1785-1998 September 1998
Total Page:16
File Type:pdf, Size:1020Kb
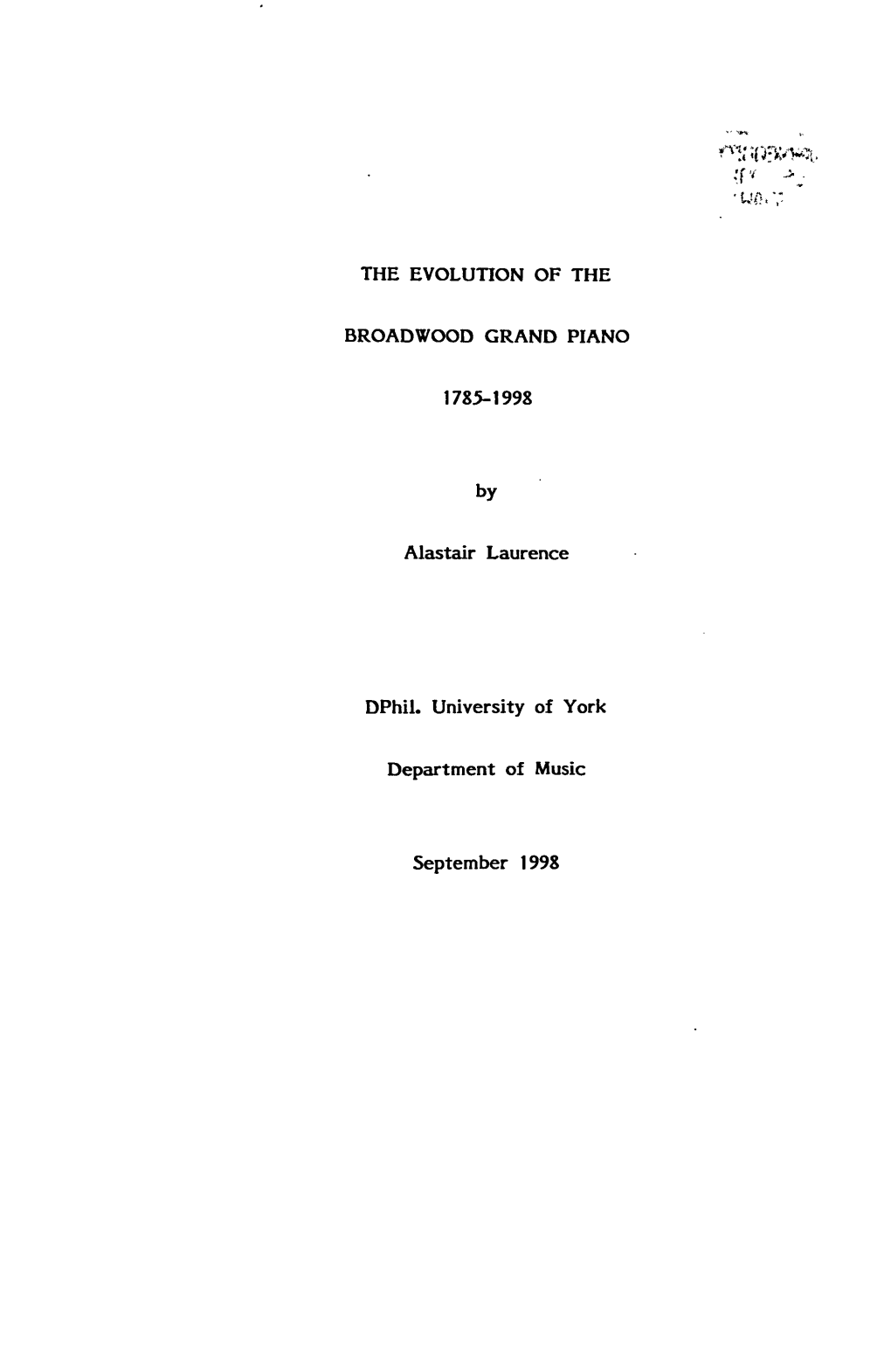
Load more
Recommended publications
-
Index (Complete)
Sample page from Pianos Inside Out. Copyright © 2013 Mario Igrec. 527 Index composite parts 375 rails, repairing 240 facing off 439 Numerics compressed 68 rebuilding, overview 325 grooved, effects on tuning 132 105 System 336 diagram 64 regulating 166 reducing height of 439 16th Tone Piano 94 Double Repetition in verticals 77 regulating on the bench 141 replacing 436 1867 Exposition in Paris 13 double-escapement 5, 12 regulation, effects on tuning 129 to rebuild or replace 326 3M 267, 338 dropped 68, 113, 140, 320 removing 136 Air microfinishing film 202 English 9 removing from keyboard 154 dehumidifying 85 409 89 escapement of jack 76 repairing 240 humidifying 86 Fandrich 68 repetition, speed of 77 Air conditioner 86, 328 frame stability in verticals, Schwander 77 Albert Steinway 13, 76 A inspecting 191 single-escapement 4 Alcohol 144, 145, 147, 155, 156, 158, Abel 66, 71, 72, 340, 383 geometry 273, 303 spread 149, 280, 282, 287, 315 161, 179, 182, 191, 213, 217, 221, hammers 72, 384 geometry troubleshooter 304 tape-check 11 237, 238, 264, 265, 337, 338, 352, Naturals 71 grand, inserting into the piano troubleshooters 304 353, 356, 437, 439, 449, 478 Abrasive cord 338 137 Tubular Metallic Frame 66, 68 as sizing agent 215, 491 Abrasives, in buffing compounds grand, rebuilding 373 vertical 68 as solvent for shellac 480 364 grand, regulating 166 vertical, development of 15 as suspension for blue chalk 449 ABS grand, removing 136 vertical, Double Repetition 77 as suspension for chalk 240, 364, Carbon 17, 66 grand, removing from keyboard vertical, -
Cds by Composer/Performer
CPCC MUSIC LIBRARY COMPACT DISCS Updated May 2007 Abercrombie, John (Furs on Ice and 9 other selections) guitar, bass, & synthesizer 1033 Academy for Ancient Music Berlin Works of Telemann, Blavet Geminiani 1226 Adams, John Short Ride, Chairman Dances, Harmonium (Andriessen) 876, 876A Adventures of Baron Munchausen (music composed and conducted by Michael Kamen) 1244 Adderley, Cannonball Somethin’ Else (Autumn Leaves; Love For Sale; Somethin’ Else; One for Daddy-O; Dancing in the Dark; Alison’s Uncle 1538 Aebersold, Jamey: Favorite Standards (vol 22) 1279 pt. 1 Aebersold, Jamey: Favorite Standards (vol 22) 1279 pt. 2 Aebersold, Jamey: Gettin’ It Together (vol 21) 1272 pt. 1 Aebersold, Jamey: Gettin’ It Together (vol 21) 1272 pt. 2 Aebersold, Jamey: Jazz Improvisation (vol 1) 1270 Aebersold, Jamey: Major and Minor (vol 24) 1281 pt. 1 Aebersold, Jamey: Major and Minor (vol 24) 1281 pt. 2 Aebersold, Jamey: One Dozen Standards (vol 23) 1280 pt. 1 Aebersold, Jamey: One Dozen Standards (vol 23) 1280 pt. 2 Aebersold, Jamey: The II-V7-1 Progression (vol 3) 1271 Aerosmith Get a Grip 1402 Airs d’Operettes Misc. arias (Barbara Hendricks; Philharmonia Orch./Foster) 928 Airwaves: Heritage of America Band, U.S. Air Force/Captain Larry H. Lang, cond. 1698 Albeniz, Echoes of Spain: Suite Espanola, Op.47 and misc. pieces (John Williams, guitar) 962 Albinoni, Tomaso (also Pachelbel, Vivaldi, Bach, Purcell) 1212 Albinoni, Tomaso Adagio in G Minor (also Pachelbel: Canon; Zipoli: Elevazione for Cello, Oboe; Gluck: Dance of the Furies, Dance of the Blessed Spirits, Interlude; Boyce: Symphony No. 4 in F Major; Purcell: The Indian Queen- Trumpet Overture)(Consort of London; R,Clark) 1569 Albinoni, Tomaso Concerto Pour 2 Trompettes in C; Concerto in C (Lionel Andre, trumpet) (also works by Tartini; Vivaldi; Maurice André, trumpet) 1520 Alderete, Ignacio: Harpe indienne et orgue 1019 Aloft: Heritage of America Band (United States Air Force/Captain Larry H. -
Radio 3 Listings for 12 – 18 June 2010 Page 1
Radio 3 Listings for 12 – 18 June 2010 Page 1 of 11 SATURDAY 12 JUNE 2010 Symphony No.22 in E flat, 'The Philosopher' Tom Service meets conductor Jonathan Nott, principal Amsterdam Bach Soloists conductor of the Bamberg Symphony Orchestra, and talks to SAT 01:00 Through the Night (b00smvg2) tenor Ian Bostridge and director David Alden about performing Jonathan Swain presents rarities, archive and concert recordings 4:35 AM Janacek. Robin Holloway talks about the appeal for from Europe's leading broadcasters Abel, Carl Friedrich (1723-1787) contemporary composers of Schumann's music, plus a report on Sonata No.6 in G major (Op.6 No.6) classical club nights. 1:01 AM Karl Kaiser (transverse flute), Susanne Kaiser (harpsichord) Wagner, Richard (1813-1883) Wie Lachend sie mir Lieder singen ( Tristan und Isolde, Act 1) 4:45 AM SAT 13:00 The Early Music Show (b00sq42f) Brigit Nilsson (Isolde), Irene Dalis (Brangäne), Metropolitan Rore, Cipriano de (c1515-1565) Ghostwriter: The Story of Henri Desmarest Opera Orchestra, Karl Böhm (conductor) Fera gentil The Consort of Musicke, Anthony Rooley (director) Henry Desmarest was obviously a talented musican and 1:10 AM composer, first boy page and then musician in Louis XIV's Wagner, Richard (1813-1883) 4:51 AM court, he began ghost-writing Grands Motets for one of the Amfortas! Die Wunde! (Parsifal, Act 1) Berlioz, Hector (1803-1869) chapel directors Nicholas Goupillet when he was in his early Jon Vickers (Parsifal), Christa Ludwig (Kundry), Metropolitan Le Carnaval romain - overture (Op.9) twenties. -
Pedal in Liszt's Piano Music!
! Abstract! The purpose of this study is to discuss the problems that occur when some of Franz Liszt’s original pedal markings are realized on the modern piano. Both the construction and sound of the piano have developed since Liszt’s time. Some of Liszt’s curious long pedal indications produce an interesting sound effect on instruments built in his time. When these pedal markings are realized on modern pianos the sound is not as clear as on a Liszt-time piano and in some cases it is difficult to recognize all the tones in a passage that includes these pedal markings. The precondition of this study is the respectful following of the pedal indications as scored by the composer. Therefore, the study tries to find means of interpretation (excluding the more frequent change of the pedal), which would help to achieve a clearer sound with the !effects of the long pedal on a modern piano.! This study considers the factors that create the difference between the sound quality of Liszt-time and modern instruments. Single tones in different registers have been recorded on both pianos for that purpose. The sound signals from the two pianos have been presented in graphic form and an attempt has been made to pinpoint the dissimilarities. In addition, some examples of the long pedal desired by Liszt have been recorded and the sound signals of these examples have been analyzed. The study also deals with certain aspects of the impact of texture and register on the clarity of sound in the case of the long pedal. -
Ellen Fullman
A Compositional Approach Derived from Material and Ephemeral Elements Ellen Fullman My primary artistic activity has been focused coffee cans with large metal mix- around my installation the Long String Instrument, in which ing bowls filled with water and rosin-coated fingers brush across dozens of metallic strings, rubbed the wires with my hands, ABSTRACT producing a chorus of minimal, organ-like overtones, which tipping the bowl to modulate the The author discusses her has been compared to the experience of standing inside an sound. I wanted to be able to tune experiences in conceiving, enormous grand piano [1]. the wire, but changing the tension designing and working with did nothing. I knew I needed help the Long String Instrument, from an engineer. At the time I was an ongoing hybrid of installa- BACKGROUND tion and instrument integrat- listening with great interest to Pau- ing acoustics, engineering In 1979, during my senior year studying sculpture at the Kan- line Oliveros’s album Accordion and and composition. sas City Art Institute, I became interested in working with Voice. I could imagine making mu- sound in a concrete way using tape-recording techniques. This sic with this kind of timbre, playing work functioned as soundtracks for my performance art. I also created a metal skirt sound sculpture, a costume that I wore in which guitar strings attached to the toes and heels of my Fig. 1. Metal Skirt Sound Sculpture, 1980. (© Ellen Fullman. Photo © Ann Marsden.) platform shoes and to the edges of the “skirt” automatically produced rising and falling glissandi as they were stretched and released as I walked (Fig. -
Navigating, Coping & Cashing In
The RECORDING Navigating, Coping & Cashing In Maze November 2013 Introduction Trying to get a handle on where the recording business is headed is a little like trying to nail Jell-O to the wall. No matter what side of the business you may be on— producing, selling, distributing, even buying recordings— there is no longer a “standard operating procedure.” Hence the title of this Special Report, designed as a guide to the abundance of recording and distribution options that seem to be cropping up almost daily thanks to technology’s relentless march forward. And as each new delivery CONTENTS option takes hold—CD, download, streaming, app, flash drive, you name it—it exponentionally accelerates the next. 2 Introduction At the other end of the spectrum sits the artist, overwhelmed with choices: 4 The Distribution Maze: anybody can (and does) make a recording these days, but if an artist is not signed Bring a Compass: Part I with a record label, or doesn’t have the resources to make a vanity recording, is there still a way? As Phil Sommerich points out in his excellent overview of “The 8 The Distribution Maze: Distribution Maze,” Part I and Part II, yes, there is a way, or rather, ways. But which Bring a Compass: Part II one is the right one? Sommerich lets us in on a few of the major players, explains 11 Five Minutes, Five Questions how they each work, and the advantages and disadvantages of each. with Three Top Label Execs In “The Musical America Recording Surveys,” we confirmed that our readers are both consumers and makers of recordings. -
Andrew Nolan Viennese
Restoration report South German or Austrian Tafelklavier c. 1830-40 Andrew Nolan, Broadbeach, Queensland. copyright 2011 Description This instrument is a 6 1/2 octave (CC-g4) square piano of moderate size standing on 4 reeded conical legs with casters, veneered in bookmatched figured walnut in Biedermeier furniture style with a single line of inlaid stringing at the bottom of the sides and a border around the top of the lid. This was originally stained red to resemble mahogany and the original finish appearance is visible under the front lid flap. The interior is veneered in bookmatched figured maple with a line of dark stringing. It has a wrought iron string plate on the right which is lacquered black on a gold base with droplet like pattern similar to in concept to the string plates of Broadwood c 1828-30. The pinblock and yoke are at the front of the instrument over the keyboard as in a grand style piano and the bass strings run from the front left corner to the right rear corner. The stringing is bichord except for the extreme bass CC- C where there are single overwound strings, and the top 1 1/2 octaves of the treble where there is trichord stringing. The top section of the nut for the trichords is made of an iron bar with brass hitch pins inserted at the top, this was screwed and glued to the leading edge of the pinblock. There is a music rack of walnut which fits into holes in the yoke. The back of this rack is hinged in the middle and at the bottom. -
A Harpsichord Odyssey
A Harpsichord Odyssey (II) by Edgar Hunt Major Benton Fletcher had acquired Old Devonshire House in 1934 when it was in a very poor state, cleaned it up, stripping off several coats of wall paper and plaster to reveal the original wood panelling, and made it a fit home for his collections. Built in the seventeenth century, it had been the town house of the Cavendish family, one of whom once rode his horse up the broad staircase for a wager. Now it was to provide the perfect setting for the Major's collection of early keyboard instruments and antique furniture. The Major himself, besides having been a soldier (he served in the Boer War and World War I), an egyptologist who had worked with Flinders Petrie and an artist (among other things he illustrated Braybrook's Pepys* Diary for Dent), had built up a collection of The first floor 'Great Chamber'. harpsichords and other early keyboard Old Devonshire House. (Photo: Country Life) instruments as he feared lest their tone quality instruments to be available for concerts (one might otherwise be lost to future generations. was regularly used for Bach performances at He strongly disapproved of the way the Westminster Abbey) and for students to modern harpsichord was going, with its metal practice on at 6d (=2ip) an hour. A Mr Irwin frame, row of pedals and lack of sonority, and Hinchliffe ARCM, who helped with the wanted his restoration and maintenance of his harpsichords, was available to teach, and Mrs Frances Jackson, his housekeeper, acted as curator. But the Major also wanted Old Devonshire House to become a centre for early music where anyone interested could also study the viola da gamba or recorder and join in ensembles with harpsichord continue. -
NOVEMBER 2020 COMPLIMENTARY GUIDE Catskillregionguide.Com
Catskill Mountain Region NOVEMBER 2020 COMPLIMENTARY GUIDE catskillregionguide.com WELCOME HOME TO THE CATSKILL MOUNTAINS! With a Special Section: Visit Woodstock November 2020 • GUIDE 1 2 • www.catskillregionguide.com IN THIS ISSUE www.catskillregionguide.com VOLUME 35, NUMBER 11 November 2020 PUBLISHERS Peter Finn, Chairman, Catskill Mountain Foundation Sarah Finn, President, Catskill Mountain Foundation EDITORIAL DIRECTOR, CATSKILL MOUNTAIN FOUNDATION Sarah Taft ADVERTISING SALES Barbara Cobb Steve Friedman CONTRIBUTING WRITERS & ARTISTS Benedetta Barbaro, Darla Bjork, Rita Gentile, Liz Innvar, Joan Oldknow, Jeff Senterman, Sarah Taft, Margaret Donsbach Tomlinson & Robert Tomlinson ADMINISTRATION & FINANCE Candy McKee On the cover: The Ashokan Reservoir. Photo by Fran Driscoll, francisxdriscoll.com Justin McGowan & Emily Morse PRINTING Catskill Mountain Printing Services 4 A CATSKILLS WELCOME TO THE GRAF PIANO DISTRIBUTION By Joan Oldknow & Sarah Taft Catskill Mountain Foundation 12 ART & POETRY BY RITA GENTILE EDITORIAL DEADLINE FOR NEXT ISSUE: November 10 The Catskill Mountain Region Guide is published 12 times a year 13 TODAY BUILDS TOMORROW: by the Catskill Mountain Foundation, Inc., Main Street, PO Box How to Build the Future We Want: The Fear Factor 924, Hunter, NY 12442. If you have events or programs that you would like to have covered, please send them by e-mail to tafts@ By Robert Tomlinson catskillmtn.org. Please be sure to furnish a contact name and in- clude your address, telephone, fax, and e-mail information on all correspondence. For editorial and photo submission guidelines 14 VISIT WOODSTOCK send a request via e-mail to [email protected]. The liability of the publisher for any error for which it may be held legally responsible will not exceed the cost of space ordered WELCOME HOME TO THE CATSKILL MOUNTAINS! or occupied by the error. -
Piano Manufacturing an Art and a Craft
Nikolaus W. Schimmel Piano Manufacturing An Art and a Craft Gesa Lücker (Concert pianist and professor of piano, University for Music and Drama, Hannover) Nikolaus W. Schimmel Piano Manufacturing An Art and a Craft Since time immemorial, music has accompanied mankind. The earliest instrumentological finds date back 50,000 years. The first known musical instrument with fibers under ten sion serving as strings and a resonator is the stick zither. From this small beginning, a vast array of plucked and struck stringed instruments evolved, eventually resulting in the first stringed keyboard instruments. With the invention of the hammer harpsichord (gravi cembalo col piano e forte, “harpsichord with piano and forte”, i.e. with the capability of dynamic modulation) in Italy by Bartolomeo Cristofori toward the beginning of the eighteenth century, the pianoforte was born, which over the following centuries evolved into the most versitile and widely disseminated musical instrument of all time. This was possible only in the context of the high level of devel- opment of artistry and craftsmanship worldwide, particu- larly in the German-speaking part of Europe. Since 1885, the Schimmel family has belonged to a circle of German manufacturers preserving the traditional art and craft of piano building, advancing it to ever greater perfection. Today Schimmel ranks first among the resident German piano manufacturers still owned and operated by Contents the original founding family, now in its fourth generation. Schimmel pianos enjoy an excellent reputation worldwide. 09 The Fascination of the Piano This booklet, now in its completely revised and 15 The Evolution of the Piano up dated eighth edition, was first published in 1985 on The Origin of Music and Stringed Instruments the occa sion of the centennial of Wilhelm Schimmel, 18 Early Stringed Instruments – Plucked Wood Pianofortefa brik GmbH. -
Trevor Pinnock Journey
TREVOR PINNOCK JOURNEY Two Hundred Years of Harpsichord Music TREVOR PINNOCK JOURNEY Two Hundred Years of Harpsichord Music ANTONIO DE CABEZÓN (c.1510–1566) GIROLAMO FRESCOBALdi (1583–1643) 1. Diferencias sobre 15. Toccata nona ................................ 4:32 ‘El canto del caballero’ .................. 3:10 16. Balletto primo e secondo .............. 5:39 from Toccate d’intavolatura di cimbalo et WILLIAM BYRD (c.1540–1623) organo,1637 2. The Carman’s Whistle .................. 3:58 GEORGE FRIDERIC HAndel (1685–1759) THOMAS TaLLIS (c.1505–1585) 17. Chaconne in G major, HWV 435 ... 6:36 3. O ye tender babes ........................ 2:37 DOMENICO SCARLAtti (1685–1757) JOHN Bull (1562/3–1628) Three Sonatas in D major, K. 490–92 4. The King’s Hunt ............................ 3:25 18. Sonata, K. 490: Cantabile ............ 5:02 JAN PIETERSZOON SWEELINCK 19. Sonata, K. 491: Allegro ................ 4:57 (1562–1621) 20. Sonata, K. 492: Presto ................. 4:17 5. Variations on ‘Mein junges Leben hat ein End’, SwWV 324 .............. 6:10 Total Running Time: 68 minutes JOHANN SEBASTIAN BACh (1685–1750) French Suite No. 6 in E major, BWV 817 6. Prélude ......................................... 1:31 7. Allemande .................................... 3:28 8. Courante ...................................... 1:47 9. Sarabande ................................... 3:22 10. Gavotte ........................................ 1:07 11. Polonaise ...................................... 1:20 12. Bourrée ........................................ 1:41 13. -
UCL CMC Newsletter No.5
UCL Chamber Music Club Newsletter No.5 October 2015 In this issue: Welcome to our newsletter Welcome to the fifth issue of the Chamber Mu- Cohorts of muses, sic Club Newsletter and its third year of pub- unaccompanied lication. We offer a variety of articles, from a composers and large survey of last season’s CMC concerts – now a ensembles – a view on the regular feature – to some reflections, informed sixty-third season - by both personal experience and scholarship, page 2 on the music of Sibelius and Nielsen (whose 150th anniversaries are celebrated in the first UCLU Music Society concert of our new season). In the wake of UC- concerts this term - Opera’s production last March of J.C. Bach’s page 8 Amadis de Gaule we have a brief review and two articles outlining the composer’s biogra- UCOpera’s production of phy and putting him in a wider context. The Amadis de Gaule, CMC concert last February based on ‘the fig- UCL Bloomsbury Theatre, ure 8’ has prompted an article discussing some 23-28 March 2015 - aspects of the topic ‘music and numbers’. Not page 9 least, our ‘meet the committee’ series continues with an interview with one of our newest and Meet the committee – youngest committee members, Jamie Parkin- Jamie Parkinson - son. page 9 We hope you enjoy reading the newslet- A biographical sketch of ter. We also hope that more of our readers Johann Christian Bach will become our writers! Our sixth issue is (1735-82): composer, scheduled for February 2016, and any material impresario, keyboard on musical matters – full-length articles (max- player and freemason - imum 3000 words), book or concert reviews – page 12 will be welcome.