M32, Bristol, UK
Total Page:16
File Type:pdf, Size:1020Kb
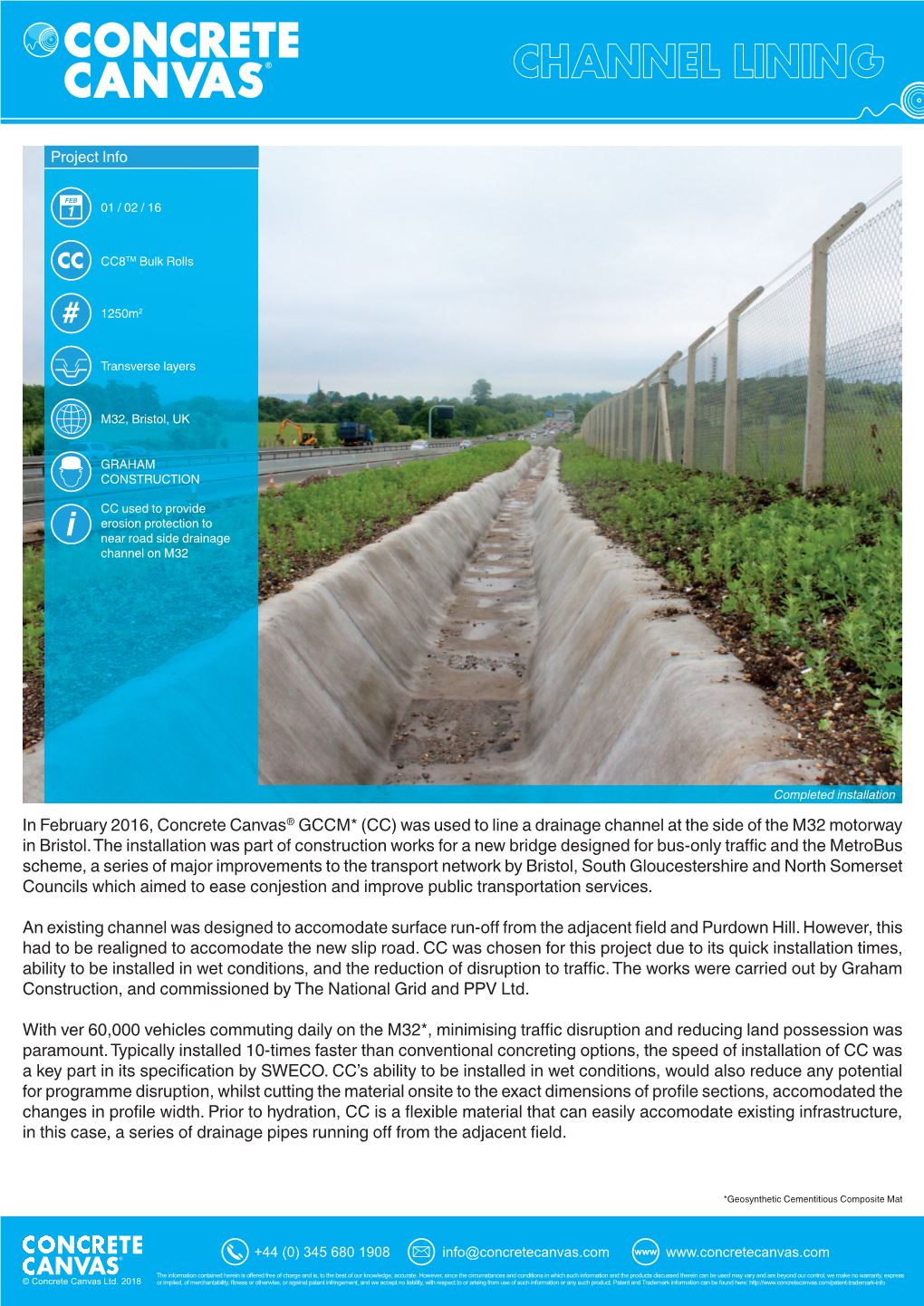
Load more
Recommended publications
-
Particulars Do Not Form Part of Any Offer Or Contract and Must Not Be Relied Upon As Statements Or Representations of Fact
NORFOLK HOUSE / BRISTOL / BS2 8RQ www.nohobristol.com BRISTOL Bristol boasts a world-class “ knowledge and financial based economy and is recognised as one of the UK’s creative, tech and media hotspots.” THE NOHO NINE Classic Facade¸ with Creative Finishes for a Chic Feel BRISTOL. The city of Bristol continues to grow at an exponential rate with regeneration projects planned across the entire city. The development of Bristol Temple Quarter is a sustainable and flourishing urban new quarter and a brand new Redcliff Quarter set to have some of the best bars, restaurants and shopping in the city. The existing Cabot Circus, is deemed “the best shopping centre in Europe” and all of this is just a short walk from NOHO. The larger urban area population is estimated to be 1.6 million and is amongst the most attractive, successful and culturally prestigious cities in the UK, enjoying a rising profile within Europe and beyond. It is one of the UK’s fastest growing cities economically. Bristol has a relatively young population profile with the median age of people living in Bristol standing at 32.5 years. The City is an ideal place for regeneration with a distinct identity as Bristol’s independent retail centre with a growing population of professionals and young families. THE MATTHEW, BRISTOL HARBOUR Bristol has a long association with the 'green' movement and is proud of its status as a Green Capital. Not only is it the UK's first Cycling City, Bristol is also a Fair trade City which sees it trading fairly with nearly five million workers in 58 developing countries. -
Thyssen Mining Report 2002
www.thyssen-schachtbau.com THYSSEN SCHACHTBAU GROUP Report 2002 THYSSEN SCHACHTBAU GROUP SCHACHTBAU THYSSEN www.thyssen-schachtbau.com 2002 Content MINING GERMANY CONSTRUCTION GERMANY 1 Situation update DIG 48 High-lustre mesh proves to be a brilliant TS Mining solution in every way 5 AV 8 – A symbol for the future TS Bau GmbH TS Shaft Sinking and Drilling 51 Riesa gets new youth training centre 9 Tunnelling through frozen sand 52 One thousand years of shipping on the river Saale 10 Controlled fall is the shortest route to the shaft 55 New road scheme looks to the future 13 Ventilation borehole doubles as coal clearance shaft DIG 56 Interior design by DIG provides the TS Mining finishing touch 14 Combination support system proves its worth TS Bau GmbH as an all rounder 58 Gohlis Bypass gets the traffic moving again TS Shaft Sinking and Drilling 60 Regeneration of high-profile refuse site 20 Mechanised sinking of the Primsmulde upcast 62 Duisburg’s new coal import terminal shaft sets new raise boring and shaft boring records (1,260 m) CONSTRUCTION INTERNATIONAL Central Services · Work Safety Östu-Stettin 24 Trend reversal but TS still tops safety league 64 „Knoten Rohr“ relieves rail congestion 66 Vienna underground extension line poses MINING INTERNATIONAL engineering challenge TMCC Östu-Stettin – Tunnelbau 26 McArthur River –Year 9, Ongoing Infrastructure 69 Kaprun Hydroelectric plant: New poser descent Development stage is a triumph of environmental engineering TS Shaft Sinking and Drilling Stettin Hungaria 30 Constructing underground sealings and dams 72 Casinos Ausztria in the MAGYAR MÜVELÖDÈS HÀZA in the Potash and Rock-Salt Industry TGB Construction Division 74 Avon Ring Road TGB 78 Thyssen Construction Ltd. -
2016 Air Quality Annual Status Report (ASR)
South Gloucestershire Council 2016 Air Quality Annual Status Report (ASR) In fulfilment of Part IV of the Environment Act 1995 Local Air Quality Management October 2016 LAQM Annual Status Report 2016 South Gloucestershire Council Local Authority Sally Radwell Officer Department Environment & Community Services Environmental Protection, PO Box 299, Address Civic Centre, High Street, Kingswood, Bristol BS15 0DR Telephone 01454 868001 E-mail [email protected] Report Reference SGC_ASR_2016 number Date October 2016 LAQM Annual Status Report 2016 South Gloucestershire Council Executive Summary: Air Quality in Our Area Air pollution is associated with a number of adverse health impacts. It is recognised as a contributing factor in the onset of heart disease and cancer. Additionally, air pollution particularly affects the most vulnerable in society: children and older people, and those with heart and lung conditions. There is also often a strong correlation with equalities issues, because areas with poor air quality are also often the less affluent areas1, 2. The annual health cost to society of the impacts of particulate matter alone in the UK is estimated to be around £16 billion3. The Council has a duty to review and assess air quality within its district under the Part IV of the Environment Act 1995 and this Annual Status Report has been prepared to fulfil this requirement. Air pollutants can arise from a variety of sources, including transport and industry. Pollutant levels are assessed against health-based national air quality objectives. Where the objectives are not met, Air Quality Management Areas (AQMAs) must be declared and an Action Plan put in place to improve the air quality in these areas. -
Cubem4 Vantage Final.Pdf
OFFICES FOR SALE / TO LET Old Gloucester Road, Parkway, Bristol BS16 1FX ■ Highly specifi ed self-contained o ces with air conditioning ■ Located between the M4/M5 interchange & M32 motorways ■ Suites of 1,650–7,109 sq ft, with 20 car parking spaces ■ Built in 2006, fully refurbished in Spring 2017 M4/M5 INTERCHANGE CUBE M4, OLD GLOUCESTER ROAD, PARKWAY, BRISTOL BS16 1FX NEW STOKE GIFFORD BYPASS M4 M32/M4 INTERCHANGE M32 WHY CUBEM4, Parkway Parking Bristol Parkway for 20 cars Train Station 20 minutes walk M4/M5 interchange 5 minutes drive Pub lunch Winter Stream Farm pub/restaurant 2 minutes walk Shopping Tesco Extra 7 minutes drive MetroBus coming 2017 Bus stop 4 minutes walk. Buses every Superfast 10 minutes – Fibre Internet shorter journey times Connection in with dedicated lanes place on park CUBE M4, OLD GLOUCESTER ROAD, PARKWAY, BRISTOL BS16 1FX LOCATION AND AMENITIES M5 MetroBus route: CUBEM4 is situated on the MetroBus - coming 2017 Old Gloucester Road within 15 North Bristol approximately 1.4 miles from Parkway railway 20 station, 2 miles from junction 1 16 D A of M32 motorway and 4 miles Tesco Extra supermarket AZTEC O R WEST R from junction 16 of the M5. E A38 T B S R E A C M5 D U L O E L Y Woodlands Golf & Country Club G S T D O M4 L K O M5 BRADLEY E 2 CRIBBS M48 1 A38 W STOKE A CAUSEWAY D Y B4427 2 A O M48 THORNBURY R 21 1 M4 22 M4 R 15 E A403 A38 20 T 16 S 21 M4 E M4 22 M5 M5 C B4057 M49 19 M4 18 U 15 A4174 17 1 O 16 20 A403 L M4 18 2 G M49 17 AZTEC A4018 WEST A432 M5 M32 A46 19 A38 A4174 M5 18A A4018 1 18 FILTON 3 M32 19 -
Joint Local Transport Plan 3 – Progress Report 2016
West of England Joint Local Transport Plan 3 Progress Report 2015/16 1. Introduction In the Joint Local Transport Plan 3 (JLTP3) we said that we would produce an annual report on progress made in delivering transport improvements. This report outlines what was delivered in 2015/16 and how we performed against our targets and indicators. 2. Major Schemes In late 2011 the Department for Transport (DfT) agreed to make available £135m towards the cost of five major schemes in the West of England and during 2015/16 we continued to focus our efforts on progressing delivery of these substantial infrastructure projects: Bath Transportation Package The great news is this scheme was substantially complete by the end of March 2016 with the final 17 bus shelters and 12 stops, junction upgrades including Charles Street/Monmouth Street and the Lower Borough Walls and Stall Street pedestrian improvements installed. MetroBus Ashton Vale to Temple Meads Key achievements in 2015/16 include: Permanent guideway works next to the Create Centre and on-highway works on Smeaton Road/Cumberland Road and the busway on Ashton Fields started. Completion of the Redcliffe Hill inbound works and commencement of outbound works. Flood defence wall construction on Cumberland Road. Ashton Avenue Swing Bridge shot-blasting. Qualifying tenders returned for Bathurst Basin Bridge work, and Network Rail over-bridge agreement completed. MetroBus refurbishment works on Ashton Avenue Swing Bridge North Fringe to Hengrove Package Diggers went on site in early August 2015 and works are now well progressed with over a year left to run in the construction programme. -
Frome Valley Walkway Hambrook to City Download
1 Frome Valley Walkway - Distance: 6 /2 miles Walking Time: 3 hours 14 Hambrook to City GRADE : Easy 2 The Frome Valley Walkway is an 18 mile (29km) long path that follows Maps: the River Frome from the Cotswolds Hills near Old Sodbury to the centre Explorer 155 Bristol & Bath of Bristol where it joins the River Avon. This walk explores the section 1:25 000 scale from Hambrook to the city centre as the path passes through the pretty Explorer 167 Thornbury, Dursley, village of Frenchay and landscaped parks in Bristol including Oldbury & Yate Court Estate, originally an old hunting lodge within the Royal Forest of 1:25 000 scale Landranger 172 Bristol & Bath Kingswood. The route mostly follows off-road tarmac paths close to the 1:50,000 scale river or pavements for short sections in the city. Between Hambrook and Grid Ref: (start of walk) 664 707 Frenchay the path wanders through riverside woodlands and runs over both surfaced and unsurfaced paths. PUBLIC TRANSPORT INFORMATION Bus Services 328 and X30 from Bristol to Yate via Hambrook both operate hourly Monday to Saturday. Service 329 operates to Yate every two hours on Sundays and Bank Holidays. We recommend you check your journey times by logging on to www.firstgroup.com or by calling the Traveline number below. PUBLIC HOUSES/CAFES EN ROUTE PUBLIC TOILETS EN ROUTE Crown Inn, Hambrook 0117 956 6701 Oldbury Court Estate The White Horse, Hambrook 0117 956 6902 Snuff Mill The Hambrook, Hambrook 0117 957 1510 Eastville Park The Masons Arms 0117 939 3919 Castle Park The White Lion, Frenchay 0117 956 8787 Merchant Arms, Eastville Park 0117 951 8771 The Old Fox Inn 0117 952 2674 Numerous pubs and cafes, Bristol City Centre FURTHER INFORMATION Information for this walk has been taken from the Frome Valley Walkway leaflet, this describes the route from the centre of Bristol to the Cotswolds Hills. -
Aeb6-2D26570fe208
Contents VISION 1 CHAPTER 5 WIDENING CHOICE 41 CHAPTER 1 INTRODUCTION 3 Moving People 41 Success to date 3 Public Transport 41 Community Involvement and Participation 3 Buses 41 Focused Participation 4 Bus-Based Park & Ride 45 Joint Working with Neighbouring Authorities 5 Community Transport 45 A Radical Strategy 7 Taxis 47 Working Towards the Solution: Key Elements 7 Coaches 48 Centre of Excellence Bid 8 Rail 49 CHAPTER 2 OBJECTIVES 11 Light Rapid Transit 52 National Guidance 11 Bristol Electric Railbus 56 Local Transport Plan Objectives 11 Ferries 58 European Objectives 11 Interchange 58 Air Quality Management 11 Benign Modes 59 Regional objectives 13 Walking 59 Former Avon Area 13 Cycling 63 Bristol Local Transport Plan 13 Safer Routes to School (and case study) 68 (including user priority groups) Disabled People 74 Social Exclusion (and case studies) 76 CHAPTER 3 PROBLEMS AND 17 Airport Surface Access Strategy 80 OPPORTUNITIES Community Car Clubs 80 Motorised Modes 81 CHAPTER 4 STRATEGY 29 Cars 81 Introduction 29 Powered Two Wheelers 82 The link between strategy and 29 Moving Goods 83 the 5 year programme Rail Freight 83 Five Year Plan 31 Road Freight 83 Technical Assessment of 32 Ports 86 Preferred Strategy (and case study) Waterways 86 Presenting the programme in detail 32 Major Highway Improvements 87 Callington Road Link 87 A38 to A370 Link 89 The image of the Rubik’s Cube® is used by permission of Severn Towns Ltd, London, England. Maps contained within this document are based upon the Ordnance survey mapping with the permission of the Controller of Her Majesty’s Stationery Office © Crown copyright. -
Archaeological Review No. 36 2011
Trans. Bristol & Gloucestershire Archaeological Society 130 (2012), 307–332 Archaeological Review No. 36 2011 Edited by JAN WILLS and JON HOYLE The Archaeological Review presents brief summaries of archaeological research, fieldwork and building recording undertaken during the year. Information is arranged mostly by civil parishes (as shown on the OS 1:10,000 series maps) with the parish name followed by the site name or description and grid reference. For the cities of Bristol and Gloucester entries are arranged by street or area. Contributions for the next review should be sent to the Archaeology Service, Gloucestershire County Council, Shire Hall, Gloucester, GL1 2TH. Abbreviations AA Absolute Archaeology AAU Avon Archaeological Unit AOC AOC Archaeology ARS Archaeological Research Services Ltd. ArScn Archeoscan BA Benchmark Archaeology BaRAS Bristol and Region Archaeological Services BUSAS Bournemouth University School of Applied Sciences CA Cotswold Archaeology CADHAS The Campden and District Historical and Archaeological Society CHHC Castle House Heritage Consulting FA Foundations Archaeology GADARG Gloucester and District Archaeological Research Group GCCAS Gloucestershire County Council Archaeology Service HA Headland Archaeology JMHS John Moore Heritage Services LHA Lawrence Hayes Associates MA Monmouth Archaeology NA Northamptonshire Archaeology NT The National Trust OAS Oxford Archaeology South TVAS Thames Valley Archaeological Services WHEAS Worcestershire Historic Environment and Archaeology Service 110 Arch 110 Archaeology AMPNEY CRUCIS, Happy Lands, Wiggold, SP 04500530. A single 20m2 evaluation trench was hand-excavated across the western perimeter of an oval enclosure measuring c. 60m × 45m which had first been recognised as a cropmark by O.G.S. Crawford in 1931. Geophysical surveys in 307-332 Archaeological Review.indd 307 19/02/2013 13:58 308 archaeological review 2011 2010 and 2011 suggested the presence of two roughly concentric rings of interrupted ditches and a possible entrance opening to the east. -
The M25 Motorway (Junctions 6
90 THE LONDON GAZETTE FRIDAY 1 APRIL 2011 SUPPLEMENT No. 1 The M25 Motorway (Junctions6-5,Clacket Lane) The M40 Motorway (Junction 10, Oxfordshire) (Temporary Restriction of Traffic) Order 2011 No. Northbound Entry Slip Road (Temporary Restriction 2011/359. - Enabling power: Road Traffic Regulation Act and Prohibition of Traffic) Order 2011 No. 2011/267.- 1984, s. 14 (1) (a). - Issued: 16.02.2011. Made: Enabling power: Road Traffic Regulation Act 1984, s. 14 07.02.2011. Coming into force: 26.02.2011. Effect: None. (2) (b). - Issued: 11.02.2011. Made: 26.01.2011. Coming Territorial extent & classification: E. Local. - Available at into force: 02.02.2011. Effect: None. Territorial extent & http://www.legislation.gov.uk/uksi/2011/359/contents/mad classification: E. Local. - Available at e Non-print http://www.legislation.gov.uk/uksi/2011/267/contents/mad The M25 Motorway (Junctions8-9)(Temporary e Non-print Restriction and Prohibition of Traffic) Order 2011 No. The M42 Motorway (Junction 2) (Southbound Entry 2011/204. - Enabling power: Road Traffic Regulation Act Slip Road) (Temporary Prohibition of Traffic) Order 1984, s. 14 (1) (a). - Issued: 04.02.2011. Made: 2011 No. 2011/355. - Enabling power: Road Traffic 24.01.2011. Coming into force: 29.01.2011. Effect: None. Regulation Act 1984, s. 14 (1) (a). - Issued: 15.02.2011. Territorial extent & classification: E. Local. - Available at Made: 02.02.2011. Coming into force: 09.02.2011. Effect: http://www.legislation.gov.uk/uksi/2011/204/contents/mad None. Territorial extent & classification: E. Local. - e Non-print Available at The M25 Motorway (Junctions 9 - 10) (Temporary http://www.legislation.gov.uk/uksi/2011/355/contents/mad Restriction and Prohibition of Traffic) Order 2011 No. -
2012 No. 1381 ROAD TRAFFIC the M4 Motorway, the M5 Motorway, The
STATUTORY INSTRUMENTS 2012 No. 1381 ROAD TRAFFIC The M4 Motorway, the M5 Motorway, the M48 Motorway and the M32 Motorway (Temporary Restriction of Traffic) Order 2012 Made - - - - 18th May 2012 Coming into force - - 21st May 2012 WHEREAS the Secretary of State for Transport, being the traffic authority for the M4 Motorway (“the M4”), the M5 Motorway (“the M5”), the M48 Motorway (“the M48”), the M32 Motorway (“the M32”) and connecting roads, is satisfied that traffic on lengths of those roads and some of those connecting roads in South Gloucestershire and in the City of Bristol should be restricted because works are being executed thereon: NOW, THEREFORE, the Secretary of State, in exercise of the powers conferred by section 14(1)(a) of the Road Traffic Regulation Act 1984(a), hereby makes the following Order:- 1. This Order may be cited as the M4 Motorway, the M5 Motorway, the M48 Motorway and the M32 Motorway (Temporary Restriction of Traffic) Order 2012 and shall come into force on 21st May 2012. 2. In this Order – “the lengths of the motorways” means (i) the eastbound carriageway of the M4 between Junctions 22 and 18 from a point at the centre of Holme Road Overbridge to a point at the centre of Bromley Heath Road Underbridge; (ii) the westbound carriageway of the M4 between Junctions 18 and 21 from a point at the centre of the A432 Badminton Road Underbridge to a point at the centre of the A38 Gloucester Road Overbridge; (iii) the eastbound carriageway of the M48 from a point at the centre of the Ingst Road Overbridge (east of Junction -
Triangle West, Clifton, Bristol, BS8 1EJ
Triangle West, Clifton, Bristol, BS8 1EJ ENTER A LANDMARK BUILDING FACILITIES PROVIDED SITUATED Clifton Heights is one of Bristol’s - Newly refurbished including comfort cooling landmark office buildings, offering - Shower facilities IN THE HEART modern office accommodation on - 4 lifts 14 floors with stunning views - 24 hour access OF BRISTOL across the city. - Secure parking - Security system with 24/7 call out service - Cycle Storage ABOUT UNDER OFFER AVAILABILITY FLOOR 1 1 N 1st floor availability: 2,128 – 6,553 sq ft 1.1 1st FLOOR PLAN (WHOLE FLOOR) UNDER OFFER AVAILABILITY FLOOR 1 1 N 1st floor availability: 2,128 – 6,553 sq ft 1.2 1st FLOOR PLAN (WHOLE FLOOR) AVAILABILITY FLOOR 2 2 N 2nd floor Availability: 1,550 – 8,870 sq ft 2.1 2nd FLOOR PLAN AVAILABILITY FLOOR 2 2 N 2nd floor Availability: 1,550 – 8,870 sq ft 2.2 / 2.3 2nd FLOOR PLAN AVAILABILITY FLOOR 2 2 N 2nd floor Availability: 1,550 – 8,870 sq ft 2.4 2nd FLOOR PLAN AVAILABILITY FLOOR 2 2 N 2nd floor Availability: 1,550 – 8,870 sq ft 2.5 2nd FLOOR PLAN AVAILABILITY FLOOR 3 3 N 3rd floor Availability: 701 – 2,000 sq ft South Suite – 186 sqm (2,000 sq ft) S S 3rd FLR N AVAILABILITY FLOOR 3 3 N 3rd floor Availability: 701 – 2,000 sq ft North East Suite – 65 sqm (701 sq ft) North Suite 3rd FL AVAILABILITY FLOOR 4 4 N 4th floor Availability: 2,000 sq ft South Suite – 186 sqm (2,000 sq ft) South Suite 4th FL PROMINENTLY LOCATED ON YOUR Clifton is a prime business The City Centre and public location, home to a number transport are readily accessible, DOORSTEP of major professional, media as is the M32 motorway which and marketing occupiers. -
AUCTION RESULTS 19Th April 2018
AUCTION RESULTS 19th April 2018 Property Auction The Bristol Pavilion, County Ground, Nevil Road, Bishopston, Bristol, BS7 9EJ Thursday 19th April 2018 at 7.00pm Maggs & Allen Auction I 19th April 2018 LOT 7 West Street, Kingswood, Bristol BS15 8JJ 1 Mid-Terraced House for Renovation Mid-terraced 2 bedroom Victorian house in need of renovation, situated in a convenient residential location providing easy access to the shops and amenities on Kingswood high street. Guide Price: £135,000+ SOLD FOR £193,000 LOT 2 Merlin Close, Westbury on Trym, Bristol BS9 3PA 2 Potential Development Site A 2 bedroom prefabricated bungalow in need of modernisation, situated in a highly sought after residential location within close proximity to Westbury-On- Trym village. The property occupies a large corner plot offering the potential to demolish the existing bungalow and replace with a larger detached bungalow or potentially two bungalows, subject to obtaining the necessary planning consents. Guide Price: £150,000+ SOLD FOR £215,000 LOT Undercroft Parking Space Balloon Court, 18 Cave Street, 3 St Pauls, Bristol BS2 8AG Secure Parking Space in Central Bristol A secure undercroft parking space in a modern development of apartments in St Pauls. The parking space is situated in an excellent central location and provides easy access to the city centre and Cabot Circus shopping centre. Guide Price: £5,000-£10,000 SOLD PRIOR 1 Cherrytree Crescent, Fishponds, Bristol BS16 4ES LOT End Terraced House - Planning for Two Further Flats 4 3 bedroom semi-detached house occupying a large corner plot with full planning consent granted for two 1 bedroom flats to adjoin the existing property.