U Nited States Patent (19)
Total Page:16
File Type:pdf, Size:1020Kb
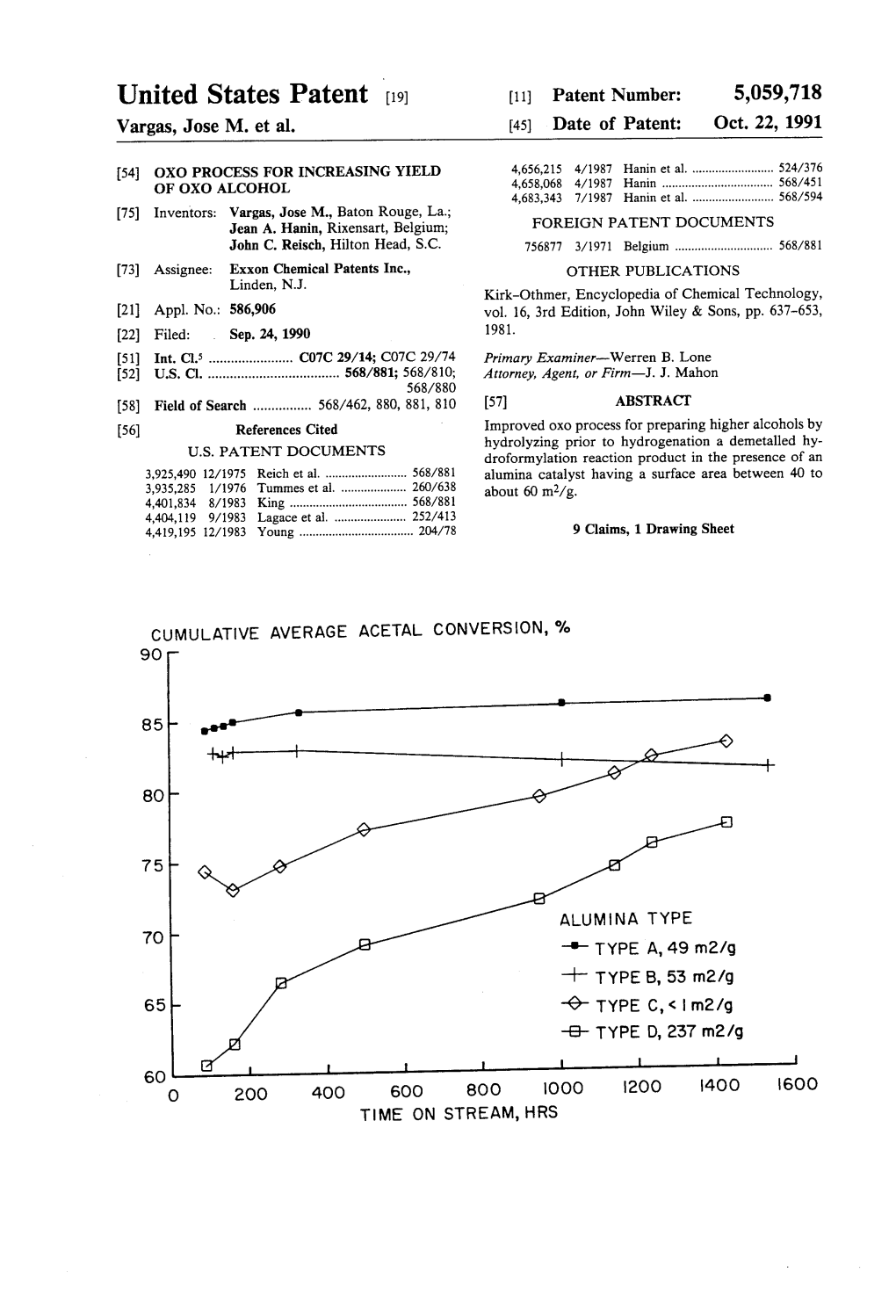
Load more
Recommended publications
-
Oxo Alcohols Market.Pdf
Oxo Alcohols Market – Business Opportunities, Key-players Analysis and Forecast to 2020 Oxo alcohols are prepared from a two-step process. First step is to convert olefins to alcohols by reaction with syn gas (carbon monoxide & hydrogen) followed by hydrogenation of the resultant aldehyde. In the first step, hydroformylation reaction is carried out under low pressure in the presence of rhodium catalyst (LP Oxo process). For example, ethylene may be hydro formulated to produce normal-butyraldehyde and iso-butyraldehyde which are hydrogenated to produce n-butanol and isobutanol. Browse detailed TOC, Tables, Figures, Charts and Companies mentioned in Oxo alcohols market research report at- http://www.absolutereports.com/10165437 The major applications of Oxo alcohols are plasticizers, paints, coatings & adhesives, lubricant additives, and chemical intermediates. Asia-Pacific is the global leader in the consumption of Oxo alcohols and this dominance is expected to continue till 2020. China is the key market in the region, consuming more than half of the demand for Oxo alcohols, followed by Japan, South Korea, and India, where consumption is growing steadily. Increase in the consumption of Oxo alcohol for air conditioning & refrigeration, chemical processing, transportation, and consumer goods industry has been observed in Asia-Pacific due to continued industrialization and rise in the manufacturing sector of the region. Growing innovation and developments in the Oxo alcohol consumer industries are directly affecting the rise in the use of Oxo alcohols. Request for sample PDF of Oxo alcohols market research report at- http://www.absolutereports.com/enquiry/request-sample/10165437 The Oxo alcohols market is very competitive due to the presence of big players in the business, which inhibits the new entrants and local manufacturers to capture a good share at global level. -
1.1. Introduction the Reaction Between Olefinic Double Bond and a Mixture
Chapter-1 Hydroformylation of alkenes 1.1. Introduction The reaction between olefinic double bond and a mixture of carbon monoxide and hydrogen leads to linear and branched aldehydes as primary products and is known as hydroformylation reaction. Aldehydes O H O (i) Catalyst R R + CO + H + 2 (ii) Pressure H R alkene (iii) Temperature linear (normal) branched (iso) side reactions R R alkene isomerization alkene hydrogenation Adkins [1] has introduced the term “hydroformylation” for this reaction, since there is attack of hydrogen and formyl group (–CHO) at the unsaturated center of the carbon chain of alkenes. This reaction is an ideal example of atom economic C-C bond formation since the product aldehyde is formed with an additional carbon atom than starting olefin. Although the primary products of hydroformylation reactions are aldehydes, the formation of other oxygen containing by-products [2] accompanied with the side-products such as alcohols, formic acid esters, and higher boiling residues is also observed. Other products namely oxo alcohol and carboxylic acid are formed by hydrogenation and oxidation respectively of the primary oxo products, the aldehydes. Otto Roelen discovered hydroformylation reaction in 1938 [3], during his work on increasing the chain-length of Fischer-Tropsch (FT) hydrocarbons. When a mixture of ethylene and syn-gas was passed over a fixed bed cobalt containing catalyst at 1500C and 100 bar pressure, Roelen’s could perceive, isolate and characterize the small amount of propanal (and diethyl ketone) that had formed under the unconventional F-T conditions. It was his scientific perceptions that made him possible to link the formation of propanal from ethylene and syn-gas, which was catalyzed by metal-carbonyl formed the F-T reaction conditions. -
Linear Alpha-Olefins (681.5030)
IHS Chemical Chemical Economics Handbook Linear alpha-Olefins (681.5030) by Elvira O. Camara Greiner with Yoshio Inoguchi Sample Report from 2010 November 2010 ihs.com/chemical November 2010 LINEAR ALPHA-OLEFINS Olefins 681.5030 B Page 2 The information provided in this publication has been obtained from a variety of sources which SRI Consulting believes to be reliable. SRI Consulting makes no warranties as to the accuracy completeness or correctness of the information in this publication. Consequently SRI Consulting will not be liable for any technical inaccuracies typographical errors or omissions contained in this publication. This publication is provided without warranties of any kind either express or implied including but not limited to implied warranties of merchantability fitness for a particular purpose or non-infringement. IN NO EVENT WILL SRI CONSULTING BE LIABLE FOR ANY INCIDENTAL CONSEQUENTIAL OR INDIRECT DAMAGES (INCLUDING BUT NOT LIMITED TO DAMAGES FOR LOSS OF PROFITS BUSINESS INTERRUPTION OR THE LIKE) ARISING OUT OF THE USE OF THIS PUBLICATION EVEN IF IT WAS NOTIFIED ABOUT THE POSSIBILITY OF SUCH DAMAGES. BECAUSE SOME STATES DO NOT ALLOW THE EXCLUSION OR LIMITATION OF LIABILITY FOR CONSEQUENTIAL OR INCIDENTAL DAMAGES THE ABOVE LIMITATION MAY NOT APPLY TO YOU. IN SUCH STATES SRI CONSULTING’S LIABILITY IS LIMITED TO THE MAXIMUM EXTENT PERMITTED BY SUCH LAW. Certain statements in this publication are projections or other forward-looking statements. Any such statements contained herein are based upon SRI Consulting’s current knowledge and assumptions about future events including without limitation anticipated levels of global demand and supply expected costs trade patterns and general economic political and marketing conditions. -
9 WO 7/NFC Re
Oct. 14, 1952 W. M. SMITH 2,614,070 HEAT TREATING AND DISTILLATION OF OXO ALCOHOLS Filed Nov. 16, 1949 COMAAM sa, a A42A Ayala 7aa 7O OCMAA2 A/ASA Ad S7Coa a GA 2 -pCOMADAM, CAE Ae 9 WO 7/NFC re - 15 2O HS 7aas/A/ZaAs, 7O UAE a (3) -o 22 7o s7 oadca /2 AFA2a C7 / C /ya 7/NG M6 Es 7O CL/AA /6 eas Cd/a Aa Patented Oct. 14, 1952 2,614,070 UNITED STATES PATENT OFFICE 2,614,070 HEATREATING AND DASALLATION OF OXO ALCOHOLS Warren M. Smith, Baton Rouge, La., assignor to Standard Oil Development Company, a corpo ration of Delaware Application November 16, 1949, Seria No. 2,628 5 Claims. (C. 202-5) 1. 2 This invention relates to improvements for the a large number of different types of reactions purification of crude alcohols, by a distillation take place to form a variety of products. The procedure. More specifically the invention re chief primary reaction products as Outlined lates to an improved distillation method for puri above are aldehydes. These aldehydes themselves fying higher boiling Oxo alcohols which contain 5 can undergo further reactions to yield other prod inpurities of the type tending to undergo de ucts. For instance, the aldehydes condense: With composition at the normal boiling point of the each other to yield aldols. At least a part of Oxo alcohol undergoing purification by distilla the aldols undergo dehydration to yield alpha-, tion. beta-unsaturated aldehydes. Some ketones are In practicing this invention, the crude Oxo 0 also formed under the reagtion conditions. -
Surfactant Book 2007
Surfactants: Strategic Personal Care Ingredients Anthony J. O’Lenick, Jr. ISBN 978-1-932633-96-2 Copyright 2014, by Anthony J. O'Lenick, Jr. This book is out of print. The copyright has reverted back to the author. It is being made available free of charge in electronic version. Please feel free to use it, download it or cite it in other publications. Allured Publishing Corporation 362 South Schmale Road, Carol Stream, IL 60188-2787 USA Tel: 630/653-2155 Fax: 630/653-2192 e-mail: [email protected] Table of Contents Preface................................................................................................................... vii About the Author ................................................................................................. viii Acknowledgments .................................................................................................. ix Chapter 1: Raw Materials for Surfactant Preparation Background ............................................................................................................. 1 Triglycerides............................................................................................................ 4 Methyl Esters ........................................................................................................ 20 Fatty Acids ............................................................................................................ 20 Natural Acids .................................................................................................... 20 Guerbet -
New Branched Oxo Alcohol Based Acrylates for Pressure Sensitive Adhesive Applications
New Branched Oxo Alcohol Based Acrylates for Pressure Sensitive Adhesive Applications Chunzhao Li, Donald Mattran, ExxonMobil Chemical Company, Baytown, TX Bernard Leroy, Levi Salaets, Silvio Carrettin, Geert Steenbeke, ExxonMobil Chemical Company, Machelen, Belgium Frank Chen, ExxonMobil Chemical Company, Shanghai, China Xinxin Sheng, Guangdong University of Technology, Guangzhou, China Xinya Zhang, South China University of Technology, Guangzhou, China Introduction Pressure sensitive adhesive (PSA) designates a type of polymeric material that when dried, is aggressively and permanently tacky at room temperature. A PSA will firmly adhere to a variety of similar or dissimilar surfaces upon mere contact with no more than finger pressure. Acrylic PSAs can be either solventborne, waterborne emulsion or the more recent 100% solids UV curable hot melt. Pressure sensitive adhesive compositions are useful for a wide variety of applications such as labels, tapes, decals, decorative and protective sheets, medical and other specialty areas. Three properties critical to PSAs are tack, peel (adhesion) and shear strength (cohesion). To achieve desired performance, acrylic PSAs are produced using a combination of monomers. The monomer mixture typically includes one or more soft monomers such as butyl acrylate (BA) or 2- ethyl hexyl acrylate (2-EHA), to impart good tack and deformability, and one or more hard monomers such as methyl methacrylate, styrene or vinyl acetate, to provide the cohesive strength. Small amounts of functional monomers such as acrylic acid (AA) or methacrylic acid (MAA) and 2-hydroxyethyl acrylate, are also typically used to provide crosslinking points and improve adhesion characteristics to highly polar substrates. Adhesive properties are affected by a number of factors such as polymer compositions, molecular weight, glass transition temperature (Tg), morphology, gel content and formulations which may incorporate plasticizer, tackifiers or crosslinkers. -
2. Project Design Basic
Mitsubishi Chemical Oxo Alcohol Technology 1. PROCESS FEATURE The characteristic and superiority of Mitsubishi Oxo Process are following points. (1) Very high quality of products The major derivatives of OXO alcohols are plasticizers and acrylates. From the quality point of view, not only the normal specifications but also small amounts of impurities are highlighted by our investigations. The small amounts of impurities are hardly able to be removed by easy distillation of alcohol. Typical advantage of Mitsubishi OXO Process is it provides super grade alcohol, containing negligible level of those impurities. Mitsubishi OXO Process is able to produce the highest grade alcohol in the world. This feature would be a great advantage for the user of Mitsubishi OXO Process. (2) High conversion efficiency Two steps reaction makes high propylene conversion. (3) Economical process Investment cost and energy consumption are low, because of lower reaction pressure and moderate reaction temperature, Plant utilizing Mitsubishi OXO Process needs less labor cost, because of simple process and stable operation. Particularly less management man-power is needed because the catalyst activity is stable and so management is not necessary. (4) Easy operation Simple process and adequate control system provides easy operation. Mitsubishi OXO Process has specially advanced OXO Reactor control system to stabilize the reaction rate and productivity. The selectivity, which is related to the product ratio of normal- and iso-Butyraldehyde, is also adjusted easily. (5) Catalyst recovery process Catalyst activity is stable and high, because of continuous operation of Heavy End Separation process and Catalyst Recovery process. Stable and high catalyst activity Copyright © 2014 Mitsubishi Chemical Corporation. -
Forty-Five Years of Progress for the LP Oxosm Process
https://doi.org/10.1595/205651317X695875 Johnson Matthey Technol. Rev., 2017, 61, (3), 246–256 JOHNSON MATTHEY TECHNOLOGY REVIEW www.technology.matthey.com Industrial Low Pressure Hydroformylation: Forty-Five Years of Progress for the LP OxoSM Process A long standing collaboration between Johnson Matthey and Dow continues to sustain the high standing of their oxo technology through innovative solutions to address the changing needs of the global oxo alcohol market By Richard Tudor Introduction Retired, Reading, UK The LP OxoSM Process is the rhodium-catalysed Atul Shah* hydroformylation process in wide use today in a variety Johnson Matthey, 10 Eastbourne Terrace, London, W2 of industrial applications. These applications have been 6LG, UK developed, co-marketed and licensed as a cooperation between affiliates of The Dow Chemical Company *Email: [email protected] (‘Dow’) and Johnson Matthey or their predecessors, for over 45 years. The LP OxoSM Process first made an impact in the 1970s when its technical elegancy, environmental Since the mid-1970s when the ‘Low Pressure Oxo’ footprint and economics attracted huge attention by process (LP OxoSM Process) was first commercialised, the world’s producers of normal butyraldehyde for it has maintained its global position as the foremost conversion to the plasticiser alcohol 2-ethylhexanol oxo process, offering particular appeal to independent (2EH). producers of commodity plasticisers facing increasing regulatory pressure. The story of this important The Early Dominance of Cobalt Catalysis industrial process is told from its early beginnings when laboratory discoveries by independent groups of Hydroformylation is the reaction of an unsaturated researchers in USA and UK revealed the remarkable olefinic compound with hydrogen and carbon ability of organophosphine containing rhodium monoxide to yield an aldehyde. -
169-264-Jmtr-Jul2017.Pdf
ISSN 2056-5135 JOHNSON MATTHEY TECHNOLOGY REVIEW Johnson Matthey’s international journal of research exploring science and technology in industrial applications Volume 61, Issue 3, July 2017 Published by Johnson Matthey www.technology.matthey.com © Copyright 2017 Johnson Matthey Johnson Matthey Technology Review is published by Johnson Matthey Plc. This work is licensed under a Creative Commons Attribution-NonCommercial-NoDerivatives 4.0 International License. You may share, copy and redistribute the material in any medium or format for any lawful purpose. You must give appropriate credit to the author and publisher. You may not use the material for commercial purposes without prior permission. You may not distribute modified material without prior permission. The rights of users under exceptions and limitations, such as fair use and fair dealing, are not affected by the CC licenses. www.technology.matthey.com JOHNSON MATTHEY TECHNOLOGY REVIEW www.technology.matthey.com Johnson Matthey’s international journal of research exploring science and technology in industrial applications Contents Volume 61, Issue 3, July 2017 170 Guest Editorial: Industry and Sustainability By Deirdre Black 172 Methanol Production – A Technical History By Daniel Sheldon 183 One Hundred Years of Gauze Innovation By Hannah Frankland, Chris Brown, Helen Goddin, Oliver Kay and Torsten Bünnagel 190 Osmium vs. ‘Ptène’: The Naming of the Densest Metal By Rolf Haubrichs and Pierre-Léonard Zaffalon 196 The ‘Nano-to-Nano’ Effect Applied to Organic Synthesis in Water By Bruce H. Lipshutz 203 “Sustainability Calling: Underpinning Technologies” A book review by Niyati Shukla and Massimo Peruffo 207 Highlights of the Impacts of Green and Sustainable Chemistry on Industry, Academia and Society in the USA By Anne Marteel-Parrish and Karli M. -
ANALYSIS of ALTERNATIVES Non-Confidential Report
ANALYSIS OF ALTERNATIVES non-confidential report Legal name of applicant(s): GRUPA AZOTY ZAKŁADY AZOTOWE KĘDZIERZYN S.A. Submitted by: GRUPA AZOTY ZAKŁADY AZOTOWE KĘDZIERZYN S.A. Substance: BIS(2-ETHYLHEXYL) PHTHALATE (DEHP) Use title: Formulation of DEHP in compounds, dry-blends and plastisol formulations Industrial use in polymer processing by calendering, spread coating, extrusion, injection moulding to produce PVC articles [except erasers, sex toys, small household items (<10cm) that can be swallowed by children, clothing intended to be worn against the bare skin; also toys, cosmetics and food contact material (restricted under other EU regulation)] Use number: Uses 1 and 2 ANALYSIS OF ALTERNATIVES © Grupa Azoty Zakłady Azotowe Kędzierzyn S.A. 2013 The information in this document is the property of Grupa Azoty Zakłady Azotowe Kędzierzyn S.A and may not be copied, communicated to a third party, or used for any purpose other than that for which it is supplied, without the express written consent of Grupa Azoty Zakłady Azotowe Kędzierzyn S.A. While the information is given in good faith based upon the latest information available to Grupa Azoty Zakłady Azotowe Kędzierzyn S.A, no warranty or representation is given concerning such information, which must not be taken as establishing any contractual or other commitment binding upon Grupa Azoty Zakłady Azotowe Kędzierzyn S.A or any of its subsidiary or associated companies. ii ANALYSIS OF ALTERNATIVES CONTENTS 1 SUMMARY .....................................................................................................................................................1 -
SIAM 22, 18-21 April 2006 SIDS INITIAL ASSESSMENT PROFILE CAS Nos. 68526-84-1 Alcohols C8-C10-Iso, C9 Rich 27458-94-2 Isononyl A
SIAM 22, 18-21 April 2006 BE+DE/ICCA SIDS INITIAL ASSESSMENT PROFILE 68526-84-1 Alcohols C8-C10-iso, C9 rich CAS Nos. 27458-94-2 Isononyl alcohol 68526-85-2 Alcohols C9-C11-iso, C10 rich 25339-17-7 Isodecyl alcohol 10042-59-8 2-Propylheptan-1-ol 68526-86-3 Alcohols C11-C14-iso, C13 rich 27458-92-0 Isotridecan-1-ol Chemical Category Name Oxo Alcohols C9 to C13 68526-84-1 CH3-CH(CH3)-(CH2)6-OH (based on a C9 alcohol; general structure; contains essentially methyl branching patterns) 27458-94-2 CH3-CH(CH3)-(CH2)6-OH (general structure; contains various methyl and/or ethyl branching patterns) 68526-85-2 CH3-CH(CH3)-(CH2)7-OH (based on a C10 alcohol; general structure; contains various methyl branching patterns) 25339-17-7 CH3-CH(CH3)-(CH2)7-OH (general structure; contains Structural Formula various methyl branching patterns) 10042-59-8 CH3-(CH2)4-CH(CH2-CH2-CH3)-CH2-OH (based on a C10 alcohol general structure; may also contain methyl branching) 68526-86-3 CH3-CH(CH3)-(CH2)10-OH (based on a C13 alcohol; general structure; contains various methyl branching patterns) 27458-92-0 CH3-CH(CH3)-(CH2)10-OH(general structure; contains various methyl and/or ethyl branching patterns) SUMMARY CONCLUSIONS OF THE SIAR Category Justification The Oxo Alcohols C9 to C13 Category is a family of saturated alcohols that are produced from olefins by the hydroformylation or "oxo" process. Hydroformylation is the reaction of an olefin with carbon monoxide and hydrogen to produce an aldehyde, and its subsequent hydrogenation to the alcohol. -
2-ETHYLHEXANOL (2-EH) MARKET by APPLICATIONS (Plasticizers, 2-EH Acrylate, 2-EH Nitrate, & Others) & GEOGRAPHY — Trends & Forecasts to 2018
2-ETHYLHEXANOL (2-EH) MARKET BY APPLICATIONS (Plasticizers, 2-EH Acrylate, 2-EH Nitrate, & Others) & GEOGRAPHY — Trends & Forecasts to 2018 MarketsandMarkets [email protected] www.marketsandmarkets.com 2-Ethylhexanol (2-EH) Market – By Applications (Plasticizers, 2-EH Acrylate, 2-EH Nitrate, & Others) & Geography — Trends & Forecasts to 2018 MarketsandMarkets is a global market research and consulting company based in the U.S. We publish strategically analyzed market research reports and serve as a business intelligence partner to Fortune 500 companies across the world. MarketsandMarkets also provides multi-client reports, company profiles, databases, and custom research services. MarketsandMarkets covers fourteen industry verticals, including aerospace & defence, advanced materials, automotives and transportation, banking and financial services, biotechnology, chemicals, consumer goods, energy and power, food and beverages, industrial automation, medical devices, pharmaceuticals, semiconductor and electronics, and telecommunications and IT. Copyright © 2014 MarketsandMarkets All Rights Reserved. This document contains highly confidential information and is the sole property of MarketsandMarkets. No part of it may be circulated, copied, quoted, or otherwise reproduced without the approval of MarketsandMarkets. MarketsandMarkets Sample Pages | 2 2-Ethylhexanol (2-EH) Market – By Applications (Plasticizers, 2-EH Acrylate, 2-EH Nitrate, & Others) & Geography — Trends & Forecasts to 2018 1 EXECUTIVE SUMMARY The global 2-EH industry