Study and Characterization of EN AW 6181/6082-T6 and EN AC
Total Page:16
File Type:pdf, Size:1020Kb
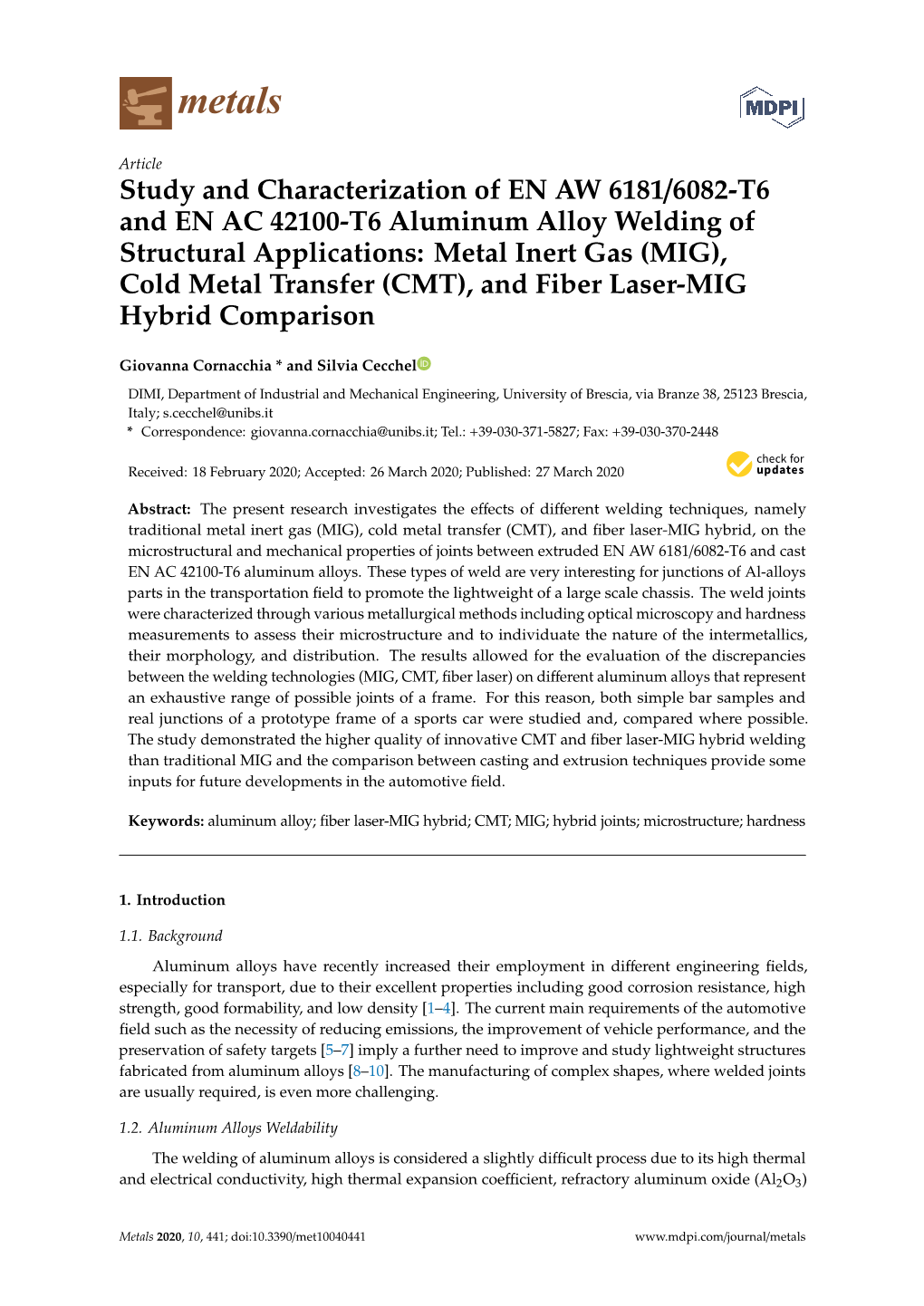
Load more
Recommended publications
-
Product Catalog This Hobart® Catalog Represents an Interim Stage in the Brand Consolidation Process Announced by Hobart Brothers Company in May 2013
Product Catalog This Hobart® catalog represents an interim stage in the brand consolidation process announced by Hobart Brothers Company in May 2013. Included are products branded Tri-Mark® by Hobart alongside Hobart products. In these instances, the products are identical in formulation and manufacturing. Ultimately, Hobart will replace all Tri-Mark options. The catalog now also includes aluminum products formerly under the MAXAL® brand. Why the consolidation and this transition? In one word: simplification. Offering a single Hobart brand allows distributors and end users access to a full line of filler metals, ensuring the right product for the right application — every time. The addition of our collaborative-based service and filler metal expertise helps provide solutions to lower costs and increase productivity. For further information, contact our customer service team at 800-424-1543 or call our Applications Engineering Team at 800-532-2618 or email [email protected] Table of Contents Mild Steel & Low Alloy Stick Electrodes AWS Classifications and Oven Storage and Reconditioning of Stick Electrodes ............................................................... 2 Pipemaster® Pro-60, Pipemaster® 60, Hobart® 610 ...................................................................................................... 3 Pipemaster® 70, Pipemaster® 80, Pipemaster® 90 ......................................................................................................... 4 Hobart® 335A, Hobart® 335C, Hobart® 447A -
Weldability of High Strength Aluminium Alloys
Muyiwa Olabode WELDABILITY OF HIGH STRENGTH ALUMINIUM ALLOYS Thesis for the degree of Doctor of Science (Technology) to be presented with due permission for public examination and criticism in lecture hall 1382 at Lappeenranta University of Technology, Lappeenranta, Finland on the 1st of December, 2015, at noon. Acta Universitatis Lappeenrantaensis 666 Supervisors Professor Jukka Martikainen Laboratory of Welding Technology LUT School of Energy Systems Lappeenranta University of Technology Finland Associate Professor Paul Kah Laboratory of Welding Technology LUT School of Energy Systems Lappeenranta University of Technology Finland Reviewers Professor Leif Karlsson Department of Engineering Science University West Sweden Professor Thomas Boellinghaus Department of Component Safety Federal Institute of Material Research and Testing Germany Opponent Professor Leif Karlsson Department of Engineering Science University West Sweden ISBN 978-952-265-865-4 ISBN 978-952-265-866-1 (PDF) ISSN-L 1456-4491 ISSN 1456-4491 Lappeenrannan teknillinen yliopisto Yliopistopaino 2015 Abstract Muyiwa Olabode Weldability of high strength aluminium alloys Lappeenranta 2015 59 pages Acta Universitatis Lappeenrantaensis 666 Diss. Lappeenranta University of Technology ISBN 978-952-265-865-4, ISBN 978-952-265-866-1 (PDF), ISSN-L 1456-4491, ISSN 1456-4491 The need for reduced intrinsic weight of structures and vehicles in the transportation industry has made aluminium research of interest. Aluminium has properties that are favourable for structural engineering, including good strength-to-weight ratio, corrosion resistance and machinability. It can be easily recycled saving energy used in smelting as compared to steel. Its alloys can have ultimate tensile strength of up to 750 MPa, which is comparable to steel. -
Guidelines for the Welded Fabrication of Nickel-Containing Stainless Steels for Corrosion Resistant Services
NiDl Nickel Development Institute Guidelines for the welded fabrication of nickel-containing stainless steels for corrosion resistant services A Nickel Development Institute Reference Book, Series No 11 007 Table of Contents Introduction ........................................................................................................ i PART I – For the welder ...................................................................................... 1 Physical properties of austenitic steels .......................................................... 2 Factors affecting corrosion resistance of stainless steel welds ....................... 2 Full penetration welds .............................................................................. 2 Seal welding crevices .............................................................................. 2 Embedded iron ........................................................................................ 2 Avoid surface oxides from welding ........................................................... 3 Other welding related defects ................................................................... 3 Welding qualifications ................................................................................... 3 Welder training ............................................................................................. 4 Preparation for welding ................................................................................. 4 Cutting and joint preparation ................................................................... -
Alcotec Aluminum Technical Guide
AlcoTec Aluminum Technical Guide Contents AlcoTec Aluminum Wire & Equipment Technical Guide Table of Contents AlcoTec Aluminum Wire & Equipment Technical Guide ......................................................................................................... 1 Table of Contents ................................................................................................................................................................ 1 Environmental Health and Safety ......................................................................................................................................... 3 Technical Services Heat Treatable & Non-Heat Treatable Base & Fillers ............................................................................................................. 6 Filler Alloys: Chemical Composition Limits & Physical Properties ......................................................................................... 7 Conversion Factors ............................................................................................................................................................ 7 Welded Joint Strength ......................................................................................................................................................... 8 Typical Tensile Properties - Groove Welds ............................................................................................................................ 9 Weld Profiles ..................................................................................................................................................................... -
Part 2, Materials and Welding
RULE REQUIREMENTS FOR MATERIALS AND WELDING 2002 PART 2 American Bureau of Shipping Incorporated by Act of Legislature of the State of New York 1862 Copyright 2001 American Bureau of Shipping ABS Plaza 16855 Northchase Drive Houston, TX 77060 USA Rule Change Notice (2002) The effective date of each technical change since 1993 is shown in parenthesis at the end of the subsection/paragraph titles within the text of each Part. Unless a particular date and month are shown, the years in parentheses refer to the following effective dates: (2000) and after 1 January 2000 (and subsequent years) (1996) 9 May 1996 (1999) 12 May 1999 (1995) 15 May 1995 (1998) 13 May 1998 (1994) 9 May 1994 (1997) 19 May 1997 (1993) 11 May 1993 Listing by Effective Dates of Changes from the 2001 Rules EFFECTIVE DATE 1 January 2001 (based on the contract date for construction) Part/Para. No. Title/Subject Status/Remarks 2-1-1/15.1 Permissible Variations in To clarify that mill scale is to be considered when the Dimensions – Scope plate is produced for compliance with the specified under tolerance Section 2-4-4 Piping To align ABS requirements with IACS UR P2 regarding fabrication of piping and non-destructive examinations, and to outline the requirements for the heat treatment of piping. This Section is applicable only to piping for installation on vessels to be built in accordance with the Rules for Building and Classing Steel Vessels. ii ABS RULE REQUIREMENTS FOR MATERIALS AND WELDING . 2002 PART 2 Foreword For the 1996 edition, the “Rules for Building and Classing Steel Vessels – Part 2: Materials and Welding” was re-titled “Rule Requirements for Materials and Welding – Part 2.” The purpose of this generic title was to emphasize the common applicability of the material and welding requirements in “Part 2” to ABS-classed vessels, other marine structures and their associated machinery, and thereby make “Part 2” more readily a common “Part” of the various ABS Rules and Guides, as appropriate. -
Welding on the Farm: Selecting a Welding Unit for the Farm Or Ranch
Welding on the Farm: Selecting a Welding Unit for the Farm or Ranch Farms encounter a wide variety of welding repairs and projects – having the right welder depends on a lot of factors. Do you have to bring the welder to the work or can you take the work to the welder? Which process (MIG, Stick, or TIG) fits your needs? This article examines all these issues and more. The weather finally cleared, and Wisconsin dairy farmer Al Hoffmann has 385 acres of haylage to cut and store when the chopper blower band for the silo snaps in half. Part of the 3/16 in. steel band has worn paper thin and snapped, and on this Saturday, the nearest replacement band is two days away. Using a 200 amp Millermatic® wire welder, Al saves the band by tack welding it together and then welding on a back-up strip of steel. The repaired chopper blower moves more than 800 tons of haylage in the next few days... ...It's evening milking time. Al is half done with his 185 cows when a hinge breaks on the air gate in the milking parlor. Al resumes milking a few minutes later, after he repairs the gate with a portable Millermatic wire welder that runs off his 115 V household current. "This farm has a lot of old iron, but welders keep my machinery running," Al says. In addition to the two wire welders, Al also uses a 175 amp Stick (shielded metal arc) welder, primarily for hardfacing the bucket on his skid loader or repairing his manure spreader. -
Aluminum Selection Chart
ALUMINUM FILLER Pure Aluminum - METAL GROUPS Aluminum - Copper Aluminum - Magnesium AL-Mg Si AL - Zinc AL - Castings METAL GROUPS METAL SELECTION CHART Aluminum Manganese 2 1100, 1060, 5086, 511.0, 512.0 6061,6005 7005, 7021 413.0, 443.0 319.0, 333.0 BASE 5005, 5050 513.0, 514.0 6063,6070 444.0, 356.0 FILLER 1070, 1080, 2014, 2036 2219 3003, 3004, 5083, 5454 7039, 7046 354.0, 355.0 FILLER BASE Alclad 3003 Alclad 3004 5052, 5652 535.0 6151,6201 A356.0, 357.0 METAL METAL 1350 5456, 5383 7146 METAL METAL WELD METAL PROPERTIES 5154, 5254 6351,6951,6082 359.0 C355.0, 380.0 C S DUC T C P T C STDUC T C P T C STDUC T C P T C STDUC T C P T C S DUC T C P T C S DUC T C P T C S DUC T C P T C S DUC T C P T C S DUC T C P T C S DUC T C P T C710.0,S DUC 711.0T C P T C S DUC T C P T C S DUC T C P T C CRACK SENSITIVITY The Probability of Hot Cracking - this rating is established through use R T ORROE OLORW O R ORROE OLORW O R ORROE OLORW O R ORROE OLORW O R T ORROE OLORW O R T ORROE OLORW O R T ORROE OLORW O R T ORROE OLORW O R T ORROE OLORW O R T ORROE OLORW O R T ORROE OLORW O R T ORROE OLORW O R T ORROE OLORW O R of crack sensitivity curves (Developed by Alcoa) and the consideration of filler metal and base ACREC M H U ACREC M H U A REC M H U ACREC M H U A REC M H U A REC M H U A REC M H U A REC M H U A REC M H U A REC M H U A REC M H U A REC M H U A REC M H U A T P T GH T P T GHC T P T GH T P T GHC T P T GHC T P T GHC T P T GHC T P T GHC T P T GHC T P T GHC T P T GHC T P T GHC T P T GH C metal chemistry combinations. -
Arc Welding and Implanted Medical Devices
A Closer Look SUMMARY Arc Weldi ng and Implanted Medical Devices Electromagnetic Interference (EMI) is the disruption of normal operation of an electronic device when it is in the vicinity of Description an electromagnetic field created by another The electrical signals generated by arc welders may interfere with the proper electronic device. function of ICDs, S-ICDs, CRT-Ds, CRT-Ps or pacing systems. This Electric arc welding refers to a process that interference may have the potential to be interpreted by the device as uses a power supply to create an electric electrical noise or as electrical activity of the heart. Such interference may arc between two metals. result in temporary asynchronous pacing (loss of coordination between the This article describes the potential heart and the device), inhibition of pacing and/or shock therapy (therapy not interaction between the arc welder and delivered when required), or inappropriate tachyarrhythmia therapy (therapy Boston Scientific implantable pacemakers and defibrillators. It also provides delivered when not required). This article refers to Gas Metal Arc Welding— suggestions to minimize potential including Metal Inert Gas (MIG) and Metal Active Gas (MAG)—Manual Metal interactions. Arc (MMA),Tungsten Inert Gas (TIG) welding, and plasma cutting. For questions regarding inductive or spot welding, or welding using current Products Referenced All CRM ICDs, S-ICDs, CRT-Ds, greater than 160 amps, please contact Technical Services. CRT-Ps, and Pacing Systems Products referenced are unregistered or Potential EMI interactions registered trademarks of Boston Scientific Corporation or its affiliates. All other trademarks Electromagnetic interference (EMI) may occur when electromagnetic waves are the property of their respective owners. -
SOLDERING OR UNSOLDERING; WELDING; CLADDING OR PLATING by SOLDERING OR WELDING; CUTTING by APPLYING HEAT LOCALLY, E.G
B23K CPC COOPERATIVE PATENT CLASSIFICATION B PERFORMING OPERATIONS; TRANSPORTING (NOTES omitted) SHAPING B23 MACHINE TOOLS; METAL-WORKING NOT OTHERWISE PROVIDED FOR (NOTES omitted) B23K SOLDERING OR UNSOLDERING; WELDING; CLADDING OR PLATING BY SOLDERING OR WELDING; CUTTING BY APPLYING HEAT LOCALLY, e.g. FLAME CUTTING; WORKING BY LASER BEAM (making metal-coated products by extruding metal B21C 23/22; building up linings or coverings by casting B22D 19/08; casting by dipping B22D 23/04; manufacture of composite layers by sintering metal powder B22F 7/00; arrangements on machine tools for copying or controlling B23Q; covering metals or covering materials with metals, not otherwise provided for C23C; burners F23D) NOTES 1. This subclass covers also electric circuits specially adapted for the purposes covered by the title of the subclass. 2. In this subclass, the following term is used with the meaning indicated: • "soldering" means uniting metals using solder and applying heat without melting either of the parts to be united WARNINGS 1. The following IPC groups are not in the CPC scheme. The subject matter for these IPC groups is classified in the following CPC groups: B23K 35/04 - B23K 35/20 covered by B23K 35/0205 - B23K 35/0294 B23K 35/363 covered by B23K 35/3601 - B23K 35/3618 2. In this subclass non-limiting references (in the sense of paragraph 39 of the Guide to the IPC) may still be displayed in the scheme. Soldering, e.g. brazing, or unsoldering (essentially requiring the use 1/018 . Unsoldering; Removal of melted solder or other of welding machines or welding equipment, see the relevant groups residues for the welding machines or welding equipment) 1/06 . -
Boilermaker B2
BOILERMAKER B2 AWS E8018-B2 H4R WELDING POSITIONS: FEATURES: BENEFITS: • Good arc characteristics • Stable easy to control arc, x-ray clear welds • Low spatter level • Improved weld bead appearance, less clean-up • Quick, easy slag removal • No slag inclusions, increased welding efficiency • Low moisture absorption • Reduces chance of starting porosity • Low hydrogen less than 4 ml/100 g • Resistant to hydrogen induced cracking APPLICATIONS: • Boilers • Tubing TYPE OF CURRENT: Direct Current Electrode Positive (DCEP) or AC RECOMMENDED WELDING TECHNIQUES: ENERAL Electrode positive, work negative (DCEP) or AC G : RC ENGTH Very short arc A L : LAT Angle electrode 10°-15° from 90° F : ERTICAL P Use weaving techniques V -U : ERTICAL OWN Not recommended V -D : OVERHEAD: Use slight weaving motion within the puddle STORAGE: After opening, store in holding oven (220°F to 350°F) until used. RECONDITIONING If exposed to atmosphere for extended periods, reconditioned for one (1) hour at 600°F. TYPICAL WELD METAL PROPERTIES* (Chem Pad): Weld Metal Analysis (%) AWS Spec Carbon (C) 0.05 0.12 max Manganese (Mn) 0.68 0.90 max Sulphur (S) 0.01 0.03 max Phosphorus (P) 0.01 0.03 max Silicon (Si) 0.36 0.80 max Chromium (Cr) 1.12 1.00 - 1.50 Molybdenum (Mo) 0.40 0.40 - 0.65 TYPICAL MECHANICAL PROPERTIES* (As Welded): Stress relieved 1 hr. @ 1275°F AWS Spec Tensile Strength 98,000 psi (673 MPa) 80,000 psi Yield Strength 86,000 psi (592 MPa) 67,000 psi Elongation % in 2” 23% 19% TYPICAL CHARPY V-NOTCH IMPACT VALUES* (As Welded): Stress relieved 1 hr. -
Weld Quality in Aluminium Alloys
Q14003 Examensarbete 30 hp Maj 2014 Weld Quality in Aluminium Alloys Rujira Deekhunthod Abstract Weld Quality in Aluminium Alloys Rujira Deekhunthod Teknisk- naturvetenskaplig fakultet UTH-enheten The aims of this project are to present an understanding in what happens when aluminium-(Al) alloys are welded, and to investigate how the Mg-, Si- and Cr-contents Besöksadress: in AA6005A influence the weld strength and cracking susceptibility. Ångströmlaboratoriet Lägerhyddsvägen 1 It is known that heat from welding affects the mechanical properties (strength) of the Hus 4, Plan 0 material. Different heat cycles during welding are one of the main reasons that the strength varies. Welding can cause various phenomena such as decreased strength, Postadress: porosity, deformation, cracks and corrosion. To minimize these phenomena one has Box 536 751 21 Uppsala to have a balance between the welding parameters, alloy composition and welding fixture setup. Al alloys are sensitive to heat from welding because they have high heat Telefon: conductivity and high thermal expansion coefficient. They also deform easily when the 018 – 471 30 03 material is heated locally. If the material is deformed too much then cracking easily Telefax: occurs. 018 – 471 30 00 This project has examined how the Mg-, Si- and Cr-contents in AA6005A, affect the welded material. A V-joint with MIG welding is used for producing weld samples. For Hemsida: evaluation Vickers micro-hardness, tensile testing, radiography (X-ray), LOM and SEM http://www.teknat.uu.se/student with EBSD and EDS was used. The evaluation focuses on mechanical properties and microstructure. The results show that small variations of Mg-, Si- and Cr-content do not have any clear effects on the welded material. -
Weldability of High Strength Line Pipe Steels
Weldability of High Strength Line Pipe Steels 90 to 100° C preheat eliminates cracking at moderate levels of applied stress when Grade 483 line pipe is misaligned during welding BY T. H. NORTH, A. B. ROTHWELL, A. G. GLOVER AND R. J. PICK ABSTRACT. Full-scale weldability tests why such a situation still exists, and cracking arises (and may be prevented) in showed that Grade 483 line pipe material whether, despite the vastly increased the real world. Weldability tests that are was resistant to cracking up to very high fund of knowledge related to hydrogen- able to simulate, in full-scale, the exact levels of general stress, in the absence of assisted cold cracking, we are still sequence of welding and manipulation misalignment. When pipe misalignment approaching practical problems in the which a pipe may experience in the field was introduced a preheat of 90 to 100°C wrong way. are the only ones in which this relation (194 to 212°F) was necessary to eliminate One of the difficulties which arises in ship is direct. Such tests are expensive cracking at moderate levels of applied addressing the specification of suitably and cumbersome, however, and only stress. crack-resistant materials is the plethora of one pipeline company is known to use Full-scale weldability and laboratory formulae which are proposed for the them on a production basis (Ref. 3, 4). weldability test results correlated well assessment of a material's cracking ten Lastly, it is important to realize that the when using slot testing and WIC restraint dency. While many authorities agree that one "full-scale" test which is habitually cracking tests.