Mineralogical Characterization of Slags from Oiola Site (Biscay)
Total Page:16
File Type:pdf, Size:1020Kb
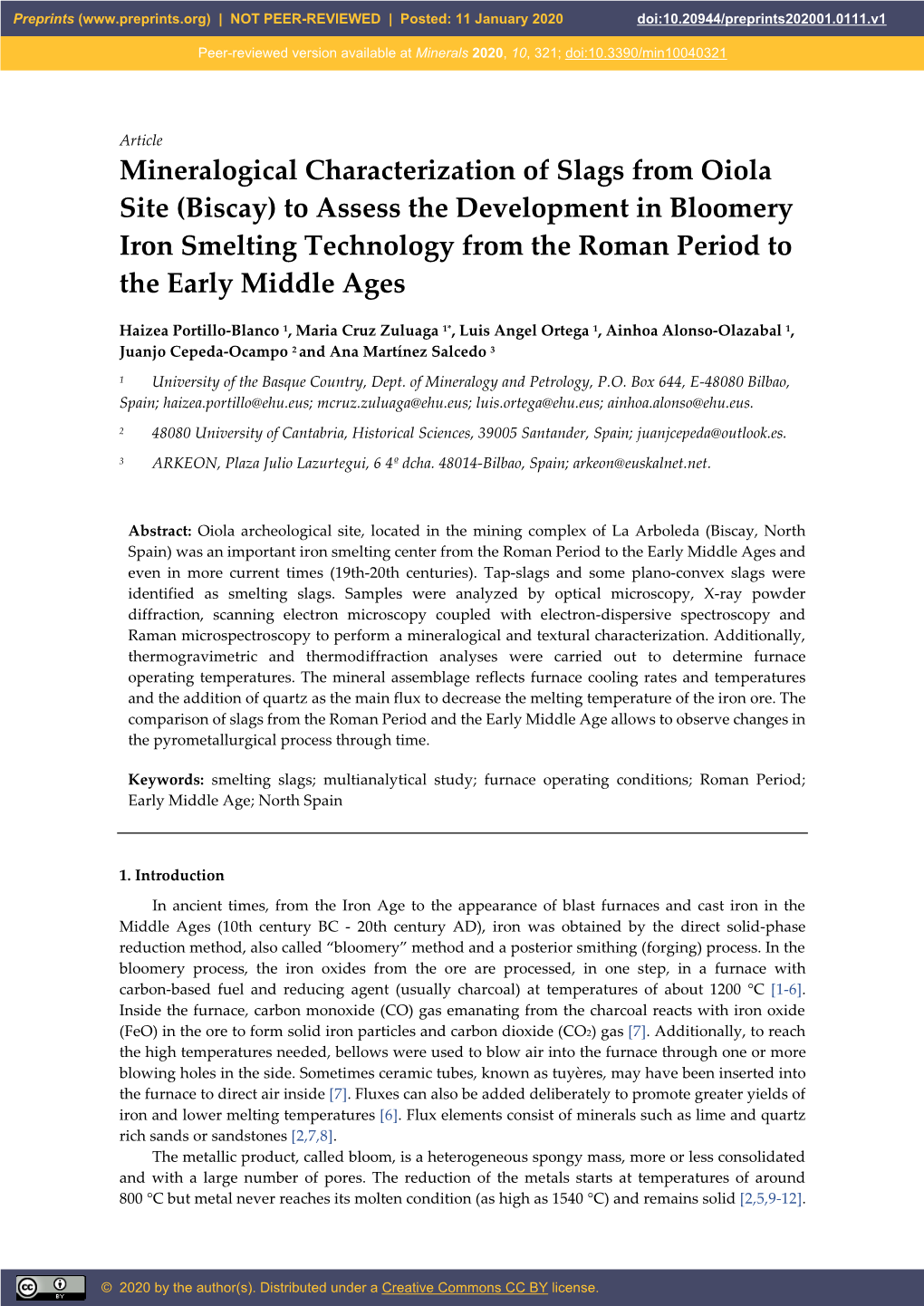
Load more
Recommended publications
-
Influence of Temperature and Water Content on Microstructure Evolution
Contributions to Mineralogy and Petrology (2018) 173:5 https://doi.org/10.1007/s00410-017-1429-y ORIGINAL PAPER Synthesis of monticellite–forsterite and merwinite–forsterite symplectites in the CaO–MgO–SiO2 model system: influence of temperature and water content on microstructure evolution P. Remmert1 · W. Heinrich1 · B. Wunder1 · L. Morales1 · R. Wirth1 · D. Rhede1 · R. Abart2 Received: 17 September 2017 / Accepted: 28 November 2017 / Published online: 21 December 2017 © The Author(s) 2018. This article is an open access publication Abstract Homogeneous single crystals of synthetic monticellite with the composition Ca0.88Mg1.12SiO4 (Mtc I) were annealed in a ◦ piston-cylinder apparatus at temperatures between 1000 and 1200 C , pressures of 1.0–1.4 GPa, for run durations from 10 min to 24 h and applying bulk water contents ranging from 0.0 to 0.5 wt% of the total charge. At these conditions, Mtc I breaks down to a fine-grained, symplectic intergrowth. Thereby, two types of symplectites are produced: a first symplectite type (Sy I) is represented by an aggregate of rod-shaped forsterite immersed in a matrix of monticellite with end-member composition (Mtc II), and a second symplectite type (Sy II) takes the form of a lamellar merwinite–forsterite intergrowth. Both symplectites may form simultaneously, where the formation of Sy I is favoured by the presence of water. Sy I is meta- stable with respect to Sy II and is successively replaced by the latter. For both symplectite types, the characteristic spacing of the symplectite phases is independent of run duration and is only weeakly influenced by the water content, but it is strongly ◦ ◦ ◦ temperature dependent. -
Ore, Iron, Artefacts and Corrosion
. SERIE C NR 626 AVHANDLINGAR OCH UPPSATSER ARSBOK 61 NR 11 OLOF ARRHENIUS ORE, IRON, ARTEFACTS AND CORROSION WITH 4 PLATES STOCKHOLM 1967 SVERTGES GEOLOGISKA UNDERSOKNING SERIE C NR 626 ARSBOK 6 l NR I I OLOF ARRHENIUS ORE, IRON, ARTEFACTS AND CORROSION WITH 4 PLATES STOCKHOLM 196 7 Contents The conditions of the investigation ....................... Elements on which studies are made. ...................... Methods and sources of material ........................ Conditions of analysis ............................ What ores were first used in the production of iron? ................ The formation, occurrence and chemical composition of limonite ores ........ Synopsis of regions in which lake iron ore has a relatively high frequency of high con- centration of the elements indicated ...................... Rock ores. ................................. Synopsis of regions in which rock ores have a relatively high frequency of high concentra- tions of the elements indicated ........................ Artefacts .................................. Synopsis of regions where artefacts show relatively high frequencitl of the elements indicated ................................. Phosphorus in iron ............................. Coal in iron ............................... Alloying elements. Rust ........................... Summary .................................. Appendix: The microstructure after reduction of phosphorus-rich iron ore with charcoal at different temperatures. By Torsten Hansson and Sten Modin .......... Literature. ................................ -
Magnesioferrite-Olivine Rock and Monticellite-Bearing Dunite from the Iwanai-Dake Alpine-Type Peridotite Mass in the Kamuikotan Structural Belt, Hokkaido, Japan
J. Japan. Assoc. Min, Petr. Econ. Geol. 77, 23-31. 1982 Magnesioferrite-olivine rock and monticellite-bearing dunite from the Iwanai-dake alpine-type peridotite mass in the Kamuikotan structural belt, Hokkaido, Japan JITSUYA NAGATA Department of Earth Sciences, Kanazawa University, Kanazawa 920, Japan Magnesioferrite, monticellite, perovskite and calcium brittle mica occur in the alpine- type Iwanai-dake peridotite mass in the Kamuikotan structural belt, Hokkaido. These minerals were not primary phases, but were produced through metasomatic processes at a later stage of the granulite facies equilibration. Introduction Magnesioferrite, monticellite, perovskite and calcium brittle mica were found in the Iwanai-dake peridotite mass, an alpine-type intrusion in Hokkaido. As these minerals have not been described in alpine-type peri dotite, their modes of occurrence, chemis tries and paragenetic relations will be described in this paper. The Iwani-dake mass (Fig. 1) is intrud- ed in the Kamuikotan structural belt which is a melange zone consisting of high-pressure metamorphic rocks, low-pressure metamor Fig. 1. Locality of the Iwanai-dake peridotite phic rocks derived from an ophiolitic suite, mass, Hokkaido. and ultramafic rocks (Banno et al., 1978; Asahina and Komatsu, 1979). The Iwanai- ing to Arai (1978), equilibrium temperature dake mass is composed largely of dunite and of ultramafic rocks is estimated to 600 to harzburgite and is almost free from ser 700°C using the olivine-Ca-rich clinopyroxene pentinization (Bamba, 1955; Kato, 1978; geothermometer and olivine-spinel geother Niida and Kato, 1978; Arai, 1978). Gener mometer. ally, dunite and harzburgite form layered structures. Small amounts of chromitite Mode of occurrence, petrography and are also present. -
Iron, Steel and Swords Script
Iron Ores General Remarks This planet consists of iron (32.1%), oxygen (30.1%), silicon (15.1%), magnesium (13.9%), sulfur (2.9%), nickel (1.8%), calcium (1.5%), and aluminium (1.4%); the remaining 1.2% are "trace amounts" of the 80 or so remaining elements. Most of that iron constitutes the core of the planet but we will not run out of iron compounds or iron ore found near to the surface for some time to come. Why is iron so prominent in this (and other) planet ? Because planets were formed from the stuff bred inside the first stars. The reaction chain for generating energy by nuclear fusion starts with hydrogen and stops after iron has been bred. Iron, if you like, is the ash eventually produced by fusing hydrogen to helium, helium and hydrogen to lithium, and so on. When those first stars "burnt out" after a few billon years, some of them coughed up their ashes in a mighty supernova explosion. In time, new stars were formed. Some of these are still burning and visible at night. One (our very own sund) is only visible during the day from a clumped-together iron-rich ash ball called earth. Advanced From the viewpoint of chemistry, iron (like copper) is a tricky element that can form many oxides, sulfides, carbonates, and so on. All these compounds could be used for smelting iron but some are better for that purpose than others. Sulfides are usually bad news. We know that from smelting copper and expect similar problems when smelting iron. -
List of Abbreviations
List of Abbreviations Ab albite Cbz chabazite Fa fayalite Acm acmite Cc chalcocite Fac ferroactinolite Act actinolite Ccl chrysocolla Fcp ferrocarpholite Adr andradite Ccn cancrinite Fed ferroedenite Agt aegirine-augite Ccp chalcopyrite Flt fluorite Ak akermanite Cel celadonite Fo forsterite Alm almandine Cen clinoenstatite Fpa ferropargasite Aln allanite Cfs clinoferrosilite Fs ferrosilite ( ortho) Als aluminosilicate Chl chlorite Fst fassite Am amphibole Chn chondrodite Fts ferrotscher- An anorthite Chr chromite makite And andalusite Chu clinohumite Gbs gibbsite Anh anhydrite Cld chloritoid Ged gedrite Ank ankerite Cls celestite Gh gehlenite Anl analcite Cp carpholite Gln glaucophane Ann annite Cpx Ca clinopyroxene Glt glauconite Ant anatase Crd cordierite Gn galena Ap apatite ern carnegieite Gp gypsum Apo apophyllite Crn corundum Gr graphite Apy arsenopyrite Crs cristroballite Grs grossular Arf arfvedsonite Cs coesite Grt garnet Arg aragonite Cst cassiterite Gru grunerite Atg antigorite Ctl chrysotile Gt goethite Ath anthophyllite Cum cummingtonite Hbl hornblende Aug augite Cv covellite He hercynite Ax axinite Czo clinozoisite Hd hedenbergite Bhm boehmite Dg diginite Hem hematite Bn bornite Di diopside Hl halite Brc brucite Dia diamond Hs hastingsite Brk brookite Dol dolomite Hu humite Brl beryl Drv dravite Hul heulandite Brt barite Dsp diaspore Hyn haiiyne Bst bustamite Eck eckermannite Ill illite Bt biotite Ed edenite Ilm ilmenite Cal calcite Elb elbaite Jd jadeite Cam Ca clinoamphi- En enstatite ( ortho) Jh johannsenite bole Ep epidote -
Kirschsteinite Cafe Sio4 C 2001 Mineral Data Publishing, Version 1.2 ° Crystal Data: Orthorhombic
2+ Kirschsteinite CaFe SiO4 c 2001 Mineral Data Publishing, version 1.2 ° Crystal Data: Orthorhombic. Point Group: 2=m 2=m 2=m: In crystals, to 0.5 mm; as skeletal rims on other minerals; crystalline massive. Physical Properties: Hardness = n.d. D(meas.) = 3.434 D(calc.) = 3.596 Optical Properties: Transparent. Color: Pale green; colorless in thin section. Optical Class: Biaxial ({). Orientation: X = b; Y = c; Z = a. ® = 1.660{1.689 ¯ = 1.720 ° = 1.694{1.728 2V(meas.) = 51(1)± 2V(calc.) = 53±{61± Cell Data: Space Group: [P bnm] (by analogy to the olivine group). a = 4.859 b = 11.132 c = 6.420 Z = 4 X-ray Powder Pattern: Mt. Shaheru, Congo. 2.949 (100), 2.680 (85), 2.604 (80), 3.658 (70), 1.830 (60), 2.414 (40), 5.569 (35) Chemistry: (1) (2) SiO2 32.71 31.96 TiO2 0.23 Al2O3 0.26 Fe2O3 0.66 FeO 29.34 38.21 MnO 1.65 MgO 4.95 CaO 29.30 29.83 Na2O 0.34 K2O 0.36 + H2O 0.25 H2O¡ 0.06 P2O5 0.07 Total 100.18 100.00 (1) Mt. Shaheru, Congo. (2) CaFeSiO4: Polymorphism & Series: Forms a series with monticellite. Occurrence: In melilite-nephelinite lava (Mt. Shaheru, Congo); in calcareous skarn (Tazheran massif, Russia). Association: Melilite, nepheline, clinopyroxene, kalsilite, gÄotzenite, combeite, sodalite, magnetite, perovskite, apatite, \hornblende," biotite (Mt. Shaheru, Congo); titanian augite, wollastonite, melilite, garnet, calcite, cuspidine, diopside, perovskite, troilite, graphite (Tazheran massif, Russia). Distribution: On Mt. Shaheru, the extinct southern cone of Mt. Nyiragongo, Kivu Province, Congo (Zaire). -
Iron Making in Argyll
HISTORIC ARGYLL 2009 Iron smelting in Argyll, and the chemistry of the process by Julian Overnell, Kilmore. The history of local iron making, particularly the history of the Bonawe Furnace, is well described in the Historic Scotland publication of Tabraham (2008), and references therein. However, the chemistry of the processes used is not well described, and I hope to redress this here. The iron age started near the beginning of the first millennium BC, and by the end of the first millennium BC sufficient iron was being produced to equip thousands of troops in the Roman army with swords, spears, shovels etc. By then, local iron making was widely distributed around the globe; both local wood for making charcoal, and (in contrast to bronze making) local sources of ore were widely available. The most widely distributed ore was “bog iron ore”. This ore was, and still is, being produced in the following way: Vegetation in stagnant water starts to rot and soon uses up all the available oxygen, and so produces a water at the bottom with no oxygen (anaerobic) which also contains dissolved organic compounds. This solution is capable of slowly leaching iron from the soils beneath to produce a weak solution of dissolved iron (iron in the reduced, ferrous form). Under favourable conditions this solution percolates down until it meets some oxygen (or oxygenated water) at which point the iron precipitates (as the oxidized ferric form). This is bog iron ore and comprises a somewhat ill-defined brown compound called limonite (FeOOH.nH2O), often still associated with particles of sand etc. -
The Iron-Ore Resources of Europe
DEPARTMENT OF THE INTERIOR ALBERT B. FALL, Secretary UNITED STATES GEOLOGICAL SURVEY GEORGE OTIS SMITH, Director Bulletin 706 THE IRON-ORE RESOURCES OF EUROPE BY MAX ROESLER WASHINGTON GOVERNMENT PRINTING OFFICE 1921 CONTENTS. Page. Preface, by J. B. Umpleby................................................. 9 Introduction.............................................................. 11 Object and scope of report............................................. 11 Limitations of the work............................................... 11 Definitions.........................:................................. 12 Geology of iron-ore deposits............................................ 13 The utilization of iron ores............................................ 15 Acknowledgments...................................................... 16 Summary................................................................ 17 Geographic distribution of iron-ore deposits within the countries of new E urope............................................................. 17 Geologic distribution................................................... 22 Production and consumption.......................................... 25 Comparison of continents.............................................. 29 Spain..................................................................... 31 Distribution, character, and extent of the deposits....................... 31 Cantabrian Cordillera............................................. 31 The Pyrenees.................................................... -
The Iron Ores of Maryland, with an Account of the Iron Industry
Hass 77,>0 3- Book ffjZd6 MARYLAND GEOLOGICAL AND ECONOMIC SURVEY WM. BULLOCK CLARK, State Geologist REPORT ON THE IRON ORES OF MARYLAND WITH AN ACCOUNT OF THE IRON INDUSTRY BY JOSEPH T. SINGEWALD, JR.- (Special Publication, Volume IX, Part III) THE JOHNS HOPKINS PRESS Baltimore, December, 1911 / / MARYLAND GEOLOGICAL AND ECONOMIC SURVEY WM. BULLOCK CLARK, State Geologist REPORT ON r? Sr THE IRON ORES OF MARYLAND / £ WITH AN ACCOUNT OF THE IRON INDUSTRY BY JOSEPH T. SINGEWALD, JR. M (Special Publication, Volume IX, Part III) THE JOHNS HOPKINS PRESS • Baltimore, December, 1911 V n, ffi ft- sre so i CONTENTS PAGE PART III. REPORT ON THE IRON ORES OF MARYLAND, WITH AN ACCOUNT OF THE IRON INDUSTRY. By Joseph T. Sxngewald, Jr. 121 The Ores of Iron.123 Magnetite . 124 Hematite . 124 Limonite . 124 Carbonate or Siderite. 125 Impurities in the Ores and Their Effects. 125 Mechanical Impurities. 125 Chemical Impurities. 126 Practical Considerations. 127 History of the Maryland Iron Industry. 128 The Colonial Period. 128 The Period from 1780 to 1830. 133 • The Period from 1830 to 1885. 133 The Period from 1885 to the present time. 136 Description of Maryland Iron Works.139 Maryland Furnaces. 139 Garrett County..'... 139 Allegany County. 139 Washington County. 143 Frederick County. 146 Carroll County. 149 Baltimore County. 150 Baltimore City. 159 Harford County. 160 Cecil County. 162 Howard County. 168 Anne Arundel County. 169 Prince George’s County. 171 Worcester County. 172 9 Other Iron Works in Maryland. 173 Allegany County. 173 Baltimore County. 173 Cecil County. 174 CONTENTS PAGE Queen Anne’s County. -
Diopside Camgsi2o6 C 2001 Mineral Data Publishing, Version 1.2 ° Crystal Data: Monoclinic
Diopside CaMgSi2O6 c 2001 Mineral Data Publishing, version 1.2 ° Crystal Data: Monoclinic. Point Group: 2=m: As prismatic crystals with nearly square cross sections, to 50 cm; granular, columnar, lamellar massive. Twinning: Simple or multiple twins on 100 or 010 , common. f g f g Physical Properties: Cleavage: Distinct on 110 , (110) (110) 87±; partings on 100 and probably 010 . Fracture: Uneven to conchofidal.g Tenaci^ty: Britt»le. Hardness = 5f.5{6.g5 D(meas.) = 3.f22{3g.38 D(calc.) = 3.278 Optical Properties: Transparent to opaque. Color: Colorless, white, yellow, pale to dark green, black; colorless in thin section. Streak: White, gray, gray-green. Luster: Vitreous or dull. Optical Class: Biaxial (+). Orientation: Y = b; Z c = 38± on (010); X a = 22±. ^ ¡ ^ ¡ Dispersion: r > v; weak to moderate. ® = 1.664 ¯ = 1.672 ° = 1.694 2V(meas.) = 59± Cell Data: Space Group: C2=c: a = 9.746 b = 8.899 c = 5.251 ¯ = 105:63± Z = 4 X-ray Powder Pattern: Schwartzenstein, Austria. (ICDD 11-654). 2.991 (100), 2.528 (40), 2.893 (30), 2.518 (30), 3.23 (25), 2.952 (25), 1.625 (25) Chemistry: (1) (2) (1) (2) (1) (2) SiO2 54.66 54.09 FeO 0.07 1.47 K2O 0.15 + TiO2 0.28 MnO 0.02 0.09 H2O 0.22 0.22 Al2O3 0.07 1.57 MgO 18.78 16.96 H2O¡ 0.08 Fe2O3 0.68 0.74 CaO 25.85 21.10 rem: 0.49 Cr2O3 2.03 Na2O 1.37 Total 100.35 100.64 3+ (1) Juva, Finland; corresponds to Ca1:00(Mg1:01Fe0:02)§=1:03Si1:98O6: (2) Dutoitspan mine, 2+ Kimberley, Cape Province, South Africa; corresponds to (Ca0:82Na0:05Fe0:04Mg0:04K0:01)§=0:96 3+ (Mg0:88Cr0:06Al0:03Fe0:02Ti0:01)§=1:00(Si1:96Al0:04)§=2:00O6: Polymorphism & Series: Forms two series, with hedenbergite, and with johannsenite. -
NASSAWANGO IRON FURNACE Ca1828-1850 NEAR SNOW HILL, MARYLAND
NASSAWANGO IRON FURNACE ca1828-1850 NEAR SNOW HILL, MARYLAND A NATIONAL HISTORIC MECHANICAL ENGINEERING LANDMARK OCTOBER 19, 1991 The American Society of Mechanical Engineers FURNACE DelMarVa Group TOWN Nassawango Iron Furnace HISTORY OF NASSAWANGO IRON FURNACE Bog iron was first discovered in the swamps produced over 700 tons of pig iron per year at along Nassawango Creek in the 1780’s and in Nassawango; Spence was also credited with 1828 the Maryland Iron Company was the installation of the hot-blast stove on top of incorporated to extract and process it. In the furnace. 1830, the Company constructed a furnace along the creek at a point roughly four miles Iron was produced at Nassawango until 1847 northwest of its confluence with the when lack of labor and poor market Pocomoke River near Snow Hill, MD. Shortly conditions caused Spence (who fell into thereafter, the Nassawango furnace began financial ruin) to shut down the furnace. The producing pig iron by the cold-blast process. property sat idle from that time forward and was used by successive owners mostly for In 1836, two of the Company’s creditors, the timber rights. In 1962, the heirs of Arthur Milby and Joseph Waples, foreclosed Georgia Smith Foster donated the property to on the property; that same year they sold it to the Worcester County Historical Society Benjamin Jones, a Philadelphia ironmonger. which undertook a systematic long range Jones, who owned other furnaces and had a program to stabilize the furnace and cut back formidable business that bought and sold the plant growth of the previous 100 years. -
CRYSTAL STRUCTURES of NATURAL OLIVINES J. D. Brnmt
THE AMERICAN MINERALOGISI', VOL 53, MAY_JUNE, 1968 CRYSTAL STRUCTURES OF NATURAL OLIVINES J. D. Brnmt, G.V. Grnns2,P. B. MoonE, ANDJ. V. SurrH, Departmentof the GeophysicalSciences, (Jn'ittersity of Chicago Chicago,Illinois 60637,U.S.A. Ansrnncr Atomic parameters were obtained by 3D least-squares X-ray difiraction analysis of forsterite (Mgo go,Feo1s), plutonic hyalosiderite (Mgo u:u,Feonso,Mrio ooo,CzIo oor), dike hortonolite (Mgo as,Feoas,Mno or,Cao or), and fayalite (Feo gz,Mgoor,Mns ,r). The closeness in value of the isotropic temperature factors calculated for the M sites indicates substitutional disorder of the Mg and Fe atoms in all four structures. Poiyhedra distortions are closely similar in all four structures showing that they depend on the struc- ture type rather than on the Mg, Fe substitution. Simple electrostatic rules allied with papk- ing considerations permit qualitative explanation of the structural distortions. The M(l) octahedron has six short shared edges to give a distorted and elongated trigonal antiprism. The M(2) octahedron has a triangle of three short shared edges. Metal-oxygen distances tend to compensate e.g., the longest Si-O distance and the shortest (MS,Fe)-O distance go to the same oxygen. INrnorucrroN The type structure of olivine was determined by Bragg and Brown (1926) on a forsterite crystal with composition Mgo noFeo.ro.Three- dimensionalrefinement of another forsterite crystal by Belov, Belova, Andrianova, and Smirnova (1951) yielded Si-O and M-O distancesfar outside the usual ranges for silicates. More recently Hanke a\d Zemarn (1963) determined the atomic parameters of forsterite from a two-di- mensionalanalysis, and Born (1964) followed this by showing that the observedposition ol M(2) falls on the maximum of the total attractive plus repulsiveenergy for half-ionizedatoms.