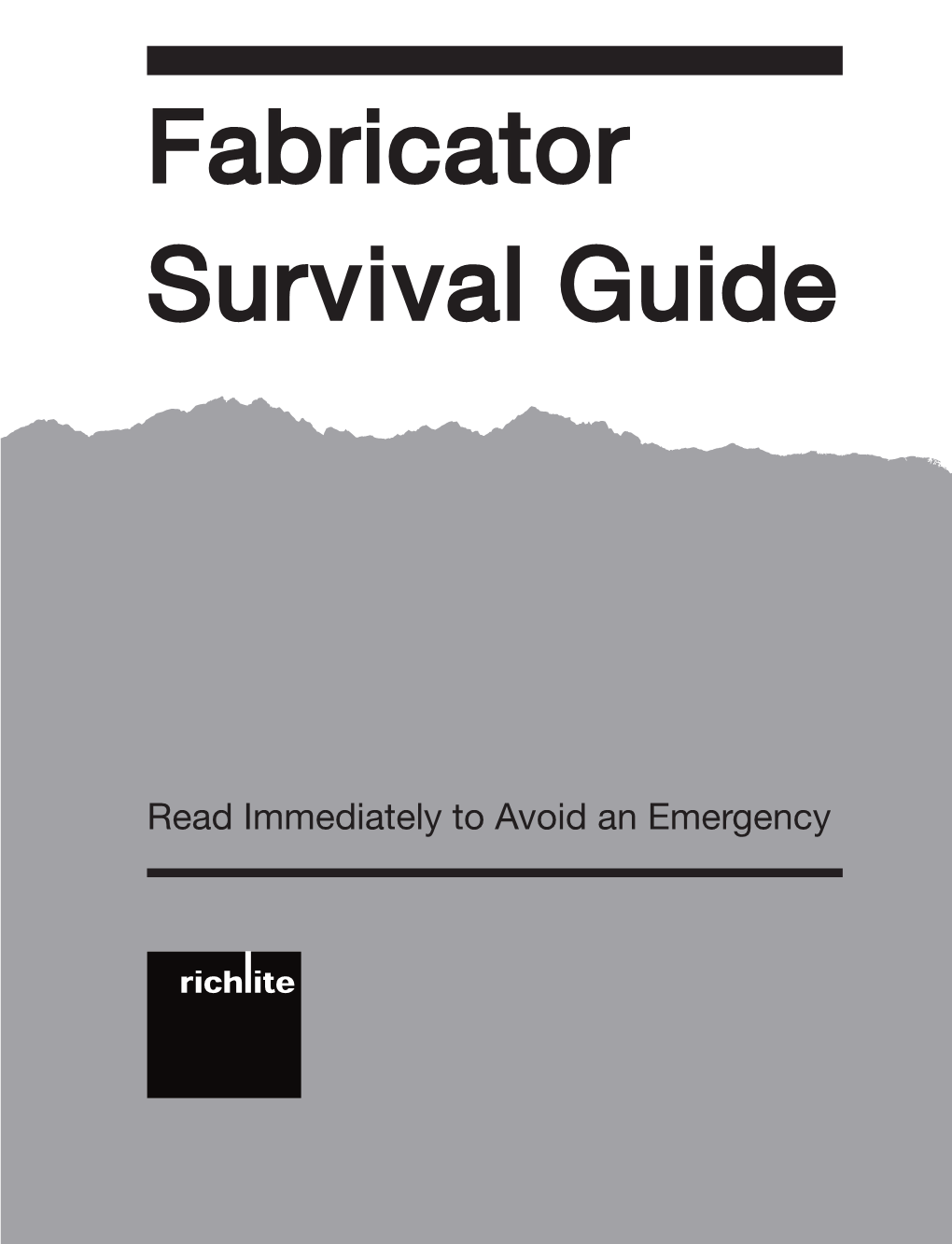
Load more
Recommended publications
-
Everform™ Solid Surface Fabrication Guide Table of Contents
Formica Group Technical Guide EVERFORM™ SOLID SURFACE FABRICATION GUIDE TABLE OF CONTENTS SCOPE: This guide outlines the basic fabrication and installation techniques for Everform™ Solid Surface, including those patterns in the Designer Series. The Designer Series, because of its unique directional visual attributes, requires special fabrication procedures. Please review the information specific to the Designer Series before attempting fabrication. I General Safety 53 Bath Surrounds 1 Health and Safety Information 55 Shower Surrounds 3 Countertops 56 Commercial 3 Kitchens Visual Index 56 Commercial Visual Index | Nurses Station 4 Color and Matching 57 Commercial Visual Index | Lobbies 4 Job Preparation 58 Commercial Visual Index | Batrooms 4 Cutting Everform™ Solid Surface Sheets 59 Commercial Visual Index | Restrooms 5 Seam Placement 60 Wall Application 7 Seam Preparation 63 Hand Rail 17 Basic Edge Assemblies 68 Windowsills 23 Custom Profiles 70 Knee Walls 24 Undermounted Sinks 73 Lavatory Tops 28 Installing Cooktops 78 ADA Standards 30 Countertop Support 80 Toilet and Urinal Partitions 32 Overhang Support 84 Toilet Partitions 33 Overhang Support Techniques 86 Urinal Partitions 36 Overhang Support (For countertops with cutouts) 87 Food Service Countertops 37 Square Backsplashes 93 Table Tops 41 Coved Backsplashes 94 Thermoforming 47 Tiled Backsplashes 98 Finishing 50 Bathrooms 98 Finishing Visual Index 50 Bathrooms Visual Index 105 Adhesives 51 Undermounted Lavatory Bowls 106 Tools 109 Index FTG-0923 | Rev 6 | 10/20 Formica Group Technical Guide | 1 EVERFORM™ SOLID SURFACE FABRICATION GUIDE HEALTH AND SAFETY INFORMATION FOR SHEETS AND SHAPED PRODUCTS HEALTH HAZARD DATA AND HEALTH HAZARD DATA AND GENERAL FIRST AID PROCEDURES FIRST AID PROCEDURES SAFETY Everform™ Solid Surface is not hazardous in normal use. -
Sinks and Lavatories
DUPONT™ CORIAN® SOLID SURFACE FABRICATION/INSTALLATION FUNDAMENTALS NA/ENGLISH SINKS AND LAVATORIES INTRODUCTION A.2. “Soft” seam undermount This bulletin discusses installing DuPont™ Corian® solid • strong, level workbench that can accommodate the shape surface sinks and lavatories. when installed • a 3-hp router with a 1" (25 mm) template guide and a 1/2" OVERVIEW (13 mm) collet High quality installations of DuPont™ Corian® solid surface • appropriate template for the sink model being installed sinks and lavatories are attractive and easy to clean. To properly install sinks, the correct tools and techniques are B. “HARD” SEAM SUBMOUNT INSTALLATION required. Two installation techniques are discussed, In a submount installation the sink is hard seamed with undermount installations with “soft” silicone seams and DuPont™ Joint Adhesive or DuPont™ Joint Adhesive 2.0 to submount installations with “hard” joint adhesive seams. the underside of the countertop. The seam is then on the vertical plane of the sink, as illustrated in Figure B-1. A. TOOLS REQUIRED The installation of Corian® solid surface sinks requires Submount Hard Seam precise fabrication to ensure a proper installation. It is essential to use the correct tools. In addition, all tools must be kept in good condition and bits must be sharp. There are two typical methods of mounting a sink. The preferred method for mounting DuPont™ Corian® solid surface sinks and lavatories is a “hard” seam submount Bowl where the edge of the deck and the sink are flush and the sink is attached to the deck with DuPont™ Joint Adhesive or DuPont™ Joint Adhesive 2.0. -
| 800.220.1966| 800.220.1966 | |[email protected] [email protected] KEEP-NUT™ Parts and Kits
KEEP-NUT™ Sink Anchor Inserts for Under-Mount Sinks KEEP-NUT™ Press-In self-anchoring sink fasteners are the strongest and most efficient mounting system for attaching undermount sinks to granite, quartz, solid surface, porcelain, and a variety of other hard surfaces. Originally designed to support building facades, vertical wall panels and furniture, the KEEP-NUT™ also offers exceptional performance for sink mounting. • Quick Assembly by Pressure • Can be drilled with standard tools (CNC, Grinder or by Hand) • No Need for Resins or Adhesives • Average Strength of 562 lbs per Insert • Stongest Anchor on the Market • Crowns (or Teeth) Provide Axial Strength and Flex, • Save Time & Money Providing Higher Strength Works on: GRANITE MARBLE ENGINEERED STONE UHPC SOLID PORCELAIN GLASS COMPOSITES SURFACE Drilling Methods: Hand Drill KEEP-NUT™ Drilling Machine CNC (All Surfaces) (Solid Surface) (All Surfaces) KDM110KDM110 KEEP-NUT™ Drilling Machine Use 11.8 drill bits only CCH-KN-KDM110 (Vacuum Drilling Machine w/Polisher) Which Bit is Right for Me? Type of Bit Drilling Method Surfaces 11.8 mm 5/8-11 Thread Grinder Bit KEEP-NUT™ Drilling Machine Natural/Engineered Stone 11.8 mm 1/2 GAS CNC Bit CNC Natural/Engineered Stone 11.4 mm 5/8-11 Thread Grinder Bit Manual (without KEEP-NUT™ Drilling Machine) Natural/Engineered Stone 11.8 mm Hand Drill / Drill Press Bit Manual Solid Surface/Plastics KEEP-NUT™ Insert & Pull-Out Strength Minimum Surface Hole Hole Threaded Post Number of Average Thread (d1) Part Depth(s) Depth (l2) Diameter (d2) Depth (h1) -
Richlite Fabrication Guide Cirque Distribution
RICHLITE FABRICATION GUIDE CIRQUE DISTRIBUTION Enhancing innovative design through sales, distribution and support of premium architectural, maker and specialty building materials. TABLE OF CONTENTS FABRICATION GUIDE and OVERVIEW.......... 4 TROUBLESHOOTING.............................26 DELIVERY, HANDLING and STORAGE.......... 5 CANTILEVER GUIDELINES...................... 27 PLANNING.......................................... 7 PROPERTIES.......................................28 CUTTING ............................................ 9 MSDS................................................29 ROUTING............................................ 11 WARRANTY........................................30 DRILLING .......................................... 13 IMPORTANT LINKS...............................33 CNC MACHINING.................................. 14 SEAMING........................................... 16 ASSEMBLIES....................................... 18 SURFACE FINISHING............................. 19 APPLIED FINAL FINISHES.......................22 CARE and MAINTENANCE.......................24 RICHLITE FABRICATION GUIDE The.following.document.describes.how.Richlite.paper.composite.is.received,. handled,.and.fabricated..These.guidelines.should.ensure.that.your.experience. with.Richlite.is.informed.and.positive..Richlite.is.not.like.any.other.material.avail- able.and.by.following.the.instructions.below,.it.is.not.difficult.to.fabricate.and. the.results.are.tremendously.rewarding. Please.note,.these.are.general.guidelines.and.it.is.recommended.that.any.fab- -
Quality Tools for Solid Surface Fabrication PRODUCTS YOU CAN BE PROUD of START with TOOLS YOU CAN TRUST 20Th Anniversary Issue
Quality Tools for Solid Surface Fabrication PRODUCTS YOU CAN BE PROUD OF START WITH TOOLS YOU CAN TRUST 20th Anniversary Issue POWER PRECISION PROFITS “If these tools work for me, they’re gonna work for you.” –Tom Pinske 01/08 – Updated 10/09 A TIP FROM TOM Use tools that were made for the material. No matter how skilled you are or how expensive your materials, you can’t get good results on solid surface using tools made for woodworking. That’s what Tom Pinske discovered, in his own shop and in talking to dozens of professional fabricators who struggled to get the quality results they were used to. “It’s the tools.” Tom said, and set out to find some that would work specifically for solid surface material. Anyone who knows Tom will tell you that he’s very particular, so it wasn’t surprising when he couldn’t find even the most basic tool—a straight edge that was exactly what he wanted. Remembering his dad’s attitude (“If you can’t find it, make it”), Tom decided to design his own solution, and after another long search, found a company that could machine an exact edge—The Pinske Edge. That was the start. He originally designed the tools for use in his own shop, but when other fabricators saw the preci- sion results Tom was getting on his finished pieces, they wanted to know where he got his tools. Every tool that Tom makes starts with one basic idea: a Pinske tool should make your job easier and the finished product better. -
Countertop Glossary
Granite/Solid Surface Countertop Glossary Accents – a contrast, outline or highlight added for detail and emphasis. See “inlays”. Apron front sink - is a sink with a large apron in front that sits on a short cabinet. This may also be referred to as a “farmhouse sink”. Backsplash – is the wall protection at the back edge of the countertop; designed to seal the counter and protect the wall from spills and damage; can be integral to the counter or applied directly to the wall. Build-up – are strips of material that are sometimes attached to the under-side of countertops to raise it flush with the cabinet tops. Bull-nose – is a finished edge on an otherwise unfinished natural or mad-made tile. Butcher block – wood countertops or butcher block countertops come in a variety of hardwoods such as maple or oak. Seldom used for all the countertops in a kitchen, instead they are often used on islands or inserts. Caesarstone – us a nab-made stone that is many times harder than natural stone, making it scratch and stain resistant. Cambria – is a manufacturer of natural quartz countertop material also sold under the name “Cambria”. Cantilever – is a beam projecting beyond its supports, for instance, the area where a countertop overhangs a cabinet by a few inches. Cook-top – is an assembly of stove burners that fits into a countertop. Corian® - is a brand of solid surface material made by DuPont which offers a non-porous, repairable, renewable surface with the ability to integrate sinks. Drain board – are depressions in a countertop which allow water to run into the sink. -
Corian® Solid Surface Care and Maintenance for Facility Managers
CORIAN® SOLID SURFACE TECHNICAL BULLETIN NA/ENGLISH CORIAN® SOLID SURFACE CARE AND MAINTENANCE FOR FACILITY MANAGERS INTRODUCTION Some of the guidance for renewing Corian® Solid Surface with Corian® Solid Surface meets the demanding needs of today’s Resilience Technology™ is different as noted below. commercial surfacing applications. As a solid, nonporous surface, Corian® Solid Surface can be maintained with minimum care to retain For more information, call Corian® Design 1-800-4Corian the original appearance. Because it can be repaired, Corian® Solid (1-800-426-7426). Surface will still look and perform like a new installation, while other surfacing materials will often need to be replaced. With proper care the OVERVIEW Corian® Solid Surface in your commercial application will stay looking This document provides care and maintenance guidance for like new. end-users and facilities management. More severe damage may require professional repair. Corian® Solid Surface with Resilience Technology™ features superior damage forgiveness, easier and quicker stain removal, and less need for A. ROUTINE CARE maintenance. This best-in-class premium technology reduces physical There are three types of Corian® Solid Surface finishes: matte/ damage from scratching, heat, and impact, typical of daily usage in satin, semi-gloss and high-gloss. Contact your Corian® Design commercial environments. sales expert if you are unsure of your finish. Typically, lighter colors have a matte finish, while darker colors have a semi-gloss Corian® Solid Surface with Resilience Technology™ is also quicker and or gloss finish. All sinks and lavatories are finished with a matte/ easier to renew. Its surface looks new for a longer time and is easily satin finish. -
Corian® Quartz Sink Integration
CORIAN® QUARTZ SPECIALTY APPLICATION BULLETIN NA/ENGLISH CORIAN® QUARTZ SINK INTEGRATION Introduction 1. Fabricate the cutout for the Corian® Solid Surface sink or bowl in the Corian® Quartz top. Allow for 1/32" (0.8 mm) less in the Corian® This bulletin discusses installing Corian® Solid Surface sinks and lavatories Quartz cutout than the inside flange measurement of the Corian® with Corian® Quartz tops with a smooth transition between top and sink Solid Surface sink or bowl. This adjustment allows for the edge or lavatory. polishing of the Corian® Quartz cutout. Overview 2. Smooth any rough edges around the cutout with a medium This Technical Bulletin describes recommended fabrication techniques sandpaper or 800+ grit diamond hand pad to remove any chipping that can be used to integrate an undermount Corian® Solid Surface sink from cutting. If making the sink or bowl cut using a CNC router, or lavatory with a Corian® Quartz countertop or vanity top using Corian® most CNC tooling will provide an adequate cut and touch up may Joint Adhesive. This is an allowed exception to the general prohibition of not be necessary. bonding dissimilar materials with Corian® Joint Adhesive. Additional 3. Make sure the backside area within a 2" (51 mm) width around the details on basic techniques can be found in Corian® Solid Surface cutout is somewhat flat and true. This is where the sink or bowl will Fabrication/Installation Fundamentals – Sinks and Lavatories (K-25296) be adhered. Grind, flat and true, the back side of the Corian® Quartz An assumption is that these techniques will be performed in the top with a medium grit (approximately 320) diamond pad, cup fabrication shop and not on the jobsite therefore, careful planning is wheel, or similar tool to aid adhesion. -
Installing Edge Sinks Into Solid Surface Countertops April 2017 Step 1
INSTALLING EDGE SINKS INTO SOLID SURFACE COUNTERTOPS APRIL 2017 STEP 1 ŌĞƌƌĞŵŽǀ ŝŶŐƚŚĞƐŝŶŬĨƌŽŵŝƚƐďŽdž͕ŝŶƐƉĞĐƚŝƚĨŽƌĚĂŵĂŐĞ͘ ŚĞĐŬ the integrity of the rim as well as the bowls for any signs of shipping damage. If the sink is damaged or flawed, call your Karran Sinks distributor immediately. STEP 2 On the back side of the solid surface material, measure and mark where the sink needs to be installed. STEP 3 Mark the sink center line. Next mark a setback from the front edge of the countertop. The recommended amount is about 2” to 2-1/2” but always take into ĐŽŶƐŝĚĞƌĂƟŽŶƚŚĞƐƉĞĐŝĮ ĐĐŝƌĐƵŵƐƚĂŶĐĞƐŽĨĞĂĐŚŝŶƐƚĂůůĂƟŽŶƌĞůĂƟŶŐ to cabinet and plumbing placement. STEP 4 Place the sink upside down on the back of the solid surface in the ŝŶĚŝĐĂƚĞĚƉŽƐŝƟŽŶ͘ DĂŬĞƐƵƌĞƚŚĞƐŝŶŬŝƐĐĞŶƚĞƌĞĚŽŶƚŚĞƐŝŶŬĐĞŶƚĞƌ line and the front edge of the rim is on the setback line. STEP 5 Use hot melt glue to adhere wood locator blocks to the back side of the solid surface around the perimeter of the sink. These will hold the sink in place once seaming adhesive has been applied in Step 11. STEP 6 Clean the rim of the sink thoroughly with denatured alcohol and a clean rag. When installing a quartz sink into solid surface, always tape the top 1” to 2” of bowl wall and trim flush with the rim. This prevents excess adhesive ƐƟĐŬŝŶŐƚŽƚŚĞďŽǁ ůǁĂůů͘ STEP 7 Clean the back of the solid surface where the sink will adhere with denatured alcohol and a clean rag. STEP 8 Prepare to glue the sink to the back of the solid surface. You will need a 10:1 mix gun and a 10:1 two part solid surface seaming adhe- sive cartridge. -
Router Bits for Working on Solid Surface Materials 3.05
2019 - Router bits for wood, chipboard and solid surface materials ROUTER BITS FOR WORKING HW STRAIGHT PLUNGE BITS ON SOLID SURFACE MATERIALS WITH BALL BEARING GUIDE Z=2 The series of tools on page 3.05 to page 3.13 have been specifi- ART. E302 - G302 cally designed for working Solid Surface materials (CORIAN ® ). The type of raw material, cutting angles and components used in manufacturing the router bits shown here have been carefully selected to get the best finishing. Special router bits can be manufactured on request. 5° ball bearing with Delrin® ring S ∅ 12 S ∅ 12,7 (1/2“) D B α E L E302.190.R G302.190.R 19 25 5° 1,6 82,5 Z050.103.N Z053.002.N Z051.004.R S ∅ 12 S ∅ 12,7 (1/2“) D B L α E302.191.R G302.191.R 19 25,4 80 0° Z050.101.N Z053.002.N Z051.004.R HW ROUTER BITS WITH NEGATIVE AXIAL ANGLE Z=2 ART. E300 - G300 HW FACE-INLAY BITS WITH BALL BEARING GUIDE Z=2 ART. E305 - GE306 - E307 S ∅ 12 D B L E S ∅ 12 S ∅ 12,7 (1/2“) D B L E305.064.R Selling out 22 6,4 76 4,8 E300.095.R G300.095.R 9,5 50 70 E305.095.R Selling out 22 9,5 78 4,8 E300.127.R G300.127.R 12,7 32 73 E305.127.R 22 12,7 82 4,8 E300.128.R G300.128.R 12,7 38 79 E305.190.R Selling out 22 19 88 4,8 E300.129.R G300.129.R 12,7 50 107,5 HW STRAIGHT PLUNGE BITS Z=1 Z050.007.N Z054.003.N Z051.004.R ART. -
Fabrication Manual Manual
FabricationFabrication ManualManual AndAnd TechnicalTechnical ReferenceReference GuideGuide 2010 Written by Gordon Shell WelcomeWelcome toto thethe worldworld ofof EOSEOS™™3cm3cm SolidSolid SurfaceSurface “The only “Solid” Solid Surface” Click on title to view Video Clips Introduction • It started with a great idea... Make a thicker solid surface – Eos Solid Surface bridges the gap between seamless solid surface and high-end laminate. Our patent pending 3cm (1 1/4") material offers all the advantages of premium solid surface, in a thicker, more durable material at a surprisingly low price. – By eliminating up to 75% of the labor required for traditional 1/2" solid surface, Eos combines the massive look of granite with a lower price point and faster delivery. The end result is a true value in the classic sense a higher quality product at a competitive price, offering you the flexibility to create the countertop you have always wanted. – In addition, 2cm (3/4”) EOS™ sheet goods offer a great, low cost, low labor alternative to laminate, cultured marble, and other materials in the bath, window sill, hospitality, medical, retail, etc. market. Introduction • Eos offers you: – The massive look of natural stone without conspicuous seams. – A food safe, non-porous surface that is easy to clean and maintain. – Seamless integrated bowls and backsplashes. – Greater heat resistance. – A 10-year transferable product warranty. – A surface that is renewable and repairable. – All the advantages of premium solid surface, at a surprisingly low price. • Eos Solid Surface is ideal for both residential and commercial applications. With a large color palette to choose from, unlimited designer options, enhanced durability backed by a 10-year product warranty, Eos is changing the solid surface industry. -
Solid Surface Fabricators... Give Your Company the Leading Edge
INTERNATIONAL SURFACE FABRICATORS ASSOCIATION INTERNATIONAL SURFACE VOLUME 4 • ISSUE 2 • 2011 • SINGLE ISSUE $14.95 What’s Inside: New Colors and Materials Page 26 A Preview of the Upcoming Int’l Countertop Expo Surfacing Olympic Village Page 32 Page 22 A Look at Trends in Sinks Page 36 Upcycling Solid Surface in Sweden Page 40 VOLUME 4 • ISSUE 2 • 2011 • COUNTERTOPS SURFACES & ARCHITECTURAL VOLUME 4 • ISSUE 2 2011 INTERNATIONAL SURFACE FABRICATORS ASSOCIATION www.ISFAnow.org 100’s of New Products FREE New Full Color Catalog Thousands of ™ Request Your Free Copy Today www.FreeDomainCatalog.com One Company. Premium Products. Superior Service. or Call Toll Free 866.385.7775 Circle Reader Service # 01 on the Reader Service Page or go to www.isfanow.org/info Magazine Credits Letters To The Editor ISFA Directors Countertops & Architectural Surfaces welcomes Letters to the Editor. If you Mike Nolan, Director have questions about the magazine, or would like to make a comment, or Martin Funck, Director voice an opinion about the magazine, ISFA, or the industry in general, please Dave Paxton, Director feel free to write to us. Joe Hoffman, Director Michael Bustin, Director Please send letters to [email protected] or to Letters, ISFA, 165 N 1330 W Harry Hollander, Associate Member Rep. Unit A3, Orem, UT 84057 or fax to (801) 341-7361 attention: Editor. Include Bryan Stannard, Associate Member Rep. a telephone number and address (preferable email address). Letters may be edited for clarity or space. Because of the high volume of mail we receive, we ISFA Staff cannot respond to all letters.