Design and Analysis of the Eddy Current Brake with the Winding Change
Total Page:16
File Type:pdf, Size:1020Kb
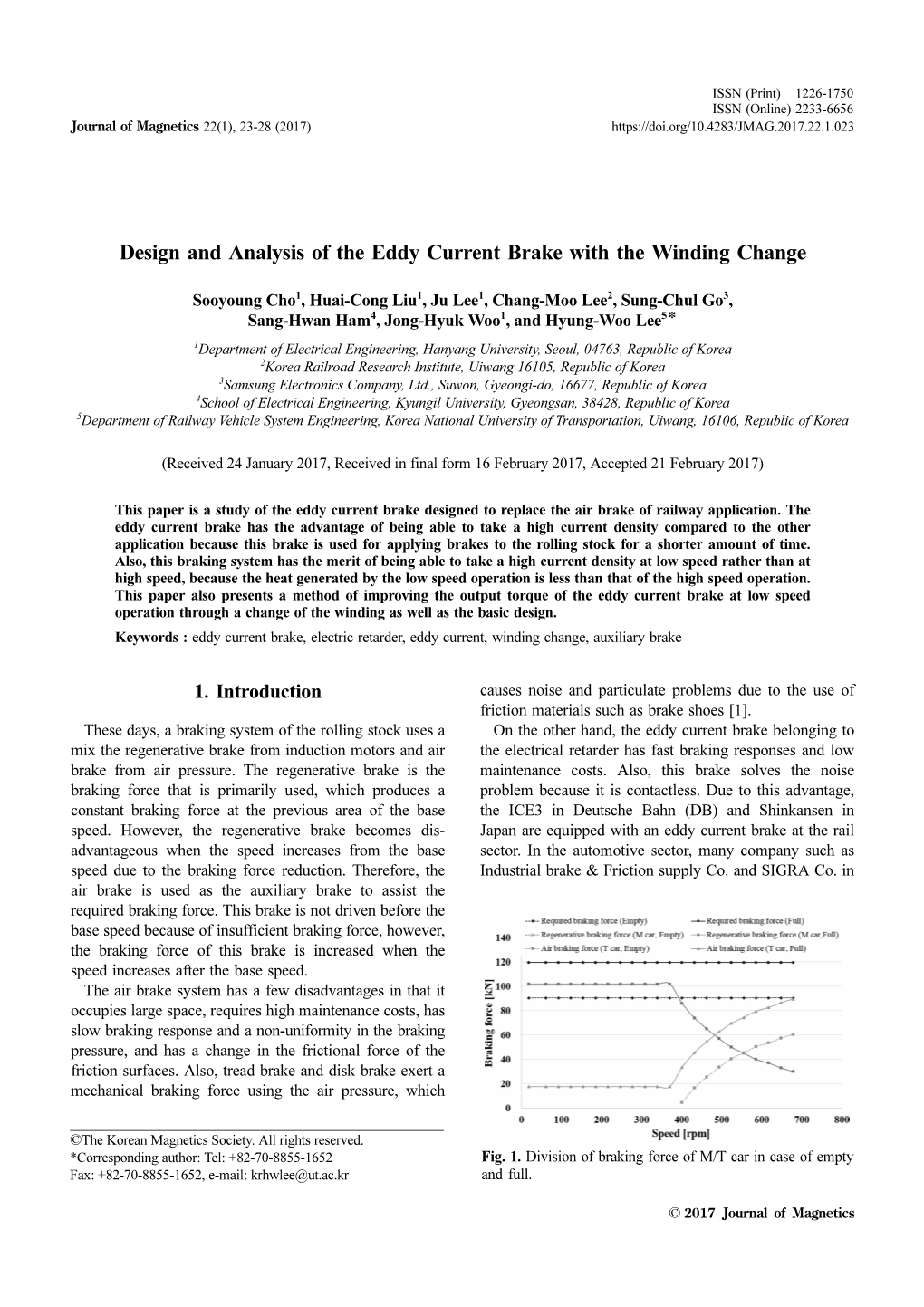
Load more
Recommended publications
-
Eddy Current Braking in Automobiles Sarath G Nath1, Rohith Babu2, George Varghese Biju3, Ashin S4 , Dr
International Research Journal of Engineering and Technology (IRJET) e-ISSN: 2395-0056 Volume: 05 Issue: 04 | Apr-2018 www.irjet.net p-ISSN: 2395-0072 Eddy Current Braking In Automobiles Sarath G Nath1, Rohith Babu2, George Varghese Biju3, Ashin S4 , Dr. Cibu K Varghese5 1,2,3,4B Tech student, Mechanical Engineering Department Mar Athanasius college of Engineering, Kerala 5Professor, Mechanical Engineering Department, Mar Athanasius College of Engineering, Kerala ---------------------------------------------------------------------***--------------------------------------------------------------------- Abstract - Eddy Current Braking slows a moving object by through a stationary magnetic field (Jou et al, 2006) [8]. The creating eddy currents through electromagnetic induction changing magnetic flux induces eddy currents in the which create resistance. In normal case if the speed of the conductor and these currents dissipate energy and generate vehicle is very high, the brake does not provide that amount of drag force (Jou et al, 2006) [8]. Therefore, there are no high braking force and it will leads to skidding and wear& tear contacting elements by using this electromagnetic braking of the vehicle. Because of this drawbacks of ordinary brakes, system which will lead to reduce the wear of brake pad. This arises a simple and effective mechanism of braking system situation will also reduce the wear debris pollution into our ‘The eddy current brake’. Eddy current is one of the most environment. outstanding of electromagnetic induction phenomena. Even though it appear many technical problems because dissipative 1.1 Conventional Braking System nature it has some valuable contributions. It is a frictionless method for braking of vehicles including trains. As it is a Braking forms an important part of motion of any frictionless brake, periodic change of braking components are automobile or locomotive. -
EP / BP Compact Product Family
EP / BP Compact Product Family Foto Siemens AG“ APPLICATIONS High-Speed Trains | Locomotives | Metros | Regional and Commuter Trains 2 EP / BP COMPACT PRODUCT FAMILY IS A FLEXIBLE AND POWERFUL BRAKE CONTROL SYSTEM providing not only brake cylinder pressure control for central and decentralized systems but also for brake pipe pressure control. Its modular design of electronic and pneumatic modules makes it configurable for all types of high-speed trains, multiple units and metros. With its variety of modules, EP / BP CUSTOMER BENEFITS DIVERSIFICATION Compact can be used for a wide n Lightweight and compact EP Compact offers control of various range of different applications of all n Flexible system layout functions of the braking systems: car builders across different markets. n Maximum economy thanks to n Service brake (direct and indirect) Every electropneumatic module standardized modules n Emergency brake (direct and controls either brake pipe n Discrete, highly integrable indirect) applications, single bogies components n Magnetic track brake separately or several bogies with n Straightforward service and n Parking brake identical braking requirements. maintenance concept n Wheel slide control Different electronic modules allow n For central or decentralized control n Continuous load correction and the use of different communication n Multifunctional for numerous load limitation interfaces: wheel slide protection, system configurations pressure regulation and diagnosis n Innovative use of proven Electronic control functions: functions. Anti-skid valves as well as technology n Blending / brake management different auxiliary control functions n Integrated electronics for n Diagnostics and monitoring can be integrated into the module underfloor or separate electronics n Sanding and other auxiliary systems as an option. -
Modeling and Design Optimization of Electromechanical Brake Actuator Using Eddy Currents
Modeling and Design Optimization of Electromechanical Brake Actuator Using Eddy Currents by Kerem Karakoc MASc, University of Victoria, 2007 BSc, Bogazici University, 2005 A Dissertation Submitted in Partial Fulfillment of the Requirements for the Degree of DOCTOR OF PHILOSOPHY in the Department of Mechanical Engineering. Kerem Karakoc, 2012 University of Victoria All rights reserved. This dissertation may not be reproduced in whole or in part, by photocopy or other means, without the permission of the author. ii Modeling and Design Optimization of Electromechanical Brake Actuator Using Eddy Currents by Kerem Karakoc MASc, University of Victoria, 2007 BSc, Bogazici University, 2005 Supervisory Committee Dr. Afzal Suleman, Dept. of Mechanical Engineering, University of Victoria Co-Supervisor Dr. Edward Park, Dept. of Mechanical Engineering, University of Victoria Co-Supervisor Dr. Ned Djilali, Dept. of Mechanical Engineering, University of Victoria Departmental Member Dr. Issa Traore, Dept. of Electrical and Computer Engineering, University of Victoria Outside Member iii Supervisory Committee Dr. Afzal Suleman, Dept. of Mechanical Engineering, University of Victoria Co-Supervisor Dr. Edward Park, Dept. of Mechanical Engineering, University of Victoria Co-Supervisor Dr. Ned Djilali, Dept. of Mechanical Engineering, University of Victoria Departmental Member Dr. Issa Traore, Dept. of Electrical and Computer Engineering, University of Victoria Outside Member Abstract A novel electromechanical brake (EMB) based on the eddy current principle is proposed for application in electrical vehicles. The proposed solution is a feasible replacement for the current conventional hydraulic brake (CHB) systems. Unlike CHBs, eddy current brakes (ECBs) use eddy currents and their interaction with an externally applied magnetic field to generate braking torque. -
Real-World Exhaust Emissions of Diesel Locomotives and Motorized Railcars During Scheduled Passenger Train Runs on Czech Railroads
atmosphere Article Real-World Exhaust Emissions of Diesel Locomotives and Motorized Railcars during Scheduled Passenger Train Runs on Czech Railroads Michal Vojtisek-Lom 1,2,* , Jonáš Jirk ˚u 3 and Martin Pechout 4 1 Department of Automobile, Combustion Engine and Railway Engineering, Faculty of Mechanical Engineering, Czech Technical University of Prague, 160 00 Prague, Czech Republic 2 Department of Vehicles and Engines, Technical University of Liberec, 46117 Liberec, Czech Republic 3 Department of Vehicle Technology, Faculty of Transportation Sciences, Czech Technical University in Prague, 110 00 Prague, Czech Republic; [email protected] 4 Department of Vehicles and Ground Transport, Faculty of Engineering, Czech University of Life Sciences, 165 21 Prague, Czech Republic; [email protected] * Correspondence: [email protected] or [email protected]; Tel.: +420-774-262-854 Received: 17 April 2020; Accepted: 28 May 2020; Published: 2 June 2020 Abstract: The paper summarizes exhaust emissions measurements on two diesel-electric locomotives and one diesel-hydraulic railcar, each tested for several days during scheduled passenger service. While real driving emissions of buses decrease with fleet turnaround and have been assessed by many studies, there are virtually no realistic emissions data on diesel rail vehicles, many of which are decades old. The engines were fitted with low-power portable online monitoring instruments, including a portable Fourier Transform Infra Red (FTIR) spectrometer, online particle measurement, and in two cases with proportional particle sampling systems, all installed in engine compartments. Due to space constraints and overhead electric traction lines, exhaust flow was computed from engine operating data. Real-world operation was characterized by relatively fast power level transitions during accelerations and interleaved periods of high load and idle, and varied considerably among service type and routes. -
TRANSPORTATION NOTICE #2018-045 Effective 0001, Friday, December 14, 2018
THE BELT RAILWAY COMPANY OF CHICAGO TRANSPORTATION NOTICE #2018-045 Effective 0001, Friday, December 14, 2018 To: ALL CONCERNED Subject: Clearing Yard Transportation Work Instructions (Hump Notice) Transportation Notice 2018-034, effective August 21, 2018 is cancelled. The following changes are made to Clearing Yard Transportation Work Instructions (Hump) Addition: • CY 5.20 – Cars on Hump Needing Repairs (NEW) • CY 8.2.1 - Braking During Shove Over Movements (NEW) Transportation Notice 2018-045 Page 1 Clearing Yard Transportation Work Instructions (Hump) The instructions contained within this document are specifically intended for any Transportation Department employees working in Clearing Yard. These instructions provide specific instructions on the operation of the Clearing Yard. Where these instructions may differ from published rules, these instructions will govern operations as they relate to the operation of the Clearing Yard. Transportation Department Employees working in Train, Yard, and Engine Service; including Yardmasters (Humpmasters), Hump Conductors, and all crew members on BRC yard assignments, must have these instructions in their possession while on duty for reference while working in Clearing Yard. These instructions will be published quarterly, with additions made as needed using Transportation Notices, under the direction of the Superintendent-Transportation. CY 1 - Hump Operations: Hump Operations are under the direct control of the Trainmaster-Operations. Reporting to the Trainmaster- Operations are Yardmasters, Hump Conductors, Train Crews, and Transportation-Clerks. CY 2 - Hump Speeds: The Hump Conductor is responsible for regulating hump speeds and communicating this information to Hump Crews. Speed Settings: SPEED SETTING SPEED (MPH) HUMP SLOW 1.4 MPH HUMP 1.7 MPH HUMP FAST 2.2 MPH The default speed for hump operations is Hump. -
ABS 6 Standard Anti-Lock Braking System
Systems for Commercial Vehicles Product Manual ABS 6 Standard Anti-lock Braking System • Basic Principles of Operation of the System • Component Descriptions • Troubleshooting and Fault-Finding • Service Guidance to ensure Safe and Efficient Operation Training Nutzfahrzeug Bremssysteme Contents Contents 3 Disclaimer 4 Safety Checks 5 1. General Information 6 1.1 Service Intervals 6 1.2 Principles of Anti-lock Braking System (ABS) Operation 7 1.2.1 Introduction 7 1.2.2 Operation 9 1.3 General Advice when working with ABS 14 1.3.1 Dos and Don’ts for Drivers / Operators 14 1.3.2 Dos and Don’ts for ABS electrical components and cabling 15 1.3.3 Dos and Don’ts for ABS pneumatic components and pipework 17 1.4 Troubleshooting and Fault-finding 18 1.4.1 Normal Operation 18 1.4.2 Start-up Check 18 1.4.3 Fault Detection 18 1.4.4 Using Blink Codes 18 1.4.5 Configuration Blink Codes 19 1.4.6 Fault Blink Codes 21 1.4.7 Erasing Fault Codes from the ECU memory 26 1.4.8 PC Diagnostics 27 2. System Components 28 2.1 Electronic Control Unit (ECU) 28 2.2 ABS Warning Lamp 29 2.3 Sensing Ring 30 2.4 Wheel Speed Sensor 31 2.5 Sensor Extension Cable 34 2.6 Pressure Modulator Valves 35 2.7 VOSS plug connection system 230 (assembly instructions) 41 3. Wiring Diagrams 43 3 3 Disclaimer The information contained in this document is intended for the exclusive use of trained persons within the commercial vehicle industry, and must not be passed on to any third party. -
Environmental Product Portfolio 2 KNORR-BREMSE ENVIRONMENTAL PRODUCT PORTFOLIO
1 Environmental product portfolio 2 KNORR-BREMSE ENVIRONMENTAL PRODUCT PORTFOLIO Our contribution towards making mobility more environmentally friendly and energy-efficient In recent years, climate change and environmental Our product portfolio offers solutions that protection have taken on greater relevance for >> minimize energy consumption and enhance the commercial vehicle and rail vehicle sectors. In fuel efficiency, response, Knorr-Bremse has for many years been >> reduce atmospheric emissions, giving top priority to developing fuel-saving, >> minimize noise emissions, emission-reducing technologies with solutions >> protect the environment by using eco-friendly tailored to market needs. materials and manufacturing processes. ENERGY EFFICIENCY PROTECTING RESOURCES AND REDUCING EMISSIONS • CFCB bogie-mounted block brakes • Oil-free compressor with sound insulation • Compact brake calipers • Flexpad Silent brake pad • Lightweight HVAC units, doors, brake discs • LL composite brake block • iCOM Assist (LEADER) driver assistance system • Sanding systems with reduced sand use DIVISION • Driving and training simulators • iCOM Energy Metering • HVAC systems • IFE Generation 4 entrance system RAIL VEHICLE RAIL • Isobar brake pads • Aluminum brake discs • Pneumatic disc brakes • Electronic braking system (EBS) • Electronic air treatment • Engine retarder DIVISION • Aluminum compressor casing • Genuine remanufactured products • Compressor with clutch • Electric screw compressor • Compressor with energy-saving system • Mechatronic transmission -
Non-Propellant Eddy Current Brake and Traction in Space Using Magnetic Pulses
aerospace Article Non-Propellant Eddy Current Brake and Traction in Space Using Magnetic Pulses Yi Zhang †, Qiang Shen †, Liqiang Hou † and Shufan Wu * School of Aeronautics and Astronautics, Shanghai Jiao Tong University, No. 800, Dongchuan Road, Minhang District, Shanghai 200240, China; [email protected] (Y.Z.); [email protected] (Q.S.); [email protected] (L.H.) * Correspondence: [email protected]; Tel.: +86-34208597 † These authors contributed equally to this work. Abstract: The safety of on-orbit satellites is threatened by space debris with large residual angular velocity and the space debris removal is becoming more challenging than before. This paper explores the non-contact despinning and traction problem of high-speed rotating targets and proposes an eddy current brake and traction technology for space targets without any propellant consumption. The principle of the conventional eddy current brake is analyzed in this article and the concept of eddy current brake and traction without propellant is put forward for the first time. Secondly, according to the key technical requirements, a brand-new structure of a satellite generating artificial magnetic field is designed accordingly. Then the control mechanism of eddy current brake and traction without propellant is analyzed qualitatively by simplifying the model and conditions. Then, the magnetic pulse control method is proposed and analyzed quantitatively. Finally, the feasibility of the technology is verified by the numerical simulation method. According to the simulation results, the eddy current brake and traction technology based on magnetic pulses can make the angular speed of target decrease linearly without propellant during the process. -
Effective Eddy Current Braking at Low and High Vehicular Speeds – a Simulation Study
Archives of Current Research International 8(4): 1-11, 2017; Article no.ACRI.34042 ISSN: 2454-7077 Effective Eddy Current Braking at Low and High Vehicular Speeds – A Simulation Study Alumona Louis Olisaeloka 1* , Azaka Onyemazuwa Andrew 2 and Nwadike Emmauel Chinagorom 2 1Department of Electrical Engineering, Nnamdi Azikiwe University, Awka, Nigeria. 2Department of Mechanical Engineering, Nnamdi Azikiwe University, Awka, Nigeria. Author’s contributions This work was carried out in collaboration between all authors. Author ALO designed the study, performed the statistical analysis, wrote the protocol, and wrote the first draft of the manuscript. Authors AOA and NEC managed the analyses of the study. Author NEC managed the literature searches. All authors read and approved the final manuscript. Article Information DOI: 10.9734/ACRI/2017/34042 Editor(s): (1) Preecha Yupapin, Department of Physics, King Mongkut’s Institute of Technology Ladkrabang, Thailand. (2) M. A. Elbagermi, Chemistry Department, Misurata University, Libya. (3) Alexandre Gonçalves Pinheiro, Physics, Ceara State University, Brazil. Reviewers: (1) Meshack Hawi, Jomo Kenyatta University of Agriculture and Technology, Kenya. (2) Mohamed Zaher, University of Illinois at Chicago, USA. Complete Peer review History: http://www.sciencedomain.org/review-history/20351 Received 10 th May 2017 Accepted 16 th July 2017 Original Research Article th Published 4 August 2017 ABSTRACT Conventional eddy current braking is limited in effectiveness to only the high vehicular speed region. As the vehicle slows, the conventional eddy current brake loses effectiveness. This inherent drawback is due to the use of static/stationary magnetic field in the brake system. This study presents a solution - the use of rotating magnetic field in the brake system. -
Chapter 2. General Principle of Electromagnetic Brakes
Chapter 2. General Principle of Electromagnetic Brakes 2.1. Introduction Electromagnetic brakes have been used as supplementary retardation equipment in addition to the regular friction brakes on heavy vehicles. We outline the general principles of regular brakes and several alternative retardation techniques in this section. The working principle and characteristics of electromagnetic brakes are then highlighted. 2.2. General Principle of Brake System The principle of braking in road vehicles involves the conversion of kinetic energy into thermal energy (heat). When stepping on the brakes, the driver commands a stopping force several times as powerful as the force that puts the car in motion and dissipates the associated kinetic energy as heat. Brakes must be able to arrest the speed of a vehicle in a short periods of time regardless how fast the speed is. As a result, the brakes are required to have the ability to generating high torque and absorbing energy at extremely high rates for short periods of time. Brakes may be applied for a prolonged periods of time in some applications such as a heavy vehicle descending a long gradient at high speed. Brakes have to have the mechanism to keep the heat absorption capability for prolonged periods of time. 2.3. Conventional Friction Brake 4 The conventional friction brake system is composed of the following basic components: the “master cylinder” which is located under the hood is directly connected to the brake pedal, and converts the drivers’ foot pressure into hydraulic pressure. Steel “brake hoses” connect the master cylinder to the “slave cylinders” located at each wheel. -
“Road Vehicles — Endurance Braking Systems of Motor Vehicles and Towed Vehicles — Test Procedures”
Presentation to GRRF, 55th Session, Geneva Febr. 3rd, 2004 ISO CD 12161 Doc TC22/SC2 N 597 “Road vehicles — Endurance braking systems of motor vehicles and towed vehicles — Test procedures” by ISO TC22/SC2/WG6 SWG 6 „Endurance braking systems“ Dr. Reinhold Pittius (VOITH TURBO) Pittius 2004-02-03 page 1 ISO 22/2/6/SWG 6 / Retarders / Test procedures for type approval / WD 12161 1. Structure of ISO Working Group Subworking group SWG 6 „Endurance braking systems“ Chairman Dr. Reinhold Pittius • reporting to ISO 22/2/WG6 „Braking Systems“ Chairman Prof. v. Glasner • Active members of SWG 6: DaimlerChrysler TELMA IVECO VOITH TURBO MAN ZF • Status - Working Draft agreed by TC22 Æ Committee Draft (CD) - Distribution as ISO DIS in Dec. 2003 - Balloting until May 2004 Pittius 2004-02-03 page 2 ISO 22/2/6/SWG 6 / Retarders / Test procedures for type approval / WD 12161 Contents 1. Structure of ISO Working Group 2. The Target 3. Basic legal requirements 4. Basic understanding of equivalent energy 5. Specific properties of different types of retarders 6. Test methods 7. Conclusion Pittius 2004-02-03 page 3 ISO 22/2/6/SWG 6 / Retarders / Test procedures for type approval / WD 12161 2. The Target Standardization • of testing procedures • of vehicles - equipped with endurance braking systems - to be type approved • according to existing legal requirements ¾ Detailed description of ¾ different test methods such that ¾ results are • objectiv, • realistic and • compatible Pittius 2004-02-03 page 4 ISO 22/2/6/SWG 6 / Retarders / Test procedures for type approval / WD 12161 3. Basic legal requirements (1) ECE-R 13, Annexe 4 para. -
Conceptualization of a New Product Development Framework for Eddy Current Braking Systems for Heavy Vehicles in Zimbabwe
Proceedings of the 2017 International Conference on Industrial Engineering and Operations Management (IEOM) Bristol, UK, July 24-25, 2017 Conceptualization of a New Product Development Framework for Eddy Current Braking Systems for Heavy Vehicles in Zimbabwe Wilson R. Nyemba Department of Mechanical Engineering Science, Faculty of Engineering and the Built Environment, University of Johannesburg, Auckland Park 2006, Johannesburg, South Africa [email protected] Chris Pote, Tauyanashe Chikuku Department of Mechanical Engineering, University of Zimbabwe, P O Box MP 167, Mount Pleasant, Harare, Zimbabwe [email protected], [email protected] Charles Mbohwa Professor of Sustainability Engineering, Department of Quality and Operations Management & Vice Dean for Research and Innovation, Faculty of Engineering and the Built Environment, University of Johannesburg, Auckland Park 2006, Johannesburg, South Africa [email protected] Abstract One of the most critical requirements for safety in vehicles is the availability of reliable braking systems. Most heavy vehicles in Zimbabwe employ the conventional hydraulic braking system. However changes and improvements in technology have seen the introduction of retarders that make use of magnets and eddy currents. The new technology is friction free but still deemed expensive and thus not yet readily acceptable to vehicle manufacturers for fears of reliability and cost. Hydraulic brakes are equally expensive in the long run owing to maintenance and frequent replacement of brake pads and rotors, particularly in Zimbabwe where the road infrastructure has deteriorated significantly over the years. A case study was carried out at a Zimbabwean company which specializes in the sales, service and backup of Scania heavy vehicles, with a special focus on the braking systems.