Feb. 19, 1935. J. W. LOGAN, JR 1,991,903 IEEE
Total Page:16
File Type:pdf, Size:1020Kb
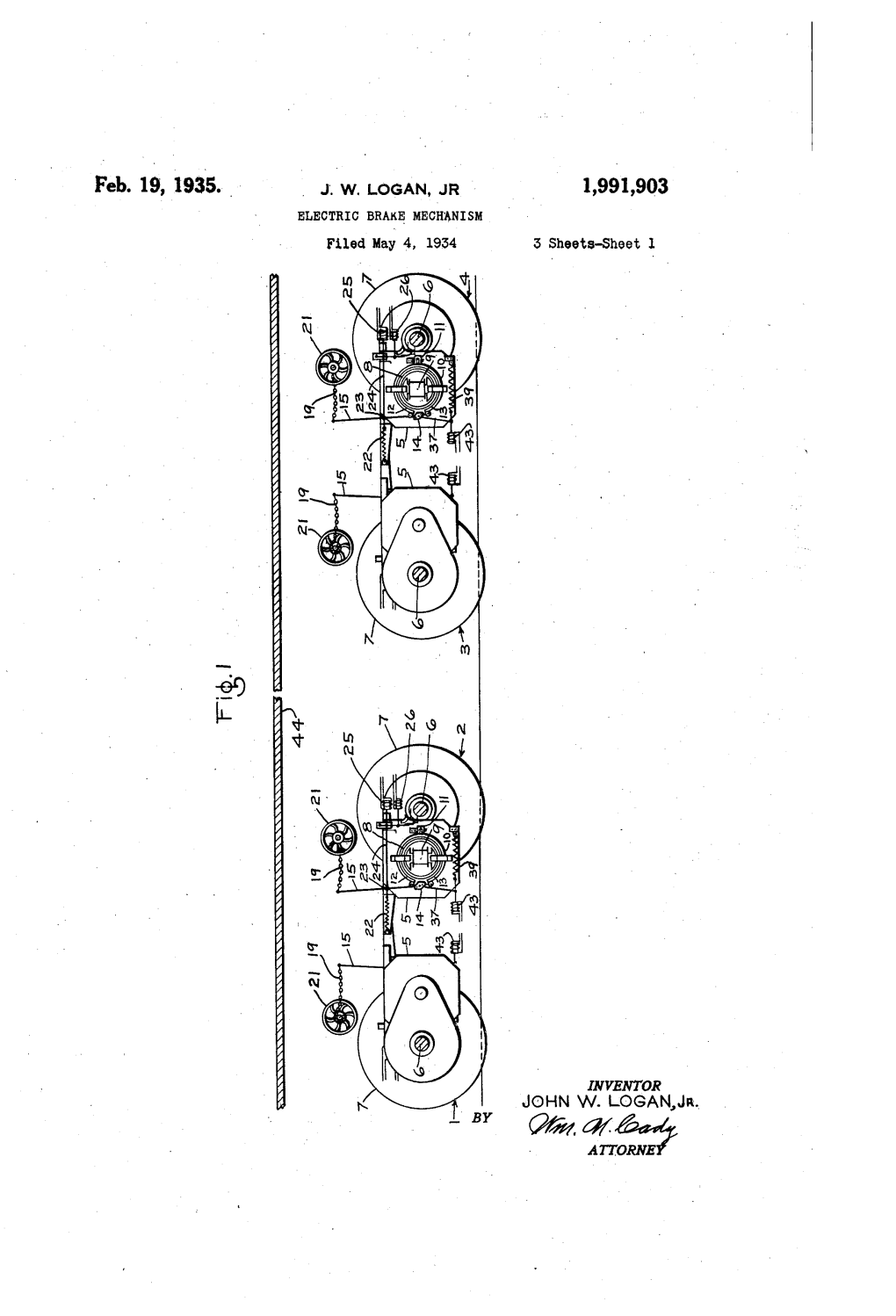
Load more
Recommended publications
-
Eddy Current Braking in Automobiles Sarath G Nath1, Rohith Babu2, George Varghese Biju3, Ashin S4 , Dr
International Research Journal of Engineering and Technology (IRJET) e-ISSN: 2395-0056 Volume: 05 Issue: 04 | Apr-2018 www.irjet.net p-ISSN: 2395-0072 Eddy Current Braking In Automobiles Sarath G Nath1, Rohith Babu2, George Varghese Biju3, Ashin S4 , Dr. Cibu K Varghese5 1,2,3,4B Tech student, Mechanical Engineering Department Mar Athanasius college of Engineering, Kerala 5Professor, Mechanical Engineering Department, Mar Athanasius College of Engineering, Kerala ---------------------------------------------------------------------***--------------------------------------------------------------------- Abstract - Eddy Current Braking slows a moving object by through a stationary magnetic field (Jou et al, 2006) [8]. The creating eddy currents through electromagnetic induction changing magnetic flux induces eddy currents in the which create resistance. In normal case if the speed of the conductor and these currents dissipate energy and generate vehicle is very high, the brake does not provide that amount of drag force (Jou et al, 2006) [8]. Therefore, there are no high braking force and it will leads to skidding and wear& tear contacting elements by using this electromagnetic braking of the vehicle. Because of this drawbacks of ordinary brakes, system which will lead to reduce the wear of brake pad. This arises a simple and effective mechanism of braking system situation will also reduce the wear debris pollution into our ‘The eddy current brake’. Eddy current is one of the most environment. outstanding of electromagnetic induction phenomena. Even though it appear many technical problems because dissipative 1.1 Conventional Braking System nature it has some valuable contributions. It is a frictionless method for braking of vehicles including trains. As it is a Braking forms an important part of motion of any frictionless brake, periodic change of braking components are automobile or locomotive. -
Modeling and Design Optimization of Electromechanical Brake Actuator Using Eddy Currents
Modeling and Design Optimization of Electromechanical Brake Actuator Using Eddy Currents by Kerem Karakoc MASc, University of Victoria, 2007 BSc, Bogazici University, 2005 A Dissertation Submitted in Partial Fulfillment of the Requirements for the Degree of DOCTOR OF PHILOSOPHY in the Department of Mechanical Engineering. Kerem Karakoc, 2012 University of Victoria All rights reserved. This dissertation may not be reproduced in whole or in part, by photocopy or other means, without the permission of the author. ii Modeling and Design Optimization of Electromechanical Brake Actuator Using Eddy Currents by Kerem Karakoc MASc, University of Victoria, 2007 BSc, Bogazici University, 2005 Supervisory Committee Dr. Afzal Suleman, Dept. of Mechanical Engineering, University of Victoria Co-Supervisor Dr. Edward Park, Dept. of Mechanical Engineering, University of Victoria Co-Supervisor Dr. Ned Djilali, Dept. of Mechanical Engineering, University of Victoria Departmental Member Dr. Issa Traore, Dept. of Electrical and Computer Engineering, University of Victoria Outside Member iii Supervisory Committee Dr. Afzal Suleman, Dept. of Mechanical Engineering, University of Victoria Co-Supervisor Dr. Edward Park, Dept. of Mechanical Engineering, University of Victoria Co-Supervisor Dr. Ned Djilali, Dept. of Mechanical Engineering, University of Victoria Departmental Member Dr. Issa Traore, Dept. of Electrical and Computer Engineering, University of Victoria Outside Member Abstract A novel electromechanical brake (EMB) based on the eddy current principle is proposed for application in electrical vehicles. The proposed solution is a feasible replacement for the current conventional hydraulic brake (CHB) systems. Unlike CHBs, eddy current brakes (ECBs) use eddy currents and their interaction with an externally applied magnetic field to generate braking torque. -
Non-Propellant Eddy Current Brake and Traction in Space Using Magnetic Pulses
aerospace Article Non-Propellant Eddy Current Brake and Traction in Space Using Magnetic Pulses Yi Zhang †, Qiang Shen †, Liqiang Hou † and Shufan Wu * School of Aeronautics and Astronautics, Shanghai Jiao Tong University, No. 800, Dongchuan Road, Minhang District, Shanghai 200240, China; [email protected] (Y.Z.); [email protected] (Q.S.); [email protected] (L.H.) * Correspondence: [email protected]; Tel.: +86-34208597 † These authors contributed equally to this work. Abstract: The safety of on-orbit satellites is threatened by space debris with large residual angular velocity and the space debris removal is becoming more challenging than before. This paper explores the non-contact despinning and traction problem of high-speed rotating targets and proposes an eddy current brake and traction technology for space targets without any propellant consumption. The principle of the conventional eddy current brake is analyzed in this article and the concept of eddy current brake and traction without propellant is put forward for the first time. Secondly, according to the key technical requirements, a brand-new structure of a satellite generating artificial magnetic field is designed accordingly. Then the control mechanism of eddy current brake and traction without propellant is analyzed qualitatively by simplifying the model and conditions. Then, the magnetic pulse control method is proposed and analyzed quantitatively. Finally, the feasibility of the technology is verified by the numerical simulation method. According to the simulation results, the eddy current brake and traction technology based on magnetic pulses can make the angular speed of target decrease linearly without propellant during the process. -
Effective Eddy Current Braking at Low and High Vehicular Speeds – a Simulation Study
Archives of Current Research International 8(4): 1-11, 2017; Article no.ACRI.34042 ISSN: 2454-7077 Effective Eddy Current Braking at Low and High Vehicular Speeds – A Simulation Study Alumona Louis Olisaeloka 1* , Azaka Onyemazuwa Andrew 2 and Nwadike Emmauel Chinagorom 2 1Department of Electrical Engineering, Nnamdi Azikiwe University, Awka, Nigeria. 2Department of Mechanical Engineering, Nnamdi Azikiwe University, Awka, Nigeria. Author’s contributions This work was carried out in collaboration between all authors. Author ALO designed the study, performed the statistical analysis, wrote the protocol, and wrote the first draft of the manuscript. Authors AOA and NEC managed the analyses of the study. Author NEC managed the literature searches. All authors read and approved the final manuscript. Article Information DOI: 10.9734/ACRI/2017/34042 Editor(s): (1) Preecha Yupapin, Department of Physics, King Mongkut’s Institute of Technology Ladkrabang, Thailand. (2) M. A. Elbagermi, Chemistry Department, Misurata University, Libya. (3) Alexandre Gonçalves Pinheiro, Physics, Ceara State University, Brazil. Reviewers: (1) Meshack Hawi, Jomo Kenyatta University of Agriculture and Technology, Kenya. (2) Mohamed Zaher, University of Illinois at Chicago, USA. Complete Peer review History: http://www.sciencedomain.org/review-history/20351 Received 10 th May 2017 Accepted 16 th July 2017 Original Research Article th Published 4 August 2017 ABSTRACT Conventional eddy current braking is limited in effectiveness to only the high vehicular speed region. As the vehicle slows, the conventional eddy current brake loses effectiveness. This inherent drawback is due to the use of static/stationary magnetic field in the brake system. This study presents a solution - the use of rotating magnetic field in the brake system. -
Conceptualization of a New Product Development Framework for Eddy Current Braking Systems for Heavy Vehicles in Zimbabwe
Proceedings of the 2017 International Conference on Industrial Engineering and Operations Management (IEOM) Bristol, UK, July 24-25, 2017 Conceptualization of a New Product Development Framework for Eddy Current Braking Systems for Heavy Vehicles in Zimbabwe Wilson R. Nyemba Department of Mechanical Engineering Science, Faculty of Engineering and the Built Environment, University of Johannesburg, Auckland Park 2006, Johannesburg, South Africa [email protected] Chris Pote, Tauyanashe Chikuku Department of Mechanical Engineering, University of Zimbabwe, P O Box MP 167, Mount Pleasant, Harare, Zimbabwe [email protected], [email protected] Charles Mbohwa Professor of Sustainability Engineering, Department of Quality and Operations Management & Vice Dean for Research and Innovation, Faculty of Engineering and the Built Environment, University of Johannesburg, Auckland Park 2006, Johannesburg, South Africa [email protected] Abstract One of the most critical requirements for safety in vehicles is the availability of reliable braking systems. Most heavy vehicles in Zimbabwe employ the conventional hydraulic braking system. However changes and improvements in technology have seen the introduction of retarders that make use of magnets and eddy currents. The new technology is friction free but still deemed expensive and thus not yet readily acceptable to vehicle manufacturers for fears of reliability and cost. Hydraulic brakes are equally expensive in the long run owing to maintenance and frequent replacement of brake pads and rotors, particularly in Zimbabwe where the road infrastructure has deteriorated significantly over the years. A case study was carried out at a Zimbabwean company which specializes in the sales, service and backup of Scania heavy vehicles, with a special focus on the braking systems. -
Eddy Current Brake Eddy Current Brake (Order Code DTS-ECB) (Order Code DTS-ECB)
Eddy Current Brake Eddy Current Brake (Order Code DTS-ECB) (Order Code DTS-ECB) The Eddy Current Brake is a braking mechanism for use with our Dynamics Cart The Eddy Current Brake is a braking mechanism for use with our Dynamics Cart and Track System (order code DTS) carts and and Track System (order code DTS) carts and Go Direct® Sensor Cart (order code GDX-CART). Go Direct® Sensor Cart (order code GDX-CART). As the cart moves over the track, the magnets in the Eddy Current Brake create an As the cart moves over the track, the magnets in the Eddy Current Brake create an electromagnetic drag on the cart that is proportional to the cart’s speed. electromagnetic drag on the cart that is proportional to the cart’s speed. The Eddy Current Brake is not compatible with older metal carts that were part of The Eddy Current Brake is not compatible with older metal carts that were part of the discontinued Vernier Dynamics Systems (order code VDS) sold from 2005 to the discontinued Vernier Dynamics Systems (order code VDS) sold from 2005 to 2012. 2012. Assembly Assembly Insert the desired number of magnets into the Eddy Current Brake. Insert the desired number of magnets into the Eddy Current Brake. The Eddy Current Brake connectors swivel to allow 4 mm of height adjustment The Eddy Current Brake connectors swivel to allow 4 mm of height adjustment when installed in a cart. when installed in a cart. When the DTS stamp on the connector is upright, it is set at the correct height for When the DTS stamp on the connector is upright, it is set at the correct height for our DTS carts. -
Evaluation of Brake Parameters in Copper Discs of Various Thicknesses and Speeds Using Neodymium – Iron – Boron Magnets
MATEC Web of Conferences 144, 01003 (2018) https://doi.org/10.1051/matecconf/201814401003 RiMES 2017 Evaluation of brake parameters in copper discs of various thicknesses and speeds using Neodymium – Iron – Boron Magnets G. L. Anantha Krishna1 and K. M. Sathish Kumar1* 1Department of Mechanical Engineering, BMS Institute of Technology & Management, Bengaluru, 560064, India Abstract. Neodymium – Iron – Boron (NdFeB) permanent magnets of 12.5 mm thickness and 50 mm diameter are chosen for analyses because of their higher remanence and coercivity. Experimental analyses were carried out with Copper discs of thickness 4 mm, 6 mm and 8 mm at 2000 rpm, 3000 rpm, 4000 rpm and 5000 rpm. Experiments were conducted with three different positions of magnets such as 2 coaxial magnets, single magnet and single magnet with sudden application conditions. The brake parameters recorded are % speed reduction, deceleration and time taken. In 2 coaxial magnets condition, brake parameters are better in 6 mm thick disc. In single magnet condition, the brake parameters in 6 mm thick disc are found to be more consistent than 4 mm and 8 mm thick discs. In single magnet with sudden application condition, in 4 mm thick disc, the brake parameters are found better. During analysis, very high repulsion was experienced by magnet with 8 mm thick Copper disc at all the above mentioned speeds in single magnet with sudden application condition. For high speed train applications, single magnet condition with 6mm thick disc may be suitable. For high speed automotive applications, single magnet with sudden application condition with 4 mm thick disc may be suitable. -
ERTMS/ETCS – Class 1
ERTMS/ETCS Failure Modes and Effects Analysis for TIU in Application Level 1 and Level 2 REF : SUBSET 080-1/2 ISSUE : 3.0.12 DATE : 2014-05-08 Company Technical Approval Management approval ALSTOM ANSALDO AZD BOMBARDIER CAF SIEMENS THALES © This document has been developed and released by UNISIG SUBSET-080 1/2 Failure Modes and Effects Analysis for TIU in Application Level 1 and Level 2 Page 1/64 3.0.12 1. MODIFICATION HISTORY Issue Number Section Number Modification / Description Author Date 0.0.1. ALL Creation S. 16/03/01 Chassard 0.0.2 5 Revised after comments and to SCH 26/02/02 achieve consistency with subset 88 2.0.0. 3.1.1.2. Raised in issue for release to the WLH EEIG. 2.2.2. Final release after amendment to WLH reflect the comments in the final report from the ISA’s version 1.1 dated 07-03-03 as proposed via the Unisig consolidated review comments on the ISA report v 0.0.2 March 03. 3.0.0 ALL Update to SRS Baseline 3.3.0 C. Latorre (MERMEC) 3.0.1 ALL Update followed to RAMS WG C. Latorre meeting of 03-04 July 2012 (MERMEC) (Stockholm) 3.0.2 ALL Update followed to RAMS WG C. Latorre comments (MERMEC) 3.0.3 ALL Update followed to RAMS WG C. Latorre conf call meeting of 09 October (MERMEC) 2012 (see MoM ‘RAMS Meeting nr 2012:10 – telecon 2012-10- 09’). 3.0.4 - Footer of the first Some editorial changes. -
The Eddy-Current Brake Compatibility Project
GENERAL ENGINEERING Taking the brakes off Dr Daniel Valderas, leader of a project investigating the compatibility of state-of-the-art electromagnetic brakes with high-speed train systems across Europe, reveals some surprising findings from the research Could you outline how you came to work no mechanical contact between the brake and damage. This temperature limit can now on the Eddy CUrrent brake Compatibility track, there is no wear, fine dust, smell or noise be observed from the point of view of ECB (ECUC) project? from its usage. It can be used as both a service performance superimposed on the current and an emergency brake. Catenary power agents that increase rail temperature. In Our department at the Centro de supply is not essential in all ECBs. the case of electromagnetic emissions, the Investigaciones Técnicas de Gipuzkoa (CEIT), standard that probably lies closest to our a non-profit research institute in Spain, has a How has the project used electromagnetic and case study is the CLC TS 50238-3, which wealth of experience in the railway sector and thermal modelling to anticipate the behaviour defines compatibility between rolling stock provides technology to train manufacturers of railway systems? and train detection systems, particularly such as the Constructions and Auxiliary of in regard to axle counters. However, this Railways (CAF) and has coordinated high- Two computer models have been developed standard ignores the usage of ECBs. ECUC profile European Union projects. Together with in ECUC: one thermal, to anticipate the does not intend to directly impact on any major manufacturers such as Knorr-Bremse temperature of the track, and another standard, but can initiate a review by and Deutsche Bahn, we have encountered electromagnetic, to calculate the interference providing insights and recommendations. -
Pere.Pdf (1.778Mt)
SANNI PERE MAGNEETTITEKNOLOGIAN HYÖDYNTÄMINEN ENERGIA- JA LIIKENNESOVELLUTUKSISSA Kandidaatintyö Tarkastaja: lehtori Risto Mikkonen 18. joulukuuta 2017 i TIIVISTELMÄ Sanni Pere: Magneettiteknologian hyödyntäminen energia- ja liikennesovellutuksissa Tampereen teknillinen yliopisto Kandidaatintyö, 38 sivua, Joulukuu 2017 Tieto- ja sähkötekniikan kandidaatin tutkinto-ohjelma, sähkötekniikka Pääaine: Uusiutuvat sähköenergiateknologiat Tarkastaja: lehtori Risto Mikkonen Avainsanat: magneetti, magnetismi, energia, liikenne Työssä tarkastellaan energia- ja liikennesovelluksia magneettiteknologian näkökulmasta. Energiasovelluksissa pääpaino on sähkömagneettisessa induktiossa ja siinä, kuinka il- miötä hyödynnetään generaattoreissa. Tyypillisesti generaattoreissa käytetään sähkömag- neettia, mutta suuremman kokoluokan generaattoreissa kestomagneetin suosio on kasva- massa sen pienempien huoltokustannusten, painon, koon ja paremman hyötysuhteen an- siosta. Suprajohteet pitää jäähdyttää oikeaan toimintalämpötilaan, jotta suprajohtavia ominai- suuksia voidaan hyödyntää. Suprajohteiden avulla generaattorin painoa saadaan pienen- nettyä huomattavasti. Suprajohteissa tasavirta kulkee häviöttömästi, minkä ansiosta ge- neraattorin hyötysuhdetta saadaan kasvatettua sekä energiaa voidaan varastoida teoriassa kuinka pitkäksi aikaa vaan. Suprajohteiden ongelmaksi muodostuu nestemäisellä typellä tai heliumilla jäähdytetyn järjestelmän kalleus. Uudet tulevaisuuden kulkuneuvot hyödyntävät lineaarimoottoria ja magneettista levitaa- tiota. Kitkan aiheuttama vastus -
FFFIS Train Interface
ERTMS/ETCS FFFIS TI – Safety Analysis REF : SUBSET-120 ISSUE : 0.2.11 DATE : 2014-10-27 Company Technical Approval Management approval ALSTOM ANSALDO STS AZD BOMBARDIER CAF FAIVELEY TRANSPORT KNORR-BREMSE SIEMENS THALES © This document has been developed and released by UNISIG in collaboration with Faiveley Transport, Knorr-Bremse, Voith Turbo and Vossloh SUBSET-120 FFFIS TI – Safety Analysis Page 1/91 0.2.11 VOITH TURBO VOSSLOH © This document has been developed and released by UNISIG in collaboration with Faiveley Transport, Knorr-Bremse, Voith Turbo and Vossloh SUBSET-120 FFFIS TI – Safety Analysis Page 2/91 0.2.11 MODIFICATION HISTORY Issue Number Section Number Modification / Description Author Date 0.1.0 All First draft TIU safety group 2012-12-13 0.2.0 All Submission to sector for FB 2013-09-05 review 0.2.1 All Changes see review sheet JPG, FB Unisig_RAMS_WG_COM_ SS-120v0.2.0_v1.1.doc 0.2.2 All Changes see review sheet TIU safety group Unisig_SG_COM_SS- 120v0.2.0_v1.0.doc, Unisig_RAMS_WG_COM_ SS-120v0 2 0_v1 3.doc and Subset-120v020_review sheet_ERA_091013.doc; changed the FDT values to 48 h for regular functional tests and as typical FDT for TI inputs; changed the structure of the fault trees with redundancy; analysis added for Open MCB 0.2.3 5.1.4.8 – 5.1.4.10 SG comment 84 to Subset- FB 5.1.7.2.3.2; 119; 6.1 corrections in the FMEA and consistency with Subset-080 0.2.4 6.1 Failure reaction for sleeping FB changed according to discussion of SG comment 75 to Subset-119 0.2.5 3 – 5 EB option 4 deleted and TI Meeting Test in Progress -
WB/PB 43 Series Eddy-Current and Powder Dynamometers
WB/PB 43 MAGTROL Data Sheet WB/PB 43 Series Eddy-Current and Powder Dynamometers FEATURES • 4 Models with Maximum Torque from 1.5 N·m to 10 N·m (1.1 lb·ft to 7.3 lb·ft) • Braking Power: 0.5 kW to 3 kW • Stable Braking Torque, without Shock • Low Moment of Inertia • Low Residual Torque • Operation in Either Rotational Direction • Braking Torque Measurement Included • High Rotational Speed • Rated Torque Available From Zero Speed (Powder Dynamometers) Model 2 WB 43 • Integrated Optical Speed Sensor Eddy-Current Dynamometer DESCRIPTION MOTOR TESTING SYSTEMS Eddy-Current Brake Dynamometers (WB series) are ideal for Magtrol’s M-TEST 7 Software is a state-of-the-art motor applications requiring high speeds and also when operating in testing program for Windows®-based data acquisition. Used the middle to high power range. Eddy-Current Brakes provide with a Magtrol DSP7000 Programmable Dynamometer increasing torque as the speed increases, reaching peak torque Controller, Magtrol M-TEST 7 Software provides the control at rated speed. The dynamometers have low inertia as a result of any Magtrol Eddy-Current or Powder Brake Dynamometer of small rotor diameter. Brake cooling is provided by a water and runs test sequences in a manner best suited to the overall circulation system, which passes inside accuracy and efficiency of the Magtrol the stator to dissipate heat generated by Magtrol offers three types of dynamometer Motor Test System. The data that is the braking power. The water cooling brakes to absorb load: Hysteresis, Eddy- generated by Magtrol’s Motor Testing in the WB provides high continuous Current and Magnetic Powder.