MCE 323: Manufacturing Processes II Manufacturing Technology and Welding Processes
Total Page:16
File Type:pdf, Size:1020Kb
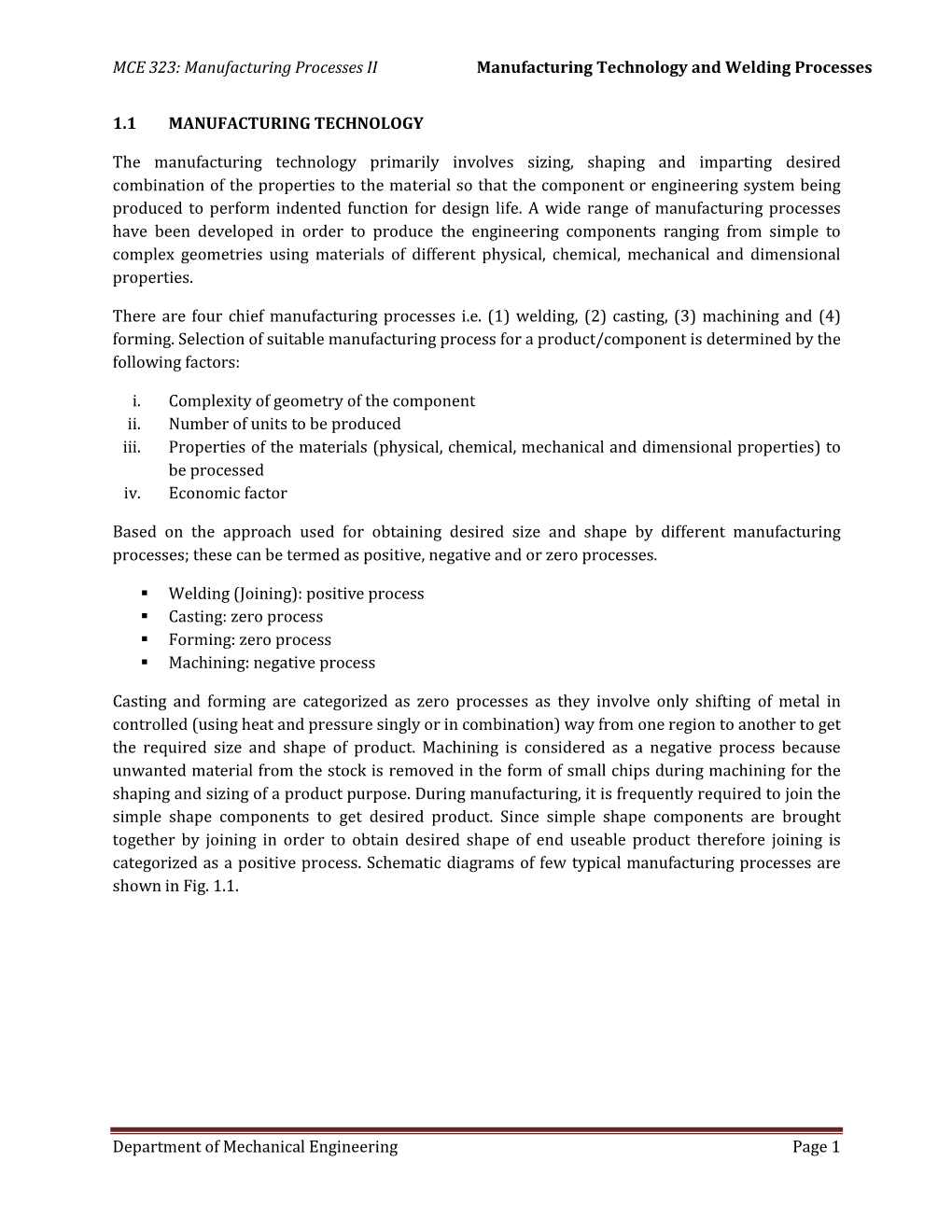
Load more
Recommended publications
-
Welding and Joining Guidelines
Welding and Joining Guidelines The HASTELLOY® and HAYNES® alloys are known for their good weldability, which is defined as the ability of a material to be welded and to perform satisfactorily in the imposed service environment. The service performance of the welded component should be given the utmost importance when determining a suitable weld process or procedure. If proper welding techniques and procedures are followed, high-quality welds can be produced with conventional arc welding processes. However, please be aware of the proper techniques for welding these types of alloys and the differences compared to the more common carbon and stainless steels. The following information should provide a basis for properly welding the HASTELLOY® and HAYNES® alloys. For further information, please consult the references listed throughout each section. It is also important to review any alloy- specific welding considerations prior to determining a suitable welding procedure. The most common welding processes used to weld the HASTELLOY® and HAYNES® alloys are the gas tungsten arc welding (GTAW / “TIG”), gas metal arc welding (GMAW / “MIG”), and shielded metal arc welding (SMAW / “Stick”) processes. In addition to these common arc welding processes, other welding processes such plasma arc welding (PAW), resistance spot welding (RSW), laser beam welding (LBW), and electron beam welding (EBW) are used. Submerged arc welding (SAW) is generally discouraged as this process is characterized by high heat input to the base metal, which promotes distortion, hot cracking, and precipitation of secondary phases that can be detrimental to material properties and performance. The introduction of flux elements to the weld also makes it difficult to achieve a proper chemical composition in the weld deposit. -
Laser Beams a Novel Tool for Welding: a Review
IOSR Journal of Applied Physics (IOSR-JAP) e-ISSN: 2278-4861.Volume 8, Issue 6 Ver. III (Nov. - Dec. 2016), PP 08-26 www.iosrjournals.org Laser Beams A Novel Tool for Welding: A Review A Jayanthia,B, Kvenkataramananc, Ksuresh Kumard Aresearch Scholar, SCSVMV University, Kanchipuram, India Bdepartment Of Physics, Jeppiaar Institute Of Technology, Chennai, India Cdepartment Of Physics, SCSVMV University, Kanchipuram, India Ddepartment Of Physics, P.T. Lee CNCET, Kanchipuram, India Abstract: Welding is an important joining process of industrial fabrication and manufacturing. This review article briefs the materials processing and welding by laser beam with its special characteristics nature. Laser augmented welding process offers main atvantages such as autogenous welding, welding of high thickness, dissimilar welding, hybrid laser welding, optical fibre delivery, remote laser welding, eco-friendly, variety of sources and their wide range of applications are highlighted. Significance of Nd: YAG laser welding and pulsed wave over continuous wave pattern on laser material processesare discussed. Influence of operating parameter of the laser beam for the welding process are briefed including optical fibre delivery and shielding gas during laser welding. Some insight gained in the study of optimization techniques of laser welding parameters to achieve good weld bead geometry and mechanical properties. Significance of laser welding on stainless steels and other materials such as Aluminium, Titanium, Magnesium, copper, etc…are discussed. I. INTRODUCTION Welding is the principal industrial process used for joining metals. As materials continue to be highly engineered in terms of metallic and metallurgical continuity, structural integrity and microstructure, hence, welding processes will become more important and more prominent. -
Metal Casting and Welding (17ME45A)
[METAL CASTING AND WELDING – 17M45-A] Metal Casting and Welding (17ME45A) Prepared by: Prof. Sachin S Pande Dept of Mechanical Engineering, SECAB I E T-586109 Page 1 [METAL CASTING AND WELDING – 17M35-A] METAL CASTING AND WELDING [AS PER CHOICE ASED CREDIT SYSTEM (CBCS) SCHEME] SEMESTER – III Subject Code 17 ME 35 A IA Marks 20 Number of Lecture Hrs / Week 04 Exam Marks 80 Total Number of Lecture Hrs 50 Exam Hours 03 CREDITS – 04 COURSE OBJECTIVE 1) To provide detailed information about the moulding processes. 2) To provide knowledge of various casting process in manufacturing. 3) To impart knowledge of various joining process used in manufacturing. 4) To provide adequate knowledge of quality test methods conducted on welded and casted components. MODULE -1 INTRODUCTION & BASIC MATERIALS USED IN FOUNDRY Introduction: Definition, Classification of manufacturing processes. Metals cast in the foundry-classification, factors that determine the selection of a casting alloy. Introduction to casting process & steps involved. Patterns: Definition, classification, materials used for pattern, various pattern allowances and their importance. Sand molding: Types of base sand, requirement of base sand. Binder, Additives definition, need and types Preparation of sand molds: Molding machines- Jolt type, squeeze type and Sand slinger. Study of important molding process: Green sand, core sand, dry sand, sweep mold, CO2 mold, shell mold, investment mold, plaster mold, cement bonded mold.Cores: Definition, need, types. Method of making cores, concept of gating (top, bottom, parting line, horn gate) and risering (open, blind) Functions and types. 10 hours MODULE -2 MELTING & METAL MOLD CASTING METHODS Melting furnaces: Classification of furnaces, Gas fired pit furnace, Resistance furnace, Coreless induction furnace, electric arc furnace, constructional features & working principle of cupola furnace. -
Ch7 Welding Processes.Pdf
ME 410: Casting and Welding Engineering Welding processes Faculty of Engineering Mechanical Dept. Importance of joining Wide use in manufacture Occurs late in manufacturing process Large number of practitioners Cost is high proportion of manufactured item Risk and cost of defective welds is high Science is complex Overview of joining methods Mechanical methods Screwed fasteners, rivets, crimp or snap locks Adhesive bonding Brazing and Soldering Base metal does not fuse. Molten filler drawn into close-fit joints by capillary action (surface tension forces). Brazing filler melts >450˚C, solder <450˚C Welding Weld A joint produced by heat or pressure or both so there is continuity of material. Filler (if used) has a melting temperature similar to the base material Welding processes Fusion welding Welding in the liquid state with no pressure Union is by molten metal bridging Solid phase welding Carried out below the melting point without filler additions Pressure often used Allied processes Thermal cutting Oxyfuel gas, plasma, laser cutting Gouging Air-arc, plasma, oxyfuel gas Surfacing Powder and arc spray coating Clad welding, hardfacing Solid phase welding Hot processes Forge welding Friction welding Diffusion bonding Cold processes Ultrasonic welding Explosive welding Fusion welding Intense energy source melts base metal locally Energy density 0.001 W/cm2 to 1 MW/cm2 Energy source may be stationary or move at a constant speed Filler metal From electrode Independently added filler No filler (autogenous -
Effects of Pulsed Nd:YAG Laser Welding Parameters on Penetration and Microstructure Characterization of a DP1000 Steel Butt Joint
metals Article Effects of Pulsed Nd:YAG Laser Welding Parameters on Penetration and Microstructure Characterization of a DP1000 Steel Butt Joint Xin Xue 1,2, António B. Pereira 2 ID , José Amorim 2 and Juan Liao 1,* 1 School of Mechanical Engineering and Automation, Fuzhou University, Fuzhou 350116, China; [email protected] or [email protected] 2 Centre for Mechanical Technology and Automation, Department of Mechanical Engineering, University of Aveiro, 3810-193 Aveiro, Portugal; [email protected] (A.B.P.); [email protected] (J.A.) * Correspondence: [email protected] or [email protected]; Tel.: +86-0591-2286-6793 Received: 13 June 2017; Accepted: 27 July 2017; Published: 1 August 2017 Abstract: Of particular importance and interest are the effects of pulsed Nd:YAG laser beam welding parameters on penetration and microstructure characterization of DP1000 butt joint, which is widely used in the automotive industry nowadays. Some key experimental technologies including pre-welding sample preparation and optimization design of sample fixture for a sufficient shielding gas flow are performed to ensure consistent and stable testing. The weld quality can be influenced by several process factors, such as laser beam power, pulse duration, overlap, spot diameter, pulse type, and welding velocity. The results indicate that these key process parameters have a significant effect on the weld penetration. Meanwhile, the fusion zone of butt joints exhibits obviously greater hardness than the base metal and heat affected zone of butt joints. Additionally, the volume fraction of martensite of dual-phase steel plays a considerable effect on the hardness and the change of microstructure characterization of the weld joint. -
Award No. 1529 Docket No. 1387 2-MP-CM-'52
Award No. 1529 Docket No. 1387 2-MP-CM-‘52 NATIONAL RAILROAD ADJUSTMENT BOARD SECOND DIVISION The Second Division consisted of the regular members and in addition Referee Jay S. Parker when award was rendered. PARTIES TO DISPUTE: SYSTEM FEDERATION NO. 2, RAILWAY EMPLOYES’ DEPARTMENT, A. F. of L. (Carmen) MISSOURI PACIFIC RAILROAD COMPANY DISPUTE: CLAIM OF EMPLOYES: (a) That carrier is violating the controlling agreement at North Little Rock Shops, particularly Rules 29 and 136 (a) by refusing to pay the welders’ rate of pay to Car-man Welder R. A. Parkhill when assigned to operating spot welding machine. (b) In consideration of the foregoing, Carman Welder R. A. Parkhill is entitled to be additionally compensated in the amount of 5c per hour from March 21, 1949 to August 31, 1949, both dates inclusive, and 6c per hour from September 1, 1949, to date, for all time engaged in operating spot welding machine. EMPLOYES’ STATEMENT OF FACTS: At North Little Rock, carrier maintains a universal or multirange spot welder in coach shop. This machine is presently operated by Carman R. A. Parkhill, hereinafter referred to as the claimant, and is capable of welding all types and gauges of metal from 28% to 1/2 inch, inclusive. When machine was first installed, a factory representative was on hand to teach claimant how to operate machine, which was a slow process at first because in addition to learning the actual operation, he had to acquire a thorough knowledge of the various metals and their reaction to the spot welding process in order to set the electronic controls for maximum weld- ing efficiency. -
Joining of Copper and Copper Alloys Lou Brown
Copper Development Association Cost-Effective Manufacturing: Joining of Copper and Copper Alloys Lou Brown CDA Publication No 98, 1994 Cost-Effective Manufacturing: Joining of Copper and Copper Alloys CDA Publication No 98 September 1994 Members as at 1st January 1994 ASARCO Inc Boliden MKM Ltd Thomas Bolton Ltd Brandeis Ltd The British Non-Ferrous Metals Federation Chile Copper Ltd Falconbridge Ltd Gecamines Commerciale IMI plc Inco Europe Ltd Noranda Sales Corporation of Canada Ltd Palabora Mining Co Ltd RTZ Limited Southern Peru Copper Corporation Acknowledgements The author is grateful to members of the Welding Institute (TWI), Loctite (UK) Limited, the British Non- Ferrous Metals Federation and the Association of Bronze and Brass Founders for helpful comment during the compilation of this handbook. The preparation of this publication has been financed by International Copper Association. Copper Development Association Copper Development Association is a non-trading organisation sponsored by the copper producers and fabricators to encourage the use of copper and copper alloys and to promote their correct and efficient application. Its services, which include the provision of technical advice and information, are available to those interested in the utilisation of copper in all its aspects. The Association also provides a link between research and user industries and maintains close contact with other copper development associations throughout the world. Website: www.cda.org.uk Email: [email protected] Copyright: All information -
Novel Ways of Using Nd:YAG Laser for Welding Thick Section Austenitic 522 Mangs, Johan
ESPOO 2004 VTT PUBLICATIONS 522 VTT PUBLICATIONS 522 VTT PUBLICATIONS 502 Bäckström, Mika. Multiaxial fatigue life assessment of welds based on nominal and hot spot stresses. 2003. 97 p. + app. 9 p. 503 Hostikka, Simo, Keski-Rahkonen, Olavi & Korhonen, Timo. Probabilistic Fire Simulator. Theory and User's Manual for Version 1.2. 2003. 72 p. + app. 1 p. 504 Torkkeli, Altti. Droplet microfluidics on a planar surface. 2003. 194 p. + app. 19 p. 505 Valkonen, Mari. Functional studies of the secretory pathway of filamentous fungi. The Tommi Jokinen effect of unfolded protein response on protein production. 2003. 114 p. + app. 68 p. 506 Mobile television – technology and user experiences. Report on the Mobile-tv project. Novel ways of using Nd:YAG laser for welding thick section austenitic stainless steel Novel ways of using Nd:YAG laser for Caj Södergård (ed.). 2003. 238 p. + app. 35 p. 507 Rosqvist, Tony. On the use of expert judgement in the qualification of risk assessment. Novel ways of using Nd:YAG laser 2003. 48 p. + app. 82 p. 508 Parviainen, Päivi, Hulkko, Hanna, Kääriäinen, Jukka, Takalo, Juha & Tihinen, Maarit. for welding thick section austenitic Requirements engineering. Inventory of technologies. 2003. 106 p. 509 Sallinen, Mikko. Modelling and estimation of spatial relationships in sensor-based robot stainless steel workcells. 2003. 218 p. 510 Kauppi, Ilkka. Intermediate Language for Mobile Robots. A link between the high-level planner and low-level services in robots. 2003. 143 p. 511 Mäntyjärvi, Jani. Sensor-based context recognition for mobile applications. 2003. 118 p. + app. 60 p. 512 Kauppi, Tarja. -
Technical Report 09-05
nagra Technical Report 09-05 Critical Review of Welding Technology for Canisters for Disposal of Spent Fuel and High LevelWaste March 2010 5. Pike, C. Allen, C. Punshon, P. Threadgill, M. Gallegillo, B. Holmes, J. Nicholas TWI, Ltd. National Cooperative forthe Disposal of Radioactive Waste Hardstrasse 73 CH-5430 Wettingen Switzerland Tel. +41 56 437 1 1 1 1 www.nagra.ch nagra Technical Report 09-05 Critical Review of Welding Technology for Canisters for Disposal of Spent Fuel and High LevelWaste March 2010 5. Pike, C. Allen, C. Punshon, P. Threadgill, M. Gallegillo, B. Holmes, J. Nicholas TWI, Ltd. National Cooperative forthe Disposal of Radioactive Waste Hardstrasse 73 CH-5430 Wettingen Switzerland Tel. +41 56437 11 11 www.nagra.ch This report was prepared on behalf of Nagra. The viewpoints presented and conclusions reached are those of the author(s) and do not necessarily represent those of Nagra. ISSN 1015-2636 "Copyright © 2010 by Nagra, Wettingen (Switzerland)/All rights reserved. All parts of this work are protected by copyright. Any utilisation outwith the remit of the copyright law is unlawful and liable to prosecution. This applies in particular to translations, storage and processing in electronic systems and programs, microfilms, reproductions, etc." I NAGRA NTB 09-05 Executive Summary Background Nagra is the Swiss national cooperative for the disposal of radioactive waste and is responsible for final disposal of all types of radioactive waste produced in Switzerland. As part of Nagra's long term disposal strategy, plans must be developed for two repositories, one for spent fuel (SF), vitrified high-level waste (HLW) and long-lived intermediate level waste and one for low and intermediate level waste. -
Laser Welding of High-Strength Galvanized Steels in a Gap-Free Lap Joint Configuration Under Different Shielding Conditions
Yang Supplement December 2010:Layout 1 12/13/10 4:32 PM Page 8 Laser Welding of High-Strength Galvanized Steels in a Gap-Free Lap Joint Configuration under Different Shielding Conditions By designing the specific shielding conditions, completely defect-free lap joints of the galvanized steels in a lap joint configuration are achieved by a single laser beam without pre- and postweld processing BY S. YANG, B. CARLSON, AND R. KOVACEVIC veloped at the interface of the two metal ABSTRACT sheets. The highly pressurized zinc vapor expels the liquid metal out of the molten It is a great challenge to laser weld zinc-coated steels in a gap-free lap joint con- pool and produces weld defects such as figuration due to the formation of highly pressurized zinc vapor. In this study, dif- spatter and porosity during the laser weld- WELDING RESEARCH ferent shielding conditions were designed to mitigate the highly pressurized zinc ing process. These defects significantly de- vapor. Argon, helium, the mixture of argon and carbon dioxide, and the mixture of grade the mechanical properties of the argon and oxygen were selected as the shielding gases to study the effects of shield- weld joints. ing conditions on weld quality. The introduction of a side shielding gas not only blew In the past several decades, many ef- away the laser-induced plasma but also suppressed the instability of the molten pool forts have been made to suppress the ef- caused by the highly pressurized zinc vapor. Under the optimal setting of shielding fect of the highly pressurized zinc vapor on gas conditions, a stable keyhole was consistently formed that provided a channel to the weld quality. -
UNIT 3: WELDING Definition: Welding Is a Process of Joining Similar Or Dissimilar Materials by the Application of Heat And/Or Pressure
UNIT 3: WELDING Definition: Welding is a process of joining similar or dissimilar materials by the application of heat and/or pressure. Principle of welding: If two surfaces are brought together in such a way that nothing but the grain boundaries separate them then the two bodies with adhere with a very large force resulting in what we called welding. Types of welding: 1 Fusion Welding Processes Fusion welding is a joining process that uses fusion of the base metal to make the weld. The three major types of fusion welding processes are as follows: 1. Gas welding: Oxyacetylene welding (OAW) 2. Arc welding: Shielded metal arc welding (SMAW) Gas–tungsten arc welding (GTAW) Gas–metal arc welding (GMAW) Submerged arc welding (SAW) 3. High-energy beam welding: Laser beam welding (LBW) Electron Beam Welding (EBW) OXYACETYLENE WELDING The Process Gas welding is a welding process that melts and joins metals by heating them with a flame caused by the reaction between a fuel gas and oxygen. Oxyacetylene welding (OAW), shown in Figure 1, is the most commonly used gas welding process because of its high flame temperature. A flux may be used to deoxidize and cleanse the weld metal. The flux melts, solidifies, and forms a slag skin on the resultant weld metal. Figure 2 shows three different types of flames in oxyacetylene welding: neutral, reducing, and oxidizing (4), which are described next. Three Types of Flames A. Neutral Flame This refers to the case where oxygen (O2) and acetylene (C2H2) are mixed in equal amounts and burned at the tip of the welding torch. -
Aluminium Design and Construction
Aluminium Design and Construction Copyright 1999 by Taylor & Francis Group. All Rights Reserved. Aluminium Design and Construction John Dwight MSc, FI Struct E Former Reader in Structural Engineering, University of Cambridge; and Fellow of Magdalene College, Cambridge E & FN SPON An Imprint of Routledge London and New York Copyright 1999 by Taylor & Francis Group. All Rights Reserved. First published 1999 by E & FN Spon, an imprint of Routledge 11 New Fetter Lane, London EC4P 4EE This edition published in the Taylor & Francis e-Library, 2002. Simultaneously published in the USA and Canada by Routledge 29 West 35th Street, New York, NY 10001 © 1999 John Dwight All rights reserved. No part of this book may be reprinted or reproduced or utilized in any form or by any electronic, mechanical, or other means, now known or hereafter invented, including photocopying and recording, or in any information storage or retrieval system, without permission in writing from the publishers. British Library Cataloguing in Publication Data A catalogue record for this book is available from the British Library Library of Congress Cataloging in Publication Data Dwight, J.B. (John B.), 1921– Aluminium design and construction/J.B.Dwight. p. cm. Includes bibliographical references and index. ISBN 0-419-15710-7 (Print Edition) 1. Aluminum construction. 2. Aluminum. 3. Aluminum, Structural. 4. Structural design—Standards—Europe. I. Title TA690.D855 1998 624.1'826–dc21 98–39235 CIP ISBN 0 419 15710 7 (Print Edition) ISBN 0-203-02819-8 Master e-book ISBN ISBN 0-203-13449-4 (Glassbook Format) Copyright 1999 by Taylor & Francis Group.