Guideline for the Certification of Wind Turbines
Total Page:16
File Type:pdf, Size:1020Kb
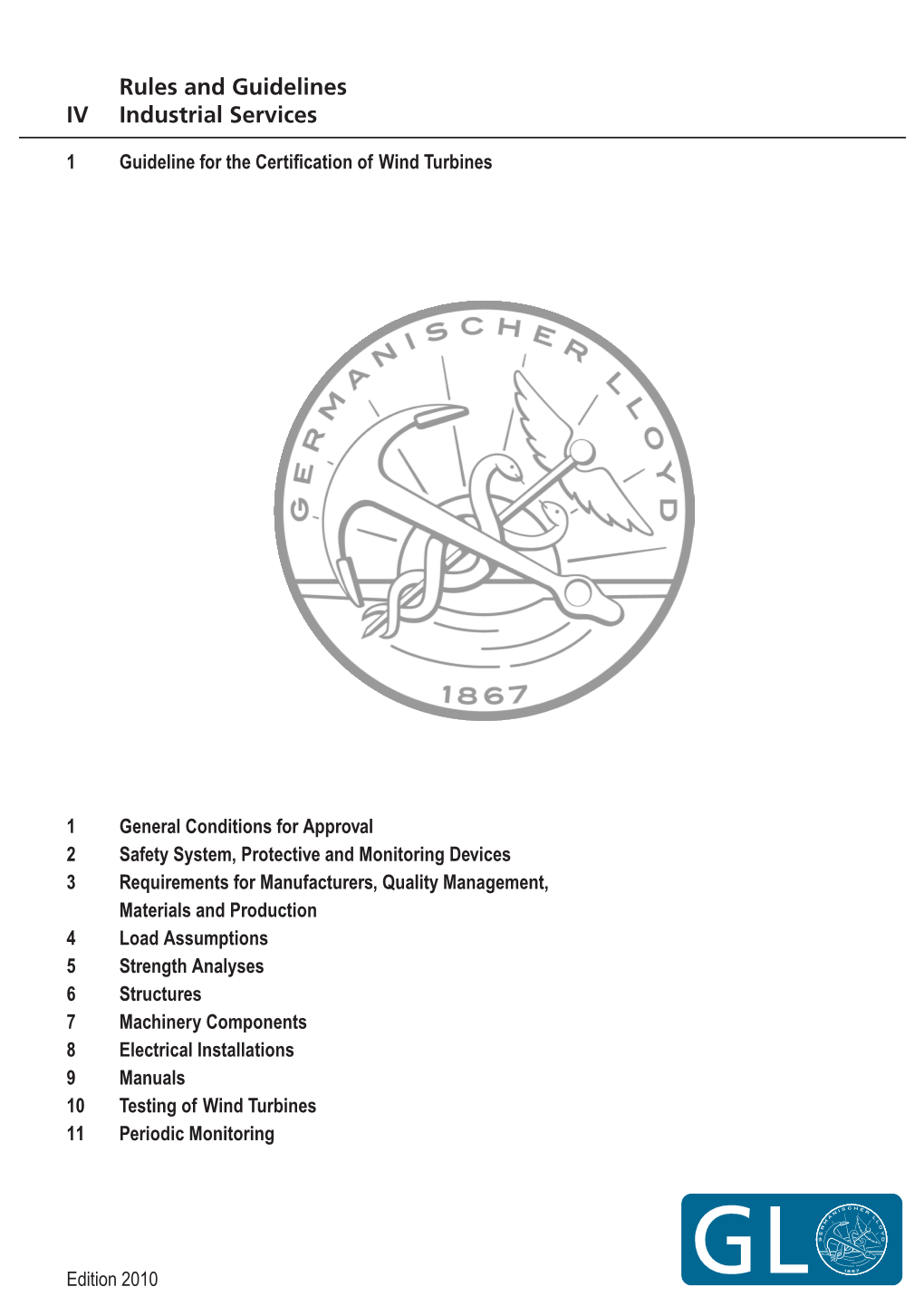
Load more
Recommended publications
-
Page 1 of 37 Current Standards Activities 5/4/2014 Http
Current Standards Activities Page 1 of 37 Browse By Group: View All New Publications | Supplements | Amendments | Errata | Endorsements | Reaffirmations | Withdrawals | Formal Interpretations | Informs & Certification Notices | Previous Reports Last updated: May 2, 2014 New Publications This section lists new standards, new editions (including adoptions), and special publications that have been recently published. Clicking on "View Detail" will display the scope of the document and other details available on CSA’s Online store. Program Standard Title Date Posted Scope Electrical / CAN/CSA-C22.2 NO. Household and similar electrical appliances - Safety - Part 2-45: 4/17/2014 View Detail Electronics 60335-2-45:14 Particular requirements for portable heating tools and similar appliances (Adopted IEC 60335-2-45:2002, edition 3:2002, consolidated with amendment 1:2008 and amendment 2:2011, with Canadian deviations) Appareils électrodomestiques et analogues - Sécurité - Partie 2-45 : Règles particulières pour les outils chauffants mobiles et appareils analogues (norme CEI 60335-2-45:2002 adoptée, edition 3:2002, consolidée par l'amendement 1:2008 et l'amendement 2:2011, avec exigences propres au Canada) http://standardsactivities.csa.ca/standardsactivities/recent_infoupdate.asp 5/4/2014 Current Standards Activities Page 2 of 37 Gas Equipment ANSI Z21.41-2014/CSA Quick disconnect devices for use with gas fuel appliances 4/10/2014 View Detail 6.9-2014 Gas Equipment ANSI Z21.74-2014 Portable refrigerators for use with HD-5 propane gas 4/10/2014 View Detail Electrical / CAN/CSA-C22.2 NO. Low-voltage switchgear and controlgear - Part 4-1: Contactors and 4/10/2014 View Detail Electronics 60947-4-1-14 motor-starters - Electromechanical contactors and motor-starters (Bi-national standard, with UL 60947-1) Electrical / CAN/CSA-C22.2 NO. -
Analysis and Countermeasures of China's Green Electric Power
sustainability Review Analysis and Countermeasures of China’s Green Electric Power Development Keke Wang 1,2, Dongxiao Niu 1,2, Min Yu 1,2, Yi Liang 3,4,* , Xiaolong Yang 1,2, Jing Wu 1 and Xiaomin Xu 1,2 1 School of Economics and Management, North China Electric Power University, Changping District, Beijing 102206, China; [email protected] (K.W.); [email protected] (D.N.); [email protected] (M.Y.); [email protected] (X.Y.); [email protected] (J.W.); [email protected] (X.X.) 2 Beijing Key Laboratory of New Energy Power and Low-Carbon Development, School of Economics and Management, North China Electric Power University, Changping District, Beijing 102206, China 3 School of Management, Hebei GEO University, Shijiazhuang 050031, China 4 Strategy and Management Base of Mineral Resources in Hebei Province, Hebei GEO University, Shijiazhuang 050031, China * Correspondence: [email protected] Abstract: The green development of electric power is a key measure to alleviate the shortage of energy supply, adjust the energy structure, reduce environmental pollution and improve energy efficiency. Firstly, the situation and challenges of China’s power green development is analyzed. On this basis, the power green development models are categorized into two typical research objects, which are multi-energy synergy mode, represented by integrated energy systems, and multi-energy combination mode with clean energy participation. The key points of the green power development model with the consumption of new energy as the core are reviewed, and then China’s exploration of the power green development system and the latest research results are reviewed. -
Efficient Probabilistic Analysis of Offshore Wind Turbines Based On
Efficient probabilistic analysis of offshore wind turbines based on time-domain simulations Von der Fakultät für Bauingenieurwesen und Geodäsie der Gottfried Wilhelm Leibniz Universität Hannover zur Erlangung des Grades Doktor-Ingenieur - Dr.-Ing. - genehmigte Dissertation von Clemens Janek Hübler M. Sc. 2019 Hauptreferent: Prof. Dr.-Ing. habil. Raimund Rolfes, Leibniz Universität Hannover Korreferent: Prof. John Dalsgaard Sørensen, M.Sc., Lic.techn., B.Com. Aalborg University Tag der mündlichen Prüfung: 11. Januar 2019 Abstract Offshore wind energy plays an important role in the successful implementation of the energy transition. However, without subsidies, it is not yet sufficiently competitive compared to other renewables or conventional fossil fuels. This is why offshore wind turbines have to be structurally optimised with regard to economic efficiency. One possibility to significantly increase economic efficiency is to improve the reliability or at least to assess present reliability levels precisely. For an accurate reliability assessment during the design phase, probabilistic analyses based on time-domain simulations have to be conducted. In this thesis, a methodol- ogy for a comprehensive probabilistic design of offshore wind turbines with special focus on their substructures is developed and applied. All investigations are based on time-domain simulations. This leads to more accurate results compared to semi-analytical approaches that are commonly used for probabilistic modelling at the expense of higher computing times. In contrast to previous probabilistic analyses, considering only particular aspects of the probabilistic design, this work defines a comprehensive analysis that can be split up into the following seven aspects: deterministic load model, resistance model (failure modes), uncer- tainty of inputs, design of experiments, sensitivity analysis, long-term extrapolation/lifetime distribution, and economic effects. -
Assessment of Offshore Wind System Design, Safety, and Operation
Assessment of Offshore Wind System Design, Safety, and Operation Standards Senu Sirnivas and Walt Musial National Renewable Energy Laboratory Bruce Bailey and Matthew Filippelli AWS Truepower LLC NREL is a national laboratory of the U.S. Department of Energy Office of Energy Efficiency & Renewable Energy Operated by the Alliance for Sustainable Energy, LLC. This report is available at no cost from the National Renewable Energy Laboratory (NREL) at www.nrel.gov/publications. Technical Report NREL/TP-5000-60573 January 2014 Contract No. DE-AC36-08GO28308 Assessment of Offshore Wind System Design, Safety, and Operation Standards Senu Sirnivas and Walt Musial National Renewable Energy Laboratory Bruce Bailey and Matthew Filippelli AWS Truepower LLC Prepared under Task No. WE11.5057 NREL is a national laboratory of the U.S. Department of Energy Office of Energy Efficiency & Renewable Energy Operated by the Alliance for Sustainable Energy, LLC. This report is available at no cost from the National Renewable Energy Laboratory (NREL) at www.nrel.gov/publications. National Renewable Energy Laboratory Technical Report 15013 Denver West Parkway NREL/TP-5000-60573 Golden, CO 80401 January 2014 303-275-3000 • www.nrel.gov Contract No. DE-AC36-08GO28308 NOTICE This report was prepared as an account of work sponsored by an agency of the United States government. Neither the United States government nor any agency thereof, nor any of their employees, makes any warranty, express or implied, or assumes any legal liability or responsibility for the accuracy, completeness, or usefulness of any information, apparatus, product, or process disclosed, or represents that its use would not infringe privately owned rights. -
Adobe Reader
Turinys AKTUALIJOS .................................................................................................... 5 SEMINARAS MAÞOMS IR VIDUTINËMS ÁMONËMS „DALYVAVIMAS STANDARTIZACIJOJE IR STANDARTØ TAIKYMAS – MVÁ PRIVALUMAI“ ........... 5 RENGIAMAS LST EN ISO 5667-3 VANDENS KOKYBË. MËGINIØ ËMIMAS. 3 DALIS. VANDENS MËGINIØ KONSERVAVIMAS IR APDOROJIMAS (ISO 5667-3:2012) LIETUVIØ KALBA .................................................................. 5 SUKURTA PAGRINDINIØ MAÐINØ SRITIES TERMINØ DUOMENØ BAZË, PALENGVINANTI STANDARTØ RENGIMÀ NACIONALINËMIS KALBOMIS ......... 6 ISO SEMINARAS APIE ENERGIJOS VADYBOS STANDARTÀ ISO 50001, JO TAIKYMO GALIMYBES IR NAUDÀ VYKO VILNIUJE ...................................... 6 STANDARTIZACIJA .......................................................................................... 9 INFORMACIJA APIE VIEÐAJAI APKLAUSAI TEIKIAMUS EUROPOS IR LIETUVOS STANDARTØ BEI KITØ LEIDINIØ PROJEKTUS ................................ 9 IÐLEISTI LIETUVOS STANDARTAI IR KITI LEIDINIAI ........................................... 9 NETEKÆ GALIOS LIETUVOS STANDARTAI IR KITI LEIDINIAI .............................. 16 NETEKSIANTIS GALIOS LIETUVOS STANDARTAS ............................................. 21 SIÛLOMAS SKELBTI NETEKSIANÈIU GALIOS ORIGINALUSIS LIETUVOS STANDARTAS ................................................................................... 21 TARPTAUTINIØ IR EUROPOS ÁSTAIGØ BEI ORGANIZACIJØ STANDARTAI IR KITI LEIDINIAI, KURIUOS DEPARTAMENTAS GAVO KOVO MËNESÁ .................. 22 TARPTAUTINËS STANDARTIZACIJOS -
The Economics of Wind Power in China and Policy Implications
Energies 2015, 8, 1529-1546; doi:10.3390/en8021529 OPEN ACCESS energies ISSN 1996-1073 www.mdpi.com/journal/energies Article The Economics of Wind Power in China and Policy Implications Zifa Liu 1, Wenhua Zhang 2,†, Changhong Zhao 2,† and Jiahai Yuan 2,* 1 School of Electrical & Electronic Engineering, North China Electric Power University, Chang Ping District, Beijing 102206, China; E-Mail: [email protected] 2 School of Economics and Management, North China Electric Power University, Chang Ping District, Beijing 102206, China; E-Mails: [email protected] (W.Z.); [email protected] (C.Z.) † These authors contributed equally to this work. * Author to whom correspondence should be addressed; E-Mail: [email protected]; Tel./Fax: +86-10-6177-3091. Academic Editor: Erik Gawel Received: 6 December 2014 / Accepted: 4 February 2015 / Published: 17 February 2015 Abstract: In 2009, the implementation of feed-in tariff (FIT) and attractive public subsidies for onshore wind farms aroused great investment enthusiasm and spurred remarkable development of wind power in China. Meanwhile, rapid learning-by-doing has significantly cut down the cost of wind turbines and the capital cost of wind farms as well. Therefore, it is the right time to examine the appropriateness of the existing FIT policy for wind power in China. In this paper, we employ the analytical framework for levelized cost of electricity (LCOE) to model the generation cost of wind power. Results show that the existing FIT policy is attractive to investors, but serious curtailment and turbine quality issues could make wind power unprofitable. Meanwhile, rapid substantial decreases in the cost of wind power have made it competitive to coal power in 2013, implying that it is possible and necessary to reform the FIT policy for new wind farms. -
I.ICT-2011-285135 FINSENY D1.11 Version 1.0 Security Elements for the FINSENY Functional Architecture
Ref. Ares(2014)490312 - 25/02/2014 FINSENY D1.11 , Version 1.0 I.ICT-2011-285135 FINSENY D1.11 version 1.0 Security Elements for the FINSENY Functional Architecture Contractual Date of Delivery to the CEC: March 30 th , 2013 Actual Date of Delivery to the CEC: March 30 th , 2013 Author(s): Lionel Besson, Steffen Fries, Andreas Furch, Henryka Jormakka, Fabienne Waidelich, Maria M artin-De-Vidales-Ramirez Participant(s): Siemens AG, Thales, VTT, Atos Research & Innovation Workpackage: WP1, Task 1.6 Security Estimated person months: (resources spent on the deliverable) Security: PU Nature: R Version: 1.0 Total number of pages: 134 Abstract: Deliverable D1.11 presents all FINSENY security elements, especially including the energy domain specific security elements needed for the FINSENY scenarios. These are described as enablers, constraints, general elements countermeasures, or controls. Scenario specific security elements needed for FINSENY are also analyzed. It represents a direct continuation of deliverable D1.10 [181] and therefore fully includes its structure and content. Keyword list: Threat and risk analysis, security, risk assessment, interfaces, security requirements, scenario, use case, system analysis, authentication, authorization, privacy, confidentiality, trust domain, availability, reliability, functional architecture, security enablers, security standards, security elements, FINSENY, FI- WARE Disclaimer: Page 1 (134) FINSENY D1.11 , Version 1.0 Not applicable. Page 2 (134) FINSENY D1.11 , Version 1.0 Executive Summary D1.11, titled “Security Elements for the FINSENY Functional Architecture” is a direct continuation of deliverable D1.10 [181] and therefore fully includes the structure and contents of it. D1.11 is thus as well based upon a threat and risk analysis which led to the definition of a set of security requirements that can be applied to all scenario work packages and a scenario specific security requirement. -
Decarbonizing China's Power System with Wind Power
January 2015 Decarbonizing China’s power system with wind power: the past and the future OIES PAPER: EL 11 Xin Li The contents of this paper are the author’s sole responsibility. They do not necessarily represent the views of the Oxford Institute for Energy Studies or any of its members. Copyright © 2015 Oxford Institute for Energy Studies (Registered Charity, No. 286084) This publication may be reproduced in part for educational or non-profit purposes without special permission from the copyright holder, provided acknowledgment of the source is made. No use of this publication may be made for resale or for any other commercial purpose whatsoever without prior permission in writing from the Oxford Institute for Energy Studies. ISBN 978-1-78467-019-1 i Abstract Wind power in China has experienced significant growth since the beginning of this century. Total installed capacity has increased almost 300 fold – from 346 MW in 2000 to 91,413 MW in 2013. This rapid development has had two major drivers: • First, the excellent wind power resource in China, especially in the north of the country, and the increasing competitiveness of wind generation worldwide. • Second, favourable government policies such as: mandatory targets for major power generators in relation to renewable energy; the decentralization of plant approval rights; and feed-in tariffs for wind generation. Along with the development of domestic wind turbine manufacturing capacity, these factors have stimulated the growth of wind power over the past 10 years or so. However, this rapid development has itself created new challenges. In particular, wind power has not been fully integrated into the electricity system as a whole, as the growth of wind generation capacity has not been matched by a corresponding growth in transmission capacity. -
Twincat 3 Wind Framework for Wind Turbine Automation 1 Framework and 10 Years of Expertise Through 40,000 Installations
cover PC Control | Wind Special 2015 PC Control | Wind Special 2015 cover TwinCAT 3 Wind Framework for wind turbine automation 1 Framework and 10 years of expertise through 40,000 installations The new TwinCAT 3 Wind Framework will enable manufacturers of wind turbines to program their systems quickly and easily on their own. All functions are integrated into one universal software package: from event management to database connectivity, and even basic func- ttitionsonns susuchch aass sststateate macmachinehine anandd hyhydraulics.draulics. A preprefabricatedf application template considerably sisimplifiesmmplifies tthehhe pprogrammingrogramming pprocess,rocess, enablienablingng ddevelopers to concentrate on the essential sysystemstem ffunctions.unctions. The resuresult:lt: efefficientficient enengineering,gineering shorter time-to-market, and the benefits oof IndIndustryusttry 4.4.00 foforr ththee wind indindustry.ustry. © AREVA Wind/Jan Oelker cover PC Control | Wind Special 2015 Cloud Database TwinCAT Transport Layer – ADS Proxy Database TcCOM TcCOM Status Parameter Command TcCOM TcCOM TcCOM Statistics Capture User Framework (Generic) Framework TcCOM TcCOM TcCOM TwinCAT 3 Wind Library PLC Supervisory Operational Simulation TcCOM Control Control Pitch Rotor Generator Converter Yaw Template (Specifi c) Fieldbus Application templates and encapsulated Comprehensive functionalities are implemented in encapsulated TwinCAT mod- ules, which are then integrated into the TwinCAT 3 architecture. Efficient soft- modules enable modular software ware development is ensured through a modular architecture in the application architecture with high functionality template, as well as through proven and directly applicable TwinCAT modules and functions. The flexible configuration makes adaptation to user-specific application requirements very straightforward. System diagnostic functionality Beckhoff has offered advanced wind industry solutions for over 16 years. -
Communication Network Standards for Smart Grid Infrastructures
Article Communication Network Standards for Smart Grid Infrastructures Konstantinos Demertzis 1,2,* , Konstantinos Tsiknas 3, Dimitrios Taketzis 4 , Dimitrios N. Skoutas 5 , Charalabos Skianis 5, Lazaros Iliadis 2 and Kyriakos E. Zoiros 3 1 Department of Physics, Faculty of Sciences, Kavala Campus, International Hellenic University, 65404 St. Loukas, Greece 2 Faculty of Mathematics Programming and General Courses, School of Civil Engineering, Democritus University of Thrace, Kimmeria, 67100 Xanthi, Greece; [email protected] 3 Department of Electrical and Computer Engineering, Democritus University of Thrace, Vas. Sofias 12, 67100 Xanthi, Greece; [email protected] (K.T.); [email protected] (K.E.Z.) 4 Hellenic National Defense General Staff, Stratopedo Papagou, Mesogeion 227-231, 15561 Athens, Greece; [email protected] 5 Department of Information and Communication Systems Engineering, University of the Aegean, Samos, 83200 Karlovassi, Greece; [email protected] (D.N.S.); [email protected] (C.S.) * Correspondence: [email protected] Abstract: Upgrading the existing energy infrastructure to a smart grid necessarily goes through the provision of integrated technological solutions that ensure the interoperability of business processes and reduce the risk of devaluation of systems already in use. Considering the heterogeneity of the current infrastructures, and in order to keep pace with the dynamics of their operating environment, we should aim to the reduction of their architectural complexity and the addition of new and more efficient technologies and procedures. Furthermore, the integrated management of the Citation: Demertzis, K.; Tsiknas, K.; overall ecosystem requires a collaborative integration strategy which should ensure the end-to-end Taketzis, D.; Skoutas, D.N.; Skianis, interconnection under specific quality standards together with the establishment of strict security C.; Iliadis, L.; Zoiros, K.E. -
Communication Network Architectures for Smart-Wind Power Farms
Energies 2014, 7, 3900-3921; doi:10.3390/en7063900 OPEN ACCESS energies ISSN 1996-1073 www.mdpi.com/journal/energies Article Communication Network Architectures for Smart-Wind Power Farms Mohamed A. Ahmed 1 and Young-Chon Kim 2,* 1 Department of Computer Engineering, Chonbuk National University, Jeonju 561-756, Korea; E-Mail: [email protected] 2 Smart Grid Research Center, Chonbuk National University, Jeonju 561-756, Korea * Author to whom correspondence should be addressed; E-Mail: [email protected]; Tel.: +82-63-270-2413; Fax: +82-63-270-2394. Received: 11 February 2014; in revised form: 28 May 2014 / Accepted: 9 June 2014 / Published: 23 June 2014 Abstract: Developments in the wind power industry have enabled a new generation of wind turbines with longer blades, taller towers, higher efficiency, and lower maintenance costs due to the maturity of related technologies. Nevertheless, wind turbines are still blind machines because the control center is responsible for managing and controlling individual wind turbines that are turned on or off according to demand for electricity. In this paper, we propose a communication network architecture for smart-wind power farms (Smart-WPFs). The proposed architecture is designed for wind turbines to communicate directly and share sensing data in order to maximize power generation, WPF availability, and turbine efficiency. We also designed a sensor data frame structure to carry sensing data from different wind turbine parts such as the rotor, transformer, nacelle, etc. The data frame includes a logical node ID (LNID), sensor node ID (SNID), sensor type (ST), and sensor data based on the International Electrotechnical Commission (IEC) 61400-25 standard. -
HZN Oglasnik Za Normativne Dokumente 3
Hrvatski zavod za norme Oglasnik za normativne dokumente 3/2013 lipanj, 2013. Oglasnik za normativne dokumente Hrvatskog zavoda za norme sadrži popise hrvatskih norma, nacrta hrvatskih norma, prijedloga za prihvaćanje stranih norma u izvorniku, povučene hrvatske norme, povučene nacrte hrvatskih norma te ispravke, rezultate europske i međunarodne normizacije razvrstane po predmetnom ustroju i obavijesti HZN-a. Tko u popisima normativnih dokumenata koji su objavljeni u ovom Oglasniku otkrije koju grešku, koja može voditi do krive primjene, moli se da o tome neodložno obavijesti Hrvatski zavod za norme, kako bi se mogli otkloniti uočeni propusti. Izdavač: Sadržaj: 1 Rezultati hrvatske normizacije 2 Rezultati međunarodne i europske 1.1 Hrvatske norme ............................................................ A3 normizacije razvrstani po predmetnom ustroju .................................................A57 1.2 Nacrti hrvatskih norma ............................................... A28 1.3 Prijedlozi za prihvaćanje stranih norma u izvorniku ... A28 3 Popis radnih dokumenata Codex Alimentariusa 1.4 Povučene hrvatske norme.......................................... A38 1.5 Povučeni nacrti hrvatskih norma ....................................... 4 Obavijesti HZN-a 4.1 Cjenik hrvatskih norma 1.6 Ispravci hrvatskih norma .............................................A52 1.7 Naslovi objavljenih hrvatskih norma na hrvatskome jeziku........................................................A53 1.8 Drugi normativni dokumenti 1.9 Opća izdanja HZN-a A2 HZN