Machine Time Line
Total Page:16
File Type:pdf, Size:1020Kb
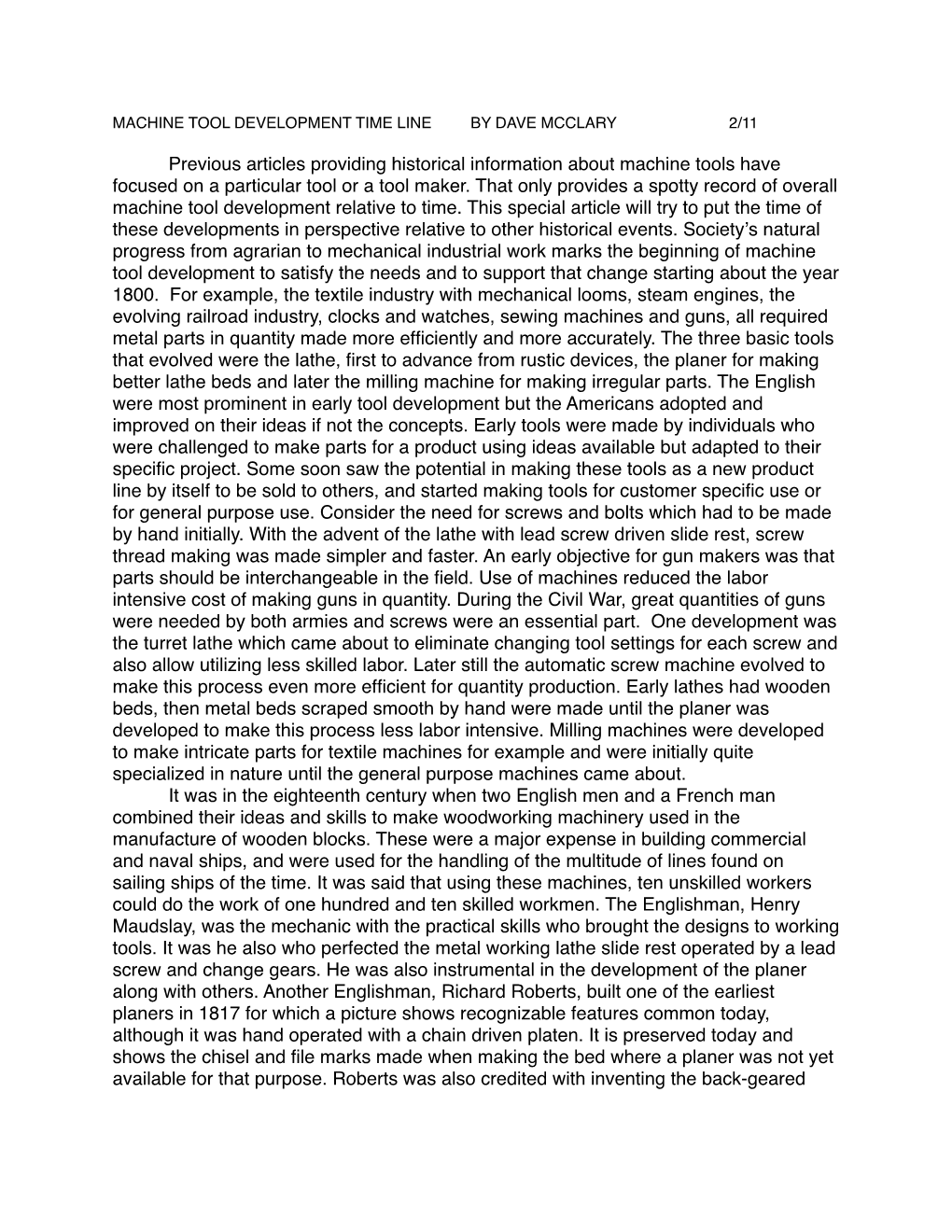
Load more
Recommended publications
-
Milling Machines and Cnc Mills
MILLING MACHINES AND CNC MILLS Safety Precautions MILL SAFETY HAZARDS Milling machines and computer-numerical-controlled (CNC) mills use moving cutters and/or move stock materials to cut shapes materials such as metal, wood or plastic. Mills cut away material using rotating blades, and can throw or eject dust and chips at high speed. Flying chips present an eye injury hazard. Fine dust can be a respiratory hazard. Mills can also be very loud, presenting a threat to hearing as well as drowning out voices, phones, and alarms. Rotating machinery presents a serious hazard, as gloves, clothing, jewelry or loose hair can be caught and body parts drawn into the running machine. Mills have guards to prevent some exposure, and some are completely enclosed when running. • Keep hands, tools, and clothing at least 12 inches away from the moving mill and do not SAFETY PRECAUTIONS attempt to adjust the mill while operating. • Wear safety glasses or goggles, and hearing Safety rules include: protection if needed. Do not wear gloves near • Get trained on the operation of the specific mill operating equipment. you are going to use. • Keep the mill surfaces and shop floor clean of • Never work alone, never leave the milling cuttings and dust. Metal filings can combust machine unattended while running, and know spontaneously and require a Class D fire where the emergency stop controls are located. extinguisher. • Securely clamp the stock material in place. • Secure guards, shields, doors in place prior to Machinery must be completely disconnected from starting. power (and tested) if it is to be repaired or adjusted (see the Hazardous Energy Control page). -
The Industrial Revolution in America
DO NOT EDIT--Changes must be made through “File info” CorrectionKey=TX-A SECTION 1 The Industrial TEKS 5B, 5D, 7A, 11A, 12C, 12D, 13A, Revolution in 13B, 14A, 14B, 27A, 27D, 28B What You Will Learn… America Main Ideas 1. The invention of new machines in Great Britain If YOU were there... led to the beginning of the You live in a small Pennsylvania town in the 1780s. Your father is a Industrial Revolution. 2. The development of new blacksmith, but you earn money for the family, too. You raise sheep machines and processes and spin their wool into yarn. Your sisters knit the yarn into warm brought the Industrial Revolu- tion to the United States. wool gloves and mittens. You sell your products to merchants in the 3. Despite a slow start in manu- city. But now you hear that someone has invented machines that facturing, the United States made rapid improvements can spin thread and make cloth. during the War of 1812. Would you still be able to earn the same amount The Big Idea of money for your family? Why? The Industrial Revolution trans- formed the way goods were produced in the United States. BUILDING BACKOU GR ND In the early 1700s making goods depend- ed on the hard work of humans and animals. It had been that way for Key Terms and People hundreds of years. Then new technology brought a change so radical Industrial Revolution, p. 385 that it is called a revolution. It began in Great Britain and soon spread to textiles, p. -
Introduction to Selecting Milling Tools Iimportant Decisions for the Selection of Cutting Tools for Standard Milling Operations
Introduction to Selecting Milling Tools IImportant decisions for the selection of cutting tools for standard milling operations The variety of shapes and materials machined on modern milling machines makes it impera- tive for machine operators to understand the decision-making process for selecting suitable cutting tools for each job. This course curriculum contains 16-hours of material for instructors to get their students ready to make basic decisions about which tools are suitable for standard milling operations. ©2016 MachiningCloud, Inc. All rights reserved. Table of Contents Introduction .................................................................................................................................... 2 Audience ..................................................................................................................................... 2 Purpose ....................................................................................................................................... 2 Lesson Objectives ........................................................................................................................ 2 Where to Start: A Blueprint and a Plan .......................................................................................... 3 Decision 1: What type of machining is needed? ............................................................................ 7 Decision 2: What is the workpiece material? ................................................................................. 7 ISO Material -
DRAFT – Subject to NIST Approval 1.5 IMPACTS of AUTOMATION on PRECISION1 M. Alkan Donmez and Johannes A. Soons Manufacturin
DRAFT – Subject to NIST approval 1.5 IMPACTS OF AUTOMATION ON PRECISION1 M. Alkan Donmez and Johannes A. Soons Manufacturing Engineering Laboratory National Institute of Standards and Technology Gaithersburg, MD 20899 ABSTRACT Automation has significant impacts on the economy and the development and use of technology. In this section, the impacts of automation on precision, which directly influences science, technology, and the economy, are discussed. As automation enables improved precision, precision also improves automation. Followed by the definition of precision and the factors affecting precision, the relationship between precision and automation is described. This section concludes with specific examples of how automation has improved the precision of manufacturing processes and manufactured products over the last decades. 1.5.1 What is precision Precision is the closeness of agreement between a series of individual measurements, values, or results. For a manufacturing process, precision describes how well the process is capable of producing products with identical properties. The properties of interest can be the dimensions of the product, its shape, surface finish, color, weight, etc. For a device or instrument, precision describes the invariance of its output when operated with the same set of inputs. Measurement precision is defined by the International Vocabulary of Metrology [1] as the "closeness of agreement between indications obtained by replicate measurements on the same or similar objects under specified conditions." In this definition, the "specified conditions" describe whether precision is associated with the repeatability or the reproducibility of the measurement process. Repeatability is the closeness of the agreement between results of successive measurements of the same quantity carried out under the same conditions. -
Milling Machine Operations
SUBCOURSE EDITION OD1644 8 MILLING MACHINE OPERATIONS US ARMY WARRANT OFFICER ADVANCED COURSE MOS/SKILL LEVEL: 441A MILLING MACHINE OPERATIONS SUBCOURSE NO. OD1644 EDITION 8 US Army Correspondence Course Program 6 Credit Hours NEW: 1988 GENERAL The purpose of this subcourse is to introduce the student to the setup, operations and adjustments of the milling machine, which includes a discussion of the types of cutters used to perform various types of milling operations. Six credit hours are awarded for successful completion of this subcourse. Lesson 1: MILLING MACHINE OPERATIONS TASK 1: Describe the setup, operation, and adjustment of the milling machine. TASK 2: Describe the types, nomenclature, and use of milling cutters. i MILLING MACHINE OPERATIONS - OD1644 TABLE OF CONTENTS Section Page TITLE................................................................. i TABLE OF CONTENTS..................................................... ii Lesson 1: MILLING MACHINE OPERATIONS............................... 1 Task 1: Describe the setup, operation, and adjustment of the milling machine............................ 1 Task 2: Describe the types, nomenclature, and use of milling cutters....................................... 55 Practical Exercise 1............................................. 70 Answers to Practical Exercise 1.................................. 72 REFERENCES............................................................ 74 ii MILLING MACHINE OPERATIONS - OD1644 When used in this publication "he," "him," "his," and "men" represent both -
Rotary Transfer Machines Hydromat® Hc Product Line
ROTARY TRANSFER MACHINES HYDROMAT® HC PRODUCT LINE Precise | Productive | Reliable The FFG Rotary Transfer Platform Flexible Multi-Machining with Hydromat® Precise, modular and efficient: The FFG group is the The ability to set up working stations horizontally as well as world’s leading manufacturer of rotary transfer machines vertically allows big machining jobs with the highest output and offers the best solutions for workpieces at the high just-in-time. The enormous flexibility of the rotary transfer volume end. machines gives our clients a major advantage in dealing with the growing challenges of today’s global markets: United under the roof of the FFG group: with the rotary 3 The most cost-effective solutions transfer machines of the tradition brands IMAS, Pfiffner and 3 Maximum precision and process reliability in mass production Witzig & Frank, you are always one cycle ahead. 3 High investment security thanks to extensive modularity 3 High reusability thanks to reconfigurable machine systems The rotary transfer machine program covers all applications for 3 High flexibility and variability (simpler retooling, reduced the serial production of complex metal parts. Rotary transfer setup times) machines are designed for the handling of bar and coil materials, 3 High machine availability or automatic part feeding. They guarantee high-precision 3 Low maintenance costs (TCO) machining of each workpiece, being carried out simultaneously 3 Turnkey solutions on each station. Every rotary transfer machine is specified, 3 Process optimisation -
Milling Machine Operations
Milling Machine Operations Milling Machine This full article is about milling machine operations. If you haven’t read our complete article on types of milling machine you can read now by clicking here. Let's starts with some little introduction about milling machine and milling machine operations. A milling machine is a machine tool that cuts metal as the workpiece is fed against a rotating multipoint cutter. The milling cutter rotates at a very high speed because of the multiple cutting edges, it cuts the metal at a very fast rate. This machine can also hold single or multiple cutters at the same time. This is why a milling machine has wide application in production work. This is better for other machines as regards accuracy and better surface finish. And also it is designed for machining a variety of tool room work. Milling Machine Operations The 15 different types of milling machine operations are as follow: 1. Plain Milling Operation 2. Face Milling Operation 3. Side Milling Operation 4. Straddle Milling Operation 5. Angular Milling Operation 6. Gang Milling Operation 7. Form Milling Operation 8. Profile Milling Operation 9. End Milling Operation 10. Saw Milling Operation 11. Milling Keyways, Grooves and Slot 12. Gear Milling 13. Helical Milling 14. Cam Milling 15. Thread Milling Read also: Types of Milling Cutters [Complete Guide] TheEngineersPost.com Page 1 Milling Machine Operations Read also: Milling Machine: Main Parts and It’s Working Principle Types of Milling Machine Operations Plain Milling The plain milling is the most common types of milling machine operations. Plain milling is performed to produce a plain, flat, horizontal surface parallel to the axis of rotation of a plain milling cutter. -
Colt╎s Patent Fire Arms Manufacturing Company Collection
http://oac.cdlib.org/findaid/ark:/13030/c8hh6mgb No online items Finding Aid to the Colt’s Patent Firearms Manufacturing Company Collection 89.62 Finding aid prepared by Holly Rose Larson and Jeffrey Richardson Autry National Center, Autry Library 4700 Western Heritage Way Los Angeles, CA, 90027 (323) 667-2000 ext. 349 [email protected] 2012 March 7 Finding Aid to the Colt’s Patent 89.62 1 Firearms Manufacturing Company Collection 89.62 Title: Colt’s Patent Fire Arms Manufacturing Company Collection Identifier/Call Number: 89.62 Contributing Institution: Autry National Center, Autry Library Language of Material: English Physical Description: 3.4 Linear feet(2 boxes) Date (inclusive): 1894-1946 Abstract: Samuel Colt patented his revolver with a mechanically rotating cylinder in 1835 and 1836. It revolutionized the firearms industry and was the first truly global manufacturing export in American history. The success of the revolver ultimately allowed Samuel Colt to incorporate Colt’s Patent Fire Arms Manufacturing Company in 1855. This collection of Colt’s Patent Fire Arms Manufacturing Company documents spans 1894-1946 and includes contracts, correspondence, invoices, memos, notes, receipts, stock certificates, and trademark registration certificates regarding manufacture, registration and trade of Colt products. Language: English, Spanish, French. creator: Colt Manufacturing Company creator: Colt's Patent Fire Arms Manufacturing Company creator: Colt, Samuel, 1814-1862 Access Collection is open for research. Appointments to view materials are required. To make an appointment please visit http://theautry.org/research/research-rules-and-application or contact library staff at [email protected]. An item-level inventory is available from library staff. -
Manufacuting Technology
ME 6402 -Manufacturing Technology - II IV Sem / II Year B.E. (Mechanical Engineering) Department of Mechanical Engineering R.M.K.ENGINEERINGCOLLEGE R.S.M. Nagar, Kavaraipettai – 601 206. UNIT I - THEORY OF METAL CUTTING INTRODUCTION: CUTTING TOOL: SINGLE POINT CUTTING TOOL: NOMENCLATURE SINGLE POINT TOOL: MECHANICS OF METAL CUTTING: TYPES OF CHIPS: COOLANT OR CUTTING FLUIDS OR EMULSIONS: FUNCTIONS OR USES OF COOLANTS OR CUTTING FLUIDS: TYPICAL PROPERTIES OF TOOL MATERIALS: ------------------------------X-------------------------------- UNIT-II - CENTRE LATHE AND SPECIAL PURPOSE LATHE INTRODUCTION: TYPES OF LATHE: SPEED LATHE: CENTRE LATHE OR ENGINE LATHE: BENCH LATHE: TOOL ROOM LATHE: CAPSTAN AND TURRET LATHE: SPECIAL PURPOSE LATHE: AUTOMATIC LATHE: CONSTRUCTION OF LATHE MACHINE: BED: HEAD STOCK: TAIL STOCK: CARRIAGE: THREAD CUTTING MECHANISM: ACCESSORIES AND ATTACHMENTS OF LATHE: SPECIFICATION OF LATHE: LATHE OPERATIONS: TAPERS AND TAPER TURNING: TAPER TURNING BY SWIVELLING THE COMPOUND REST: TAPER TURNING ATTACHMENT METHOD: TAPER TURNING WITH TAILSTOCK SET OVER METHOD: FORM TOOL METHOD: TAPER TURNING WITH DOUBLE HEADS: THREAD CUTTING: DRILLING ON A LATHE: CUTTING SPEED: FEED: ---------------------------X------------------------------ UNIT-III, OTHER MACHINE TOOLS DRILLING INTRODUCTION: CONSTRUCTION OF DRILLING MACHINE: TYPES OF DRILLING MACHINE: PORTABLE DRILLING MACHINE: SENSITIVE DRILLING MACHINE: UPRIGHT DRILLING MACHINE: RADIAL DRILLING MACHINE: GANG DRILLING MACHINE: MULTIPLE-SPINDLE DRILLING MACHINE: TYPES OF DRILLS: TWIST DRILL -
Manufacturing Processes
Module 7 Screw threads and Gear Manufacturing Methods Version 2 ME, IIT Kharagpur Lesson 31 Production of screw threads by Machining, Rolling and Grinding Version 2 ME, IIT Kharagpur Instructional objectives At the end of this lesson, the students will be able to; (i) Identify the general applications of various objects having screw threads (ii) Classify the different types of screw threads (iii) State the possible methods of producing screw threads and their characteristics. (iv) Visualise and describe various methods of producing screw threads by; (a) Machining (b) Rolling (c) Grinding (i) General Applications Of Screw Threads The general applications of various objects having screw threads are : • fastening : screws, nut-bolts and studs having screw threads are used for temporarily fixing one part on to another part • joining : e.g., co-axial joining of rods, tubes etc. by external and internal screw threads at their ends or separate adapters • clamping : strongly holding an object by a threaded rod, e.g., in c-clamps, vices, tailstock on lathe bed etc. • controlled linear movement : e.g., travel of slides (tailstock barrel, compound slide, cross slide etc.) and work tables in milling machine, shaping machine, cnc machine tools and so on. • transmission of motion and power : e.g., lead screws of machine tools • converting rotary motion to translation : rotation of the screw causing linear travel of the nut, which have wide use in machine tool kinematic systems • position control in instruments : e.g., screws enabling precision movement of the work table in microscopes etc. • precision measurement of length : e.g., the threaded spindle of micrometers and so on. -
What Was the Assembly Line ?
59 WHAT WAS THE ASSEMBLY LINE ? DAVID E. NYE INTRODUCTION Today, ”assembly line” immediately suggests Asian or Latin-American factories where poorly-paid workers make consumer goods for export to the West. For example, many US corporations shifted jobs to northern Mexico beginning in 1965 as part of the Border Industrialization Program. This process accelerated dramatically after January 1, 1994, when the North American Free Trade Agreement (NAFTA) went into effect. It abolished tariffs and made re-importation of assembly line goods easy. By 2000, 1.2 million US jobs had been relocated to Mexico. Most of the Mexicans hired were semi-skilled women, preferred both for their manual dexterity and their willingness to accept low wages.1 Corporations built factories where environmental legislation was lax and unions were weak or non-existent. In such places, “the danger is that repression rather than innovation becomes a competitive advantage.”2 Yet if the assembly line of today is often part of a global production system for offshore, semi-skilled work, at its inception in 1913 the Americans saw the assembly line as the guarantor of high wages and domestic prosperity. This essay reviews the origins of the assembly line, what exactly it was as a technology, and how it was initially understood. In hindsight, it was less a beginning than a mid-point in long- term developments that are still underway. Historians frequently refer to the assembly line as an historical stage, in a sequence from Taylorism to Fordism to “post-Fordism,” with additional stages sometimes included such as “lexible production,” “lean production” and most recently “post- lean production.”3 As convenient as these historical stages once seemed, their proliferation suggests that the whole notion of a sequence was mistaken to begin with. -
Screw Threads and Tap-Drill Sizes
CS24-43 Screw Threads and Tap-Drill Sizes U. S. DEPARTMENT OF COMMERCE JESSE H. JONES, Secretary NATIONAL BUREAU OF STANDARDS LYMAN J. BRIGGS, Director SCREW THREADS AND TAP-DRILL SIZES COMMERCIAL STANDARD CS24-43 (Revision and consolidation of CS24”30 and CS25-30) Effective Date for New Production from February 10, 1943 A RECORDED VOLUNTARY STANDARD OF THE TRADE UNITED STATES GOVERNMENT PRINTING OFFICE WASHINGTON : 1943 For sale by the Superintendent of Documents, U. S. Government Printing Office Washington 25, D. C. - Price 15 cents U. S. Department of Commerce National Bureau of Standards PROMULGATION of COMMERCIAL STANDARD CS24-43 for SCREW THREADS AND TAP-DRILL SIZES (Revision and consolidation of CS24-30 and CS25-30) At the request of the National Screw Thread Commission, American National screw-thread tables for shop use were circulated January 23, 1930, as recommended commercial standards to producers, distri- butors, and users for a written acceptance. They were subsequently accepted in writing by the industry and published under the titles, American National Standard Screw Threads, Coarse and Fine-Thread Series, Commercial Standard CS24-30; and American National Special Screw Threads, Commercial Standard CS25-*30. On July 28, 1942, on the recommendation of the Interdepartmental Screw Thread Committee, and with the endorsement of the standing committee, a consolidation and revision of CS24-30 and CS25-30, under the title of Recommended Commercial Standard for Screw Threads and Tap-Drill Sizes, was circulated for acceptance. Those concerned have since accepted and approved the standard as shown herein for promulgation by the United States Department of Com- merce, through the National Bureau of Standards.