What Is Lean Manufacturing ?
Total Page:16
File Type:pdf, Size:1020Kb
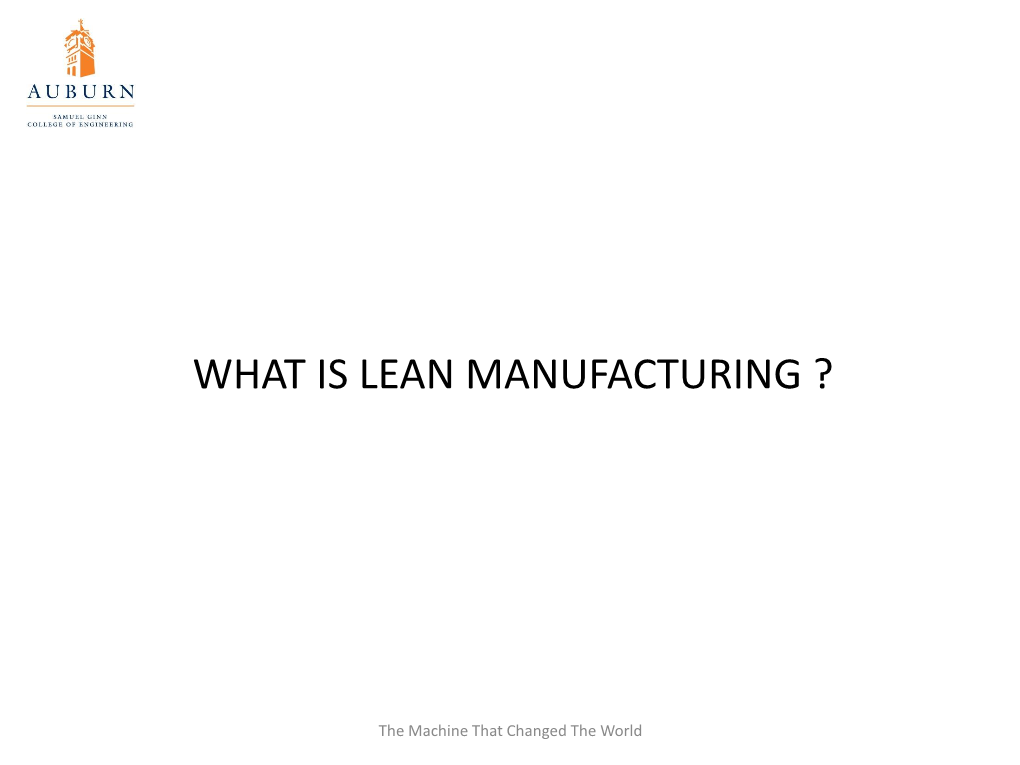
Load more
Recommended publications
-
Taiichi Ohno's Workplace Management: Special 100Th Birthday Edition
“This book brings to us Taiichi Ohno’s philosophy of workplace management— the thinking behind the Toyota Production System. I personally get a thrill down my spine to read these thoughts in Ohno’s own words. My favorite part is his discussion of the misconceptions hidden within common sense and how management needs a revolution of awareness.” Dr. Jeffrey Liker Director Japan Technology Management Program University of Michigan Author, The Toyota Way “While no one person invented lean, no one is given more credit than Taiichi Ohno. Access to his true thoughts and ideas are rare, and this book is the best and most useful of Ohno’s work. Many lean students would want nothing more than to spend a day with Taiichi Ohno walking through their plant. This book is the closest thing we have left to that experience. Jon Miller has done a diligent job, not just in translation, but ensuring that the true meaning comes through in a readable fashion. You truly feel as if you are in conversation with the father of the Toyota Production System. While this book won’t paint a clear picture of what to do next on your lean journey, it should be required reading for any serious student of the subject.” Jamie Flinchbaugh Co-author, The Hitchhiker’s Guide to Lean: Lessons from the Road “This book and its translation provide the reader a wonderful opportunity to learn directly from the master architect of the Toyota Production System. One is able to hear, in his own words, the principles that have evolved into the most successful management method ever developed. -
SC2020: Toyota Production System & Supply Chain
SC2020: Toyota Production System & Supply Chain by Macharia Brown Bachelor of Science in Comparative Politics United States Military Academy, West Point 2003 Submitted to Zaragoza Logistics Center in Fulfillment of the Requirement for the Degree of Master of Engineering in Logistics and Supply Chain Management at the Zaragoza Logistics Center June 2005 © 2005 Brown, Macharia. All rights reserved The author hereby grant to M.I.T and ZLC permission to reproduce and to distribute publicly paper and electronic copies of this thesis document in whole or in part. Signature of Author Zaragoza Logistics Center May 10th, 2005 Certified by Prashant Yadav, PhD ZLC Thesis Supervisor Approved by Larry Lapide, PhD. Research Director, MIT-CTL Brown, TPS 0 Toyota Production System & Supply Chain by Macharia Brown Bachelor of Science in Comparitive Politics United States Military Academy, West Point 2003 Submitted to Zaragoza Logistics Center in Fulfillment of the Requirement for the Degree of Master of Engineering in Logistics and Supply Chain Management Abstract Over the past 50 years Toyota created and honed a production system that fostered its ascension in the automotive industry. Furthermore, the concepts that fuel Toyota’s production system extend beyond its manufacturing walls to the entire supply chain, creating a value chain where every link is profitable with an unwavering focus on teamwork, communication, efficient use of resources, elimination of waste, and continuous improvement. This report is a part of MIT’s Supply Chain 2020 (SC2020) research project focusing on Toyota’s production system and supply chain. The study begins by examining the automotive industry, evolution of top 5 automotive companies, and Toyota’s positioning against its main competitors. -
The Impact of a Collaborative Planning Approach on Engineering Construction Performance
The Impact of a Collaborative Planning Approach on Engineering Construction Performance VINCE HACKETT An abridged Thesis submitted in partial fulfilment of the requirements of Nottingham Trent University for the degree of Doctor of Philosophy August 2017 ACKNOWLEDGEMENT Completion of this thesis was made possible by the help, advice, guidance and encouragement of many people in the last four years. I would like to thank my academic supervisors – Christine Pasquire, Roy Stratton, Andrew Knight and UWA academic advisor David Day, for their contribution to the research and help above and beyond what could be reasonably expected. Also, my industrial supervisor Neil Maxfield for his kindness, patience, mentoring and the demonstration of what true transformation leadership looks like, my KGP mentor Mike Watson, for his help, wit and wisdom. Also to some of the true “heroes” of the lean implementation process, Ropes, Paris, Dobbie, Robbo, George and Simon for their good humour and generosity, whose tall tales must be true, for who could make those stories up. Finally, I wish to dedicate this thesis to my wife and love of my life Annamaria. I could not have started, never mind finished this journey without you. I ABSTRACT The thesis presents the findings from the longitudinal implementation of lean construction on the ongoing refurbishment of an integrated liquefied natural gas (LNG) plant in North Western Australia. Refurbishment of existing plant is a sub-sector of the Engineering Construction (EC) industry, an industry involved in the design and construction of large-scale industrial facilities including oil and gas plants. The sector is called engineering construction in the United Kingdom and Australia and industrial construction in the United States and Canada. -
A Brief Investigation Into the Origins of the Toyota Production System
A Brief Investigation into the Origins of the Toyota Production System July 2006 Draft 1.0 Art Smalley President Art of Lean, Inc. © Art of Lean, Inc. Background •There is unfortunately little that is well understood by most people about the historical development of the Toyota Production System. Mostly anecdotes and stories are used in explaining the various origins of the system. •Some parties have claimed for example that Mr. Shigeo Shingo actually invented much of the Toyota Production System and was the teacher of Mr. Taiichi Ohno. •Others that worked at Toyota during the era in question dispute this notion pointing out that Mr. Shingo basically taught a shop floor level training course for about two or three weeks per year on average between 1955-1980. •There is ample material available in the form of books, timelines, historical records, interviews, and articles to look at that can shed light the matter for interested parties to study and form their own opinion. •On the following pages I’ll highlight what is verifiable about history of the Toyota Production System for interested parties to learn more. After a trip to Japan this summer I will create a more detailed investigation and comprehensive document. This initial effort will not focus on Henry Ford’s influence, TWI materials, or the Quality movement which are all duly recognized by the company. © Art of Lean, Inc. Outline •Origins of TPS •Jidoka •Just-in-Time •SMED •The role of Mr. Shingo at Toyota •Summary comments © Art of Lean, Inc. Who developed TPS? Perception voiced by some parties: Mr. -
Just-In-Time/Lean Manufacturing (JIT/Lean)
CHAPTER TWENTY ONE JUST-IN-TIME/LEAN MANUFACTURING (JIT/LEAN) LEARNING OBJECTIVES After completing this chapter, you should be able to: ■■ Define the concept Just-in-Time/Lean (JIT/Lean). ■■ Explain the rationale for JIT/Lean. ■■ Summarize the development of JIT/Lean from its beginnings. ■■ Explain the relationship of JIT/Lean to total quality and world-class manufacturing. ■■ List the benefits of JIT/Lean. ■■ Explain the requirements of JIT/Lean. ■■ Describe how JIT/Lean relates to automation. The manufacturing system we will be discussing in this chapter was initially developed by Taiichi Ohno in the 1950s as the succes- sor to Henry Ford’s mass production system. Ohno named it the Toyota Production System (TPS). Since it involved making products only when needed from materials that were made available by suppliers only as required, just-in-time (JIT) became its generic name. For 30 odd years, Toyota Production System or Just-In-Time were the names used for Ohno’s remarkably efficient manufacturing system. Then in 1990, three senior managers of MIT’s International Motor Vehicle Program (IMVP), Jim Womack, Dan Jones, and Dan Roos, published a book that has had a great influence on the way industries around the world make things. That book, entitled The Machine That Changed the World: The Story of Lean Production, was the result of a five-year, in-depth scholarly study of the Toyota Production System. It detailed in clear terms the superiority of the TPS to the mass production system used by the rest of the world, and virtually unchanged since World War I, and concluded that mass production simply could not compete with the Japanese system. -
Lean Misconceptions
Lean Misconceptions Why Many Lean Initiatives Fail and How You Can Avoid the Mistakes http://taylorandfrancis.com Lean Misconceptions Why Many Lean Initiatives Fail and How You Can Avoid the Mistakes Cordell Hensley CRC Press Taylor & Francis Group 6000 Broken Sound Parkway NW, Suite 300 Boca Raton, FL 33487-2742 © 2018 by Taylor & Francis Group, LLC CRC Press is an imprint of Taylor & Francis Group, an Informa business No claim to original U.S. Government works Printed on acid-free paper International Standard Book Number-13: 978-1-138-21745-4 (Hardback) This book contains information obtained from authentic and highly regarded sources. Reasonable efforts have been made to publish reliable data and information, but the author and publisher cannot assume responsibility for the validity of all materials or the consequences of their use. The authors and publishers have attempted to trace the copyright holders of all material reproduced in this publication and apologize to copyright holders if permission to publish in this form has not been obtained. If any copyright material has not been acknowledged please write and let us know so we may rectify in any future reprint. Except as permitted under U.S. Copyright Law, no part of this book may be reprinted, reproduced, trans- mitted, or utilized in any form by any electronic, mechanical, or other means, now known or hereafter invented, including photocopying, microfilming, and recording, or in any information storage or retrieval system, without written permission from the publishers. For permission to photocopy or use material electronically from this work, please access www.copyright .com (http://www.copyright.com/) or contact the Copyright Clearance Center, Inc. -
TPS), Introduced Kaizen to Suppliers, Resulting in Them Becoming More Productive and Competitive, with a Substantial Reduction in Time and Cost
Kaizen in the automotive industry Six years ago, South Africa’s Department of Trade and Industry (DTI) and Japan’s Ministry of Economy, Trade and Industry (METI) agreed to a joint study on (inter alia) the automotive industry to increase and diversify trade between the two countries. This followed the need for increased competitiveness in the automotive industry to ensure greater productivity and profit. As a result, JICA has been working with DTI’s Automotive Industry Development Centre (AIDC) in Rosslyn, Gauteng, to strengthen automotive supplier capability. Two AIDC-hosted JICA experts with vast experience on the Toyota Production System (TPS), introduced Kaizen to suppliers, resulting in them becoming more productive and competitive, with a substantial reduction in time and cost. Baires Plastics in Roodepoort, Gauteng, is one of the suppliers benefitting from this Kaizen training, which has resulted in an improved Material and Information Flow Diagram (MIFD) for the production line or “shop-floor”. Baires Plastics manufactures plastic automotive components such as moulds and grilles. Outcomes observed by Baires Plastics include an accessible planning and monitoring board to reduce overproduction, an improved operation instruction sheet for the moulding line to reduce stagnation, a revised operation standard for the double-check method for customers, and improved inspection reducing back-logs. Baires Plastics plans on improving the quality-check step through training of both the production and champion operators to ensure that quality is integrated into the entire production process. Messrs Michiharu Suzuki and Kazunori Hayashi, JICA Experts hosted by AIDC, observes a demonstration by their trainee, Baatseba Motubatsa from Baires Plastics, along with Mr Martin Keller, Managing Director. -
The Origins and Evolution of Lean Management System
Łukasz Dekier “Th e Origins and Evolution of Lean Management System”, Journal Journal of International Studies, Vol. 5, No 1, 2012, pp. 46-51. of International Studies c Papers c © Foundation fi of International Studies, 2012 © CSR, 2012 Th e Origins and Evolution of Lean Management System Scienti Łukasz Dekier Poznan University of Economics al. Niepodległości 10, 61 - 875 Poznań e-mail: [email protected] tel: 61 854 35 31 fax: 61 854 35 30 [email protected] Abstract. In 2008 the worldwide economic crisis grew in strength and many companies Received: January, 2012 from diff erent walks of life commenced to seek the opportunity to enhance their eco- 1st Revision: nomic situation. Th e outcomes of the eff ort resulted in the implementation of mod- March, 2012 ern management methods, such as Six Sigma, Th eory of Constraints, TQM or Lean Accepted: May, 2012 Management. Due to its high effi cacy the last one turned most preferred. Th e aim of this paper is to give an account of the origins and evolution of Lean Management. Th e brief history of Toyota Production System (TPS) will be outlined alongside its most es- sential instruments: jidoka, Just-in-time and “pull-fl ow production”. Additionally, the functioning of companies exercising Lean Management as a direct successor of TPS will be demonstrated. Eventually, the underlying rules of Lean Management with their applications will be put forward to elicit its assets and discern the diff erences between Lean Management and the former systems. Keywords: Lean Management, Lean Manufacturing, Toyota Production System, Lean Leadership. -
Eiji Toyoda on the Roots of TPS
Eiji Toyoda on the Roots of TPS While on a recent trip to Japan I ran across an old article written by Eiji Toyoda about the roots of TPS and its early development. Quite some time ago I was fortunate enough to meet and help translate for Eiji once when I still worked for Toyota in Japan. On that afternoon he patiently answered questions about the company and talked briefly about the origins of its production system with some American visitors from the U.S. Consulate Office in Osaka who came to tour Toyota’s Tsutsumi facility. The topic was very interesting to hear about and to help translate. It struck me recently in hindsight almost twenty years later that we still really don’t know all that much about the historical development of TPS. Mostly we have a lot of superficial knowledge regarding “what” some of the production system tools are but not exactly “why” they were developed or even “how” for that matter. Partly as a result I see a fair amount of misapplication of the tools in the United States or at least usage in some ways that Toyota never envisioned. Additionally there are just a lot of incorrect anecdotes that float around the lean community about the history of TPS. For example over the years I have heard and read different commentaries about how Taiichi Ohno first envisioned pull and kanban while visiting an American supermarket, how Henry Ford or W. Edwards Demming directly taught Toyota, or how Shigeo Shingo somehow invented TPS and later taught it to Taiichi Ohno. -
Toyota Production System
Toyota Production System From Wikipedia, the free encyclopedia The Toyota Production System (TPS) is an integrated socio-technical system, developed by Toyota, that comprises its management philosophy and practices. The TPS organizes manufacturing and logistics for the automobile manufacturer, including interaction with suppliers and customers. The system is a major precursor of the more generic "Lean manufacturing." Taiichi Ohno, Shigeo Shingo and Eiji Toyoda developed the system between 1948 and 1975.[1] Originally called "Just In Time Production," it builds on the approach created by the founder of Toyota, Sakichi Toyoda, his son Kiichiro Toyoda, and the engineer Taiichi Ohno. The founders of Toyota drew heavily on the work of W. Edwards Deming and the writings of Henry Ford. When these men came to the United States to observe the assembly line and mass production that had made Ford rich, they were unimpressed. While shopping in a supermarket they observed the simple idea of an automatic drink resupplier; when the customer wants a drink, he takes one, and another replaces it. The principles underlying the TPS are embodied in The Toyota Way. Contents 1 Goals 2 Origins 3 Principles o 3.1 Long-term philosophy o 3.2 The right process will produce the right results o 3.3 Add value to the organization by developing your people and partners o 3.4 Continuously solving root problems drives organizational learning 4 Results 5 Commonly used terminology 6 See also 7 Notes 8 References 9 External links Goals The main objectives of the TPS are to design out overburden (muri) and inconsistency (mura), and to eliminate waste (muda). -
Toyota Production System Basic Handbook
TOYOTA PRODUCTION SYSTEM BASIC HANDBOOK TABLE OF CONTENTS Introduction & History of the Toyota Production System ........................3 Goals of the Toyota Production System..................................................4 TPS Model Overview............................................................................5-6 Respect for People..................................................................................7 Focus Areas of TPS ................................................................................8 Eliminating Waste..........................................................................9-10 Quality .........................................................................................11-12 Cost. .................................................................................................13 Productivity.......................................................................................14 Safety & Morale................................................................................15 Jidoka . .............................................................................................16-18 Standardization……………………………………………………………….19 Just in Time ...........................................................................................20 Pull Production………………………………………………………………..21 Kanban……………………………………………………………………..22-23 Level Production....................................................................................24 Takt Time. .............................................................................................25 -
Mark Gajewski
Evolution of the “Respect for People” Principle in Progressive Management Mark Gajewski A Special Project Submitted in Partial Fulfillment of the Requirements for the Degree of Master of Science In Technology Management Department of Manufacturing and Construction Management Central Connecticut State University New Britain, Connecticut April 2014 Special Project Advisor: Bob Emiliani © Mark Gajewski 2 Abstract A historical account of how “Respect for People” in Progressive Management has been understood over time is presented with an aim to provide a framework for managers in practical application of the principle. Respect for People is characterized by practical, non-zero-sum management methods, and the effects that improving processes has on stakeholders. Management has long sought to improve efficiencies and reduce costs to remain competitive. In recent times, Lean production methods have become widely accepted in manufacturing and service organizations to achieve cost reductions. Lean production has advanced from a set of improvement tools to become more broadly recognized as a management system, predominantly at Toyota. The Respect for People and Continuous Improvement principles are the pillars of the Toyota Management System. Although the continuous improvement tools are well known and widely practiced for the past twenty five years, there exist few documented cases of organizations that have achieved lasting results, therefore suggesting that an essential element of Lean is missing or possibly misunderstood. There is wide variation in the interpretation of Respect for People, which may be a significant contributor to failed Lean transformations. This paper examines the evolution of the Respect for People principle from the days of Scientific Management through the early twenty-first century.