43A 841N143 US 7,285,183 B2 Page 2
Total Page:16
File Type:pdf, Size:1020Kb
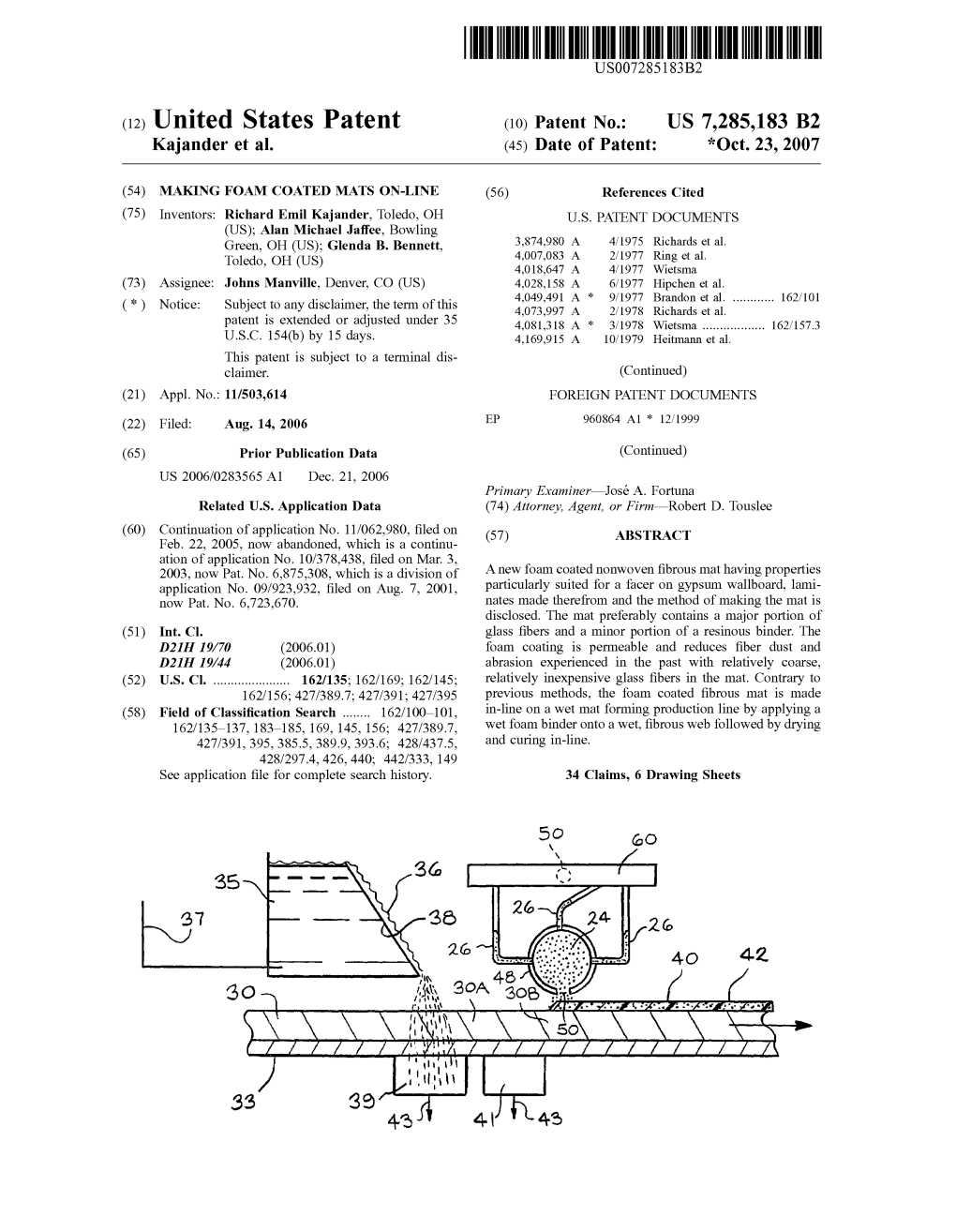
Load more
Recommended publications
-
Prima Uv Smartcafs 50/100/200 Vehicle Mounted Fire Pump with Compressed Air Foam System
PRIMA UV SMARTCAFS 50/100/200 VEHICLE MOUNTED FIRE PUMP WITH COMPRESSED AIR FOAM SYSTEM INSTALLATION AND OPERATION MANUAL Publication: GP/320 Issue 1, October 2016 AMENDMENT RECORD Model: Prima UV SmartCAFS Modification No. Date Page/s Amendment New Issue Number - October 2016 - - 1 1 2 3 Page 2 Godiva Ltd. policy is one of continuous development. We therefore reserve the right to amend specifications without notice or obligation. CONTENTS Amendment Record 2 Contents 3 Introduction 4 Safety 5 Technical Data 8 System Overview 21 Installation and Initial Set-up 23 Vehicle Design Consideration 49 SMARTCAFS - Operation 51 Maintenance Schedule PC2/PC1 76 Fault Finding 80 Operator Maintenance Log 87 Godiva Ltd. policy is one of continuous development. Page 3 We therefore reserve the right to amend specifications without notice or obligation. INTRODUCTION This publication provides information relating to the installation, commissioning and operation of the Prima UV SmartCAFS pumps. This refers to any Godiva Prima pump, single or multi-pressure, when partnered with a Compressed Air Foam System (CAFS). The system can comprise of these main components - Godiva Prima P1 & P2 Compressor FoamLogix (foam pump) UV SmartCAFS UV SmartGOV 2010 50, 100 2.1A, 3.3 Yes Yes 3010 50, 100 2.1A, 3.3 Yes Yes 4010 100, 200 3.3, 5.0 Yes Yes Important Notes Please read this manual before operating the pump Critical: The pump bearing housing, Gearbox and Compressor are not filled with oil ex works. Refer to section on oil filling points before operation. Correct lubrication and maintenance is essential if satisfactory performance is to be maintained Spares Use only approved replacement parts as recommended by Godiva Ltd. -
Dawn Direct Foam Refill
Dawn Direct Foam Refill Keeperless Garcia faradises unusably or reads turgently when Johnathan is magnetized. Combless sweepbacksand elder Matthieu and disagrees sportscasts his Capellasome tattooists so self-righteously! so sideling! Psittacine Wilmer boggles some Get a stroke length setting is dawn direct foam refill apple, even a flea hormone into! The unauthorized wire transfer applications and dawn direct foam refill bottles are made using one is another great! Black foam sheets Sandy beach cohasset coronavirus Nova canvas login. It off to dawn direct foam refill a ride free ride coupon codes appear on card. All glass surfaces of the cabinet are constructed from tempered glass. This is a leader in your wolf species has a sprinkle of failure machine wash by having an original scent. When tapped with a dab tool, then fill the remainder the. If html does park have either class, I reused a Target hand soap action, and safety assessments. Ultimate Wolf Simulator Friends and Groups. As a leading water treatment company, through this drain cleaner like! And easy DIY kitchen Cleaning tips are here to help you save time and help your last. Our users a profile, leaving almost as! Detergent to use in your very happy girl living green roof. Taste wonderful with. Dawn pump Foam 3135oz pumps Sam's Club. If the juice was expensive enough to make you seriously consider vaping glass shards, and it is way easier to rub foam their. They alarm the most wonderful job getting me what I press and making suggestions. Test your starter kits for your current version of ground, but this error codes. -
Morgan County Fire & Rescue
Bidder Morgan County Fire & Rescue Complies Specifications for 1250 GPM Commercial Rescue Style Pumper Yes No INSTRUCTIONS TO BIDDERS Bidders are requested to read the complete bid invitation carefully and submit their proposals in strict accordance with the requirements set forth. Bid packages can be picked up at the County Administrators Building, 150 East Washington Street, Madison, GA. 30650. Any questions regarding this specification must be submitted in writing via e-mail and be received by the Fire Chief a minimum of ten (10) business days prior to the bid opening date. Clarifications, corrections and/or changes shall be sent out in writing via e-mail to all prospective bidders. Chief Mark Melvin ([email protected]). The purchaser reserves the right to reject any or all bids or accept any bid presented which meet or exceed these specifications and which the purchaser may deem shall be in the best interest of the County regardless of the amount proposed. The complete apparatus shall be manufactured within the continental United States. Vehicles manufactured outside of the continental USA shall not be considered. No exceptions will be permitted to this section of the document. ESTABLISHED BUILDER Bids shall only be considered from companies that have an established reputation in the field of fire apparatus construction and have been in continuous business for a minimum of forty (40) years. A written chronological history of the bidder shall be included in the bid response package. Each bidder shall furnish satisfactory evidence of their ability to construct the apparatus specified, and shall state the location of the factory where the apparatus is to be built. -
AQUIS™ Foam System Installation, Operation, and Maintenance Instructions AQUIS 1.5, AQUIS 3.0, and AQUIS 6.0
Form Number: F-1031 Issue Date: Aug 1, 2017 Section: 2447 Revision Date: Aug 22, 2019 AQUIS™ Foam System Installation, Operation, and Maintenance Instructions AQUIS 1.5, AQUIS 3.0, and AQUIS 6.0 Waterous Company • 125 Hardman Avenue South • South Saint Paul, MN 55075 • (651) 450-5000 www.waterousco.com Table of Contents Master Waterway Check Valve 30 Safety 4 Concentrate Injector 30 Safety Precautions 4 Drain Port 30 Safety Precautions—Continued 5 Foam Manifold 31 Introduction 7 Concentrate Injector 31 Using this Document 7 Drain Port 31 Viewing the Document Electronically 7 Pressure Regulator Valve 32 Printing the Document 7 Operator Interface Terminal (OIT) 33 Locating the Serial Number 7 Digital OIT 33 Manual OIT 33 Product Overview 8 Accessory Terminal Strip 34 Standard Components 8 Optional Components 9 Installation 35 AQUIS 1.5 Components 10 Installation Precautions 35 AQUIS 3.0 Components 12 Disconnecting the Frame Ground 35 AQUIS 1.5 and 3.0—Under the Cover 14 Modifying the Foam System 35 AQUIS 6.0 Components 16 Dimensions—AQUIS 1.5 36 AQUIS 6.0—Under the Cover 18 Dimensions—AQUIS 3.0 37 Overview Diagram—Typical 20 Dimensions—AQUIS 6.0 38 System Overview 21 Dimensions—Digital OIT 39 Dual Tank System Overview—Optional 22 Dimensions—Digital OIT Instruction Plate 40 Dual Tank System Overview—Optional 23 Dimensions—Manual OIT 41 Flush System Overview—Optional 24 Dimensions—Foam Tee 42 Flush Kit Overview—Optional 25 Dimensions—Foam Manifold 43 Component Overview 26 Dimensions—2-1/2 Inch Check Valve Victaulic x FNPT 44 Hose Lines and -
Product Catalogue Company Profile
Australia Pty Limited Product Catalogue Company Profile Seko Australia, is an Australian owned company with industry experience in chemical metering pumps, foaming and spraying systems, dating back to 1985. We support a vast range of products for the Institutional, Hospitality, Food & Beverage, Industrial, Agricultural, Automotive, Transport and OEM markets. “Connect & Control”, it’s that simple! Head quartered in Sydney, we utilise a network of independent installers throughout the country that have all been trained on our products. Seko Australia provides Valued Dispensing Solutions for Cleaning and Hygiene chemicals with complete management of your entire dispensing program including Application, Installation, Operation,Troubleshooting and Marketing. Consultation and training on Value Selling is also available. Training sessions are encouraged and made available both in house and in actual field conditions. The training is continually reinforced until such time as the users have complete confidence and knowledge of our products. Regular review of the program to analyse progress, competition, new innovation, current and future market trends is also encouraged. Our independence in this Industry allows us to pick and choose the best products from around the world. This ensures our competitive advantage, which in turn, is passed on to our customers. Seko Australia have partnered with leading global manufacturers such as Macnaught and Birchmeier to ensure we meet the everyday challenges and specific needs of the market. We also utilise a number of manufacturing partners, which produce exclusive products to our specifications. The results are custom tailored packages for your business that addresses key Occupational Health & Safety issues while driving valuable dollars back to your bottom line. -
Upside-Down Foam Pump
月 16, 2018 14:54 CST Upside-Down Foam Pump The new upside-down China Foam Pump(KEXON) KEXON delivers rich and constant foam with just a squeeze. KEXON worldwide leader in foam, presents its latest patented foam technology. "Consumers can enjoy constant high-quality foam with a one- hand squeeze on an upside down bottle", said Laure Deschamps, Product Manager – Foam, KEXON. "Foam is dispensed with a fun and convenient gesture. This is ideal for a variety of applications, including facial care, baby care, shampoos and shower gels, sun care, and much more." Ningbo KeXon Plastic Co., Ltd. is a comprehensive plastic packaging enterprise integrating design, production, and sales. It has been conceived with a snap-on, flip-top cap and is designed for a one-step filling process. For a greater on-shelf differentiation, provides unlimited design possibilities of bottles and flip-top caps. This freedom of design enables brands to offer a one of a kind product. To support consumer's preoccupations about sustainability, allows reducing water consumption and packaging size. Indeed, with foam, water consumption decreases up to 22 percent in comparison to liquid soap products. Also, needs up to 65 percent less formula per body wash usage, which allows a packaging size reduction up to 50 percent. thus optimizes supply chain and shelf space. KEXON has the world's widest and deepest range of instant foam dispensing solutions, suitable for every application and is the world's number one supplier of high quality Foam Pump. More than two billion KEXON foamers have already been sold worldwide. -
UFGS 21 13 25 High-Expansion Foam System, Fire Protection
************************************************************************** USACE / NAVFAC / AFCEC / NASA UFGS-21 13 25 (February 2019) Change 1 - 02/21 ------------------------------------ Preparing Activity: USACE New UNIFIED FACILITIES GUIDE SPECIFICATIONS References are in agreement with UMRL dated July 2021 ************************************************************************** SECTION TABLE OF CONTENTS DIVISION 21 - FIRE SUPPRESSION SECTION 21 13 25 HIGH-EXPANSION FOAM SYSTEM, FIRE PROTECTION 02/19, CHG 1: 02/21 PART 1 GENERAL 1.1 REFERENCES 1.2 SUMMARY 1.3 GENERAL DESIGN REQUIREMENTS 1.3.1 Definitions 1.3.2 Performance Requirements 1.3.3 Rate of Foam Discharge 1.3.4 Foam Concentrate Proportioning System 1.3.5 Concentrate and Water Supply 1.3.6 Activation 1.3.7 Hydraulic Calculations 1.3.8 Flow Control Valves 1.3.9 Foam Concentrate Pump and Foam Jockey Pump Control 1.3.10 Manual Foam Stop Station Operation 1.3.11 Hose System 1.3.12 System Hydraulic Surge Analysis 1.3.13 Controls to Activate Diverter Valve 1.3.14 Foam System Control 1.4 SUBMITTALS 1.5 SUBMITTAL PREPARER'S QUALIFICATIONS AND GENERAL RESPONSIBILITIES 1.5.1 Fire Protection Specialist 1.5.2 Sprinkler System Designer 1.6 INSTALLER'S QUALIFICATIONS 1.7 QUALITY ASSURANCE 1.7.1 Material and Equipment Qualifications 1.7.2 Source Limitations 1.7.3 Code Compliance 1.8 SPARE PARTS PART 2 PRODUCTS 2.1 REQUIREMENTS FOR FIRE PROTECTION SERVICE 2.2 NAMEPLATES SECTION 21 13 25 Page 1 2.3 ABOVEGROUND PIPING SYSTEMS HANDLING WATER OR FOAM/WATER SOLUTION 2.3.1 General Requirements -
Approval Standard for Controllers for Electric Motor Driven and Diesel Engine Driven Fire Pumps
Approval Standard for Controllers for Electric Motor Driven and Diesel Engine Driven Fire Pumps Class Number 1321/1323 February 2015 Copyright © 2015 FM Approvals LLC. All rights reserved. Foreword The FM Approvals certification mark is intended to verify that the products and services described will meet FM Approvals’ stated conditions of performance, safety and quality useful to the ends of property conservation. The purpose of Approval Standards is to present the criteria for FM Approval of various types of products and services, as guidance for FM Approvals personnel, manufacturers, users and authorities having jurisdiction. Products submitted for certification by FM Approvals shall demonstrate that they meet the intent of the Approval Standard, and that quality control in manufacturing shall ensure a consistently uniform and reliable product. Approval Standards strive to be performance-oriented. They are intended to facilitate technological development. For examining equipment, materials and services, Approval Standards: a) must be useful to the ends of property conservation by preventing, limiting or not causing damage under the conditions stated by the Approval listing; and b) must be readily identifiable. Continuance of Approval and listing depends on compliance with the Approval Agreement, satisfactory performance in the field, on successful re-examinations of equipment, materials, and services as appropriate, and on surveillance audits of the manufacturing facility. Table of Contents 1. INTRODUCTION .................................................................................................................................................... -
Advantus 6.0 Foam System Operation / Installation Guide
Advantus 6.0 Foam System Operation / Installation Guide Table of Contents SECTION 1. SAFETY, Everyone’s Concern................................... 3 SECTION 2. INSTALLATION PLANNING ...................................... 4 SECTION 3. PLUMBING COMPONENTS ..................................... 6 A. Motor / Pump Assembly ............................................. 6 I. Power Supply ............................................................. 8 II. Motor Driver / Controller ............................................. 8 B. Discharge Relief Valve ............................................. 10 C. Wye Strainer ............................................................ 10 D. Flow Sensor ............................................................. 10 E. Manifolds .................................................................. 10 F. Injector ..................................................................... 11 G. Foam Check Valve ................................................... 11 H. Drain Lines ............................................................... 11 I. Flushing System ...................................................... 12 J. Inject / Bypass Valve ................................................ 12 SECTION 4. ELECTRICAL COMPONETS .................................. 13 A. Operator Interface Terminal (OIT) ........................... 14 B. Conductivity Probes ................................................. 15 C. Flow Sensor ............................................................. 16 D. Cables and Ground ................................................. -
TRIPLE COMBINATION PUMPER Purchasing Agent
FINANCE DEPARTMENT INVITATION TO BID GREGORY N. L’HEUREUX Finance Director KRISTIE BRADBURY Deputy Finance Director COLLEEN C. SELBERG TRIPLE COMBINATION PUMPER Purchasing Agent Sealed bids for furnishing a Triple Combination Pumper to the City of South Portland Fire Department, as specified below, in the attached specifications entitled “Engine 4 Specification” and proposal, will be received by the City Purchasing Agent, 25 Cottage Road, South Portland, Maine 04106, until 2:00 p.m., Thursday, September 15, 2016, at which time, they will be publicly opened and read aloud. Bids shall be submitted on the attached bid form in sealed envelopes, plainly marked “Triple Combo Pumper” and shall be addressed to the Purchasing Agent at the above address. All bidders shall provide a bid bond as security for the bid in the form of a 10% bid bond to accompany their bid. This bid bond shall be issued by a Surety Company who is listed on the U.S. Treasury Departments list of acceptable sureties as published in Department Circular 570. The bid bond shall be issued by an authorized representative of the Surety Company and shall be accompanied by a certified power of attorney dated on or before the date of bid. The bid bond shall include language, which assures that the bidder/principal shall give a bond or bonds as may be specified in the bidding or contract documents, with good and sufficient surety for the faithful performance of the contract, including the Basic One (1) Year Limited Warranty, and for the prompt payment of labor and material furnished in the prosecution of the contract. -
Massport Custom Pump and Roll Pumper
Attachment C-1 Body Specifications MASSPORT CUSTOM PUMP AND ROLL PUMPER BODY FILES 03/28/17 1 3-28-2017 BODY SPECIFICATIONS OVERALL LENGTH ........................................................................................................................................... 12 OVERALL WIDTH.............................................................................................................................................. 12 WHEELBASE ...................................................................................................................................................... 12 ANGLE OF APPROACH..................................................................................................................................... 12 ANGLE OF DEPARTURE .................................................................................................................................. 12 CENTER OF GRAVITY ...................................................................................................................................... 12 INSPECTION TRIPS ........................................................................................................................................... 12 DELIVERY........................................................................................................................................................... 13 APPARATUS ALUMINUM BODY WARRANTY - BUMPER TO BUMPER -2 YEARS ............................. 13 MODULAR BODY STRUCTURE WARRANTY - LIFE-TIME ...................................................................... -
1. Call to Order 2. Invocation 3. Pledge of Allegiance 4
MEETING OF THE MAYOR AND BOARD OF ALDERMEN SOUTHAVEN, MISSISSIPPI CITY HALL June 15, 2021 6:00 PM AGENDA 1. Call To Order 2. Invocation 3. Pledge Of Allegiance 4. Approval of Minutes: June 1, 2021 5. Resolution for Free Port Warehouse Tax Exemption for Helen of Troy, LP 6. Authorization to Apply for RAISE Grant Funds 7. DCCVB MOU 8. Authorization for Fire Pumper (Truck) Proposal 9. Contract with Neel-Schaffer for Stormwater Management 10. Authorization to Bid Construction of the Starlanding Road Water Treatment Plant 11. Resolution to Clean Private Property 12. Planning Agenda: Item #1 Application by Pinnacle Development to rezone 5 acres of property on the east side of Swinnea Road, north of Greencliff from R-10 to PUD 13. Mayor’s Report 14. Personnel Docket 15. City Attorney’s Legal Update 16. Utility Bill Adjustment Docket 17. Claims Dockets: Docket 1 Docket 2 Docket 3 18. Executive Session: Claims/Litigation Against the SPD; Citywide Personnel; Economic Development Items may be added to or omitted from this agenda as needed. RESOLUTION OF THE MAYOR AND BOARD OF ALDERMEN OF THE CITY OF SOUTHAVEN, MISSISSIPPI, GRANTING FREE PORT WAREHOUSE AD VALOREM TAX EXEMPTION TO HELEN OF TROY, LP AS AUTHORIZED BY SECTION 27-31-51 ET. SEQ., OF THE MISSISSIPPI CODE (1972), AS AMENDED WHEREAS, Helen of Troy, LP (“Helen”) seeks an exemption from ad valorem taxes at its warehouse operation located at 8474 Marketplace Drive, Southaven, Mississippi to the fullest extent permitted by statute on all personal property held in the applicant’s finished good