(12) Patent Application Publication (10) Pub. No.: US 2004/0043217 A1 Dezutter Et Al
Total Page:16
File Type:pdf, Size:1020Kb
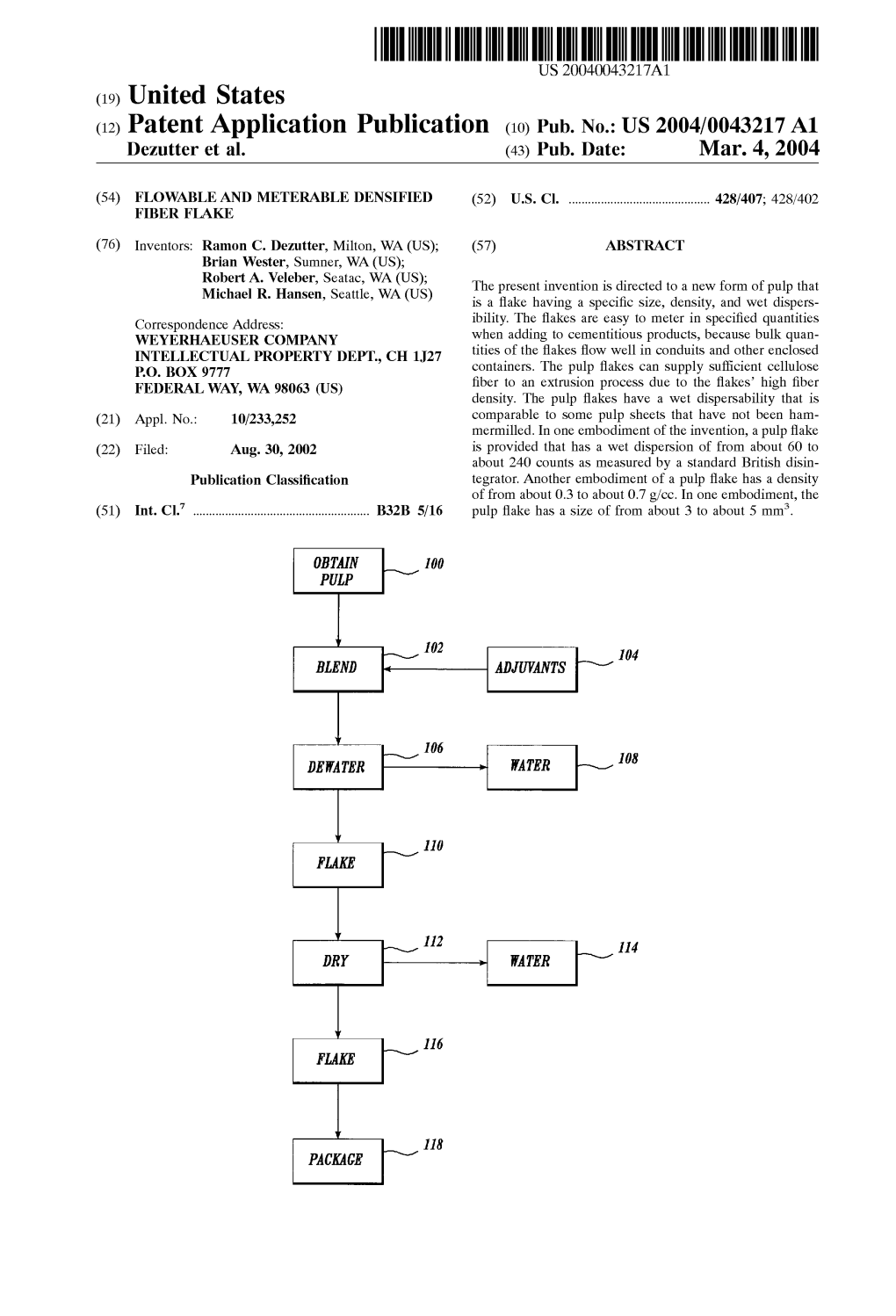
Load more
Recommended publications
-
United States Patent (10) Patent No.: US 9.458,297 B2 Miller (45) Date of Patent: Oct
USOO9458297B2 (12) United States Patent (10) Patent No.: US 9.458,297 B2 Miller (45) Date of Patent: Oct. 4, 2016 (54) MODIFIED FIBER, METHODS, AND 4,898,642 A 2f1990 Moore SYSTEMS 4,900,324 A 2f1990 Chance 4,935,022 A 6, 1990 Lash (71) Applicant: WEYERHAEUSERNR COMPANY., 4,936,8651538 A S366, 1990 WelchWE Federal Way, WA (US) 5,049,235 A 9, 1991 Barcus 5,137,537 A 8, 1992 Herron (72) Inventor: Charles E. Miller, Federal Way, WA 5,5,160,789 183,707 A 11/19922f1993 BarcusHerron (US) 5, 190,563 A 3/1993 Herron 5,221,285 A 6/1993 Andrews (73) Assignee: WEYERHAEUSERNR COMPANY., 5,225,047 A 7, 1993 Graef Federal Way, WA (US) 5,247,072 A 9/1993 Ning et al. 5,366,591 A 11, 1994 Jewell (*) Notice: Subject to any disclaimer, the term of this 3.222 A 8.32 Shiki patent is extended or adjusted under 35 5,496.476 A 3/1996 Tang U.S.C. 154(b) by 0 days. 5,496.477 A 3/1996 Tang 5,536,369 A 7/1996 Norlander (21) Appl. No.: 14/320,279 5,549,791 A 8/1996 Herron 5,556,976 A 9, 1996 Jewell 1-1. 5,562,740 A 10, 1996 Cook (22) Filed: Jun. 30, 2014 5,698,074. A 12/1997 Barcus 5,705,475 A 1, 1998 T (65) Prior Publication Data 5,728,771 A 3, 1998 E. 5,843,061 A 12/1998 Chauvette US 2015/0376347 A1 Dec. -
Hybrid Composites: Combining Cellulose Fibers and Wollastonite Mineral Fibers Into a Nylon 6 Matrix
The Seventh International Conference on Woodfiber-Plastic Composites ~ Hybrid Composites: Combining Cellulose Fibers and Wollastonite Mineral Fibers into a Nylon 6 Matrix Rodney E. Jacobson and Daniel F. Caulfield Abstract The objective of this research was to develop a tion. Attempts to maximize the composite proper- high purity cellulose/wollastonite pellet that could ties were not the focus of this research. Stable, then be accurately metered and feed into a labora- controllable processing characteristics and re- tory scale twin-screw extruder and compounded peatability of the twin-screw extrusion trials was with a nylon 6 resin. The major focus was targeted the goal. It is the authors’ opinion that this goal on a 20 percent cellulose/20 percent wolla- was accomplished. Future research will focus on stonite/60 percent nylon 6 composite. Limited re- maximizing composite properties and determin- search with nylon 6,6 resins was also attempted ing if cellulose fibers alone or in combination with and will be discussed briefly. A process for devel- mineral fibers can be compounded on larger com- oping a cellulose/wollastonite pellet was success- mercial scale equipment. Extreme care and pre- ful and 100 Kg were produced for twin screw ex- cise processing knowledge is needed to develop a trusion processing with nylons. The 100 Kg of commercial scale process that works. If this can- pellets were then compounded via a “low temper- not be accomplished, then cellulose fibers as rein- ature compounding” technique as discussed in de- forcement in any of the high melting point engi- tail elsewhere (1). Further information can be ob- neering thermoplastics may remain as a lab- tained in U.S. -
Surprise!Surprise! Is Never Surprised by the Things That a Message from Leave Us Anxious and Worried
NATIONAL ASSOCIATION OF CHURCH FACILITIES MANAGERS The answer depends largely on your perspective, but we know that God Surprise!Surprise! is never surprised by the things that A MESSAGE FROM leave us anxious and worried. NACFM PRESIDENT PATRICK HART Do not be anxious about anything, but in every situation, by prayer and petition, with thanksgiving, present your requests to God. And the peace of God, which transcends all understanding, will guard your hearts and your minds in Christ Jesus. – Philippians 4:6-7 The Lord has gone before us and has a plan. The board will meet this Recently, we purchased a new car, a Fiat 500X, for my wife, Amy. She drove it month for our annual national con- home from the dealership on Saturday evening. On her way to work a few days ference planning meetings. We will later the car stalled out and couldn’t be restarted…surprise! That’s not supposed be discussing in depth and praying to happen with a brand new vehicle! After waiting four hours for the tow truck hard about where the Lord is leading and getting the car to the dealership, we were told that no loaner vehicles were the NACFM during this time. He has available…surprise! The next day I received a call from the dealership Service this and that should be no surprise. Center and was told that they needed to order parts for our new car. The parts We would appreciate your prayers would have to be shipped from Italy, so it might be a few weeks before it would for the board as we gather to chart be repaired…surprise! Oh, but they did have a loaner car available…a Fiat 500 a course for the future and finalize convertible (a very tiny car, by the way)…surprise! national conference details. -
Natural Fibers and Fiber-Based Materials in Biorefineries
Natural Fibers and Fiber-based Materials in Biorefineries Status Report 2018 This report was issued on behalf of IEA Bioenergy Task 42. It provides an overview of various fiber sources, their properties and their relevance in biorefineries. Their status in the scientific literature and market aspects are discussed. The report provides information for a broader audience about opportunities to sustainably add value to biorefineries by considerin g fiber applications as possible alternatives to other usage paths. IEA Bioenergy Task 42: December 2018 Natural Fibers and Fiber-based Materials in Biorefineries Status Report 2018 Report prepared by Julia Wenger, Tobias Stern, Josef-Peter Schöggl (University of Graz), René van Ree (Wageningen Food and Bio-based Research), Ugo De Corato, Isabella De Bari (ENEA), Geoff Bell (Microbiogen Australia Pty Ltd.), Heinz Stichnothe (Thünen Institute) With input from Jan van Dam, Martien van den Oever (Wageningen Food and Bio-based Research), Julia Graf (University of Graz), Henning Jørgensen (University of Copenhagen), Karin Fackler (Lenzing AG), Nicoletta Ravasio (CNR-ISTM), Michael Mandl (tbw research GesmbH), Borislava Kostova (formerly: U.S. Department of Energy) and many NTLs of IEA Bioenergy Task 42 in various discussions Disclaimer Whilst the information in this publication is derived from reliable sources, and reasonable care has been taken in its compilation, IEA Bioenergy, its Task42 Biorefinery and the authors of the publication cannot make any representation of warranty, expressed or implied, regarding the verity, accuracy, adequacy, or completeness of the information contained herein. IEA Bioenergy, its Task42 Biorefinery and the authors do not accept any liability towards the readers and users of the publication for any inaccuracy, error, or omission, regardless of the cause, or any damages resulting therefrom. -
Cellulose Nanofibers and Its Applications for Resin Reinforcements
Chapter 14 Cellulose Nanofibers and Its Applications for Resin Reinforcements Mariko Yoshioka, Yoshiyuki Nishio, Satoru Nakamura, Yoshiyuki Kushizaki, Ryo Ishiguro, Toshiki Kabutomori, Takeo Imanishi and Nobuo Shiraishi Additional information is available at the end of the chapter http://dx.doi.org/10.5772/55346 1. Introduction It is widely recognized that technologies that can convert biomass resources into commercially viable materials are needed. Cellulose is a candidate among biomass due to its abundance in nature. The characteristics of cellulose, which include no thermoplasticity and being insoluble in ordinary solvents, have limited its applications. With the aim of widening its application possibilities, several works have been documented on mechanochemical treatments of cellulose in the dry state and in the wet states.[1-6] Endo et al. [1-4] developed novel cellulose composites by ball milling mixtures of cellulose and poly(ethylene glycol) (PEG). The composites are reported to have formed by insertion of PEG molecules among the cellulose molecular chains. [3,4] Works of Kondo et al. [5] and ours [7] appeared as patent publications. In the former case, fine cellulose powder (average powder length and width: 28 and 11 μm, respectively) was pulverized in aqueous suspension by counter collision at a pressure of 200 MPa, being done once or repeatedly up to 60 times or more, using an ultra high-pressure homogenizer, Star Burst System HJP-25005( Sugino Machine Ltd.). In our case [7], cellulose micronized powder (KC flock W-400G, average particle size 24 μm) was used in the same way at a pressure of 245 MPa, being done once or repeatedly up to ten times, using a Star Burst System HJP- 25080. -
Introduction to Nfrc and Review of Mechanical
International Journal of Scientific & Engineering Research, Volume 8, Issue 3, March-2017 ISSN 2229-5518 318 Introduction to natural fiber reinforced polymer composites and review of mechanical properties of hemp fibers and hemp/PP composite: effects of chemical surface treatment Shaikh Sameer Rashidkhan,1 H. D. Sawant,2 1Final year student, Department of mechanical engineering, Maharashtra State Board of Technical Education, A. I. Abdul Razzak Kalsekar Polytechnic, New Panvel. 2 I/C Professor, Department of mechanical engineering, Maharashtra State Board of Technical Education, A. I. Abdul Razzak Kalsekar Polytechnic, New Panvel. Abstract—This review article introduced about natural fiber reinforced composite (NFRC) and also study of mechanical INTRODUCTION TO NFRC properties and effect of surface treatment on hemp fiber and hemp PP composites. In this article we studied about natural The natural fiber material are environmentally friendly fiber, their properties, composition and application in automobile materials compared to synthetic fiber. It is defined as fiber as well as hemp fiber’s properties and properties after chemical which are not manmade or synthetic is called natural fiber (1, surface treatment. 2, 3). It comes from both renewable and non-renewable resources. Because of good properties fiber polymer matrix Keywords -- low density, high strength, recyclability got considerable attention in various application. Natural renewable, biodegradable, fiber gives superior advantages over synthetic fiber like relatively low weight, low cost, less damage to processing INTRODUCTION equipment, good relative mechanical properties such as Synthetic polymer composite materials are currently used in tensile modulus and flexural modulus, improved surface industries to meet light-weight and high strength finish of molded parts composite, biodegradability and less requirements (4, 5, 6). -
Natural Cellulose Fibers for Surgical Suture Applications
polymers Article Natural Cellulose Fibers for Surgical Suture Applications María Paula Romero Guambo 1, Lilian Spencer 1, Nelson Santiago Vispo 1 , Karla Vizuete 2 , Alexis Debut 2 , Daniel C. Whitehead 3 , Ralph Santos-Oliveira 4 and Frank Alexis 1,5,* 1 School of Biological Sciences and Engineering, Yachay Tech University, Urcuquí, Imbabura 100115, Ecuador; [email protected] (M.P.R.G.); [email protected] (L.S.); [email protected] (N.S.V.) 2 Center of Nanoscience and Nanotechnology, Universidad de las Fuerzas Armadas ESPE, Sangolquí 1715231, Ecuador; [email protected] (K.V.); [email protected] (A.D.) 3 Department of Chemistry, Clemson University, Clemson, SC 29634, USA; [email protected] 4 Brazilian Nuclear Energy Commission, Nuclear Engineering Institute, Laboratory of Nanoradiopharmaceuticals and Synthesis of Novel Radiopharmaceuticals, Rio de Janeiro 21941906, Brazil; [email protected] 5 Biodiverse Source, San Miguel de Urcuquí 100651, Ecuador * Correspondence: [email protected] Received: 10 November 2020; Accepted: 11 December 2020; Published: 18 December 2020 Abstract: Suture biomaterials are critical in wound repair by providing support to the healing of different tissues including vascular surgery, hemostasis, and plastic surgery. Important properties of a suture material include physical properties, handling characteristics, and biological response for successful performance. However, bacteria can bind to sutures and become a source of infection. For this reason, there is a need for new biomaterials for suture with antifouling properties. Here we report two types of cellulose fibers from coconut (Cocos nucifera) and sisal (Agave sisalana), which were purified with a chemical method, characterized, and tested in vitro and in vivo. -
Extraction and Characterization of New Cellulose Fiber from the Agro- Waste of Lagenaria Siceraria (Bottle Guard) Plant N
CORE Metadata, citation and similar papers at core.ac.uk Provided by KHALSA PUBLICATIONS I S S N 2 3 2 1 - 807X Volume 12 Number9 Jou r n a l of Advances in Chemistry Extraction and Characterization of New Cellulose Fiber from the Agro- waste of Lagenaria Siceraria (Bottle Guard) Plant N. Saravanan1 , P.S.Sampath2 , T.A.Sukantha3 , T.Natarajan4 1Department of Mechatronics Engineering, K.S. Rangasamy College of Technology, Tiruchengode 637215, Tamil Nadu, India. E-mail: [email protected] 2Department of Mechanical Engineering, K.S. Rangasamy College of Technology, Tiruchengode 637215, Tamil Nadu, India E-mail: [email protected] 3Department of Chemistry, K.S. Rangasamy College of Technology, Tiruchengode 637215, Tamil Nadu, India E-mail: [email protected] 4Department of Mechanical Engineering, K.S. Rangasamy College of Technology, Tiruchengode 637215, Tamil Nadu, India E-mail: [email protected] ABSTRACT This article explores the extraction and characterization of natural fiber from the agro-waste of Lagenaria siceraria (LS) plant stem (commonly known as „bottle guard‟) for the first time. The extracted fiber from the waste stems has high cellulose content (79.91 %) with good tensile strength (257–717 MPa) and thermal stability (withstand up to 339.1°C). The immense percentage of crystalline index (92.4%) with the crystalline size (7.2 nm) as well as low density (1.216 g/cm3) of the LS fiber renders their possibility to use as an effective reinforcement material in lightweight eco-friendly composites for various industrial applications. Indexing terms/Keywords Natural fiber; Lagenaria siceraria; TGA analysis; FTIR; XRD; Crystalline index Academic Discipline And Sub-Disciplines Mechanical Engineering, Chemistry, Composites SUBJECT CLASSIFICATION Natural fiber composites TYPE (METHOD/APPROACH) Analysis and Characterization 1. -
Improving the Barrier Properties of Packaging Paper by Polyvinyl Alcohol Based Polymer Coating—Effect of the Base Paper and Nanoclay
polymers Article Improving the Barrier Properties of Packaging Paper by Polyvinyl Alcohol Based Polymer Coating—Effect of the Base Paper and Nanoclay Zhenghui Shen 1, Araz Rajabi-Abhari 1 , Kyudeok Oh 2 , Guihua Yang 3, Hye Jung Youn 1,2,3 and Hak Lae Lee 1,2,3,* 1 Program in Environmental Materials Science, Department of Agriculture, Forestry and Bioresources, College of Agriculture and Life Sciences, Seoul National University, Seoul 08826, Korea; [email protected] (Z.S.); [email protected] (A.R.-A.); [email protected] (H.J.Y.) 2 Research Institute of Agriculture and Life Sciences, Seoul National University, Seoul 08826, Korea; [email protected] 3 State Key Laboratory of Biobased Material and Green Papermaking, Qilu University of Technology, Shandong Academy of Sciences, Jinan 250353, China; [email protected] * Correspondence: [email protected] Abstract: The poor barrier properties and hygroscopic nature of cellulosic paper impede the wide application of cellulosic paper as a packaging material. Herein, a polyvinyl alcohol (PVA)-based polymer coating was used to improve the barrier performance of paper through its good ability to form a film. Alkyl ketene dimer (AKD) was used to enhance the water resistance. The effect of the absorptive characteristics of the base paper on the barrier properties was explored, and it was shown that surface-sized base paper provides a better barrier performance than unsized base paper. Nanoclay (Cloisite Na+) was used in the coating formulation to further enhance the Citation: Shen, Z.; Rajabi-Abhari, A.; barrier performance. The results show that the coating of PVA/AKD/nanoclay dispersion noticeably Oh, K.; Yang, G.; Youn, H.J.; Lee, H.L. -
Fibers in Different Lengths, Thicknesses and Shapes
bers USA & Canada Program Kobo offers a variety of natural and synthetic fibers in different lengths, thicknesses and shapes. They can be used to promote texturizing, soft focus, lengthening and volumizing effects in finished products. Nylon Fibers Natural Origin Fibers Synthetic Nylon fibers are commonly used in mascara and CELL-U-LASH™ fibers are made of cellulose, a natural polymer, eyebrow products for lengthening and volumizing effects. and vary in length from 20µm to 110µm; they are hydrophilic Polypropylene Fibers and disperse easily in the initial water phase of an emulsion. These fibers are an excellent choice for finished products Synthetic fibers made from Polypropylene can be used for containing natural ingredients. lengthening and volumizing effects in mascara and eyebrow products or to achieve a soft focus effect in powders, color and skin care emulsions, and lipsticks. Trade Name INCI Name Length Diameter Shape Color Notes Nylon NYLON-66 FIBER 20D 2mm 20 Denier Fibrous Powder of White to Nylon-66 (And) Uniform Length Yellow Synthetic Titanium Dioxide KNY-3D 1.2mm 3 Denier Fiber of White Uniform Length HEART FIBER 15T-1MM 1mm Nylon-6 (And) 13.5 Denier Unique “Heart” White Synthetic Silica Shape; Hollow HEART FIBER 15T-2MM 2mm 0.8-1.1 N-6 ARCH 3.3T1 Fiber; Synthetic; mm Triangular with 3.3 Volumizing, Nylon-6 Decitex Round Edge White 1.6-2.2 Cross Section Long Lash and Curl N-6 ARCH 3.3T2 mm Polypropylene PP FIBER 6D05 Polypropylene 0.5mm 5.6 Short Fibers White Synthetic PP FIBER 6D2 (And) Silica 2mm Denier Natural Origin -
WO 2016/062866 Al 28 April 2016 (28.04.2016) P O P C T
(12) INTERNATIONAL APPLICATION PUBLISHED UNDER THE PATENT COOPERATION TREATY (PCT) (19) World Intellectual Property Organization International Bureau (10) International Publication Number (43) International Publication Date WO 2016/062866 Al 28 April 2016 (28.04.2016) P O P C T (51) International Patent Classification: (81) Designated States (unless otherwise indicated, for every C04B 41/46 (2006.01) C04B 28/04 (2006.01) kind of national protection available): AE, AG, AL, AM, C04B 24/00 (2006.01) C04B 40/00 (2006.01) AO, AT, AU, AZ, BA, BB, BG, BH, BN, BR, BW, BY, BZ, CA, CH, CL, CN, CO, CR, CU, CZ, DE, DK, DM, (21) Number: International Application DO, DZ, EC, EE, EG, ES, FI, GB, GD, GE, GH, GM, GT, PCT/EP20 15/0746 18 HN, HR, HU, ID, IL, IN, IR, IS, JP, KE, KG, KN, KP, KR, (22) International Filing Date: KZ, LA, LC, LK, LR, LS, LU, LY, MA, MD, ME, MG, 23 October 2015 (23.10.201 5) MK, MN, MW, MX, MY, MZ, NA, NG, NI, NO, NZ, OM, PA, PE, PG, PH, PL, PT, QA, RO, RS, RU, RW, SA, SC, (25) Filing Language: English SD, SE, SG, SK, SL, SM, ST, SV, SY, TH, TJ, TM, TN, (26) Publication Language: English TR, TT, TZ, UA, UG, US, UZ, VC, VN, ZA, ZM, ZW. (30) Priority Data: (84) Designated States (unless otherwise indicated, for every 14190059.7 23 October 2014 (23. 10.2014) EP kind of regional protection available): ARIPO (BW, GH, GM, KE, LR, LS, MW, MZ, NA, RW, SD, SL, ST, SZ, (71) Applicant: BASF SE [DE/DE]; 67056 Ludwigshafen TZ, UG, ZM, ZW), Eurasian (AM, AZ, BY, KG, KZ, RU, (DE). -
Cellulose Fiber-Reinforced High-Density Polyethylene
JOURNAL OF COMPOSITE Article MATERIALS Journal of Composite Materials 2017, Vol. 51(13) 1807–1815 ! The Author(s) 2016 Cellulose fiber-reinforced high-density Reprints and permissions: sagepub.co.uk/journalsPermissions.nav polyethylene composites—Mechanical DOI: 10.1177/0021998316665241 journals.sagepub.com/home/jcm and thermal properties Daniella R Mulinari1, Herman JC Voorwald2, Maria OH Cioffi2 and Maria LCP da Silva3 Abstract In this investigation, the thermal and mechanical properties of cellulose fibers from sugarcane bagasse reinforced with high density polyethylene composites were evaluated. Cellulose fibers were modified with hydrous Zr oxide to clean the fiber surface and improve the fibers–matrix adhesion. Composites were manufactured using a thermokinetic mixer process and the fiber content was responsible for 5, 10, 20, 30, and 40wt% in the composition. The chemical modification of the cellulose fibers with zirconium oxide was verified by FTIR analysis and the fibers’ morphological aspects by SEM. After the chemical modification, the FTIR results showed reduction of OH bonds. SEM characterization showed that the modification changed the morphology of fibers. The results show that composites reinforced with modified cellulose fibers have an improvement in the thermal and mechanical properties, when compared to the non-cellulose fibers. In addition, an enhancement on the mechanical properties of composites was found, i.e. a gain of 122.4% compared to neat polymer at 40wt.% fiber loading in Young’s modulus. The thermal properties