Reconfigurable Phase-Change Photomask for Grayscale Photolithography
Total Page:16
File Type:pdf, Size:1020Kb
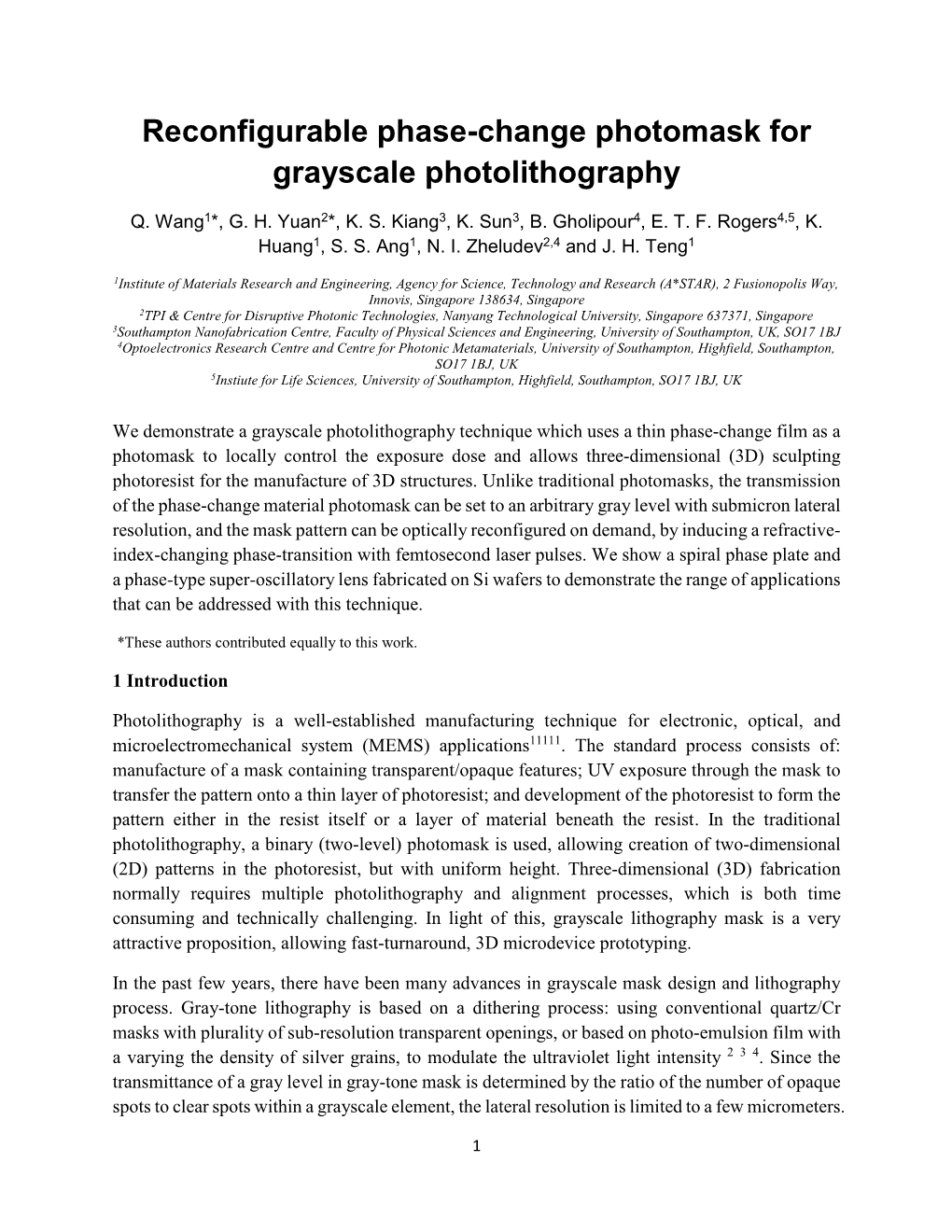
Load more
Recommended publications
-
High-End EUV Photomask Repairs for Advanced Nodes
High-end EUV Photomask Repairs for advanced nodes Dr. Michael Waldow Product Manager vZTech - Virtual SMS Tech Conference, 18.05.2021 Agenda 1 Introduction 2 High-end EUV photomask repairs 3 Summary Carl ZEISS SMT GmbH, Dr. Michael Waldow, Semiconductor Mask Solutions 18.05.2021 2 Agenda 1 Introduction 2 High-end EUV photomask repairs 3 Summary Carl ZEISS SMT GmbH, Dr. Michael Waldow, Semiconductor Mask Solutions 18.05.2021 3 Introduction EUV High-Volume manufacturing ramping up SAMSUNG newsroom C. C. Wei – TSMC - CEO & Vice Chairman* MAY 21, 2021 JULY 16, 2020 “…new production line in Pyeongtaek, Korea…will produce 14- ‚Next, let me talk about our N5 ramp up and N4 introduction. N5 is the foundry nanometer DRAM and 5-nanometer logic, …based on EUV...” industry's most advanced solution with best PPA. N5 is already in volume Anandtech.com - APRIL 02, 2021 production with good yield, while we continue to improve the “… South Korea authorities this week gave SK Hynix a green light to build We are seeing robust productivity and performance of the EUV tools. a new, 120 trillion won ($106.35 billion) fab complex…. using demand for N5 and expect a strong ramp of N5 in the second half of this year, driven by both 5G smartphones and HPC applications.‘ process technologies that rely on extreme ultraviolet lithography (EUV)…’ ▪ EUV is becoming more and more important and Intel: The Empire Strikes Back** MAY 21, 2021 amount of EUV lithographic layers is rising ‚while the outlook on EUV was still quite uncertain. Hence, Intel's initial 7nm ▪ First consumer products based on EUV seems to have used EUV quite conservatively, in relatively few layers. -
Gray-Scale Photolithography Using Microfluidic Photomasks
Gray-scale photolithography using microfluidic photomasks Chihchen Chen, Danny Hirdes, and Albert Folch* Department of Bioengineering, University of Washington, Seattle, WA 98195 Edited by George M. Whitesides, Harvard University, Cambridge, MA, and approved December 23, 2002 (received for review September 23, 2002) The ability to produce three-dimensional (3D) microstructures is of Here we demonstrate a type of gray-scale photomasks that increasing importance in the miniaturization of mechanical or allow for patterning large areas (Ͼ3 inches in diameter) using fluidic devices, optical elements, self-assembling components, and standard photolithographic equipment (i.e., a contact mask tissue-engineering scaffolds, among others. Traditional photoli- aligner with a collimated UV source). Our photomasks contain thography, the most widely used process for microdevice fabrica- light-absorbing features that are liquid (i.e., dyes) and can be tion, is ill-suited for 3D fabrication, because it is based on the addressed (i.e., altered) by means of microfluidic channels. We illumination of a photosensitive layer through a ‘‘photomask’’ term them ‘‘microfluidic photomasks’’ (FPMs). The FPMs (a transparent plate that contains opaque, unalterable solid-state are advantageous in that (i) they contain a virtually unlimited features), which inevitably results in features of uniform height. number of gray scales as given by variations in dye concentration, We have devised photomasks in which the light-absorbing fea- (ii) they can be manufactured rapidly and inexpensively, and tures are made of fluids. Unlike in conventional photomasks, the (iii) the fluidic patterns can be changed in the time scale of a opacity of the photomask features can be tailored to an arbitrary few seconds, thus allowing for rapid reconfiguration of the number of gray-scale levels, and their spatial pattern can be photomask. -
Integrated Circuit (Ic) and Photomask Images Processing Technology
INTEGRATED CIRCUIT (IC) AND PHOTOMASK IMAGES PROCESSING TECHNOLOGY A. Doudkin, D. Vershok Laboratory of System Identification of United Institute of Informatics Problems of NASB, 6, Surganova str., BY-220012, Minsk, Belarus e-mails: doudkin{vershok}@newman.bas-net.by Abstract. The integrated circuit and photomask images processing technology is proposed. This technology allows to perform the restoration of the integrated-circuit metallization layout and the mask artwork from the images of IC metallization layers or photomask set correspondingly. It can be applied for the tasks of integrated circuits redesign and automated visual inspection of integrated circuits and photomask production. 1. Introduction The modern semiconductor manufacturing needs to control all of the critical process modules that drive IC manufacturing success. Several factors inherent in the semiconductor industry drive the critical need for comprehensive yield management and process control solutions. Among the most significant of these are: increasing device complexity; shrinking geometries; reduced product life cycles. The visual or optical inspec- tion is the important part of such control solutions. It implies the presence of some operative analysis system [1] providing image registration, visual information processing and analysis. In this paper the main attention is paid to image processing technology which was developed for this sort of the systems. 2. Problem formulation The proposed technology has the following objectives: 1 restoration of the integrated-circuit metalli- zation layout from the images of IC metallization layers; 2 restoration of the mask artwork from the images of photomask set. Thus, the objects of processing are raster patterns of IC metallization layers and IC pho- tomasks, represented as the collection of partially overlapping images (frames) without any reference marks (Fig 1.). -
Fundimentals of Photolithography
FUNDIMENTALS OF PHOTOLITHOGRAPHY One of the most widely used methods for creating nanoscale circuit components is Photolithography. The word lithography is derived from the Greek words lithos (stone) and graphein (to write) and finds its roots in a process invented by Aloys Senefelder in 1796. By treating a piece of limestone with certain chemicals, Senefelder was then able to transfer an image carved into the stone onto a piece of paper. This was done by coating certain parts of the porous limestone with a water repellant substance. When ink was applied to the stone it would only adhere to the untreated hydrophilic areas, and hence the image carved into the rock could be transferred repeatedly onto paper. Senefelder's technique is still used in some artistry applications today. As time progressed and technology improved, lithography methods evolved. In the 1820's a French scientist by the name of Nicephore Niepce developed the first photoresist, a component fundamental to photolithography. A photoresist is a substance that undergoes a chemical reaction when it is eXposed to light. Niepce's photoresist was a material known as Bitumen of Judea, a kind of naturally occurring asphalt. A sheet of stone, metal, or glass was coated with a thin layer of this bitumen, which became less soluble where it was eXposed to light. Areas that were uneXposed could then be removed using a solvent, and the resultant exposed areas of the sheet were etched using a chemical bath. After the remaining photoresist was removed, the sheet could then be used as a printing plate. Photolithography today is in many ways similar to the original process invented by Niepce. -
Contact Photolithography
Contact Photolithography Overview Contact photolithography is performed using a Mask Aligner. A mask aligner has two main tooling structures: the Mask Holder and the Wafer Chuck. The mask holder is machined to have an extremely flat surface, and the photomask is held in place on this surface by vacuum. The wafer chuck, which is also machined to be very flat, holds the wafer in place also by using vacuum. This tooling is carefully mounted so that during operation the surfaces of the two parts are kept parallel to each other. The wafer chuck can be moved up to the mask holder in order to bring the wafer into contact with the photomask using variable force. The wafer chuck surface position can also be adjusted to be as planar as possible with the mask in order to yield the best results; this is called Wedge Error Compensation. Once the wafer and mask are positioned an exposure can be performed by opening a shutter on the Lamp Housing. Inside the lamp housing there is a Mercury (Hg) arc lamp and associated optics which will allow a selected controlled band of UV light to expose the mask and wafer. There is an optical system incorporated into the tooling which can be used to view alignment marks on the wafer through complimentary marks on the photomask. Micrometers on the wafer chuck tooling allow the operator to move the wafer into alignment with the mask before exposure. Mask aligners are typically manually operated but some versions are nearly fully automated. Design Contact photolithography has the advantage of exposing the entire wafer surface in one process cycle. -
2019 Corporate Responsibility Report
TABLE OF CONTENTS 01 COMPANY PROFILE 07 COMMUNITY ENGAGEMENT 02 CEO STATEMENT 08 SUSTAINABLE MANUFACTURING 03 GOVERNANCE 09 PRODUCT STEWARDSHIP 04 STAKEHOLDER ENGAGEMENT 10 SITE PROFILES 05 SUPPLIER RESPONSIBILITY 11 ABOUT THIS REPORT 06 OUR PEOPLE AND WORKPLACE 12 GRI CONTENT INDEX GLOBALFOUNDRIES | CORPORATE RESPONSIBILITY REPORT 2019 BACK | MENU | NEXT 2 01 COMPANY PROFILE We are GLOBALFOUNDRIES, a leading full- While execution excellence remains our Today, GF operates manufacturing facili- service foundry delivering truly differentiated first priority, we are more than a manufac- ties in Dresden, Germany; Malta and East semiconductor solutions, created ten years turer. We are the catalyst for growth in the Fishkill, New York; Burlington, Vermont; and ago with an integral commitment to social and industries we serve. With one of the largest Singapore. GF’s corporate offices are in Santa environmental responsibility and dedicated to populations of leading-edge scientists Clara, California (Silicon Valley) with a global ethical and responsible business practices. and technologists in the semiconductor network of R&D, design enablement, and manufacturing industry, we make possible customer support operations (please refer to GF provides a unique combination of design, the technologies and systems that trans- the map “Company Locations”). GF is owned development, and fabrication services for a form industries. We are dedicated to being by Mubadala Investment Company, which is range of high-growth markets. With a manu- the best possible partner for our clients, owned by the Government of Abu Dhabi. facturing footprint spanning three continents, delivering the expertise and insights to GF has the flexibility and agility to meet the help position them as the leaders in their 2019 marks the tenth anniversary of the dynamic needs of clients across the globe. -
An Empirical Study of Photomask Manufacturing Productivity
Benchmarking the Productivity of Photomask Manufacturers C. Neil Berglund and Charles M. Weber Charles Weber (primary corresponding author) Department of Engineering and Technology Management Portland State University P.O. Box 751 Portland, Oregon 97207-0751 Phone: 503 725 8133 Facs: 503 725 4667 Email: [email protected] Neil Berglund Department of Engineering and Technology Management Portland State University P.O. Box 751 Portland, Oregon 97207-0751 Phone: 503 725 4660 Facs: 503 725 4667 Email: [email protected] Page 1 of 27 Benchmarking the Productivity of Photomask Manufacturers C. Neil Berglund1 and Charles M. Weber1, 1Portland State University-ETM, Portland, Oregon, 97207-0751, USA ABSTRACT A survey-based, empirical study that benchmarks the productivity of photomask manufacturers has led to some significant conclusions. Firstly, the wide variation in the productivity indicators from company to company suggests that all participants may have significant cost-reduction opportunities within their operations -- even among the best performers capital is underutilized. Secondly, the high downtime of pattern generation tools is limiting productivity. Thirdly, producing smaller feature sizes is correlated to an investment in engineering and experimentation capacity. It could not be confirmed that photomask manufacturers are successfully taking advantage of economies of scale, suggesting that the outlook for profitability of many photomask manufacturers is precarious. Keywords: Benchmarking, Photomask, Manufacturing, Productivity 1. INTRODUCTION For the past four decades, Moore’s Law [1], which states that the number of transistors that can be built into a given amount of chip space will double every 12 to 18 months, has been driving the dimensions of merit for semiconductor manufacturing and its enabling technologies. -
SPIE Photomask Conference 2014, 16 – 18 September, 2014 We Are Pleased to Present in Cooperation with Our Partners the Followi
SPIE Photomask Conference 2014, 16 – 18 September, 2014 We are pleased to present in cooperation with our partners the following topics during SPIE Photomask Conference. Don´t miss it! Tuesday, Sept. 16th, 9:15 – 10:15am | EUV mask infrastructure: Don’t miss the train! - Invited Paper, Dr. Oliver Kienzle, Carl Zeiss SMS GmbH Tuesday, Sept. 16th, 1:45 – 3:35pm | Automated hotspot analysis with aerial image CD metrology for advanced logic devices, Ute Buttgereit, Thomas Trautzsch, Carl Zeiss SMS GmbH (Germany); Min-Ho Kim, Jung-Uk Seo, Young-Keun Yoon, Hakseung Han, Dong-Hoon Chung, Chan-Uk Jeon, SAMSUNG Electronics Co., Ltd. (Korea, Republic of); Gary Meyers, Synopsys, Inc. (USA) Tuesday, Sept. 16th 6:00 – 7:30pm (Poster Session) | Further beyond – Registration & Overlay Control Enhancements for Optical masks, Kujan Gorhad, Carl Zeiss SMS Ltd. (Israel); Dirk Beyer, Carl Zeiss SMS GmbH (Germany); Avi Cohen, Dan Avizemer, Erez Graitzer, Carl Zeiss SMS Ltd. (Israel); Ch. Ehrlich W. Degel, Markus Kirsch, Carl Zeiss SMS GmbH Tuesday, Sept. 16th 6:00 – 7:30pm (Poster Session) | On the benefit of high resolution and low aberrations for in-die mask registration metrology, Thomas Scherübl, Dirk Beyer, Dirk Seidel, Steffen Steinert, Sven Heisig, Susanne Töpfer, Carl Zeiss SMS GmbH Tuesday, Sept. 16th 6:00 – 7:30pm (Poster Session) | Short feedback loop for OPC model based wafer level CD, GuoXiang Ning, GLOBALFOUNDRIES Inc. (USA); Thomas Thaler, Kristian Schulz, Ute Buttgereit, Carl Zeiss SMS GmbH; Peter Philipp, Advanced Mask Technology Ctr. GmbH Co. KG (Germany); Paul W. Ackmann, Lloyd C. Litt, Chin-Teong Lim, GLOBALFOUNDRIES Inc. (USA) Wednesday, Sept. -
Photomask Patterning for Slope-Form Deep Etching Using Deep-Reactive-Ion Etching and Gradation Exposure
Sensors and Materials, Vol. 26, No. 1 (2014) 31–37 MYU Tokyo S & M 0967 Photomask Patterning for Slope-Form Deep Etching Using Deep-Reactive-Ion Etching and Gradation Exposure Masaki Yamaguchi* and Yuki Nakayama Graduate School of Engineering, Iwate University, 4-3-5 Ueda, Morioka 020-8551, Japan (Received August 8, 2013; accepted November 8, 2013) Key words: deep-reactive-ion etching (DRIE), gradation exposure, silicon mold, micro-electro- mechanical systems (MEMS), microneedle The purpose of this research is to demonstrate a methodology for etching silicon to particular required depths that can be used when designing structures to manufacture microneedles. A photolithography technique was demonstrated using gradation exposure and deep-reactive-ion etching (DRIE). The entire photolithography process was carried out in two steps: (i) a photoresist pattern was transferred onto silicon dioxide using a layout mask, and (ii) a silicon mold was formed using exposure through the use of a gradation mask and DRIE. A digital gradation mask design that included 16 scales was proposed. The exposure time and thickness of the photoresist were optimized experimentally under 102 different conditions. The aspect ratio of the resist reached 19:1 and the maximum etched depth was 285 µm under conditions of 6 s exposure time and 3 µm thickness of the photoresist. It was demonstrated that the slopes formed by deep etching ranged between 0–285 µm, which is needed for microneedles to be realised by DRIE and grey-scale technology. 1. Introduction Microneedles, -
Photolithography Basics Photolithography Is the Process of Transferring Geometric Shapes on a Mask to the Surface of a Silicon Wafer
Photolithography Basics Photolithography is the process of transferring geometric shapes on a mask to the surface of a silicon wafer. The steps involved in the photolithographic process are wafer cleaning; barrier layer formation; photoresist application; soft baking; mask alignment; exposure and development; and hard-baking. Wafer Cleaning, Barrier Formation and Photoresist Application In the first step, the wafers are chemically cleaned to remove particulate matter on the surface as well as any traces of organic, ionic, and metallic impurities. After cleaning, silicon dioxide, which serves as a barrier layer, is deposited on the surface of the wafer. After the formation of the SiO2 layer, photoresist is applied to the surface of the wafer. High-speed centrifugal whirling of silicon wafers is the standard method for applying photoresist coatings in IC manufacturing. This technique, known as "Spin Coating," produces a thin uniform layer of photoresist on the wafer surface. Positive and Negative Photoresist There are two types of photoresist: positive and negative. For positive resists, the resist is exposed with UV light wherever the underlying material is to be removed. In these resists, exposure to the UV light changes the chemical structure of the resist so that it becomes more soluble in the developer. The exposed resist is then washed away by the developer solution, leaving windows of the bare underlying material. In other words, "whatever shows, goes." The mask, therefore, contains an exact copy of the pattern which is to remain on the wafer. Negative resists behave in just the opposite manner. Exposure to the UV light causes the negative resist to become polymerized, and more difficult to dissolve. -
Strengthening the Global Semiconductor Supply Chain in An
1 About Boston Consulting Group (BCG) Boston Consulting Group (BCG) is a leading global management consulting firm, with offices in over 50 countries. BCG partners with leaders in business and society to tackle their most important challenges and capture their greatest opportunities. BCG was the pioneer in business strategy when it was founded in 1963. Today, we help clients with total transformation—inspiring complex change, enabling organizations to grow, building competitive advantage, and driving bottom-line impact. About the Semiconductor Industry Association (SIA) The Semiconductor Industry Association (SIA) is the voice of the semiconductor industry in the US, one of America’s top export industries and a key driver of America’s economic strength, national security, and global competitiveness. The semiconductor industry directly employs nearly a quarter of a million workers in the United States, and US semiconductor company sales totaled $208 billion in 2020. SIA represents 98 percent of the US semiconductor industry by revenue and nearly two-thirds of non-US chip firms. Through this coalition, SIA seeks to strengthen leadership of semiconductor manufacturing, design, and research by working with Congress, the Administration, and key industry stakeholders around the world to encourage policies that fuel innovation, propel business, and drive international competition. About the Authors Antonio Varas is a Senior Partner and Managing Director in the Silicon Valley office of Boston Consulting Group and is a core member of its Technology, Media & Telecommunications practice. You may contact him by email at [email protected]. Raj Varadarajan is a Senior Partner and Managing Director in the Dallas office of Boston Consulting Group and leads its Global Advantage practice in North America. -
Contact Photolithography at Sub-Micrometer Scale Using a Soft Photomask
micromachines Article Contact Photolithography at Sub-Micrometer Scale Using a Soft Photomask Chun-Ying Wu , Heng Hsieh and Yung-Chun Lee * Department of Mechanical Engineering, National Cheng Kung University, Tainan 70101, Taiwan * Correspondence: [email protected] Received: 14 July 2019; Accepted: 16 August 2019; Published: 18 August 2019 Abstract: This paper proposes a method for improving the patterning resolution of conventional contact photolithography from the micrometer, down to the sub-micrometer scale. The key element is a soft polydimethylsiloxane (PDMS) photomask, which is first replicated from a silicon mold and then patterned with a black photoresist (PR) layer to selectively block ultraviolet (UV) light. This soft PDMS photomask can easily form an intimate and conformable contact with a PR-coated substrate and hence can perform contact photolithography with high pattern resolution. The fabrication processes of this black-PR/PDMS soft photomask are experimentally carried out. Using the fabricated soft photomask, UV patterning by contact photolithography with the smallest line-width of 170 nm over a 4” wafer area was successfully achieved. The advantages and potentials of this new type of contact photolithography will be addressed. Keywords: soft photomask; contact photolithography; black photoresist; ultraviolet patterning; sub-micrometer scale 1. Introduction Photolithography technologies have been successfully developed in the past few decades and are now the most mature and dominant method for micro- and nanofabrication in the industry [1–4]. There are basically two categories of photolithography. The image-projection photolithography utilizes an ultraviolet (UV) light source and an optical image projection system to project a de-magnified pattern defined by a glass or quartz photomask onto a photo-sensitive layer (known as a photoresist (PR) layer) deposited on a substrate.