Novel Solutions for Closed-Loop Reverse Electrodialysis
Total Page:16
File Type:pdf, Size:1020Kb
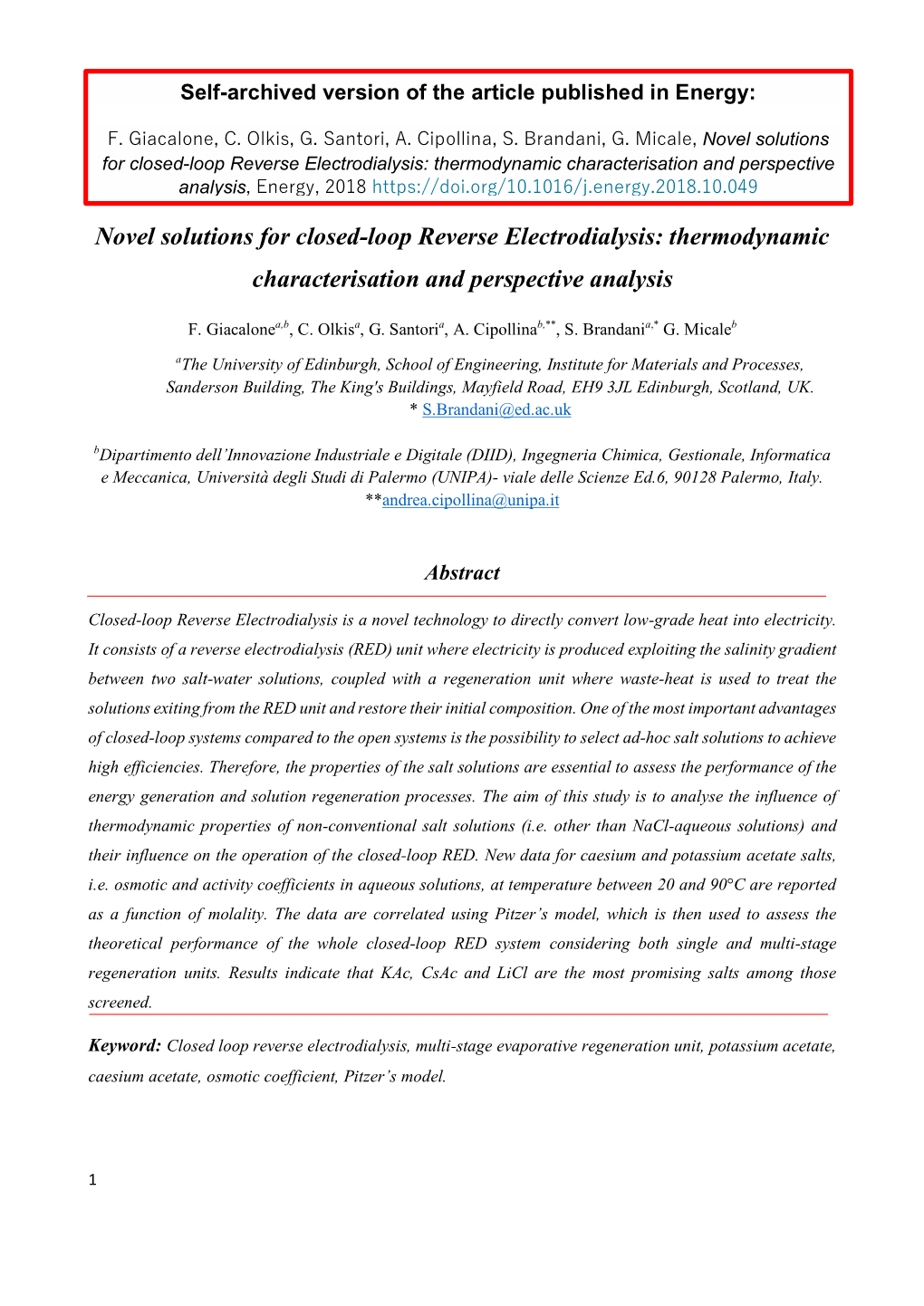
Load more
Recommended publications
-
Crystallization and Preliminary X-Ray Analysis of Ocr, the Product of Gene 0.3 of Bacteriophage T7
Edinburgh Research Explorer Crystallization and preliminary X-ray analysis of ocr, the product of gene 0.3 of bacteriophage T7 Citation for published version: Sturrock, SS, Dryden, DTF, Atanasiu, C, Dornan, J, Bruce, S, Cronshaw, A, Taylor, P & Walkinshaw, MD 2001, 'Crystallization and preliminary X-ray analysis of ocr, the product of gene 0.3 of bacteriophage T7', Acta Crystallographica Section D: Biological Crystallography, vol. 57, no. Part 11, pp. 1652-1654. https://doi.org/10.1107/S0907444901011623 Digital Object Identifier (DOI): 10.1107/S0907444901011623 Link: Link to publication record in Edinburgh Research Explorer Document Version: Publisher's PDF, also known as Version of record Published In: Acta Crystallographica Section D: Biological Crystallography Publisher Rights Statement: RoMEO green General rights Copyright for the publications made accessible via the Edinburgh Research Explorer is retained by the author(s) and / or other copyright owners and it is a condition of accessing these publications that users recognise and abide by the legal requirements associated with these rights. Take down policy The University of Edinburgh has made every reasonable effort to ensure that Edinburgh Research Explorer content complies with UK legislation. If you believe that the public display of this file breaches copyright please contact [email protected] providing details, and we will remove access to the work immediately and investigate your claim. Download date: 27. Sep. 2021 crystallization papers Acta Crystallographica Section D Crystallization and preliminary X-ray analysis of Biological Crystallography ocr, the product of gene 0.3 of bacteriophage T7 ISSN 0907-4449 Shane S. Sturrock,a David T. F. -
Chemical Names and CAS Numbers Final
Chemical Abstract Chemical Formula Chemical Name Service (CAS) Number C3H8O 1‐propanol C4H7BrO2 2‐bromobutyric acid 80‐58‐0 GeH3COOH 2‐germaacetic acid C4H10 2‐methylpropane 75‐28‐5 C3H8O 2‐propanol 67‐63‐0 C6H10O3 4‐acetylbutyric acid 448671 C4H7BrO2 4‐bromobutyric acid 2623‐87‐2 CH3CHO acetaldehyde CH3CONH2 acetamide C8H9NO2 acetaminophen 103‐90‐2 − C2H3O2 acetate ion − CH3COO acetate ion C2H4O2 acetic acid 64‐19‐7 CH3COOH acetic acid (CH3)2CO acetone CH3COCl acetyl chloride C2H2 acetylene 74‐86‐2 HCCH acetylene C9H8O4 acetylsalicylic acid 50‐78‐2 H2C(CH)CN acrylonitrile C3H7NO2 Ala C3H7NO2 alanine 56‐41‐7 NaAlSi3O3 albite AlSb aluminium antimonide 25152‐52‐7 AlAs aluminium arsenide 22831‐42‐1 AlBO2 aluminium borate 61279‐70‐7 AlBO aluminium boron oxide 12041‐48‐4 AlBr3 aluminium bromide 7727‐15‐3 AlBr3•6H2O aluminium bromide hexahydrate 2149397 AlCl4Cs aluminium caesium tetrachloride 17992‐03‐9 AlCl3 aluminium chloride (anhydrous) 7446‐70‐0 AlCl3•6H2O aluminium chloride hexahydrate 7784‐13‐6 AlClO aluminium chloride oxide 13596‐11‐7 AlB2 aluminium diboride 12041‐50‐8 AlF2 aluminium difluoride 13569‐23‐8 AlF2O aluminium difluoride oxide 38344‐66‐0 AlB12 aluminium dodecaboride 12041‐54‐2 Al2F6 aluminium fluoride 17949‐86‐9 AlF3 aluminium fluoride 7784‐18‐1 Al(CHO2)3 aluminium formate 7360‐53‐4 1 of 75 Chemical Abstract Chemical Formula Chemical Name Service (CAS) Number Al(OH)3 aluminium hydroxide 21645‐51‐2 Al2I6 aluminium iodide 18898‐35‐6 AlI3 aluminium iodide 7784‐23‐8 AlBr aluminium monobromide 22359‐97‐3 AlCl aluminium monochloride -
The Synthesis, Characterisation and Ion Exchange of Mixed Metal Phosphates by Victoria Anne Burnell
The Synthesis, Characterisation and Ion Exchange of Mixed Metal Phosphates by Victoria Anne Burnell A thesis submitted to The University of Birmingham for the degree of Doctor of Philosophy The School of Chemistry College of Engineering and Physical Sciences University of Birmingham August 2011 University of Birmingham Research Archive e-theses repository This unpublished thesis/dissertation is copyright of the author and/or third parties. The intellectual property rights of the author or third parties in respect of this work are as defined by The Copyright Designs and Patents Act 1988 or as modified by any successor legislation. Any use made of information contained in this thesis/dissertation must be in accordance with that legislation and must be properly acknowledged. Further distribution or reproduction in any format is prohibited without the permission of the copyright holder. Abstract Abstract This thesis presents work investigating the synthesis and characterisation of a range of mixed metal phosphates. The main aim of the project was to develop materials for the remediation of nuclear waste. In light of this, the materials developed were subject to ion exchange studies and leach testing. The thermal behaviour of the phosphates and nature of the decomposition products were also investigated. This study demonstrates that the true solid solution cannot be formed in any of the mixed metal series investigated, which included zirconium-titanium, germanium-titanium, germanium-zirconium, tin-titanium and tin-zirconium. In all cases a miscibility gap was observed and the reasons for these were established. The co-precipitates that formed were characterised by a variety of analytical techniques which included powder X-ray diffraction (PXRD), thermogravimetric analysis (TGA), pair distribution function (PDF) analysis and X-ray fluorescence (XRF). -
The Chemical Synthesis of the Crinine and Haemanthamine
molecules Review The Chemical Synthesis of the Crinine and Haemanthamine Alkaloids: Biologically Active and Enantiomerically-Related Systems that Serve as Vehicles for Showcasing New Methodologies for Molecular Assembly † Nan Hu, Lorenzo V. White, Ping Lan and Martin G. Banwell * Institute for Advanced and Applied Chemical Synthesis, Jinan University, Zhuhai 519070, China; [email protected] (N.H.); [email protected] (L.V.W.); [email protected] (P.L.) * Correspondence: [email protected] † Dedicated to the memory of our friend and colleague Professor Lew Mander FAA, FRS (1939–2020). Abstract: The title alkaloids, often referred to collectively as crinines, are a prominent group of structurally distinct natural products with additional members being reported on a regular basis. As such, and because of their often notable biological properties, they have attracted attention as synthetic targets since the mid-1950s. Such efforts continue unabated and more recent studies on these alkaloids have focused on using them as vehicles for showcasing the utility of new synthetic methods. This review provides a comprehensive survey of the nearly seventy-year history of these Citation: Hu, N.; White, L.V.; Lan, P.; synthetic endeavors. Banwell, M.G. The Chemical Synthesis of the Crinine and Keywords: alkaloid; crinine; haemanthamine Haemanthamine Alkaloids: Biologically Active and Enantiomerically-Related Systems that Serve as Vehicles for Showcasing 1. Introduction New Methodologies for Molecular The alkaloids isolated from the widely distributed herbaceous and bulbous flowering Assembly . Molecules 2021, 26, 765. plants of the amaryllis (Amaryllidaceae) family number more than five hundred and about https://doi.org/10.3390/molecules 10% of these embody the 2,3,4,4a-tetrahydro-1H,6H-5,10b-ethanophenanthridine ring sys- 26030765 tem (Figure1)[ 1]. -
PDF Final Report
Assistance to the Commission on technological, socio-economic and cost-benefit assessment related to exemptions from the substance restrictions in electrical and electronic equipment (RoHS Directive) Final report Freiburg, 12 December 2012 Öko-Institut e.V. – Institute for Applied Ecology, Öko-Institut e.V. Germany (main contractor) Freiburg Head Office P.O. Box 17 71 Carl-Otto Gensch 79017 Freiburg, Germany Street Address Yifaat Baron Merzhauser Str. 173 Markus Blepp 79100 Freiburg Phone +49 (0) 761 – 4 52 95-0 Andreas Manhart Fax +49 (0) 761 – 4 52 95-288 Katja Moch Darmstadt Office Rheinstr. 95 64295 Darmstadt, Germany Phone +49 (0) 6151 – 81 91-0 Fraunhofer Institute for Reliability and Fax +49 (0) 6151 – 81 91-133 Microintegration – IZM (subcontractor) Berlin Office Otmar Deubzer Schicklerstr. 5-7 10179 Berlin, Germany Phone +49 (0) 30 – 40 50 85-0 Fax +49 (0) 30 – 40 50 85-388 RoHS 2 exemptions evaluation Final report Table of contents 1 Background and objectives 1 2 Project set-up 2 3 Scope 2 4 Overview on the evaluation results 3 4.1 Guidance document 6 5 REACH-related aspects 7 6 Exemption request no. 3 14 6.1 Description of requested exemption 14 6.2 Applicants justification for exemption 14 6.3 Critical review 15 6.3.1 Relation to the REACH regulation 16 6.4 Recommendation 16 6.5 Specific references 17 7 Exemption request no. 4 17 7.2 Description of requested exemption 18 7.3 Applicants justification for exemption 19 7.3.1 Possible design alternatives 20 7.3.2 Possible substitute alternatives 21 7.3.3 Environmental arguments 24 7.3.4 Road map for substitution 24 7.4 Critical review 25 7.4.1 Relation to the REACH regulation 25 7.4.2 Scientific and technical practicability of lead substitution 25 7.4.3 Environmental arguments 26 7.4.4 Conclusion 26 7.5 Recommendation 27 7.6 Specific references 27 8 Exemption request no. -
Results and Discussion the 4-Bromophenacyl Esters 6 (Table VII)
A Convenient Preparation of Anhydrous Alkali Metal Thiocarboxylates Shinzi Kato*, Motohiro Oguri, and Masaru Ishida Department of Chemistry, Faculty of Engineering, Gifu University, Yanagido, Gifu 501-11, Japan Z. Naturforsch. 38b, 1585-1590 (1983); received July 5, 1983 Lithium Thiocarboxylates, Sodium Thiocarboxylates, Potassium Thiocarboxylates, Rubidium Thiocarboxylates, Caesium Thiocarboxylates A series of alkali metal thiocarboxylates (1-5) were found to be readily obtained in high yields by the reaction of thiocar boxy lie acids with metal hydrides (LiH, NaH, KH), and rubidium or caesium acetates, respectively. Their physical properties were disclosed. Alkali metal salts of thiocarboxylic acid, espe- cially lithium thiocarboxylates (la-e), sodium 2- cially anhydrous salts, are of the most important methyl- (2c), 3-methyl- (2d), and 2-chlorothio- starting materials. However, only a limited amount benzoates (2f), and rubidium 2-methylthiobenzoate of information on their preparation and spectral (4 c) are too strong hygroscopic (deliquescent) to data has been available because of their strong carry out their microanalyses. The lithium salts (1) hygroscopicity [1]. Recently, the convenient prep- are soluble in ether, but less soluble in chloroform. aration methods of a series of anhydrous alkali Surprisingly, alkali metal thiocarboxylates except metal dithiocarboxylates were developed [2]. This the lithium salts (1), especially in an anhydrous result stimulated us to develop similar convenient solid state, show very strong static electrical prop- methods for the preparation of anhydrous alkali erties. This is in sharp contrast to alkali metal metal thiocarboxylates and to compare their phys- carboxylates, which do not show such a property. ical properties. The structures of 1, 2, 3, 4, and 5 obtained here were established by IR and UV spectral data, and elemental analysis (Table VI), or by conversion to Results and Discussion the 4-bromophenacyl esters 6 (Table VII). -
United States Patent (19) 11) 4,131,743 Yoshida Et Al
United States Patent (19) 11) 4,131,743 Yoshida et al. 45 Dec. 26, 1978 (54) PROCESS FOR PREPARING 3,959,352 5/1976 Onoda .............................. 260/497. A UNSATURATED DESTERS Primary Examiner-James O. Thomas, Jr. 75 Inventors: Yoshinori Yoshida, Yokohama; Assistant Examiner-Michael Shippen Tutomu Kobayashi, Ibaraki; Attorney, Agent, or Firm-Stevens, Davis, Miller & Hironobu Shinohara, Yokohama; Mosher Izumi Hanari, Tokyo, all of Japan 57 ABSTRACT 73) Assignee: Japan Synthetic Rubber Co., Ltd., Unsaturated diesters are produced by a process which Tokyo, Japan comprises reacting, in a flowing gaseous phase, a gase 21 Appl. No.: 702,935 ous mixture comprising a conjugated diene, a carbox ylic acid and molecular oxygen in the presence of (A) a 22 Filed: Jul. 6, 1976 catalyst comprising palladium, vanadium, antimony and (30) Foreign Application Priority Data at least one alkali metal carboxylate, or in the presence of (B) a catalyst comprising palladium, vandium, anti Jul. 17, 1975 (JP) Japan. 50/86657 mony, at least one alkali metal carboxylate and at least Dec. 11, 1975 JP Japan ................................ 50/146902 one alkali metal halide. The catalyst (A) maintains a 51 int. Cl’.............................................. CO7C 67/05 high activity and a high selectivity for a long time. The 52 U.S.C. ........................................ 560/244; 560/1; catalyst (B), in which further the alkali metal halide is 560/112; 252/472 added, shows a higher activity and a higher selectivity 58 Field of Search ................... 260/497 A; 560/244, for a longer time. And its activity and selectivity are 560/1, 112 stable and durable at high temperatures such as 160 - 200 C. -
In-Situ Spectroscopic Studies of the Mechanism of Solid Super-Acid Catalysed Methanol Carbonylation
In-situ spectroscopic studies of the mechanism of solid super-acid catalysed methanol carbonylation Lee D. Dingwall Submitted for the degree of Doctor of Philosophy University of York Department of Chemistry July 2010 Acknowledgements I would like to thank BP Chemicals and the EPSRC for funding this PhD research. For Supervision and helpful discussions throughout the project, thanks go to Professor Adam Lee, Dr Karen Wilson and Dr Jason Lynam at the University of York and Drs Jon Deeley, Glenn Sunley and David Law (and the rest of my colleagues at BP Chemicals) at the BP Chemicals site in Hull. Thank you to Durham Solid State NMR service, the Swansea Mass Spectrometry Service, MEDAC and Dr Nigel Young for providing some analytical data discussed herein. I would also like to thank The University of York Chemistry workshops for support with construction and maintenance of in-house equipment, as well as Drs Luca Olivi and Andrea Cognigni for their support with XAFS measurements at the Sincrotrone in Trieste. Thank you to the University of York for providing a comfortable and dynamic environment for my personal development, and all of my colleagues and friends (of whom there are too many to mention here, but are written in white ink in the background of this thesis – as promised) who made my time so enjoyable. On the academic side, I would particularly like to thank the York Surface Science and Catalysis group who have recently moved to join the Cardiff Catalysis Institute and the SLUG research group, and wish all current members every success for the future. -
Kiran Light Laboratories 2012-13 Final
PRICE LIST 2012-13 (Distributor for KEM LIGHT LABORATORIES & KEMIE LABS) www.labchemindia.com SPECIAL PRICE LIST (Distributor for KEM LIGHT LABORATORIES & KEMIE LABS) www.labchemindia.com INDIA- 2012-13 ( Product Name Grade Code Quantity D/P Rs ) ABSCISIC ACID 98% LPR A00110B03 25 mg 322 ABA * (+)-cis,trans-abscisic acid ,abscisin II; dormin; LPR A00110B04 100 mg 980 (2Z,4E)-5-[(1S)-Hydroxy-2,6,6-trimethyl-4-oxo-2-cyclohexen-1-yl]-3-methyl-2,4-pentadienoic acid LPR A00110B06 500 mg 5075 LPR A00110B07 1 gm 9205 ABSCISIC ACID 98+% APR A00110A03 25 mg 437.5 ABA * (+)-cis,trans-abscisic acid ,abscisin II; dormin; APR A00110A04 100 mg 1225 (2Z,4E)-5-[(1S)-Hydroxy-2,6,6-trimethyl-4-oxo-2-cyclohexen-1-yl]-3-methyl-2,4-pentadienoic acid APR A00110A06 500 mg 5950 APR A00110A07 1 gm 10465 ACENAPTHENE 96% EPR A00200C12 100 gm 154 (1,8-Ethylenenaphthalene) EPR A00200C14 500 gm 490 ACETANILIDE 98% EPR A00700C13 250 gm 73.5 (N-Phenylacetamide Antifebrin; Acetylaniline; Acetylaminobenzene) EPR A00700C14 500 gm 140 ACETANILIDE 98% LPR A00700B13 250 gm 98 (N-Phenylacetamide Antifebrin; Acetylaniline; Acetylaminobenzene) LPR A00700B14 500 gm 189 ACETO CARMINE See Carmine Aceto ACETYLACETONE 97% EPR A00900C13 250 ml 231 (2,4-Pentanedione, Diacetylmethane) EPR A00900C14 500 ml 451.5 ACETYLACETONE 98% LPR A00900B13 250 ml 280 (2,4-Pentanedione ,Diacetylmethane) LPR A00900B14 500 ml 525 ACETYLCHOLINE CHLORIDE 98% LPR A01250B10 25 gm 1170 (Ach ,2-(Acetyloxy)-N,N,N-trimethylethanaminium chloride) LPR A01250B12 100 gm 4050 ACETYLCHOLINE CHLORIDE 99% APR A01250A10 -
(12) United States Patent (10) Patent No.: US 9,334,465 B2 Fernandez Prieto Et Al
USOO9334465B2 (12) United States Patent (10) Patent No.: US 9,334,465 B2 Fernandez Prieto et al. (45) Date of Patent: May 10, 2016 (54) STRUCTURING USING AN EXTERNAL USPC .................................................. 510/535, 353 STRUCTURANT AND A COSMOTROPE See application file for complete search history. (71) Applicant: The Procter & Gamble Company, (56) References Cited Cincinnati, OH (US) U.S. PATENT DOCUMENTS (72) Inventors: Susana Fernandez Prieto, Benicarlo 5,916,967 A * 6/1999 Jones ..................... A61K 8,731 (BE); Johan Smets, Lubbeek (BE); 510/405 Vincent Josep Nebot Carda, Vila Real 8,222, 197 B2* 7/2012 Fernandez Prieto . C07C 237/22 510,303 (ES); Beatriu Escuder Gil, Sant Mateu 8,236,748 B2* 8/2012 Fernandez Prieto . C07C 237/22 (ES); Juan Felipe Miravet-Celades, 510,501 Castellon (ES) 2008/0057005 A1 3/2008 Lehn et al. 2008, 0087293 A1* 4, 2008 Glenn ................ A45D 19,0008 132/210 (73) Assignee: The Procter & Gamble Company, 2009, O124.533 A1 5, 2009 Kottke et al. Cincinnati, OH (US) 2011/0166291 A1 7, 2011 Turk et al. 2011 O220537 A1* 9, 2011 Fernandez-Prieto CO7C 237/22 (*) Notice: Subject to any disclaimer, the term of this 206,524.7 patent is extended or adjusted under 35 2011/0223125 A1* 9/2011 Hough ................. A61K 8,8152 424.70.12 U.S.C. 154(b) by 0 days. 2011/0224124 A1* 9, 2011 Fernandez Prieto ... CO7C 237/22 510/405 (21) Appl. No.: 14/106,891 2011/0243873 A1* 10/2011 Hough ..................... A61K 8.91 424.70.16 (22) Filed: Dec. 16, 2013 2011/0256085 A1 * 10/2011 Talingting Pabalan A61 K8/042 424.70.13 (65) Prior PublicationO O Data 2013/0029894 A1 1/2013 Bettiol ................ -
In Organic Salts Solubility Table
Copyright © Tarek Kakhia. All rights reserved. http://tarek.kakhia.org In Organic Salts Solubility Table A Substance Formula 0 °C 20 °C 40 °C 60 °C 80 °C 100 °C Actinium (III) hydroxide Ac(OH)3 0.0021 Aluminium chloride AlCl3 43.9 45.8 47.3 48.1 48.6 49.0 Aluminium fluoride AlF3 0.56 0.67 0.91 1.1 1.32 1.72 Aluminium hydroxide Al(OH)3 0.0001 Aluminium nitrate Al(NO3)3 60 73.9 88.7 106 132 160 Aluminium perchlorate Al(ClO4)3 122 133 Aluminium sulfate Al2(SO4)3 31.2 36.4 45.8 59.2 73 89.0 Ammonia (Unit:mL/mL) NH3 1176 702 428 252 138 88 Ammonium acetate NH4C2H3O2 102 143 204 311 533 Ammonium azide NH4N3 16 25.3 37.1 Ammonium benzoate NH4C7H5O2 21.3 83 Ammonium bicarbonate NH4HCO3 11.9 21.7 36.6 59.2 109 Ammonium bromide NH4Br 60.6 76.4 91.2 108 125 145 Ammonium carbonate (NH4)2CO3.H2O 55.8 10 dec Ammonium chlorate NH4ClO3 28.7 Ammonium chloride NH4Cl 29.4 37.2 45.8 55.3 65.6 77.3 Ammonium hexa chloro platinate (NH4)2PtCl6 0.289 0.499 0.815 1.44 2.16 3.36 Ammonium chromate (NH4)2CrO4 25 34 45.3 59.0 76.1 Ammonium di chromate (NH4)2Cr2O7 18.2 35.6 58.5 86.0 115 156 1 Copyright © Tarek Kakhia. All rights reserved. http://tarek.kakhia.org Ammonium di hydrogen arsenate NH4H2AsO4 33.7 48.7 63.8 83 107 Ammonium di hydrogen phosphate NH4H2PO4 22.7 37.4 56.7 82.5 118.3 173.2 Ammonium fluoride NH4F 100 Ammonium fluorosilicate (NH4)2SiF6 12.28 18.6 31.6 40.4 75℃:48.1 61.0 Ammonium formate NH4HCO2 102 143 204 311 533 Ammonium hydrogen phosphate (NH4)2HPO4 42.9 68.9 81.8 97.2 110 121 Ammonium hydrogen sulfate NH4HSO4 100 Ammonium hydrogen tartrate NH4HC4H4O6 -
Investigation of Crown Ether Cation
Investigation of crown ether cation- systems using electrophoretic NMR Fredrik Petersson physical Chemistry royal institute of technology (KTH) Stockholm Sweden Supervisor Marianne Giesecke Examiner prof Istvan´ Furo´ Stockholm June 29, 2012 Abstract The purpose of this thesis was to investigate how crown ethers behave and interact with different cations and to optimise the setup of the electrophoretic NMR. To get a good electrophoretic NMR measurement the electrophoretic phase shift needs to be big. To increase the phase shift some parameters needed to be adjusted, parameters such as the concentration of crown ether and cation, the duration of magnetic field gradient pulse δ, the magnetic field gradient strength g,the diffusion time Δ and the applied voltage V. The main focus then put on crown ethers 15-crown-5 and 18-crown-6. The cations used were lithium (Li), sodium (Na), potassium (K), caesium (Cs), calcium (Ca) and barium(Ba). The effective charge was obtained by using pulsed gradient NMR to derive the diffusion coefficient and electrophoretic NMR to get the electrophoretic mobility. These data were used to calculate the equilibrium constant of the formed complex. The outcome of the investigation: the affinity for 18-crown-6 was in the following order barium > potassium > caesium > sodium > calcium > lithium and for 15-crown-5 barium > sodium > calcium > caesium > potassium > lithium. Sammanfattning Syftet med denna avhandling var att unders¨oka hur kronetrar beter sig och inter- agerar med olika katjoner och optimera den elektroforetiska NMR upps¨attningen, F¨or att f˚a en bra elektroforetiska NMR m¨atning m˚aste fasskiftet vara stort.