Mai Motomontant Hiu Miu Miu Miui
Total Page:16
File Type:pdf, Size:1020Kb
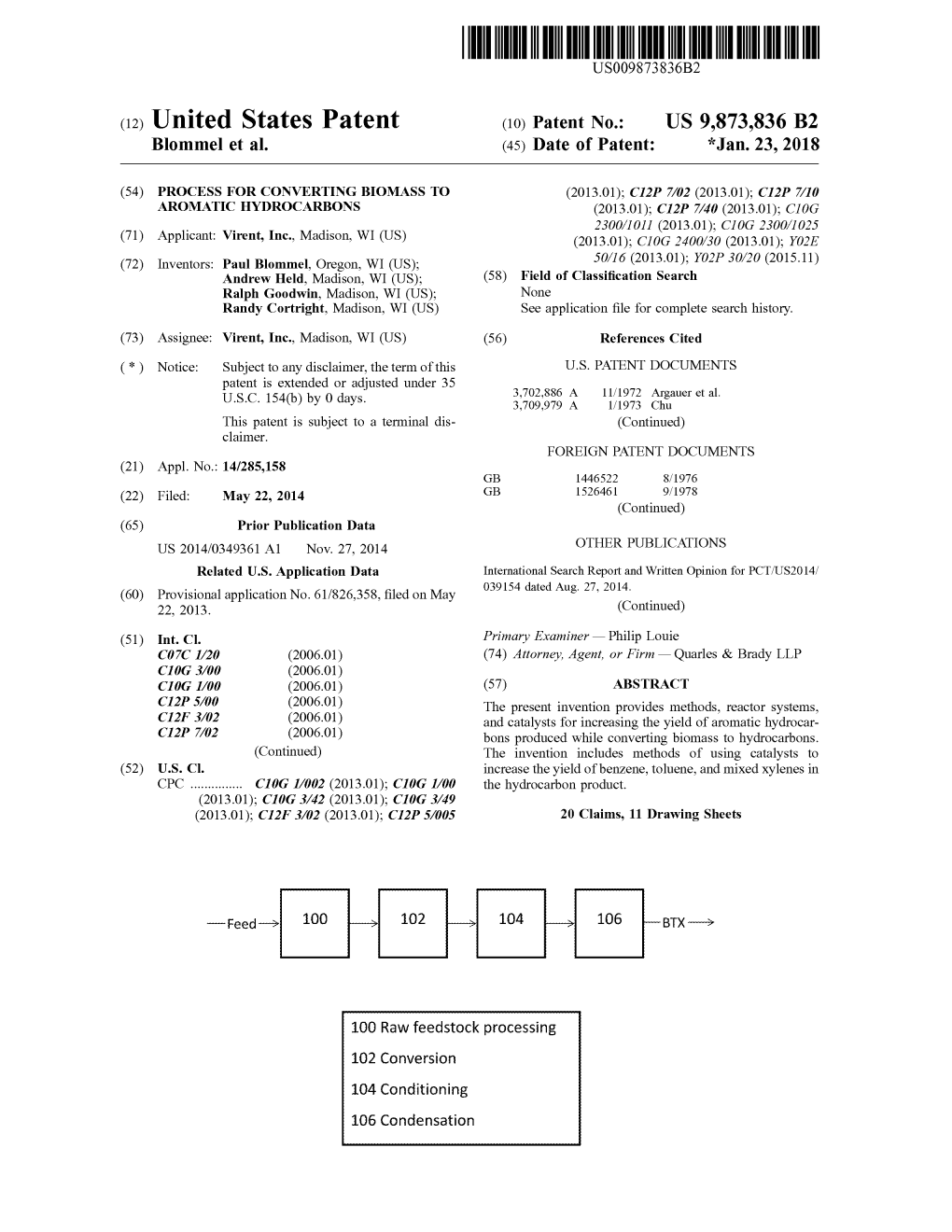
Load more
Recommended publications
-
Benzyl-L-Threitol
A Publication of Reliable Methods for the Preparation of Organic Compounds Working with Hazardous Chemicals The procedures in Organic Syntheses are intended for use only by persons with proper training in experimental organic chemistry. All hazardous materials should be handled using the standard procedures for work with chemicals described in references such as "Prudent Practices in the Laboratory" (The National Academies Press, Washington, D.C., 2011; the full text can be accessed free of charge at http://www.nap.edu/catalog.php?record_id=12654). All chemical waste should be disposed of in accordance with local regulations. For general guidelines for the management of chemical waste, see Chapter 8 of Prudent Practices. In some articles in Organic Syntheses, chemical-specific hazards are highlighted in red “Caution Notes” within a procedure. It is important to recognize that the absence of a caution note does not imply that no significant hazards are associated with the chemicals involved in that procedure. Prior to performing a reaction, a thorough risk assessment should be carried out that includes a review of the potential hazards associated with each chemical and experimental operation on the scale that is planned for the procedure. Guidelines for carrying out a risk assessment and for analyzing the hazards associated with chemicals can be found in Chapter 4 of Prudent Practices. The procedures described in Organic Syntheses are provided as published and are conducted at one's own risk. Organic Syntheses, Inc., its Editors, and its Board of Directors do not warrant or guarantee the safety of individuals using these procedures and hereby disclaim any liability for any injuries or damages claimed to have resulted from or related in any way to the procedures herein. -
Bio-Based Chemicals from Renewable Biomass for Integrated Biorefineries
energies Review Bio-Based Chemicals from Renewable Biomass for Integrated Biorefineries Kirtika Kohli 1 , Ravindra Prajapati 2 and Brajendra K. Sharma 1,* 1 Prairie Research Institute—Illinois Sustainable Technology Center, University of Illinois, Urbana Champaign, IL 61820, USA; [email protected] 2 Conversions & Catalysis Division, CSIR-Indian Institute of Petroleum, Dehradun, Uttarakhand 248005, India; [email protected] * Correspondence: [email protected] Received: 10 December 2018; Accepted: 4 January 2019; Published: 13 January 2019 Abstract: The production of chemicals from biomass, a renewable feedstock, is highly desirable in replacing petrochemicals to make biorefineries more economical. The best approach to compete with fossil-based refineries is the upgradation of biomass in integrated biorefineries. The integrated biorefineries employed various biomass feedstocks and conversion technologies to produce biofuels and bio-based chemicals. Bio-based chemicals can help to replace a large fraction of industrial chemicals and materials from fossil resources. Biomass-derived chemicals, such as 5-hydroxymethylfurfural (5-HMF), levulinic acid, furfurals, sugar alcohols, lactic acid, succinic acid, and phenols, are considered platform chemicals. These platform chemicals can be further used for the production of a variety of important chemicals on an industrial scale. However, current industrial production relies on relatively old and inefficient strategies and low production yields, which have decreased their competitiveness with fossil-based alternatives. The aim of the presented review is to provide a survey of past and current strategies used to achieve a sustainable conversion of biomass to platform chemicals. This review provides an overview of the chemicals obtained, based on the major components of lignocellulosic biomass, sugars, and lignin. -
Sugar Alcohols a Sugar Alcohol Is a Kind of Alcohol Prepared from Sugars
Sweeteners, Good, Bad, or Something even Worse. (Part 8) These are Low calorie sweeteners - not non-calorie sweeteners Sugar Alcohols A sugar alcohol is a kind of alcohol prepared from sugars. These organic compounds are a class of polyols, also called polyhydric alcohol, polyalcohol, or glycitol. They are white, water-soluble solids that occur naturally and are used widely in the food industry as thickeners and sweeteners. In commercial foodstuffs, sugar alcohols are commonly used in place of table sugar (sucrose), often in combination with high intensity artificial sweeteners to counter the low sweetness of the sugar alcohols. Unlike sugars, sugar alcohols do not contribute to the formation of tooth cavities. Common Sugar Alcohols Arabitol, Erythritol, Ethylene glycol, Fucitol, Galactitol, Glycerol, Hydrogenated Starch – Hydrolysate (HSH), Iditol, Inositol, Isomalt, Lactitol, Maltitol, Maltotetraitol, Maltotriitol, Mannitol, Methanol, Polyglycitol, Polydextrose, Ribitol, Sorbitol, Threitol, Volemitol, Xylitol, Of these, xylitol is perhaps the most popular due to its similarity to sucrose in visual appearance and sweetness. Sugar alcohols do not contribute to tooth decay. However, consumption of sugar alcohols does affect blood sugar levels, although less than that of "regular" sugar (sucrose). Sugar alcohols may also cause bloating and diarrhea when consumed in excessive amounts. Erythritol Also labeled as: Sugar alcohol Zerose ZSweet Erythritol is a sugar alcohol (or polyol) that has been approved for use as a food additive in the United States and throughout much of the world. It was discovered in 1848 by British chemist John Stenhouse. It occurs naturally in some fruits and fermented foods. At the industrial level, it is produced from glucose by fermentation with a yeast, Moniliella pollinis. -
The Generation and Reactivity of Organozinc Carbenoids
The Generation and Reactivity of Organozinc Carbenoids A Thesis Presented by Caroline Joy Nutley In Partial Fulfilment of the Requirements for the Award of the Degree DOCTOR OF PHILOSOPHY of the UNIVERSITY OF LONDON Christopher Ingold Laboratories Department of Chemistry University College London London WCIH OAJ September 1995 ProQuest Number: 10016731 All rights reserved INFORMATION TO ALL USERS The quality of this reproduction is dependent upon the quality of the copy submitted. In the unlikely event that the author did not send a complete manuscript and there are missing pages, these will be noted. Also, if material had to be removed, a note will indicate the deletion. uest. ProQuest 10016731 Published by ProQuest LLC(2016). Copyright of the Dissertation is held by the Author. All rights reserved. This work is protected against unauthorized copying under Title 17, United States Code. Microform Edition © ProQuest LLC. ProQuest LLC 789 East Eisenhower Parkway P.O. Box 1346 Ann Arbor, Ml 48106-1346 Through doubting we come to questioning and through questioning we come to the truth. Peter Abelard, Paris, 1122 Abstract This thesis concerns an investigation into the generation and reactivity of organozinc carbenoids, from both a practical and mechanistic standpoint, using the reductive deoxygenation of carbonyl compounds with zinc and a silicon electrophile. The first introductory chapter is a review of organozinc carbenoids in synthesis. The second chapter opens with an overview of the development of the reductive deoxygenation of carbonyl compounds with zinc and a silicon electrophile since its inception in 1973. The factors influencing the generation of the zinc carbenoid are then investigated using a control reaction, and discussed. -
A Simple Synthesis of 2-Keto-3-Deoxy-D-Erythro-Hexonic
A simple synthesis of 2-keto-3-deoxy-D-erythro-hexonic acid isopropyl ester, a key sugar for the bacterial population living under metallic stress Claire Grison, Brice-Loïc Renard, Claude Grison To cite this version: Claire Grison, Brice-Loïc Renard, Claude Grison. A simple synthesis of 2-keto-3-deoxy-D-erythro- hexonic acid isopropyl ester, a key sugar for the bacterial population living under metallic stress. Bioorganic Chemistry, Elsevier, 2014, 52, pp.50-55. 10.1016/j.bioorg.2013.11.006. hal-03149058 HAL Id: hal-03149058 https://hal.archives-ouvertes.fr/hal-03149058 Submitted on 15 Mar 2021 HAL is a multi-disciplinary open access L’archive ouverte pluridisciplinaire HAL, est archive for the deposit and dissemination of sci- destinée au dépôt et à la diffusion de documents entific research documents, whether they are pub- scientifiques de niveau recherche, publiés ou non, lished or not. The documents may come from émanant des établissements d’enseignement et de teaching and research institutions in France or recherche français ou étrangers, des laboratoires abroad, or from public or private research centers. publics ou privés. A simple synthesis of 2-keto-3-deoxy-D-erythro-hexonic acid isopropyl ester, a key sugar for the bacterial population living under metallic stress ⇑ Claire M. Grison a, , Brice-Loïc Renard b, Claude Grison b a ICMMO UMR 8182, Equipe Synthèse Organique & Méthodologie, Université Paris Sud, Bât. 420, 15 rue Georges Clémenceau, 91405 Orsay cedex, France b CEFE UMR 5175, Campus CNRS, 1919 route de Mende, 34293 Montpellier cedex 5, France abstract 2-Keto-3-deoxy-D-erythro-hexonic acid (KDG) is the key intermediate metabolite of the Entner Doudoroff (ED) pathway. -
Evaluation of Fundamental Characteristics of D-Threitol As
Evaluation of fundamental characteristics of D-Threitol as phase change material at high temperature On Line Number 790 Hideto Hidaka,1 Masanori Yamazaki,1 Masayoshi Yabe,1 Hiroyuki Kakiuchi,1 Erwin P. Ona,2 Yoshihiro Kojima3 and Hitoki Matsuda2 1 Mitsubishi Chemical Group Science and Technology Research Center, Toho-Cho 1, Yokkaichi, Mie 540-8530, Japan, [email protected] 2 Department of Chemical Engineering, Nagoya University, Furo-Cho, Chikusa, Aichi 464-8630, Japan 3 Research Center for Advanced Waste and Emission Management, Nagoya University, Furo-Cho, Chikusa, Aichi 464-8630, Japan ABSTRACT This study focused on polyalcohols as phase change material, which stores a large amount of latent heat at high temperature. D-Threitol, which is an isomer of meso-Erythritol, was studied to obtain its phase change characteristics by means of DSC analysis and a lab-scale heating and cooling apparatus. Usability of D-Threitol as phase change material was evaluated by comparison with other polyalocohols. It was found that D-Threitol started to melt at around 90 degrees C with a relatively large latent heat of 225 kJ/kg. On the other hand, D-Threitol started solidification when the temperature was cooled between at 40 degrees C and 46 degrees C, indicated by a rapid rise to 89 degrees C in a lab-scale heating and cooling apparatus. It was then considered that D-Threitol was applicable as an environmental-friendly PCM for a hot water supply. KEYWORDS Phase change materials, Polyalcohols, Threitol INTRODUCTION Latent heat storage by Phase Change Materials (PCMs) has the advantage to store and release a relatively large quantity of heat in a constant narrow temperature range during phase change. -
Synthesis of New Agonists of Cd1d
Novel Glycolipids in CD1d-mediated Immunity: Synthesis of New Agonists of CD1d by Justyna Wojno A thesis submitted to the University of Birmingham for the degree of DOCTOR OF PHILOSOPHY School of Chemistry College of Engineering and Physical Sciences University of Birmingham February 2012 University of Birmingham Research Archive e-theses repository This unpublished thesis/dissertation is copyright of the author and/or third parties. The intellectual property rights of the author or third parties in respect of this work are as defined by The Copyright Designs and Patents Act 1988 or as modified by any successor legislation. Any use made of information contained in this thesis/dissertation must be in accordance with that legislation and must be properly acknowledged. Further distribution or reproduction in any format is prohibited without the permission of the copyright holder. For my Family Abstract A detailed understanding of the human immune system is crucial for developing novel pharmaceuticals to fight a range of diseases. The glycolipid α-galactosyl ceramide, α-GalCer, has been shown to stimulate the proliferation of murine spleen cells and activate the immune system. Stimulation occurs through binding of the glycolipid to the protein CD1d. Subsequent presentation of the CD1d−glycolipid complex to invariant Natural Killer T cells (iNKT cells) initiates the proliferation of a host of cytokines leading to an immune response. The therapeutic potential of α-GalCer is currently being explored; however the induction of both Th1 and Th2 cytokines by this agent is likely to limit its therapeutic application. The crystal structure of human CD1d in complex with α- GalCer reveals a key hydrogen bond between the N-H of the amide group of the glycolipid and the side-chain O-H of Thr 154 located on the α2 helix of the CD1d molecule; however, the carbonyl group of the amide is not directly involved in binding. -
Accumulation of Inositol by Hibernating Adults of Coccinellid and Chrysomelid Beetles
Title Accumulation of Inositol by Hibernating Adults of Coccinellid and Chrysomelid Beetles Author(s) HOSHIKAWA, Kazuo Citation Low temperature science. Ser. B, Biological sciences, 39, 45-48 Issue Date 1982-03-25 Doc URL http://hdl.handle.net/2115/19112 Type bulletin (article) Note Short Report File Information 39_p45-48.pdf Instructions for use Hokkaido University Collection of Scholarly and Academic Papers : HUSCAP Low T em.p. SeL, Ser. B 39 : 45-48, 1981 Accumulation of Inositol by Hibernating Adults of Coccinellid and Chrysomelid Beetles' Kazuo HOSHIKAWAZ Abstract Accumulation of inositol in hibernating adults of some ladybird species, J-Iellosepilacll11a pustulosa (1.9% of body weight), Eocaria nUllrl (l.8%), Prapylea japanica (l.6%), Halyzia sedecimguttata (l.5%), and a chrysomelid species Paridea angulicaliis (2.3%) is reported. This sugar alcohol, a substance which has not been reported in hibernating insects, decreased rapidly when these insects ceased their hibernation. Introduction Since the first discovery of glycerol and so rbitol accumulated in diapause eggs of Bambyx mari (1), the prevalence of glycerol accumulated in hibernat ing insects has been proved (5). Concomitantly, accumulation of two other substances, trehalose (4) and threitol (2), were also discovered in some insects. H ere the occurrence of another sugar-alcohol, inositol, accumulated in hiber nating adults of some beetles is preliminarily reported, leaving detailed ac" counts. Before going further, I wish to express my sincere thanks to Prof. Sh6ichi F. Sakagami and Dr. Ichir6 Takehara for their reading through the manuscript. Cordial thanks are also due to Dr. Kimio S himada for his kind advice throughout this study. -
Consolidated Bioprocessing of Cellulose to Isobutanol Using Clostridium Thermocellum
Metabolic Engineering 31 (2015) 44–52 Contents lists available at ScienceDirect Metabolic Engineering journal homepage: www.elsevier.com/locate/ymben Consolidated bioprocessing of cellulose to isobutanol using Clostridium thermocellum Paul P. Lin a,1, Lou Mi a,1, Amy H. Morioka a, Kouki M. Yoshino a, Sawako Konishi a, Sharon C. Xu a, Beth A. Papanek c,d, Lauren A. Riley c,e, Adam M. Guss c,d,e, James C. Liao a,b,n a Department of Chemical and Biomolecular Engineering, University of California, Los Angeles, CA 90095, USA b UCLA-DOE Institute of Genomics and Proteomics, USA c Biosciences Division, Oak Ridge National Laboratory, Oak Ridge, TN 37831, USA d Bredesen Center for Interdisciplinary Research and Graduate Education, University of Tennessee, Knoxville, TN 37996, USA e BioEnergy Science Center, Oak Ridge National Laboratory, Oak Ridge, TN 37831, USA article info abstract Article history: Consolidated bioprocessing (CBP) has the potential to reduce biofuel or biochemical production costs by Received 28 April 2015 processing cellulose hydrolysis and fermentation simultaneously without the addition of pre- Received in revised form manufactured cellulases. In particular, Clostridium thermocellum is a promising thermophilic CBP host 6 June 2015 because of its high cellulose decomposition rate. Here we report the engineering of C. thermocellum to Accepted 1 July 2015 produce isobutanol. Metabolic engineering for isobutanol production in C. thermocellum is hampered by Available online 10 July 2015 enzyme toxicity during cloning, time-consuming pathway engineering procedures, and slow turnaround Keywords: in production tests. In this work, we first cloned essential isobutanol pathway genes under different Biofuel promoters to create various plasmid constructs in Escherichia coli. -
Sugar Matrix
Based on perfact’s database holding ingredients for over 250,000 products, we found that almost 300 names for sugar that appear on food labels aren’t covered by the “56 names of sugar” and SugarScience’s 61 names of sugar. The exact number depends on how one counts. This document aims to be a basis to help draw the lines between what should be considered “sugar” within the scope of those lists – and what shouldn’t. Diagram elements ANNOTATED ALTERNATIVE NAME Molecular Source Product sugar or sugar alcohol Diagram element constituting a dietary / functional fiber Molecular Source Product sugar or sugar alcohol Diagram elements explicitly ANNOTATED on 56/61 lists ALTERNATIVE NAME Molecular Source Product sugar or sugar alcohol Diagram elements explicitly or implicitly on 56/61 lists (e.g. because listed by one of its alternative name) Molecular Source Product sugar or sugar alcohol Production pathways Most common Less common This is a working document in progress. Current as of February 2019 Polysaccharides Disaccharides Monosaccharides Sugar alcohols Heat under pressure with hydrogen and Raney-nickel Feed with glucose Ribose Ribitol Ribose syrup Ribitol syrup Bacillus spp. Treat with acid E 967 E 460 Xylose Xylitol E 460I, MCC, CELLULOSE GEL, Treat with acid, pulp, and bleach Xylose syrup Xylitol syrup MICROCELLULOSE Heat under pressure with hydrogen and Raney-nickel Woody plant Cellulose Microcrystalline parts cellulose Wood Treat with acid or enzymes Treat with acid, pulp, and bleach Feed with glucose/sucrose Curdlan Agrobacterium Feed -
Aldrich Alcohols and Phenols
Aldrich Alcohols and Phenols Library Listing – 1,200 spectra Subset of Aldrich FT-IR Library related to alcohols and phenols. The Aldrich Material-Specific FT-IR Library collection represents a wide variety of the Aldrich Handbook of Fine Chemicals' most common chemicals divided by similar functional groups. These spectra were assembled from the Aldrich Collection of FT-IR Spectra and the data has been carefully examined and processed by Thermo. The molecular formula, CAS (Chemical Abstracts Services) registry number, when known, and the location number of the printed spectrum in The Aldrich Library of FT-IR Spectra are available. Aldrich Alcohols and Phenols Index Compound Name Index Compound Name 306 ((1S)-ENDO)-(-)-BORNEOL, 99% 310 (1S,2S,3S,5R)-(+)- 1044 (+)-(4,6-O-BENZYLIDENE)METHYL- ISOPINOCAMPHEOL, 98% ALPHA-D- GLUCOPYRANOSIDE, 351 (2-ENDO, 3-EXO)-5-NORBORNENE- 97% 2,3- DIMETHANOL 1042 (+)-2,3-O-BENZYLIDENE-D- 355 (2-ENDO,3-EXO)- THREITOL, 99% BICYCLO(2.2.2)OCT-5-ENE- 2,3- 528 (+)-ARABINOGALACTAN DIMETHANOL, 96% 305 (+)-BORNEOL, 98% 1130 (2R,3R)-(+)-2-METHYL-3- 1198 (+)-CATECHIN HYDRATE, 98% PHENYLGLYCIDOL, 97% 284 (+)-CIS-P-MENTHANE-3,8-DIOL, 1166 (2R,3R)-(+)-3-(4- 97% BROMOPHENYL)GLYCIDOL, 97% 334 (+)-ISOPULEGOL, 99% 1128 (2R,3R)-(+)-3-PHENYLGLYCIDOL, 340 (+)-LIMONEN-10-OL, 95% 97% 330 (+)-P-MENTH-1-EN-9-OL, 97%, 121 (2R,3R)-(-)-2,3-BUTANEDIOL, 97% MIXTURE OF ISOMERS 129 (2R,4R)-(-)-PENTANEDIOL, 99% 445 (+)-PERSEITOL 122 (2S,3S)-(+)-2,3-BUTANEDIOL, 99% 332 (+)-TERPINEN-4-OL, 96% 1131 (2S,3S)-(-)-2-METHYL-3- 958 (+/-)-4-FLUORO-ALPHA-(N- -
Review on the Impact of Polyols on the Properties of Bio-Based Polyesters
polymers Review Review on the Impact of Polyols on the Properties of Bio-Based Polyesters Kening Lang 1 , Regina J. Sánchez-Leija 1,2, Richard A. Gross 1,3,* and Robert J. Linhardt 1,3,4,* 1 Department of Chemistry and Chemical Biology and Center for Biotechnology and Interdisciplinary Studies, Rensselaer Polytechnic Institute, Troy, NY 12180, USA; [email protected] (K.L.); [email protected] (R.J.S.-L.) 2 Pritzker School of Molecular Engineering, The University of Chicago, 5640 S Ellis Ave, Chicago, IL 60637, USA 3 Department of Biomedical Engineering and Center for Biotechnology and Interdisciplinary Studies, Rensselaer Polytechnic Institute, Troy, NY 12180, USA 4 Department of Biology and Center for Biotechnology and Interdisciplinary Studies, Rensselaer Polytechnic Institute, Troy, NY 12180, USA * Correspondence: [email protected] (R.A.G.); [email protected] (R.J.L.); Tel.: +1-518-276-3734 (R.A.G.); +1-518-276-3404 (R.J.L.) Received: 25 November 2020; Accepted: 9 December 2020; Published: 12 December 2020 Abstract: Bio-based polyol polyesters are biodegradable elastomers having potential utility in soft tissue engineering. This class of polymers can serve a wide range of biomedical applications. Materials based on these polymers are inherently susceptible to degradation during the period of implantation. Factors that influence the physicochemical properties of polyol polyesters might be useful in achieving a balance between durability and biodegradability. The characterization of these polyol polyesters, together with recent comparative studies involving creative synthesis, mechanical testing, and degradation, have revealed many of their molecular-level differences. The impact of the polyol component on the properties of these bio-based polyesters and the optimal reaction conditions for their synthesis are only now beginning to be resolved.