UNITED STATES PATENT of FICE 2,640,086 PROCESS for SEPARATING HYDROGEN FLUORIDE from CHLORODFLUORO METHANE Robert H
Total Page:16
File Type:pdf, Size:1020Kb
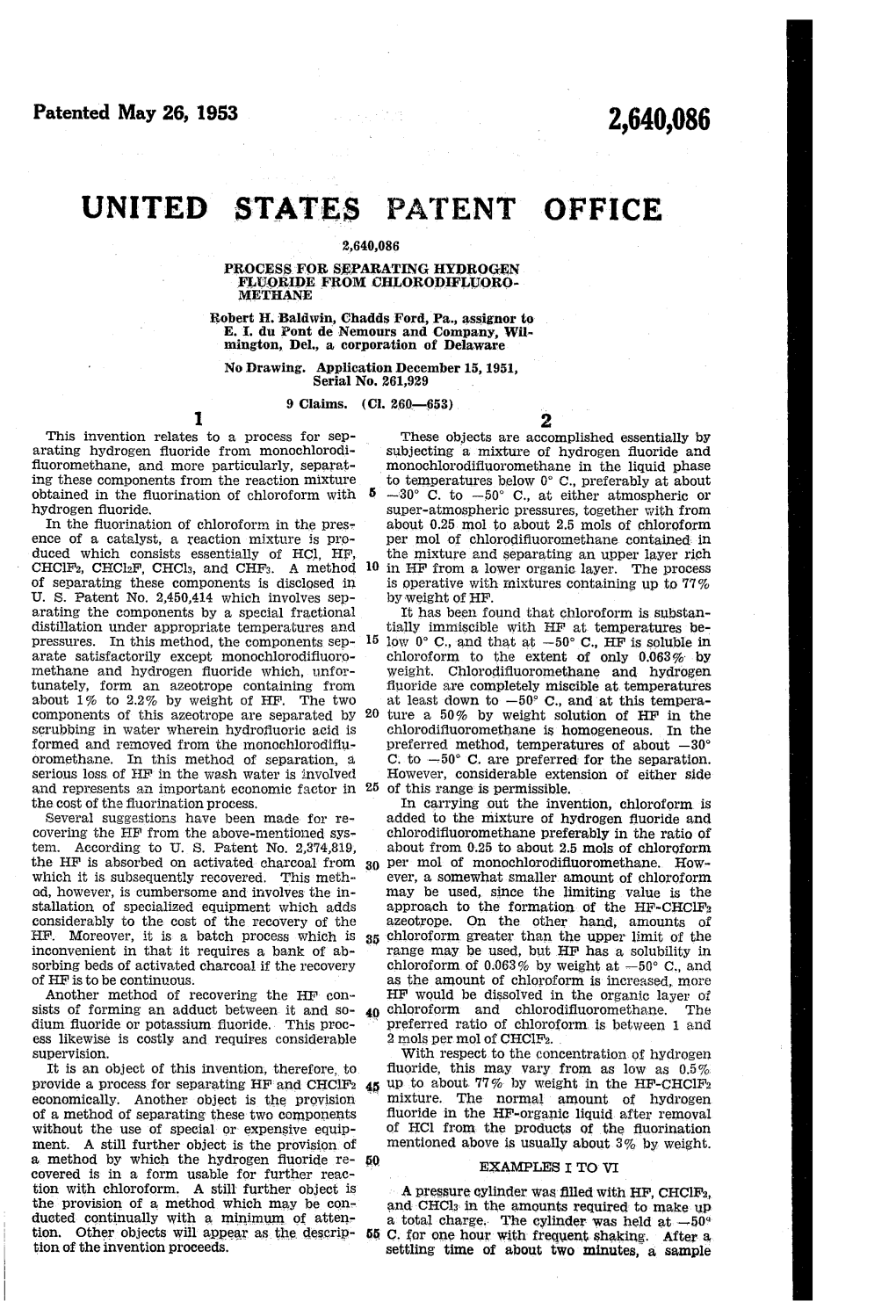
Load more
Recommended publications
-
Vibrationally Excited Hydrogen Halides : a Bibliography On
VI NBS SPECIAL PUBLICATION 392 J U.S. DEPARTMENT OF COMMERCE / National Bureau of Standards National Bureau of Standards Bldg. Library, _ E-01 Admin. OCT 1 1981 191023 / oO Vibrationally Excited Hydrogen Halides: A Bibliography on Chemical Kinetics of Chemiexcitation and Energy Transfer Processes (1958 through 1973) QC 100 • 1X57 no. 2te c l !14 c '- — | NATIONAL BUREAU OF STANDARDS The National Bureau of Standards' was established by an act of Congress March 3, 1901. The Bureau's overall goal is to strengthen and advance the Nation's science and technology and facilitate their effective application for public benefit. To this end, the Bureau conducts research and provides: (1) a basis for the Nation's physical measurement system, (2) scientific and technological services for industry and government, (3) a technical basis for equity in trade, and (4) technical services to promote public safety. The Bureau consists of the Institute for Basic Standards, the Institute for Materials Research, the Institute for Applied Technology, the Institute for Computer Sciences and Technology, and the Office for Information Programs. THE INSTITUTE FOR BASIC STANDARDS provides the central basis within the United States of a complete and consistent system of physical measurement; coordinates that system with measurement systems of other nations; and furnishes essential services leading to accurate and uniform physical measurements throughout the Nation's scientific community, industry, and commerce. The Institute consists of a Center for Radiation Research, an Office of Meas- urement Services and the following divisions: Applied Mathematics — Electricity — Mechanics — Heat — Optical Physics — Nuclear Sciences" — Applied Radiation 2 — Quantum Electronics 1 — Electromagnetics 3 — Time 3 1 1 and Frequency — Laboratory Astrophysics — Cryogenics . -
Effect of Insulations on Cop in Vapor Compression Refrigeration System
International Journal of Mechanical Engineering and Technology (IJMET) Volume 10, Issue 01, January 2019, pp. 1201-1208, Article ID: IJMET_10_01_122 Available online at http://www.iaeme.com/ijmet/issues.asp?JType=IJMET&VType=10&IType= 01 ISSN Print: 0976-6340 and ISSN Online: 0976-6359 © IAEME Publication Scopus Indexed EFFECT OF INSULATIONS ON COP IN VAPOR COMPRESSION REFRIGERATION SYSTEM Anusha Peyyala Assistant Professor P V P Siddhartha Institute of Technology, Research Scholar, Acharya Nagarjuna University, India. Dr N V V S Sudheer Associate Professor, R V R & J C College of Engineering, Guntur India ABSTRACT In this project, experimentation is done on Vapour Compression Refrigeration System [VCRS] as the COP is high for this system and it is the present trend of the HVAC in the domestic industry. This study presents investigation of best suited refrigerant and insulation combination for gas pipeline and liquid pipeline of a split air conditioning system. Analysis are performed for R22-Chlorodiflouromethane, a HydroChloroFlouro Carbon refrigerant, which has been using in the present world that cause both global warming and ozone layer depletion and R410a, mixture of di- flouromethane and pentaflouroethane, a Hydroflouro carbon refrigerant, which is future of HVAC which reduces the effect of ozone layer depletion [ODP] and Global Warming Potential [GWP].For these two refrigerants, we had found out the best insulation suitable as insulation also affects the COP of air conditioner, which has been observed from the literature. Minimizing the temperature of refrigerant in suction line helps condensing unit work more effectively intern the system performance increases. This reduces the overall power required for working of air conditioner, thereby reducing the maintenance cost of system. -
New and Improved Infrared Absorption Cross Sections for Chlorodifluoromethane (HCFC-22)
Atmos. Meas. Tech., 9, 2593–2601, 2016 www.atmos-meas-tech.net/9/2593/2016/ doi:10.5194/amt-9-2593-2016 © Author(s) 2016. CC Attribution 3.0 License. New and improved infrared absorption cross sections for chlorodifluoromethane (HCFC-22) Jeremy J. Harrison1,2 1Department of Physics and Astronomy, University of Leicester, University Road, Leicester, LE1 7RH, UK 2National Centre for Earth Observation, University of Leicester, University Road, Leicester, LE1 7RH, UK Correspondence to: Jeremy J. Harrison ([email protected]) Received: 10 December 2015 – Published in Atmos. Meas. Tech. Discuss.: 18 January 2016 Revised: 3 May 2016 – Accepted: 6 May 2016 – Published: 17 June 2016 Abstract. The most widely used hydrochlorofluorocarbon 1 Introduction (HCFC) commercially since the 1930s has been chloro- difluoromethane, or HCFC-22, which has the undesirable The consumer appetite for safe household refrigeration led effect of depleting stratospheric ozone. As this molecule to the commercialisation in the 1930s of dichlorodifluo- is currently being phased out under the Montreal Pro- romethane, or CFC-12, a non-flammable and non-toxic re- tocol, monitoring its concentration profiles using infrared frigerant (Myers, 2007). Within the next few decades, other sounders crucially requires accurate laboratory spectroscopic chemically related refrigerants were additionally commer- data. This work describes new high-resolution infrared ab- cialised, including chlorodifluoromethane, or a hydrochlo- sorption cross sections of chlorodifluoromethane over the rofluorocarbon known as HCFC-22, which found use in a spectral range 730–1380 cm−1, determined from spectra wide array of applications such as air conditioners, chillers, recorded using a high-resolution Fourier transform spectrom- and refrigeration for food retail and industrial processes. -
SAFETY DATA SHEET Chlorodifluoromethane (R 22) Issue Date: 16.01.2013 Version: 1.0 SDS No.: 000010021746 Last Revised Date: 18.06.2015 1/15
SAFETY DATA SHEET Chlorodifluoromethane (R 22) Issue Date: 16.01.2013 Version: 1.0 SDS No.: 000010021746 Last revised date: 18.06.2015 1/15 SECTION 1: Identification of the substance/mixture and of the company/undertaking 1.1 Product identifier Product name: Chlorodifluoromethane (R 22) Trade name: Gasart 503 R22 Additional identification Chemical name: Chlorodifluoromethane Chemical formula: CHClF2 INDEX No. - CAS-No. 75-45-6 EC No. 200-871-9 REACH Registration No. 01-2119517587-31 1.2 Relevant identified uses of the substance or mixture and uses advised against Identified uses: Industrial and professional. Perform risk assessment prior to use. Refrigerant. Using gas alone or in mixtures for the calibration of analysis equipment. Using gas as feedstock in chemical processes. Formulation of mixtures with gas in pressure receptacles. Uses advised against Consumer use. 1.3 Details of the supplier of the safety data sheet Supplier Linde Gas GmbH Telephone: +43 50 4273 Carl-von-Linde-Platz 1 A-4651 Stadl-Paura E-mail: [email protected] 1.4 Emergency telephone number: Emergency number Linde: + 43 50 4273 (during business hours), Poisoning Information Center: +43 1 406 43 43 SDS_AT - 000010021746 SAFETY DATA SHEET Chlorodifluoromethane (R 22) Issue Date: 16.01.2013 Version: 1.0 SDS No.: 000010021746 Last revised date: 18.06.2015 2/15 SECTION 2: Hazards identification 2.1 Classification of the substance or mixture Classification according to Directive 67/548/EEC or 1999/45/EC as amended. N; R59 The full text for all R-phrases is displayed in section 16. Classification according to Regulation (EC) No 1272/2008 as amended. -
Cylinder Valve Selection Quick Reference for Valve Abbreviations
SHERWOOD VALVE COMPRESSED GAS PRODUCTS Appendix Cylinder Valve Selection Quick Reference for Valve Abbreviations Use the Sherwood Cylinder Valve Series Abbreviation Chart on this page with the Sherwood Cylinder Valve Selection Charts found on pages 73–80. The Sherwood Cylinder Valve Selection Chart are for reference only and list: • The most commonly used gases • The Compressed Gas Association primary outlet to be used with each gas • The Sherwood valves designated for use with this gas • The Pressure Relief Device styles that are authorized by the DOT for use with these gases PLEASE NOTE: The Sherwood Cylinder Valve Selection Charts are partial lists extracted from the CGA V-1 and S-1.1 pamphlets. They can change without notice as the CGA V-1 and S-1.1 pamphlets are amended. Sherwood will issue periodic changes to the catalog. If there is any discrepancy or question between these lists and the CGA V-1 and S-1.1 pamphlets, the CGA V-1 and S-1.1 pamphlets take precedence. Sherwood Cylinder Valve Series Abbreviation Chart Abbreviation Sherwood Valve Series AVB Small Cylinder Acetylene Wrench-Operated Valves AVBHW Small Cylinder Acetylene Handwheel-Operated Valves AVMC Small Cylinder Acetylene Wrench-Operated Valves AVMCHW Small Cylinder Acetylene Handwheel-Operated Valves AVWB Small Cylinder Acetylene Wrench-Operated Valves — WB Style BV Hi/Lo Valves with Built-in Regulator DF* Alternative Energy Valves GRPV Residual Pressure Valves GV Large Cylinder Acetylene Valves GVT** Vertical Outlet Acetylene Valves KVAB Post Medical Valves KVMB Post Medical Valves NGV Industrial and Chrome-Plated Valves YVB† Vertical Outlet Oxygen Valves 1 * DF Valves can be used with all gases; however, the outlet will always be ⁄4"–18 NPT female. -
Ammonium Bifluoride CAS No
Product Safety Summary Ammonium Bifluoride CAS No. 1341-49-7 This Product Safety Summary is intended to provide a general overview of the chemical substance. The information on the summary is basic information and is not intended to provide emergency response information, medical information or treatment information. The summary should not be used to provide in-depth safety and health information. In-depth safety and health information can be found in the Safety Data Sheet (SDS) for the chemical substance. Names • Ammonium bifluoride (ABF) • Ammonium difluoride • Ammonium acid fluoride • Ammonium hydrogen difluoride • Ammonium fluoride compound with hydrogen fluoride (1:1) Product Overview Solvay Fluorides, LLC does not sell ammonium bifluoride directly to consumers. Ammonium bifluoride is used in industrial applications and in other processes where workplace exposures can occur. Ammonium bifluoride (ABF) is used for cleaning and etching of metals before they are further processed. It is used as an oil well acidifier and in the etching of glass or cleaning of brick and ceramics. It may also be used for pH adjustment in industrial textile processing or laundries. ABF is available as a solid or liquid solution (in water). Ammonium bifluoride is a corrosive chemical and contact can severely irritate and burn the skin and eyes causing possible permanent eye damage. Breathing ammonium bifluoride can severely irritate and burn the nose, throat, and lungs, causing nosebleeds, cough, wheezing and shortness of breath. On contact with water or moist skin, ABF can release hydrofluoric acid, a very dangerous acid. Inhalation or ingestion of large amounts of ammonium bifluoride can cause nausea, vomiting and loss of appetite. -
Hexafluorosilicic Acid
Sodium Hexafluorosilicate [CASRN 16893-85-9] and Fluorosilicic Acid [CASRN 16961-83-4] Review of Toxicological Literature October 2001 Sodium Hexafluorosilicate [CASRN 16893-85-9] and Fluorosilicic Acid [CASRN 16961-83-4] Review of Toxicological Literature Prepared for Scott Masten, Ph.D. National Institute of Environmental Health Sciences P.O. Box 12233 Research Triangle Park, North Carolina 27709 Contract No. N01-ES-65402 Submitted by Karen E. Haneke, M.S. (Principal Investigator) Bonnie L. Carson, M.S. (Co-Principal Investigator) Integrated Laboratory Systems P.O. Box 13501 Research Triangle Park, North Carolina 27709 October 2001 Toxicological Summary for Sodium Hexafluorosilicate [16893-85-9] and Fluorosilicic Acid [16961-83-4] 10/01 Executive Summary Nomination Sodium hexafluorosilicate and fluorosilicic acid were nominated for toxicological testing based on their widespread use in water fluoridation and concerns that if they are not completely dissociated to silica and fluoride in water that persons drinking fluoridated water may be exposed to compounds that have not been thoroughly tested for toxicity. Nontoxicological Data Analysis and Physical-Chemical Properties Analytical methods for sodium hexafluorosilicate include the lead chlorofluoride method (for total fluorine) and an ion-specific electrode procedure. The percentage of fluorosilicic acid content for water supply service application can be determined by the specific-gravity method and the hydrogen titration method. The American Water Works Association (AWWA) has specified that fluorosilicic acid contain 20 to 30% active ingredient, a maximum of 1% hydrofluoric acid, a maximum of 200 mg/kg heavy metals (as lead), and no amounts of soluble mineral or organic substance capable of causing health effects. -
Occupational Exposure to Hydrogen Fluoride
criteria for a recommended standard OCCUPATIONAL EXPOSURE TO HYDROGEN FLUORIDE U.S. DEPARTMENT OF HEALTH, EDUCATION, AND WELFARE Public Health Service Center for Disease Control National Institute for Occupational Safety and Health M arch 1976 HEW Publication No. (NIOSH) 7 6 -1 4 3 PREFACE The Occupational Safety and Health Act of 1970 emphasizes the need for standards to protect the health and safety of workers exposed to an ever-increasing number of potential hazards at their workplace. The National Institute for Occupational Safety and Health has projected a formal system of research, with priorities determined on the basis of specified indices, to provide relevant data from which valid criteria for effective standards can be derived. Recommended standards for occupational exposure, which are the result of this work, are based on the health effects of exposure. The Secretary of Labor will weigh these recommen dations along with other considerations such as feasibility and means of implementation in developing regulatory standards. It is intended to present successive reports as research and epide miologic studies are completed and as sampling and analytical methods are developed. Criteria and standards will be reviewed periodically to ensure continuing protection of the worker. I am pleased to acknowledge the contributions to this report on hydrogen fluoride by members of my staff and the valuable constructive comments by the Review Consultants on Hydrogen Fluoride, by the ad hoc committees of the American Academy of Occupational Medicine and the Society for Occupational and Environmental Health, and by Robert B. O'Connor, M.D., NIOSH consultant in occupational medicine. -
CYCLE D-HX: NIST Vapor Compression Cycle Model Accounting for Refrigerant Thermodynamic and Transport Properties
NIST Technical Note 1974 CYCLE_D-HX: NIST Vapor Compression Cycle Model Accounting for Refrigerant Thermodynamic and Transport Properties Version 1.0 User’s Guide J.S. Brown R. Brignoli P.A. Domanski This publication is available free of charge from: https://doi.org/10.6028/NIST.TN.1974 NIST Technical Note 1974 CYCLE_D-HX: NIST Vapor Compression Cycle Model Accounting for Refrigerant Thermodynamic and Transport Properties Version 1.0 User’s Guide J.S. Brown The Catholic University of America R. Brignoli P.A. Domanski Engineering Laboratory National Institute of Standards and Technology This publication is available free of charge from: https://doi.org/10.6028/NIST.TN.1974 December 2017 U.S. Department of Commerce Wilbur L. Ross, Jr., Secretary National Institute of Standards and Technology Walter Copan, NIST Director and Under Secretary of Commerce for Standards and Technology This software package was developed by the National Institute of Standards and Technology (NIST), is not subject to copyright protection, and is in the public domain. It can be used freely provided that any derivative works bear some notice that they are derived from it. NIST used its best efforts to provide a high-quality software package and to select modeling methods and correlations based on sound scientific judgement. However, NIST assumes neither responsibility nor liability for any damage arising out of or relating to the use of CYCLE_D-HX. The software is provided “AS IS”; NIST makes NO GUARANTIES and NO WARRANTIES OF ANY TYPE, expressed or implied, including NO WARRANTY OF MERCHANTABILITY OR FITNESS FOR A PARTICULAR PURPOSE. -
Liquefied Gas Conversion Chart
LIQUEFIED GAS CONVERSION CHART Cubic Feet / Pound Pounds / Gallon Product Name Column A Column B Acetylene UN/NA: 1001 14.70 4.90 CAS: 514-86-2 Air UN/NA: 1002 13.30 7.29 CAS: N/A Ammonia Anhydrous UN/NA: 1005 20.78 5.147 CAS: 7664-41-7 Argon UN/NA: 1006 9.71 11.63 CAS: 7440-37-1 Butane UN/NA: 1075 6.34 4.86 CAS: 106-97-8 Carbon Dioxide UN/NA: 2187 8.74 8.46 CAS: 124-38-9 Chlorine UN/NA: 1017 5.38 11.73 CAS: 7782-50-5 Ethane UN/NA: 1045 12.51 2.74 CAS: 74-84-0 Ethylene Oxide UN/NA: 1040 8.78 7.25 CAS: 75-21-8 Fluorine UN/NA: 1045 10.17 12.60 CAS: 7782-41-4 Helium UN/NA: 1046 97.09 1.043 CAS: 7440-59-7 Hydrogen UN/NA: 1049 192.00 0.592 CAS: 1333-74-0 1. Find the gas you want to convert. 2. If you know your quantity in cubic feet and want to convert to pounds, divide your amount by column A 3. If you know your quantity in gallons and want to convert to pounds, multiply your amount by column B 4. If you know your quantity in pounds and want to convert to gallons, divide your amount by column B If you have any questions, please call 1-800-433-2288 LIQUEFIED GAS CONVERSION CHART Cubic Feet / Pound Pounds / Gallon Product Name Column A Column B Hydrogen Chloride UN/NA: 1050 10.60 8.35 CAS: 7647-01-0 Krypton UN/NA: 1056 4.60 20.15 CAS: 7439-90-9 Methane UN/NA: 1971 23.61 3.55 CAS: 74-82-8 Methyl Bromide UN/NA: 1062 4.03 5.37 CAS: 74-83-9 Neon UN/NA: 1065 19.18 10.07 CAS: 7440-01-9 Mapp Gas UN/NA: 1060 9.20 4.80 CAS: N/A Nitrogen UN/NA: 1066 13.89 6.75 CAS: 7727-37-9 Nitrous Oxide UN/NA: 1070 8.73 6.45 CAS: 10024-97-2 Oxygen UN/NA: 1072 12.05 9.52 CAS: 7782-44-7 Propane UN/NA: 1075 8.45 4.22 CAS: 74-98-6 Sulfur Dioxide UN/NA: 1079 5.94 12.0 CAS: 7446-09-5 Xenon UN/NA: 2036 2.93 25.51 CAS: 7440-63-3 1. -
Hydrogen Fluoride-Catalyzed Addition of Carbon Monoxide to Propylene Under High Pressures*
Hydrogen Fluoride-Catalyzed Addition of Carbon Monoxide to Propylene under High Pressures* Yoshimasa Takezaki**, Yoshio Fuchigami**, Hiroshi Teranishi**, Nobuyuki Sugita** and Kiyoshi Kudo** Summary: Isobutyric acid forming reaction of propylene with carbon monoxide has been studied in the presence of HF-H2O catalyst under high pressures. The optimum conditions for the formation of acid have been decided as follows: water content of HF catalyst, 20 wt. %; charge ratio of HF to C3H6, 15 (mole ratio);reaction temperature,94℃ or lower;and the total pressure,190kg/cm2 or higher. Reaction temperature higher than 94℃ is unfavorable because of accelerated polymerization of C3H6. Reaction mechanism of the formation of isobutyric acid has been proposed, where the rate determining step, C3H7++CO(dissolved)→C3H7CO+, being first-order with regard to each reactant. The rate expression for the yield of the acid has been derived and the apparent activation energy of the over-all reaction has been found to be 21.7kcal/mole. Introduction Since 1933 when several patents1) on the production of carboxylic acids from olefins and carbon monoxide in acidic media were In these works Koch obtained good yield published, many works have been carried (better than 90%) of acids when butene or out2)-22)on this process. On propylene as an higher olefin was used8),9), but in the case of olefin, the first systematic study was reported propylene5), detailed data on experimental by Hardy in 19362), in which the author, conditions and yields were not reported except using 87 %-phosphoric acid as the catalyst, for the formations of alcohols, esters and observed 50% yield of total acids (isobutyric carboxylic acids as the products. -
R-22 Safety Data Sheet
R-22 Safety Data Sheet R-22 1. CHEMICAL PRODUCT AND COMPANY IDENTIFICATION PRODUCT NAME: R-22 OTHER NAME: Chlorodifluoromethane USE: Refrigerant Gas DISTRIBUTOR: National Refrigerants, Inc. 661 Kenyon Avenue Bridgeton, New Jersey 08302 FOR MORE INFORMATION CALL: IN CASE OF EMERGENCY CALL: (Monday-Friday, 8:00am-5:00pm) CHEMTREC: 1-800-424-9300 1-800-262-0012 2. HAZARDS IDENTIFICATION CLASSIFICATION: Gases under pressure, Liquefied Gas SIGNAL WORD: WARNING HAZARD STATEMENT: Contains gas under pressure, may explode if heated SYMBOL: Gas Cylinder PRECAUTIONARY STATEMENT: STORAGE: Protect from sunlight, store in a well ventilated place EMERGENCY OVERVIEW: Colorless, volatile liquid with ethereal and faint sweetish odor. Non-flammable material. Overexposure may cause dizziness and loss of concentration. At higher levels, CNS depression and cardiac arrhythmia may result from exposure. Vapors displace air and can cause asphyxiation in confined spaces. At higher temperatures, (>250C), decomposition products may include Hydrochloric Acid (HCI), Hydrofluoric Acid (HF) and carbonyl halides. POTENTIAL HEALTH HAZARDS SKIN: Irritation would result from a defatting action on tissue. Liquid contact could cause frostbite. EYES: Liquid contact can cause severe irritation and frostbite. Mist may irritate. INHALATION: R-22 is low in acute toxicity in animals. When oxygen levels in air are reduced to 12-14% by displacement, symptoms of asphyxiation, loss of coordination, increased pulse rate and deeper respiration will occur. At high levels, cardiac arrhythmia may occur. INGESTION: Ingestion is unlikely because of the low boiling point of the material. Should it occur, discomfort in the gastrointestinal tract from rapid evaporation of the material and consequent evolution of gas would result.