The Arup Journal
Total Page:16
File Type:pdf, Size:1020Kb
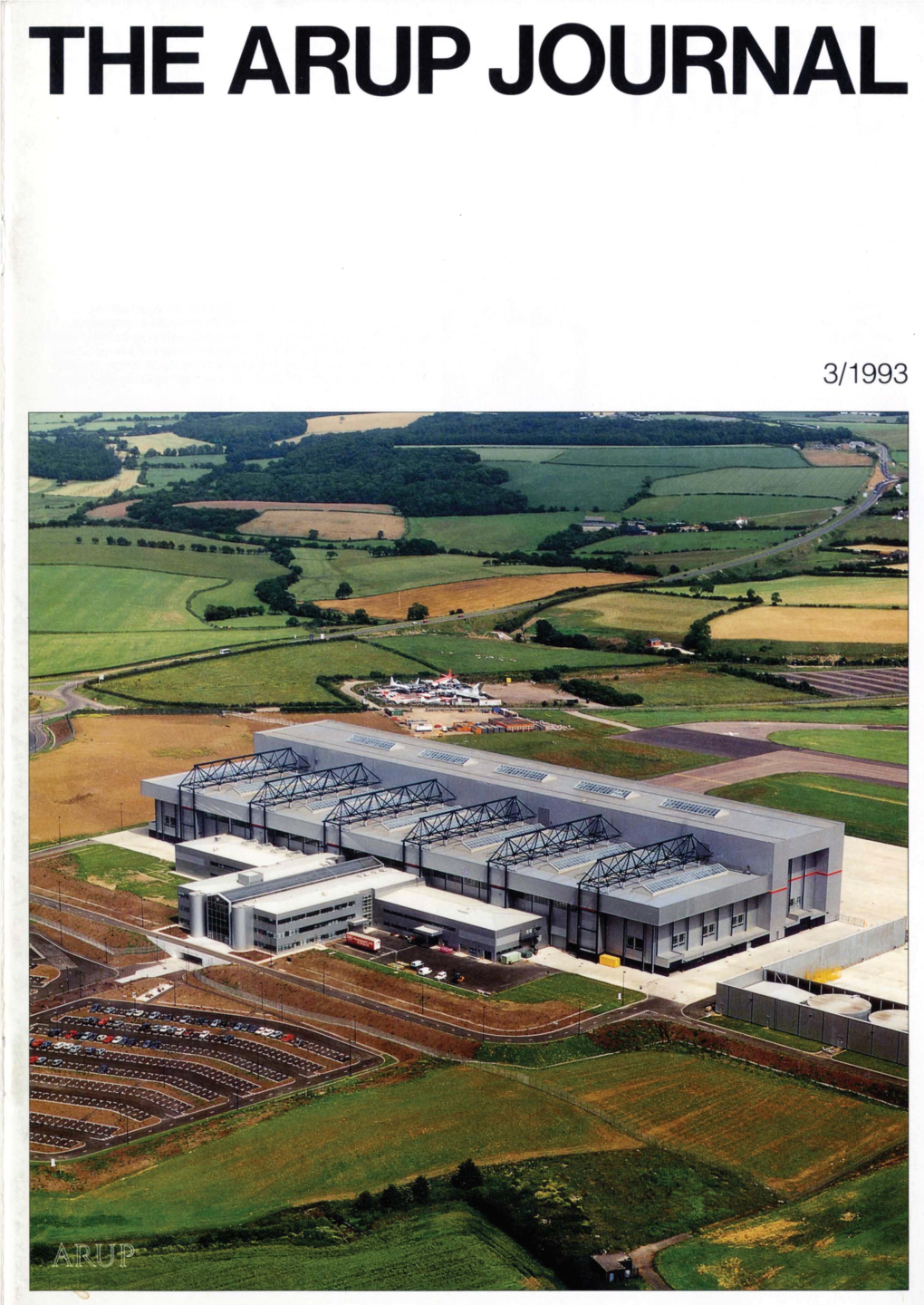
Load more
Recommended publications
-
The Belford Neighborhood Revitalization Plan
The Belford Neighborhood Revitalization Plan Rutgers, The State University of New Jersey Edward J. Bloustein School of Planning and Public Policy Fall 2012 Members: Rich Bartholomew, Andrew Chew, Charlotte Colon-Alvarez, Greg Contente, Kevin Dillon, Jonathan Kristofich, Kayla Malsbury, Emily Manz, Marisa Rodriguez-McGill, & Jonathan Scharff 1 Table of Contents Mission Statement This plan, the Belford Neighborhood Revitalization Plan, was prepared as the final outcome of a graduate student studio class at The Edward J. Bloustein School of Planning and Public Policy at Executive Summary .............................................................4 Rutgers, the State University of New Jersey. The studio met from September through December TheNeighborhood Belford Revitalization Plan of 2012 and was tasked by Middletown Township with developing a document that would refine, TheNeighborhood Belford Revitalization Plan Neighborhood Context .............................................................8 build upon, and put into action the Port of Belford Economic Feasibility Study and Conceptual Relation to Other Plans .............................................................38 Development Plan completed in 2009 by the Louis Berger Group for the Township of Middletown. During the formation of the Belford Neighborhood Revitalization plan, Hurricane Sandy struck New Research Process .............................................................45 Jersey. This event inflenced both the objectives and the strategies contained within the plan. Goals -
COUNTRY SECTION United States Fishery Products
Validity date from COUNTRY United States 22/01/2021 00499 SECTION Fishery products Date of publication 28/07/2007 List in force Approval number Name City Regions Activities Remark Date of request 1000025102 GET SEAFOOD, INC. Winter Haven Florida PP 08/04/2013 1000025909 Fagan Alligator Products, Inc. Dade City Florida PP 1000084596 Sea-Trek Enterprises, Inc. East Greenwich Rhode Island PP O! 10/07/2008 1000112376 Pontchartrain Blue Crab Slidell Louisiana PP 14/04/2010 1000113172 Fishermen's Ice & Bait, Inc. Madeira Beach Florida PP 1000113708 Beck's Smokery Pompano Beach Florida PP 1000113902 Colorado Boxed Beef Co. Port Everglades Florida CS 16/11/2011 1000114005 D & D Seafood Corporation Marathon Florida PP 1000114027 BAMA SEA PRODUCTS St. Petersburg Florida PP 1000114048 Moon's Seafood Company W. Melbourne Florida PP O! 1000114049 Glanbia Performance Nutrition (Manufacturing), Inc., Florida Sunrise Florida PP 13/10/2017 Facility 1000114069 Placeres & Sons Seafood Hialeah Florida PP 1000114070 Webb's Seafood, Inc. Youngstown Florida PP 14/10/2009 1000114156 Cox's Wholesale Seafood, Inc. Tampa Florida PP 1000114170 Kings Seafood, Inc. Port Orange Florida PP 1 / 59 List in force Approval number Name City Regions Activities Remark Date of request 1000114326 Optimus, Inc. Dba Marky's Miami Florida PP 1000115645 AMERIQUAL FOODS LLC Evansville Indiana PP 06/02/2019 1000115810 Henriksen Fisheries, Inc Sister Bay Wisconsin PP 1000117125 RB Manufacturing LLC Salt Lake City Utah PP 08/01/2015 1000120312 Stauber Performance Ingredients, Inc. Florida New York PP 08/08/2019 1000120556 Plenus Group, Inc. Lowell Massachusetts PP 06/05/2008 1000120753 GARBO LOBSTER LLC Groton Connecticut PP 17/10/2016 1000121950 True World Foods, NY LLC Elizabeth New Jersey PP Aq 1000122358 Lamonica Fine Foods, Inc. -
Environmental Management Plan
Environmental Management Plan Exigrade Feeds Pty (Ltd.) Luderitz, Namibia Endorsed By: Jacobus Smit Endorsed By: Operational Director Signature: ____________________________ Date: 1/06/2019 ENVIRONMENTAL MANAGEMENT PLAN Exigrade Feeds, Luderitz EXECUTIVE SUMMARY Exigrade Feeds Pty Ltd is an existing fishmeal plant, situated on the premises of Pescanova Seafood factory in Luderitz, Namibia. The aim of this Environmental Management Plan (EMP) is to identify and address any environmental risks associated with the facility. As the facility is within an industrial area in the Fishing Harbour of Luderitz, it is surrounded by similar industrial facilities. Due to the nature and location of the development, impact can however be expected on the surrounding environment, see summary of potential impact below. Regular environmental performance monitoring will continue and be updated on an continues basis, to ensure compliance and that corrective measures be taken if necessary. The fishing industry is one of the biggest contributors to the Namibian economy and is a major contributor to employment in the coastal area. The existing operations at Exigrade Feeds is contributing to the local economy by increased productivity and value addition, through continued employment, and by providing opportunities for other local businesses for service delivery. The major concerns related to the operational activities at the Exigrade Feeds premises are that of air quality, waste production, fuel storage and consumption, and surface water impacts. All relevant local regulations and accepted best practices should always be adhered to. Noise and air pollution should always meet the minimum requirements to prevent air pollution and not to cause a nuisance to nearby receptors. -
The Final Report and Action Plan Can Be Downloaded Here
Kevin Irons Aquaculture and Aquatic Nuisance Species Program Manager Illinois Department of Natural Resources One Natural Resources Way Springfield, IL 62702-1271 Email: [email protected] Phone: 217.557.0719 Gina Behnfeldt Vice President, Economic Development Services Tetra Tech One Oxford Valley, Suite 200 Langhorne, PA 19047 Email: [email protected] Phone: 215.702.4094 ILLINOIS DEPARTMENT OF NATURAL RESOURCES ASIAN CARP BUSINESS PROCESS ANALYSIS | FINAL REPORT AND ACTION PLAN TABLE OF CONTENTS EXECUTIVE SUMMARY ............................................................................................................................................1 METHODOLOGY ........................................................................................................................................................1 Steering Committee ..............................................................................................................................................1 Asian Carp Regional Coordinating Committee (ACRCC) .....................................................................................2 Research ..............................................................................................................................................................2 Recommendation Development.......................................................................................................................... 10 FINDINGS ................................................................................................................................................................ -
Aquaculture and Marine Mammals: Co-Existence Or Conflict?
P ART I CHAPTER 11 AQUACULTURE AND MARINE MAMMALS: CO-EXISTENCE OR CONFLICT? Catherine M. Kemper, David Pemberton, Martin Cawthorn, Sonja Heinrich, Janet Mann, Bernd Würsig, Peter Shaughnessy and Rosemary Gales .................................................................................................... ................................................................................................................................................................................................................................................................. INTRODUCTION Feeding mechanisms are equally diverse, ranging from no sup- Marine and freshwater aquaculture is the fastest growing world plementary feeding for most molluscs to using vegetable prod- food industry; 11% per year during the 1990s (Newton 2000). ucts, fishmeal, pellets (made from wild caught marine fish) and In part, this is a result of the reduction of both major and minor whole fish (e.g. pilchards to fatten tuna). Almost all operations wild fisheries (Pauly et al. 2002) and an increased demand for are in sheltered coastal or estuarine waters and therefore add seafood. An estimated 25% of seafood consumed is produced by pressure on environments already influenced by human aquaculture and this is set to rise to 40% by 2010 (FAO 2000). impacts. Even land-based aquaculture can affect the coastal One of the justifications given for turning to aquaculture is that marine environment through increased nutrients and pollution it will relieve the pressure on wild fish stocks, -
Boat Conference Organized by the U.N
Copiesavellshie from: SeeGrant Extension Program 6022 MoCartyHall Universityof Florida Gslnssvlila,F I.3281 1 PletW.SseOrant Cogsge le supportedhy awed of the Officeof SeeOrant, NationalOceania aad AtrnoepherieAdmlnletradon, U4. Depert- raentef Cetmmrm,grant nwahw NAESAA-~, underprovisions of the Natkmef8ee GrantCogege and ProgramsAot of 1888. This hdenaatlaals pehlldtedhy the SeeOrant Eatenekm Proipam wideh funatlons as ~ componentof the Florida CooperativeEatenslon Ssrvtse. JehuT. ggaeste,dom, In mmduetlngCoeperadve Extension work in Agriculture.Home Eoonomies, and ggerineSeieneee. State of Fkrride.U.S. gttpartnrsntef Agrharlture,UA Qspartmentof Commerse,and Soerdeof County Commiesloasm,cooperating. printed end dlstrlhutedIn ferdsemnseof the Acts of CengrWsof Stay 8 aadJune 1 1,1814. The Florida See Orant College h anEqual Employment Opportunity-Affirme- ~ eeAetkm employeraatharlmd m 'yrow4h~h, edaoatloaalkrformadon and other earvtaeeonly to individualsand InstNutlomthat ~ aoettenwithout Nacrd ta ress,eaktr, eea, or nationalorigin. I NTERNATIQNAL CONFERENCE DN DESIGN, CONSTRUCTION,AND OPERATIONOF COMMERCIAL F I SHING VESSELS Sponsored By: Florida Sea Grant College Program Society of Naval Architects and Marine Engineers, Southeast Section Florida Institute of Technology College of Science and Engineering: OceanEngineering Program Held At: Florida Institute of Technology Edi ted By: John C. Sainsbury Thomas M. Leahy Sea Grant Project No. IR/84-6 Grant No. NA 80AA-D-00038 Report Number 67 Florida Sea Grant College May 1985 Price: $10.00 ACKNOWLEDGEMENTS SPONSORS: Florida Sea Grant College Society of Naval Architects and Marine Engineers, Southeast Section Florida Institute of Technology, College of Engineering: OceanEngineering Program CONFERENCEGENERAL CHAIRMAN: Dr. JohnC. Sainsbury,Professor Chairman, Ocean Engineering Program, Florida Institute of Technology, Melbourne, Florida 32901, USA CDGRDI NATI NG COMMITTEE: Tom Col 't ins, Desco. -
Proposals for a Luga River Salmon Management Plan
Proposals for a Luga River Salmon management plan ‐ Russian Implementation of the HELCOM Baltic Sea Action Plan and Actions Connected to Biodiversity and Wild Baltic Salmon February 2010 Table of content 1. Proposals for a Luga River salmon management plan .................................................................... 3 2. Important Components in a Salmon Management Plan for the Luga River ................................... 4 2.1 Luga Salmon Management Goals .................................................................................................. 4 2.2 Fisheries Management and Illegal fishing ..................................................................................... 5 a) State Control of illegal fishing activities in the Luga ................................................................... 5 B) Public control of illegal fishing activities in the Luga .................................................................. 6 c) Fisheries management in Luga River estuary and Luga Bay ........................................................ 7 2.3 Monitoring and Research .............................................................................................................. 7 2.4 Protection of the Luga River as a Natural and Free‐flowing River ................................................ 9 2.5 Habitat Restoration and Protection .............................................................................................. 9 2.6 Safeguarding of the Genetic Variability of Luga salmon ............................................................ -
Guidelines for Presenting Claims in the Fisheries, Mariculture and Fish Processing Sector
Guidelines for presenting claims in the fisheries, mariculture and fish processing sector International Oil Pollution Compensation Fund 1992 December 2008 Edition Guidelines for presenting claims in the fisheries, mariculture and fish processing sector December 2008 Edition Adopted by the Assembly in June 2008 International Oil Pollution Compensation Fund 1992 1 Designed and produced in the United Kingdom by: Impact PR and Design Limited, 125 Blean Common, Blean, Canterbury, Kent CT2 9JH Telephone: +44 (0)1227 450022 Web site: www.impactprdesign.co.uk 2 CONTENTS PREFACE 4 1 INTRODUCTION TO THE INTERNATIONAL OIL POLLUTION COMPENSATION FUND 1992 5 What is the Fund? 5 What does the Fund do? 5 How is money raised to pay compensation? 5 When does the Fund come into play? 5 2 WHO CAN CLAIM? 6 3 WHAT SHOULD YOU DO IF THERE IS OIL POLLUTION? 7 Fishermen 8 Mariculture operators 8 Other fishing businesses (fish processing, marketing, supply etc) 9 4 WHAT LOSSES ARE COVERED? 9 Property damage 9 Consequential loss 9 Pure economic loss 10 Preventive measures 10 Use of advisers 10 5 WHAT CLAIMS CAN BE COMPENSATED? 10 6 WHEN TO MAKE A CLAIM 11 7 HOW TO MAKE A CLAIM 11 8 WHAT INFORMATION SHOULD YOU PROVIDE? 12 9 WHAT IF YOU HAVE POOR RECORDS OR NO EVIDENCE? 14 10 HOW ARE CLAIMS ASSESSED? 14 11 HOW ARE PAYMENTS MADE? 14 12 CONTACTING THE FUND 15 3 PREFACE A general practical guide to presenting claims for losses due to oil pollution caused by an oil tanker can be found in the Claims Manual published by the International Oil Pollution Compensation Fund 1992. -
Recent Development of Scale Marine Aquaculture Wastewater Treatment
4th International Conference on Sustainable Energy and Environmental Engineering (ICSEEE 2015) Recent development of scale marine aquaculture wastewater treatment Panpan LIU1, a, Liping Qiu1, b*, Shoubin Zhang1,c, Jiabin Wang1,d, Kang Xie1,e 1 School of Civil Engineering and Architecture, University of Jinan, No.336.West Road of Nan Xinzhuang. Jinan. 250022, PR China a [email protected], [email protected], [email protected], [email protected], [email protected], * Corresponding Author Keywords: sea-water aquiculture; effluent treatment; marine environment Abstract. With the rapid development of China's large-scale mariculture, the emissions of mariculture wastewater are increasing, which had already exceeded land-based sewage, and becoming a serious marine environmental problem, therefore, the treatment and control of large-scale mariculture wastewater have been more and more important. In this paper, recent development of large-scale mariculture in China was first introduced, and then, the characteristics of mariculture wastewater quality and quantity was analyzed as well as the mariculture wastewater treatment technology in the world was also reviewed. Finally, the development direction of China's future mariculture wastewater treatment technology and policy were predicted in order to provide references for the environmental protection and development of mariculture. Seawater aquaculture has become an important source of protein in the world. With the increase of aquaculture scale and strength ,the development of mariculture was increasing scale and indu- strialization, wastewater emissions increased rapidly and has a large amount of water, high strength and difficult to control, such as characteristics .A lot of mariculture wastewater into the sea water will lead to the seawater nutrient salt content increased rapidly, the abnormal reproduction of algae, the frequent occurrence of red tide and water in species diversity of damage, it has been bring serious pollution of the marine environment . -
COUNTRY SECTION Sri Lanka Fishery Products
Validity date from COUNTRY Sri Lanka 10/08/2007 00058 SECTION Fishery products Date of publication 28/05/2019 List in force Approval number Name City Regions Activities Remark Date of request DFAR/FPE/98/01 Tropic Frozen Foods Ltd. Negombo Western Province PP DFAR/FPE/98/02 Southern Fish Factory Kosgoda Southern Province PP Aq DFAR/FPE/98/03 Skyway Sea Foods Specialist's (Pvt.) Ltd. Negombo Western Province PP DFAR/FPE/98/07 Prawn Ceylon (Pvt.) Ltd. Marawila North Western Province PP Aq DFAR/FPE/98/08 Alpex Marine (Pvt.) Ltd. Hendala Western Province PP Aq DFAR/FPE/98/09 Jay Sea Foods Processing (Pvt.) Ltd. Pamunugama Western Province PP DFAR/FPE/98/10 OLS Foods (Pvt) Ltd Thoduwawa North Western Province PP DFAR/FPE/98/11 Apollo Marine International (Pvt.) Ltd. Nittambuwa Western Province PP Aq DFAR/FPE/98/12 Quality Fish Processing Lanka (Pvt.) Ltd. Mundel North Western Province PP Aq DFAR/FPE/98/15 Global Sea Foods (Ptv.) Ltd. Badalgama Western Province PP DFAR/FPE/98/16 Taprobane Seafoods (Pvt.) Ltd. Dankotuwa North Western Province PP Aq DFAR/FPE/98/17 J P Fresh Products Negombo Western Province PP DFAR/FPE/98/18 Aloy Expo (Pvt.) Ltd. Wattala Western Province PP DFAR/FPE/98/21 Lihini Sea Foods (Ptv.) Ltd. Katuneriya North Western Province PP DFAR/FPE/98/22 Foreconns Canneries Beruwala Western Province PP 1 / 3 List in force Approval number Name City Regions Activities Remark Date of request DFAR/FPE/98/23 Srimic Exports (Pvt.) Ltd. Uswetakeiyawa Western Province PP Aq DFAR/FPE/98/25 East Globe Lanka Export Company Dankotuwa North Western Province PP DFAR/FPE/98/26 Western Lanka Aquatic (Pvt) Limited Pamunugama Western Province PP 09/04/2010 DFAR/FPE/98/29 Global Sea Foods (Pvt.) Ltd. -
History, Profiles and Implications of Feed Fish and Fishmeal Supply from Domestic Trawlers in the East and South China Seas
Sadovy de Mitcheson, Leadbitter and Law, May 2018, Final Report to ADMCF pp. 131 History, profiles and implications of feed fish and fishmeal supply from domestic trawlers in the East and South China Seas 1Yvonne Sadovy de Mitcheson, 2Duncan Leadbitter, 1Calton Law 1 University of Hong Kong, Swire Institute of Marine Science, School of Biological 2 Sciences, Hong Kong; FISHMATTER, Australia Contact: [email protected] Report (+ Appendix I and II) to ADMCF: June 2018 Sadovy de Mitcheson, Leadbitter and Law, May 2018, Final Report to ADMCF pp. 131 Table of Contents Contents 1 SECTION 1 ........................................................................................................................ 10 1.1 General background ...................................................................................................... 10 1.2. Fisheries of the East and South China Seas; from past to present .......................... 12 1.3. Objectives of this Study ........................................................................................... 17 1.4. Methods .................................................................................................................. 17 2 SECTION 2 ........................................................................................................................ 19 2.1 General Introduction on Marine Fisheries in East and South China Seas and Growth in Demand for Aquaculture Feed ........................................................................................ 19 2.2 The role of bottom -
Public Comment Summary with WDFW Responses
Comments on DNS 21-008 Anadromous Salmon and Steelhead Hatchery Policy C-3624 supersedes policy C-3619. SEPA comments received from March 9, 2021, through March 23, 2021. The public comments copied here were as submitted. Commenter Comments Agency response or number of similar comments 311 form Dear SEPA Proposals Review, Thank you for your letters comments. DNS 20-045 was Subject: Comments for SEPA EA for Revised Hatchery ANADROMOUS SALMON AND STEELHEAD HATCHERY POLICY withdrawn on January 11, C3624/ Determination of Nonsignificance for DNS 20-045. 2021, and that there is no EA for this proposal. The Determination of Nonsignificance for DNS 21-008 on Hatchery Policy C-3624 is a great document and we believe this is sufficient to support this new policy. Please accept this as my approval to move forward, as I am in full agreement with it. This is an important next step to make more fish for the Southern Resident Killer Whale and also for the tribal, recreational, and commercial fishing communities. This policy is long overdue and its great to see a positive change. The new hatchery policy C-3624 will not be the tool that approves specific projects but allows the information to move forward to the merits of the already highly scrutinized Hatchery Genetic Management Plans. These plans or allowable blueprint for the river systems, stand on their own merit. These HGMPs are written by the world's best scientists, both tribal and state. Then followed up by more to the world's best scientists for rigorous scientific vetting and peer review.