Plasma Arc and Cold Crucible Furnace Vitrification for Medium Level Waste: a Review S
Total Page:16
File Type:pdf, Size:1020Kb
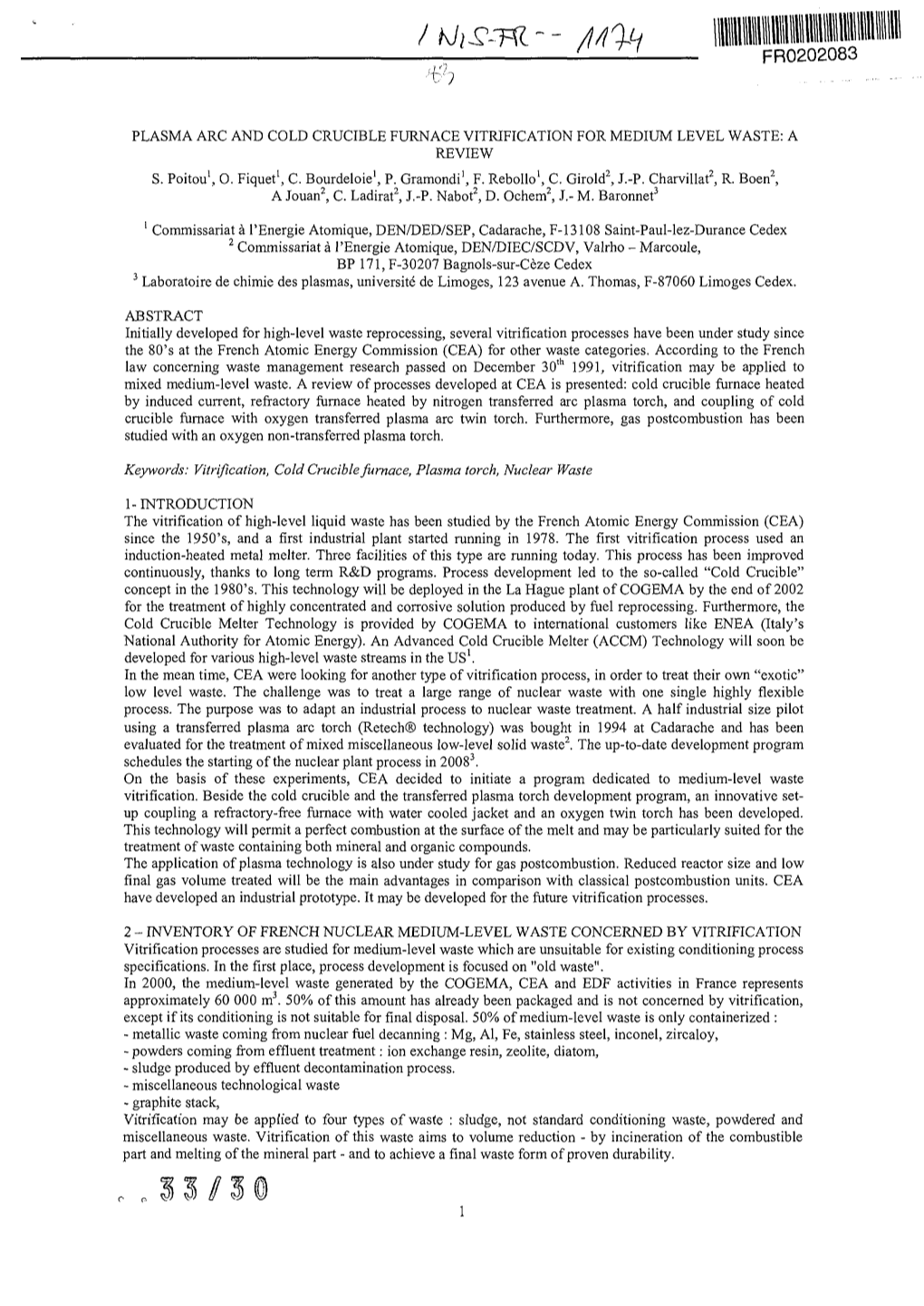
Load more
Recommended publications
-
Grasp Success by the Roots
Grasp success by the roots Forming and root protection ensure perfect weld seams and roots Profit from forming For more than 40 years, root protection and forming have proven their value in welding technology. They permit an increase in weld Laminar and turbulent flow seam quality and contribute to a reduction of follow-up costs. The focus here is on reworking, pickling costs, the associated transport costs and Laminar flow instead of turbulence the not inconsiderable loss of time. With correct In order to ensure the high quality and economy forming, weld seams and roots can be produced of the work, a few basic rules must be observed. which need no reworking. One of the most important concerns the feed of the shield gas to the weld seam region. This Forming and root protection should never be uncontrolled. In an optimum Root protection is the bathing of the weld root shield gas feed, the flow is laminar. If the flow is and the heat affected zone with shield gases, turbulent, the eddies result in mixing of the while simultaneously displacing atmospheric forming gas and the atmosphere. A laminar flow oxygen (DVS Data Sheet 0937). When applied to is generated with the help of a diffusor, usually pipes and tanks, it is known as forming. This comprising pipes, sheets or mouldings of sinter technique is used for the welding of gas sensitive material. The sinter metal distributes the gas materials such as high alloyed CrNi steels, for feed over a large area, from which the forming example, to ensure the corrosion resistance of gas is emitted in laminar form. -
Shielding Gas. Gases for All Types of Stainless Steel
→ Stainless Steel - New Zealand edition Shielding gas. Gases for all types of stainless steel. Argon 03 Stainless steel is usually defined as an iron-chromium alloy, containing at least 11% chromium. Often containing other elements such as silicon, manganese, nickel, molybdenum, titanium and niobium, it is most widely used as corrosion resistant engineering material in applications where aggressive environments or elevated temperatures are prevalent. Stainless steel is traditionally categorised into four main groups and each group is further sub-divided into specific alloys. The main groups are: austenitic, ferritic, martensitic and duplex. → Austenitic stainless steels are the most widely used, accounting for around 70% of all stainless steels fabricated. They are used in applications such as chemical processing, pharmaceutical manufacturing, food processing and brewing, and liquid gas storage. The weldability of these grades is usually very good. → Ferritic stainless steels are not as corrosion resistant or as weldable as austenitic stainless steels. They have high strength and good high temperature properties and are used for products such as exhausts, catalytic converters, air ducting systems, and storage hoppers. → Martensitic stainless steels are high strength but are more difficult to weld than other types of stainless steels. They are used for products such as vehicle chassis, railway wagons, mineral handling equipment and paper and pulping equipment. → Duplex stainless steels combine the high strength of ferritic steels and the resistance of austenitic steels. They are used in corrosive environments such as offshore and petrochemical plants, where the integrity of the welded material is critical. ARGOSHIELD®, ALUSHIELD® STAINSHIELD® and SPECSHIELD® are registered trademarks of BOC a Member of The Linde Group. -
EFFICIENT GAS HEATING of INDUSTRIAL FURNACES EFFICIENT GAS HEATING of INDUSTRIAL FURNACES COMPANY PROFILE: Gasbarre Furnace Group JANUARY/FEBRUARY 2017
THERMAL PROCESSI NG MAGAZINE MAGAZINE NG EFFICIENT GAS HEATING OF INDUSTRIAL FURNACES FURNACES INDUSTRIAL OF GAS HEATING EFFICIENT EFFICIENT GAS HEATING OF INDUSTRIAL FURNACES COMPANY PROFILE: Gasbarre Furnace Group JANUARY/FEBRUARY 2017 JANUARY/FEBRUARY JANUARY/FEBRUARY 2017 Technologies and Processes for the Advancement of Materials thermalprocessing.com TP-2017-01-02.indb 1 12/23/16 10:43 AM Regardless of the industry you are in or the Regardless of the industry you are in or the Regardless of the industry you are in or the processes you run, The Ipsen, Harold blog is processes you run, The Ipsen, Harold blog is processes you run, The Ipsen, Harold blog is devoted to providing expert-curated best devoted to providing expert-curated best devoted to providing expert-curated best practices, maintenance tips and details about practices, maintenance tips and details about practices, maintenance tips and details about the latest industry news and innovations. the latest industry news and innovations. the latest industry news and innovations. Want to know what everyone else is reading? Want to know what everyone else isWant reading? to know what everyone else is reading? Here are our top blog posts of 2016 ... Here are our top blog posts of 2016 ... Here are our top blog posts of 2016 ... 5 Quick Tips on How to Become a Brazing Superhero 5 Quick Tips on How to Become a Brazing Superhero 5 Quick Tips on How to Become a Brazing Superhero When it comes to vacuum aluminum brazing there are a lot of advantages, but you also need to know When it comes to vacuum aluminum brazing there are a lot of advantages,When but you also need to know it comes to vacuum aluminum brazing there are a lot of advantages, but you also need to know the details on how to properly braze your parts. -
Measuring the Dewpoint of Hydrogen Forming Gas with a Zirconia Oxygen Sensor
Measuring the Dewpoint of Hydrogen Forming Gas with a Zirconia Oxygen Sensor By Dr M A Swetnam 1 Abstract This paper describes the uses of hydrogen forming gas in reducing and oxidising industrial applications and explains why controlling the water content is so important in the metal heat treatment industry. Measuring water at elevated temperatures is extremely difficult to do with normal equipment. Cambridge Sensotec has developed a high temperature forming gas analyser capable of measuring the hydrogen dewpoint using a series of thermodynamic calculations, based on the signals from a modified Rapidox zirconia oxygen sensor. 2 Background Forming gas is used in many heat treatment applications as a cheap way to remove oxygen and control water in an oven or heat treatment process. Forming gas is a mixture of hydrogen (H2) and an inert gas which is nearly always nitrogen (N2). It can be made chemically by cracking ammonia: 2 3 + 1 3 → 2 2 which produces a ratio of 3:1 hydrogen to nitrogen. This method is not generally used because it is chemically inefficient and costly. More commonly the hydrogen and nitrogen are either mixed together on site or purchased as a pre-mixed cylinder from the gas company. Any mix of hydrogen and nitrogen can refer to forming gas, but the most common blend is 5% H2 in 95% N2. This mix is always below the lower explosive limit (LEL) Forming Gas White Paper v1.0 1 of hydrogen and is therefore considered a safe gas which does not require any special equipment or handling. 3 Forming Gas Applications Forming gas is used in specialist soldering applications as well as some photographic applications to clean long exposed film (e.g. -
Mathematical Modeling of Discharge Plasma Generation and Diffusion Saturation of Metals and Alloys
Information Technologies in Science, Management, Social Sphere and Medicine (ITSMSSM 2016) Mathematical Modeling of Discharge Plasma Generation and Diffusion Saturation of Metals and Alloys Nguyen Bao Hung1, T. V. Koval2, Tran My Kim An3 1,2,3 National Research Tomsk Polytechnic University Tomsk, Russia E-mail: [email protected], [email protected], [email protected] Abstract. This paper presents a mathematical modeling of the for which it is required to provide an ion current density of plasma generation in a hollow cathode and the diffusion ~1 mA/cm2 to a treated surface and a discharge operating saturation of metals and alloys by nitrogen atoms in the plasma voltage of hundred volts [8–11]. of a low-pressure non-self-sustained glow discharge. Characteristics of gas discharge are obtained. The relations The complexity and multiple relations of nitriding process between main technological parameters and structural-phase make difficult to define the general laws in the structuration of states of nitrited material are defined. Furthermore, this paper modified layers and their properties [12-16]. Such problems leads a comparison of calculated results with the experimental can be solved by mathematical modeling of the processes in data. plasma generation and material nitriding. This is also an effective way to establish the mechanisms of forming the Keywords: hollow cathode, glow discharge, low-pressure modified layer with specified properties and their dependences discharge, plasma, plasma cathode, plasma nitriding, diffusion on -
Confirming the Dew Point of Forming Gas Using Intrinsically Safe
Application Note Confirming the Dew Point of Forming Gas using Intrinsically Safe Impedance Dew Point Transmitters Application Background Hydrogen gas is widely used for the bright hardening of many kinds of metals. There are two main delivery methods for this process - bulk hydrogen from storage cylinders and cracked ammonia. Both delivery methods have advantages and disadvantages - cost and fire hazard in the case of pure hydrogen and corrosion risk and human safety being the main considerations in the case of cracked ammonia. However, nowadays cracked ammonia plants are the more common method of providing a reducing/hardening atmosphere for metallurgical furnaces. What is the process in an ammonia cracker? Pressurised liquid ammonia is heated in order to vaporise it and is then passed over a nickel catalyst at a temperature of around 1000°C, which causes it to dissociate into its component parts - hydrogen and nitrogen. The chemical equation for this reaction is: 2NH3 N2 +3H2 The diagram below illustrates the cracking process: As a result of complete dissociation into hydrogen and nitrogen, very little undissociated ammonia remains and the dew-point temperature of the resulting gas should be very low (well below -30°C). This gas can also be dried further by use of a heated-regeneration twin column desiccant dryer, the molecular sieve will also adsorb traces of uncracked ammonia still present in the gas, the gas exits the system dryer than -65°Cdp, consisting of 75 Vol% hydrogen and 25 Vol% nitrogen. Applications for dissociated ammonia The forming gas is used in conveyer furnaces and in tube furnaces for annealing processes in a reducing atmosphere, such as brazing, sintering, de-oxidation, and nitrization. -
Efficiency Improvement of Reducing Agents in the Blast Furnace to Reduce Co2 Emissions and Costs*
ISSN 2176-3135 EFFICIENCY IMPROVEMENT OF REDUCING AGENTS IN THE BLAST FURNACE TO REDUCE CO2 EMISSIONS AND COSTS* Robin Schott 1 Franz Reufer 2 Abstract The blast furnace process is the most important process to produce pig iron. The necessary process energy is mainly covered by coke. But the production of coke is connected with CO2-emissions and high costs. A significant measure to reduce the coke rate and with it the CO2-emissions plus costs is pulverized coal injection (PCI) through the tuyeres into the blast furnace. A further increase to substitute coke by coal can be achieved by using the Oxycoal+ technology. This article compares and shows the cost effectiveness and the decrease of CO2-emissions with the help of simplified energy balances for the only coke operation of the blast furnace, the operation using pulverized coal injection and the operation using the Oxycoal+ technology. Keywords: Blast furnace; Substitute fuel; Pulverized coal injection (PCI); Reduction in costs. 1 Dr.-Ing., Vice President Iron Making Technology; Küttner GmbH & Co. KG, Essen, Deutschland. 2 Dr.-Ing., Managing Director Sales; Küttner GmbH & Co. KG, Essen, Deutschland. * Technical contribution to the 46º Seminário de Redução de Minério de Ferro e Matérias-primas, to 17º Simpósio Brasileiro de Minério de Ferro and to 4º Simpósio Brasileiro de Aglomeração de Minério th th de Ferro, part of the ABM Week, September 26 -30 , 2016, Rio de Janeiro, RJ, Brazil. 379 ISSN 2176-3135 1 INTRODUCTION The worldwide energy requirement for the year 2010 was approx. 12 billion tons oil equivalent [1]. This corresponds to approx. -
Chapter 5 Plasma Nitridation
Chapter 5 Plasma Nitridation This chapter deals with the nitridation of GaAs and porous GaAs for the formation of GaN using N2+H2 gas mixture as the plasma forming gas. High Speed M2 steel has also been nitrided to form Iron Nitride Chapter 5:Plasma Nitr. 108 Index Introduction 109 5A Section A: Gallium Nitride (GaN) 109 5A.1. Background Literature 109 5A. 1.1 Importance of GaN 109 5A. 1.2 Surface chemistry 110 5A.1.3 Electrical properties 110 5A. 1.4 The applications of GaN 111 5A. 1.5 Different techniques of synthesizing GaN 112 i) Chemical process 112 ii) Physical process 112 iii) Nitridation of porous GaAs 112 5A.2 Present experimental techniques of synthesis 114 5A.2.1 Nitridation of GaAs 114 5A.2.2 Nitridation of Porous GaAs 114 5A.3 Results and discussions 115 5A.3.1 Nitridation of GaAs 116 5A.3.2 Nitridation of porous GaAs 119 5A.4 Conclusions 122 5B: Section B: Iron Nitride 122 5B.1 Background 122 5B. 1.1 Surface Hardening 122 5B. 1.2 Nitridation 123 5B.2 Experimental details 125 5B.3 Results and discussions 126 5B.4 Conclusions 132 References Chapter 5:PIasma Nitr. 109 CHAPTER 5 Plasma Nitridation Introduction Present chapter deals with the process of nitridation and presents some of results obtained by plasma nitridation over two important classical materials, namely GaAs and Steel. The main intention of the work is to demonstrate the potential of ECR plasma in reducing the time of nitridation usually required in the conventional chemical methods. -
The Use of Nitriding to Enhance Wear Resistance of Cast Irons and 4140 Steel
University of Windsor Scholarship at UWindsor Electronic Theses and Dissertations Theses, Dissertations, and Major Papers 2013 The Use of Nitriding to Enhance Wear Resistance of Cast Irons and 4140 Steel Zaidao Yang University of Windsor Follow this and additional works at: https://scholar.uwindsor.ca/etd Recommended Citation Yang, Zaidao, "The Use of Nitriding to Enhance Wear Resistance of Cast Irons and 4140 Steel" (2013). Electronic Theses and Dissertations. 4714. https://scholar.uwindsor.ca/etd/4714 This online database contains the full-text of PhD dissertations and Masters’ theses of University of Windsor students from 1954 forward. These documents are made available for personal study and research purposes only, in accordance with the Canadian Copyright Act and the Creative Commons license—CC BY-NC-ND (Attribution, Non-Commercial, No Derivative Works). Under this license, works must always be attributed to the copyright holder (original author), cannot be used for any commercial purposes, and may not be altered. Any other use would require the permission of the copyright holder. Students may inquire about withdrawing their dissertation and/or thesis from this database. For additional inquiries, please contact the repository administrator via email ([email protected]) or by telephone at 519-253-3000ext. 3208. The Use of Nitriding to Enhance Wear Resistance of Cast Irons and 4140 Steel by Zaidao Yang A Thesis Submitted to the Faculty of Graduate Studies through Engineering Materials in Partial Fulfillment of the Requirements -
An Investigation of Stainless Steels for Long-Term Use in Liquid Sodium At
DEGREE PROJECT IN MATERIALS SCIENCE AND ENGINEERING, SECOND CYCLE, 30 CREDITS STOCKHOLM, SWEDEN 2019 What If We Tilt the AOD? Developing a numerical and physical model of a downscaled AOD converter to investigate flow behaviour when applying an inclination. SERG CHANOUIAN KTH ROYAL INSTITUTE OF TECHNOLOGY SCHOOL OF INDUSTRIAL ENGINEERING AND MANAGEMENT Abstract In a scrap based stainless steel plant the dominant process for carbon reduction is the Argon oxygen decarburisation process (AOD). The process goes through three steps: decarburisation, reduction and desulphurisation where the main challenge is to oxidise carbon to CO without oxidising the expensive chromium. The general practical approach is to inject a mixture of oxygen and an inert gas, like argon or nitrogen, through tuyeres at the converter side starting with a high amount of oxygen gas which followingly is reduced as the inert gas is increased during the decarburisation steps. This allows for a decrease in partial pressure for the CO bubbles which is thermodynamically favourable for carbon oxidation. Recent studies have shown that an aged AOD converter with a worn lining can decarburise the melt faster than a fresh vessel due to favourable thermodynamic conditions occurring since the bath height is lower in the aged converter. The studies show 8-10% savings of oxygen gas which have led to an interest to study the matter. One of two approaches are taken in the present work with the focus to develop a numerical model that simulates a downscaled AOD converter with applied inclinations that is to be validated through physical modelling. A 75-ton industrial converter was downscaled for water-air experiments where three inclination angles namely 0, 5.5 and 14° were studied with focus on mixing time and penetration length. -
Perfectly Joined Gases for Life
No. 10 Issue 03 | August 2013 Gases for Life The industrial gases magazine Service and know-how for welding and cutting: Perfectly joined Gas supply: Paper production: PVC recycling: MegaPack The footprint is Floor powder innovation getting smaller Editorial View of the “Big Air Package”, inside the Oberhausen Gasometer. Dear Readers, Did you take the car for a spin or go for a bike ride at the weekend, or did you simply relax in a sun lounger? If you did any of these things, you will have come into contact with steel or aluminium structures, the compo- nents of which are cut to size and joined with the aid of welding and cutting gases. Welding and cutting – at first, that sounds like a traditional trade. But there is much more to it than that. It requires extensive experience as well as the optimal gas and the right process for the particular application in question. Messer is happy to pass this knowledge on to its customers, including in the form of welder train- ing. We also supply the appropriate gases – from standard through to customised special mixtures. You can find out more about this in our cover story. One example of an unusual metal structure is the Gasometer in Oberhausen, where the “Big Air Package”, a fascinating installation by artist Christo, can presently be experienced. Messer is sponsoring this event and we are offering a special prize for the winner of our competition (page 19): a copy of the exhibition catalogue signed by Christo. So it is certainly worth leafing through this issue of “Gases for Life”. -
Corrosion of Materials in Liquid Magnesium Alloys and Its Prevention
Chapter 5 Corrosion of Materials in Liquid Magnesium Alloys and Its Prevention Frank Czerwinski Additional information is available at the end of the chapter http://dx.doi.org/10.5772/59181 1. Introduction Magnesium alloys with their unique physical and chemical properties are important candi‐ dates for many modern engineering applications. Their density, being the lowest of all structural metals, makes them the primary choice in global attempts aimed at reducing the weight of transportation vehicles. However, magnesium also creates challenges at certain stages of raw alloy melting, fabrication of net-shape components and their service. The first one is caused byvery high affinity of magnesium to oxygen, which requires protective atmospheres increasing manufacturing cost and heavily contributing to greenhouse gas emissions [1] [2] [3]. While magnesium exhibits high affinity to oxygen, at temperatures corresponding to semisolid or liquid states it is also highly corrosive towards materials it contacts [4] [5] [6]. This imposes challenges to the selection of materials used to contain, transfer or process molten magnesium during manufacturing operations. Understanding the reactivity of liquid magnesium with engineering materials to eliminate or at least reduce the progress of corrosion is paramount not only during fabrication processes but also in other unique applications. They include joining of dissimilar materials where magnesium is one part of the joint couple and involves similar liquid/solid interface phenom‐ ena [7] [8]. Another example is the liquid battery cell, having two liquid metal electrodes, e.g. magnesium and antimony, separated by a molten salt electrolyte, that self-segregate into three layers based upon density and immiscibility.