INSTALLATION INSTRUCTIONS Victor Small-Block Ford Race Heads
Total Page:16
File Type:pdf, Size:1020Kb
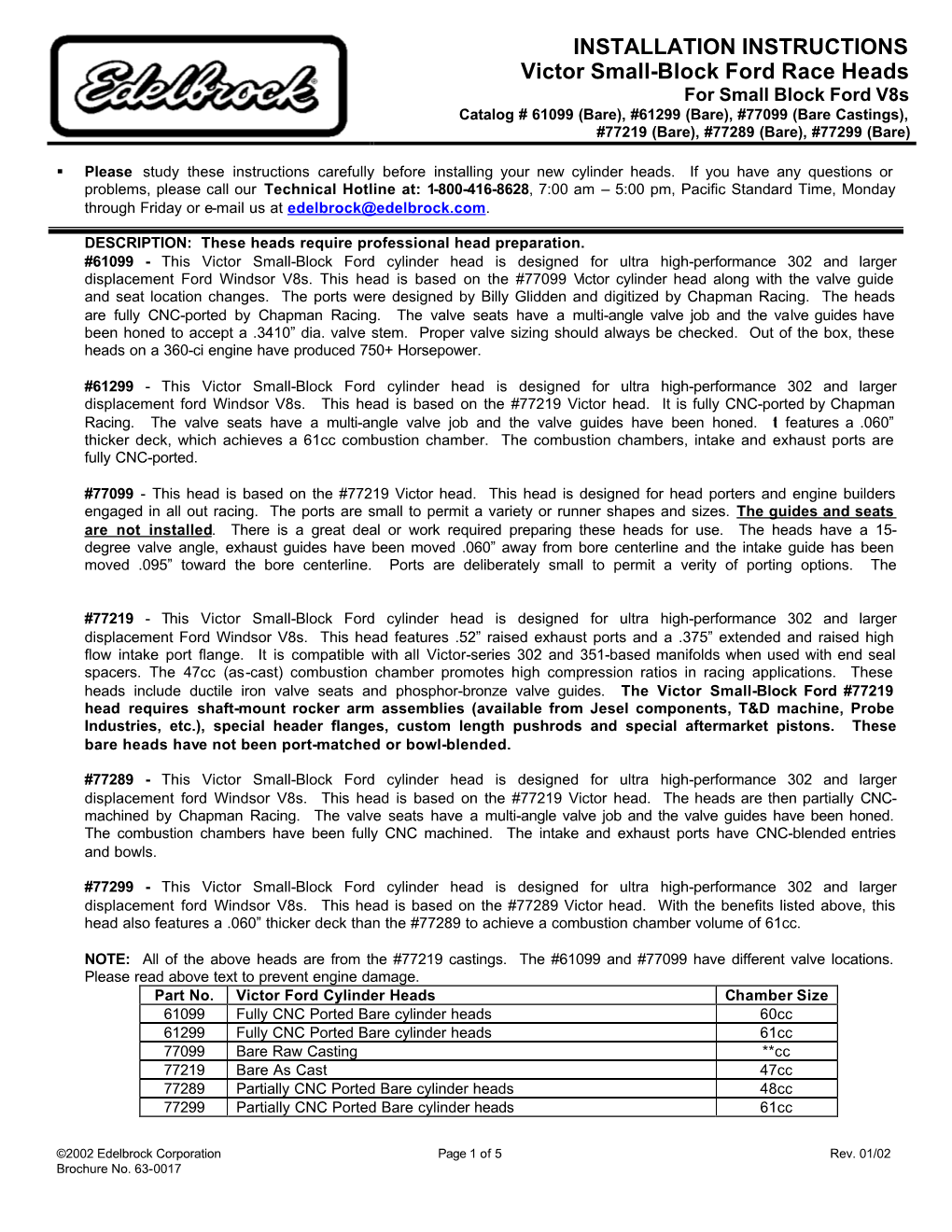
Load more
Recommended publications
-
Testing the System Page 1 of 4
Testing the system Page 1 of 4 Testing the system Vehicle diagnostic, testing and information system -VAS 5051B- Test sequence Coolant temperature at least 80 °C. Vehicles with automatic gearbox: selector lever in position P or N – Connect vehicle diagnostic, testing and information system -VAS 5051B- and select vehicle system “01 - Engine electronics” from list. Engine must be idling. WARNING Test equipment must always be secured on the rear seat and operated from that position by a second person. If test and measuring instruments are operated from front passenger's seat and the vehicle is involved in an accident, the person sitting in this seat could be seriously injured when the airbag is triggered. Display on -VAS 5051B-: – From list -1- select diagnostic function “04 - Basic setting”. Display on -VAS 5051B-: 1 - Enter display group – Using the keypad -2-, enter “094” to select “Display group 094” and confirm entry with the Q key. vw-wi://rl/A.en-GB.A04.5636.29.wi::37889621.xml?xsl=3 14.01.2014 Testing the system Page 2 of 4 – Activate basic setting by touching key A . Display on -VAS 5051B-: – Increase the engine speed to above 2000 rpm for approx. 10 seconds. – Check specifications in display zones -3- and -4-. Display zones 1234 Display group 94: variable valve timing, bank 1 (right-side) and bank 2 (left-side) Display xxxx rpm --- --- --- Readout Engine speed Variable valve timing Variable valve timing Variable valve timing bank 1 bank 2 Range CS-ctrl ON Test OFF Test OFF CS-ctrl OFF Test ON Test ON Syst. -
Camshaft Deviation Codes.Pdf
AD07.61 -P-4000 -94VA Page 1 of 2 AD07.61-P-4000- Continuous camshaft adjustment - 94VA fault code description ME Angular deviation of camshafts to the crankshaft 1 Fault code 1197 Exhaust camshaft on right cylinder bank, permanent advanced ( Readout on generic scan tool) position (P0017) 1198 Exhaust camshaft on right cylinder bank, permanent retarded position (P0017) 1200 Exhaust camshaft on right cylinder bank, displacement (P0017) 1201 Exhaust camshaft on left cylinder bank, permanent advanced position (P0019) 1202 Exhaust camshaft on left cylinder bank, permanent retarded position (P0019) 1204 Exhaust camshaft on left cylinder bank, displacement (P0019) 1205 Intake camshaft on right cylinder bank, permanent advanced position (P0016) 1206 Intake camshaft on right cylinder bank, permanent retarded position (P0016) 1208 Intake camshaft on right cylinder bank, displacement (P0016) 1209 Intake camshaft on left cylinder bank, permanent advanced position (P0018) 1210 Intake camshaft on left cylinder bank, permanent retarded position (P0018) 1212 Intake camshaft on left cylinder bank, displacement (P0018) 2 Fault storage After expiry of test duration and fault Actuation of engine diagnosis Following two successive driving cycles with faults indicator lamp (EURO4) or CHECK ENGINE (MIL) malfunction indicator lamp 3 Checking frequency Continuous 4 Checked signal or status Comparison of position of the intake camshaft or exhaust camshaft to position of the crankshaft 5 Fault setting conditions 1197, 1201, 1205, 1209 - Permanent advanced position greater than a 20° crank angle 1198, 1202, 1206, 1210 - Permanent retarded position greater than a 20° crank angle 1200, 1204, 1208, 1212 - Fault if after adjustment of a camshaft the new position deviates more than a 9° crank angle from the required value. -
Off-Road Industrial Engines MAN Engines Off-Road Diesel Engines Fordiesel Agricultural and Environmental, Construction and Special Machinery and Special Construction
Industrial engines Off-Road Off-Road Diesel engines for agricultural and environmental, construction and special machinery MAN Engines Built for everyone who wants to move things in a big way. Contents MAN diesel engines for agricultural and construction machinery Performance spectrum and applications . 4 MAN key technologies . 4 Development to meet operational requirements . 4 Easy system integration . 4 Intelligent service solutions . 4 The shared component concept . 4 Modular exhaust gas treatment kit (AGN kit) . 4 Reliability . 4 Description of engines D0834 and D0836 . 6 D2676 . 8 D3876 . 10 D2868 . 12 D2862 . 14 MAN diesel engines for agricultural and construction machinery Time and cost pressure are increasing, both in agriculture and in the construction industry. This is why reliability and economic efficiency are more important in these businesses than ever before. MAN engines are the constant factor that makes the machines reliable, both in brisk day-to-day business and in their life-cycle costs. Our MAN engines can help you move things in a big way – either as a vehicle operator or as a designer. Performance spectrum and applications MAN off-road engines with a displacement of 4.6 to 24.2 liters come with ratings ranging from 110 kW to 882 kW (150 hp to 1 200 hp). Applications include: nnAgricultural machinery nnCutters and shredders nnSpecial machinery such as nnConstruction machinery nnEnvironmental and recycling snowcats nnMobile cranes and materials technology transport MAN key technologies Development to meet operational Easy system integration Our key to your success: When de signing requirements One name – one system . MAN makes and developing an MAN off-road engine, Our concepts are off-road in the truest use of a single defined engine inter- we rely on innovative technologies such sense of the word, that is to say they face to exchange data and commands as turbo-charging using variable turbine are extraordinary . -
Table of Contents S65B40 Engine
Table of Contents S65B40 Engine Subject Page Crankcase and Crankshaft Drive . .3 Engine Block with Bedplate Construction . .3 Crankshaft . .4 Connecting Rods . .4 Pistons . .5 Oil Supply . .6 Oil Supply Hydraulic Circuit Diagram . .8 Valvetrain . .10 Cylinder Head . .10 Hydraulic Bucket Tappet . .11 CamshaftDrive................................................12 VANOS . .13 Belt Drive . .16 Air Supply . .17 Air Intake Guide/Oil Separator/Secondary Air System . .17 Oil Separators . .18 Secondary Air System . .18 Individual Throttle Butterfly System . .19 Idle Control System . .20 Fuel Supply . .21 Cooling System . .22 Exhaust System . .24 Initial Print Date: 1/08 Revision Date: S65B40 Engine Model: E90 M3, E92 M3 Production: 2/2008 After completion of this module you will be able to: Identify the components of the S65B40 engine Identify the difference between the S85B50 and S65B40 engines Explain the oil supply system of the engine 2 S65B40 Engine Crankcase and Crankshaft Drive Engine Block with Bedplate Construction The construction and materials are identical to the S85; the upper low-pressure die-cast crankcase is made from an aluminum-silicon alloy. The cylinder bores are formed using exposed hard silicon crystals, rendering the use of cylinder liners redundant. The lower crankcase (bedplate) is also constructed using die-cast aluminum. Due to the extreme forces, grey cast iron inlays are used to reinforce the bedplate construction. These also limit crankshaft bearing clearances over a greater temperature range and thus have a positive effect on the oil flow rate. S65B40 Engine block with bedplate construction Index Explanation 1 Engine block (upper section) 2 Grey cast iron inlays 3 Bedplate construction (lower section) 3 S65B40 Engine Crankshaft The five-bearing crankshaft is forged from a single piece, including the two double-chain wheels for driving the valve gear. -
M62 Engine Details (PDF)
TABLE OF CONTENTS Subject Page M62TU Engine . .. .. 2 Vanos Operation . .3-12 Engine Cooling System. 13 IHKA System Auxilary Pump. 14 DME-ME 7.2 Engine Management. 15 IPO ME 7.2. 16 Integral Electronic Throttle System (EML). .17 Input Signal/Components. .19 Camshaft Position Sensors. 19 Hot Film Air Mass Sensor (HFM 5). 20 Integrated Ambient Barometeric Pressure Sensor. .21 Radiator Outlet Temperature Sensor. 22 DSC III Road Speed Signal. 22 Accelerator Pedal Sensor (PWG). 23 EDK Throttle Position Feedback Signal. 24 MFL Cruise Control Data Signal. .25 Brake Light Switch. 25 Can Bus. .26 Output Control Functions. .. .27 E-Box. .27 Secondary Air Injection. .28 Auxiliary Fan Control. .29 Electric Throttle Control. 30 DM-TL. .. 31 Leak Diagnosis Test Precondition. 34 M62TU Engine / ME7.2 The 4.4i X5 is equipped with the M62 TU B44 (4.4 liter) engine. Features of the M62 TU engine include: • Digital motor Electronics Control ME 7.2. • Variable positioned intake camshaft VANOS system. • “EML” Electronic Throttle Control System identified as EDK. • Compact water cooled generator (F-alternator). • Thermostat controlled transmission fluid/engine coolant heat exchanger system for automatic transmission equipped vehicles. • Non Return Fuel Rail (Running Loss Compliance). • IHKA Auxillary Water Pump. 2 M62 TU VANOS OVERVIEW The variable intake valve timing system on the M62 TU continues to be identified as VANOS. This acronym comes from the German words; VAriable NOckenwellen Steuerung, which means Variable Camshaft Control. The M62 TU VANOS system is a new variant providing stepless VANOS functionality on each intake camshaft. The system is continuously variable within its range of adjustment providing optimized camshaft positioning for all engine operating conditions. -
(12) United States Patent (10) Patent N0.: US 6,321,698 B1 Rau Et Al
US006321698B1 (12) United States Patent (10) Patent N0.: US 6,321,698 B1 Rau et al. (45) Date of Patent: Nov. 27, 2001 (54) INTERNAL COMBUSTION ENGINE 1024825 * 4/1953 (FR). 121605A * 5/1919 (GB) ................................. .. 123/551 (75) Inventors; Erhard Rau, We?heim; Wilhelm 97/40267 * 10/1997 (WO) ..................................... .. 75/22 Huettner, Waiblingen; Joerg Abtho?', Pluederhausen, all of (DE) OTHER PUBLICATIONS (73) Assignee; Daimlerchrysler AG, Stuttgart (DE) “18—Zylinder von Volkswagen”, Autos Test Technik, mot No. 11, ISSN 0027—1462, pp. 16—23, (May 15, 1998). ( * ) Notice: Subject to any disclaimer, the term of this patent is extended or adjusted under 35 * cited by examiner U.S.C. 154(b) by 0 days. Primary Examiner—Noah P. Kamen (21) Appl- NOJ 09/369,225 Assistant Examiner—Hai Huynh (22) Filed Aug 5 1999 (74) Attorney, Agent, or Firm—Kenyon & Kenyon . , _ _ (57) ABSTRACT Related US. Application Data (60) Provisional application No. 60/095,774, ?led on Aug. 7, An internal combustion engine having four individual cyl 1998- inder banks, in each case tWo cylinder banks being arranged (51) Int. c1.7 .................................................... .. F02B 75/22 in a V-éharw With respect to one another in such a Way that (52) us CL 123/54_4 the cylinder banks forming a V are disposed on both sides (58) Field of i i i i i i 4 1 54 4 of one engine plane E de?ned by a vertical aXis H that 123/54 8 55 1 54 6 54 7 54 2 symmetrically divides the internal combustion engine and ' ’ ' ’ ' ’ ' ’ ' by a longitudinal aXis L of the internal combustion engine, (56) References Cited one cylinder bank of the cylinder banks that are associated With one another in a V-shape being con?gured closer to the US. -
Diagnosis and Prognosis of Fuel Injectors Based on Control Adaptation
Diagnosis and Prognosis of Fuel Injectors based on Control Adaptation Azeem Sarwar1, Chaitanya Sankavaram2, and Xiangxing Lu3 1,2,3 Vehicle Health Management Group, Vehicle Systems Research Laboratory, General Motors Company, 30565 William Durant Blvd, Warren, MI, USA [email protected] [email protected] [email protected] ABSTRACT 54.5 mpg by 2025 (Ferguson & Kirkpatrick, 2015). Follow- ing the stricter requirements, the emission level of current in- Spark Ignition Direct Injection (SIDI) technology enables ternal combustion engines has decreased to about 5% of the better fuel economy and tail pipe emissions in vehicles emission levels that were prevalent 40 years ago (Ferguson & equipped with gasoline engines. The SIDI technology de- Kirkpatrick, 2015). pends on the ability of the system to deliver fuel at high pres- sure directly into the combustion chamber, hence making the Up until 1990s, Port Fuel Injection (PFI) Engines reflected fuel injectors key subcomponents. Reliable performance of state of the art for production gasoline engines (C¸elik & fuel injectors is vital as it directly relates to the operability of Ozdalyan, 2010). Advancement in computer-based con- the vehicle, and hence customer satisfaction in case of failure. trol made it possible to deliver gasoline precisely through It, therefore, becomes very important to devise a scheme that solenoid-based fuel injectors, just upstream or at the back of can effectively diagnose and prognose such a component. In each cylinder’s intake valve. The fuel then mixes with the this article, algorithm development for diagnosis and a path- incoming air, and gets pulled into the combustion chamber way to prognosis of fuel injectors is presented. -
Piston Engine Fundamentals TC010-05-01S
LEVEL F PPiissttoonn EEnnggiinnee FFuunnddaammeennttaallss TTCC001100--0055--0011SS Mazda Motor Corporation Technical Service Training Piston Engine Fundamentals CONTENTS TC010-05-01S 1 – INTRODUCTION ............................................................................1 Course Overview ..................................................................................1 Audience and Purpose...................................................................1 Course Content and Objectives .................................................2 How to Use This Guide .........................................................................3 Section Objectives .........................................................................3 Text and Illustrations......................................................................3 Review Exercises ..........................................................................4 2 – BASIC OPERATION.......................................................................5 Objectives .............................................................................................5 How Power is Developed......................................................................6 Harnessing Power..........................................................................6 Controlling Combustion..................................................................7 The Four-Stroke Cycle..........................................................................9 Intake Stroke............................................................................... -
Internal Combustion Engine
AccessScience from McGraw-Hill Education Page 1 of 15 www.accessscience.com Internal combustion engine Contributed by: Neil MacCoull, Donald L. Anglin Publication year: 2014 A prime mover that burns fuel inside the engine, in contrast to an external combustion engine, such as a steam engine, which burns fuel in a separate furnace. See also: ENGINE . Most internal combustion engines are spark-ignition gasoline-fueled piston engines. These are used in automobiles, light- and medium-duty trucks, motorcycles, motorboats, lawn and garden equipment, and light industrial and portable power applications. Diesel engines are used in automobiles, trucks, buses, tractors, earthmoving equipment, as well as marine, power-generating, and heavier industrial and stationary applications. This article describes these types of engines. For other types of internal combustion engines see GAS TURBINE ; ROCKET PROPULSION ; TURBINE PROPULSION . The aircraft piston engine is fundamentally the same as that used in automobiles but is engineered for light weight and is usually air-cooled. See also: RECIPROCATING AIRCRAFT ENGINE . Engine types Characteristics common to all commercially successful internal combustion engines include (1) the compression of air, (2) the raising of air temperature by the combustion of fuel in this air at its elevated pressure, (3) the extraction of work from the heated air by expansion to the initial pressure, and (4) exhaust. Four-stroke cyc le. William Barnett first drew attention to the theoretical advantages of combustion under compression in 1838. In 1862 Beau de Rochas published a treatise that emphasized the value of combustion under pressure and a high ratio of expansion for fuel economy; he proposed the four-stroke engine cycle as a means of accomplishing these conditions in a piston engine ( Fig. -
Modeling and Simulation of Airflow Dynamics in a Dynamic Skip Fire
Downloaded from SAE International by Mark Wilcutts, Tuesday, February 02, 2016 Modeling and Simulation of Airfow Dynamics in 2015-01-1717 a Dynamic Skip Fire Engine Published 04/14/2015 Li-Chun Chien, Matthew Younkins, and Mark Wilcutts Tula Technology Inc. CITATION: Chien, L., Younkins, M., and Wilcutts, M., "Modeling and Simulation of Airfow Dynamics in a Dynamic Skip Fire Engine," SAE Technical Paper 2015-01-1717, 2015, doi:10.4271/2015-01-1717. Copyright © 2015 SAE International Abstract Over the years, a number of skip-fre engine control arrangements have been proposed which do not simply switch back and forth to Dynamic skip fre is a control method for internal combustion reduced cylinder sets. Förster et al [5] described use of a relatively engines in which engine cylinders are selectively fred or skipped to large number of fxed cylinder fre-skip patterns but did not describe meet driver torque demand. In this type of engine operation, fueling, how the fxed patterns could be switched in order to effectively and possibly intake and exhaust valves of each cylinder are actuated achieve smooth torque delivery in practice. on an individual fring opportunity basis. The ability to operate each cylinder at or near its best thermal effciency, and to achieve fexible In contrast to these strategies, Tula Technology's Dynamic Skip Fire control of acoustic and vibrational excitations has been described in (DSF) considers activation or deactivation of each cylinder event previous publications. independently, varying the density frings as driver demanded torque changes. Figure 1 shows the simple concept of using density of Due to intermittent induction and exhaust events, air induction and cylinder frings to produce a driver-demanded torque. -
EEE- Hill, 25-1
USOO893 1444B2 (12) United States Patent (10) Patent No.: US 8,931,444 B2 McConville et al. (45) Date of Patent: Jan. 13, 2015 (54) HEAD PACKAGING FOR CYLINDER (58) Field of Classification Search DEACTIVATION USPC ........................ 123/90.1590.18, 90.27, 90.6 See application file for complete search history. (71) Applicant: Ford late styles LLC, (56) References Cited earborn, U.S. PATENT DOCUMENTS (72) Inventors: Gregory Patrick McConville, Ann Arbor, MI (US); Kim Hwe Ku, West 4,615.308 A 10, 1986 Asanomi et al. B1 field, MI (US 4,794,893 A * 1/1989 Masuda et al. ............. 123,90.17 oomfield, MI (US) 4,848,284. A * 7/1989 Konno ........... ... 123.90.16 5,445,117 A * 8/1995 Mendler ........ ... 123.90.16 (73) Assignee: Ford Global Technologies, LLC, 5,758,612 A * 6/1998 Tsuzuku et al. ... 123.90.16 Dearborn, MI (US) 5,836,274 A * 1 1/1998 Saito et al. ..... ... 123.90.16 6,832,583 B2 * 12/2004 Hayman ..... ... 123.90.16 ck (*) Notice: Subject to any disclaimer, the term of this g R 23. Ano et al. 123.90.24 patent is extended or adjusted under 35 7,980 17 B2 7/2011 Evans et al. U.S.C. 154(b) by 0 days. 2002/0017259 A1 2/2002 Tosaka et al. .............. 123,90.27 2005/0066932 A1 3/2005 Patterson et al. 2008/017081.6 A1* 7, 2008 Ueno et al. .. ... 384,418 (21) Appl. No.: 13/682,477 2009, O151673 A1* 6, 2009 Choi ....... 123/90.15 2009,030.1086 A1 12/2009 Ralston (22) Filed: Nov. -
Or Fault Code Entry "Plausibility of Camshaft Position"
Engine noises (rattling) after engine start and/ or fault code entry "Plausibility of camshaft position" Topic number LI05.10-P-058758 Version 1 Design group 05.10 Timing chain drive, toothed belt drive Date 03-19-2014 Validity ENGINE 271.8 EVO Reason for change Reason for block Complaint: Noise: A rattling noise may be heard from the area of the chain drive for approx. 2-5 seconds after engine start. And/or: Fault code entries in engine control unit: SIM271DE20: P001177 The position of the intake camshaft (cylinder bank 1) deviates from the specified value. The commanded po- sition cannot be reached. P001762 The position of the exhaust camshaft (cylinder bank 1) is implausible in comparison with the position of the crankshaft. The signal comparison is faulty. P001192 The position of the intake camshaft (cylinder bank 1) deviates from the specified value. The function or the instruction is faulty. P001195 The position of the intake camshaft (cylinder bank 1) deviates from the specified value. The mechanical se- tup is not OK. P001477 The position of the exhaust camshaft (cylinder bank 1) deviates from the specified value. The commanded position cannot be reached. P001492 The position of the exhaust camshaft (cylinder bank 1) deviates from the specified value. The function or the instruction is faulty. P001495 The position of the exhaust camshaft (cylinder bank 1) deviates from the specified value. The mechanical setup is not OK. P001600 The position of the intake camshaft (cylinder bank 1) is implausible in comparison with the position of the crankshaft. P001662 The position of the intake camshaft (cylinder bank 1) is implausible in comparison with the position of the crankshaft.