US5625088.Pdf
Total Page:16
File Type:pdf, Size:1020Kb
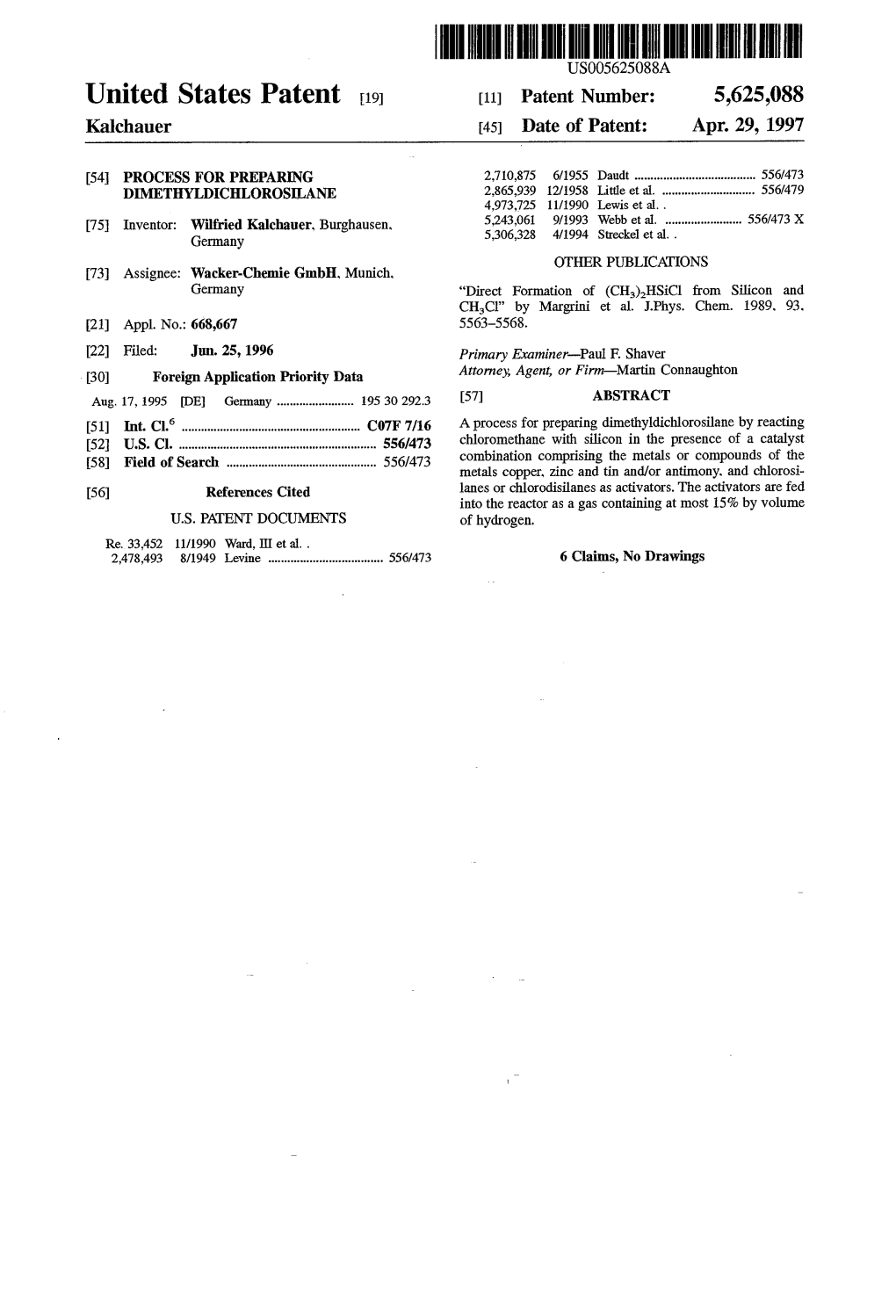
Load more
Recommended publications
-
Progresses in Synthesis and Application of Sic Films: from CVD to ALD and from MEMS to NEMS
micromachines Review Progresses in Synthesis and Application of SiC Films: From CVD to ALD and from MEMS to NEMS Mariana Fraga 1,* and Rodrigo Pessoa 2,* 1 Instituto de Ciência e Tecnologia (ICT), Universidade Federal de São Paulo (Unifesp), São José dos Campos SP 12231-280, Brazil 2 Laboratório de Plasmas e Processos (LPP), Instituto Tecnológico de Aeronáutica (ITA), São José dos Campos SP 12228-900, Brazil * Correspondence: [email protected] (M.F.); [email protected] (R.P.) Received: 2 August 2020; Accepted: 20 August 2020; Published: 24 August 2020 Abstract: A search of the recent literature reveals that there is a continuous growth of scientific publications on the development of chemical vapor deposition (CVD) processes for silicon carbide (SiC) films and their promising applications in micro- and nanoelectromechanical systems (MEMS/NEMS) devices. In recent years, considerable effort has been devoted to deposit high-quality SiC films on large areas enabling the low-cost fabrication methods of MEMS/NEMS sensors. The relatively high temperatures involved in CVD SiC growth are a drawback and studies have been made to develop low-temperature CVD processes. In this respect, atomic layer deposition (ALD), a modified CVD process promising for nanotechnology fabrication techniques, has attracted attention due to the deposition of thin films at low temperatures and additional benefits, such as excellent uniformity, conformability, good reproducibility, large area, and batch capability. This review article focuses on the recent advances in the strategies for the CVD of SiC films, with a special emphasis on low-temperature processes, as well as ALD. In addition, we summarize the applications of CVD SiC films in MEMS/NEMS devices and prospects for advancement of the CVD SiC technology. -
Transport of Dangerous Goods
ST/SG/AC.10/1/Rev.16 (Vol.I) Recommendations on the TRANSPORT OF DANGEROUS GOODS Model Regulations Volume I Sixteenth revised edition UNITED NATIONS New York and Geneva, 2009 NOTE The designations employed and the presentation of the material in this publication do not imply the expression of any opinion whatsoever on the part of the Secretariat of the United Nations concerning the legal status of any country, territory, city or area, or of its authorities, or concerning the delimitation of its frontiers or boundaries. ST/SG/AC.10/1/Rev.16 (Vol.I) Copyright © United Nations, 2009 All rights reserved. No part of this publication may, for sales purposes, be reproduced, stored in a retrieval system or transmitted in any form or by any means, electronic, electrostatic, magnetic tape, mechanical, photocopying or otherwise, without prior permission in writing from the United Nations. UNITED NATIONS Sales No. E.09.VIII.2 ISBN 978-92-1-139136-7 (complete set of two volumes) ISSN 1014-5753 Volumes I and II not to be sold separately FOREWORD The Recommendations on the Transport of Dangerous Goods are addressed to governments and to the international organizations concerned with safety in the transport of dangerous goods. The first version, prepared by the United Nations Economic and Social Council's Committee of Experts on the Transport of Dangerous Goods, was published in 1956 (ST/ECA/43-E/CN.2/170). In response to developments in technology and the changing needs of users, they have been regularly amended and updated at succeeding sessions of the Committee of Experts pursuant to Resolution 645 G (XXIII) of 26 April 1957 of the Economic and Social Council and subsequent resolutions. -
Gas-Phase Chemistry of Methyl-Substituted Silanes in a Hot-Wire Chemical Vapour Deposition Process
University of Calgary PRISM: University of Calgary's Digital Repository Graduate Studies The Vault: Electronic Theses and Dissertations 2013-08-27 Gas-phase Chemistry of Methyl-Substituted Silanes in a Hot-wire Chemical Vapour Deposition Process Toukabri, Rim Toukabri, R. (2013). Gas-phase Chemistry of Methyl-Substituted Silanes in a Hot-wire Chemical Vapour Deposition Process (Unpublished doctoral thesis). University of Calgary, Calgary, AB. doi:10.11575/PRISM/26257 http://hdl.handle.net/11023/891 doctoral thesis University of Calgary graduate students retain copyright ownership and moral rights for their thesis. You may use this material in any way that is permitted by the Copyright Act or through licensing that has been assigned to the document. For uses that are not allowable under copyright legislation or licensing, you are required to seek permission. Downloaded from PRISM: https://prism.ucalgary.ca UNIVERSITY OF CALGARY Gas-phase Chemistry of Methyl-Substituted Silanes in a Hot-wire Chemical Vapour Deposition Process by Rim Toukabri A THESIS SUBMITTED TO THE FACULTY OF GRADUATE STUDIES IN PARTIAL FULFILMENT OF THE REQUIREMENTS FOR THE DEGREE OF DOCTOR OF PHILOSOPHY DEPARTMENT OF CHEMISTRY CALGARY, ALBERTA August, 2013 © Rim Toukabri 2013 Abstract The primary decomposition and secondary gas-phase reactions of methyl- substituted silane molecules, including monomethylsilane (MMS), dimethylsilane (DMS), trimethylsilane (TriMS) and tetramethylsilane (TMS), in hot-wire chemical vapour deposition (HWCVD) processes have been studied using laser ionization methods in combination with time of flight mass spectrometry (TOF-MS). For all four molecules, methyl radical formation and hydrogen molecule formation have been found to be the common decomposition steps on both tungsten (W) and tantalum (Ta) filaments. -
Development of Novel Cycloaliphatic Siloxanes for Thermal
DEVELOPMENT OF NOVEL CYCLOALIPHATIC SILOXANES FOR THERMAL AND UV-CURABLE APPLICATIONS A Dissertation Presented to The Graduate Faculty of the University of Akron In Partial Fulfillment of the Requirements for the Degree Doctor of Philosophy Ruby Chakraborty May, 2008 DEVELOPMENT OF NOVEL CYCLOALIPHATIC SILOXANES FOR THERMAL AND UV-CURABLE APPLICATIONS Ruby Chakraborty Dissertation Approved: Accepted: _____________________________ ______________________________ Advisor Department Chair Dr. Mark D. Soucek Dr. Sadhan C. Jana ______________________________ ______________________________ Committee Member Dean of the College Dr. Sadhan C. Jana Dr. Stephen Cheng ______________________________ ______________________________ Committee Member Dean of the Graduate School Dr. Erol Sancaktar Dr. George R. Newkome ______________________________ ______________________________ Committee Member Date Dr. George G. Chase ______________________________ Committee Member Dr. Chrys Wesdemiotis ii ABSTRACT Siloxanes have been extensively used as additives to modulate surface properties such as surface tension, hydrophobicity/hydrophobicity, and adhesion, etc. Although, polydimethyl -siloxane and polydiphenylsiloxane are the most commonly used siloxanes, the properties are at extremes in terms of glass transition temperature and flexibility. It is proposed that the ability to control the properties in between the these extremes can be provided by cycloaliphatic substitutions at the siloxane backbone. It is expected that this substitution might work due to the intermediate backbone rigidity. In order to achieve the above objectives, a synthetic route was developed to prepare cycloaliphatic (cyclopentane and cyclohexane) silane monomers followed by subsequent polymerization and functionalizations to obtain glycidyl epoxy, aliphatic amine and methacrylate telechelic siloxanes. The siloxanes were either thermally or UV- cured depending on end functionalizations. Chemical characterization of monomers, oligomers and polymers were performed using 1H, 13C, 29Si-NMR, FT-IR and GPC. -
Environmental Risk Assessment Report: Decamethylcyclopentasiloxane
Environmental Risk Assessment Report: Decamethylcyclopentasiloxane Science Report Environmental Risk Assessment: Decamethylcyclopentasiloxane 1 The Environment Agency is the leading public body protecting and improving the environment in England and Wales. It’s our job to make sure that air, land and water are looked after by everyone in today’s society, so that tomorrow’s generations inherit a cleaner, healthier world. Our work includes tackling flooding and pollution incidents, reducing industry’s impacts on the environment, cleaning up rivers, coastal waters and contaminated land, and improving wildlife habitats. Published by: Author(s): Environment Agency, Rio House, Waterside Drive, Aztec West, Brooke D N, Crookes M J , Gray D and Robertson S Almondsbury, Bristol, BS32 4UD Tel: 01454 624400 Fax: 01454 624409 Dissemination Status: www.environment-agency.gov.uk Publicly available / released to all regions ISBN: 978-1-84911-029-7 Keywords: © Environment Agency April 2009 Decamethylcyclosiloxane, siloxane All rights reserved. This document may be reproduced with prior Research Contractor: permission of the Environment Agency. Building Research Establishment Ltd, Bucknalls Lane, Garston, Watford, WD25 9XX. Tel. 01923 664000 The views expressed in this document are not necessarily those of the Environment Agency. Environment Agency’s Project Manager: Steve Robertson, Chemicals Assessment Unit, Red Kite House, This report is printed on Cyclus Print, a 100 per cent recycled Howbery Park, Wallingford OX10 8BD. Tel 01491 828555 stock, which is 100 per cent post consumer waste and is totally chlorine free. Water used is treated and in most cases returned Collaborator(s): to source in better condition than removed. D Gray, Health and Safety Executive Further copies of this report are available from: Product code: The Environment Agency’s National Customer Contact Centre SCHO0309BPQX-E-P by emailing [email protected] or by telephoning 08708 506506. -
Polyorganosiloxanes: Molecular Nanoparticles, Nanocomposites and Interfaces
University of Massachusetts Amherst ScholarWorks@UMass Amherst Doctoral Dissertations Dissertations and Theses November 2017 POLYORGANOSILOXANES: MOLECULAR NANOPARTICLES, NANOCOMPOSITES AND INTERFACES Daniel H. Flagg University of Massachusetts Amherst Follow this and additional works at: https://scholarworks.umass.edu/dissertations_2 Part of the Materials Chemistry Commons, Polymer and Organic Materials Commons, and the Polymer Chemistry Commons Recommended Citation Flagg, Daniel H., "POLYORGANOSILOXANES: MOLECULAR NANOPARTICLES, NANOCOMPOSITES AND INTERFACES" (2017). Doctoral Dissertations. 1080. https://doi.org/10.7275/10575940.0 https://scholarworks.umass.edu/dissertations_2/1080 This Open Access Dissertation is brought to you for free and open access by the Dissertations and Theses at ScholarWorks@UMass Amherst. It has been accepted for inclusion in Doctoral Dissertations by an authorized administrator of ScholarWorks@UMass Amherst. For more information, please contact [email protected]. POLYORGANOSILOXANES: MOLECULAR NANOPARTICLES, NANOCOMPOSITES AND INTERFACES A Dissertation Presented by Daniel H. Flagg Submitted to the Graduate School of the University of Massachusetts in partial fulfillment of the degree requirements for the degree of DOCTOR OF PHILOSOPHY September 2017 Polymer Science and Engineering © Copyright by Daniel H. Flagg 2017 All Rights Reserved POLYORGANOSILOXANES: MOLECULAR NANOPARTICLES, NANOCOMPOSITES AND INTERFACES A Dissertation Presented by Daniel H. Flagg Approved as to style and content by: Thomas J. McCarthy, Chair E. Bryan Coughlin, Member John Klier, Member E. Bryan Coughlin, Head, PS&E To John Null ACKNOWLEDGEMENTS There are countless individuals that I need to thank and acknowledge for getting me to where I am today. I could not have done it alone and would be a much different person if it were not for the support of my advisors, friends and family. -
Synthesis, Recycling, and Modification of Thermoset Silicone Resins Via Fluoride Ion Catalyzed Rearrangement
Synthesis, Recycling, and Modification of Thermoset Silicone Resins via Fluoride Ion Catalyzed Rearrangement by David James Krug III A dissertation submitted in partial fulfillment of the requirements for the degree of Doctor of Philosophy (Macromolecular Science and Engineering) in The University of Michigan 2019 Doctoral Committee: Professor Richard M. Laine, Chair Professor Nicholas A. Kotov Associate Professor Kenichi Kuroda Professor Richard E. Robertson David James Krug III [email protected] ORCID iD: 0000-0003-1584-7872 © David James Krug III 2019 Dedication This dissertation is dedicated to my parents who made everything possible and to my wife who made everything worthwhile Everything I am, I owe to them ii Acknowledgements I could not have embarked on, let alone finished, this dissertation without the help of many wonderful people. First, I would like to thank my advisor, Professor Richard M. Laine, for his guidance, mentorship, and the many opportunities he has given to me over the years. I am also grateful for the support of my committee members Professor Nicholas A. Kotov, Professor Kenichi Kuroda, and Professor Richard E. Robertson. I would also like to thank all past and present members of the Laine Group. In particular, Dr. Michael Z. Asuncion, Dr. Jose Azurdia, Dr. Julien C. Marchal, and Dr. Santy Sulaiman for their direction and patience when I was an undergraduate researcher. And Dr. Eongyu Yi and Dr. Joseph C. Furgal for their support during graduate school. A special thanks to the Macromolecular Science and Engineering Department and the program coordinators over my tenure: Nonna Hamilton, Adam Mael, and Julie Pollak I thank Continental Structural Plastics (CSP) for their financial support of this work. -
Process for Separation of Methyltrichlorosilane from Dimethyldichlorosilane
Europaisches Patentamt (19) European Patent Office Office europeen des brevets (11) EP 0 776 902 A1 (12) EUROPEAN PATENT APPLICATION (43) Date of publication: (51) IntCI.6: C07F7/20 04.06.1997 Bulletin 1997/23 (21) Application number: 96119093.1 (22) Date of filing: 28.11.1996 (84) Designated Contracting States: • Halm, Roland Lee DE FRGBITNL Midland, Michigan 48640 (US) • Mclntyre, Michael Andrew (30) Priority: 29.11.1995 US 564550 Midland, Michigan 48640 (US) • Wilding, Oliver K. (71) Applicant: DOW CORNING CORPORATION Lagrange, Kentucky 40031 (US) Midland, Michigan 48686-0994 (US) (74) Representative: Spott, Gottfried, Dr. (72) Inventors: Patentanwalte • Diaz, Michael Spott, Weinmiller & Partner Lexington, Kentucky 40507 (US) Sendlinger-Tor-Platz 11 80336 Munchen (DE) (54) Process for separation of methyltrichlorosilane from dimethyldichlorosilane (57) A process is disclosed for separating methyl- trichlorosilane from dimethyldichlorosilane in a mixture. The process comprises contacting a mixture comprising methyltrichlorosilane and dimethyldichlorosilane with activated carbon, where the methyltrichlorosilane is selectively adsorbed by the activated carbon. The proc- ess allows for the recovery of a dimethyldichlorosilane fraction reduced in methyltrichlorosilane concentration. The methyltrichlorosilane is recovered by desorption from the activated carbon. The present process is espe- cially useful for removing low levels of methyltrichlorosi- lane present as a contaminate in dimethyldichloro- silane. < CM O <7> CO r»- o Q_ LU Printed by Rank Xerox (UK) Business Services 2.14.7/3.4 EP 0 776 902 A1 Description The present invention is a process for separating methyltrichlorosilane from dimethyldichlorosilane in a mixture. The process comprises contacting a mixture comprising methyltrichlorosilane and dimethyldichlorosilane with activated 5 carbon, where the methyltrichlorosilane is selectively adsorbed by the activated carbon. -
Article in Press
ARTICLE IN PRESS Prog. Polym. Sci. xx (2004) xxx–xxx www.elsevier.com/locate/ppolysci Oligo- and polysilo xanes Yoshimoto Abe*, Takahiro Gunji Department of Pure and Applied Chemistry, Faculty of Science and Technology, Tokyo University of Science, 2641 Yamazaki, Noda, Chiba 278-8510, Japan Received 14 January 2003; revised 5 August 2003; accepted 21 August 2003 Abstract The article reviews the work on the synthesis, properties, and structure of curious oligo- and polysiloxanes which have been done mainly by the authors, referring the related papers. So far as oligosiloxanes, the topic is especially focused on sila- functional siloxanes as the building block for the synthesis of ladder or cube oligosiloxanes, while the another is the polysiloxanes derived from silicic acid and trimethoxysilanes RSi(OMe)3 which are able to form fibers and flexible free- standing films. The review also refers to the new routes for the selective synthesis of sila-functional oligosiloxanes in addition to the reaction control based on the relative reactivity of sila-functional groups. Finally, the application of polysiloxanes as the precursors to ceramics, high performance coatings, and interlayer low dielectric materials are described. q 2003 Elsevier Ltd. All rights reserved. Keywords: Sila-functional oligosiloxanes; New synthetic routes; Siloxanenols; Cube; Ladder; Polysilicic acid esters; Partially silylated silicic acids; Polysilsesquioxanes; Spinnablility; Flexible free-standing films; Ceramic precursor; Coatings; Interlayer low dielectrics Contents 1. Introduction ................................................................... 000 2. Commercially available sila-functional oligosiloxanes . ................................. 000 3. Formation of siloxanes ........................................................... 000 3.1. Various oligo- and polysiloxanes ............................................... 000 3.2. Reactivity of sila-functional groups.............................................. 000 3.3. Siloxane bond formation .................................................... -
United States Patent (19) 11) Patent Number: 4,552,973 Feldner Et Al
United States Patent (19) 11) Patent Number: 4,552,973 Feldner et al. (45) Date of Patent: Nov. 12, 1985 54 PROCESS FOR THE PREPARATION OF 2,647,912 8/1953 Barry et al. ......................... 556/469 DMETHYLDCHLOROSLANE 2,717,257 9/1955 Bluestein ............................. 556/469 (75. Inventors: Kurt Feldner; Wolfgang Grape, both 3,384,652 5/1968 Hamilton ............................ 556/469 of Cologne, Fed. Rep. of Germany 4,477,631 5/1984 Faure et al. ......................... 556/469 Primary Examiner-Paul F. Shaver 73 Assignee: Bayer Aktiengesellschaft, Attorney, Agent, or Firm-Sprung, Horn, Kramer & Leverkusen, Fed. Rep. of Germany Woods (21) Appl. No.: 713,501 57 ABSTRACT 22 Filed: Mar. 19, 1985 A process for the preparation of dimethyldichlorosilane (30) Foreign Application Priority Data from the low-boiling and high-boiling by-products of the direct synthesis of methylchlorosilane, comprising Mar. 23, 1984 (DE) Fed. Rep. of Germany ....... 3410644 reacting methyltrichlorosilane simultaneously with the 51) Int. Cl." ................................................ C07F 7/12 low-boiling components having a high content of 52 U.S.C. .................................................... 556/469 methyl groups and with the high-boiling non-cleavable 58 Field of Search ......................................... 556/469 components, in the presence of a catalyst, at a tempera 56) References Cited ture between about 250 C. and 400 C. and under a U.S. PATENT DOCUMENTS pressure of up to 100 bar. 2,647,136 7/1953 Sauer ................................... 556/469 4 Claims, No Drawings 4,552,973 1. 2 minum chloride which, however, is converted to the PROCESS FOR THE PREPARATION OF known catalyst AlCl3 by hydrogen chloride gas fed DIMETHYTLDICHLOROSLANE simultaneously into the reaction mixture. -
University of California Riverside
UNIVERSITY OF CALIFORNIA RIVERSIDE Thermal Decomposition of Molecules Relevant to Combustion and Chemical Vapor Deposition by Flash Pyrolysis Time-of-Flight Mass Spectrometry A Dissertation submitted in partial satisfaction of the requirements for the degree of Doctor of Philosophy in Chemistry by Jessy Mario Lemieux December 2013 Dissertation Committee: Dr. Jingsong Zhang, Chairperson Dr. Christopher Bardeen Dr. David Bocian Copyright by Jessy Mario Lemieux 2013 The Dissertation of Jessy Mario Lemieux is approved: Committee Chairperson University of California, Riverside ACKNOWLEDGMENTS Professor Jingsong Zhang Dr. Steven Chambreau Dr. Kevin Weber Paul Jones Jeff Lefler Mike Fournier Stan Sheldon Professor Christopher Bardeen Professor David Bocian iv DEDICATION This work is dedicated to my parents who taught me the value of curiosity and learning and have always been there for me. v ABSTRACT OF THE DISSERTATION Thermal Decomposition of Molecules Relevant to Combustion and Chemical Vapor Deposition by Flash Pyrolysis Time-of-Flight Mass Spectrometry by Jessy Mario Lemieux Doctor of Philosophy, Graduate Program in Chemistry University of California, Riverside, December 2013 Dr. Jingsong Zhang, Chairperson Flash pyrolysis coupled with vacuum-ultraviolet photoionization time-of-flight mass spectrometry was used to study the thermal decomposition mechanisms of molecules relevant to fuel combustion and the chemical vapor deposition (CVD) of SiGe, SiC, and GeC. For combustion research, the thermal decomposition of benzyl radical, n- alkanes CnH2n+2 (n = 5-8 and 10), 1-butyl radical, and 1-pentyl radical was performed. Benzyl was confirmed to decompose primarily by ejection of H atom after significant isomerization with loss of methyl observed as a minor decomposition pathway. -
Method for Producing Trichlorosilane Verfahren Zur Herstellung Von Trichlorosilan Procédé De Production De Trichlorosilane
(19) TZZ __T (11) EP 2 546 197 B1 (12) EUROPEAN PATENT SPECIFICATION (45) Date of publication and mention (51) Int Cl.: of the grant of the patent: C01B 33/107 (2006.01) B01D 3/00 (2006.01) 24.08.2016 Bulletin 2016/34 B01D 3/14 (2006.01) (21) Application number: 11753001.4 (86) International application number: PCT/JP2011/001189 (22) Date of filing: 01.03.2011 (87) International publication number: WO 2011/111335 (15.09.2011 Gazette 2011/37) (54) METHOD FOR PRODUCING TRICHLOROSILANE VERFAHREN ZUR HERSTELLUNG VON TRICHLOROSILAN PROCÉDÉ DE PRODUCTION DE TRICHLOROSILANE (84) Designated Contracting States: • TABATA, Masaki AL AT BE BG CH CY CZ DE DK EE ES FI FR GB Joetsu-shi GR HR HU IE IS IT LI LT LU LV MC MK MT NL NO Niigata 942-8601 (JP) PL PT RO RS SE SI SK SM TR (74) Representative: Smaggasgale, Gillian Helen et al (30) Priority: 10.03.2010 JP 2010052548 WP Thompson 138 Fetter Lane (43) Date of publication of application: London EC4A 1BT (GB) 16.01.2013 Bulletin 2013/03 (56) References cited: (73) Proprietor: Shin-Etsu Chemical Co., Ltd. EP-A1- 0 146 148 EP-A2- 2 033 937 Tokyo 100-0004 (JP) EP-A2- 2 036 857 EP-A2- 2 036 859 JP-A- 7 089 709 JP-A- 2004 149 351 (72) Inventors: JP-A- 2007 269 679 JP-A- 2009 062 209 • TANAKA, Shuji JP-A- 2009 062 210 JP-A- 2009 062 212 Joetsu-shi Niigata 942-8601 (JP) Note: Within nine months of the publication of the mention of the grant of the European patent in the European Patent Bulletin, any person may give notice to the European Patent Office of opposition to that patent, in accordance with the Implementing Regulations.