3,032,391 Sttes ICC Patented May 1, 1962
Total Page:16
File Type:pdf, Size:1020Kb
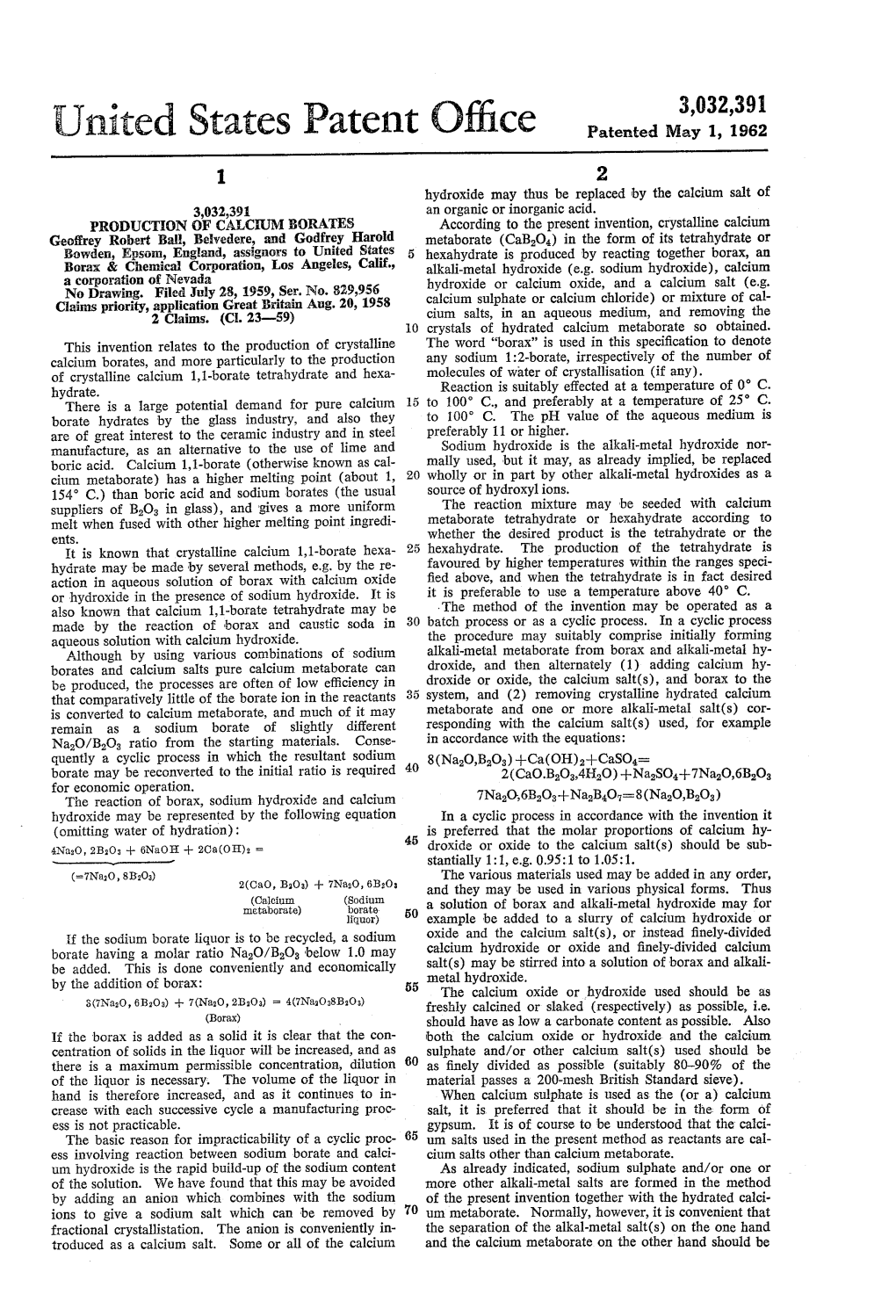
Load more
Recommended publications
-
An Introduction to Boron: History, Sources, Uses, and Chemistry William G
CORE Metadata, citation and similar papers at core.ac.uk Provided by PubMed Central An Introduction to Boron: History, Sources, Uses, and Chemistry William G. Woods Office of Environmental Health and Safety, University of California, Riverside, California Following a brief overview of the terrestrial distribution of boron in rocks, soil, and water, the history of the discovery, early utilization, and geologic origin of borate minerals is summmarized. Modern uses of borate-mineral concentrates, borax, boric acid, and other refined products include glass, fiberglass, washing products, alloys and metals, fertilizers, wood treatments, insecticides, and microbiocides. The chemistry of boron is reviewed from the point of view of its possible health effects. It is concluded that boron probably is complexed with hydroxylated species in biologic systems, and that inhibition and stimulation of enzyme and coenzymes are pivotal in its mode of action. - Environ Health Perspect 102(Suppl 7): 5-11 (1994) Key words: boron, borax, colemanite, glass, boric acid, health effects, enzyme, review Introduction retardants, as micronutrients in fertilizers were an important source of boric acid in Boron is an ubiquitous element in rocks, and for many other purposes, as well. Europe from about 1820 to the 1950s. soil, and water. Most of the earth's soils The varied chemistry and importance Borax also was made from Italian boric have <10 ppm boron, with high concen- of boron is dominated by the ability of acid in England, France, and Germany. trations found in parts of the western borates to form trigonal as well as tetrahe- The borate industry in Turkey com- United States and in other sites stretching dral bonding patterns and to create com- menced in 1865 with mining of the calci- from the Mediterranean to Kazakhstan. -
Living up to Life Special Stain Kit Modified Grocott's Methenamine
Living up to Life Special Stain Kit Modified Grocott’s Methenamine Silver Stain Catalog No: 38016SS12 Intended Use 16. Rinse slides briefly in deionized water. For In Vitro Diagnostic Use. For Laboratory Use. 17. Dehydrate slides in three changes of absolute alcohol. The reagents in this kit are intended for “In Vitro“ use only. The Modified Grocott’s Methenamine 18. Clear slides in two changes of xylene and mount in a xylene miscible medium. Silver Stain when used with appropriate histological protocols may be used for the demonstration of defined fungi and infectious agents such as Aspergillus sp., Pneumocystis Staining Protocol (Microwave) carinii and Cryptococcus neoformans in formalin fixed, paraffin embedded tissue sections. Exercise caution when using the microwave oven to heat any solution or reagent. The microwave must be properly ventilated to prevent the accumulation of fumes in the laboratory. Probable Mode of Action Microwave transparent Coplin jars and caps should be used during the staining process. The The mechanism of action of Modified Grocott’s Methenamine Silver Stain is based upon the caps should be loosely attached to prevent spills. Caps with ventilation holes also may be used. capacity of aldehyde groups to reduce cationic silver (Ag+) to metallic silver. Chromic acid is All microwave ovens should be used in accordance with the manufacturer’s instructions. The used to generate aldehyde groups by the oxidation of 1-2 glycol groups within polysaccharide procedures described here were performed using an Energy Beam Sciences H2250 laboratory rich tissue components, e.g. glycogen, mucin, reticulin and fungal cell walls. When cationic microwave. -
Scientific Committee on Consumer Safety SCCS
SCCS/1249/09 Revision of 28 September 2010 Scientific Committee on Consumer Safety SCCS OPINION ON Boron compounds The SCCS adopted this opinion at its 7th plenary meeting of 22 June 2010 SCCS/1249/09 Opinion on boron compounds ___________________________________________________________________________________________ About the Scientific Committees Three independent non-food Scientific Committees provide the Commission with the scientific advice it needs when preparing policy and proposals relating to consumer safety, public health and the environment. The Committees also draw the Commission's attention to the new or emerging problems which may pose an actual or potential threat. They are: the Scientific Committee on Consumer Safety (SCCS), the Scientific Committee on Health and Environmental Risks (SCHER) and the Scientific Committee on Emerging and Newly Identified Health Risks (SCENIHR) and are made up of external experts. In addition, the Commission relies upon the work of the European Food Safety Authority (EFSA), the European Medicines Evaluation Agency (EMA), the European Centre for Disease prevention and Control (ECDC) and the European Chemicals Agency (ECHA). SCCS The Committee shall provide opinions on questions concerning all types of health and safety risks (notably chemical, biological, mechanical and other physical risks) of non-food consumer products (for example: cosmetic products and their ingredients, toys, textiles, clothing, personal care and household products such as detergents, etc.) and services (for example: tattooing, artificial sun tanning, etc.). Scientific Committee members Jürgen Angerer, Ulrike Bernauer, Claire Chambers, Qasim Chaudhry, Gisela Degen, Gerhard Eisenbrand, Thomas Platzek, Suresh Chandra Rastogi, Vera Rogiers, Christophe Rousselle, Tore Sanner, Kai Savolainen, Jacqueline Van Engelen, Maria Pilar Vinardell, Rosemary Waring, Ian R. -
BORON Boron Compounds Are Used in the Manufacture of Glass, Soaps and Detergents and As Flame Retardants
BORON Boron compounds are used in the manufacture of glass, soaps and detergents and as flame retardants. Naturally occurring boron is present in groundwater primarily as a result of leaching from rocks and soils containing borates and borosilicates. The borate content of surface water can be increased as a result of wastewater discharges, but this use has decreased significantly, and levels of boron in wastewater discharges continue to fall. Guideline value 2.4 mg/l Occurrence Concentrations vary widely and depend on the surrounding geology and wastewater discharges. For most of the world, the concentration of boron in drinking-water is judged to be below 0.5 mg/l. TDI 0.17 mg/kg body weight, based on a BMDL 05 of 10.3 mg boron/kg body weight per day for developmental toxicity (decreased fetal body weight in rats) and an uncertainty factor of 60 (10 for interspecies variation and 6 for intraspecies variation) Limit of detection 0.15 µg/l by ICP/MS; 6–10 µg/l by ICP/AES Treatment performance Conventional water treatment (coagulation, sedimentation, filtration) does not significantly remove boron, and special methods need to be installed in order to remove boron from waters with high boron concentrations. Ion exchange and reverse osmosis processes may enable substantial reduction but are likely to be prohibitively expensive. Blending with low-boron supplies may be the only economical method to reduce boron concentrations in waters where these concentrations are high. Guideline derivation • allocation to water 40% of TDI • body weight 60 kg adult • consumption 2 litres/day Additional comments Because it will be difficult to achieve the guideline value of 2.4 mg/l in some desalinated supplies and in areas with high natural boron levels, local regulatory and health authorities should consider a value in excess of 2.4 mg/l by assessing exposure from other sources. -
Synthesis, Characterization and Fungicidal Effects of Some
Journal of Manmohan Memorial Institute of Health Sciences (JMMIHS) Synthesis, Characterization and Fungicidal Effects of some Organoborates Shaheen Akther1 Khanal DP2 Ullah SS3 Abstract Synthesis of benzoyl borate, phthasloyl borate and oxyl borate was done and characterized by infra red, ultraviolet and mass spectra. All newly synthesized and characterized organoborates were tested for their antifungal activity against pencillium that spoilt mostly celluloid materials stored in museum. All synthesized organoborates are unstable in room temperature and quickly degraded on exposure to air. Benzoyl borate found to be most active antifungal compound of the series against penicillium. The fungicidal activity increases in hydrophobicity and electron withdrawing nature of the benzene ring substituents. These compounds may be good fungicidal for the conservation of celluloid materials lying in the museum. Key words: Organoborates, Silver metaborate, Acyl chloride, spore, Antifungal. Introduction All organoborates are synthesized with the used of silver metaborate (AgBO2) and boric acid [1] with organic halides such as 3,5, dinitrobenzoyl chloride and p-nitrobenzoyl chloride. Since the silver atom in AgBO2 in photo activated state the reaction with organic halides having a polarized halogen atom will readily takes place with the formation of silver halides. Steric effect is an important factor in determining the course of reactions well as the stability of the product. It is observed that acyl chloride reacts more readily than sterically hindered pyrollium chloride [2]. The reaction of silver metaborate with organic halides may be ascribed to an ionic mechanism. Indeed acyllium [3] ion have been recognized as possible intermediate in acid catalyzed etherification in Friedel- Crafts reactions through the universality of such mechanism in doubt and the ion is assumed to resonate between the below structures: R – C O+ R – C+ O The presence of CO group polarizes the carbon halogen bond to great extent. -
Views of the Borax Industry, Ca
http://oac.cdlib.org/findaid/ark:/13030/tf0n39n8j3 Online items available Views of the Borax Industry, ca. 1898-ca. 1915 Processed by Katherine Ruiz. The Bancroft Library, University of California, Berkeley Berkeley, California 94720-6000 1997 Views of the Borax Industry, ca. BANC PIC 1905.17174--PIC 1 1898-ca. 1915 Views of the Borax Industry, ca. 1898-ca. 1915 BANC PIC 1905.17174--PIC The Bancroft Library University of California Berkeley, California1997 Finding aid and digital representations of archival materials funded in part by a grant from the National Endowment for the Humanities. Processed and encoded by: California Heritage Digital Image Access Project staff in The Bancroft Library and The Library's Electronic Text Unit Digital images processed by: The Library Photographic Service Finding aid completed: December 1996 © 1997 The Regents of the University of California Collection Summary Collection Title: Views of the Borax Industry, Date: ca. 1898-ca. 1915 Collection Number: BANC PIC 1905.17174--PIC Creator: Pacific Coast Borax Company Extent: 49 photographic prints ; 20 x 25 cm.49 digital objects Repository: The Bancroft Library. University of California, Berkeley. Berkeley, California 94720-6000 Languages Represented: English Access Collection is available for use. Publication Rights Copyright has not been assigned to The Bancroft Library. All requests for permission to publish photographs must be submitted in writing to the Curator of Pictorial Collections. Permission for publication is given on behalf of The Bancroft Library as the owner of the physical items and is not intended to include or imply permission of the copyright holder, which must also be obtained by the reader. -
The Effects of Borax on Milk Yield and Selected Metabolic Parameters in Austrian Simmental (Fleckvieh) Cows
Veterinarni Medicina, 60, 2015 (4): 175–180 Original Paper doi: 10.17221/8104-VETMED The effects of borax on milk yield and selected metabolic parameters in Austrian Simmental (Fleckvieh) cows M. Kabu, C. Uyarlar Faculty of Veterinary Medicine, Afyon Kocatepe University, Afyonkarahisar, Turkey ABSTRACT: This study was conducted to determine the effects of orally administered borax on milk yield and on several blood variables related to metabolism in early lactation in Austrian Simmental cows (Fleckvieh). Twenty primiparous cows were selected at parturition and then assigned to one of two groups, the control group or the borax group. The study lasted for four weeks. Borax was administered orally at 0.2 mg/kg/day (Boron group) to all treatment cows shortly after the noon milking, whereas cows in the control group were not treated. All cows consumed the same diet. All feeds in the diet were analysed for crude cellulose, protein, ether extract, ash, and dry matter according to the Weende Analysis Systems, in addition to ADF and NDF, according to Van Soest. Blood samples were collected from all cows via the vena jugularis on lactation Days 0, 7, 15, 21 and 28 and ana- lysed for the following: serum boron (B), non-esterified fatty acids (NEFA), beta-hydroxybutyric acid (BHBA), total cholesterol (TChol), high density lipids (HDL), total protein (TP), blood urea nitrogen (BUN), albumin (ALB), creatine (CRE), uric acid (UA), glucose (GLU), aspartate aminotransferase (AST), alanine aminotrans- ferase (ALT) and gamma-glutamyl transpeptidase (GGT) concentrations. Serum B concentration was higher in the borax group than in the control group at Weeks 1, 2, 3, and 4 of the experiment. -
Effect of Borate Addition on the Sintered Properties of Pulverised Fuel Ash E.A
Ceramics International 33 (2007) 993–999 www.elsevier.com/locate/ceramint Effect of borate addition on the sintered properties of pulverised fuel ash E.A. Uwe a, A.R. Boccaccini b, S.G. Cook c, C.R. Cheeseman a,* a Centre for Environmental Control and Waste Management, Department of Civil and Environmental Engineering, Imperial College London, SW7 2BU, UK b Department of Materials, Imperial College London, SW7 2BP, UK c Borax Europe Limited, 1A Guildford Business Park, Guildford GU2 8XG, UK Received 15 December 2005; received in revised form 8 January 2006; accepted 22 February 2006 Available online 25 April 2006 Abstract The effect of borate addition on the properties of sintered pulverised fuel ash (PFA) has been investigated. PFA from a major coal-fired power station in the UK has been formed into monolithic ceramic samples using dry powder compaction and sintering. Borax pentahydrate (Na2B4O7Á5H2O), anhydrous borax (Na2B4O7) and boric acid (H3BO3) were individually added to the PFA and the effects of firing between 1000 and 1200 8C have been investigated. Physical properties (density, water absorption and linear shrinkage), mechanical properties (bending strength and Vickers hardness), phase composition (X-ray diffraction) and sintered microstructure (scanning electron microscopy) are reported. Milling PFA containing 8% (by weight) of borax pentahydrate, to an average particle size of 7.25 mm and sintering at 1130 8C for 1 h, produces ceramics with properties comparable to those of commercial unglazed ceramic wall and floor tiles. The results indicate that PFA could be used to produce commercial ceramics using an economic manufacturing process, although current formulations display excessive shrinkage. -
Available At
Downloaded from https://www.cambridge.org/core. IP address: 170.106.33.19, on 24 Sep 2021 at 18:25:48, subject to the Cambridge Core terms of use, available at https://www.cambridge.org/core/terms. https://doi.org/10.1017/S1755145500148705 VOL. IV.—1890. c THE JOURNAL OF LARYN GO LOGY AND RHINOLOGY; AN ANALYTICAL RECORD OF CURRENT LITERATURE RELATING TO THE THROAT AND NOSE. EDITED BY SIR MORELL MACKENZIE, M.D. Lond., AM) R. NORRIS WOLFENDEN, M.D. Cantab., WITH TUT'. CO-OI'EKAl IuN OF DR. JOHN N. MACKENZIE (BALTIMORE) DR. VALERIUS IDELSON (BERNE) DR. BRYSON DELAVAN (NEW YORK) DR. MICHAEL (HAMBURG) DR. W. PORTER (ST. LOUIS) PROF. RAMON DE LA SOTA Y LASTRA DR. JOAL (MONT DORE) (SEVILLE) PROF. MASSEI (NAPLES) DR. HOLGER MYGIND (COPENHAGEN) PROF. GUYE (AMSTERDAM) DR. SMYLY (DUBLIN) DR. CAPART (BRUSSELS) DR. DAVID COLLINGWOOD (SYDNEY; DR. CONSTANTIN KARWOWSKI (WARSAW) DR. G. W. MAJOR (MONTREAL) DR. BARCLAY J. BARON (BRISTOL) DR. MAXWELL ROSS (EDINBURGH) Dr. G. HUNTER MACKENZIE (Edinburgh). F. A. DAVIS, LONDON: PHILADELPHIA: 40, BERNERS STREET, \V. 1231, FILBERT STREET. Downloaded from https://www.cambridge.org/core. IP address: 170.106.33.19, on 24 Sep 2021 at 18:25:48, subject to the Cambridge Core terms of use, available at https://www.cambridge.org/core/terms. https://doi.org/10.1017/S1755145500148705 Downloaded from https://www.cambridge.org/core. IP address: 170.106.33.19, on 24 Sep 2021 at 18:25:48, subject to the Cambridge Core terms of use, available at https://www.cambridge.org/core/terms. https://doi.org/10.1017/S1755145500148705 CONTENTS. -
14 Boron Element Pub 2020
Publication WSFNR-20-14C March 2020 BORON (B) – Tree Essential Element Dr. Kim D. Coder, Professor of Tree Biology & Health Care / University Hill Fellow University of Georgia Warnell School of Forestry & Natural Resources Boron (B) is a hard, brittle, brown, but light weight solid called a metalloid discovered in 1808. Its name is derived from Persian for a boron containing compound. The rest of its elemental family are all metals. It is never found in pure form. It is used for cleaning products, water softening, antiseptics, heat resistant glass, nuclear reactor rods, and transistors. In Trees Boron is a rare element and the lightest (except for hydrogen) element essential for trees. Boron is one of two essential elements (i.e. silicon is the other) usually present in a tree as a neutral molecule (undissociated form) rather than as an ion. The concentration of boron can vary widely in tissues. Its form in a tree depends upon tissue pH, existing as boric acid (B(OH)3 / H3BO3) where pH is less than 7.0 and the borate ion (B(OH)4-) where pH >7.5. Figure 1. At soil pH of 6.5 to 10.0, boron is poorly available or unavailable to trees. Boron performs one dominant role in trees as part of cell wall structure. Boron helps bind pectic polysaccharides in and between tree cell walls. Deficiency symptoms can quickly occur physiologically and structurally. Element Availability Problems Boron deficiency causes many biological and structural problems in trees. Boron can act as an antibiological agent in trees and when it is in short supply pathogens attacks are more effective and move quicker. -
The Influence of the Presence of Borax and Nacl on Water
sensors Letter The Influence of the Presence of Borax and NaCl on Water Absorption Pattern during Sturgeon Caviar (Acipenser transmontanus) Storage Massimo Brambilla 1 , Marina Buccheri 2, Maurizio Grassi 2 , Annamaria Stellari 1, Mario Pazzaglia 3, Elio Romano 1 and Tiziana M. P. Cattaneo 2,* 1 Consiglio per la Ricerca in Agricoltura e L’analisi Dell’economia Agraria–CREA–Centro di Ricerca Ingegneria e Trasformazioni Agroalimentari, Via Milano, 43–24047 Treviglio (Bergamo), Italy; [email protected] (M.B.); [email protected] (A.S.); [email protected] (E.R.) 2 Consiglio per la Ricerca in Agricoltura e L’analisi Dell’economia Agraria–CREA–Centro di Ricerca Ingegneria e Trasformazioni Agroalimentari, Via G. Venezian, 26–20133 Milano, Italy; [email protected] (M.B.); [email protected] (M.G.) 3 Agroittica Lombarda S.p.A., Via Kennedy, 25012 Calvisano Brescia, Italy; [email protected] * Correspondence: [email protected]; Tel.: +39-02-239-557-212 Received: 10 November 2020; Accepted: 10 December 2020; Published: 15 December 2020 Abstract: Sturgeon caviar quality relies not only on the perfect dosage of the ingredients but also on the long sturgeon breeding cycle (about 12–15 years) and the exact timing of the egg extraction. For the improvement and the promotion of Italian caviar, the development of an analytical system dedicated to fish products, and caviar, in particular, is fundamental. The use of near-infrared spectrometry (NIRS) technology is auspicious. The aquaphotomics approach proved to be an adequate analytical tool to highlight, in real-time, the differences in caviar quality stored with, or without, borax as a preservative. -
Safety Data Sheet
Conforms to Regulation (EC) No. 1907/2006 (REACH), Annex II, as amended by Commission Regulation (EU) 2015/830 - Europe SAFETY DATA SHEET SECTION 1: Identification of the substance/mixture and of the company/ undertaking 1.1 Product identifier Product name : Borax decahydrate - Refining Grade Chemical name : Disodium tetraborate decahydrate Index number : 005-011-01-1 EC number : 215-540-4 REACH Registration number Registration number Legal entity 01-2119490790-32-0019 Rio Tinto Iron & Titanium GmbH (5) CAS number : 1303-96-4 Product type : Solid. Other means of : Borax decahydrate, Sodium tetraborate decahydrate, Borax 10 mol identification 1.2 Relevant identified uses of the substance or mixture and uses advised against Material uses : Refer to the table "Identified uses" below. Identified uses Binding agent Chemical production Complexing agent Corrosion inhibitors and anti-scaling agents Fertilisers Flame retardants Flux agents for casting Intermediate Laboratory chemicals Lubricants and lubricant additives Oxidising agents Photosensitive agents and other photo-chemicals pH-regulating agents Plating agents and metal surface treating agents Process regulator (other than polymerisation or vulcanization processes) Process regulator (used in polymerisation or vulcanization processes) Processing aid not otherwise listed Stabilisers Surface active agents Viscosity modifiers A complete list of uses is provided in the introduction to Annex - Exposure Scenarios Uses advised against Reason Consumer uses above the specific concentration limit. Annex XVII - Restrictions on the manufacture, placing on the market and use of certain dangerous substances, mixtures and articles Date of issue/Date of revision : 18/07/2018 Version : 1 1/16 Conforms to Regulation (EC) No. 1907/2006 (REACH), Annex II, as amended by Commission Regulation (EU) 2015/830 Borax decahydrate - Refining Grade SECTION 1: Identification of the substance/mixture and of the company/ undertaking 1.3 Details of the supplier of the safety data sheet Borax Europe Limited 6 St.