Unite States Patented Aug
Total Page:16
File Type:pdf, Size:1020Kb
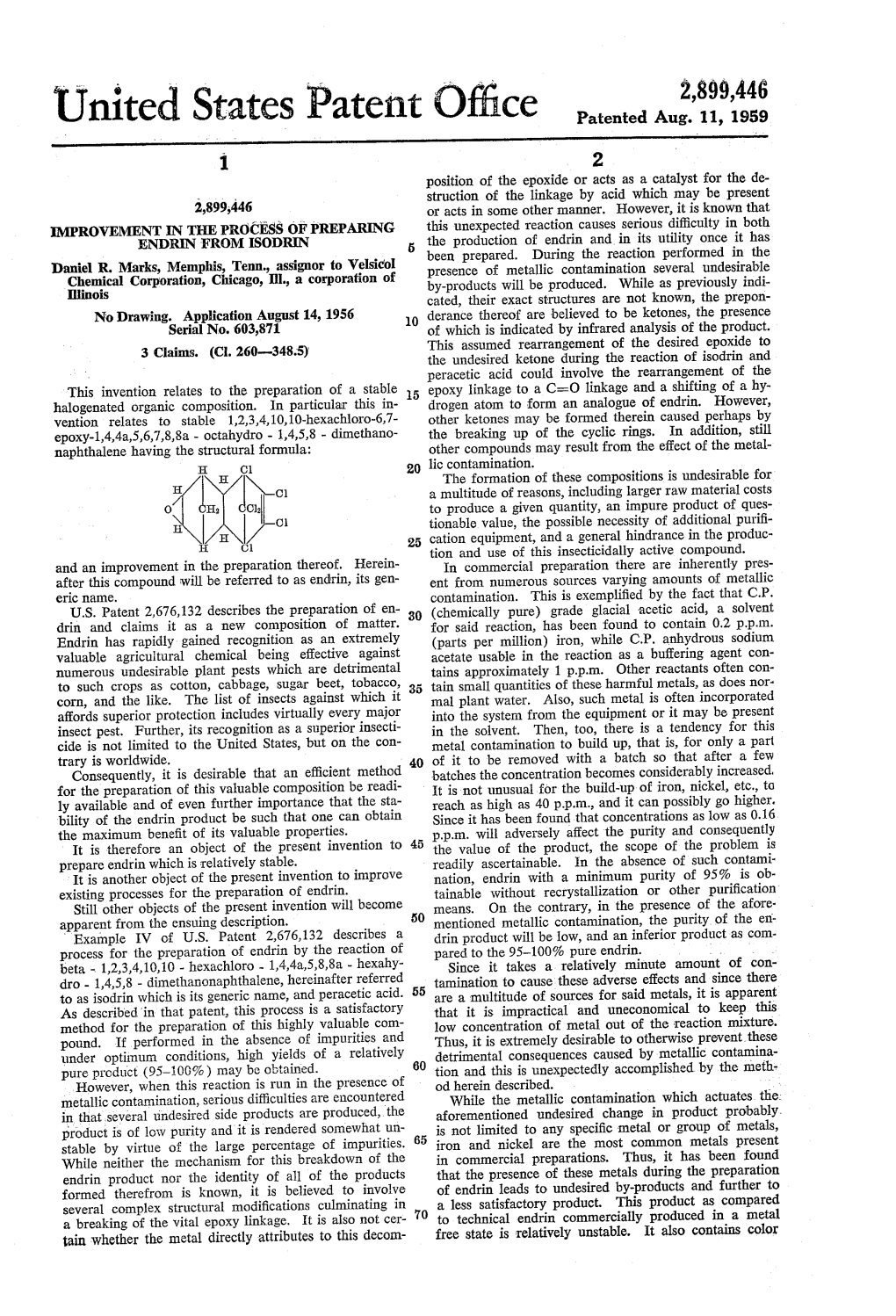
Load more
Recommended publications
-
The Decomposition Kinetics of Peracetic Acid and Hydrogen Peroxide in Municipal Wastewaters
Disinfection Forum No 10, October 2015 The Decomposition Kinetics of Peracetic Acid and Hydrogen Peroxide in Municipal Wastewaters INTRODUCTION Efficient control of microbial populations in municipal wastewater using peracetic acid (PAA) requires an understanding of the PAA decomposition kinetics. This knowledge is critical to ensure the proper dosing of PAA needed to achieve an adequate concentration within the contact time of the disinfection chamber. In addition, the impact of PAA on the environment, post-discharge into the receiving water body, also is dependent upon the longevity of the PAA in the environment, before decomposing to acetic acid, oxygen and water. As a result, the decomposition kinetics of PAA may have a significant impact on aquatic and environmental toxicity. PAA is not manufactured as a pure compound. The solution exists as an equilibrium mixture of PAA, hydrogen peroxide, acetic acid, and water: ↔ + + Acetic Acid Hydrogen Peroxide Peracetic Acid Water PeroxyChem’s VigorOx® WWT II Wastewater Disinfection Technology contains 15% peracetic acid by weight and 23% hydrogen peroxide as delivered. Although hydrogen peroxide is present in the formulation, peracetic acid is considered to be the active component for disinfection1 in wastewater. There have been several published studies investigating the decomposition kinetics of PAA in different water matrices, including municipal wastewater2-7. Yuan7 states that PAA may be consumed in the following three competitive reactions: 1. Spontaneous decomposition 2 CH3CO3H à 2 CH3CO2H + O2 Eq (1) 2. Hydrolysis CH3CO3H + H2O à CH3CO2H + H2O2 Eq (2) 3. Transition metal catalyzed decomposition + CH3CO3H + M à CH3CO2H + O2 + other products Eq (3) At neutral pH’s, both peracetic acid and hydrogen peroxide can be rapidly consumed by these reactions7 (hydrogen peroxide will decompose to water and oxygen via 2H2O2 à 2H2O + O2). -
Peracetic Acid Processing
Peracetic Acid Processing Identification Chemical Name(s): CAS Number: peroxyacetic acid, ethaneperoxic acid 79-21-0 Other Names: Other Codes: per acid, periacetic acid, PAA NIOSH Registry Number: SD8750000 TRI Chemical ID: 000079210 UN/ID Number: UN3105 Summary Recommendation Synthetic / Allowed or Suggested Non-Synthetic: Prohibited: Annotation: Synthetic Allowed (consensus) Allowed only for direct food contact for use in wash water. Allowed as a (consensus) sanitizer on surfaces in contact with organic food. (consensus) From hydrogen peroxide and fermented acetic acid sources only. (Not discussed by processing reviewers--see discussion of source under Crops PAA TAP review.) Characterization Composition: C2H4O3. Peracetic acid is a mixture of acetic acid (CH3COOH) and hydrogen peroxide (H2O2) in an aqueous solution. Acetic acid is the principle component of vinegar. Hydrogen peroxide has been previously recommended by the NOSB for the National List in processing (synthetic, allowed at Austin, 1995). Properties: It is a very strong oxidizing agent and has stronger oxidation potential than chlorine or chlorine dioxide. Liquid, clear, and colorless with no foaming capability. It has a strong pungent acetic acid odor, and the pH is acid (2.8). Specific gravity is 1.114 and weighs 9.28 pounds per gallon. Stable upon transport. How Made: Peracetic acid (PAA) is produced by reacting acetic acid and hydrogen peroxide. The reaction is allowed to continue for up to ten days in order to achieve high yields of product according to the following equation. O O || || CH3-C-OH + H2O2 CH3C-O-OH + H2O acetic acid hydrogen peroxyacetic peroxide acid Due to reaction limitations, PAA generation can be up to 15% with residual levels of hydrogen peroxide (up to 25%) and acetic acid (up to 35%) with water up to 25%. -
Peracetic Acid
Regulation (EU) No 528/2012 concerning the making available on the market and use of biocidal products Evaluation of active substances Assessment Report Peracetic acid Product-types 11 and 12 (Preservatives for liquid cooling and processing systems) (Slimicides) August 2016 Finland Peracetic acid Product-types 11 and 12 August 2016 CONTENTS 1. STATEMENT OF SUBJECT MATTER AND PURPOSE ........................................................ 2 1.1. Procedure followed ............................................................................................. 2 1.2. Purpose of the assessment report ....................................................................... 2 2. OVERALL SUMMARY AND CONCLUSIONS ..................................................................... 4 2.1. Presentation of the Active Substance .................................................................. 4 2.1.1. Identity, Physico-Chemical Properties & Methods of Analysis ................. 4 2.1.2. Intended Uses and Efficacy ..................................................................... 7 2.1.3. Classification and Labelling ..................................................................... 8 2.2. Summary of the Risk Assessment ....................................................................... 9 2.2.1. Human Health Risk Assessment .............................................................. 9 2.2.1.1. Hazard identification ................................................................................... 9 2.2.1.2. Effects assessment ................................................................................... -
Particularly Hazardous Substances
Particularly Hazardous Substances In its Laboratory Standard, OSHA requires the establishment of additional protections for persons working with "Particularly Hazardous Substances" (PHS). OSHA defines these materials as "select" carcinogens, reproductive toxins and acutely toxic materials. Should you wish to add: explosive, violently reactive, pyrophoric and water-reactve materials to this category, the information is included. Carbon nanotubes have also been added due to their suspected carcinogenic properties. This table is designed to assist the laboratory in the identification of PHS, although it is not definitively conclusive or entirely comprehensive. *Notes on the proper use of this table appear on page 12. 1 6 5 2 3 4 Substance CAS National Toxicity National Program Carcinogen Toxin Acute Regulated OSHA Carcinogen Group IARC Carcinogen Toxin Reproductive Violently Reactive/ Explosive/Peroxide Forming/Pyrophoric A-a-C(2-Amino-9H-pyrido[2,3,b]indole) 2648-68-5 2B Acetal 105-57-7 yes Acetaldehyde 75-07-0 NTP AT 2B Acrolein (2-Propenal) 107-02-8 AT Acetamide 126850-14-4 2B 2-Acetylaminofluorene 53-96-3 NTP ORC Acrylamide 79-06-6 NTP 2B Acrylyl Chloride 814-68-6 AT Acrylonitrile 107-13-1 NTP ORC 2B Adriamycin 23214-92-8 NTP 2A Aflatoxins 1402-68-2 NTP 1 Allylamine 107-11-9 AT Alkylaluminums varies AT Allyl Chloride 107-05-1 AT ortho-Aminoazotoluene 97-56-3 NTP 2B para-aminoazobenzene 60-09-3 2B 4-Aminobiphenyl 92-67-1 NTP ORC 1 1-Amino-2-Methylanthraquinone 82-28-0 NTP (2-Amino-6-methyldipyrido[1,2-a:3’,2’-d]imidazole) 67730-11-4 2B -
Peracetic Acid Bleaching CH CO H
Peracetic Acid Bleaching CH3CO3H Introduction of Bleaching Bleaching is a chemical decoloration and delignification process carried out on various types of pulp. DliDelignifi cati on Removal of the chromophores At in dus tr ia l scal e, bl eachi ng i s perf ormed b y chl ori ne, chl ori ne dioxide, oxygen, hydrogen peroxide, ozone and peracetic acid. Effic iency: ClO2 = Cl2 = O3 >CH3COOOH > H2O2 >O> O2 Often bleaching chemicals are wasted in secondary reactions. D. Lachenal and C. Chirat, Cellulose Chem. Technol., 39, 5-6, 511-156 (2005) 2 Electron Exchange Theory Ring opening of the aromatic units necessitates the exchange of 4 e - # of e- can be exchanged per bleaching molecule - + O3 + 6 e + 6 H → 3 H2O - + - CCOlO2 + 55e e + 4 H → Cl + 2 H2O2 - + O2 + 4 e + 4 H → 2 H2O - + H2O2 + 2 e + 2 H → 2 H2O - + CH3COOOH + 2 e + 2 H → CH3COOH + H2O # of e- exchanged per molecule decreases in the following order: O3 > ClO2 > O2 > H2O2 = CH3COOOH D. Lachenal and C. Chirat, Cellulose Chem. Technol., 39, 5-6, 511-156 (2005) 3 Actual Electron Exchange - ClO2 and O3 100 g un bleac he d SW k raf t pul p, k appa # f rom 30 to ~ 4 -5 - 2.3% ClO2 (0.034 mole) on pulp: 0.034 x 5 = 0.17 e is exchanged - 14%1.4% O3 (0.03 mole)on pulp: 0 .03 x 6 = 018e0.18 e is exchanged Chemicals % consumed1 Kappa number * ClO2 2.3 4.5 O3 1.5 3.5 O3 1.4 5.0 O3 1.3 6.5 1Chemicals consumed are shown as % on pulp. -
List of Extremely Hazardous Substances
Emergency Planning and Community Right-to-Know Facility Reporting Compliance Manual List of Extremely Hazardous Substances Threshold Threshold Quantity (TQ) Reportable Planning (pounds) Quantity Quantity (Industry Use (pounds) (pounds) CAS # Chemical Name Only) (Spill/Release) (LEPC Use Only) 75-86-5 Acetone Cyanohydrin 500 10 1,000 1752-30-3 Acetone Thiosemicarbazide 500/500 1,000 1,000/10,000 107-02-8 Acrolein 500 1 500 79-06-1 Acrylamide 500/500 5,000 1,000/10,000 107-13-1 Acrylonitrile 500 100 10,000 814-68-6 Acrylyl Chloride 100 100 100 111-69-3 Adiponitrile 500 1,000 1,000 116-06-3 Aldicarb 100/500 1 100/10,000 309-00-2 Aldrin 500/500 1 500/10,000 107-18-6 Allyl Alcohol 500 100 1,000 107-11-9 Allylamine 500 500 500 20859-73-8 Aluminum Phosphide 500 100 500 54-62-6 Aminopterin 500/500 500 500/10,000 78-53-5 Amiton 500 500 500 3734-97-2 Amiton Oxalate 100/500 100 100/10,000 7664-41-7 Ammonia 500 100 500 300-62-9 Amphetamine 500 1,000 1,000 62-53-3 Aniline 500 5,000 1,000 88-05-1 Aniline, 2,4,6-trimethyl- 500 500 500 7783-70-2 Antimony pentafluoride 500 500 500 1397-94-0 Antimycin A 500/500 1,000 1,000/10,000 86-88-4 ANTU 500/500 100 500/10,000 1303-28-2 Arsenic pentoxide 100/500 1 100/10,000 1327-53-3 Arsenous oxide 100/500 1 100/10,000 7784-34-1 Arsenous trichloride 500 1 500 7784-42-1 Arsine 100 100 100 2642-71-9 Azinphos-Ethyl 100/500 100 100/10,000 86-50-0 Azinphos-Methyl 10/500 1 10/10,000 98-87-3 Benzal Chloride 500 5,000 500 98-16-8 Benzenamine, 3-(trifluoromethyl)- 500 500 500 100-14-1 Benzene, 1-(chloromethyl)-4-nitro- 500/500 -
(12) Patent Application Publication (10) Pub. No.: US 2016/0372276 A1 HAN Et Al
US 20160372276A1 (19) United States (12) Patent Application Publication (10) Pub. No.: US 2016/0372276 A1 HAN et al. (43) Pub. Date: Dec. 22, 2016 (54) A PRECIOUS METAL SWITCH CONTACT C2.5D 5/48 (2006.01) COMPONENT AND ITS PREPARATION C2.5D 3/48 (2006.01) METHOD C2.5D 3/46 (2006.01) C2.5D 5/02 (2006.01) (71) Applicant: NANTONG MEMTECH HIH II/04 (2006.01) TECHNOLOGIES CO., LTD, C23C 8/42 (2006.01) Nantong (CN) (52) U.S. Cl. CPC ................ H01H I/02 (2013.01); H0IH II/04 (72) Inventors: Huisheng HAN, Nantong (CN); (2013.01); C23C 18/1605 (2013.01); C23C HONGMEI ZHANG, NANTONG 18/1689 (2013.01); C23C 18/42 (2013.01); (CN); YANG DING, NANTONG (CN); C25D 3/48 (2013.01); C25D 3/46 (2013.01); ZHIHONG DONG, NANTONG (CN); C25D 5/022 (2013.01); C25D 5/48 (2013.01) CHENG HUANG, NANTONG (CN) (57) ABSTRACT (21) Appl. No.: 14/896,403 This invention discloses a preparation method for precious metal Switching contact components by means of plating (22) PCT Filed: Sep. 15, 2014 masking, plating and etching processes. The plating masking PCT/CN2014/090913 process is performed by using a plating mask ink with or (86). PCT No.: without a photo exposure machine. Plating of precious S 371 (c)(1), metals is performed by electroless plating or electro plating (2) Date: Dec. 7, 2015 methods. Etching is carried out with etching solutions con taining weak organic acids, weak inorganic acids or acidic (30) Foreign Application Priority Data buffering agents. Improvement of the etched Surface gloss and prevention of the side etching are realized with the Sep. -
The Use of Peracetic Acid As a “Pre-Oxidant” for Drinking Water Applications
Disinfection Forum No. 18, September 2017 The Use of Peracetic Acid as a “Pre-Oxidant” for Drinking Water Applications BACKGROUND Chlorination as a technology for drinking water disinfection has significantly reduced the incidence of human disease and is one of the most significant contributions to the improvement of human health over the past century. Chlorine’s ability to provide a stable residual concentration makes it suitable as a drinking water disinfectant at the point of use. However, natural organic matter in the raw water being treated and disinfected at the drinking water treatment plant may interact with the residual chlorine to form compounds classified as disinfection by-products (DBPs). The most commonly employed disinfectants are chlorine, chlorine dioxide and ozone – each of which can generate a variety of DBPs. Many DBPs have been identified as potential cancer-causing agents, and include trihalomethanes (THMs) and haloacetic acids (HAAs). Examples of THMS and HAAs include: chloroform, dibromochloromethane, bromoform, trichloracetic acid, monchloracetic acid and monobromoacetic acid. Peracetic acid (PAA) has gained momentum in the United States as a primary wastewater disinfection technology and alternative to chlorine. PAA has low residual toxicity, does not form harmful DBPs and has minimal impact on the environment. While the lack of a stable residual reduces its environmental impact post wastewater treatment, this characteristic decreases its values as a terminal drinking water disinfection technology – PAA residual at the point of use would be impractical to maintain. However, PAA may potentially be used in a disinfection treatment train approach as an early stage disinfection chemistry coupled with other methods such as membrane filtration, ozone and UV. -
Tg-Pesticides-E.Pdf
Technical guidelines on the environmentally sound management of wastes consisting of, containing or contaminated with the pesticides aldrin, chlordane, dieldrin, endrin, heptachlor, hexachlorobenzene (HCB), mirex or toxaphene or with HCB as an industrial chemical K0760095 230307 Contents I. Introduction .............................................................................................................5 A. Scope .............................................................................................................5 B. Description, production, use and wastes ......................................................................5 1. Aldrin .............................................................................................................5 (a) Description ..........................................................................................5 (b) Production...........................................................................................5 (c) Use.......................................................................................................6 2. Chlordane.........................................................................................................6 (a) Description ..........................................................................................6 (b) Production...........................................................................................6 (c) Use.......................................................................................................6 3. Dieldrin............................................................................................................7 -
2.2.Uncatalysed Formation of Peracetic Acid from Hydrogen Peroxide and Acetic Acid
Peroxide Reactions of Environmental Relevance in Aqueous Solution MELOD MOHAMED Ali UNIS PhD 2010 i Peroxide Reactions of Environmental Relevance in Aqueous Solution MELOD MOHAMED Ali UNIS PhD 2010 ii Peroxide Reactions of Environmental Relevance in Aqueous Solution A thesis submitted in partial fulfilment of the requirements of the University of Northumbria at Newcastle For the degree of Doctor of Philosophy Research undertaken in the School of Applied Sciences at Northumbria University Oct 2010 iii ACKNOWLEDGEMENTS First and foremost, all praise be to God, Lord of the Universe, the most beneficent, the most merciful who has blessed me through my life with health, patience and ability to pursue and complete this work. I would like to express utmost appreciation to my supervisors Dr. Michael Deary and Dr. Martin Davies for their guidance and cooperation throughout this work, and also special thanks to Dr Michael Deary for his patience, endless support, excellent guidance, and helpful comments throughout my PhD writing. He has always provided valuable, challenging and constructive comments which have encourage me to improve my research skills and demonstrate the work precisely. I would like to thanks Mr Gary Askwith, for his assistance during this research work. I am particularly indebted to the people of my country Libya, who provided me with the opportunity to continue higher studies. I would like to acknowledge my gratitude to the Ministry of Education for the financial support to accomplish this study, which otherwise was impossible to be achieved. Therefore, I wish to be able to repay at least a portion of this debt to my home country. -
(Rqs) for EPCRA Section 302(A)(2) Extremely Hazardous Substances
§ 355.50 40 CFR Ch. I (7–1–01 Edition) of this paragraph, a transportation-re with the requirements of § 355.40 shall lated release means a release during be subject to civil penalties of up to transportation, or storage incident to $25,000 for each day during which the transportation if the stored substance violation continues, in accordance with is moving under active shipping papers section 325(b)(2) of the Act. In the case and has not reached the ultimate con of a second or subsequent violation, signee. any such person may be subject to civil [52 FR 13395, Apr. 22, 1987, as amended at 54 penalties of up to $75,000 for each day FR 22543, May 24, 1989; 55 FR 30188, July 24, the violation continues, in accordance 1990; 63 FR 13475, Mar. 19, 1998; 64 FR 13115, with section 325(b)(2) of the Act. Mar. 17, 1999] (c) Criminal penalties. Any person who knowingly and willfully fails to pro- § 355.50 Penalties. vide notice in accordance with § 355.40 (a) Civil penalties. Any person who shall, upon conviction, be fined not fails to comply with the requirements more than $25,000 or imprisoned for not of § 355.40 shall be subject to civil pen more than two (2) years, or both (or, in alties of up to $25,000 for each violation the case of a second or subsequent con in accordance with section 325(b)(1) of viction, shall be fined not more than the Act. $50,000 or imprisoned for not more than (b) Civil penalties for continuing viola five (5) years, or both) in accordance tions. -
Chemical Compatibility Storage Group
CHEMICAL SEGREGATION Chemicals are to be segregated into 11 different categories depending on the compatibility of that chemical with other chemicals The Storage Groups are as follows: Group A – Compatible Organic Acids Group B – Compatible Pyrophoric & Water Reactive Materials Group C – Compatible Inorganic Bases Group D – Compatible Organic Acids Group E – Compatible Oxidizers including Peroxides Group F– Compatible Inorganic Acids not including Oxidizers or Combustible Group G – Not Intrinsically Reactive or Flammable or Combustible Group J* – Poison Compressed Gases Group K* – Compatible Explosive or other highly Unstable Material Group L – Non-Reactive Flammable and Combustible, including solvents Group X* – Incompatible with ALL other storage groups The following is a list of chemicals and their compatibility storage codes. This is not a complete list of chemicals, but is provided to give examples of each storage group: Storage Group A 94‐75‐7 2,4‐D (2,4‐Dichlorophenoxyacetic acid) 94‐82‐6 2,4‐DB 609-99-4 3,5-Dinitrosalicylic acid 64‐19‐7 Acetic acid (Flammable liquid @ 102°F avoid alcohols, Amines, ox agents see SDS) 631-61-8 Acetic acid, Ammonium salt (Ammonium acetate) 108-24-7 Acetic anhydride (Flammable liquid @102°F avoid alcohols see SDS) 79‐10‐7 Acrylic acid Peroxide Former 65‐85‐0 Benzoic acid 98‐07‐7 Benzotrichloride 98‐88‐4 Benzoyl chloride 107-92-6 Butyric Acid 115‐28‐6 Chlorendic acid 79‐11‐8 Chloroacetic acid 627‐11‐2 Chloroethyl chloroformate 77‐92‐9 Citric acid 5949-29-1 Citric acid monohydrate 57-00-1 Creatine 20624-25-3